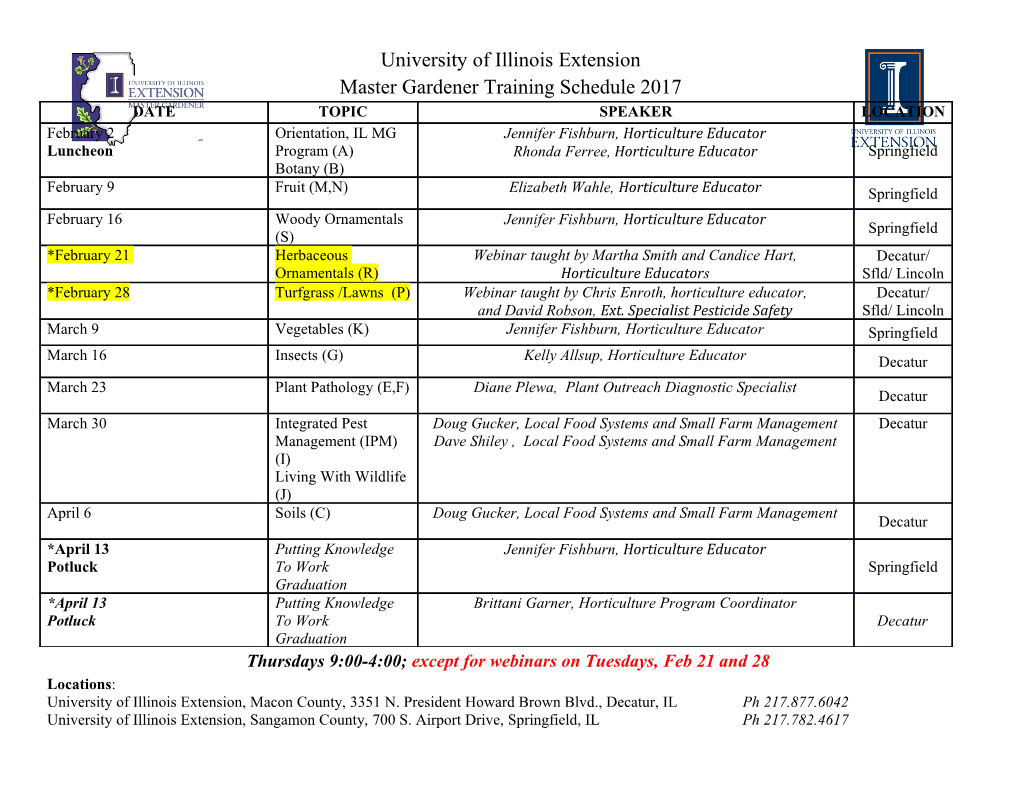
Project No. 16-10226 Enhancement of EM Pump Performance through Modeling and Testing Reactor Concepts Research Development and Demonstration (RCRD&D) Mark Anderson University of Wisconsin, Madison Collaborators Fort Lewis College Melissa Bates, Federal POC Yoichi Momozaki, Technical POC Nuclear Energy University Programs (NEUP) Final Report on Enhancement of EM Pump Performance through Modeling and Testing Project Number: 16-10226 Authors: Jordan Reina, Mike Hvastab, William Nolletc, and Mark Andersona aUniveristy of Wisconsin – Madison, Madison, WI 53706, USA bAlkali Consulting LLC, Lawrenceville, NJ 08648, USA cFort Lewis College, Durango, CO 81301, USA i Executive Summary Liquid sodium has seen development as a nuclear reactor coolant in the United States for over 50 years. While sodium has many desirable characteristics as a heat transfer fluid, its reactivity poses numerous engineering challenges for even the most basic plant components like pumps. Despite the challenges, mechanical pumps have seen success in sodium service albeit at the expense of simplicity and flexibility. In fact, significant failures of these pumps have been recorded which can be attributed to their complexity. Notwithstanding the complexity, mechanical pumps are still widely proposed for the main circuit pump of sodium cooled reactors. However, an alternative to mechanical pumps are Electromagnetic Induction Pumps (EMIPs) which use the principle of the Lorentz Force. EMIPs avoid mechanically moving parts in contact with sodium which simplifies the design by avoiding mechanical wear and seals. Therefore, these pumps are generally safer and more reliable than their mechanical counterparts. That being said, EMIPs suffer from relatively low efficiencies that range from 5% to 45%. Some of the inefficiencies are inherent to the EMIPs pumps; namely, inefficiencies arise in the form of resistive heating losses in the fluid itself. However, other inefficiencies arise from Edge Effects which include Finite Length and Finite Width effects. Due to the significant safety advantages EMIPs have compared to mechanical pumps, there is a strong motivation to integrate these technologies into the design of Generation IV liquid-metal-cooled nuclear power plants. However, EMIPs have low efficiencies partly attributed to Edge Effects. Much of the literature focusing on Edge Effects is dated or simply does not exist in the public domain. More recently, numerical models of EMIPs have shown promising results. However, these models are often custom solvers or use complex software suits which limit their application. This report describes the work completed to understand Edge Effects in two EMIPs designs. These designs are the Annular Linear Induction Pump (ALIP) and Permanent Magnet Induction Pump (PMIP) also known as a Moving Magnet Pump (MMP). The methodology developed during this project aim at measuring key performance parameters (pressure-flowrate and efficiency-slip performance) using high temperature liquid-sodium. Baseline experimental measurements were then used to verify the accuracy of numerical models developed in the software suit ANSYS/FLUENT. On the experimental side, instrumentation was developed to characterize the pressure-flowrate and efficiency-slip performance of both the ALIP and PMIP in high-temperature liquid-sodium. Additionally, instrumentation was developed to measure potential output pressure pulsations and the magnetic field distributions. Moreover, a specialized ALIP was constructed to study the impacts magnetic field tapering, also known as coil grading, on the Finite Length Effect. Lastly, experimental performance curves of the PMIP were collected at 300 oC and 600 oC and compared to analytical theory which accounted for Finite Width Effects. These results showed that the Finite Width Effect and non-uniform magnetic field in a PMIP impact the performance. On the numerical side, models were developed using the software suit FLUENT/ANSYS. These methods were initially compared against a simple MHD flow in a Permanent Magnet Electromagnet Flowmeter (PMEMFM). The results were significant in that they showed agreeance between the numerical model and demonstrated that PMEMFM’s could be calibrated numerically. These modeling methods were then applied to a prototypic PMIP. Results showed that this simple model provided reasonably accurate results of the PMIP p-Q performance. ii Table of Contents Executive Summary ....................................................................................................................................... i List of Figures .............................................................................................................................................. iv List of Tables ................................................................................................................................................ x 1 Introduction ........................................................................................................................................... 1 1.1 Project Objectives ......................................................................................................................... 2 1.2 Methodology and Technical Approach ......................................................................................... 2 2 Literature Review .................................................................................................................................. 4 2.1 Permanent Magnet Electromagnet Flowmeters ............................................................................ 4 2.2 Electromagnetic Induction Pumps ................................................................................................ 6 2.3 Annular Linear Induction Pumps ................................................................................................ 15 2.3.1 Fundamental Components ................................................................................................... 15 2.3.2 Analytical Solution of a Finite Length Pump ..................................................................... 15 2.3.3 Effects of the Finite Length ................................................................................................ 16 2.3.4 Conclusions ......................................................................................................................... 21 2.4 Permanent Magnet Induction Pumps .......................................................................................... 21 2.4.1 Fundamental Components ................................................................................................... 21 2.4.2 Analytical Solution of a Finite Width Pump ....................................................................... 22 2.4.3 Effects of the Finite Width .................................................................................................. 27 2.4.4 Conclusions ......................................................................................................................... 30 2.5 Literature Review Summary ....................................................................................................... 30 3 Numerical Calibration of a PMEMFM ............................................................................................... 32 3.1 Model Development .................................................................................................................... 32 3.2 Experimental Setup ..................................................................................................................... 37 3.3 Results ......................................................................................................................................... 41 3.4 Conclusions ................................................................................................................................. 43 4 Experimental Measurements of ALIP Performance and the Finite Length Effect ............................. 44 4.1 Technical Approach .................................................................................................................... 44 4.2 ALIP Specifications .................................................................................................................... 47 4.3 Experimental Facility .................................................................................................................. 49 4.4 Instrumentation ........................................................................................................................... 51 4.4.1 Permanent Magnet Electromagnet Flowmeter .................................................................... 51 4.4.2 Venturimeter ....................................................................................................................... 52 4.4.3 Magnetic Field .................................................................................................................... 61 iii 4.4.4 Differential Pressure and Pressure Pulsations ..................................................................... 63 4.4.5 Frequency, Power, and Efficiency ...................................................................................... 66 4.5 Results ......................................................................................................................................... 67 4.5.1 Duct Pressure Losses .........................................................................................................
Details
-
File Typepdf
-
Upload Time-
-
Content LanguagesEnglish
-
Upload UserAnonymous/Not logged-in
-
File Pages119 Page
-
File Size-