Appendix R Project Management Plan INTERSERVE CONSTRUCTION Q201 PROJECT MANAGEMENT PLAN Page 1 of 19
Total Page:16
File Type:pdf, Size:1020Kb
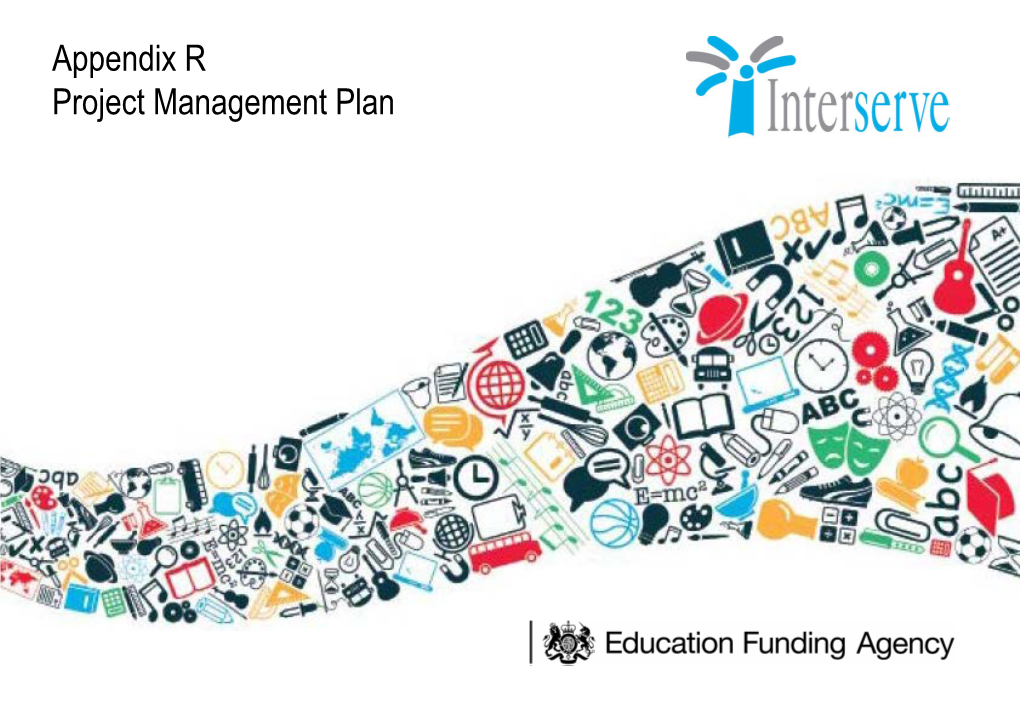
Load more
Recommended publications
-
Industrial Railways July 2019
The R.C.T.S. is a Charitable Incorporated Organisation registered with The Charities Commission Registered No. 1169995. THE RAILWAY CORRESPONDENCE AND TRAVEL SOCIETY PHOTOGRAPHIC LIST LIST 7 - INDUSTRIAL RAILWAYS JULY 2019 The R.C.T.S. is a Charitable Incorporated Organisation registered with The Charities Commission Registered No. 1169995. www.rcts.org.uk VAT REGISTERED No. 197 3433 35 R.C.T.S. PHOTOGRAPHS – ORDERING INFORMATION The Society has a collection of images dating from pre-war up to the present day. The images, which are mainly the work of late members, are arranged in in fourteen lists shown below. The full set of lists covers upwards of 46,900 images. They are : List 1A Steam locomotives (BR & Miscellaneous Companies) List 1B Steam locomotives (GWR & Constituent Companies) List 1C Steam locomotives (LMS & Constituent Companies) List 1D Steam locomotives (LNER & Constituent Companies) List 1E Steam locomotives (SR & Constituent Companies) List 2 Diesel locomotives, DMUs & Gas Turbine Locomotives List 3 Electric Locomotives, EMUs, Trams & Trolleybuses List 4 Coaching stock List 5 Rolling stock (other than coaches) List 6 Buildings & Infrastructure (including signalling) List 7 Industrial Railways List 8 Overseas Railways & Trams List 9 Miscellaneous Subjects (including Railway Coats of Arms) List 10 Reserve List (Including unidentified images) LISTS Lists may be downloaded from the website http://www.rcts.org.uk/features/archive/. PRICING AND ORDERING INFORMATION Prints and images are now produced by ZenFolio via the website. Refer to the website (http://www.rcts.org.uk/features/archive/) for current prices and information. NOTES ON THE LISTS 1. Colour photographs are identified by a ‘C’ after the reference number. -
Lease of Premises to William Aylward 1851. HG / 2 / 297B Handwritten Note
Lease of premises to William Aylward 1851. HG / 2 / 297b Handwritten note, " Whitecliff – Brading". This Indenture made the twentieth day of December in the Year of our Lord one thousand, eight hundred and fifty one Between Sir Graham Eden Hamond of Norton Lodge in the parish of Freshwater in the Isle of Wight, Baronet, of the one part and William Aylward of the parish of cattle Wymmering in the County of Southampton, Brickmaker, of the other part, Witnesseth that in consideration of the Rent and Covenants hereinafter reserved and contained, the said Sir Graham Eden Hamond doth hereby demise and lease unto the said William Aylward, his Executors, administrators and assigns All that piece or parcel of Land situate at Whitecliff in the parish of Brading in the said Isle adjoining the seashore as the same is more particularly described by the Plan thereof drawn in the Margin of these presents on part of which said piece of Land there was formerly a Brick Kiln in the occupation of Cooper Together with full liberty to erect Kilns, Sheds and other Erections upon the said piece of land and to dig and get upon the said piece of land Brick-Earth, Loam, Sand, Chalk and Flints and to make and manufacture the same upon the said premises and not elsewhere into Bricks, Tiles and other articles for the purposes of Sale and to sell and dispose of the same when so manufactured, but not otherwise, Together also with all ways, paths, waters, profits, privileges and appurtenances to the said piece of land belonging ....... -
Freight Train Operation in Inter-War Britain
Management Information and Management Practice: A Freight Train Operation in Inter-War Britain Roy A. Edwards Department of Economic History, The London School of Economics Phd Dissertation UMI Number: U616001 All rights reserved INFORMATION TO ALL USERS The quality of this reproduction is dependent upon the quality of the copy submitted. In the unlikely event that the author did not send a complete manuscript and there are missing pages, these will be noted. Also, if material had to be removed, a note will indicate the deletion. Dissertation Publishing UMI U616001 Published by ProQuest LLC 2014. Copyright in the Dissertation held by the Author. Microform Edition © ProQuest LLC. All rights reserved. This work is protected against unauthorized copying under Title 17, United States Code. ProQuest LLC 789 East Eisenhower Parkway P.O. Box 1346 Ann Arbor, Ml 48106-1346 I Hr££ £ S F 7382. POLITICAL tOMl C & ACKNOWLEDGEMENTS A thesis always involves contributions and support from family and friends, as well as colleagues. It was my good fortune that in the writing of the thesis, colleagues became friends. In particular, my supervisor Dudley Baines provided insights both into railway operation and analysis. Mary Morgan as my second supervisor provided a critical review of early drafts which both built confidence and demolished long cherished ideas. To them both I owe a great deal. In my more desperate moments, Linda Sampson provided an insight into the correct use of Word Perfect and prevented, or at least ameliorated, a complete loss of mental faculties as the submission date drew near. I am also greatful to Rajiv Ball who helped in the final preparations for submission. -
Environmental Statement, Volume 2
A421 Improvements M1 Junction 13 to Bedford Environmental Statement, Volume 2 March 2007 A421 Improvements M1 Junction 13 to Bedford Environmental Statement, Volume 2 CONTENTS (Volume 2A) 5 POLICIES AND PLANS 6 LAND USE AND AGRICULTURE 7 CULTURAL HERITAGE 8 LANDSCAPE AND VISUAL ASSESSMENT 9 ECOLOGY AND NATURE CONSERVATION Volume 2B 10 GEOLOGY AND SOILS 11 ROAD DRAINAGE AND THE WATER ENVIRONMENT 12 NOISE AND VIBRATION 13 AIR QUALITY 14 PEDESTRIANS, CYCLISTS, EQUESTRIANS AND COMMUNITY EFFECTS 15 VEHICLE TRAVELLERS 16 DISRUPTION DUE TO CONSTRUCTION March 2007 A421 Improvements M1 Junction 13 to Bedford Environmental Statement, Volume 2 March 2007 A421 Improvements M1 Junction 13 to Bedford Environmental Statement, Volume 2 CONTENTS 10 GEOLOGY AND SOILS ....................................................................................10-1 10.1 Introduction .............................................................................................10-1 10.2 Potential Impacts and Effects..................................................................10-1 10.3 Methodology ...........................................................................................10-1 10.4 Baseline Conditions ................................................................................10-4 10.5 Mitigation and Detailed Development of the Scheme Design ...............10-21 10.6 Environmental Effects ...........................................................................10-26 10.7 Summary ..............................................................................................10-30 -
'A Study of the Suitability of Callow for Reclamation' By
'A STUDY OF THE SUITABILITY OF CALLOW FOR RECLAMATION' BY LILLIAN MARY STUART HARRISON A THESIS SUBMITTED FOR THE DEGREE OF DOCTOR OF PHILOSOPHY OF THE UNIVERSITY OF LONDON. DEPARTMENT OF MINERAL RESOURCES ENGINEERING IMPERIAL COLLEGE OF SCIENCE AND TECHNOLOGY UNIVERSITY OF LONDON ' OCTOBER I9#f ABSTRACT The purpose of this project was to investigate the suitability of callow (calcareous clay overburden arising from the excavation of Oxford Clay) as a growing medium in reclamation schemes. Its abundance and relative "cheapness" means that it is an ideal top-soil replacement material, if it could be proved to be of benefit to reclamation schemes, Samples of the callow were analysed in the laboratory for nutrient status, pH, water-relationships, cation exchange capacities and other soil-related variables. A series of sites was established so that natural succession on callow could be studied, to investigate whether natural colonisation may provide clues as to the suitability of certain species for reclamation. Field and greenhouse trials were carried out on the callow, to investigate the best types of agricultural uses and fertiliser regimes for use with callow as a growing medium, A variety of grasses, legumes, herbs, shrubs and trees colonise the callow when it is left to natural succession. Natural succession, analysed by ordination techniques could not be related to any of the measured soil-related variables. The callow was found to be deficient in nitrates and phosphates. Growth trial results confirmed these findings. A variety of grass seed mixes with or without legumes can be established on the callow, once nutrient deficiencies are corrected. -
Central Bedfordshire Council
An application for Development Consent Order for an up to 299 megawatts (MW) gas fired peaking power generation plant designed to produce electricity, along with associated development, such as a gas connection and electrical connection at Rookery South Pit, near Stewartby, Bedfordshire LOCAL IMPACT REPORT IPC Reference Number EN01006 Local Impact Report Central Bedfordshire Council 1.0 Introduction 1.1 This report has been prepared on behalf of Central Bedfordshire Council in accordance with the advice and requirements set out in the Planning Act 2008 and the Advice Note One: Local Impact Reports issued by the Infrastructure Planning Commission in March 2010. 1.2 The Advice note states that a Local Impact Report is a ‘Report in writing giving details of the likely impact of the proposed development on the authority’s area. 1.3 The Advice Note states that when the Commission decides to accept an application it will ask the relevant local authorities to prepare a Local Impact Report and this should be prioritised whether or not the local authority considers that the development would have a positive, negative or neutral effect on the area. The Report may include any topics that they consider to be relevant to the impact of the development on their area as a means by which their existing body of knowledge and evidence on local issues can be fully and robustly reported to the Commission. 1.4 The Advice Note indicates that topics addressed in the LIR may include: • Site description and surroundings/location • Details of the proposal • Relevant -
SUPPLEMENT to the LONDON GAZETTE, 31St DECEMBER 1986
64 SUPPLEMENT TO THE LONDON GAZETTE, 31sT DECEMBER 1986 Name Description Address Kodak, Ltd Manufacturers of Photographic Supplies Hemel Hempstead LEP (Bloodstock) Ltd International Bloodstock Forwarders Tunbridge Wells Lambert, James & Sons, Ltd. Suppliers of Building Materials Snettisham Langton.WJE Suppliers of Milking Machine Components Coventry Latham, James PLC Wood Merchants London Launer, S. & Co. (London) Ltd. ... Manufacturers of Handbags Croydon Ken Leech Trees Fruit Tree Nurserymen Buhner Tye, Sudbury Lewis East Ltd Manufacturers of Stationery Leicester Leyland Vehicles Ltd Manufacturers of Commercial Vehicles Preston Lidstone, W. A., Ltd. Suppliers of Animal Feed, Fertiliser and Crop Protection Maidenhead Chemicals. Lilliman and Cox, Ltd. Dry Cleaners London Lillywhites, Ltd Outfitters London Lincolnshire Drainage Co. Ltd. ... Drainage Contractors Boston Lister Shearing Equipment Limited Manufacturers of Animal Health Care Products Gloucester Lock, S., Ltd Embroiderers London London Brick Company Limited ... Brick Makers Bedford Longmire, Paul, Ltd Supplier of Jewellery and Leather Goods London Luda Pet Food Limited Dog and Game Food Manufacturers Louth Lusher, W. S. & Son, Ltd Building Contractor Norwich M.K. Electric Limited Manufacturers of Electrical Equipment London Mann, Egerton & Co. Ltd. Automobile Engineers Norwich Mappin & Webb, Ltd Silversmiths London Marley Building Products Limited Building Manufacturers and Constructors Guildford Marley Floors Ltd. Suppliers of Floor Tiles Maidstone Marley Roof Tile Co. Ltd., -
Interserve AR 2006 Cover Tp
Interserve Plc Annual report and financial statements 2006 Whole-life services Extended reach, expanded markets, enhanced capabilities Contents 1 Highlights of 2006 2 Our profile and principal activities 4 Directors and advisers 6 Chairman’s statement 7 Directors’ report 7 Business review 7 Strategy 8 Operational review 18 Case studies 22 Financial review 26 Principal risks and uncertainties 28 Corporate social responsibility 38 Corporate governance 43 General information and disclosures 45 Directors’ remuneration report 54 Directors’ responsibility statement 55 Independent auditors’ report (consolidated financial statements) 56 Consolidated financial statements 56 Income statement 57 Statement of recognised income and expense 58 Balance sheet 59 Cash flow statement 60 Notes 95 Independent auditors’ report (Company financial statements) 96 Company financial statements 96 Balance sheet 97 Notes 103 Principal undertakings and trading activities 108 Shareholder information Highlights of 2006 Interserve is a services, maintenance and building group. • Revenue up 16 per cent to £1,408.5 million (2005: £1,214.5 million) • Profit before tax, exceptional items and amortisation: up 61 per cent to £58.1 million (2005: £36.0 million)a • Net cashflow from operating activities up 15 per cent to £40.1 million (2005: £34.8 million) • Earnings per share before exceptional items and amortisation: up 68 per cent to 31.7p (2005: 18.9p)b • Full-year dividend: increased by 4.8 per cent to 15.4p (2005: 14.7p) “Our trading performance emphatically demonstrated the strength of each of Interserve’s three main operating divisions, with headline earnings per share rising by 68 per cent to 31.7 pence (2005: 18.9 pence). -
Annual Report 2010 Financial Highlights
Annual Report 2010 Financial highlights Figures in EURm 2004 2005 2006 2007 2008 2009 2010 Number of employees as at 31 December 42,062 41,260 40,983 67,916 60,841 53,302 53,437 Sales volumes Cement and clinker (million tonnes) 65.2 68.4 79.7 87.9 89.0 79.3 78.4 Aggregates (million tonnes) 69.5 77.2 85.8 179.6 299.5 239.5 239.7 Asphalt (million tonnes) 4.8 12.1 10.0 9.1 Ready-mixed concrete (million cubic metres) 19.5 21.8 24.9 32.7 44.4 35.0 35.0 Profit and loss accounts Total Group turnover 6,929 7,803 7,997 10,862 14,187 11,117 11,762 Operating income before depreciation (OIBD) 1) 1,243 1,547 1,890 2,423 2,946 2,102 2,239 Operating income 1) 759 1,051 1,429 1,850 2,147 1,317 1,430 Profit/loss for the financial year -333 471 1,026 2,119 1,920 168 511 Group share -366 415 951 2,022 1,808 43 343 Dividend in EUR per share 0.55 1.15 1.25 1.30 0.12 0.12 0.25 4) Investments Investment in tangible fixed assets 466 548 506 1,039 1,101 795 734 Investment in financial fixed assets 45 389 315 11,735 150 25 138 Total investment in fixed assets 511 937 821 12,774 1,251 820 872 Free cash flow Cash flow from operating activities 937 795 1,259 1,911 1,523 1,164 1,144 Cash flow from investing activities 2) -309 -747 -665 -10,677 1,113 -539 -648 Balance sheet Shareholders' equity and minority interests 3,936 5,058 5,828 7,519 8,261 11,003 12,884 Balance sheet total 10,716 11,935 12,318 29,201 26,288 25,508 27,377 Net debt 3) 3,668 3,545 3,081 14,608 11,566 8,423 8,146 Ratios OIBD margin 17.9 % 19.8 % 23.6 % 22.3 % 20.8 % 18.9 % 19.0 % Net debt/shareholders’ equity (gearing) 3) 92.7 % 70.1 % 52.5 % 193.4 % 139.8 % 76.5 % 62.9 % Net debt/OIBD 3) 2.95x 2.29x 1.63x 6.03x 3.93x 4.01x 3.64x Earnings per share (EUR) -3.64 3.74 8.22 17.11 14.55 0.30 1.83 1) 2004 - 2006: figures have been restated as a result of the reclassification of emission rights and pension interest (IAS 19). -
Roofing Today 67 Nov16
RoofingIssue 67 magazine TODAY November 2016 Contents Page 4 News Page 8 The Only Way is Up for the Roofing Sector Richard Clews, Prater Page 10 Brexit and the Impact on Raw Materials Liam O’Hara, SIG Building Solutions Page 12 Liquid Roofing: the Quality Debate Terry Wain, LRWA Page 16 An Integrated Supply Chain Tony Burke, Avonside Group Services Page 18 Pitching in with Fibre Cement Justin Ransted, Cembrit Page 20 Specifying Single Ply Roofing Jim Hooker, SPRA Page 24 Ignore Roofing Sealants at Your Peril Debra Taylor, Brett Martin Daylight Systems Page 26 Knee Injuries Go Through the Roof Page 28 A Right Royal Roof Refurbishment Page 30 Time To Check Your Warranties? Janine Brady, SIG Roofing Page 32 Rainwater Systems for Commercial and Industrial Buildings Jon Angrave, Hunter Plastics Page 34 Roofers’ Duty of Care Doesn’t Stop with Feet on the Ground David Mountfield, Kinesis Telematics Page 36 Risk, Margins and Insurance Karl Jones, Kerry London Ltd Page 40 Natural Slate - Insist on the Best Amanda Green, SIGA Slate Page 42 Calling Young Roofers- Your Industry Needs You! Page 43 Reader Offer – Win a Werner Double-section Sliding Roof Ladder Page 46 Technical Roofing Queries Simon Dixon, Competent Roofer Page 48 Product News Publisher: David Cowell - [email protected] Roofing Today Magazine is published by Editor: Dr Claire Griffiths - [email protected] Construction Media Publishing Ltd 31 Seymour Terrace, Seymour Street, Liverpool L3 5PE Administration: Jemma Daly - [email protected] Tel. 0151 708 0070 Fax. 0151 708 0888 Media Accounts: Brenda McNally - [email protected] [email protected] Media Accounts: Paul Fitzgerald - [email protected] www.roofingtoday.co.uk Every effort has been made by the publishers to ensure the accuracy of the contents of this magazine. -
Slslibrarymasteraccessionlist
US 15000 The Minneapolis & St Louis Railway Co Minneapolis & St Louis 1943 US 15001 The Tootin' Louie A History of the Minneapolis & St D.F.Hofsommer University of Minnesota 2005 Louis Railway US 15002 Mopac Power Missouri Pacific Lines & Locomotives J.G.Collias Howell-North Books 1980 1905-1955 US 15003 Natchez Route A Mississippi Central Railroad D.S.Price & L.R.Saillard NRHS 1975 US 15004 Missouri Pacific Annual 1975-1976 J.Eagan Prototype Modeler 1978 US 15005 Morristown & Erie Railroad T.T.Taber III Railroadians of America 1967 US 15006 Katy Power Locomotives & Trains of the Missouri- J.G.Collia & R.B.George Jr MM Books 1986 Kansas-Texas RR 1912-1985 US 15007 The North Arkansas Line J.R.Fair Jr Howell-North Books 1969 US 15008 The Missouri Pacific Lines in Colour J.G.Collias MM Books 1993 US 15009 Missouri Pacific Diesel Power K.EuDaly White River Pubs 1994 US 15010 Missouri Pacific Northwest The Kansas City I.E.Quastler South Platte Press 1994 Northwestern RR US 15011 The Moffat Road E.T.Bollinger & F.Bauer Alan Swallow 1967 US 15012 Monon The Hoosier Line G.W.Dolzall & S.F.Dolzall Interurban Press 1987 US 15013 Monon Route G.W.Hilton Howell-North Books 1978 US 15014 The Monongahela Railway History & Operation 1903- D.E.Gratz & T.E.Arbogast M2FQ Pubs 2003 2003 US 15015 The Morristown & Erie Railway B.Pennisi Redwood Press 1986 US 15016 Napa Valley Route I.A.Swett & H.C.Aitken Jr Interurban Press 1975 US 15017 Narragansett Pier RR A Short Haul to the Bay J.N.J.Henwood Greene 1968 US 15018 Nashville, Chattanooga & St Louis RR R.E.Prince -
Permit Number
Permit Number (as Operator Name Installation Name 2013 2014 2015 2016 2017 2018 2019 2020 shown in the Registry) GB-DTI0200 Centrica Storage Ltd Rough 47/3B 66144 64995 63833 62658 61471 60272 59059 57841 GB-DTI0300 EnQuest Heather Limited Kittiwake Alpha 61921 60846 59758 58658 57547 56425 55288 54148 GB-DTI0400 Apache North Sea Limited Forties Alpha 69336 68131 66913 65682 64437 63181 61909 60632 GB-DTI0600 Apache North Sea Limited Forties Charlie 47229 46409 45579 44740 43892 43037 42170 41300 GB-DTI0700 Apache North Sea Limited Forties Delta 66347 65195 64029 62851 61660 60458 59240 58019 GB-DTI9250 Premier Oil UK Limited Balmoral 34174 33580 32980 32379 31760 31140 30513 29884 CNR International (UK) GB-DTI9300 Limited Tiffany 104432 102618 100783 98929 97055 95162 93246 91323 GB-DTI1000 Britannia Operator Limited Britannia 286653 281674 276637 271547 266402 261207 255947 250670 Morecambe Central Processing GB-DTI1200 Hydrocarbon Resources Ltd Complex 168235 165313 162356 159369 156350 153301 150214 147116 Dana Petroleum (E&P) GB-DTI1300 Limited Triton FPSO 38711 38039 37359 36671 35977 35275 34565 33852 Eni Liverpool Bay Operating GB-DTI1400 Company Douglas 55085 54128 53160 52182 51193 50195 49184 48170 Eni Liverpool Bay Operating Oil Storage GB-DTI1500 Company Installation (OSI) 3024 2971 2918 2864 2810 2755 2700 2644 GB-DTI1600 Apache Beryl I Limited Beryl Alpha 197253 193827 190360 186858 183317 179743 176124 172492 GB-DTI1700 Apache Beryl I Limited Beryl Bravo 185158 181942 178688 175400 172077 168721 165324 161915 GB-DTI1011