SWIFT® Evo SPINNING WHEEL INTEGRATED FORCE TRANSDUCER
Total Page:16
File Type:pdf, Size:1020Kb
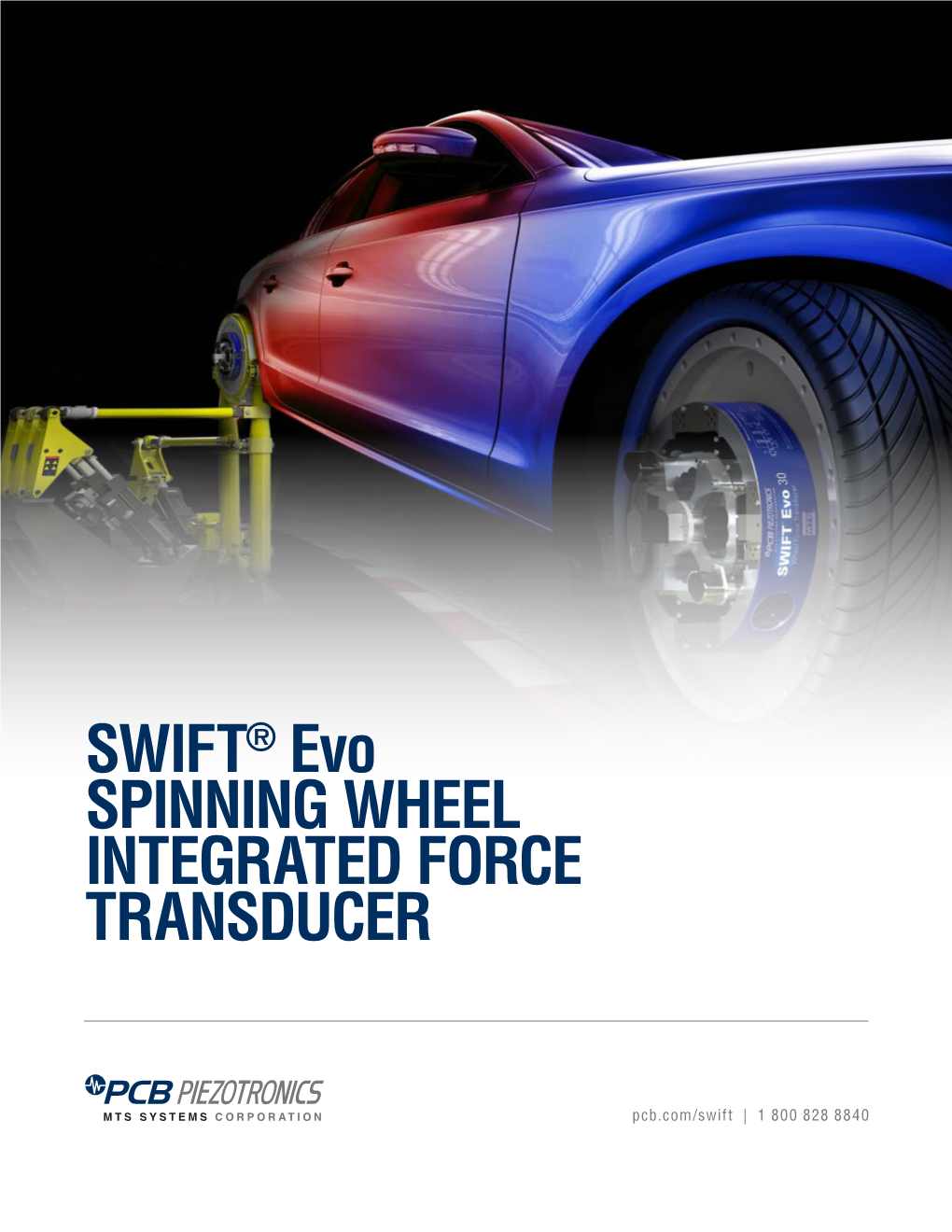
Load more
Recommended publications
-
And Rear Driveline Package for Formula SAE
Lightweight Torsen Style Limited Slip Differential and Rear Driveline Package for Formula SAE by Tony Scelfo SUBMITTED TO THE DEPARTMENT OF MECHANICAL ENGINEERING IN PARTIAL FULFILLMENT OF THE REQUIREMENTS FOR THE DEGREE OF BACHELOR OF SCIENCE AT THE MASSACHUSETTS INSTITUTE OF TECHNOLOGY JUNE 2006 C2006 Tony Scelfo. All Rights Reserved. The author hereby grants to MIT permission to reproduce and to distribute publicly paper and electronic MASSACHUt'i'Fl-. I I'ITUTE copies of this thesis document in whole or in part Or 'r.. v,, in any medium now known or hereafter created. AU 0 2 2006 /, // LIBRARIES Signature of Author 4::epx ep ,tof Mechanical Engineering May 12, 2006 Certified by I 1// ' ) J ?Daniel Frey Professor of Mechanical Engineering Thesis Supervisor Accepted by _ i__ _l.__ __ John H. Lienhard V KCj I . rossor of Mechanical Engineering Chairman, Undergraduate Thesis Committee ARCHIVES Table of Contents ABSTRACT......................................................................................................................... 7 I FSAE Competition ........................................................................................................... 9 2 Overall Design Philosophy........................................ 10 2.1 Functional Requirements....................................................................................... 10 2.2 Manufacturing Concerns ........................................ 11 2.3 Integration ............................................................................................................. -
The Butler Passport to Higher Performance Rel
The Butler Passport to Higher Performance rel. Sept. 2003 2.0.0 RIM. 2.1.0 DEFINITION. The rim is the part of the wheel that has a suitable profi le and is of suitable dimensions to be a seat for the tyre. Passenger car rims are made up of three distinct areas, each of which performs a particular function: • a dropped central part, which is necessary for the operations of mounting and demounting the tyre; • two lateral fl anges, which bear the axial thrusts; • two conical seats, which serve as fastening seats for the tyre beads. The profi le can be symmetric as regards the central line. Usually, however, it is asymmetric in order to leave more room for the braking equipment. 2.1.1 RIM DESIGNATION. The dimensions of existing rim types are (further) expressed in F.E.: 4 1⁄2× 12. New concepts or types have to be expressed in mm when mounted in combination with new types/concept of tyres. F.E.: 365 × 150 TD, CT 450 × 150, PAX 145 × 360 A (Pict.1) Most of the times, also the type of rim edge is mentioned: F.E.: 4 1⁄2 ×B 12, 5 1⁄2 J × 13 (see chapter 2.11.0 “Different Rim Edges). Symmetrical rims are indicated with an additional “s” F.E.: 4 1⁄2 ×J 13 - S The symbol “×” indicates a “one-piece” rim: F.E.: 4 1⁄2× 12 The symbol “-” indicates a “multi-piece” rim: F.E.: 15 - 5 1⁄2 F SDC. The “DIN” and “ETRTO” sizing are putting fi rst the rim width followed by the diameter: F.E.: 6 J × 15. -
Keyways for Drive Wheels & Custom Specials Wheels
Wheels: Keyways for Drive wheels & Custom Specials Durable Superior Casters® Drive wheels can be made out of a variety of steel core wheels; most drive wheels have a molded tread (Polyurethane or Rubber) for traction, to grab and drive the desired materials. A Keyway is a machined notch in a wheel bore allowing the wheel to be locked onto a drive shaft using a “key” that slides into correlating notches between the wheel bore and a drive shaft, the shaft is then able turn or drive the wheel. Keyways can be machined into steel wheel bores with sufficient material thickness; sleeves can also be pressed into wheel bores to provide a keyway for smaller shaft sizes and are anchored by the means of set screws. Due to the stress & friction associated with drive wheel application, wheel capacities will be reduced by 50% and tread life of Polyurethane & Rubber will be shorter depending on speed, weight and duration of driving activity. Normal warranties do not apply to any drive wheels other than guaranteeing specification characteristics. Below chart shows guidelines for standard dimensions, actual part numbers may vary according to desired dimensions. Some wheel bores / shaft sizes and keyway configurations may not be available for certain wheel diameters, tread width and materials, please inquire with our customer service or engineering department for details. Standard Keyways, Key O.D. Sizes & Set Screws Wheel Bore or Diameter of Keyway **Keyway Part# **Keyway Part# with *Shaft. Use plain bore part# for *Key O.D. **Keyway Part# with 1 Set Screw 2 Set Screws (1 over standard sizes, please contact us Width Depth Dimensions. -
Superior Rideability
SUPERIOR RIDEABILITY RAZOR ▶ RAZOR IRS CONVERSION FOR HONDA GL 1800 MOTORCYCLES WANTED: RIDERS WITH AN EDGE Let out the aggressive side of your Gold Wing with the Razor: a sharp new body design on top of the best independent rear suspension conversion for the Honda® GL 1800™. Shown with optional 17" chrome BLVD rear wheels & tires, Performance Machine front wheel, side cover upgrade, and dual disc mechanical parking brake. 1-800-90-TRIKE • www.motortrike.com • FIND AN AUTHORIZED DEALER NEAR YOU AVAILABLE - Front & Rear Billet Aluminum Wheels OPTIONS - Front Wheel Balancer - Fender Bras with Optional Embroidery Motor Trike offers more Standard - Front End 4.5 Degree Rake Kit Features and Accessories than anyone - ABS Integration Kit - Parking Brake Kit else in the industry. - One-Piece Weight-Bearing Aqua Shields* - Aqua Shields Fog Lights* - Aqua Shield Color-Match Paint* - Aqua Shield Bras* - Trailer with Complementary Styling - Trailer Hitch Assembly - Trailer Wiring Harness with 6 Pin Connector - Chrome Nerf Bumper - Matte Black Nerf Bumper - Chrome Peterson Light Bar* - Chrome Küryakyn Light Bar* - Echo Exhaust - Trunk Carpet - Embroidered Trunk Mat - Chrome Side Cover Upgrade (2012 & Up) STANDARD FEATURES - Trike Cover - Independent Rear Suspension - Chrome Fender Trim - On-Board Air Compressor - Color-Match Paint - Patented Air Ride Suspension *Coming soon. - Over 4” of Suspension Travel Please visit our website for pricing. - Progressive Coil Over Shocks - Integrated Disc Brake System - Trike Trunk "Open" Warning Indicator - Trunk Light on Interior of Door - Hidden Trunk Door Hinges - Chrome Steel Wheels - 12 Volt Power Outlet in Trunk - Exceptional Plastic Side Cover Fit - LED Air Suspension & Voltmeter Readout All Motor Trike conversions include a patented air ride suspension, rear tires and wheels, interior trunk light, and a 3-year/60,000 mile warranty. -
What Is Match Mounting?
dding performance vehi- cle owners to your cus- tomer list can give a huge boost to your shop’s bot- tom line. These owners may be demanding—even picky—but they’ll pay well to get the jobA done exactly the way they want it. Some of the most common types of work done on performance vehicles in- volve the wheels and/or tires. The wheels are one of the most visible parts of a vehicle, so any work done on them must be top-notch—meaning clean, pretty and accurate. Custom wheel service can be broken down into two primary topics, essential- ly—tire match mounting and custom wheel handling. Since you’ll never mount a wheel without a tire, we’ll cov- er the ins and outs of tire match mounting first. What Is Match Mounting? Match mounting involves positioning the tire onto the wheel to minimize or eliminate the final combination of radial force variation and/or imbalance (radial force variation is explained later in this article). One match mounting approach involves aligning the tire’s point of maxi- mum radial force variation (its high spot) to the wheel’s radial low spot (where the wheel’s radial runout is the lowest). This is called the Uniformity Method. The other approach involves simply aligning the tire’s lightest balance point to the wheel’s heaviest balance point, called the Weight Method. OE tire suppliers are required to mark a tire’s radial runout high point, and OE wheel makers are required to mark a wheel’s radial runout low point. -
Vehicle Warranty Manual
VEHICLE WARRANTY MANUAL Please read completely thoroughly to ensure your safety and proper care of your SCA Performance vehicle. SCA Performance, Inc. 7769 Gadsden Highway Trussville, AL 35173 (205) 655-1063 Fax (205) 655-2689 www.scaperformance.com Important First Step! Please visit www.scaperformance.com/warranty, fill out the warranty registration form, and automatically enroll in the SCA Performance Passion. Driven. Owners’ Club today! Table of Contents Vehicle Operation and Maintenance………………………………………………….3 Custom Component Maintenance Schedule………………………………………4 Original Owner’s Assistance Program…………………………………………………6 Warranty Coverage At-A-Glance………………………………………………………..9 Wheel Warranty………………………………………………………………………………11 Custom Paint/Striping Warranty………………………………………………………11 Electronics/Auxiliary Lighting Warranty……………………………………………11 Engine Upgrades/Tuning Warranty………………………………………………….11 Suspension Warranty……………………………………………………………………….11 What Is Not Covered………………………………………………………………………..12 CUSTOM VEHICLE WARRANTY AN IMPORTANT MESSAGE TO SCA PERFORMANCE CUSTOM VEHICLE OWNERS… COMMITMENT TO YOU At SCA Performance, we are committed to assuring your satisfaction with your new custom vehicle. Your dealer also wants you to be completely satisfied and invites you to return for all your service needs. VEHICLE OPERATION AND CARE Considering the investment you have made in your custom vehicle, we know you will want to operate and maintain it properly. We urge you to follow the FACTORY MAINTENANCE INSTRUCTIONS contained in your original equipment owner’s manual. We also encourage you to follow the Custom Component Maintenance Schedule for SCA Performance installed parts, which can be found on Pages 4-5 of your SCA warranty manual. NOTE: Lack of maintenance, as recommended by the OE/SCA Owner’s Manuals, may result in damage to your custom vehicle. If you have specific questions on how to keep your custom vehicle in good working condition, see your dealer or contact SCA Performance for instruction. -
Rolling Contact Fatigue: a Comprehensive Review Administration
U.S. Department of Transportation Federal Railroad Rolling Contact Fatigue: A Comprehensive Review Administration Office of Railroad Policy and Development Washington, DC 20590 DOT/FRA/ORD-11/24 Final Report November 2011 NOTICE This document is disseminated under the sponsorship of the Department of Transportation in the interest of information exchange. The United States Government assumes no liability for its contents or use thereof. Any opinions, findings and conclusions, or recommendations expressed in this material do not necessarily reflect the views or policies of the United States Government, nor does mention of trade names, commercial products, or organizations imply endorsement by the United States Government. The United States Government assumes no liability for the content or use of the material contained in this document. NOTICE The United States Government does not endorse products or manufacturers. Trade or manufacturers‘ names appear herein solely because they are considered essential to the objective of this report. REPORT DOCUMENTATION PAGE Form Approved OMB No. 0704-0188 Public reporting burden for this collection of information is estimated to average 1 hour per response, including the time for reviewing instructions, searching existing data sources, gathering and maintaining the data needed, and completing and reviewing the collection of information. Send comments regarding this burden estimate or any other aspect of this collection of information, including suggestions for reducing this burden, to Washington Headquarters Services, Directorate for Information Operations and Reports, 1215 Jefferson Davis Highway, Suite 1204, Arlington, VA 22202-4302, and to the Office of Management and Budget, Paperwork Reduction Project (0704-0188), Washington, DC 20503. 1. -
Actuated Linear Guidance System
TM MotionMotion Without Without Limits Limits ® Actuated Linear Guidance System Built on Motion Technology® Motion Technology® Bishop-Wisecarver, manufacturer of the ORIGINAL DualVee® guide wheel, is recognized as the market leader Hardened for guide wheel technology. In 1967, Bud Wisecarver Track Surface patented DualVee Motion Technology® (DMT). Three main components define DMT – the DualVee guide wheel, its Patented 90º DualVee mating vee profile track with patented mounting shoulder, Guide Wheel and support bushings. DMT is one of the most popular guided motion technologies due to its self-cleaning action Double Row Angular Contact Bearing • Lubed for Life and self-aligning track, which result in an overall lower • Designed for Radial and Axial Loads installation cost. Patented Mounting Shoulder • Quick and Accurate Installation • Unlimited Travel Lengths Features and Benefits • Easily Joined Track DualVee Motion Technology is ideal for a wide array of applications, from the clean room to the sawmill. DualVee’s recirculating elements are self-contained and isolated from the environment. Without direct contact with the rail that can subject bearings to contamination, and ultimately, premature failure, DMT excels in dirty and severe environments. DMT’s circular bearing design also allows for faster acceleration and speeds. ß Carbon or stainless steel components ß Speeds up to 5.5 m/s ß Acceleration up to 5 g’s ß High accuracy and repeatability Designed for Dirty and Severe Environments ß High temperature and clean room options The patented 90º DualVee design creates a velocity gradient, since the circumference of the wheel is greater at the major ß Corrosion resistant versions available diameter, resulting in a constant sweeping action that cleans ß Ground mounting surfaces not required debris from the track. -
Der Bayerische Summer 2019 | Volume 60 | Issue XI
der Bayerische Summer 2019 | Volume 60 | Issue XI Genesee Valley Chapter BMW Car Club of America Bill Howard pilots his vintage ‘72 BMW 2002 through Turn 9 at Watkins Glen. 24 Western New York’s premier BMW service specialists. 2 der bayerische brief der bayerische brief is a publication of the Genesee Valley Chapter, Inc., (GVC or The Club) a non-profit New York corporation and chapter of the BMW Car Club of America, Inc., and is not affiliated in any manner with Bayerische Motoren Werke AG or BMW NA. The Club assumes no responsibility for any of the information contained within. Ideas and technical information are solely those of the authors and no authentication is implied. Contributions from all members are welcomed and encouraged! Information contained within the newsletter is for The Club’s use and permission is granted to reproduce material only if GVC’s der BAYERISCHE brief is given credit. Credits: Images and text with BMW have been taken from the BMW Press Club web site. SPONSORS. Please support the advertisers who support us The Little Speed Shop ............................ 2 Upstate Imports...................................... 7 Gault Auto Sport BMW ......................... 13 Mr. Best Wrench ................................... 13 Berg Racing ......................................... 17 CONTENTS. Christa Barbagallo ................................ 17 SUMMER 2019 VOLUME 60 • ISSUE XI Grand Finale ......................................... 20 Imparts ................................................. 20 4 • PRESIDENT’S MESSAGE T-Shirt Express ..................................... 23 Arete Auto Salon .................................. 27 8 • WHAT DO YOU WANT OUT OF YOUR MEMBERSHIP Aratari ................................................... 34 Austin Spencer ..................................... 35 10 • THE LITTLE CAR THAT MOSTLY COULD Silvertouch Autosports ......................... 35 Redi Imports ......................................... 36 14 • THE ROAD TO THE 2018 ONE LAP OF AMERICA Finger Lakes Vintage & Sports Car ...... -
2014 Bearcats Baja Rear Suspension System
2014 Bearcats Baja Rear Suspension System A Baccalaureate thesis submitted to the Department of Mechanical and Materials Engineering College of Engineering and Applied Science University of Cincinnati In partial fulfillment of the Requirements for the degree of Bachelor of Science In Mechanical Engineering Technology By: Zack Freije April 2014 Thesis Advisor: Dean Allen Arthur 2014 Bearcats Baja – Rear Suspension System Zack Freije Rear Suspension Copyright © 2007 SAE International ABSTRACT Each vehicle is evaluated in terms of ergonomics, functionality, and producibility. To this end, design Baja SAE is an annual intercollegiate engineering design reports must demonstrate both sound engineering competition organized by the Society of Automotive principles as well as economic feasibility for Engineers, and serves as a capstone project for senior production. Mechanical Engineering Technology students at the University of Cincinnati. The 2014 Bearcats Baja team An off-road vehicle’s suspension system serves three vehicle is a complete new build from the ground up. This primary functions: to maintain tire contact with the design freedom allows for drastic improvements over the ground while the vehicle navigates rough terrain, to 2013 rear suspension system performance. Extensive reduce impact forces transferred to the driver, and to research was conducted to determine the key provide optimal vehicle handling dynamics. (1) performance metrics for the system. Several design options were considered and a final design was selected RESEARCH based on system integration, manufacturability, system weight, cost, and design specifications required to meet Full compliance with all relevant Baja SAE rules is the performance metrics. Failure modes were required. The applicable rules have been supplied in established based on 2013 in-use performance results. -
Caring for Custom Wheels
Caring for Custom Wheels Custom wheels represent an investment in your vehicle. Preserving the appearance of the wheel requires ongoing and regular maintenance. Each type of custom wheel finish has its own unique maintenance requirements. The first thing is to determine if the wheels are made of chrome and not polished aluminum. Chrome does not tarnish and only pits if it is beginning to rust. Chrome Plated Alloy Chrome plated alloy wheels need to be washed with mild soap and water. To maintain the finish, use car wax or an instant detailer product. Polished Alloy Polished alloy wheels should be washed with a heavy metal tire and wheel cleaner on a regular basis and polished with a heavy metal polisher several times a year. Painted Alloy Painted alloy wheels can be washed with mild soap and water. If brake dust is built up on the wheel and is extreme, use a heavy metal tire and wheel cleaner. Machined & Clear Coated Machined and clear coated alloy wheels can be washed with mild soap and water. If brake dust build up is extreme, use a heavy metal tire and wheel cleaner. Chrome and Painted Steel Chrome or painted steel wheels require regular washing with mild soap and water followed up with an occasional coat of car wax or a heavy metal instant detailer. Care For Custom Wheels During Winter Custom wheels can provide years of pleasure and service with the proper care. The best possible option for custom wheels in severe winter climates is the use of snow wheels with winter tires. -
Wheel Accessories
ACCESSORIES WHEEL ACCESSORIES 1 ACCESSORIES WHEEL ACCESSORIES TABLE OF CONTENTS DESCRIPTION PAGE Wheel Installation Kits 3 NEW! Spike Lug Nut Kits 6 Lug Nuts 7 Washers 11 Lug Bolts 12 Hub Centric Rings 14 Hub Centric Ring Vehicle Application Guide 15 Lifetime Wheel Locks and Lug Nuts 35 Wheel Locks 36 Lug Bolt Locks 37 Hub Cover Locks 38 Wheel Studs 39 Valve Stems 39 Chrome Hub Covers (Including Dually) 40 Black Hub Covers 41 Stainless Steel Hub Covers 42 Rallye & Smoothie Hub Covers 43 GM Licensed Hub Covers 44 NEW! Dropstars/TIS Spike Lug Caps and Spike-Only Kits 44 Lug Wrenches and Tools 45 Socket Adapters 45 Wheel Spacers 46 Billet Wheel Adapters 47 Spinners and Spinner Sets 48 Trim Rings 48 Stainless Steel Dually Simulators and Parts 49 Stainless Steel Disc Brake Simulators 49 Polishes and Cleaners 50 Display Items / Merchandising Aids 51 Bulk Accessory Program 52 Magnum Plus Balancing Compound 54 2 ACCESSORIES WHEEL INSTALLATION KITS Everything you need to install a set of custom wheels in one box! FEATURES & BENEFITS • All acorn lugs are bulge style to ensure a good seat. • All components are in individually sealed bags and each box is clearly marked for easy use. • The box provides excellent storage for retail customer’s O.E. Lug Nuts and Wheel Lock Key. BULGE SEAT ACORN KITS (Lug Length 1.40”) Each Kit Includes: 20 Lugs, 4 Locks, 4 Stems, 2 Socket Adapters NOTE: ALL LUGS ARE 3/4” HEX CAUTION: MAY NOT BE SUITABLE FOR NEWER LT’S/SUV’S WITH LONGER STUDS Internal Manufacturer Number Prod.