Modular and Flexible Payload Arrangements for Surface Ships with Reconfigurable Floors and Sliding Bulkheads
Total Page:16
File Type:pdf, Size:1020Kb
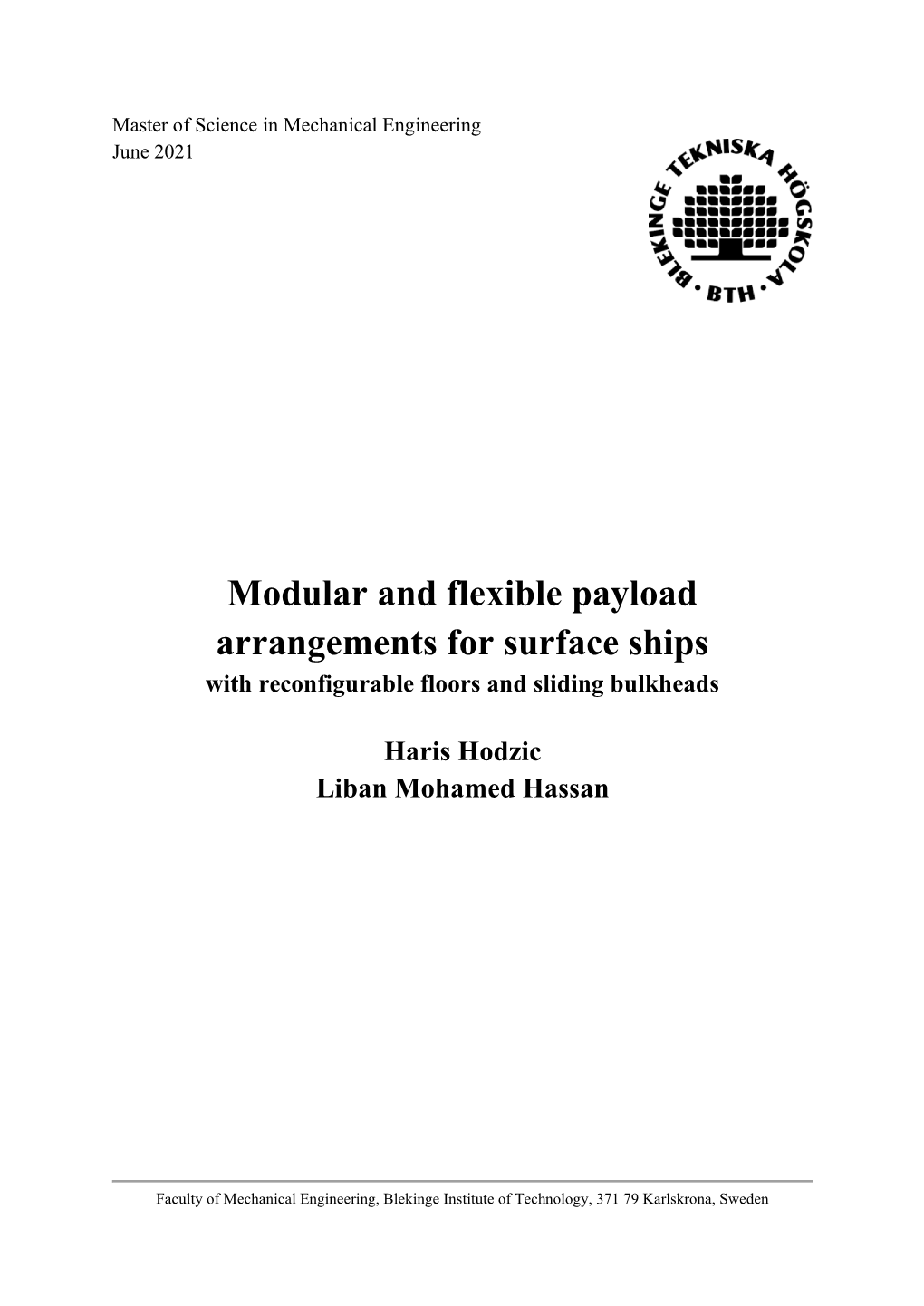
Load more
Recommended publications
-
Press Information Saab AB
PRESS RELEASE Page 1 (2) Date Reference 15 June 2018 CU 18:050 E Keel-Laying Ceremony for Swedish SIGINT Ship Built at Nauta Shiprepair Yard The keel-laying ceremony for the new Swedish signals intelligence ship took place today at the PGZ Stocznia Wojenna, located in Gdynia, Poland. The event was attended by representatives from Saab, the Polish Armaments Group (PGZ) and invited guests. Saab was awarded the contract to design and build the SIGINT ship, which will replace the Swedish Navy’s existing HMS Orion, by the Swedish Material Defence Administration FMV in 2017. Subsequently it selected Nauta Shiprepair Yard, belonging to PGZ Group, to perform the construction, launch and early sea trials of the vessel. Cooperation in ship construction between Saab and PGZ is a direct result of the agreement, signed in late 2016, to establish a close partnership between Saab and PGZ in the planning and delivery of naval programs. “Special purpose ships are primarily used for the interception and analysis of radio-transmitted signals and need to be highly reliable and available. Therefore you need highly skilled shipbuilders to build this kind of ship. We are very pleased with the progress of the construction process, and it was a pleasure to attend the keel laying ceremony at the PGZ Stocznia Wojenna, our partner in this project,” explained Gunnar Wieslander, Head of Saab Kockums. “The keel-laying ceremony was an important event in this special shipbuilding project, and we are pleased to celebrate it with our Swedish partners. We know the special purpose vessel is very important for the Swedish Navy and we are treating the construction as a high priority undertaking,” said Marcin Dąbrowski, Chairman of the Management Board, Nauta Shiprepair Yard. -
MARITIME Security &Defence M
June MARITIME 2021 a7.50 Security D 14974 E &Defence MSD From the Sea and Beyond ISSN 1617-7983 • Key Developments in... • Amphibious Warfare www.maritime-security-defence.com • • Asia‘s Power Balance MITTLER • European Submarines June 2021 • Port Security REPORT NAVAL GROUP DESIGNS, BUILDS AND MAINTAINS SUBMARINES AND SURFACE SHIPS ALL AROUND THE WORLD. Leveraging this unique expertise and our proven track-record in international cooperation, we are ready to build and foster partnerships with navies, industry and knowledge partners. Sovereignty, Innovation, Operational excellence : our common future will be made of challenges, passion & engagement. POWER AT SEA WWW.NAVAL-GROUP.COM - Design : Seenk Naval Group - Crédit photo : ©Naval Group, ©Marine Nationale, © Ewan Lebourdais NAVAL_GROUP_AP_2020_dual-GB_210x297.indd 1 28/05/2021 11:49 Editorial Hard Choices in the New Cold War Era The last decade has seen many of the foundations on which post-Cold War navies were constructed start to become eroded. The victory of the United States and its Western Allies in the unfought war with the Soviet Union heralded a new era in which navies could forsake many of the demands of Photo: author preparing for high intensity warfare. Helping to ensure the security of the maritime shipping networks that continue to dominate global trade and the vast resources of emerging EEZs from asymmetric challenges arguably became many navies’ primary raison d’être. Fleets became focused on collabora- tive global stabilisation far from home and structured their assets accordingly. Perhaps the most extreme example of this trend has been the German Navy’s F125 BADEN-WÜRTTEMBERG class frig- ates – hugely sophisticated and expensive ships designed to prevail only in lower threat environments. -
A Conceptual Design of a Reliable Hard Docking System Docking of an Autonomous Underwater Vehicle to the New Generation A26 Submarine
DEGREE PROJECT IN INDUSTRIAL ENGINEERING AND MANAGEMENT, SECOND CYCLE, 30 CREDITS STOCKHOLM, SWEDEN 2021 A Conceptual Design of a Reliable Hard Docking System Docking of an autonomous underwater vehicle to the new generation A26 submarine ELIN EKSTRÖM ELLEN SEVERINSSON KTH ROYAL INSTITUTE OF TECHNOLOGY SCHOOL OF INDUSTRIAL ENGINEERING AND MANAGEMENT This page was left intentionally blank A Conceptual Design of a Reliable Hard Docking System Docking of an utonomous underwater vehicle to the new generation A26 submarine ELIN EKSTRÖM ELLEN SEVERINSSON Master of Science Thesis TRITAITMEX 2021:379 KTH Industrial Engineering and Management Machine Design SE100 44 STOCKHOLM This page was left intentionally blank Master of Science Thesis TRITA-ITM-EX 2019:379 A Conceptual Design of a Reliable Hard Docking System Elin Ekström Ellen Severinsson Godkänt Examinator Handledare 2021-06-15 Claes Tisell Roger Berg Uppdragsgivare Kontaktperson Swedish Defence Materiel Administration Matteo Perrone, Johan Wahren Abstract In year 2024 and 2025 the Royal Swedish Navy is expected to launch two new submarines with new possibilities to dock underwater vehicles. The submarines are part of the new Blekinge Class (A26) and will aid the Swedish Armed Forces and the Swedish Defense Materiel Administration (FMV) in their aim to develop and use more autonomous systems, to increase staff efficiency and to face the technological challenges of tomorrow. This thesis was carried out at FMV, with the purpose of investigating the physical requirements put on the new submarines, when docking an autonomous underwater vehicle. These requirements were identified through an analysis of qualitative and quantitative research. The analysis resulted in ten key insights, which led to thirteen requirements. -
Standardising Flexibility: Future-Proofing Designs and Capabilities in Complex Warships
Standardising flexibility: Future-proofing designs and capabilities in complex warships Date Posted: 18-Feb-2021 Author: Dr. Lee Willett, London Publication: Jane's International Defence Review As technological change accelerates and navies seek platforms built for longer service life, shipyards are blending – in their platform designs – capacity for extended operational service and adaptability to developments in technology. Dr Lee Willett explores Damen Naval Division as a case study in applying such thinking to surface ships in build, in design, and in concept With some exceptions, most navies buy surface ships and submarines that are designed to remain operational for a relatively long time. A period of 25 years has commonly been the expected service-life baseline, though in practice many platforms operate for longer. In design and requirement today, navies need platforms that are able to operate for 30, 40, or even 50 years. The operational requirements a platform must meet over an extended service life can change significantly, as can the technology available – either enabling new offensive capability and/or requiring a defensive response. Over the next half-century, the speed of technological change is likely to accelerate rapidly (although due to the range of technologies emerging, the speed and direction of the acceleration are unlikely to be linear). Double Dutch The Netherlands’ Damen Naval Division, part of Damen Shipbuilding Group, is one shipbuilder tackling the twin challenges of designing and building platforms with flexibility to adapt to technological change while also delivering a degree of standardisation to enable future upgrade integration. The various ship types in build at Damen’s naval shipyards underlines the broad range of platforms and capabilities navies need today. -
MARITIME NEWS – 30 SEPTEMBER 2016 Royal Navy Warship Visits Durban
MARITIME NEWS – 30 SEPTEMBER 2016 Royal Navy warship visits Durban The Type 23 frigate HMS Portland arrived in Durban on Wednesday 28 Sep and berthed at the Naval Station on Salisbury Island. She hosted a special reception on 29 Sep for local dignitaries and invited guests. A Capability Demonstration has also been planned, to showcase the skills and efficiency of the Royal Navy servicemen. Organisers of the gala event say it's significant, as it's the first time in a long while that a major Royal Navy ship of its kind has sailed to the east coast. The ship is currently three-months into a nine-month deployment around the world - having set sail from Plymouth in the UK, in June. Source : East Coast Radio She will be transiting West to the South Atlantic again so Cape readers can also expect a visit by her. It is two and a half years since she was last here under Cdr Sarah West at the time. It has also been more than a year since we last had a frigate/destroyer as the South Atlantic patrol ship! Unmanned air and sea vehicles coordinate together Lockheed Martin has successfully launched a small unmanned aerial vehicle on command from its MK2 Marlin autonomous underwater vehicle. The launch was part of a cross-domain command-and- control event hosted by the U.S. Navy last month and also involved a Submaran, an unmanned surface vehicle developed by Ocean Aero, which provided surface reconnaissance and surveillance. "This effort marks a milestone in showing that an unmanned aircraft, surface vessel and undersea vehicle can communicate and complete a mission cooperatively and completely autonomously," said Kevin Schlosser, chief architect, unmanned systems technology, Lockheed Martin. -
Replacing the Collins Class
AUSTRALIAN DEFENCE IN A GLOBAL CONTEXT APR-MAY 2021 VOL.47 NO.3 REPLACING THE COLLINS CLASS AUSTRALIAN ARAFURA CLASS SEA 5000 SOVEREIGN GUIDED OFFSHORE PATROL VESSELS AND AUSTRALIAN WEAPONS CAPABILITY PROGRESS REPORT SPECIFIC CHANGES Overmatch Assured Powered by RAFAEL, Delivered by VRA TROPHY™ IRON DOME™ SPIKE LR2™ TYPHOON™ Powered by RAFAEL. Delivered by VRA www.rafael.co.il | www.vrasystems.com.au CONTENTS Print Post Approved PP349181/00104 Managing Director/Publisher FEATURES Overmatch Assured Marilyn Tangye Butler Phone: +61 (0) 410 529 324 AUSTRALIAN DEFENCE IN A GLOBAL CONTEXT 12 RAYTHEON AUSTRALIA OPENS CENTRE FOR Email: [email protected] APR-MAY 2021 VOL.47 NO.3 JOINT INTEGRATION A major boost to sovereign capability Editor Kym Bergmann Phone: +61(0)412 539 106 Powered by RAFAEL, Delivered by VRA Email: [email protected] 16 AUSTRALIAN CONTENT ON ATTACK CLASS Contributors TO REACH 60% - EVENTUALLY Vladimir Karnozov By then will anyone care? Arie Egozi Mark Farrer Mike Yeo Geoff Slocombe 18 AUTONOMOUS UNDERWATER VEHICLES George Galdorisi – THE FUTURE OF WARFARE? Australia REPLACING THE COLLINS CLASS Will crewed submarines become obsolete? Ventura Media Asia-Pacific Pty Ltd PO Box 88, Miranda AUSTRALIAN ARAFURA CLASS SEA 5000 SOVEREIGN GUIDED OFFSHORE PATROL VESSELS AND AUSTRALIAN NSW 1490 Australia WEAPONS CAPABILITY PROGRESS REPORT SPECIFIC CHANGES ABN 76 095 476 065 20 FUTURE FRIGATE DESIGN REMAINS WITHIN HMAS Rankin and her crew conducted workups and training AGREED GUIDELINES Subscriptions assessments in the Western Australian Exercise Area to ensure Growth within the safety margins Rose Jeffree the Collins Class Submarine is ready to safely deploy later in the Phone: + 61 (0)2 9526 7188 year. -
Annual and Sustainability Report 2019
Keeping people and society safe Annual and sustainability report 2019 Partnerships for greater security Vision: It is a human right to feel safe. Mission: To make people safe by pushing intellectual and technological boundaries. It is a basic human need and a human right to feel safe. Safety is subjected to many different types of threats. This includes military threats, terrorism, accidents or natural disasters. Saab develops innovative, high-tech and cost-efficient systems to increase security for societies and individuals. At the same time, there is a realisation throughout the business that some of the systems and solutions that contribute to greater security can also be used in conflicts. This entails a major responsibility. By acting responsibly in everything we do, we earn the confidence of customers, employees and society and contribute to a safer world. Value creation Strategy Saab as an investment Saab is an international company that Saab’s strategic direction means work- Saab is on a growth journey. Recent years have seen contributes to increased security and ing closely with customers, continu- strong international growth through strategic collab- defence capabilities in Sweden and ously developing our portfolio, focus- orations and research and development. This has other countries. By working toward our ing on operating efficiency and laid the foundation for a unique position as Saab strategic priorities, we create long- embracing innovation as a business- enters an execution phase and focus is on cash flow. term value. -
MARITIME Security &Defence M
Pilot Issue MARITIME October 2020 Security a7.50 D 14974 E &Defence MSD From the Sea and Beyond ISSN 1617-7983 • European Naval Shipbuilding www.maritime-security-defence.com • • Counter-Mine Capabilities in Europe • Naval Propulsion Options MITTLER • Naval Interceptors October 2020 • European Submarine Builders REPORT MISSIONREADY From o shore patrol vessels to corvettes – Lürssen has more than 140 years of experience in building naval vessels of all types and sizes. We develop tailor-made maritime solutions to meet any of your requirements. Whenever the need arises, our logistic support services and spare parts supply are always there to help you. Anywhere in the world. Across all of the seven seas. Lürssen – The DNA of shipbuilding More information: + or www.luerssen-defence.com Editorial From the Sea and Beyond You are holding a new magazine concept in your hands, and might already be asking: “Security and Defence – again? Maritime? What for?” Photo: author Conrad Waters is a contributor to Mittler Report Verlag publi- Water covers more than 70 per cent of the world’s sur- cations, serves as editor of face – including rivers and lakes of strategic importance. “Navies in the 21st Century” It is the means for defining national boundaries, outlining and is the editor of the “World regions, conducting trade, feeding populations, energising Naval Review” since 2009 when the digital planet and relaxing safely on a beach holiday. it was founded. Yet, there are many aspects about the sea that are ignored or misunderstood by the current – and shrinking pool – of defence titles focused on it. Maritime Security and Defence is dedicated to remedy the broader understanding of “the sea” in a unique way. -
Senate Economics References Committee
Senate Economics References Committee Inquiry into Australia’s Sovereign Naval Shipbuilding Industry Submission by Submarines for Australia July 2020 Contents Executive Summary and Conclusions 3 1. Purpose of the Submission 6 2. Submarine Capability 9 3. Future Frigates 20 4. Naval Shipbuilding Plan 27 Appendix A: Covering Letter from Gary Johnston 34 Appendix B: Submarines for Australia Reference Group 36 2 Executive Summary and Conclusions This Submission to the Senate Economic References Committee’s inquiry into Australia’s Sovereign Naval Shipbuilding Industry Capability is put forward by Submarines for Australia, a group founded and sponsored by Gary Johnston. In its recent Defence Strategic Update, the government has recognised that Australia’s strategic circumstances have deteriorated significantly since 2016, when the last Defence White Paper was published. This requires both an increase in the Defence budget and a significant adjustment to the ADF’s force structure. The three major acquisition projects, however, SEA 1000, SEA 5000 and AIR 6000, totalling around $155 billion in out-turned dollars, were excluded from consideration in the new Force Structure Plan. Having now seen the outcome from the FSP, we consider that a review of at least the two major naval programs is warranted to ensure they still meet the ADF’s requirements in the context of the new strategic reality: • The concept of ‘warning time’ has been discarded and instead “that future is now” – this is a problem for the two major naval programs, both of which are still at the design stage and have lengthy delivery schedules: o for SEA 1000, where the prospect of a capability gap looms large, the first new submarine won’t be operational until 2035 and the 12 submarine force announced in 2009 will not be achieved for another 35 years o the schedule for SEA 5000 takes delivery of the nine frigates well into the 2040s, requiring further upgrades to the Anzac frigates. -
Progress with the Future Submarine
Progress with the Future Submarine Submission to the ANAO by Submarines for Australia 23 June 2019 CONTENTS FOREWORD 3 SUMMARY AND CONCLUSIONS 4 1. Introduction 7 2. Deep engagement with a ‘design partner’ 9 3. Emerging risks of eliminating competition 13 4. Technical risks to FSM capability 19 5. Introducing competition 22 Attachment: Proposal to the PM by ‘Four Admirals’ 26 Submarines for Australia: Submission to the ANAO on the Future Submarine Foreword This Submission to the ANAO is made by Submarines for Australia, an entity with a website owned and operated by Gary Johnston, founder and CEO of Jaycar Electronics Pty Ltd. Over the last three years, Mr Johnston has generously supported significant research by Insight Economics Pty Ltd and others into Australia’s future submarine project, SEA 1000. As both a substantial Australian taxpayer and a supporter of the ADF, he is motivated by two overriding considerations: • The need to acquire a powerful but cost effective submarine capability for the RAN in an acceptable timeframe • While accepting that all ADF personnel undertake a certain level of personal risk in the course of their duties, to seek to ensure that Submarine Force personnel go into harm’s way on platforms that both incorporate the most advanced level of technology that Australia can afford and offer them the highest possible level of survivability in what is often a dangerous operational environment. Mr Johnston considers that the way in which SEA 1000 is being delivered addresses neither of these criteria in a satisfactory manner. Mr Johnston is pleased to acknowledge Insight Economics’ significant contribution to this submission. -
Saab Kockums' Maiden Voyage (Part.2)
Saab Tockums4 maiden 0oyage (.art.2) ducon site in Tarlskrona (next to Swe- defence technology developments. den’s main navy base), and also a for- Lef0 n is presently (September 80) mer navy dockyard at Muske for forming a government with the Green maintenance and repair. .arty (with 86._ % of the votes togeth- Saab’s broad naval presence er L leaving the Lek .arty out). 3n By April, 2014, Thyssen Krupp Marine .rior to acquiring Tockums, Saab also September 2_, the party leaders of this Systems (TKMS, the then German own- had several other facilies in the Saab two-party coalion declared that the er of Kockums) and Saab had signed a Group involved in naval defence sys- Green .arty accepts the Gripen and Memorandum of Understanding tems: torpedo development in Linke- submarine development, but that the stang that Saab would acquire ping, missiles in Linkeping, C8I systems Swedish defence export regulaons Tockums. Saab had courted TMS in Jfrfflla and radar in Gothenburg. would become more restric0e to- since the autumn of 2018 regarding an Saab’s CE3 Hgkan Buskhe stated that wards anon-democracb naons (as acquision of Tockums. During the athe acquision is in line with our the Green .arty had been suggesng for many years). spring of 2014, TMS4 grip over strategy to expand our o+ering and Tockums gradually weakened as the strengthen Saab’s posion in the mar- 3n September 2_, -MV announced Swedish state and -MV (the defence ket for naval systems. h he acquisi- two orders to Saab Tockums. -irstly, procurement agency) distanced them- on makes us a complete supplier of an order of ten underwater R3Vs selves from TMS, and supported a naval military systemsb. -
Insight Economics Pty Ltd
Submarines for Australia March 2020 Australia’s Future Submarine Do we need a Plan B? ! A USTRALIA’ S F UTURE S UBMARINE: D O W E N EED A P LAN B? Insight Economics Pty Ltd ACN:141 097 565 ABN: 29 627 712 906 Cover: Four Collins class submarines off HMAS Stirling with the Los Angeles class attack submarine, USS Santa Fe. Photo: Licence: Alamy Disclaimer: While Insight Economics endeavours to provide reliable analysis and believes the material it presents is accurate, it will not be liable for any claim by any party acting on such information. © Insight Economics 2020 ! i! A USTRALIA’ S F UTURE S UBMARINE: D O W E N EED A P LAN B? CONTENTS Glossary of acronyms iii! Acknowledgements 4! Foreword 5! Executive Summary 7! Chapter 1 11! Emerging problems with SEA 1000 11! 1.1! Elimination of competition 12! 1.2! Ambitious capability requirement 12! 1.3! Structure of the report 15! Chapter 2 16! Problems arising from lack of competition 16! 2.1! Excessive cost of design and construction 16! 2.2! Collins class life of type extension 21! 2.3! Sovereign capability – local content and access to IP 24! 2.4! Technical risks 29! Chapter 3 33! Will the Attack class be fit for purpose? 33! 3.1! What do Australian submarines do? 33! 3.2! Submarine operations ‘up threat’ in the Indo Pacific 34! 3.3! Strategic capability requirement for the Attack class 39! 3.4! Operational and tactical capability requirements 41! 3.5! Would the Attack class be suitable for a different role? 48! 3.6! Will the Attack class be cost-effective? 49! 3.7! Conclusion 49! Chapter