Research on the Influence of Backlash on Mesh Stiffness and The
Total Page:16
File Type:pdf, Size:1020Kb
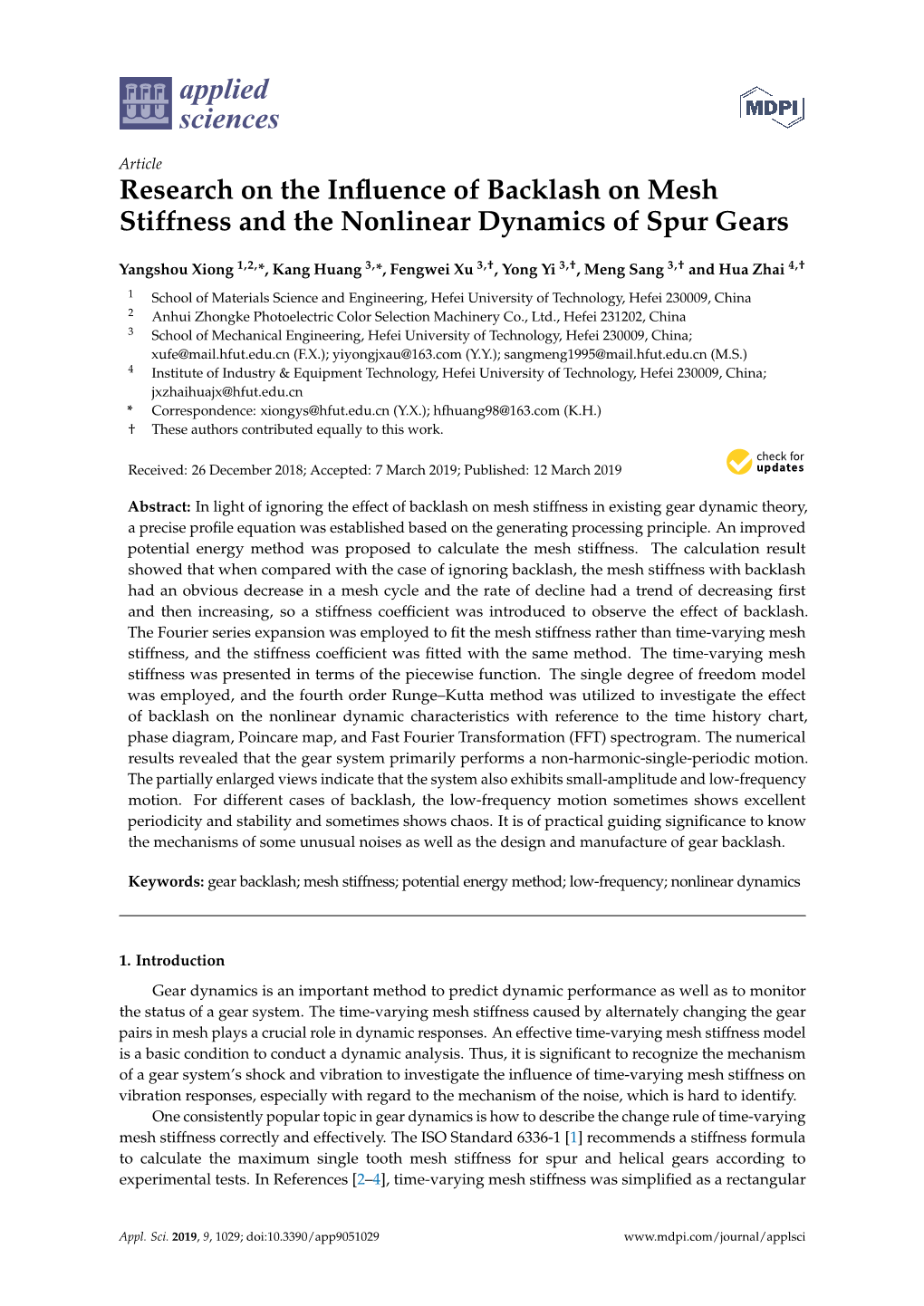
Load more
Recommended publications
-
The Rise of Controversial Content in Film
The Climb of Controversial Film Content by Ashley Haygood Submitted to the Department of Communication Studies in partial fulfillment of the requirements for the degree of Masters of Arts in Communication at Liberty University May 2007 Film Content ii Abstract This study looks at the change in controversial content in films during the 20th century. Original films made prior to 1968 and their remakes produced after were compared in the content areas of profanity, nudity, sexual content, alcohol and drug use, and violence. The advent of television, post-war effects and a proposed “Hollywood elite” are discussed as possible causes for the increase in controversial content. Commentary from industry professionals on the change in content is presented, along with an overview of American culture and the history of the film industry. Key words: film content, controversial content, film history, Hollywood, film industry, film remakes i. Film Content iii Acknowledgements I would like to thank my family for their unwavering support during the last three years. Without their help and encouragement, I would not have made it through this program. I would also like to thank the professors of the Communications Department from whom I have learned skills and information that I will take with me into a life-long career in communications. Lastly, I would like to thank my wonderful Thesis committee, especially Dr. Kelly who has shown me great patience during this process. I have only grown as a scholar from this experience. ii. Film Content iv Table of Contents ii. Abstract iii. Acknowledgements I. Introduction ……………………………………………………………………1 II. Review of the Literature……………………………………………………….8 a. -
The Popular Culture Studies Journal
THE POPULAR CULTURE STUDIES JOURNAL VOLUME 6 NUMBER 1 2018 Editor NORMA JONES Liquid Flicks Media, Inc./IXMachine Managing Editor JULIA LARGENT McPherson College Assistant Editor GARRET L. CASTLEBERRY Mid-America Christian University Copy Editor Kevin Calcamp Queens University of Charlotte Reviews Editor MALYNNDA JOHNSON Indiana State University Assistant Reviews Editor JESSICA BENHAM University of Pittsburgh Please visit the PCSJ at: http://mpcaaca.org/the-popular-culture- studies-journal/ The Popular Culture Studies Journal is the official journal of the Midwest Popular and American Culture Association. Copyright © 2018 Midwest Popular and American Culture Association. All rights reserved. MPCA/ACA, 421 W. Huron St Unit 1304, Chicago, IL 60654 Cover credit: Cover Artwork: “Wrestling” by Brent Jones © 2018 Courtesy of https://openclipart.org EDITORIAL ADVISORY BOARD ANTHONY ADAH FALON DEIMLER Minnesota State University, Moorhead University of Wisconsin-Madison JESSICA AUSTIN HANNAH DODD Anglia Ruskin University The Ohio State University AARON BARLOW ASHLEY M. DONNELLY New York City College of Technology (CUNY) Ball State University Faculty Editor, Academe, the magazine of the AAUP JOSEF BENSON LEIGH H. EDWARDS University of Wisconsin Parkside Florida State University PAUL BOOTH VICTOR EVANS DePaul University Seattle University GARY BURNS JUSTIN GARCIA Northern Illinois University Millersville University KELLI S. BURNS ALEXANDRA GARNER University of South Florida Bowling Green State University ANNE M. CANAVAN MATTHEW HALE Salt Lake Community College Indiana University, Bloomington ERIN MAE CLARK NICOLE HAMMOND Saint Mary’s University of Minnesota University of California, Santa Cruz BRIAN COGAN ART HERBIG Molloy College Indiana University - Purdue University, Fort Wayne JARED JOHNSON ANDREW F. HERRMANN Thiel College East Tennessee State University JESSE KAVADLO MATTHEW NICOSIA Maryville University of St. -
Laws, Beliefs, and Backlash.Pdf
Laws, Beliefs, and Backlash1 Brian Wheaton2 Harvard University November 12, 2020 Most Recent Version Available at: https://scholar.harvard.edu/files/wheaton/files/backlash.pdf Abstract: Do laws affect the beliefs and attitudes held by the public? I set up a model wherein families care about their children's beliefs, which are shaped by a combination of parental actions and the law set by society. These straightforward assumptions are sufficient to generate systematic backlash against laws – individuals move in the opposite direction of the law in an attempt to preserve the values which are important to them and are placed under threat by the law. Next, I turn to survey data from the ANES to test the implications of the model. I first focus in- depth on one specific case: the state Equal Rights Amendments (ERAs), which aimed to legislate gender equality. Using a dynamic difference-in-differences identification strategy, I find robust evidence that ERA passage leads to a sharp backlash amongst men in particular, who exhibit sharply more negative attitudes toward male/female equality. This shift translates into a significant increase in Republican vote share, worsened material outcomes for women, and increased marital strife. I also test and confirm the other implications of the model – such as the fact that the backlash is passed on to the next generation and that it endures more strongly in ideologically-homogeneous communities. Next, I provide evidence against a variety of alternative mechanisms. And finally, stepping back from the ERAs, I show that virtually every major U.S. social policy law of the past half-century has induced significant backlash. -
“Smackdown”: a Textual Analysis of Class, Race and Gender in WWE Televised Professional Wrestling
The University of Southern Mississippi The Aquila Digital Community Dissertations Spring 5-2012 Ideological “Smackdown”: A Textual Analysis of Class, Race and Gender in WWE Televised Professional Wrestling Casey Brandon Hart University of Southern Mississippi Follow this and additional works at: https://aquila.usm.edu/dissertations Part of the Broadcast and Video Studies Commons, Critical and Cultural Studies Commons, Gender, Race, Sexuality, and Ethnicity in Communication Commons, and the Mass Communication Commons Recommended Citation Hart, Casey Brandon, "Ideological “Smackdown”: A Textual Analysis of Class, Race and Gender in WWE Televised Professional Wrestling" (2012). Dissertations. 550. https://aquila.usm.edu/dissertations/550 This Dissertation is brought to you for free and open access by The Aquila Digital Community. It has been accepted for inclusion in Dissertations by an authorized administrator of The Aquila Digital Community. For more information, please contact [email protected]. The University of Southern Mississippi IDEOLOGICAL “SMACKDOWN”: A TEXTUAL ANALYSIS OF CLASS, RACE AND GENDER IN WWE TELEVISED PROFESSIONAL WRESTLING by Casey Brandon Hart Abstract of a Dissertation Submitted to the Graduate School of The University of Southern Mississippi in Partial Fulfillment of the Requirements for the Degree of Doctor of Philosophy May 2012 ABSTRACT IDEOLOGICAL “SMACKDOWN”: A TEXTUAL ANALYSIS OF CLASS, RACE AND GENDER IN WWE TELEVISED PROFESSIONAL WRESTLING by Casey Brandon Hart May 2012 The focus of this study is an in-depth intertextual examination of how the WWE in 2010 and by extension contemporary professional wrestling in general represents a microcosm of modern cultural ideology. The study examines three major areas in which this occurs. -
The Effect of School Closure On
Public Gaming: eSport and Event Marketing in the Experience Economy by Michael Borowy B.A., University of British Columbia, 2008 Thesis Submitted in Partial Fulfillment of the Requirements for the Degree of Master of Arts in the School of Communication Faculty of Communication, Art, and Technology Michael Borowy 2012 SIMON FRASER UNIVERSITY Summer 2012 All rights reserved. However, in accordance with the Copyright Act of Canada, this work may be reproduced, without authorization, under the conditions for “Fair Dealing.” Therefore, limited reproduction of this work for the purposes of private study, research, criticism, review and news reporting is likely to be in accordance with the law, particularly if cited appropriately. Approval Name: Michael Borowy Degree: Master of Arts (Communication) Title of Thesis: Public Gaming: eSport and Event Marketing in the Experience Economy Examining Committee: Chair: David Murphy, Senior Lecturer Dr. Stephen Kline Senior Supervisor Professor Dr. Dal Yong Jin Supervisor Associate Professor Dr. Richard Smith Internal Examiner Professor Date Defended/Approved: July 06, 2012 ii Partial Copyright Licence iii STATEMENT OF ETHICS APPROVAL The author, whose name appears on the title page of this work, has obtained, for the research described in this work, either: (a) Human research ethics approval from the Simon Fraser University Office of Research Ethics, or (b) Advance approval of the animal care protocol from the University Animal Care Committee of Simon Fraser University; or has conducted the research (c) as a co-investigator, collaborator or research assistant in a research project approved in advance, or (d) as a member of a course approved in advance for minimal risk human research, by the Office of Research Ethics. -
Theorising Backlash Politics: 2020, Vol
BPI0010.1177/1369148120947956The British Journal of Politics and International RelationsAlter and Zürn 947956research-article2020 Special Issue Article The British Journal of Politics and International Relations Theorising backlash politics: 2020, Vol. 22(4) 739 –752 Conclusion to a special issue on © The Author(s) 2020 Article reuse guidelines: backlash politics in comparison sagepub.com/journals-permissions https://doi.org/10.1177/1369148120947956DOI: 10.1177/1369148120947956 journals.sagepub.com/home/bpi Karen J Alter1 and Michael Zürn2,3 Abstract This conclusion to a special issue on backlash politics develops a proto-theory of backlash politics. The special issue’s introduction defined backlash politics as a particular form of political contestation with a retrograde objective as well as extraordinary goals or tactics that has reached the threshold level of entering mainstream public discourse. While a sub-category of contentious politics, we argue that backlash politics is distinct and should not be understood as ‘regressive contentious politics’. Drawing from the contributions to this special issue, we discuss the causes of backlash politics, yet we argue that the greatest theoretical advances may come from studying backlash dynamics and how these dynamics contribute to different outcomes. We develop a proto-theory of backlash politics that considers causes for the rise of backlash movements, how frequent companions to backlash politics – emotive politics, nostalgia, taboo breaking, and institution reshaping – intensify backlash dynamics and make it more likely that backlash politics generate consequential outcomes. Keywords backlash politics, contestation, emotional politics, taboo breaking, nostalgia, public discourse, retrograde The term backlash has been invoked in very different contexts: in discussions of reaction- ary movements, anti-feminism, the pushback against LBGT rights, movements for local autonomy, radical right-wing populism, when discussing policy reversals, rejections of European and international institutions, and more. -
An Evidence-Based Review of Sexual Assault Prevention Intervention
The author(s) shown below used Federal funds provided by the U.S. Department of Justice and prepared the following final report: Document Title: An Evidence-Based Review of Sexual Assault Preventive Intervention Programs Author(s): Shannon Morrison, Jennifer Hardison, Anita Mathew, Joyce O’Neil Document No.: 207262 Date Received: October 2004 Award Number: 2002-WG-BX-0006 This report has not been published by the U.S. Department of Justice. To provide better customer service, NCJRS has made this Federally- funded grant final report available electronically in addition to traditional paper copies. Opinions or points of view expressed are those of the author(s) and do not necessarily reflect the official position or policies of the U.S. Department of Justice. This document is a research report submitted to the U.S. Department of Justice. This report has not been published by the Department. Opinions or points of view expressed are those of the author(s) and do not necessarily reflect the official position or policies of the U.S. Department of Justice. September 2004 An Evidence-Based Review of Sexual Assault Preventive Intervention Programs Technical Report Prepared for National Institute of Justice 810 Seventh Street, N.W. Washington, DC 20531 Prepared by Shannon Morrison, Ph.D. Jennifer Hardison, M.S.W. Anita Mathew, M.P.H. Joyce O’Neil, M.A. RTI International Health, Social, and Economics Research Research Triangle Park, NC 27709 NIJ Grant Number: 2002-WG-BX-0006 This document is a research report submitted to the U.S. Department of Justice. This report has not been published by the Department. -
What's New In
What’s New in Boston & Cambridge Destination Overview November 6, 2019 www.BostonUSA.com www.CambridgeUSA.org Produced by the Greater Boston Convention & Visitors Bureau, proud partners of the Massachusetts Office of Travel & Tourism, MASSPORT Logan International Airport & CruisePort Boston. Massachusetts Convention Center Authority, Discover New England, Brand USA, Massachusetts Lodging Association, Boston Mayor’s Office of Tourism, Sports & Entertainment, Boston Mayor’s Office of Arts & Culture, National Parks Service and the Cambridge Office for Tourism. Please subscribe by emailing [email protected] or visit BostonUSA.com for the most up-to-date version. Contents I. Hotel News II. Waterfront News III. Logan Airport and Transportation Update IV. Culinary & Craft Beer News V. Museums, Attractions, Sports, Performing Arts & Entertainment News VI. Additional Developments I. Hotel News – Hotel openings in 2018/2019 & beyond Hotel inventory in Boston will grow by almost 5,000 new hotel rooms in the next 5 years, a 20% increase in supply. These hotels are a mixture of full-service hotels, boutique properties, and extended-stay facilities. More than half the rooms are planned for the South Boston Waterfront near the Boston Convention & Exhibition Center, while the area south of North Station will undergo transformative projects. East Boston, Cambridge, Somerville, and Chelsea are also key areas of new hotel development. 2018 Openings • Staypineapple opened a new addition to the pineapple family, Staypineapple, South End, at the former location of The Chandler Inn on February 28, 2018. • At the Ink Block Project in Boston’s South End, the 205-room AC by Marriott Boston Downtown is now open. -
Backlash Toward Diversity Initiatives: Examining the Impact of Diversity Program Justification, Personal and Group Outcomes
The International Journal of Conflict of Management Vol. 15, No. 1, pp. 77-102 BACKLASH TOWARD DIVERSITY INITIATIVES: EXAMINING THE IMPACT OF DIVERSITY PROGRAM JUSTIFICATION, PERSONAL AND GROUP OUTCOMES Deborah L. Kidder Towson University Melenie J. Lankau University of Georgia Donna Chrobot-Mason University of Cincinnati Kelly A. Mollica Bethel College, TN Raymond A. Friedman Vanderbilt University This study used a scenario design to examine whether there are different reactions among whites based on how a diversity program is justified by an organization. A reactive justification (affirmative action) was pro- posed to result in greater backlash than a competitive advantage justifi- cation (diversity management). In addition, this study examined the effects of personal and group outcomes on backlash and explored two individual difference variables, gender and orientation toward other ethnic groups, as potential moderators of the proposed relationships. Backlash was operationalized in four ways: an affect-based measure (negative emotions), two cognitive-based measures (attitude toward the diversity program, perceptions of unfairness of promotion procedures), and a behavioral-intentions-based measure (organizational commit- ment). Results indicated that the diversity management justification was associated with more favorable support of the diversity initiative, and that unfavorable personal and group outcomes adversely affected backlash reactions. There was no empirical support for the influence of the moderator variables on the proposed relationships, however, a main e;Correspondence conceming this article should be addressed to Deborah L. Kidder Towson University, Department of Management, 8000 York Road, Towson MD 21252. Email: [email protected] 78 BACKLASH TOWARD DIVERSITY INITIATIVES effect for gender was found. Implications of the study's findings and fu- ture research directions are discussed. -
Backlash in Gender Equality and Women's and Girls' Rights
STUDY Requested by the FEMM committee Backlash in Gender Equality and Women’s and Girls’ Rights WOMEN’S RIGHTS & GENDER EQUALITY Policy Department for Citizens' Rights and Constitutional Affairs Directorate General for Internal Policies of the Union PE 604.955– June 2018 EN Backlash in Gender Equality and Women’s and Girls’ Rights STUDY Abstract This study, commissioned by the European Parliament’s Policy Department for Citizens’ Rights and Constitutional Affairs at the request of the FEMM Committee, is designed to identify in which fields and by which means the backlash in gender equality and women’s and girls’ rights in six countries (Austria, Hungary, Italy, Poland, Romania, and Slovakia) is occurring. The backlash, which has been happening over the last several years, has decreased the level of protection of women and girls and reduced access to their rights. ABOUT THE PUBLICATION This research paper was requested by the European Parliament's Committee on Women's Rights and Gender Equality and commissioned, overseen and published by the Policy Department for Citizen's Rights and Constitutional Affairs. Policy Departments provide independent expertise, both in-house and externally, to support European Parliament committees and other parliamentary bodies in shaping legislation and exercising democratic scrutiny over EU external and internal policies. To contact the Policy Department for Citizens’ Rights and Constitutional Affairs or to subscribe to its newsletter please write to: [email protected] RESPONSIBLE RESEARCH ADMINISTRATOR Martina SCHONARD Policy Department for Citizens' Rights and Constitutional Affairs European Parliament B-1047 Brussels E-mail: [email protected] AUTHORS Borbála JUHÁSZ, indipendent expert to EIGE dr. -
Theorising Backlash Politics: Conclusion to a Special Issue on Backlash Politics in Comparison
A Service of Leibniz-Informationszentrum econstor Wirtschaft Leibniz Information Centre Make Your Publications Visible. zbw for Economics Alter, Karen J.; Zürn, Michael Article — Published Version Theorising backlash politics: Conclusion to a special issue on backlash politics in comparison British Journal of Politics and International Relations Provided in Cooperation with: WZB Berlin Social Science Center Suggested Citation: Alter, Karen J.; Zürn, Michael (2020) : Theorising backlash politics: Conclusion to a special issue on backlash politics in comparison, British Journal of Politics and International Relations, ISSN 1467-856X, Sage, Thousand Oaks, CA, Vol. 22, Iss. 4, pp. 739-752, http://dx.doi.org/10.1177/1369148120947956 This Version is available at: http://hdl.handle.net/10419/227745 Standard-Nutzungsbedingungen: Terms of use: Die Dokumente auf EconStor dürfen zu eigenen wissenschaftlichen Documents in EconStor may be saved and copied for your Zwecken und zum Privatgebrauch gespeichert und kopiert werden. personal and scholarly purposes. Sie dürfen die Dokumente nicht für öffentliche oder kommerzielle You are not to copy documents for public or commercial Zwecke vervielfältigen, öffentlich ausstellen, öffentlich zugänglich purposes, to exhibit the documents publicly, to make them machen, vertreiben oder anderweitig nutzen. publicly available on the internet, or to distribute or otherwise use the documents in public. Sofern die Verfasser die Dokumente unter Open-Content-Lizenzen (insbesondere CC-Lizenzen) zur Verfügung gestellt haben sollten, If the documents have been made available under an Open gelten abweichend von diesen Nutzungsbedingungen die in der dort Content Licence (especially Creative Commons Licences), you genannten Lizenz gewährten Nutzungsrechte. may exercise further usage rights as specified in the indicated licence. -
Conceptualising Backlash Politics: Introduction to a Special Issue on Backlash Politics in Comparison
A Service of Leibniz-Informationszentrum econstor Wirtschaft Leibniz Information Centre Make Your Publications Visible. zbw for Economics Alter, Karen J.; Zürn, Michael Article — Published Version Conceptualising backlash politics: Introduction to a special issue on backlash politics in comparison British Journal of Politics and International Relations Provided in Cooperation with: WZB Berlin Social Science Center Suggested Citation: Alter, Karen J.; Zürn, Michael (2020) : Conceptualising backlash politics: Introduction to a special issue on backlash politics in comparison, British Journal of Politics and International Relations, ISSN 1467-856X, Sage, Thousand Oaks, CA, Vol. 22, Iss. 4, pp. 563-584, http://dx.doi.org/10.1177/1369148120947958 This Version is available at: http://hdl.handle.net/10419/227463 Standard-Nutzungsbedingungen: Terms of use: Die Dokumente auf EconStor dürfen zu eigenen wissenschaftlichen Documents in EconStor may be saved and copied for your Zwecken und zum Privatgebrauch gespeichert und kopiert werden. personal and scholarly purposes. Sie dürfen die Dokumente nicht für öffentliche oder kommerzielle You are not to copy documents for public or commercial Zwecke vervielfältigen, öffentlich ausstellen, öffentlich zugänglich purposes, to exhibit the documents publicly, to make them machen, vertreiben oder anderweitig nutzen. publicly available on the internet, or to distribute or otherwise use the documents in public. Sofern die Verfasser die Dokumente unter Open-Content-Lizenzen (insbesondere CC-Lizenzen) zur Verfügung gestellt haben sollten, If the documents have been made available under an Open gelten abweichend von diesen Nutzungsbedingungen die in der dort Content Licence (especially Creative Commons Licences), you genannten Lizenz gewährten Nutzungsrechte. may exercise further usage rights as specified in the indicated licence.