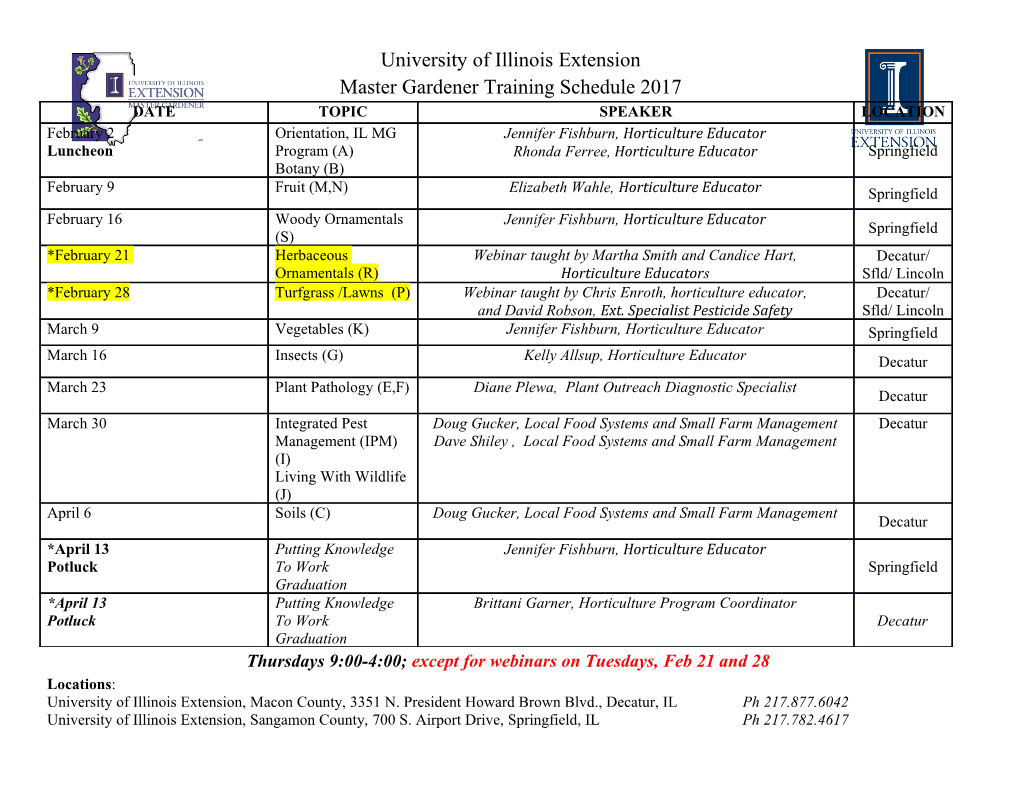
applied sciences Article Research on the Influence of Backlash on Mesh Stiffness and the Nonlinear Dynamics of Spur Gears Yangshou Xiong 1,2,*, Kang Huang 3,*, Fengwei Xu 3,†, Yong Yi 3,†, Meng Sang 3,† and Hua Zhai 4,† 1 School of Materials Science and Engineering, Hefei University of Technology, Hefei 230009, China 2 Anhui Zhongke Photoelectric Color Selection Machinery Co., Ltd., Hefei 231202, China 3 School of Mechanical Engineering, Hefei University of Technology, Hefei 230009, China; [email protected] (F.X.); [email protected] (Y.Y.); [email protected] (M.S.) 4 Institute of Industry & Equipment Technology, Hefei University of Technology, Hefei 230009, China; [email protected] * Correspondence: [email protected] (Y.X.); [email protected] (K.H.) † These authors contributed equally to this work. Received: 26 December 2018; Accepted: 7 March 2019; Published: 12 March 2019 Abstract: In light of ignoring the effect of backlash on mesh stiffness in existing gear dynamic theory, a precise profile equation was established based on the generating processing principle. An improved potential energy method was proposed to calculate the mesh stiffness. The calculation result showed that when compared with the case of ignoring backlash, the mesh stiffness with backlash had an obvious decrease in a mesh cycle and the rate of decline had a trend of decreasing first and then increasing, so a stiffness coefficient was introduced to observe the effect of backlash. The Fourier series expansion was employed to fit the mesh stiffness rather than time-varying mesh stiffness, and the stiffness coefficient was fitted with the same method. The time-varying mesh stiffness was presented in terms of the piecewise function. The single degree of freedom model was employed, and the fourth order Runge–Kutta method was utilized to investigate the effect of backlash on the nonlinear dynamic characteristics with reference to the time history chart, phase diagram, Poincare map, and Fast Fourier Transformation (FFT) spectrogram. The numerical results revealed that the gear system primarily performs a non-harmonic-single-periodic motion. The partially enlarged views indicate that the system also exhibits small-amplitude and low-frequency motion. For different cases of backlash, the low-frequency motion sometimes shows excellent periodicity and stability and sometimes shows chaos. It is of practical guiding significance to know the mechanisms of some unusual noises as well as the design and manufacture of gear backlash. Keywords: gear backlash; mesh stiffness; potential energy method; low-frequency; nonlinear dynamics 1. Introduction Gear dynamics is an important method to predict dynamic performance as well as to monitor the status of a gear system. The time-varying mesh stiffness caused by alternately changing the gear pairs in mesh plays a crucial role in dynamic responses. An effective time-varying mesh stiffness model is a basic condition to conduct a dynamic analysis. Thus, it is significant to recognize the mechanism of a gear system’s shock and vibration to investigate the influence of time-varying mesh stiffness on vibration responses, especially with regard to the mechanism of the noise, which is hard to identify. One consistently popular topic in gear dynamics is how to describe the change rule of time-varying mesh stiffness correctly and effectively. The ISO Standard 6336-1 [1] recommends a stiffness formula to calculate the maximum single tooth mesh stiffness for spur and helical gears according to experimental tests. In References [2–4], time-varying mesh stiffness was simplified as a rectangular Appl. Sci. 2019, 9, 1029; doi:10.3390/app9051029 www.mdpi.com/journal/applsci Appl. Sci. 2018, 8, 2404 2 of 13 Appl. Sci. 2019, 9, 1029 2 of 13 experimental tests. In References [2–4], time-varying mesh stiffness was simplified as a rectangular equation which had significant differences from the actual value. The authors in Reference [5] used a equationpolynomial which fitting had method significant to smooth differences the result from of thethe actualtime-varying value. Thecontact authors stiffness in Reference that was obtained [5] used aby polynomial the Hertz contact fitting algorithm. method to The smooth Fourier the series result was of used the to time-varying fit time-varying contact mesh stiffness stiffnessthat function was obtainedapproximatively by the in Hertz Reference contact [6]. algorithm. Kuang and The Yang Fourier proposed series an equation was used to to calculate fit time-varying the single meshtooth stiffnessbending functionstiffness approximativelyfor the addendum-modified in Reference gear [6]. Kuang and the and curve-fitted Yang proposed coefficients an equation took the to calculatenumber theof teeth single as tooth a variable bending [7]. stiffness In Reference for the [8], addendum-modified the mesh stiffness gearbetween and thean curve-fittedengaged gear coefficients pair was tookregarded the number as consisting of teeth of aslocal a variable Hertzian [7 stiffness]. In Reference and tooth [8], bending the mesh stiffness. stiffness Cai between and Tang an engaged revised gearKuang’s pair calculation was regarded formula as consisting and proposed of local an Hertziananalytical stiffnessmethod andto calculate tooth bending the mesh stiffness. stiffness Cai by andconsidering Tang revised the Kuang’sload condition calculation and formula the tooth and proposedprofile modification an analytical methodin References to calculate [9,10]. the Chen mesh stiffnessinvestigated by consideringthe differences the between load condition the rectangula and ther toothstiffness profile and modificationits approximate in Referencesform on the [9 gear,10]. Chennonlinear investigated dynamic thecharacteristics differences in between Reference the [11]. rectangular stiffness and its approximate form on the gearAccording nonlinear to dynamicthe available characteristics literature, inthe Reference main methods [11]. to calculate mesh stiffness are Finite ElementAccording Method to (FEM) the available and the potential literature, energy the main method. methods These to two calculate methods mesh have stiffness advantages are Finite and Elementdisadvantages. Method The (FEM) potential and theenergy potential method energy was proposed method. Theseby Yang two [12] methods and has have been advantages improved andseveral disadvantages. times [13–16]. The It potentialis widely energy used in method the fail wasure proposed analysis byof a Yang gear [ 12system] and has[17–21]. been The improved FEM, severalwhich can times reflect [13 –the16]. real It iscontact widely status, used is in often the failure applied analysis to figure of out a gear engineering system [ 17problems–21]. The [22–24]. FEM, whichMoreover, can reflectthe FEM the is real a common contact method status, is to often verify applied the validity to figure of the out potential engineering energy problems method [22 while–24]. Moreover,both the FEM the FEMand potential is a common energy method method to verify always the igno validityre the of influence the potential of backlash energy method on mesh while stiffness. both the FEMThe andbacklash potential is very energy useful method to avoid always the jam ignore phenomenon the influence in ofconditions backlash of on elastic mesh stiffness.deformation and thermalThe backlash expansion, is very i.e., useful adaptive to avoid backlash the jamis one phenomenon of the necessary in conditions conditions of to elastic ensure deformation the normal andoperation thermal of expansion,gear. One way i.e., adaptiveto achieve backlash backlash is oneis to of reduce the necessary tooth thickness. conditions The to reduction ensure the in normal tooth operationthickness will of gear. cause One a decrease way to in achieve the stiffness, backlash further is to reduceinfluencing tooth the thickness. dynamic The performance. reduction inIn toothcurrent thickness gear dynamics, will cause the a effect decrease of backlash in the stiffness, is limited further to the influencing definition theof the dynamic nonlinear performance. backlash Infunction current [25–30]. gear dynamics, the effect of backlash is limited to the definition of the nonlinear backlash functionThus, [25 this–30 work]. will focus on the influence of backlash on time-varying mesh stiffness, carry out nonlinearThus, dynamic this work analysis, will focus and on investigate the influence the of dynamic backlash responses on time-varying for various mesh values stiffness, of backlash. carry out nonlinearThis is expected dynamic to establish analysis, the and indirect investigate relationship the dynamic between responses backlash for and various dynamic values performance of backlash. as Thiswell as is expecteddirect the todesign establish and thecontrol indirect of the relationship gear’s backlash. between backlash and dynamic performance as well as direct the design and control of the gear’s backlash. 2. Influence of Backlash on Time-Varying Mesh Stiffness 2. Influence of Backlash on Time-Varying Mesh Stiffness 2.1. Mesh Stiffness Model with Backlash 2.1. Mesh Stiffness Model with Backlash Available mesh stiffness models do not consider the influence of backlash. Precision tooth profile Available mesh stiffness models do not consider the influence of backlash. Precision tooth profile equations play an important role in the analysis method to calculate the mesh stiffness. According to equations play an important role in the analysis method to calculate the mesh stiffness. According
Details
-
File Typepdf
-
Upload Time-
-
Content LanguagesEnglish
-
Upload UserAnonymous/Not logged-in
-
File Pages13 Page
-
File Size-