Chapter 1. Introduction
Total Page:16
File Type:pdf, Size:1020Kb
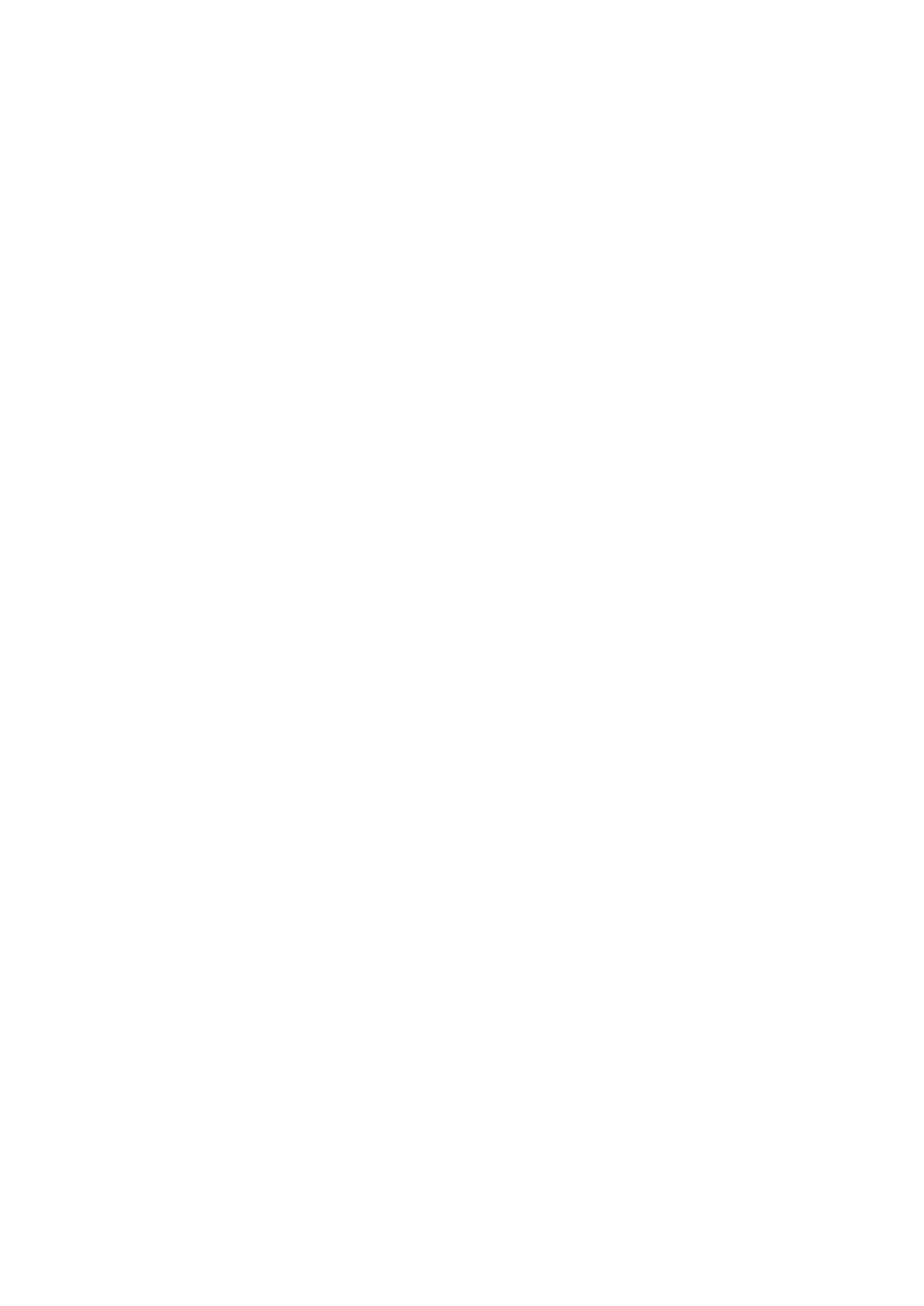
Load more
Recommended publications
-
Custom and Multichip Packaging Contract Manufacturing
Custom & Multichip Packaging Contract Manufacturing Micross’ contract assembly offers design and engineering support, BOM procurement, and a wide selection of package, substrate and interposer materials. Micross provides comprehensive semiconductor packaging services for multiple electronic components, including digital, mixed signal, analog, multi-chip and System-in-Package (SiP). We design, build and test hermetic QML and chip scale packaging for various markets including down-hole, aerospace, satellite and military. We combine advanced processes and product development to provide full turnkey support for prototype to volume production of flip chip and wire bond packages including single chip, multichip and SiP applications on organic substrates or ceramic substrates. By ensuring delivery of finished wafers through our relationships with silicon OCMs, and full coordination of customer BOM requirements, we offer complete supply-chain management services for micro- electronic assemblies. Micross Components can support your custom design with: Micross supplies modules and contract assembly services for multiple platforms: industrial, airborne; commercial and government satellites; • Complete turnkey product - including program missile and ordnance; C4ISR and medical. and vendor management of all elements throughout the product lifecycle • Co-development of a statement of work (SOW) Custom Multichip Packaging (MCP) is a die based system or sub-system • Co-design, starting with schematic, netlist or product definition and documentation assembled into a single package which is then mounted to the PCB. • Environmental requirements review In its simplest form factor, two or more of the same die are combined in one industry standard package that is smaller than the equivalent • Package and material selection for optimization of electrical and environmental performance, single die packages combined. -
The NASA Electronic Parts and Packaging (NEPP) '02 Workshop
The NASA Electronic Parts and Packaging (NEPP) ‘02 Workshop 1 JPL 400-1015, 04/02 2 The NASA Electronic Parts and Packaging (NEPP) ‘02 Workshop April 30 - May 2, 2002 Hilton Nassau Bay & Marina Houston, TX Organized by: NEPP Information, Management and Dissemination Project 3 Message ________________________ from Chuck Barnes, NEPP Program Manager Welcome to the Annual NEPP Workshop on Electronic Parts, Packaging, and Radiation Characterization for Space Applications! We’re happy you are with us and look forward to talking with you. Let’s start off with a few words about the NASA Electronic Parts and Packaging (NEPP) Program. The NEPP objectives are to: Assess the reliability of newly available electronic parts and packaging technologies for usage on NASA projects through validations, assessments and characterizations and the development of test methods/tools. Expedite infusion paths for advanced (emerging) electronic parts and packaging technologies by evaluations of readiness for manufacturability and project usage considerations. Provide NASA Projects with technology selection, application, and validation guidelines for electronic parts and packaging hardware and processes. Retain and disseminate electronic parts and packaging assurance, reliability validations, tools and availability information to the NASA community. NEPP is organized around three technology concentrations and the Information Management and Dissemination effort. The technology concentrations are Electronic Parts (EPAR), Electronic Packaging (EPAC), and Electronic Radiation Characterization (ERC). The Information Management & Dissemination (IMD) project is responsible for making all NEPP products and deliverables accessible in a controlled manner and is coordinating this conference. The Electronic Parts Project is tied to satisfying the needs of NASA programs/projects for evaluation of newly available and advanced electronic parts and maximizing effectiveness and efficiency through leveraging by teaming and partnering with industry and other agencies. -
Introduction to System IC Design Flow
Introduction to System IC and Design Flow Outline System-on-a-Chip (SoC) Trend SoC Integration & Challenge System-in-a-Package (SIP) IC Industry and Chip Production Flow System IC Design Flow Chip Debugging Tools and Reliability Issues 2 SoC Concept Analog Memory PCB ASIC CPU Chip System on a Board Analog IP Memory IP Chip IP IP CPU System on a Chip 3 Soc Advantages Minimize System Cost PCB, passive components Assembling Testing Compact System Size Board layout vs. chip layout Reduce System Power Consumption I/O, passive components, current levels Increase System Performance Interconnecting delay High speed parallel bus 4 Years 2002 – 2008 Worldwide Communication SoC Market Values Unit: Million U.S. Dollars Product 2002 2003 2004 2005 2006 2007 2008 Digital Cellular 7,480 9,463 12,560 15,210 15,855 17,202 19,013 LAN Wireless 138 333 492 662 777 938 1,134 Mobile Infrastructure 325 344 418 537 511 479 481 Other Mobile Comms. 378 520 673 859 1,077 1,215 1,440 LAN 140 184 248 316 348 392 446 Premises and CO Line Card 167 161 188 201 199 204 219 Broadband Remote Access 918 1,313 1,617 1,793 1,717 1,837 1,978 Public Infrastructure 304 360 481 607 667 810 934 Other Wired Comms. 428 568 811 1,128 1,175 1,365 1,515 Total Communications 10,278 13,246 17,488 21,313 22,326 24,442 27,160 Source: Dataquest (2004/06) 5 Example1: Siemens C35i Phone 13 1. Infineon E-GOLD PMB2851E, GSM Baseband controller and DSP. -
Electronic Packaging Technologies 1
ElectronicElectronic PackagingPackaging TechnologiesTechnologies Sergio Lopez-Buedo, Eduardo Boemo Universidad Autonoma de Madrid e-mail: [email protected] Electronic Packaging Technologies 1 Introduction to Electronic Packaging • Electronic Packaging is a multi-disciplinary subject – Mechanical, Electrical and Industrial Engineering, Chemistry, Physics and even Marketing • Electronic Packaging: Housing and interconnection of integrated circuits to form electronic systems • Electronic Packaging must provide – Circuit support and protection – Heat dissipation – Signal distribution – Manufacturability and serviceability – Power distribution Electronic Packaging Technologies 2 Issues in Electronic Packaging Electrical analysis and testing Mechanical analysis and Reliability, Chemistry, testing Physics, Mat. performance, cost, Eng.. market need/timing, manufacturability, yields…other Thermal Manufacturing analysis and and Industrial testing Eng.. Market analysis Electronic Packaging Technologies 3 Hierarchy of Interconnection Levels • Level 0 – Gate-to-gate interconnections on the silicon die • Level 1 – Connections from the chip to its package • Level 2 – PCB, from component to component or to external connector • Level 3 – Connections between PCBs, including backplanes or motherboards • Level 4 – Connections between subassemblies, for example a rack • Level 5 – Connections between physically separate systems, using for example an Ethernet LAN Electronic Packaging Technologies 4 Blue Gene: Example of Connection Hierarchy Electronic -
2005 Injection Molded & Micro Fabrication Electronic Packaging
2005 INJECTION MOLDED & MICRO FABRICATION ELECTRONIC PACKAGING Dr. Ken Gilleo ET-Trends LLC Warwick, RI Dennis Jones Matrix, Inc. Providence, RI Abstract Thermoset epoxies, discovered nearly 80 years ago, remain the workhorse plastic for electronic packaging and printed circuit boards, but this could change with increasing technical, economic and regulatory demands. Modern halogen-free thermoplastics now boast superior properties and highly automated high-efficiency high-volume processes. Injection molding can readily produce intricate 3D structures suitable for electronic component packaging and 3D molded circuits. Although there is a well-established packaging infrastructure tied to thermoset epoxies there is a much larger world-wide manufacturing base that excels in thermoplastics. Nearly 16-billion pounds of thermoplastics are molded into various parts each year in the USA alone; 30 times higher than for epoxies. We believe that the time is right for adding thermoplastic packages, interconnects and circuitry to 21st century electronics. This paper will discuss concepts, novel designs, new processes and the advancements for injection molded packaging and highlight their impressive attributes; the lowest moisture uptake, the fastest processing and the highest stability in the world of polymers. While MEMS (Micro-Electro-Mechanical Systems) packaging will be a central theme, general component packaging will also be discussed including power packages and digital camera modules. The discussion will include the development of new BGA concepts that utilize automatic insert-molding of tiny metal balls to create the 1st (to chip) and 2nd level (to circuit board) interconnect system. Assembly topics will cover package sealing methods that include laser welding. New Multi-Chip Package (MCP) ideas based on insert-molded flexible circuitry will be described that could find use in stackable designs. -
Book of Knowledge (BOK) for NASA Electronic Packaging Roadmap
National Aeronautics and Space Administration Book of Knowledge (BOK) for NASA Electronic Packaging Roadmap Reza Ghaffarian, Ph.D. Jet Propulsion Laboratory Pasadena, California Jet Propulsion Laboratory California Institute of Technology Pasadena, California JPL Publication 15-4 2/15 National Aeronautics and Space Administration Book of Knowledge (BOK) for NASA Electronic Packaging Roadmap NASA Electronic Parts and Packaging (NEPP) Program Office of Safety and Mission Assurance Reza Ghaffarian, Ph.D. Jet Propulsion Laboratory Pasadena, California NASA WBS: 724297.40.43 JPL Project Number: 104593 Task Number: 40.49.02.24 Jet Propulsion Laboratory 4800 Oak Grove Drive Pasadena, CA 91109 http://nepp.nasa.gov i This research was carried out at the Jet Propulsion Laboratory, California Institute of Technology, and was sponsored by the National Aeronautics and Space Administration Electronic Parts and Packaging (NEPP) Program. Reference herein to any specific commercial product, process, or service by trade name, trademark, manufacturer, or otherwise, does not constitute or imply its endorsement by the United States Government or the Jet Propulsion Laboratory, California Institute of Technology. ©2015 California Institute of Technology. Government sponsorship acknowledged. Acknowledgments The author would like to acknowledge many people from industry and the Jet Propulsion Laboratory (JPL) who were critical to the progress of this activity. The author extends his appreciation to program managers of the National Aeronautics and Space Administration Electronics Parts and Packaging (NEPP) Program, including Michael Sampson, Ken LaBel, Dr. Charles Barnes, and Dr. Douglas Sheldon, for their continuous support and encouragement. ii OBJECTIVES AND PRODUCTS The objective of this document is to update the NASA roadmap on packaging technologies (initially released in 2007) and to present the current trends toward further reducing size and increasing functionality. -
Quad Flat No-Lead (QFN) Evauation Test
National Aeronautics and Space Administration Quad Flat No-Lead (QFN) Evaluation Testing Reza Ghaffarian, Ph.D. Jet Propulsion Laboratory Pasadena, California Jet Propulsion Laboratory California Institute of Technology Pasadena, California 6/17 National Aeronautics and Space Administration Quad Flat No-Lead (QFN) Evaluation Testing NASA Electronic Parts and Packaging (NEPP) Program Office of Safety and Mission Success Reza Ghaffarian, Ph.D. Jet Propulsion Laboratory Pasadena, California NASA WBS: 724297.40.43 JPL Project Number: 104593 Task Number: 40.49.02.35 Jet Propulsion Laboratory 4800 Oak Grove Drive Pasadena, CA 91109 http://nepp.nasa.gov 6/17 This research was carried out at the Jet Propulsion Laboratory, California Institute of Technology, and was sponsored by the National Aeronautics and Space Administration Electronic Parts and Packaging (NEPP) Program. Reference herein to any specific commercial product, process, or service by trade name, trademark, manufacturer, or otherwise, does not constitute or imply its endorsement by the United States Government or the Jet Propulsion Laboratory, California Institute of Technology. Copyright 2017. California Institute of Technology. Government sponsorship acknowledged. Acknowledgments The author would like to acknowledge many people from industry and the Jet Propulsion Laboratory (JPL) who were critical to the progress of this activity including the Rochester Institute of Technology (RIT). The author extends his appreciation to program managers of the National Aeronautics and Space -
Fpga Hardware
L2: FPGA HARDWARE 18-545: ADVANCED DIGITAL DESIGN PROJECT FALL 2011 BILL NACE Administrivia Team assignments are done Lab 1 is due Monday Project Proposals happen on Monday Reading Assignment #1 due today 13/14 students got it in to Blackboard on time David's attempt didn't get saved (?) Submit a PDF, don't fill in the web form 18-545: FALL 2011 2 Game Plan Overview Why use FPGAs? FPGA Internals Caveat: I will use Xilinx specific terminology since that’s the FPGA company you will be using. Beware that other companies use different terms 18-545: FALL 2011 3 FPGA Overview Field Programmable Gate Array Array of generic logic gates Gates where logic function can be programmed Programmable interconnection between gates Fielded systems can be programmed i.e. post-fabrication Xilinx Virtex-5 FPGA 18-545: FALL 2011 5 Design Platform Virtex-5 Development System Xilinx XC5VLX110T FPGA 17280 slices of CLB goodness 256MB DDR2 (SODIMM) DVI Video port VGA port is for input 10/100/1000 Ethernet port Audio Codec (AC97) USB2 port 16x2 LCD, RS-232 Compact Flash card slot Expansion connectors 18-545: FALL 2011 6 Game Plan Overview Why use FPGAs? FPGA Internals 18-545: FALL 2011 7 Why use FPGAs? System designers have a Goldilocks problem Off-the-shelf parts are not efficient enough Custom ASICs cost too much Need a “just right” solution ASIC Design Difficult to design Large and complex Issues in advanced processes Interconnect delay Device leakage Power density constraints Expensive to design / fabricate Mask set costs Non-recurring engineering costs Need a high-volume, high-profit market to justify costs! Energy Efficiency (MOPS/mW) Area Efficiency (MOPS/mm2) 10000 1000 Microprocessors 100 10 1 0.1 DSPs ASICs 0.01 1 2 3 4 5 6 7 8 9 10 11 12 13 14 15 16 17 18 19 20 Efficiency View An efficiency gap exists between ASICs and CPUs N. -
Integrated Circuit Package Types
APPENDIX C Integrated Circuit Package Types Overview With the ever-increasing levels of integration, packing more circuitry into ever smaller packages, electronic systems now rely on semiconductor devices. Anything from a few circuit components (transistors, resistors, and capacitors) to complete computer systems can be placed on a single silicon die. An integrated circuit is a package containing a single silicon (silicon germanium for RF circuits, or gallium arsenide for microwave frequency circuits) that forms either part of a larger electronic circuit or system or is a complete electronic system in its own right. When the IC forms a complete electronic system, it is commonly referred to as a system on a chip (SoC). Modern communications ICs are SoC designs. An extension to the IC is the multichip module (MCM), which contains multiple dies; for example, when sensors and circuits are to be housed in a single package but which cannot be fabricated on a single die. Originally referred to as a hybrid circuit, the MCM consists of two or more ICs and passive components on a common circuit base that are interconnected by conductors fabricated within that base. The MCM helps with size reduction problem and helps alleviate signal degradation. An extension to the MCM is the system in a package (SiP), on which devices are stacked vertically. Wire bonding to the substrate is common. An extension to the SiP is the package on a package (PoP). www.newnespress.com 2 Appendix C IC Package Types The package that the IC uses is either a through-hole package or a surface mount package, made of either plastic or ceramic. -
Advanced Electronic Packaging
National Aeronautics and Space Administration Advanced Electronic Packaging The Assurance Challenges October 15, 2013 Michael J. Sampson [email protected] NASA Goddard Spaceflight Center (Greenbelt) Safety and Mission Assurance Directorate 301-614-6233 Co- Manager NEPP Program www.nasa.gov http://nepp.nasa.gov To be presented by Michael J. Sampson at the Trilateral NASA/Japan Aerospace Exploration Agency (JAXA)/European Space Agency (ESA) Safety and Mission Assurance Meeting, Washington, DC, October 15, 2013. 1 Acronyms, Abbreviations Etc. Appx Appendix BME Base Metal Electrodes CCGA Ceramic Column Grid Array CLGA Ceramic Land Grid Array DLA Defense Logistics Agency EEE Electrical, Electronic, and Electromechanical FOD Foreign Object FPGA Field Programmable Gate Array GSFC Goddard Space Flight Center HDI High Density Interconnect HST Hubble Space Telescope IC Integrated Circuit I/O Input Output LGA Land Grid Array MIL-PRF-38534 Performance Specification Hybrid Microcircuits General Specification For MIL-PRF-38535 Performance Specification Integrated Circuits (Microcircuits) Manufacturing General Specification For NASA National Aeronautics and Space Administration Pb Lead Metal PBGA Plastic Ball Grid Array RoHS Restriction of Hazardous Substances Sn/Pb Tin/Lead rev revision To be presented by Michael J. Sampson at the Trilateral NASA/Japan Aerospace Exploration Agency (JAXA)/European Space 2Agency (ESA) Safety and Mission Assurance Meeting, Washington, DC, October 15, 2013. 2 Outline • What is Electronic Packaging? • Why Package Electronic Parts? Passivation Wire Dielectric • Hermetic and Non-hermetic Etch Stop Layer Via Dielectric Capping Layer Copper Conductor with • Packaging Challenges Global Barrier/Nucleation Layer • Area Arrays • Advantages of Hermetic Intermediate Metal 1 Pre-Metal Dielectric • Increasing Complexity Tungsten Contact Plug • Class Y Concept and Update Metal 1 Pitch • Major Xilinx Package Change To be presented by Michael J. -
3-D Packaging: a Technology Review
3-D Packaging: A Technology Review R. Wayne Johnson Auburn University 162 Broun Hall/ECE Dept. Auburn, AL 36849 334-844-1880 [email protected] Mark Strickland NASA/MSFC Huntsville, AL David Gerke NASA/JPL Pasadena, CA June 23, 2005 3-D PACKAGING A TECHNOLOGY REVIEW Table of Contents 2 INTRODUCTION 3 Package Stacking 8 Benefits of Package Stacking 14 Limitations of Package Stacking 14 Reliability 15 Technology Readiness Level Assessment 17 Die Stacking 17 Benefits of Die Stacking 33 Limitations of Die Stacking 34 Reliability 35 Technology Readiness Level Assessment 36 3-D Multichip Modules 37 Benefits of 3-D Multichip Modules 54 Limitations of 3-D Multichip Modules 54 Reliability 54 Technology Readiness Level Assessment 55 Wafer Stacking 56 Benefits of Wafer Stacking 60 Limitations of Wafer Stacking 60 Technology Readiness Level Assessment 63 Conclusions and Recommendations 64 References 65 2 3-D Packaging A Technology Review Introduction Traditional electronics are assembled as a planar arrangement of components on a printed circuit board (PCB) or other type of substrate. These planar assemblies may then be ‘plugged’ into a motherboard or card cage creating a ‘volume’ of electronics. This architecture is common in many military and space electronic systems as well as large computer and telecommunications systems and industrial electronics. The individual PCB assemblies can be replaced if defective or for system upgrade. Some applications are constrained by the volume or the shape of the system and are not compatible with the motherboard or card cage architecture. Examples include missiles, camcorders, and digital cameras. In these systems, planar rigid-flex substrates are folded to create complex 3-D shapes. -
For Your System in a Package
Unify ASICs for your System in a Package with TEKMOS Introducing Unify ASICs Applications for System in a Package are driven by the requirements of space, power, and development time. The total solution needs to be small. It typically runs off of a battery. And it needs a quick time-to-market. The major semiconductor suppliers have developed a number of cost effective blocks that can meet 90% of the requirements of an application. It is the last 10% that is the problem. Developers typically face two approaches for the last 10%. You can build what you need out of discrete components. This is inexpensive, but Picture of Stacked Die. requires a lot of board space. Or you can take a SOC (System on a Chip) approach. This will work, BGA packages, die can be stacked side by side as but can be very expensive, since the presence of well as on top of each other. And in some cases, we wireless interfaces and ARM processors requires can also include components that we cannot put on advanced processing to accommodate the diverse the ASIC such as large capacitors, and crystals. No requirements of diverse technologies as well as matter what package we use, the customer wins by expensive NREs. And such solutions require more having a single, highly integrated device for their development time because of the chip complexity. system. Tekmos has a third approach. We create a cost Technology effective ASIC using an appropriate technology to It is a fact that the NRE costs roughly double for implement the missing 10%.