Aug. 30, 1966 M
Total Page:16
File Type:pdf, Size:1020Kb
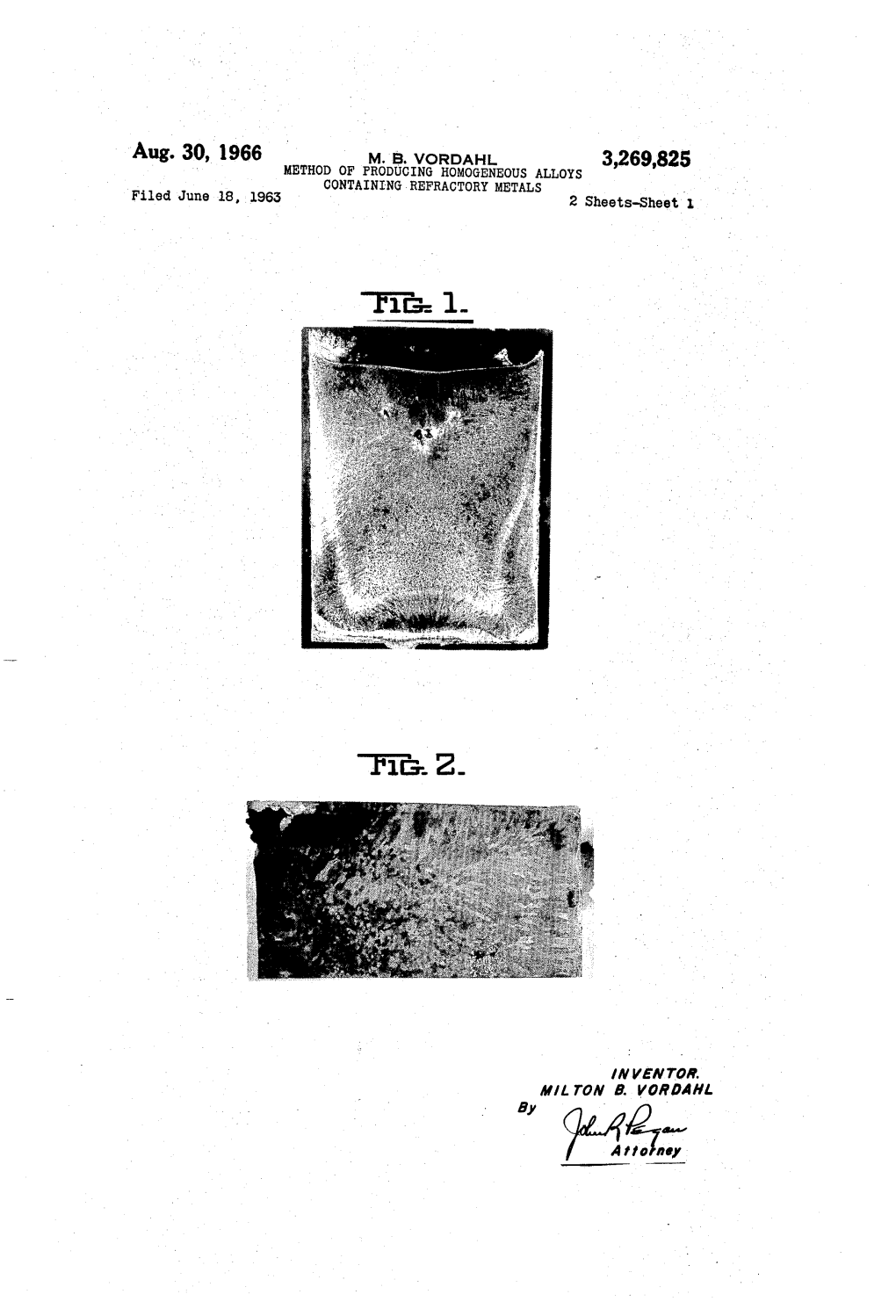
Load more
Recommended publications
-
Iron, Steel and Swords Script - Page 1 Powder Is Difficult
10.4. Crucible Steel 10.4.1 The Making of Crucible Steel in Antiquity Debunking the Myth of "Wootz" Before I start on "wootz" I want to be very clear on how I see this rather confused topic: There never has been a secret about the making of crucible (or "wootz") steel, and there isn't one now. Recipes for making crucible steel were well-known throughout the ages, and they were just as sensible or strange as recipes for making bloomery iron or other things. There are many ways for making crucible steel. If the crucible process worked properly, the steel produced was fully liquid, and it didn't matter much exactly how you made it. If the process did not work well and the steel was only partially molten, i.e. a mixture of liquid cast iron and solid austenite, the product was not good steel. Besides differences in the (always large) carbon concentration, the concentration of impurities might also be different - just like for bloomery steel. This might lead to differences in properties for comparable carbon concentrations, for example the susceptibility to cold shortness or the ability to form a good "watered silk" or "water" pattern. Crucible steel that has been liquid once is relatively homogeneous and slag-free - in contrast to bloomery steel. That is where crucible steel is "better" than bloomery steel. Crucible steel is always high carbon if not ultra-high carbon steel (UHCS). This is generally not so good. However, mixtures that would, for example, have produced 0.8 % carbon steel, a steel optimal for many applications, would not melt at the temperatures available. -
Northern Telangana, an Iron and Crucible Steel Production Landscape in India
ISIJ International, Vol. 54 (2014), No. 5, pp. 1030–1037 Northern Telangana, an Iron and Crucible Steel Production Landscape in India Gillian JULEFF,1)* Sriperumbudur JAIKISHAN,2) Sharada SRINIVASAN,2) Srinivas RANGANATHAN2) and Brian GILMOUR3) 1) University of Exeter, Laver Building, North Park Road, Exeter EX4 4QE, UK. 2) National Institute of Advanced Studies, IISc, Bangalore 560012, India. 3) Research Laboratory for Archaeology, University of Oxford, UK. (Received on November 30, 2013; accepted on March 3, 2014) Northern Telangana now lies in the remote rural heartland of India but is world renowned for its role in the past as a region of iron and crucible steel production, recorded in historical accounts and field inves- tigations by first Thelma Lowe and then S. Jaikishan. In 2010 a joint team from University of Exeter and NIAS (National Institute of Advanced Studies), Bangalore, carried out a six-week archaeological field sur- vey in the area that recorded 245 locations of which 183 are associated with metal-working. Locations of primary iron smelting dominated the survey results, with crucible steel manufacture forming c. 20% of the records. Further analysis is needed to resolve variations in smelting technologies but differences can be observed between smelting locations within settlements and those in more remote forested areas. A wide range of technologies are indicated by differences in tuyere size and shape, and techniques of fur- nace wall construction. The crucible steel-making locations show at least two different traditions using small, thin-walled crucibles and large, conical-lidded crucibles. This paper describes a preliminary assess- ment of the survey data. -
Steelmaking Technology for the Last 100 Years: Toward Highly Efficient Mass Production Systems for High Quality Steels
ISIJ International, Vol. 55 (2015), No. 1, pp. 36–66 Review Steelmaking Technology for the Last 100 Years: Toward Highly Efficient Mass Production Systems for High Quality Steels Toshihiko EMI* Formerly Tohoku University and Kawasaki Steel. Now at Takaido Higashi 1-31-6-603, Suginami, Tokyo, 168-0072 Japan. (Received on August 15, 2014; accepted on September 29, 2014; originally published in Tetsu-to-Hagané, Vol. 100, 2014, No. 1, pp. 31–58) Progress of steelmaking technology in Japan over the last 100 years is overviewed covering hot metal pretreatment, primary steelmaking with open hearth furnaces, converters and electric arc furnaces, sec- ondary refining of steel with degassers and ladle furnaces, and ingot- and continuous-casting. Key issues that contributed considerably to the progress of the unit processes are highlighted with sci- entific, technological and engineering breakthroughs involved. Also, systematization of the unit processes is depicted for optimizing full cost, productivity and quality of steel products to meet the constraints on the resources and socioeconomic demands of the steel market at times. Possible future development of steel technology is briefly commented on the basis of the above obser- vation. KEY WORDS: Historical overview; hot metal pretreatment; primary- and secondary-steelmaking; ingot- and continuous-casting; steelmaking system. phorus (P) since iron ore available there was high in P. 1. Introduction Mass production of steel in those days was dominated by Celebrating the centennial anniversary of the Iron and Britain, Germany, Belgium and USA. Japan imported nec- Steel Institute of Japan, an attempt is made to give an over- essary pieces of equipment, materials, operational skill, and view of the development of steelmaking technologies in raw materials from these countries to start industrial steel- Japan in the last 100 years with own limited experiences in making with crucible furnace in 1890. -
On Slaves and Silk Hankies Seeking Truth in Damascus Steel
On Slaves and Silk Hankies Seeking Truth in Damascus Steel Stephen C. Alter, 2017 aka: Baron Hrodr-Navar Hakonsson, OP Entry in 2017 Arts & Sciences Fair and Pentathlon Kingdom of Caid, Society for Creative Anachronism 7.6.2 Composition/Research Paper Seeking Truth in Damascus Steel Page 1 of 25 Much ink has been spilt by modern authors to extol the virtues of Damascus steel: “[The} ideal combination of strength, hardness and elasticity”1, “supersteel”2, and “Acme of Mankind’s Metallurgical Heritage .“ 3 At the same time one finds references to say that Damascus swords “were stiff and even brittle”4, and: [A]ll the rank humbugs cluster about the legendary lore of Damascus steel like flies around carrion. So it becomes necessary to expose the fallacy … that this steel was the eighth wonder of the world 5 What are we to believe? Legend and modern literature say that Damascus swords were amazingly flexible, which is an extraordinary claim for ultrahigh carbon steel. Where is the proof? We are told that the Crusaders knew and feared these weapons, giving them the name “Damascus”, but we are shown no references. Were newly forged Damascus swords really quenched in the blood of slaves? Did production of Damascus steel end when Timur carried off all the skilled workers? Modern authors say these things but don’t back them up. One finds dozens of vendors today who advertise authentic Damascus steel blades for sale, is this the same material that the Crusaders and medieval Arabs knew? Finally, modern science has answered all the questions and recreated the lost art of forging Damascus steel. -
Superalloys, the Most Successful Alloy System of Modern Times-Past, Present, and Future
SUPERALLOYS, THE MOST SUCCESSFUL ALLOY SYSTEM OF MODERN TIMES - PAST, PRESENT AND FUTURE Art Kracke Vice President Business Technology ATI Allvac Abstract The deep roots of superalloys go back to 1907, although the term ‘super-alloy’ is believed to have first been used in the mid 1940s to refer to cobalt-base alloys such as Vitallium and nickel- base Waspaloy®. During the past 50 years, much alloy, hot working, heat treating and process development has occurred, enabling many of the end use technologies we know today. This presentation will discuss some of the history of the superalloy industry related to the superalloys 718, Waspaloy and their derivatives, including ATI 718Plus® alloy. The presentation will then describe the wide range of manufacturing techniques used for the production of superalloys, available product forms and end-use applications. Concluding the presentation will be a discussion on what advancements we are likely to see in the future. Introduction Superalloys are successful today because they have solved pressing demands for durability and strength in machines and systems that were barely imaginable a hundred years ago. Superalloys have helped us conquer air and space, plumb the depths of the earth and ocean, and address many other challenges of modern life. As such, they deserve to have their story told. The nature of this industry, however, makes the telling a challenging task. Its history is one of many small events and inventions that took place across the boundaries of nations, industries and countries. Many individuals contributed to the state of the art today, and only a few left their names in the scattered records. -
Increasing Tool Steel Surface Wear Resistance by Surface Treatment
Műszaki Tudományos Közlemények vol. 13. (2020) 170–173. DOI: Hungarian: https://doi.org/10.33895/mtk-2020.13.32 English: https://doi.org/10.33894/mtk-2020.13.32 INCREASING TOOL STEEL SURFACE WEAR RESISTANCE BY SURFACE TREATMENT László Tóth,1 Zoltán NyIKEs,2 Mhatre UMEsH3 1, 2 Óbuda University, Donát Bánki Faculty of Mechanical and Safety Engineering. Budapest, Hungary, [email protected], [email protected] 3 Surface Modification Technologies Pvt. Ltd. Mombai, India, [email protected] Abstract The industry is imposing increasing wear and tear requirements on tools, which can no longer be satisfied with the development of base materials (tool steels). surface treatment technologies can provide a solution as the surface of the working tool must be suitable. It can determine a relationship between the hardness, surface roughness and the abrasion resistance of various surface treatments and the coating technologies such as PVD as a result of tool steel surface layers. These relationships form the basis for tool selection and provide a theoretical basis for the design of surface technologies. Keywords: hardness, wear resistance, PVD process, surface treatment. 1. Introduction In the 1960s the rapid development of steels and the emergence of steels with increased strength Tool steels can be graded according to their re- also placed higher expectations on the market for quirements such as high hardness, toughness, tool materials. Tool manufacturers have there- wear-resistance and other determining mechan- ical properties. fore responded by applying surface treatment to As the development of steels has its limitations, the tool steels to meet the cutting requirements. -
Damascus Steel and Crucible Steel in Central Asia
Damascus Steel and Crucible Steel in Central Asia Ann Feuerbach "Everything is mine:' said gold; "Everything is mine," said Damascus steel; "I can buy anything," said gold; "I can acquire anything,"said Damascus steel. Pushkin, 1827 (translated by Bogachev, 1952) For hundreds of years, swords made of Damascus steel have been famous for their flexibility, retention of a sharp edge and beautiful surface pattern. There are two broad cat- egories of swords that are made of what is called Damascus, Damascene or Damask steel. One category was made by forg- ing different strips of iron and steel together and is known as pattern welded Damascus steel. This method was used throughout Europe and Asia. The second category of some of the invaders who attacked the prosperous cities along Damascus steel was made from an ingot of crucible steel and the route and caused the downfall of many of them. is known as crucible Damascus steel. This method has his- The recent dissolution of the Soviet Union has greatly facil- torically been associated with the Wootz steel made in the itated the exchange of scholarly information between the for- Indian subcontinent. A reexamination of the sources of infor- mer Soviet states and the rest of the world. This has allowed the mation traditionally used to maintain the myths and legends author the opportunity for collaborative research with scholars about Damascus steel indicates that many beliefs are based in three different areas of CentralAsia,the results of which great- on little or no hard evidence. It is becoming apparent that ly increased understanding of the production and use of cru- Central Asia was a major producer of crucible steel. -
Heat Treatment of Steel Hardenin G Tempering Case-Harden in G
M A CHINERY ’S REFERENCE SERIES EACH NU M BER IS ONE U NIT IN A COM PL ETE LIBRARY OF M ACHINE DESIGN A ND SHO P PR A CTIC E R EV ISED AND R EPU BLISH ED FROM M ACHINERY NUM BER 63 HEAT TREA TM ENT OF STEEL — — HARDENING TEM PERING C ASE-HARDENING SE COND E DITION CONTE NTS H arden i n arbon tee s AL g C S l b R P H B ADGER and J . , y STOREY H ardeni ng Carbon and L ow T u ngst en Stee ls ‘ The E lectri c Hardeni ng F urnace Heat Treatm ent of Spri ng Stee l Heat Treatm ent of A lloy Steels Case - Harden i ng ase - ar deni n F urn ace s an d h i r C H g T e U se b J . , y SALL OWS Co ri ht 1910 Th e I nd u st ri al e P l i py g , , P r s s . u b sher s of M A CHIN E RY . L f a ay et t e St r e e t , N e w Y ork Ci t y CHAPTE R I H A R D E N I N G C A R B ON S TE E L S " Ori ginally the name steel was applied to various combinations of - i ron and carbon , there being present, together with these , as impuri A ties , small proportions of silicon and manganese . t the pres ent time , however , the use of the name is extended to c over combinations r of i on with tungsten , vanadium , nickel , chromium , molybdenum , titan r ium and some of the ra er elements . -
Making Steel in the "Aristotle Furnace"
Making Steel in the "Aristotle Furnace" Lee Sauder Introduction The early presence of steel is usually explained as direct production from the bloomery, or long cementation in a hearth, or later, by crucible steelmaking. There is another simple, almost obvious way to increase the carbon content and decrease the slag content of bloom iron, that we like to refer to as the “Aristotle” method. My friend Skip Williams has designed an elegant little furnace for this process, which I demonstrated at the conference. After a brief description of the building and running of the furnace, I’ll give a little background on how we stumbled onto this idea, and then summarise the variables we have identified that influence the carbon content of the resulting steel. And then, of course, pose a few questions. Experiment description Furnace Construction After several days of very hard work on the bloomery experiments, and some not insignificant celebrating afterwards, I was not really intending to do anything for the Friday morning experimental session. But I was encouraged by Steve Mankowski to build and run an Aristotle furnace. Steve had earlier had several discussions with folks who were interested in this process, and more compellingly, with several folks who didn’t believe it possible. Since this whole process is so simple, quick, and straightforward, I agreed, and we set to work. 1 I had not built or run one of these furnaces in a year and a half, and I was dusting off my memory as we went, so all dimensions and procedures recounted here are very approximate. -
Introduction
Tool Steels, 5th Edition (#06590G) Copyright © 1998 ASM International ® Author(s): G. Roberts, G. Krauss, and R. Kennedy All rights reserved. www.asminternational.org CHAPTER 1 Introduction Tool steels are the alloys used to manufacture the also used for tool applications. This chapter ex tools, dies, and molds that shape, form, and cut other plores further the philosophies which make tool materials, including steels, nonferrous metals, and steels a very special class of steels, the long histori plastics. This definition of tool steels has been ex cal evolution of iron and steel manufacture, includ panded into the following description in the 'Tools ing steels for tools, and the more recent develop Steels" section of the Steel Products Manual of the ment of tool steels as they emerged from the Iron and Steel Society (Ref 1): development of iron and steel products in general. The classification of the many types of tool steels is Tool steels are either carbon, alloy or described in Chapter 2, and subsequent chapters high-speed steels, capable of being hard describe production, alloy design, heat treatment, ened and tempered. They are usually melted and specific tool steels in detail. in electric furnaces and produced under tool steel practice to meet special requirements. They may be used in certain hand tools or in Tool Steels as Special Alloys mechanical fixtures for cutting, shaping, forming and blanking of materials at either Tool steels have long been considered to be a very ordinary or elevated temperatures. Tool special group of alloys with characteristics similar steels are also used on a wide variety of to but different from those of other steels. -
The Processes of Iron and Steel Making
The Processes of Iron and Steel Making This page has been constructed to give the reader a more in-depth insight into the processes carried out at the Wortley Forges, associated and similar works. You will find some descriptions are duplicated on other pages in this site. Iron Mining The Bloomery Iron Making Process The Finery & Chafery Iron Making Process Iron Making by Blast Furnace The Puddling Process Making Cementation Steel Making Crucible Steel Making Bessemer Steel Making Steel by the Siemens Process Magazine Article explaining iron making Iron Mining The availability of Iron Ore was the key to the early iron industry. Even today (and more conspicuously up to the 1970s) a number of steelworks sites were directly a results of a furnace and later a works built were iron ore was available, although some sites are a result of water power, transport, fuel and other economic pressures. Iron is very common on the planet earth and the British Isles are no exception, however only where the iron content of the ore is quite high is the ore worth exploiting. This is one reason why almost all iron ore is now imported into the U.K. from the likes of Africa and Australia. It seems that iron ore was mined in many areas across the country, but these area progressively reduced as the demand increase and larger scale operations became more common. The important iron mining areas were to the south of Cumbria (near Barrow in Furnace), South Teeside, North Lincolnshire and a band across the midlands from Lincolnshire to Oxfordshire. -
Wootz Crucible Steel: a Newly Discovered Production Site in South India
[Papersfrom the Instituteof Archaeology5(1994) 49-59] Wootz crucible steel: a newly discovered production site in South India Sharada Srinivasan Institute of Archaeology, VCL Introduction High-carbon iron alloys are known to have been produced in parts of Asia such as India, where a traditional crucible steel has been produced, (Bronson 1986; Smith 1960: 14-24) and in China, where cast iron was produced(Tylecote 1976: 85), long before they came into vogue in Europe (Lowe 1988). The repute of Indian iron andsteel can be tracedto Classical Mediterraneanaccounts (Bronson 1986: 18). European travellers and geologists from the seventeenth century onwardshave described the production of steel ingots,in differentparts of South India (Fig. 1), by crucible processes. Such accounts were made in the former province of Golconda, Andhra Pradesh (Voysey 1832), the former state of Mysore (modem Kamataka) (Buchanan-Hamilton 1807) and Salem district in Tamil Nadu (Buchanan-Hamilton 1807, Wood 1893); Coomaraswamy (1956: 192-3) has also described crucible steel processes at Alutnuvara in Sri Lanka. This South Indian steel was namedwootz, a European corruption of the Telegu word for steel, ukku. Indianwootz ingots are believed to havebeen used to forgethe famedOriental Damascusswords which havebeen found tohave a very high carboncontent of 1.5- 2.0% (Smith 1960: 14-6). The Persian Damascus blades,made in Khorasanand Isfahan from South Indian wootz fromGolconda, were known to be the finest weapons thenmade in Eurasia (Bronson1986: 22-3, Smith 1960: 14-6)and were reputedto cut even gauze kerchiefs (Bronson 1986: 1). The properties of South Indian steel, whichbecame synonymous with Damascus steel, wereinvestigated during the nineteenth and twentieth centuries by numerous European scientists, chemists and metallurgists with the aim of reproducing it on an industrial scale (Smith 1960: 25-9).