PATENT OFFICE 2,21,348 METHOD of MAKERNG GASSINE PAPER Robert F
Total Page:16
File Type:pdf, Size:1020Kb
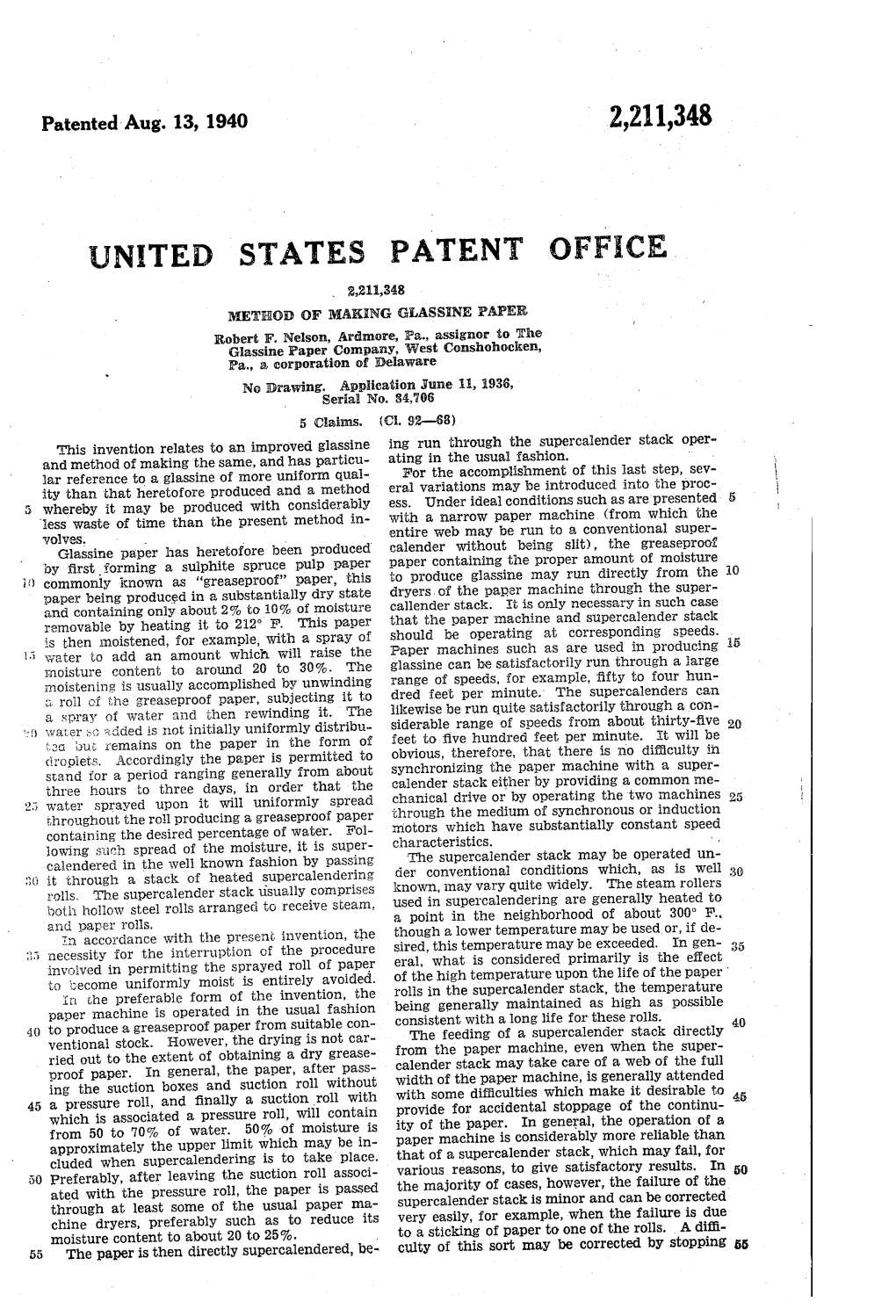
Load more
Recommended publications
-
Tariff Schedules of the United States Alphabetical Index
TARIFF SCHEDULES OF THE UNITED STATES ALPHABETICAL INDEX 447 TARIFF SCHEDULES OF THE UNITED STATES 449 References to References to Tariff Schedules Tariff Schedules A ABACA 30U.02-0U ACID(S) —Continued ABRASIVES AND ABRASIVE ARTICEES Sch 5 Ft IG fatty, of animal or vegetable origin—Con. abrasive wheels mounted on frameworks, salts of— hand or pedal operated 6i<9.39 quaternary ammonium 1+65.15-20 nspf 519.81-86 sodium and potassium 1+65.25-30 ACCESSORIES (see PARTS, specific article of other 1+90.30-50 which accessory, or name of accessory) gluconic, and its compounds 1+37-51-52 ACCORDIONS 725.1U-16 glycerophosphoric, and its compounds 1+37.51+ ACCOUNTING MACHINES incorporating calculating inorganic 1+16.05-1+0 mechanism 676.1S-25 organic, including halogenated, hydroxy, ACENAPHTHENE li01.02 sulfonated and other substituted and ACETALDEHIDE U27.U0 unsubstituted acids 1+25-70-98 ACETALS ii29.00 monohydric alcohol esters of 1+28+50-72 ACETANILIDE— polyhydric alcohol esters of 1+28.30-1+6 suitable for medicinal use U07.02 salts of I+26.IO-I+27.28 other k03.60 salicylic— ACETATE(S) — suitable for medicinal use 1+07.12 amyl lt28.SO other 1+03-60 benzyl 1+08.05 tannic, containing of tannic acid— butyl 1+28.52 under 50 percent 1+25.98 calcium 1+26.10 50 percent or more 1+37-68-69 cellulose 1+1+5.20 ACONITE 1+35-05-10 copper 1+26.28 ACRIDINE 1+01.01+ ethyl 1+28.58 ACRTLATES AND METHACRTLATES 1+28.62-66 lead 1+26.36 ACRYIIC RESINS 1+1+5.05 nickel 1+26.58 ACRTLONITRILE— 1+25.00 sodium 1+26.86 resins l+i+5.10 vinyl 1+28.68 ACTIVATED CLAY 521.87 Other -
Tate Report 08-09
Tate Report 08–09 Report Tate Tate Report 08–09 It is the Itexceptional is the exceptional generosity generosity and and If you wouldIf you like would to find like toout find more out about more about PublishedPublished 2009 by 2009 by vision ofvision individuals, of individuals, corporations, corporations, how youhow can youbecome can becomeinvolved involved and help and help order of orderthe Tate of the Trustees Tate Trustees by Tate by Tate numerousnumerous private foundationsprivate foundations support supportTate, please Tate, contact please contactus at: us at: Publishing,Publishing, a division a divisionof Tate Enterprisesof Tate Enterprises and public-sectorand public-sector bodies that bodies has that has Ltd, Millbank,Ltd, Millbank, London LondonSW1P 4RG SW1P 4RG helped Tatehelped to becomeTate to becomewhat it iswhat it is DevelopmentDevelopment Office Office www.tate.org.uk/publishingwww.tate.org.uk/publishing today andtoday enabled and enabled us to: us to: Tate Tate MillbankMillbank © Tate 2009© Tate 2009 Offer innovative,Offer innovative, landmark landmark exhibitions exhibitions London LondonSW1P 4RG SW1P 4RG ISBN 978ISBN 1 85437 978 1916 85437 0 916 0 and Collectionand Collection displays displays Tel 020 7887Tel 020 4900 7887 4900 A catalogue record for this book is Fax 020 Fax7887 020 8738 7887 8738 A catalogue record for this book is available from the British Library. DevelopDevelop imaginative imaginative education education and and available from the British Library. interpretationinterpretation programmes programmes AmericanAmerican Patrons Patronsof Tate of Tate Every effortEvery has effort been has made been to made locate to the locate the 520 West520 27 West Street 27 Unit Street 404 Unit 404 copyrightcopyright owners ownersof images of includedimages included in in StrengthenStrengthen and extend and theextend range the of range our of our New York,New NY York, 10001 NY 10001 this reportthis and report to meet and totheir meet requirements. -
Tensile Properties of Paper and Paperboard (Using Constant Rate of Elongation Apparatus) (Revision of T 494 Om-01)
WI 050808.09 T 494 DRAFT NO. 2 DATE June 13, 2006 TAPPI WORKING GROUP CHAIRMAN D Muchorski SUBJECT CATEGORY Physical Properties RELATED METHODS See “Additional Information” CAUTION: This Test Method may include safety precautions which are believed to be appropriate at the time of publication of the method. The intent of these is to alert the user of the method to safety issues related to such use. The user is responsible for determining that the safety precautions are complete and are appropriate to their use of the method, and for ensuring that suitable safety practices have not changed since publication of the method. This method may require the use, disposal, or both, of chemicals which may present serious health hazards to humans. Procedures for the handling of such substances are set forth on Material Safety Data Sheets which must be developed by all manufacturers and importers of potentially hazardous chemicals and maintained by all distributors of potentially hazardous chemicals. Prior to the use of this method, the user must determine whether any of the chemicals to be used or disposed of are potentially hazardous and, if so, must follow strictly the procedures specified by both the manufacturer, as well as local, state, and federal authorities for safe use and disposal of these chemicals. Tensile properties of paper and paperboard (using constant rate of elongation apparatus) (Revision of T 494 om-01) (Underlines indicated changes/corrections since last draft) 1. Scope 1.1 This test method describes the procedure, using constant-rate-of-elongation equipment, for determining four tensile breaking properties of paper and paperboard: tensile strength, stretch, tensile energy absorption, and tensile stiffness. -
Final Paper Products Recovered Materials Advisory Notice Response to Public Comments
FINAL PAPER PRODUCTS RECOVERED MATERIALS ADVISORY NOTICE Response to Public Comments Office of Solid Waste U.S. Environmental Protection Agency April 1996 CONTENTS I. Introduction . 1 A. The Draft Paper Products Recovered Materials Advisory Notice . 1 B. Overview of the RCRA Requirements . 1 C. Overview of the Executive Order Provisions for Paper . 3 II. Applicability . 5 A. Background. 5 B. Comments and Agency Response. 5 III. EPA's Objectives . 7 A. Background. 7 B. Comments and Agency Response. 7 IV. EPA's Approach to Recommendations. 11 A. Background . 11 B. Comments and Agency Response . 11 V. EPA's Methodology . 14 A. Background . 14 B. Comments and Agency Response . 14 VI. Recommendations for Printing and Writing Papers. 15 A. Background . 15 B. Comments and Agency Response . 19 VII. Recommendations for Newsprint . 27 A. Background . 27 B. Comments and Agency Response . 27 VIII. Recommendations for Tissue Products. 31 A. Background . 31 B. Comments and Agency Response . 32 IX. Recommendations for Paperboard and Packaging Products . 36 A. Background . 36 B. Comments and Agency Response . 38 X. Recommendations for Miscellaneous Paper Products. 45 A. Background . 45 B. Comments and Agency Response . 45 XI. Recommendations for Measurement. 46 A. Background . 46 B. Comments and Agency Response . 46 XII. Recommendations for Specifications. 48 A. Background . 48 B. Comments and Agency Response . 48 XIII. Recommendations for Recyclability. 49 A. Background . 49 B. Comments and Agency Response . 49 XIV. Definitions . 51 A. Background . 51 B. Comments and Agency Response . 51 XV. Certification and Verification . 54 A. Background . 55 B. Comments and Agency Response . 55 XVI. Sawdust as Recovered Fiber. -
Articles of Paper Pulp, of Paper Or of Paperboard
Chapter 48 Paper and paperboard; articles of paper pulp, of paper or of paperboard Notes. 1.- For the purposes of this Chapter, except where the context otherwise requires, a reference to “paper” includes references to paperboard (irrespective of thickness or weight per m²). 2.- This Chapter does not cover : (a) Articles of Chapter 30; (b) Stamping foils of heading 32.12; (c) Perfumed papers or papers impregnated or coated with cosmetics (Chapter 33); (d) Paper or cellulose wadding impregnated, coated or covered with soap or detergent (heading 34.01), or with polishes, creams or similar preparations (heading 34.05); (e) Sensitised paper or paperboard of headings 37.01 to 37.04; (f) Paper impregnated with diagnostic or laboratory reagents (heading 38.22); (g) Paper-reinforced stratified sheeting of plastics, or one layer of paper or paperboard coated or covered with a layer of plastics, the latter constituting more than half the total thickness, or articles of such materials, other than wall coverings of heading 48.14 (Chapter 39); (h) Articles of heading 42.02 (for example, travel goods); (ij) Articles of Chapter 46 (manufactures of plaiting material); (k) Paper yarn or textile articles of paper yarn (Section XI); (l) Articles of Chapter 64 or Chapter 65; (m) Abrasive paper or paperboard (heading 68.05) or paper- or paperboard-backed mica (heading 68.14) (paper and paperboard coated with mica powder are, however, to be classified in this Chapter); (n) Metal foil backed with paper or paperboard (generally Section XIV or XV); (o) Articles of heading 92.09; (p) Articles of Chapter 95 (for example, toys, games, sports requisites); or (q) Articles of Chapter 96 (for example, buttons, sanitary towels (pads) and tampons, napkins (diapers) and napkin liners for babies). -
Label Liners: Meeting the Sustainability Challenge
Label liners: meeting the sustainability challenge By Mariya Nedelcheva, Product Manager Film & With ever-greater emphasis placed on packaging and waste reduction, Jenny Wassenaar, Compliance & Sustainability brand owners are looking for solutions that secure their sustainability Director, Avery Dennison credentials. Consumers pay particularly close attention to packaging, where there are significant environmental gains to be made. For example, waste from labelling can create useful by-products and circular economies. Waste is not always visible on the final packaging, but its impact on brand reputation is no less real. Consumers’ perceptions of a brand can be enhanced when sustainability is improved. label.averydennison.com Matrix Liner Final White paper waste waste label 16% 35% 37% Start-up waste plus Challenge printed End-user The challenge of recycling waste from the labelling process in error scrap - and ideally creating useful by-products - is complex. Many 10% 1% different elements must be addressed in order to move towards the ultimate goal of zero waste. For example, the word ‘recyclable’ can mean many things, and should not be viewed in isolation. Today there is a chance that recyclable products will still end up in landfill, so what matters is establishing genuinely viable end-to-end recycling solutions. That means considering every component within packaging, including where it comes from, how much material has been used, and what happens at every stage of the package’s journey through the value chain. This paper discusses how the sustainability of labelling laminates can be improved, with a particular focus on the label release liners that are left behind once labels have been dispensed. -
Improved Oil Resistance of Cellulose Packaging Paper By
1 Improved Oil Resistance of Cellulose Packaging Paper by 2 Coating with Natural Polymer Derived Materials 3 Feijie Wang1, Liqiang Wang1,*, Xinchang Zhang1, Shufeng Ma2 4 1 Jiangsu Provincial Key Laboratory of Food Advanced Manufacturing Equipment 5 Technology, School of Mechanical Engineering, Jiangnan University, Wuxi, 214122, 6 China 7 2 School of Food Engineering, Jiangnan University, Wuxi, 214122, China 8 *Email: [email protected] 9 10 Abstract: Paper is widely used as food packaging due to its good mechanical strength 11 and degradability. However, it has a relatively strong affinity for water and oil, which 12 limits its application scope. In this work, we prepare two types of coated paper to 13 investigate, the influence the air permeability and polarity on the oil resistance of the 14 coated paper. The results showed that reducing the air permeability improved the grease 15 resistance of the coated paper. High surface energy coatings also showed better oil 16 resistance because of their higher content of polar components that resulted in a higher 17 resistance to grease. The mechanical properties of the paper also improved after 18 applying the coating. These natural derived materials offer an alternative to the fluoride- 19 containing materials currently used in the market to improve the wettability of paper. 20 Keywords: coated paper · oil resistance · air permeability · polarity 21 Introduction 22 As the variety of foods containing grease is abundant, the types of oil-resistant 23 materials used in food packaging has diversified in recent years. Environmental 24 protection and safety issues continue to be important, and as a result, scholars have paid 25 increasing attention to paper packaging materials (Coltelli et al. -
Crumpling Feasibility of Flexible Paper Sheets. Application to Packaging in the Food Industry Serge Rohmer1, Alexis Mérat1
KES Transactions on Sustainable Design and Manufacturing I Sustainable Design and Manufacturing 2014 : pp.26-37 : Paper sdm14-028 Crumpling feasibility of flexible paper sheets. Application to packaging in the food industry Serge Rohmer1, Alexis Mérat1 1University of Technology of Troyes, CS42060, Troyes, 10004, France [email protected] [email protected] Abstract Flexible packages are considered as the most-reduced form of packaging in terms of environmental performances. In order to contribute to their development, this paper proposes to explore some mechanical properties brought by a new folding process that confers elasticity to flexible materials and consequently new environmental advantages. The innovative folding process consists in sequences of crumpling actions transforming a 2D sheet into a dynamic 3D flexible structure, without cutting or gluing actions. In order to prove the efficiency of the crumpling process, a methodology is proposed to evaluate the ability of a material to be crumpled. The procedure is then applied on different types of papers used in the food industry, and a study case of a crumpled packaging highlights new innovative functionalities as well as its potential environmental gain. 1. Introduction Sustainability is gradually becoming a worldwide challenge for companies, they are conscious of the growing importance of taking into account environmental considerations in their development strategies. The directives and certification schemes adopted by public authorities [1-3] oblige industries and the packaging sector in particular to face the environmental challenge by developing new strategies and new products. Some propose their own certification to demonstrate their commitment to sustainable packaging. United Parcel Service company (UPS) proposes for example its own certification in its Eco Responsible Packaging Program for business customers [4]. -
Industry Review Semiannual Patent Review July-December 1998
Industry Review Semiannual Patent Review July-December 1998 Matthew Stroika, Marguerite Sykes, and Julie Blankenburg KEYWORDS PROCESSES Chemicals, Deinking, Enzyme, Patent, Recycling, Deinking Review, Waste paper. Many advances in deinking have recently been made to keep up with changing toner formulations INTRODUCTION and the high volume of computer-generated recov- ered paper present in today’s recycled furnish. This review summarizes patents related to paper Westvaco Corp. (1) is the assignee of a deinking recycling issued during the last 6 months of 1998. process for laser printed and photocopy printed pa- The two online databases used for this search are pers. Magnetite and an agglomerating chemical are Claim/US. Patents Abstracts and Derwent World added in the pulper. A portion of the agglomerat- Patents Index. This semiannual feature is intended ing agent can be replaced with a copolymer of sty- to inform readers about the latest developments in rene and acrylic monomers to further enhance the equipment, chemicals, and technology in the field ink removal. The pulp slurry is subsequently sub- of paper recycling. This review contains only brief jected to a magnetic field to remove the agglomer- summaries of the inventions. Readers will need to ated ink particles. This process can be used singly access the full texts of specific patents for complete or in combination with conventional flotation and information. washing. We have organized this review into the following Shell Oil has been granted a pair of related pat- broad categories of recycling: Processes, Equipment, ents (2,3) for deinking chemicals for office recov- Products, Chemicals, and Biological Treatments. -
Built-In Oven HEN201S2Z
Built-in oven HEN201S2Z [en] Instruction manual Table of contents[en]Instruction manual Important safety information.....................................................3 E number and FD number ............................................................. 11 Causes of damage .............................................................................5 Energy and environment tips..................................................11 Your new oven............................................................................5 Saving energy...................................................................................11 Control panel .......................................................................................5 Environmentally-friendly disposal.................................................. 11 Function selector.................................................................................5 Measures to be noted during transport....................................... 12 Temperature selector .........................................................................6 Tested for you in our cooking studio .....................................12 Hotplate controls.................................................................................6 Cakes and pastries ......................................................................... 12 Cooking compartment .......................................................................6 Baking tips ........................................................................................13 Your -
Making a Pinhole Camera
Homework – Autumn 11 Making a Pinhole Camera Your task this week is to make a pinhole camera. You will need to do the following: Ensure you have the correct materials to make your camera (see below) Follow the step-by-step guide carefully. Take a photo of your finished creation for us to see. You DO NOT need to bring in your camera to school. Write a paragraph about the process of making your camera. You will need to include: o What materials you used. o Were the instructions easy to follow? o Was it a success? Were you able to create an image? o Would you do anything differently? -------------------------------------------------------------------------------------------------- ----------------------------------------------------------- What is a pinhole camera? The word “camera” comes from camera obscura, which simply means “dark chamber”. A pinhole camera is one of the most basic examples of this concept. Pinhole cameras are made from a lightproof box, some photographic paper and a tiny hole (often made with a pin, hence the name). The pinhole is just an aperture, not a true lens, but because it is so small it will still focus on an image on the opposite side of the box, exposing the photo paper placed there. How to make a pinhole camera You will need: A box with a lid – You can make your own or use a shoebox or similar, but then the lid is on it must not let any light inside. You could also use a wide cardboard tube instead. A roll of aluminium foil or sheet of black paper. Sticky tape. Scissors. A needle or drawing pin. -
Pfass and Alternatives in Food Packaging (Paper and Paperboard): Report on the Commercial Availability and Current Uses
PFASs and alternatives in food packaging (paper and paperboard): Report on the commercial availability and current uses Series on Risk Management No. 58 1 Series on Risk Management 0 No. 58 PFASs and Alternatives in Food Packaging (Paper and Paperboard) Report on the Commercial Availability and Current Uses PUBE Please cite this publication as: OECD (2020), PFASs and Alternatives in Food Packaging (Paper and Paperboard) Report on the Commercial Availability and Current Uses, OECD Series on Risk Management, No. 58, Environment, Health and Safety, Environment Directorate, OECD. Acknowledgements: The OECD would like to acknowledge the drafting of a consultancy report by Steve Hollins of Exponent International Ltd. upon which this report is based. It was prepared under the framework of the OECD/UNEP Global PFC Group and included the contribution of information by several organisations (see Annex A). The report is published under the responsibility of the OECD Joint Meeting of the Chemicals Committee and the Working Party on Chemicals, Pesticides and Biotechnology. © Photo credits: Cover: Yuriy Golub/Shutterstock.com © OECD 2020 Applications for permission to reproduce or translate all or part of this material should be made to: Head of Publications Service, [email protected], OECD, 2 rue André-Pascal, 75775 Paris Cedex 16, France ABOUT THE OECD 3 About the OECD The Organisation for Economic Co-operation and Development (OECD) is an intergovernmental organisation in which representatives of 36 industrialised countries in North and South America, Europe and the Asia and Pacific region, as well as the European Commission, meet to co-ordinate and harmonise policies, discuss issues of mutual concern, and work together to respond to international problems.