Corrugated Fiber Board As a Packaging Material: Experimental and Numerical Analysis of the Mechanical Behavior
Total Page:16
File Type:pdf, Size:1020Kb
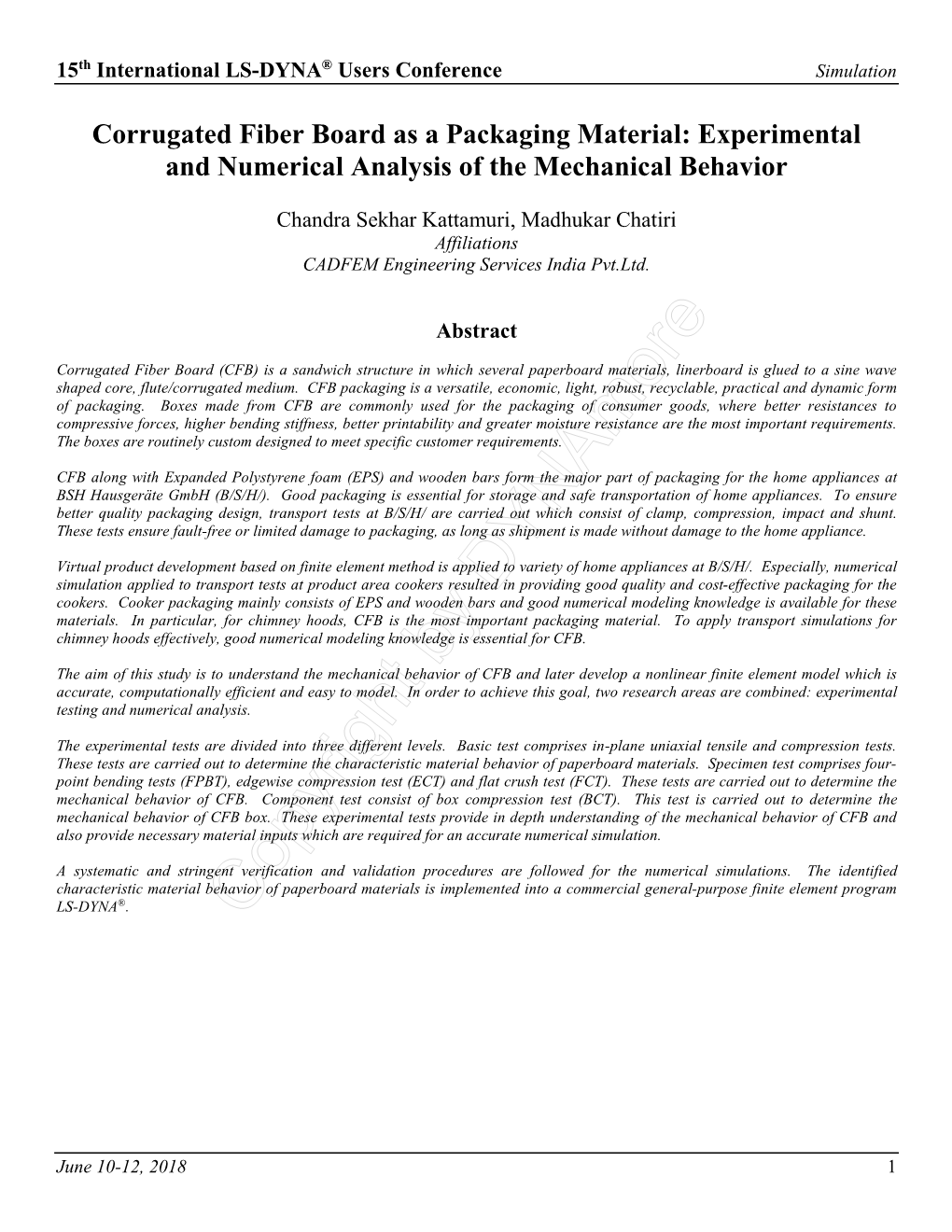
Load more
Recommended publications
-
Effects of Moisture on the Biaxial Strength of Wood-Based Composites
EFFECTS OF MOISTURE ON THE BIAXIAL STRENGTH OF WOOD-BASEDCOMPOSITES J. C. Suhling* J.M. Considine ** K. C. Yeh* * Department of Mechanical Engineering Auburn University Auburn, AL36849-5341 ** U.S.D.A. Forest Products Laboratory One Gifford Pinchot Drive Madison,WI 53705-2398 ABSTRACT applications such as corrugated containers where it is subjected to complicated biaxial stress states, In the present work, the effects of moisture on including shear. At present, lack of accurate the biaxial strength of wood-based composite materials constitutive relations and reliable strength has been examined. Experiments have been performed on predictions under biaxial loading and variable paperboard to measure the uniaxial and biaxial input environments hampers analysis of such problems. parameters of the tensor polynomial criterion at Therefore, it has been common practice in the paper several levels of relative humidity. With these data, industry to use trial and error, and empirical the dependence of the zero shear biaxial failure approaches for optimizing the designs of paperboard envelope on humidity level has been predicted and products. The current lack of technology limits trends have been observed. creative design improvements which could curtail the excess use of materials and energy. Accurate predictions of material strength under 1. INTRODUCTION general biaxial normal loading plus shear are needed by the design engineer when considering typical Unlike laminated fiber-reinforced composite structural applications of paperboard. Examples of materials, paper (paperboard) is a multiphase important current applications where biaxial stress composite composed of moisture, fibers, voids, and states exist in paperboard include the quality control possibly chemical additives. The fibers in paperboard burst test (bulged plate), material handling are typically organic with cellulose fibers from wood operations during the papermaking process, and stacked being the chief material. -
Cardboard and Brown Paper Bags Office Paper, Newspaper, Junk Mail, Magazines, and Catalogs
Recycling Center 801 Diamond Valley Drive Open: Daily to the public during daylight hours This guide will help you properly prepare your recyclable materials for drop-off at the Town of Windsor Recycle Center. This is a drop-off facility. It does not have a buy-back option and is for use by residents and small businesses. Following this information will help maintain the facility and the recycling program for the benefit of the community. IMPORTANT… • Do not leave your recyclables in plastic bags. Plastic bags are NOT recyclable! • The plastic item must be a BOTTLE or JAR. with a #1 or #2 on the bottom. • 99 percent of these will have a screw-on plastic lid (which isn’t recyclable). • Plastic containers with a #3 - #7 on the bottom are NOT acceptable. • Tubs, buckets, deli plates, microwave/fast food trays, wrappers, Styrofoam, toys, patio furniture, etc. are NOT acceptable. • Plastic bottles larger than 2.5 gallons are NOT acceptable. • Syringes and other medical supplies are NOT acceptable. Cardboard and Brown Paper Bags Corrugated cardboard is easy to recognize. It is made of paper and has an arched layer called “fluting” between smooth sheets called “liners”. The drop-off site has two 40-yard hydraulic compactor units for collecting corrugated cardboard and brown paper bags. The compaction system is self-activated by depositing the prepared materials into a six-inch tall slot. Flatten boxes. Cut or tear large boxes into sections no larger than 4 feet by 4 feet to prevent jamming the machine. No wet, waxed-coated or food-contaminated boxes. -
Wood Research Manufacture of Medium Density Fiberboard (Mdf) Panels from Agribased Lignocellulosic Biomass
WOOD RESEARCH 62 (4): 2017 615-624 MANUFACTURE OF MEDIUM DENSITY FIBERBOARD (MDF) PANELS FROM AGRIBASED LIGNOCELLULOSIC BIOMASS Mehmet Akgül Necmettin Erbakan University, Seydisehirahmet Cengiz Faculty of Engineering Department of Materials and Metallurgical Engineering Konya, Turkey Birol Uner Suleyman Demirel University, Faculty of Forestry Department of Forest Products Engineering Isparta Turkey Osman Çamlibel Kirikkale University, Kirikkale Vocational School, Department of Materials and Materials Processing Technology Yahsihan/Kirikkale, Turkey Ümit Ayata Atatürk Üniversity, Oltu Vocational School, Department of Forestry and Forest Products Oltu/Erzurum, Turkey (Received January 2016) ABSTRACTS Lignocellulosics fibers and commercially-manufactured-chip (Pinus sylvestris L., Fagus orientalis and Quercus robur L.) with 11% moisture conten twere used for the experiment. The mixingratios of lignocellulosics fibers was 20% which is from okra and tobaccos talks, hazelnut and walnuts hell, and pinecone for each mixture in preformed panel and commercially- manufactured-chip was 100 % for the control sample. A commercial ureaformaldehyde (UF) adhesive was used as a binder. The physical and mechanical properties such as density, thickness swelling (TS), bending strength (BS), modulus elasticity (MOE), internalbond (IB), screw holding ability (SHA) perpendicular to the plane of panel, Janka hardness perpendicular to the plane of panel properties of MDF were measured.The results indicated that all the panels met the general purpose-use requirements of TS-EN. Thus, our results suggest that biomass from different sources can be an alternative raw material for MDF manufacturing process. KEYWORDS: Lignocellulosic biomass, MDF, physical and mechanical properties. 615 WOOD RESEARCH INTRODUCTION The demand in forest products industry is increasing with population and new product development. -
The EMA Guide to Envelopes and Mailing
The EMA Guide to Envelopes & Mailing 1 Table of Contents I. History of the Envelope An Overview of Envelope Beginnings II. Introduction to the Envelope Envelope Construction and Types III. Standard Sizes and How They Originated The Beginning of Size Standardization IV. Envelope Construction, Seams and Flaps 1. Seam Construction 2. Glues and Flaps V. Selecting the Right Materials 1. Paper & Other Substrates 2. Window Film 3. Gums/Adhesives 4. Inks 5. Envelope Storage 6. Envelope Materials and the Environment 7. The Paper Industry and the Environment VI. Talking with an Envelope Manufacturer How to Get the Best Finished Product VII. Working with the Postal Service Finding the Information You Need VIII. Final Thoughts IX. Glossary of Terms 2 Forward – The EMA Guide to Envelopes & Mailing The envelope is only a folded piece of paper yet it is an important part of our national communications system. The power of the envelope is the power to touch someone else in a very personal way. The envelope has been used to convey important messages of national interest or just to say “hello.” It may contain a greeting card sent to a friend or relative, a bill or other important notice. The envelope never bothers you during the dinner hour nor does it shout at you in the middle of a television program. The envelope is a silent messenger – a very personal way to tell someone you care or get them interested in your product or service. Many people purchase envelopes over the counter and have never stopped to think about everything that goes into the production of an envelope. -
FAQ About Recycling Cartons
FREQUENTLY ASKED QUESTIONS ABOUT CARTONS WHAT IS A CARTON? » Cartons are a type of packaging for food and beverage products you can purchase at the store. They are easy to recognize and are available in two types—shelf-stable and refrigerated. Shelf-stable cartons (types of products) Refrigerated (types of products) » Juice » Milk » Milk » Juice » Soy Milk » Cream » Soup and broth » Egg substitutes » Wine You will find these You will find these products in the chilled products on the shelves sections of grocery stores. in grocery stores. WHAT ARE CARTONS MADE FROM? » Cartons are mainly made from paper in the form of paperboard, as well as thin layers of polyethylene (plastic) and/or aluminum. Shelf-stable cartons contain on average 74% paper, 22% polyethylene and 4% aluminum. Refrigerated cartons contain about 80% paper and 20% polyethylene. ARE CARTONS RECYCLABLE? » Yes! Cartons are recyclable. In fact, the paper fiber contained in cartons is extremely valuable and useful to make new products. WHERE CAN I RECYCLE CARTONS? » To learn if your community accepts cartons for recycling, please visit RecycleCartons.com or check with your local recycling program. HOW DO I RECYCLE CARTONS? » Simply place the cartons in your recycle bin. If your recycling program collects materials as “single- stream,” you may place your cartons in your bin with all the other recyclables. If your recycling program collects materials as “dual-stream” (paper items together and plastic, metal and glass together), please place cartons with your plastic, metal and glass containers. WAIT, YOU JUST SAID CARTONS ARE MADE MAINLY FROM PAPER. Don’t I WANT TO PUT THEM WITH OTHER PAPER RECYCLABLES? » Good question. -
Glulam Sizes and Shapes Can Help Desigggners Meet Their Most Demanding Architectural and Structural Requirements Using Numerous Innovative Design Examples
WoodWorks Webinar “The Wood Products Council” is a Registered Provider with The Decem ber 11, 2013 AmericanInstituteofArchitectsContinuingEducationSystems(AIA/CES). Credit(s) earned on completion of this program will be reported to Glued Laminated Timber – An AIA/CES for AIA members. Certificates of Completion for both AIA Innovative and Versatile members and non-AIA members are available upon request. This p rog ra m is r egiste r ed wi th AIA/CES foocotr continu in gpoessoag professional Engineered Wood Composite education. As such, it does not include content that may be deemed or construed to be an approval or endorsement by the AIA of any Product material of construction or any method or manner of handling, using, distributing, or dealing in any material or product. Tom Williamson, P.E. Timber Engineering LLC QQp,,uestions related to specific materials, methods, and services will FASCE, FSEI be addressed at the conclusion of this presentation. Retired Vice President, APA FEtiVPAITCFormer Executive VP, AITC Learning Objectives 1. To illustrate how the flexibility of glulam sizes and shapes can help desigggners meet their most demanding architectural and structural requirements using numerous innovative design examples. Copyright Materials 2. To familiarize designers with how to properly select and specify glulam incorporating relevant industry standards and codes. This presentation is protected by US and 3. To provide design professionals with an overview of key design International Copyright laws. Reproduction, considerations that must be considered to ensure both the structural distribution, display and use of the presentation performance and long-term durability of glulam structures. without written permission of the speaker is 4. -
4 Ways to Reduce Secondary Packaging Costs by Replacing Pre-Printed Corrugated Boxes with Direct Carton Marking WHITE PAPER
4 Ways to Reduce Secondary Packaging Costs by Replacing Pre-Printed Corrugated Boxes with Direct Carton Marking WHITE PAPER 4 Ways to Reduce Secondary Packaging Costs by Replacing Pre-Printed Corrugated Boxes with Direct Carton Marking Introduction Virtually ubiquitous as the standard for secondary Instead, most shippers attempt to analyze their outbound packaging of products around the world, boxes made of order fulfillment data and stock keeping unit (SKU) profiles corrugated fiberboard are anything but standard when it to determine the carton dimension(s) their shipments comes to the variety of styles and sizes. Although regular most commonly require. Depending on this information, slotted containers (RSCs) are the most commonly used style operations may elect to maintain a pre-printed box of box, they are offered in more than 1,300 different sizes. inventory anywhere from five to 50 (or more) different carton sizes. That broad range of available sizes makes it possible for shippers to most closely match the internal box dimensions Offered as a more cost-effective alternative to stocking to the size of its contents. For financial reasons particularly pre-printed corrugated boxes, direct carton marking with the recent movement of parcel shippers from weight- employs high-resolution inkjet printers to imprint text, based to dimension and weight (DIM Weight) charges it graphics and barcodes directly onto each box as needed. makes the most sense to package items for shipment in This white paper explains how direct carton marking a box sized to minimize empty space inside the carton. technology works and outlines the four ways a shipper can Otherwise, to protect the product(s) inside from shock, reduce costs by replacing pre-printed boxes with direct vibration, compression or other factors, the empty space carton marking. -
Corrugated Board Structure: a Review M.C
ISSN: 2395-3594 IJAET International Journal of Application of Engineering and Technology Vol-2 No.-3 Corrugated Board Structure: A Review M.C. Kaushal1, V.K.Sirohiya2 and R.K.Rathore3 1 2 Assistant Prof. Mechanical Engineering Department, Gwalior Institute of Information Technology,Gwalior, Assistant Prof. Mechanical Engineering 3 Departments, Gwalior Engineering College, Gwalior, M. Tech students Maharanapratap College of Technology, Gwalior, [email protected] [email protected] [email protected] ABSTRACT Corrugated board is widely used in the packing industry. The main advantages are lightness, recyclability and low cost. This makes the material the best choice to produce containers devoted to the shipping of goods. Furthermore examples of structure design based on corrugated boards can be found in different fields. Structural analysis of paperboard components is a crucial topic in the design of containers. It is required to investigate their strength properties because they have to protect the goods contained from lateral crushing and compression loads due to stacking. However in this paper complete and detailed information are presented. Keywords: - corrugated boards, recyclability, compression loads. Smaller flutes offer printability advantages as well as I. INTRODUCTION structural advantages for retail packaging. Corrugated board is essentially a paper sandwich consisting of corrugated medium layered between inside II. HISTORY and outside linerboard. On the production side, corrugated In 1856 the first known corrugated material was patented is a sub-category of the paperboard industry, which is a for sweatband lining in top hats. During the following four sub-category of the paper industry, which is a sub-category decades other forms of corrugated material were used as of the forest products industry. -
Paper and Board Packaging Recyclability Guidelines
FOR THE FU IGN TU ES R D E PAPER AND BOARD PACKAGING RECYCLABILITY GUIDELINES PAPER AND BOARD PACKAGING RECYCLABILITY GUIDELINES Helping retailers and brands specify and design packaging that can be reprocessed in paper mills 2 PAPER AND BOARD PACKAGING RECYCLABILITY GUIDELINES 3 CONTENTS PAPER AND BOARD PACKAGING RECYCLABILITY GUIDELINES Paper is a sustainable, renewable and ecologically sound choice for packaging DE because almost all paper and board is recyclable. In practice, the recyclability of 4 Plastic SIG packaging products will be determined by composition and design, and the way N they are collected and presented for reprocessing. The vast majority of paper- based products are easily recyclable. 8 Coatings FO R Paper recycling in the UK is a success story, with over 80% of paper and board 9 Peelable Solutions T packaging recovered for recycling. Paper for Recycling (PfR) is collected primarily H for use in manufacturing processes and is used as an alternative to virgin materials e.g. wood pulp. When presented it should therefore be of adequate quality and 10 Varnishes and Curable Varnishes E Recyclability of paper-based packaging economically viable to use. F As society evolves, different applications are found for paper and board which 11 Adhesives U sometimes require changes to its functionality. This is often achieved by combining 11 Alternative Barriers T the fibre substrate with another material to form a composite multi-layer laminate, U providing properties such as water resistance or a gas barrier to extend product life. These changes provide challenges for recycling, and in many instances can R 97% 12 Paper Products 3% increase the costs of reprocessing and of waste disposal. -
Corrugated 101! ! !Corrugated Vs
Corrugated 101! ! !Corrugated vs. Cardboard! • The term "cardboard box" is commonly misused when referring to a corrugated box. The correct technical term is "corrugated fiberboard carton.”! • Cardboard boxes are really chipboard boxes, and used primarily for packaging lightweight products, such as cereal or board games.! • Corrugated fiberboard boxes are widely utilized in retail packaging, shipping cartons, product displays and many other applications ! requiring lightweight, but sturdy materials.! !Corrugated Composition! Corrugated fiberboard is comprised of linerboard and heavy paper medium. Linerboard is the flat, outer surface that adheres to the medium. The medium is the wavy, fluted paper between the liners. Both are made of a special kind of heavy paper called !containerboard. Board strength will vary depending on the various linerboard and medium combinations.! • Single Face: Medium glued to 1 linerboard; flutes exposed! • Single Wall: Medium between 2 liners! • Double Wall: Varying mediums layered between 3 liners! !• Triple Wall: Varying mediums layered between 4 liners! !Flute Facts! !Corrugated board can be created with several different flute profiles. The five most common flute profiles are:! • A-Flute: Original corrugated flute design. Contains about 33 flutes per foot.! • B-Flute: Developed primarily for packaging canned goods. Contains about 47 flutes per foot and measures 1/8" thick! • C-Flute: Commonly used for shipping cartons. Contains about 39 flutes per foot and measures 5/32" thick! • E-Flute: Contains about 90 flutes per foot and measures 1/16" thick! • F-Flute: Developed for small retail packaging. Contains about 125 flutes per foot and measures 1/32" thick! • Generally, larger flute profiles deliver greater vertical compression strength and cushioning. -
Manufacturing of Paperboard and Corrugated Board Packages
Lecture 9: Manufacturing of paperboard and corrugated board packages Converting operations: printing, die-cutting, folding, gluing, deep-drawing After lecture 9 you should be able to • describe the most important converting operations in paper and paperboard package manufacturing • discuss important runnability considerations in paperboard package handling • relate factors affecting runnability to pppaperboard app earance and pyphysical performance quality parameters 1 Literature • Pulp and Paper Chemistry and Technology - Volume 4, Paper Products Physics and Technology, Chapter 10 • Paperboard Reference Manual, p. 157-225 • Fundamentals of packaging technology Chapters 4, 6, 15 and 18 Paperboard Packaging Design is the result of • Personal creativity plus – Knowledge and understanding of packaging materials, including: • Structural properties • Graphic capabilities • Converting processes and converting properties • Customer packaging systems • Marketing objectives • Distribution requirements • Retail outlet expectations • Needs and desires of end user • How end user will use the product • Many people may contribute to the design 2 Overall, the design must provide: • Containment of product • Protection of product • Ease in handling through distribution • Prevention of product spoilage • Tamper evidence • Consumer convenience • Brand identification • Communications for the consumer: – Instructions for product use – Coding for quality assurance, expiration dates – Dietary and nutritional information The design should consider: 1. Converting -
Wood-Based Composite Materials Panel Products, Glued-Laminated Timber, Structural Composite Lumber, and Wood–Nonwood Composite Materials Nicole M
CHAPTER 11 Wood-Based Composite Materials Panel Products, Glued-Laminated Timber, Structural Composite Lumber, and Wood–Nonwood Composite Materials Nicole M. Stark, Research Chemical Engineer Zhiyong Cai, Supervisory Research Materials Engineer Charles Carll, Research Forest Products Technologist The term composite is being used in this chapter to describe Contents any wood material adhesively bonded together. Wood-based Scope 11–2 composites encompass a range of products, from fiberboard Conventional Wood-Based Composite Panels 11–2 to laminated beams. Wood-based composites are used for a number of nonstructural and structural applications in prod- Elements 11–2 uct lines ranging from panels for interior covering purposes Adhesives 11–3 to panels for exterior uses and in furniture and support struc- Additives 11–5 tures in buildings (Fig. 11–1). Maloney (1986) proposed Plywood 11–5 a classification system to logically categorize the array of wood-based composites. The classification in Table 11-1 Oriented Strandboard 11–7 reflects the latest product developments. Particleboard 11–10 The basic element for wood-based composites is the fiber, Fiberboard 11–12 with larger particles composed of many fibers. Elements Speciality Composite Materials 11–15 used in the production of wood-based composites can be Performance and Standards 11–15 made in a variety of sizes and shapes. Typical elements in- Glulam Timber 11–17 clude fibers, particles, flakes, veneers, laminates, or lumber. Figure 11–2 shows the variation and relative size of wood Advantages 11–17 elements. Element size and geometry largely dictate the Types of Glulam Combinations 11–17 product manufactured and product performance.