4%-44, 2444 F2
Total Page:16
File Type:pdf, Size:1020Kb
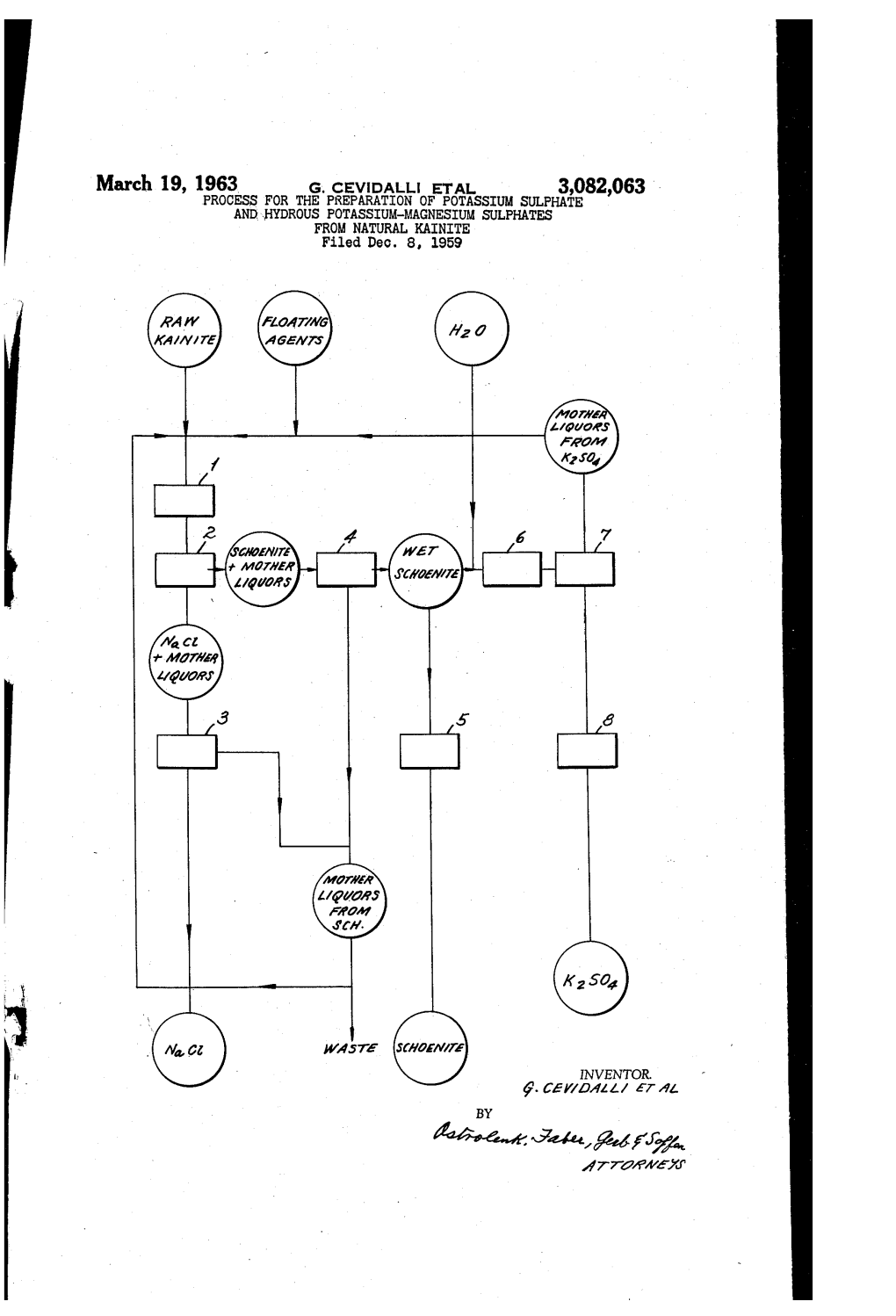
Load more
Recommended publications
-
S40645-019-0306-X.Pdf
Isaji et al. Progress in Earth and Planetary Science (2019) 6:60 Progress in Earth and https://doi.org/10.1186/s40645-019-0306-x Planetary Science RESEARCH ARTICLE Open Access Biomarker records and mineral compositions of the Messinian halite and K–Mg salts from Sicily Yuta Isaji1* , Toshihiro Yoshimura1, Junichiro Kuroda2, Yusuke Tamenori3, Francisco J. Jiménez-Espejo1,4, Stefano Lugli5, Vinicio Manzi6, Marco Roveri6, Hodaka Kawahata2 and Naohiko Ohkouchi1 Abstract The evaporites of the Realmonte salt mine (Sicily, Italy) are important archives recording the most extreme conditions of the Messinian Salinity Crisis (MSC). However, geochemical approach on these evaporitic sequences is scarce and little is known on the response of the biological community to drastically elevating salinity. In the present work, we investigated the depositional environments and the biological community of the shale–anhydrite–halite triplets and the K–Mg salt layer deposited during the peak of the MSC. Both hopanes and steranes are detected in the shale–anhydrite–halite triplets, suggesting the presence of eukaryotes and bacteria throughout their deposition. The K–Mg salt layer is composed of primary halites, diagenetic leonite, and primary and/or secondary kainite, which are interpreted to have precipitated from density-stratified water column with the halite-precipitating brine at the surface and the brine- precipitating K–Mg salts at the bottom. The presence of hopanes and a trace amount of steranes implicates that eukaryotes and bacteria were able to survive in the surface halite-precipitating brine even during the most extreme condition of the MSC. Keywords: Messinian Salinity Crisis, Evaporites, Kainite, μ-XRF, Biomarker Introduction hypersaline condition between 5.60 and 5.55 Ma (Manzi The Messinian Salinity Crisis (MSC) is one of the most et al. -
United States Patent (11) 3,615,174
United States Patent (11) 3,615,174 72 Inventor William J. Lewis 3,342,548 9/1967 Macey....... A. 2319 X South Ogden, Utah 3,432,031 3/1969 Ferris........................... 209/166 X 21 Appl. No. 740,886 FOREIGN PATENTS 22, Filed June 28, 1968 45 Patented Oct. 26, 1971 1,075,166 4f1954 France ......................... 209/66 (73) Assignee NL Industries, Inc. OTHER REFERENCES New York, N.Y. Chem. Abst., Vol. 53, 1959, 9587e I & EC, Vol. 56, 7, Jy '64, 61 & 62. Primary Examiner-Frank W. Lutter 54 PROCESSFOR THE SELECTIVE RECOVERY OF Assistant Examiner-Robert Halper POTASSUMAND MAGNESUMWALUES FROM Attorney-Ward, McElhannon, Brooks & Fitzpatrick AQUEOUSSALT SOLUTIONS CONTAINING THE SAME 11 Claims, 4 Drawing Figs. ABSTRACT: Kainite immersed in brine in equilibrium con 52) U.S. Cl........................................................ 23138, verted to carnalite by cooling to about 10 C. or under. Car 209/11, 209/166,23191, 22/121 nallite so obtained purified by cold flotation. Purified carnal (5) Int. Cl......................................................... B03b 1100, lite water leached to yield magnesium chloride brine and B03d 1102, C01f 5126 potassium chloride salt. Latter optionally converted to potas 50 Field of Search............................................ 209/166,3, sium sulfate by reaction with kainite, or by reacting the carnal 10, 11; 23.19, 38, 121 lite with kainite. Naturally occurring brine concentrated to precipitate principally sodium chloride, mother liquor warm 56 References Cited concentrated to precipitate kainite, cooled under mother UNITED STATES PATENTS liquor for conversion to carnallite. A crude kainite fraction 2,479,001 8/1949 Burke........................... 23.191 purified by warm flotation and a crude carnallite fraction pu 2,689,649 9, 1954 Atwood.... -
Crystallization of Kainite from Solutions in Syste
ineering ng & E P l r a o c i c e m s e s Journal of h T C e f c h o Kostiv and Basystiuk, J Chem Eng Process Technol 2016, 7:3 l ISSN: 2157-7048 n a o n l o r g u y o J Chemical Engineering & Process Technology DOI: 10.4172/2157-7048.1000298 Research Article Article OpenOpen Access Access + 2+ + - 2- Crystallization of Kainite from Solutions in System K , Mg , Na // Cl , SO4 -Н2О Kostiv IY1 and Yа І Basystiuk2* 1State Enterprise Scientific - Research Gallurgi Institute 5a, Fabrichna Str., 76000 Kalush, Ukraine 2Precarpathian National University named after V. Stephanyk 57, Shevchenko Str., 76025 Ivano-Frankivsk, Ukraine Abstract In isothermal conditions have been studied the influence of system solution sea salts during their evaporation and crystallization to composition of received liquid and solid phases. It is shown that evaporation of the solution leading 2- to its supersaturation by sulfate salts. In the liquid phase before crystallization of kainite concentration of SO4 ions increases to 10% and above. Through this probability of formation of crystals increases and the result of evaporation 2- is the formation of finely dispersed kainite. During crystallization of kainite concentration of SO4 in the liquid phase 2- 2+ decreases rapidly. Decreasing its intensity increases with increasing value k=E SO4 : E Mg of initial solution. For 2- the degree of evaporation of 20.0% and 31.0% concentration of SO4 in evaporated solution on the value of k does not change. Most forms of potassium salts in the solid phase for the value k=0.7573 and reaches a maximum value at 82% evaporation rate of 31%. -
Gases in Evaporites: Part 2 of 3: Nature, Distribution and Sources
www.saltworkconsultants.com Salty MattersJohn Warren - Wed., November 30, 2016 Gases in Evaporites: Part 2 of 3: Nature, distribution and sources This, the second of three articles on gases held within salt de- older and younger sets of gas analyses conducted over the years posits, focuses on the types of gases found in salt and their ori- in various salt deposits are not necessarily directly comparable. gins. The first article (Salty Matters October 31, 2016) dealt with Raman micro-spectroscopy is a modern, non-destructive meth- the impacts of intersecting gassy salt pockets during mining or od for investigating the unique content of a single inclusion in drilling operations. The third will discuss the distribution of the a salt crystal. There is a significant difference in terms of what is various gases with respect to broad patterns of salt mass shape measured in analysing gas content seeping from a fissure in a salt and structure (bedded, halokinetic and fractured) mass or if comparisons are made with conventional wet-chem- ical methods which were the pre Raman-microscopy method What’s the gas? that is sometimes still used. Wet chemical methods require sam- Gases held in evaporites are typically mixtures of varying propor- ple destruction, via crushing and subsequent dissolution, prior to tions of nitrogen, methane, carbon dioxide, hydrogen, hydrogen analysis. This can lead to the escape of a variable proportion of sulphide, as well as brines and minor amounts of Units dominated by Units dominated by Units with more or other gases such as argon inclusions from the N-O inclusions from less equal numbers CH -H -H S groups of both groups and various short chain and N2 groups 4 2 2 hydrocarbons (Table 2). -
Assessment of the Molecular Structure of the Borate Mineral Boracite
Spectrochimica Acta Part A: Molecular and Biomolecular Spectroscopy 96 (2012) 946–951 Contents lists available at SciVerse ScienceDirect Spectrochimica Acta Part A: Molecular and Biomolecular Spectroscopy journal homepage: www.elsevier.com/locate/saa Assessment of the molecular structure of the borate mineral boracite Mg3B7O13Cl using vibrational spectroscopy ⇑ Ray L. Frost a, , Yunfei Xi a, Ricardo Scholz b a School of Chemistry, Physics and Mechanical Engineering, Science and Engineering Faculty, Queensland University of Technology, G.P.O. Box 2434, Brisbane, Queensland 4001, Australia b Geology Department, School of Mines, Federal University of Ouro Preto, Campus Morro do Cruzeiro, Ouro Preto, MG 35400-00, Brazil highlights graphical abstract " Boracite is a magnesium borate mineral with formula: Mg3B7O13Cl. " The crystals belong to the orthorhombic – pyramidal crystal system. " The molecular structure of the mineral has been assessed. " Raman spectrum shows that some Cl anions have been replaced with OH units. article info abstract Article history: Boracite is a magnesium borate mineral with formula: Mg3B7O13Cl and occurs as blue green, colorless, Received 23 May 2012 gray, yellow to white crystals in the orthorhombic – pyramidal crystal system. An intense Raman band Received in revised form 2 July 2012 À1 at 1009 cm was assigned to the BO stretching vibration of the B7O13 units. Raman bands at 1121, Accepted 9 July 2012 1136, 1143 cmÀ1 are attributed to the in-plane bending vibrations of trigonal boron. Four sharp Raman Available online 13 August 2012 bands observed at 415, 494, 621 and 671 cmÀ1 are simply defined as trigonal and tetrahedral borate bending modes. The Raman spectrum clearly shows intense Raman bands at 3405 and 3494 cmÀ1, thus Keywords: indicating that some Cl anions have been replaced with OH units. -
Congolite and Trembathite from the Kłodawa Salt Mine, Central Poland: Records of the Thermal History of the Parental Salt Dome
1387 The Canadian Mineralogist Vol. 50, pp. 1387-1399 (2012) DOI : 10.3749/canmin.50.5.1387 CONGOLITE AND TREMBATHITE FROM THE KŁODAWA SALT MINE, CENTRAL POLAND: RECORDS OF THE THERMAL HISTORY OF THE PARENTAL SALT DOME JACEK WACHOWIAK§ AGH – University of Science and Technology, Department of Economic and Mining Geology; al. Mickiewicza 30, 30-059 Kraków, Poland ADAM PIECZKA AGH – University of Science and Technology, Department of Mineralogy, Petrography and Geochemistry; al. Mickiewicza 30, 30-059 Kraków, Poland ABSTRACT Pseudocubic crystals of (Fe,Mg,Mn)3B7O13Cl borate, ≤ 1.2 mm in size and yellowish through pale-violet to pale-violet- brown and brownish in color, were found in the Kłodawa salt dome, located within the Mid-Polish Trough (central Poland), an axial part of the Polish basin belonging to a system of Permian-Mesozoic epicontinental basins of Western and Central Europe. The crystals occur in adjacent parts of the Underlying Halite and Youngest Halite units bordering the Anhydrite Pegmatite unit around the PZ–3/PZ–4 (Leine/Aller) boundary. The internal texture of the crystals reflects phase-transitions from rhombohedral congolite (space-group symmetry R3c) through orthorhombic ericaite (Pca21) to a cubic, high-temperature, mainly Fe-dominant analogue of boracite (F43c), indicating formation of the phases under increasing temperature. Currently, the parts of the crystals showing orthorhombic and cubic morphology generally represent congolite and, much less frequently, trembathite paramorphs after higher-temperature structural varieties of (Fe,Mg,Mn)3B7O13Cl and (Mg,Fe,Mn)3B7O13Cl, which are unstable at room- temperature. The phase-transitions R3c → Pca21 and Pca21 → F43c recorded in the morphology of the growing crystals took place at temperatures of 230–250 °C and 310–315 °C, respectively, whereas the total range of (Fe,Mg,Mn)3B7O13Cl borate crystallization was determined to be ca. -
A Specific Gravity Index for Minerats
A SPECIFICGRAVITY INDEX FOR MINERATS c. A. MURSKyI ern R. M. THOMPSON, Un'fuersityof Bri.ti,sh Col,umb,in,Voncouver, Canad,a This work was undertaken in order to provide a practical, and as far as possible,a complete list of specific gravities of minerals. An accurate speciflc cravity determination can usually be made quickly and this information when combined with other physical properties commonly leads to rapid mineral identification. Early complete but now outdated specific gravity lists are those of Miers given in his mineralogy textbook (1902),and Spencer(M,i,n. Mag.,2!, pp. 382-865,I}ZZ). A more recent list by Hurlbut (Dana's Manuatr of M,i,neral,ogy,LgE2) is incomplete and others are limited to rock forming minerals,Trdger (Tabel,l,enntr-optischen Best'i,mmungd,er geste,i,nsb.ildend,en M,ineral,e, 1952) and Morey (Encycto- ped,iaof Cherni,cal,Technol,ogy, Vol. 12, 19b4). In his mineral identification tables, smith (rd,entifi,cati,onand. qual,itatioe cherai,cal,anal,ys'i,s of mineral,s,second edition, New york, 19bB) groups minerals on the basis of specificgravity but in each of the twelve groups the minerals are listed in order of decreasinghardness. The present work should not be regarded as an index of all known minerals as the specificgravities of many minerals are unknown or known only approximately and are omitted from the current list. The list, in order of increasing specific gravity, includes all minerals without regard to other physical properties or to chemical composition. The designation I or II after the name indicates that the mineral falls in the classesof minerals describedin Dana Systemof M'ineralogyEdition 7, volume I (Native elements, sulphides, oxides, etc.) or II (Halides, carbonates, etc.) (L944 and 1951). -
K2SO4 Across the Neogene: Implications, Part 4 of 4
www.saltworkconsultants.com Salty MattersJohn Warren - Tuesday, May 12, 2015 Danakil potash: K2SO4 across the Neogene: Implications, Part 4 of 4 marine brine feeds that most of the world’s larger Phaneorzo- How to deal with K2SO4 ic (SOP) potash ore deposits were precipitated (Warren, 2015). In this the fourth blog focusing on Danakhil potash, we look SOP is also produced from Quaternary Lake brines in China at the potash geology of formerly mined Neogene deposits in and Canada (see Cryogenic salt blog; 24 Feb. 2015). Sicily and the Ukraine, then compare them and relevant pro- cessing techniques used to exploit their K2SO4 ore feeds. This information is then used to hlep guide a discussion of process- ing implications for potash extraction in the Danakhil, where SOP in Messinian evaporites, Sicily kainite is the dominant widespread potash salt. As seen in the A number of potash mines on the island extracted kainitite from previous three blogs there are other potash mineral styles present the late Miocene Solofifera Series of Sicily (Figure 1). The last in the Danakhil, which constitute more re- stricted ore fairways than the widespread bedded kainaite, these other potash styles Sicilian-Maghrebian units (deep meteoiric -blog 2 of 4 and hydro- thermal - blog 3 of 4), could be processed Palermo X Kabylian-Calabrian units to extract MOP, but these other potash Calatami inner C styles are also tied to high levels of MgCl2, im Madonie M. in Petralia Nebrodi M. na b which must be dealt with in the brine pro- S. Ninfa asin Nicosia Be M. -
Conversion of Langbeinite and Kieserite in Schoenite With
ineering ng & E P l r a o c i c e m s e s Journal of h T C e f c h o Artus and Kostiv, J Chem Eng Process Technol 2015, 6:2 l ISSN: 2157-7048 n a o n l o r g u y o J Chemical Engineering & Process Technology DOI: 10.4172/2157-7048.1000225 Research Article Article OpenOpen Access Access Conversion of Langbeinite and Kieserite in Schoenite With Mirabilite and Sylvite in Water and Schoenite Solution Mariia Artus1* and Ivan Kostiv2 1Precarpathian National University named after V. Stephanyk 57, Shevchenko str., 76025 Ivano-Frankivsk, Ukraine 2State Enterprise Scientific-Research Gallurgi Institute 5a, Fabrychna str., 77300 Kalush, Ukraine Abstract The hydration of soluble Langbeinite and kieserite was investigated in the presence of potassium chloride and sodium sulfate. The addition of sodium sulfate affects water activity less than in the case of clean water. Therefore, we have conducted a research by adding water instead of schoenite solution. According to the results, hydration of Langbeinite by adding sodium sulfate in the first 240 hours occurs more intensively than without sodium sulfate with formation of a readily soluble schoenite and halite. Keywords: Langbeinite; Kieserite; Conversion ; Sodium sulfate; residue of hardly soluble langbeinite, kieserite and polyhalite, its drying Schoenite solution with obtaining potassium-magnesium concentrate, containing K2O - 20,4%, MgO – 16,0% and Cl - less than 1%. The solution after the Introduction stage of dissolution of ore is illuminated, evaporated, separated at first sodium chloride and then schoenite [5]. The polymineral potassium-magnesium ores contain both readily soluble minerals: kainite (KCl·MgSO4·3H2O), sylvite (KCl), halite During processing of kieserite hartzalts of Germany, containing (NaCl) as well as hardly soluble: langbeinite (K2SO4·2MgSO4), polyhalite 17-28% of kieserite, crushed ore is subjected to hot dissolution (K2SO4·MgSO4·2СаSO4·2H2O), kieserite (MgSO4·H2O). -
THE STABILITY of GYPSUM and ANHYDRITE in the GEOLOGIC ENVIRONMENT by Leonard S
THE STABILITY OF GYPSUM AND ANHYDRITE IN THE GEOLOGIC ENVIRONMENT by LEONARD STEVEN ROLNICK A.B., THE JOHNS HOPKINS UNIVERSITY (1950) SUBMITTED IN PARTIAL FULFILLMENT OF THE REQUIREMENTS FOR THE DEGREE OF DOCTOR OF PHILOSOPHY at the MASSACHUSETTS INSTITUTE OF TECHNOLOGY September, 1954 Signature of Author.......... .................... ...... *0 Department of Geology and G o s September 10, 1954 Certified by....e. .... .. e....sor Thesis Supervisor Accepted by......, .......... 0 e Chairman, Departmental Committee on raduate Students ~~~~1 THE STABILITY OF GYPSUM AND ANHYDRITE IN THE GEOLOGIC ENVIRONMENT by Leonard S. Rolnick Submitted to the Department of Geology and Geophysics on September 10, 1954, in partial fulfillment of the require- ments for the degree of Doctor of Philosophy In the CaSO-- H2 0 system, gypsum and anhydrite are the only two minerals that are sufficiently stable to exist as geologic deposits. From thermodynamic data and solubility measurements the transition temperature has previously been found to be about 4000, above which anhydrite is the stable phase and below which gypsum is the stable phase, when they are in contact with an aqueous solution at atmospheric pressure. By a process of solution and recrystallization, one can be converted to the other, after the surrounding liquid is saturated with calcium sulphate. Experimental work has been done in a study of the effects of pressure on this transition point, and the results corroborate and extend the theoretical calculations of MacDonald, which are based on thermodynamic data. This experimentally determined information was used in explaining some of the gypsum-anhydrite sequences found in geologic deposits. The experiments were conducted using high pressure bombs which contained samples of pure gypsum or anhydrite in a saturated calcium sulphate solution. -
Spectral Evolution Identifying Minerals Associated with Potash
spectral evolution Identifying Minerals Associated with Potash Potassium is a key ingredient in soil fertilizer that improves soil nutrient values, water retention and disease resistance in agricultural crops. Potash ore is the source for potas- sium in fertilizer and is associated with the minerals sylvite, carnallite, halite, kainite and anhydrite. Potash is mined from sub-surface deposits by conventional shaft mining techniques. Identifying minerals associated with potash is key for successful mining efforts. Sam- ples from a Canadian mine were scanned with an oreXpress field spectrometer with EZ -ID mineral identification software. Absorption features were noted at 529,678, 902, 1447, 1968, 2222, 2310 and 2480 nanometers. Using EZ-ID’s spectral match regions to Potash ore sample. match to three spectral libraries (USGS, SpecMIN, and GeoSPEC) the samples were identified as a mixture of hematite, carnallite, and halite. The oreXpress is a NIR mineral analyzer designed for field use. It is lightweight, rugged and reliable with no moving opti- cal parts. It can be equipped with a 3mm spot size or 10mm spot size contact probe, runs off lithium-ion batteries (2 batteries– 4 hours each) and fits in a backpack. The AGIZ 8X rugged tablet stores scans and tags them with photos from its built-in digital camera, voice notes EZ-ID mineral identification software and a scan of the potash ore. and GPS location. Running on a tablet or a PC, EZ-ID mineral identification software matches your target scans against three known libraries (USGS, SpecMIN, and GeoSPEC) of 1100 minerals and 2600 spectra. You can select different spectral match regions of key absorption fea- tures and generate a mineral identity for just those features— helping you to unmix complex samples. -
US2862788.Pdf
United States Patent Office Patented DC2,862,788 2, 1958 1. 2 potassium salts, such as kainite. In accordance with the instant invention, the liquor remaining following the re 2,862,788 moval of the mixed salts, which liquor will be termed "potassium sulfate reject liquor,” is treated in a manner PROCESS FOR PURIFYING IMPURE SOLID-PHASE to permit the recovery of magnesium values therefrom, KANTE but is also treated to recover a major proportion of Willian N. Stanley, Jr., and William B. Dancy, Carlsbad, the potassium values therefrom in the form of high N. Mex, assignors to International Minerais & Chem. grade potassium salts, such as leonite. In accordance ical Corporation, a corporation of New York with a specific embodiment of the instant invention, be O tween about 60% and about 70% of the potassium values Application May 3, 1955, serial No. 505,717 contained in potassium sulfate reject liquor are recovered as potassium sulfate. ..' . 4 Claims. (CI. 23-38) It is an object of the present invention to increase the overall recovery of potash values from langbeinite. The present invention relates to a process for the treat 5 It is another object of this invention to recover the ment of liquors to recover potassium values therefrom potassium values from kainite containing substantial and more particularly, to a process for recovering po amounts of sodium chloride. tassium and magnesium values from potassium sulfate It is a further object of this invention to provide a reject liquor. - - - - - - - - - - - - - process for recovering potash values from potassium sul In the past, processes have been developed involving 20 fate reject liquor.