Installation Guide
Total Page:16
File Type:pdf, Size:1020Kb
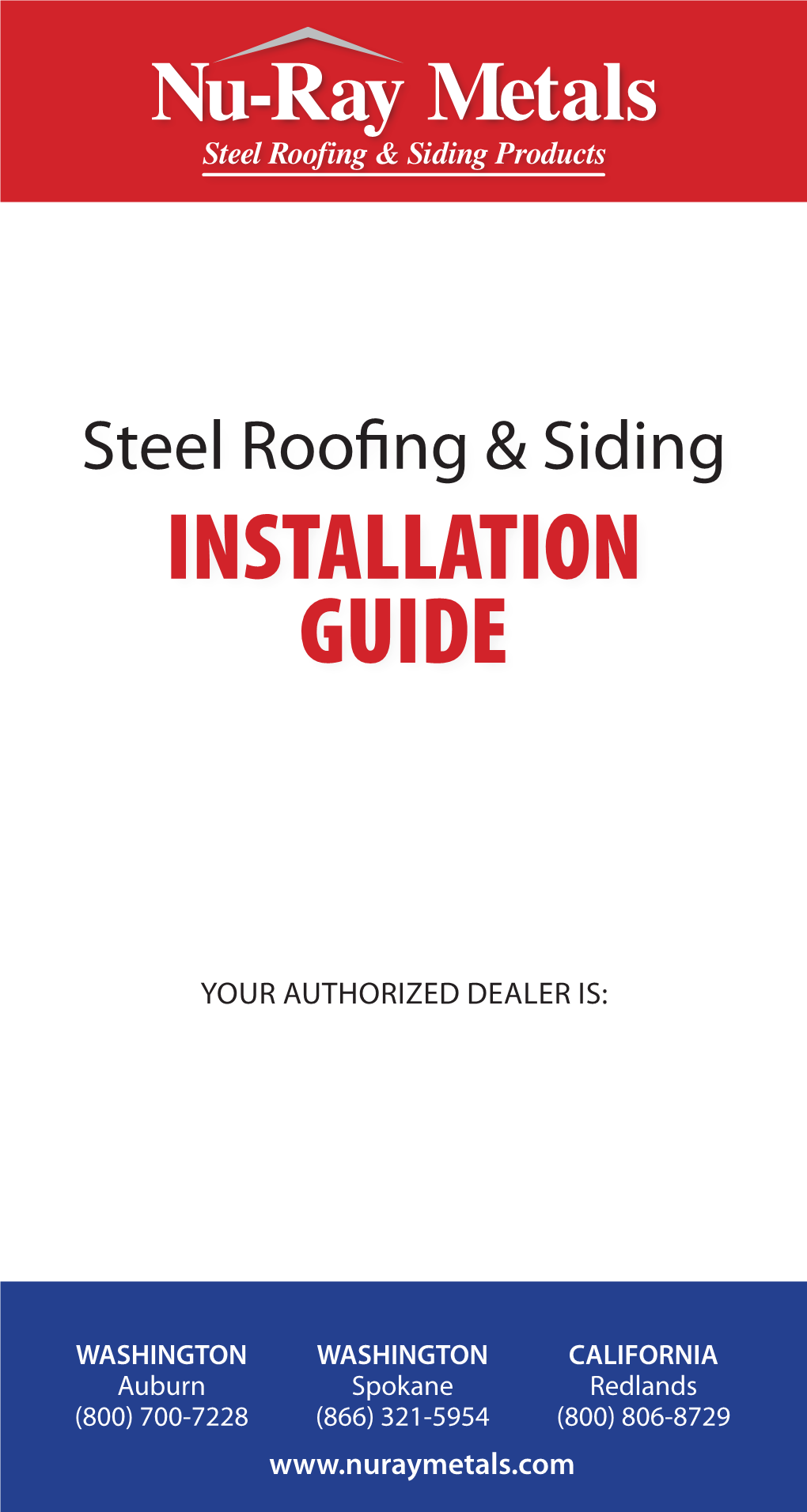
Load more
Recommended publications
-
Illuminator® Tube Skylight
Illuminator® Tube Skylight A new opportunity to help add profit and value. And make every job shine. The Owens Corning® Illuminator® Tube Skylight is a smart choice for bringing natural light into the home. It’s designed to prevent leaking and is covered by a Limited Lifetime Warranty.* This warranty offers the homeowner coverage against manufacturing defects for as long as they own their home. Natural lighting. Evenly distributes up to 500 watts† of clean, natural light, helping to reduce reliance on electricity. Excellent alternative to traditional skylights. The Illuminator® Tube Skylight is cost-effective, easier to install, and features seamless, one-piece flashing designed to prevent leaking. Also provides natural light where a traditional skylight is not an option. A solution for all — naturally. Models are available for nearly all types of roofing materials — including tile and metal — and for applications in severe weather zones, such as in HVHZ. Roof Dome The Owens Corning™ Illuminator® Tube Skylight Natural lighting. Naturally easy installation. The Illuminator® Tube Skylight is easy to install with no framing, Roof Flashing drywall or electrician required and can be installed during a re-roof process or new construction – typically in less than two hours. Just follow these four simple steps: 1. Once a location is determined, use included guide to mark and cut roof, secure flashing, and install top tubing and dome. 2. Inside the home, use included guide to mark and cut ceiling, feed bottom tubing into attic, and install trim ring. 3. In the attic, insert bottom tube into trim ring and connect to top tube. -
SKYLIGHT SYSTEMS Natural Daylighting Solutions for Residential & Commercial Applications About Us
SKYLIGHT SYSTEMS Natural Daylighting Solutions for Residential & Commercial Applications About Us DRIVE TO SUCCEED Solar has been making high quality CUSTOM DESIGNS VERTICALLY INTEGRATED At Solar Innovations® Architectural systems since 1998. We began with an Ingrained in our company’s DNA is a Engineering, product testing, and product Glazing Systems, we push the envelope idea that we could not only create better “never say no” customer service attitude. design all take place within our own by continually developing more innovative products than the market was offering at This mentality has been the catalyst facility. We machine many of our own ways to build the products our customers the time, but could also introduce new for each product line offered by Solar parts, paint most of our own material, are requesting. Our deep rooted core designs that were not even a concept in Innovations® and continues to drive us and create our own custom hardware. values strengthen our commitment to our customers' or competitors' minds. to become the premier door & window, By producing as many components completing the highest quality projects Our team was small in the beginning, but glass structure, and skylight provider in within our own manufacturing facility as delivered on time. We enjoy tackling some over time as we found a talented pool North America. Some of Solar’s greatest possible, we have greater control over of the most complex projects that others of people with our same principles, we innovations have developed from cost and lead times. Superior technical in the industry will not touch, simply began to build a company that today unique customer requests that others support can also be offered for our because innovation not only creates long conquers projects of all sizes and types could not fulfill. -
Installers' Handbook Preface
HANDBOEK VOOR INSTALLATEURS Handboek voor de installatie van VELUX dakvensters Installers' handbook Preface The purpose of this handbook is to provide an overview of the installation of VELUX products. The handbook describes the various aspects of roof construction in association with VELUX roof windows and also provides advice and information on how to obtain the optimal installation. (Third edition, 2010) The VELUX system Chapter 1 2 3 4 5 6 7 8 Other products Chapter 9 Contents Planning Considerations before choosing roof window 5-13 1 Installation of a roof window Installation step by step 15-25 2 Integration – more windows Combination of more than one window 27-45 3 Special installation conditions Installation in various roof constructions 47-63 4 Special roofing materials Installation in various roof materials 65-81 5 Replacement / renovation Replacement of a roof window 83-93 6 Building physics Roof constructions (humidity, heat, sound etc) 95-109 7 Product information Short presentation of VELUX products 111-137 8 Other products Sun tunnel / Flat roof window / Solar hot water system 139-145 9 Contact VELUX Addresses / Advising / Service 146-147 List of telephone numbers 148 Size chart 151 Planning 1 The construction of the house 6-7 User requirements 8 Building regulations 9-13 VELUX 5 Planning 1 The construction of the house To be able to choose the right VELUX roof window for a given situ- ation, it is always recommended to start from the construction of the house, user requirements and current building regulations. Normally, a standard VELUX roof window can satisfy the basic requirements, but often choosing another window type or vari- ant and/or choosing accessories can optimise the function and increase the utility value of the window. -
Residential Skylights
Residential skylights New installation Remodel or new construction Rooms filled with natural light and fresh air are invariably more beautiful, spacious, and uplifting to your spirits. Daylight is the essential element that transforms conventional rooms into splendid spaces. VELUX Skylights let you bring the best of the outdoors inside. Skylight replacement Three great reasons to replace skylights when you replace a roof 1. Save money - The most convenient and affordable time to replace a skylight is during re-roofing. 2. Coinciding warranty - You’re getting a new roof with a warranty, why not replace your skylight and enjoy one there as well. 3. Improved energy efficiency - Advanced LowE3 coating provides Replace Replace more daylight and better heat control. 2 VELUX 3 Choosing the right glass Recommended for out-of-reach applications Clean, Quiet & Safe glass Clean Features Neat® glass coating to keep your skylight cleaner longer, leaving skylights virtually spotless. Quiet Reduce unwanted outside noise by up to 25% compared to a standard double pane glass and up to 50% compared to a plastic skylight. Safe VELUX recommends and building Energy efficiency codes require laminated glass for 8’ out-of-reach applications. Most VELUX products are ENERGY STAR® qualified in all 50 states. Go Solar and improve energy efficiency even further! (See page 11) 10-year hail breakage warranty Clean, Quiet & Safe also available in impact, white laminated and snowload types of glass. Recommended for in-reach applications Tempered glass Consists of dual-pane, triple-coated glass with LowE3, is dual-sealed and injected with argon gas. 4 VELUX 5 Fresh air Fresh air skylights help your home breathe by bringing in fresh outside air to maintain good indoor air quality. -
Flat Roof Skylights and Hatches
FLAT ROOF SKYLIGHTS AND HATCHES DXW - walkable skylight 24x24 24x30 36x36 36x48 48x48 CURB MOUNTED FIXED SKYLIGHT FXC Infinity glass - virtually seam-free flat surface 360-degree orientation on sloped or flat roof A modern, trouble-free design helps with water run-off. White finished, PVC frame interior Internal and external accessories available before or after skylight’s installation. Suitable for roof with a pitch between 0-60 degrees DXW FXC WALKABLE SYLIGHT FXC 14x30 14x46 22x22 22x30 22x34 22x46 22x70 30x30 30x46 34x34 34x46 46x46 FLAT ROOF WINDOWS TYPE F An abundance of natural light. The window‘s profile have a secure glazing area that is up to 16% greater than those of competitors. The frame of the flat roof window is constructed from multi-chamber PVC profiles filled with insulating material. The external glass is laminated reflecting the sun rays while the internal pane is anti- burglary Class P2A. In addition to standard sizes, the type F window is available in custom sizes (from 24“x24“ to 48“x87“) to suit may retrofits. High energy-efficient DU6 triple-pane glazing (U-value=0.12 BTU/hf2F) and DU8 quadruple-pane glazing (U-value=0.11 BTU/hf2F) to choose from. INVITE Windows can be fitted with internal and external blinds to ensure shade and protect THE LIGHT DEF electric interiors from overheating. DMF manual DEF, DMF, DXF 22x22 22x30 22x46 30x30 46x46 DXF fixed FLAT ROOF ACCESS SKYLIGHT DRF Energy-efficient design using DU6 triple-pane glazing and insulated, multi-chamber PVC frame to achieve low U-value=0.13 BTU/hf2F. -
PVC Roof Windows
PVC roof windows Energy-efficient Windows Dobroplast Fabryka Okien Sp. z o.o. is a leading manufacturer of windows and doors in Poland and leading brand of the Arbonia Group, listed on the Swiss stock exchange based in Zurich and employs over 8000 people in Europe. Dobroplast is one of the largest manufacturers of windows in Europe. We offer a full range of PVC windows, entrance doors and roller blinds. The headquarters is located in Zambrów, where the company was founded in 2000. The second manufacturing site producing roof windows is located in Lublin. 2 Table of contents Advantages of Skylight windows 4 Unlimited choice Roof windows High thermal insulation 6 Termo Premium The only one in its category 8 Termo Versatile use 10 Skylight Premium Easy to clean 12 Skylight Safe and user-friendly Roof access windows Attractive and modern design 14 Skylight Termo Loft Premium and Loft Premium Easy to use 16 Skylight Termo Loft and Skylight Loft Flashings 18 Colours 19 Handles 20 Electric motors 21 Telescopic handle 21 Window ventilators 22 Interior blinds and pleated blinds 22 Overview of roof windows 23 Price list of roof windows, roof access windows and accessories 24 About us 38 Energy-efficient Windows 3 Advantages of Skylight windows Design of Dobroplast products combines practicality and effective appearance. Skylight roof windows have been created for users valuing comfort and convenience of use. Our offer includes a wide range of colours, shapes and accessories, which can be used to compose your project as you wish. Pleasant atmosphere in the flat - ensures optimal access of daylight to the rooms. -
ROOF TILES Build Something Great™ ROOF TILES TECHNICAL INFORMATION GUIDE
BORAL ROOF TILES Build something great™ ROOF TILES TECHNICAL INFORMATION GUIDE December 2017 Roof Tile Manual Contents Introduction 3 Concrete Roof Tiles 31 Foreword 4 Capri SA 32 Important 4 Contour NSW, VIC 33 Quality Control 4 Linea NSW, QLD 34 Specifications 4 Linea SA 35 Local Authorities 4 Linea VIC 36 Performance 4 Macquarie NSW, VIC, QLD 37 Safety 4 Slimline NSW, VIC, QLD 38 Designer Ceramic + Terracotta 5 Striata SA 39 Concrete 5 Striata VIC 40 Roofing Terminology 6 Vogue NSW, QLD 41 Vogue SA 42 Design Considerations 11 Vogue VIC 43 Code Considerations 12 Standards 12 Accessories 45 Bushfire Attack Levels (BAL) 12 Terracotta Accessories 46 Wind Forces 12 Designer Ceramic Accessories 48 Terrain Categories 13 Concrete Accessories 49 Basic Wind Regions 14 General Accessories 50 Fixing Tile Roofs in Cyclonic Regions 15 Installation Details 51 Minimum Roof Pitch 15 Preparation for Installation 52 Maximum Rafter Lengths 15 Tile Set Out 52 Maximum Rafter Lengths - No Sarking 15 Counter Battens 55 Sarking 16 Valleys 56 Insulation 16 Fascia Height 56 Ventilation 16 Barge Height 57 Performance Characteristics 17 Anti-Ponding Boards 57 Thermal Performance 18 Laying the Roof 57 Acoustic Performance 18 Roof Tile Fixing Systems 58 Water Collection 18 Sarking 59 Testing: AS 2049 - Roof Tiles 20 Ridge Systems 60 Testing: AS 2050 - Installation of Roof Tiles 20 Ridge Installation 60 Fire Resistance 21 Hip Details 63 Valley Boards 63 Terracotta Roof Tiles 23 Sarking at Valleys 63 French 24 Valley General 64 Swiss 25 Barge/Gable Systems 64 Designer Ceramic Roof Tiles 27 Roof and Flashings Details 66 Artline 28 Bedding and Pointing 68 Shingle 29 Roof Completion 68 Wave 30 Architectural Details 69 Frequently Asked Questions 85 Contacts and Further Information 88 2 December 2017 | BORAL ROOF TILES Introduction Roof Tile Manual Introduction Foreword Local Authorities This manual has been prepared to assist the builder, architect Fixing standards and product specifications contained in this leaflet and installer, to specify, detail, prepare and install Boral roof tiles. -
Section 08625 [08 62 23]
SECTION 08625 [08 62 23] TUBULAR DAYLIGHTING DEVICES Display hidden notes to Specifier. (Don't know how? Click Here) Copyright 2003 - 2021 ARCAT, Inc. - All rights reserved PART 1 GENERAL 1.1 SECTION INCLUDES A. Tubular daylighting devices and accessories. 1.2 RELATED SECTIONS A. Section 06100 [06 10 00] - Wood Framing; Site built wood curbs and nailers. B. Section 07310 [07 31 00] - Roof Shingles and Shakes: Flashing of skylight base. C. Section 07320 [07 32 00] - Roof Tiles: Flashing of skylight base. D. Section 07510 [07 51 00] - Built-Up Bituminous Roofing: Flashing of skylight base. E. Section 07520 [07 52 00] - Modified Bituminous Membrane Roofing: Flashing of skylight base. F. Section 07530 [07 53 00] - Electrometric Membrane Roofing: Flashing of skylight base. G. Section 07540 [07 54 00] - Thermoplastic Membrane Roofing: Flashing of skylight base. H. Section 07600 [07 60 00] – Flashing and Sheet Metal: Metal curb flashings. I. Section 08620 [08 60 00] - Unit Skylights: Skylights without reflective tube. J. Section 08630 [08 63 00] - Metal Framed Skylights. K. Section 15810 [23 30 00] – HVAC Air Distribution: Fan vent duct and connections. L. Section 16570 [25 50 00] – Integrated Automation Facility Controls: Lighting controllers. M. Section 16150 [26 05 00] – Common Work Results Electrical: Power cable, power supply and electrical connections. N. Section 16500 [26 50 00] – Lighting Equipment and Controls: Control cable, dimming controls, light bulbs and lamps. 08625-1 1.3 REFERENCES A. ASTM B 209 - Standard Specification for Aluminum and Aluminum-Alloy Sheet and Plate. B. ASTM E 84 - Standard Test Method for Surface Burning Characteristics of Building Materials. -
Building Designer Guide
Roof Trusses BUILDING DESIGNER GUIDE …The Purpose of this Document is to Identify to the Building Designer the Critical Information Required to Complete a Roof Truss Design. Cork Roof Truss Company Table of Contents Table of Contents ................................................................................................................................... 1 Recommended Drawings ....................................................................................................................... 1 First Floor Construction Plan.............................................................................................................. 1 Roof Schematic Drawing .................................................................................................................... 1 Section Drawings ................................................................................................................................ 2 Eaves Detail ........................................................................................................................................ 3 Elevations ........................................................................................................................................... 4 Features & Penetrations ........................................................................................................................ 5 Chimneys ............................................................................................................................................ 5 Stairwells ........................................................................................................................................... -
Wanamaker-Grand-Court.Pdf
5. Boundary Description The Grand Court of the former John Wanamaker Store at 1301-25 Chestnut Street is a seven- story open interior volume measuring approximately 122 feet long by 66 feet wide and 150 feet high. The clear-span area is enclosed by a ground-floor perimeter arcade and upper-floor colonnade walls rising the full height of the space. The boundaries of this nomination include the entire Grand Court volume from floor to ceiling; the inner, outer, and intrados surfaces of the ground-floor arcade; the inward and lateral-facing surfaces of the upper-floor columns and colonnade walls; the architectural elements that span between and in plane with these columns; and all components of the Wanamaker Organ visible from within the Court, including the organ console located in the middle bay of the east second-floor gallery. These boundaries exclude the outer faces of the upper-floor colonnade walls and those portions of the Wanamaker Organ that are not visible from within the Court. This defined Grand Court area satisfies the definition of a public interior eligible for historic designation as set forth in the Philadelphia Historic Preservation Ordinance and defined in the Philadelphia Zoning Code, §14-203 (252) as “an interior portion of a building or structure that is, or was designed to be, customarily open or accessible to the public, including by invitation,” and which retains “a substantial portion of the features reflecting design for public use.” The visible Wanamaker Organ components satisfy the definition of fixtures of a public interior space as set forth in the Philadelphia Historical Commission Rules and Regulations 2.10. -
The Glass Skylight Company
things are looking up. the glassvisionar skylighty rooflights company the glass skylight company If you’re reading this you’ve probably been looking for the type of product that few companies have experience in manufacturing. For almost 25 years Glazing Vision has been designing and manufacturing custom glass skylight systems for a uniquely diverse customer base, from our design and manufacturing facility in the UK. Offering hand built solutions for all manner of applications including natural daylight, ventilation and access. Our US team are based in Hartford, Connecticut, they project manage installations across the United States, with high value projects in New York, Boston, San Francisco and even Hawaii. We have installed our Skybox and Skydoor access skylights on multiple high specification residential developments in locations from Staten Island to the Bronx. Glazing Vision Inc have attained code compliance in all five New York boroughs and have received LPC sign off. We use different words to describe the same things, you say sneakers we say trainers; you say skylight we say rooflight. Whilst this may be true, we’re pretty certain you won’t have seen skylights like these before. Why not get in touch, we’d love to show you what’s possible. flushglaze® the original flat glass skylight 5 6 simplicity The Flushglaze is simplicity itself, a minimalist fixed skylight with 'frameless' internal views designed to allow as much natural daylight into a room as possible. The Flushglaze can be manufactured using a variety of custom glass specifications to suit your chosen application, typical variations include double glazed units utilizing tempered heat soak tested and heat strengthened laminated glass, triple glazed, and walkable specification glass suited to your required loadings. -
Solar Attic Fan Ventilates up to 2,800 Sq
30-Watt Solar Panel Solar Attic Fan Ventilates up to 2,800 Sq. Ft. Introducing the Solar Controller Includes Solar Controller 15-Watt Solar Panel Ventilates up to 1,900 Sq. Ft. Includes Solar Controller 10-Watt Solar Panel Ventilates up to 1,200 Sq. Ft. Air Vent’s Award Winning Solar Attic Fans & Solar Controller 30W, 15W and 10W Solar Attic Fans available for an enhanced product line Solar Attic Fans provide active ventilation and improved airflow to effectively ventilate the attic, helping to reduce heat and moisture buildup. This results in a cooler house with decreased air conditioning usage and increased comfort in the living space. Solar Attic Fans with Solar Controller Air Vent’s award winning AV9930TRS and AV9915TRS come equipped with the Solar Controller to intelligently manage the operation of the Solar Attic Fan. The Solar Controller is capable of powering the fan when solar power is unavailable as well as providing an electronic thermostat and humidistat feature. The AV9930TRS and AV9915TRS are perfect retrofit options for larger attic spaces - capable of ventilating 1,900 to 2,800 sq. ft. With commercial grade construction, severe weather approval, and an optional curb-mounting kit for flat roof applications, the AV9930TRS and AV9915TRS are perfect ventilation AV9930TRS options for residential and light commercial applications. 30-Watt solar panel with 15 ft. of wire for remote mounting option Ventilate the same space as two smaller Solar Attic Fans with only a single fan installation Ventilates up to 2,800 sq. ft. Maximum airflow efficiency - aluminum 14˝ fan blades, 38V high efficiency DC motor, and patent pending air deflection cone design for improved airflow Includes Solar Controller Suitable for severe weather conditions - Florida Building Code Approval and TDI AV9915TRS Black commercial-grade ABS shroud resists denting, fading and rusting 15-Watt solar panel Solar Controller operates Solar Attic Fan on intermittent cycle when solar power is unavailable Ventilates up to 1,900 sq.