Installers' Handbook Preface
Total Page:16
File Type:pdf, Size:1020Kb
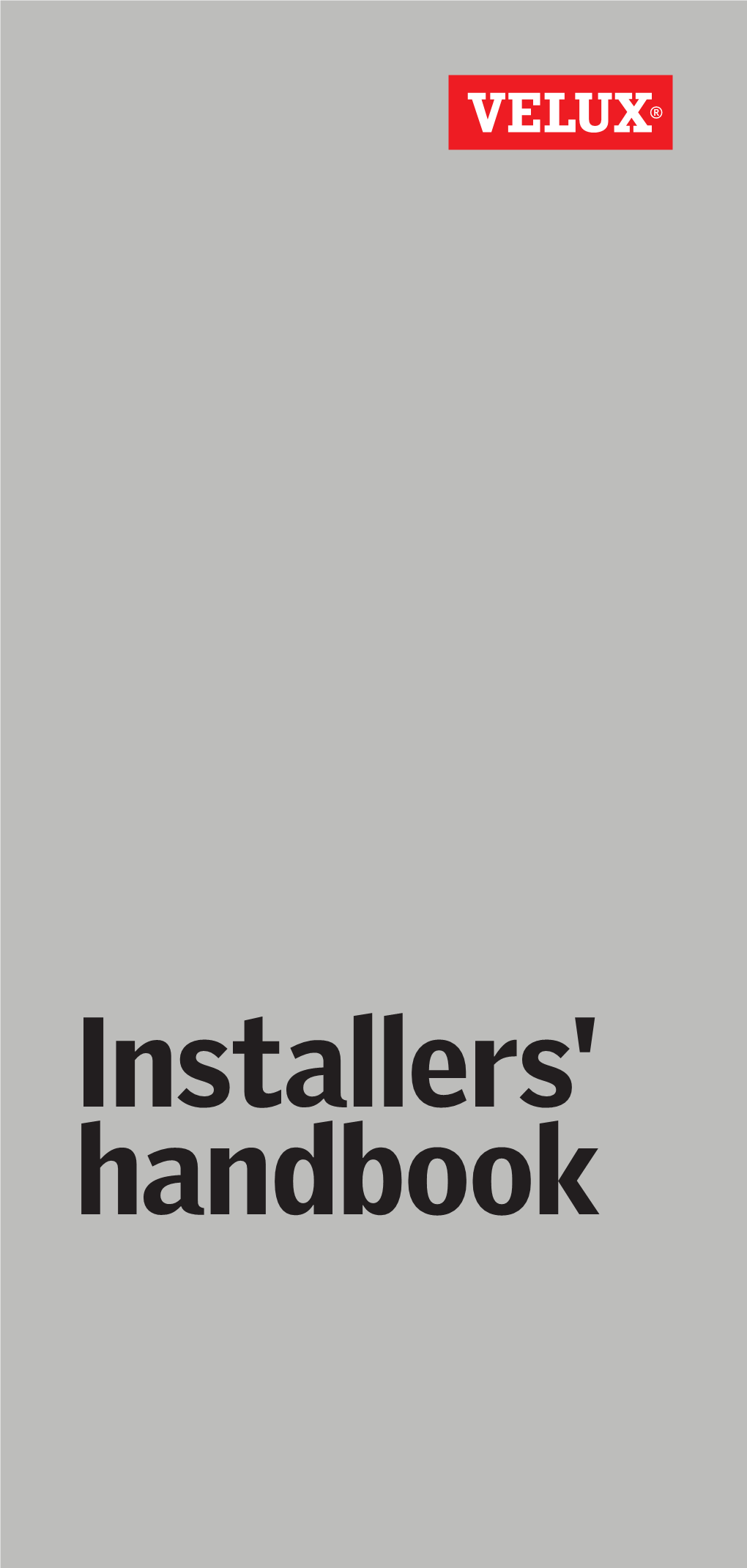
Load more
Recommended publications
-
BUILDING CONSTRUCTION NOTES.Pdf
10/21/2014 BUILDING CONSTRUCTION RIO HONDO TRUCK ACADEMY Why do firefighters need to know about Building Construction???? We must understand Building Construction to help us understand the behavior of buildings under fire conditions. Having a fundamental knowledge of buildings is an essential component of the decisiondecision--makingmaking process in successful fireground operations. We have to realize that newer construction methods are not in harmony with fire suppression operations. According to NFPA 1001: Standard for FireFighter Professional Qualifications Firefighter 1 Level ––BasicBasic Construction of doors, windows, and walls and the operation of doors, windows, and locks ––IndicatorsIndicators of potential collapse or roof failure ––EffectsEffects of construction type and elapsed time under fire conditions on structural integrity 1 10/21/2014 NFPA 1001 Firefighter 2 Level ––DangerousDangerous building conditions created by fire and suppression activities ––IndicatorsIndicators of building collapse ––EffectsEffects of fire and suppression activities on wood, masonry, cast iron, steel, reinforced concrete, gypsum wallboard, glass and plaster on lath Money, Money, Money….. Everything comes down to MONEY, including building construction. As John Mittendorf says “ Although certain types of building construction are currently popular with architects, modern practices will be inevitably be replaced by newer, more efficient, more costcost--effectiveeffective methods ”” Considerations include: ––CostCost of Labor ––EquipmentEquipment -
Illuminator® Tube Skylight
Illuminator® Tube Skylight A new opportunity to help add profit and value. And make every job shine. The Owens Corning® Illuminator® Tube Skylight is a smart choice for bringing natural light into the home. It’s designed to prevent leaking and is covered by a Limited Lifetime Warranty.* This warranty offers the homeowner coverage against manufacturing defects for as long as they own their home. Natural lighting. Evenly distributes up to 500 watts† of clean, natural light, helping to reduce reliance on electricity. Excellent alternative to traditional skylights. The Illuminator® Tube Skylight is cost-effective, easier to install, and features seamless, one-piece flashing designed to prevent leaking. Also provides natural light where a traditional skylight is not an option. A solution for all — naturally. Models are available for nearly all types of roofing materials — including tile and metal — and for applications in severe weather zones, such as in HVHZ. Roof Dome The Owens Corning™ Illuminator® Tube Skylight Natural lighting. Naturally easy installation. The Illuminator® Tube Skylight is easy to install with no framing, Roof Flashing drywall or electrician required and can be installed during a re-roof process or new construction – typically in less than two hours. Just follow these four simple steps: 1. Once a location is determined, use included guide to mark and cut roof, secure flashing, and install top tubing and dome. 2. Inside the home, use included guide to mark and cut ceiling, feed bottom tubing into attic, and install trim ring. 3. In the attic, insert bottom tube into trim ring and connect to top tube. -
Geodesic Dome Roof
GEODESIC DOME ROOF The HMT Geodesic Dome features a clear-span, all-aluminum, lightweight, corrosion-resistant structure which sets a new standard for performance in aluminum geodesic domes. HMT’s unique overlapping-panel design and attention to details at critical locations all result in a cost-effective solution that provides superior protection of your stored product. The HMT Geodesic Dome can be installed in-service and its superior design was developed under the guidance of API 650, appendix G and AWWA D-108. Key benefits: Key design features: The HMT Geodesic Dome’s advanced tBatten bar and gasket assembly completely technology provides excellent benefits. Here’s encapsulate panel edges for unparallelled how: sealing Most effective leak-protection solution— tOverlapping panels ensure additional Engineered for maximum weather-tightness for protection against weather both new tanks and retrofits tHub designed with three levels of sealing to Low maintenance — Aluminum alloys are ensure maximum leak protection corrosion resistant and don’t require painting like steel fixed roofs tHub can be easily removed for inspection or Emissions reduction — reduces wind-induced adjustment of IFR support chains vapor loss, aids in odor control and provides tOptions for fixed or sliding rim connections significant emission credits; for light products such as gasoline, a dome installed over an EFR tCan easily handle the weight of suspended can cut emissions by over 90% aluminum internal floating roofs In-service installation — Can be erected on tIndustry-leading 3D design software for the ground beside the tank or on an EFR and maximum accuracy and shorter design time lifted into place Custom engineered— To accommodate a wide range of spans and loading conditions Protecting your world, one tank at a time™ www.hmttank.com THE HMT GEODESIC DOME DESIGN HMT’s design incorporates features which dramatically Triple seal hub design improve upon existing technology. -
SKYLIGHT SYSTEMS Natural Daylighting Solutions for Residential & Commercial Applications About Us
SKYLIGHT SYSTEMS Natural Daylighting Solutions for Residential & Commercial Applications About Us DRIVE TO SUCCEED Solar has been making high quality CUSTOM DESIGNS VERTICALLY INTEGRATED At Solar Innovations® Architectural systems since 1998. We began with an Ingrained in our company’s DNA is a Engineering, product testing, and product Glazing Systems, we push the envelope idea that we could not only create better “never say no” customer service attitude. design all take place within our own by continually developing more innovative products than the market was offering at This mentality has been the catalyst facility. We machine many of our own ways to build the products our customers the time, but could also introduce new for each product line offered by Solar parts, paint most of our own material, are requesting. Our deep rooted core designs that were not even a concept in Innovations® and continues to drive us and create our own custom hardware. values strengthen our commitment to our customers' or competitors' minds. to become the premier door & window, By producing as many components completing the highest quality projects Our team was small in the beginning, but glass structure, and skylight provider in within our own manufacturing facility as delivered on time. We enjoy tackling some over time as we found a talented pool North America. Some of Solar’s greatest possible, we have greater control over of the most complex projects that others of people with our same principles, we innovations have developed from cost and lead times. Superior technical in the industry will not touch, simply began to build a company that today unique customer requests that others support can also be offered for our because innovation not only creates long conquers projects of all sizes and types could not fulfill. -
Basic Technical Rules the Nubian Vault (Nv)
PRODUCTION CENTRE INTERNATIONAL PROGRAMME BASIC TECHNICAL RULES v3 BASIC TECHNICAL RULES THE NUBIAN VAULT (NV) TECHNICAL CONCEPT THE NUBIAN VAULT ASSOCIATION (AVN) ADVICE TO MSA CLIENTS Version 3.0 SEASON 2013-2014 COUNTRY INTERNATIONAL Association « la Voûte Nubienne » - 7 rue Jean Jaurès – 34190 Ganges - France February 2015 www.lavoutenubienne.org / [email protected] / +33 (0)4 67 81 21 05 1/14 PRODUCTION CENTRE INTERNATIONAL PROGRAMME BASIC TECHNICAL RULES v3 CONTENTS CONTENTS.............................................................................................................2 1.AN ANCIENT TECHNIQUE, SIMPLIFIED, STANDARDISED & ADAPTED.........................3 2.MAIN FEATURES OF THE NV TECHNIQUE........................................................................4 3.THE MAIN STAGES OF NV CONSTRUCTION.....................................................................5 3.1.EXTRACTION, FABRICATION & TRANSPORT OF MATERIAL....................................5 3.2.CHOOSING THE SITE....................................................................................................5 3.3.MAIN STRUCTURAL WORKS........................................................................................6 3.3.1.Foundations........................................................................................................................................ 6 3.3.2.Load-bearing walls.............................................................................................................................. 7 3.3.3.Arches in load-bearing -
Insulating Thatched Roofs This Guidance Note Has Been Prepared and Edited by David Pickles
Energy Efficiency and Historic Buildings Insulating Thatched Roofs This guidance note has been prepared and edited by David Pickles. It forms one of a series of thirteen guidance notes covering the thermal upgrading of building elements such as roofs, walls and floors. First published by English Heritage March 2012. This edition (v1.1) published by Historic England April 2016. All images © Historic England unless otherwise stated. Illustrations drawn by Simon Revill. Our full range of guidance on energy efficiency can be found at: HistoricEngland.org.uk/energyefficiency Front cover: Thatch repairs in progress. © Philip White. Summary This guidance provides advice on the principles, risks, materials and methods for insulating thatched roofs. There are estimated to be about fifty thousand thatched buildings in England today, some of which retain thatch which is over six hundred years old. Thatching reflects strong vernacular traditions all over the country. Well-maintained thatch is a highly effective weatherproof coating as traditional deep thatched eaves will shed rainwater without the need for any down pipes or gutters. Locally grown thatch is a sustainable material, which has little impact on the environment throughout its life-cycle. It requires no chemicals to grow, can be harvested by hand or using traditional farm machinery, requires no mechanical processing and therefore has low embodied energy and can be fixed using hand tools. At the end of its life it can be composted and returned to the land. Thatch has a much greater insulating value than any other traditional roof covering. With the right choice of material and detailing, a well-maintained thatched roof will keep a building warm in winter and cool in summer and has the added advantage of being highly sound-proof. -
Replacing the Roof on Your Manufactured Or Mobile Home Protectmymanufacturedhome
What You Should Know: Replacing the roof on your manufactured or mobile home ProtectMyManufacturedHome An alteration permit from the Washington State Department of Labor & Industries is required when you reroof a manufactured home. In some cases, plans for the work must also be submitted to L&I for approval prior to doing the work. L&I has a four-step process for home alterations. Here’s how: Step 1: See if you need to submit plans. You need to submit plans if: You are not removing the old shingles or roof covering before installing the new roofing. The new roof covering is heavier than the original. There are repairs to any roof framing, such as trusses or rafters. A second layer of sheathing or additional framing is added to the roof. Plans must be stamped by a Washington professional engineer (PE) or architect. When you reroof, you need to submit plans when buying a permit (see step 2). There is a fee for reviewing plans which is added to the permit. Get more information It usually takes two to three weeks to process plans and plans must be approved before proceeding with the work. Visit www.Lni.wa.gov/FAS You do not need to submit plans if: For structural issues, contact plan review at: 360-902-5218 You are removing the existing roofing and installing For general permit help, call customer new roofing of the same or lesser weight. service at: 360-902-5206 Existing roof sheathing may be removed and new roof Or email [email protected] sheathing used. -
Top-Operated Centre-Pivot Polyurethane Roof Window GLU 0061
Edition 2.0 – 05.04.2017 Product information Top-operated centre-pivot polyurethane roof window GLU 0061 Product description High quality moulded polyurethane with white lacquer finish Triple insulating glass unit with Uw 1.1 Top control bar for easy operation even with furniture under the window Integrated ventilation in top control bar and cleanable dust and insect filter Maintenance-free interior surface Maintenance-free exterior covers Roof pitch Can be installed in roof pitches between 15° and 90° Materials Polyurethane around a core of thermally modified timber Glass; float glass / strengthened glass / toughened glass Lacquered aluminium VELUX ThermoTechnology™ insulation Downloads For installation instructions, CAD drawings, 3D BIM objects, 3D GDL objects etc, please visit velux.bg. Certifications The VELUX product EUTR In compliance with the EU Timber factories guarantee Regulation (EUTR), EU regulation quality systems 995/2010 implementation process and environmental REACH We are aware of the REACH regulation management systems and acknowledge the obligations. No through appropriate products are obliged to be registered in accreditations ISO accordance to REACH and none of our 9001 and ISO 14001 products contain any Substances of Very High Concern. Available sizes and daylight area Lining measurements 472 550 660 mm 780 mm 942 mm 1140 mm 1340 mm Size Width (mm) mm mm GLU p CK-- 495 CK02 mm FK-- 605 78 7 (0.22) MK-- 725 GLU MK04 PK-- 887 m m SK-- 1085 78 9 (0.47) Size Height (mm) GLU GLU FK06 MK06 --02 719 m m --04 919 78 11 --06 1119 (0.47) (0.59) GLU GLU GLU GLU --08 1339 FK08 MK08 PK08 SK08 --10 1549 m 398 m 398 1 (0.58) (0.72) (0.92) (1.16) GLU MK10 1600mm (0.85) ( ) = Effective daylight area, m2 Top-operated centre-pivot roof windows make it possible to place furniture directly below the window without obstructing operation of the window. -
Best Practices Single-Family Residences
SITE PLANNING best practices single-family residences for aesthetic review by the city of coral gables board of architects 2018 1 SINGLE-FAMILY RESIDENCE BEST PRACTICES July 2018 table of contents 1. Purpose & Uses 2. Site Planning 3. Architecture 4. Checklist Purpose & Uses The purpose of the City of Coral Gables, Florida Zoning Code is to implement the Comprehensive Plan (CP) of the City pursuant to Chapter 163, Florida Statutes for the protection and promotion of the safety, health, comfort, morals, convenience, peace, prosperity, appearance and general welfare of the City and its inhabitants. ~ Zoning Code Section 1-103 Purpose of the City of Coral Gables Zoning Code PURPOSE & USE Single-Family Residential (SFR) District The Single-Family Residential (SFR) District is intended to accommodate low density, single-family dwelling units with adequate yards and open space that characterize the residential neighborhoods of the city. The city is unique not only in South Florida but in the country for its historic and archi- tectural treasures, its leafy canopy, and its well-defined and livable neighborhoods. These residential areas, with tree-lined streets and architecture of harmonious proportion and human scale, provide an oasis of charm and tranquility in the midst of an increasingly built-up metropolitan environment. The intent of the Single-Family Residential code is to protect the distinctive character of the city, while encouraging excellent architectural design that is responsible and responsive to the individual context of the city’s diverse neighborhoods. The single-family regulations, as well as the design and performance standards in the Zoning Code, seek to ensure that the renovation of residences as well as the building of residences is in accord with the civic pride and sense of stewardship felt by the citizens of Coral Gables. -
Katalog Produktow GB 2008.Indb
ROOF WINDOWS INTRODUCTION Consultation with the architect helps make decision 8 www.fakro.com Loft Conversion-planning Building or renovation of a house is an investment which requires not only financial expenditure, but also considered decisions and solutions. Each matter should be discussed with professionals who will ad- vise the best way of solving problems. When deciding how and where to place roof windows you should consult an architect, who will help you to choose the right window type depending on the proposed use of the loft. He will also give you advice concerning the window’s glass surface area decided by the ratio to the total floor area and also where to place the win- dows to gain the maximum benefit. Nowadays roof windows are often an indispensable element of newly built structures. They create new, unique, individual possibilities. When adapting or con- The attic before conversion verting the loft and also installing roof windows your loft can be easily changed into a functional, stylish and elegant space. Depending on the client’s individ- ual requirements and the ingenuity of the architects, even the most exceptional ideas can be prepared in the form of computerised 3D visualisation of the project which helps your dreams come true. A completed conversion with two roof windows A completed conversion with four roof windows and blinds ROOF WINDOW 9 ROOF WINDOWS VERSUS DORMER When planning to develop the loft there are two options to get light in: building a dormer (until recently a very popular solution) or installing (becoming more and more popular ) modern roof windows. -
Roof Window Size Comparison
Roof Windows Roof Window Size Comparison keyliteroofwindows.com Comparison Chart Futuretherm Technology Height (mm) Width (mm) 550 660 780 940 1140 1340 01 03A 04A 07A 08A 09A Keylite CK02 N/A N/A N/A N/A N/A Velux 780 01 22 23 24 25 26 Fakro 02 03B 04 07B 08B 09 Keylite CK04 FK04 MK04 PK04 N/A UK04 Velux 980 02 03 05 15 N/A 12 Fakro 01C 03 05 07C 08 09C Keylite CK06 FK06 MK06 PK06 SK06 N/A Velux 1180 16 04 06 08 10 N/A Fakro 01F 03F 06 07F 08F 10 Keylite N/A FK08 MK08 PK08 SK08 UK08 Velux 1400 N/A N/A 07 09 11 N/A Fakro Keylite 1600 01G 03G 04G 07G 08G 09G Velux N/A N/A MK10 PK10 SK10 UK10 Fakro N/A N/A 13 N/A N/A N/A Centre Pivot Roof Windows Pine White Conservation Pine Conservation White Keylite CP WF-CP CW-CP CW-WF-CP Velux GGL GGU GGL SD5 GGU SD5 Fakro FTP-V FTU-V & PTP-V FTP-V/C PTP-V/C Top Hung / Fire Escape Pine White Conservation Pine Conservation White Keylite FE WF-FE CW-FE CW-WF-FE Velux GPL GPU GPL SD5 GPU SD5 FPP-V & FPU-V & FPP-V/C & FPU-V/C & Fakro FHP-V FHU-V FHP-V/C FHU-V/C Single Flashings Slate Tile Deep Plain Tile Conservation Conservation Conservation Conservation Corrugated Tile Slate Tile Plain Tie Deep Tile Keylite SRF TRF DTRF PTRF CWSRF CWTRF CWPTRF CWDTRF CRF (Recessed As Standard) Standard Recessed Standard Recessed Standard Recessed Standard Recessed Standard Recessed Standard Recessed Standard Recessed Standard Recessed Velux EDL/ EDN EDZ N/A EDW/ EDJ EDP/ N/A N/A EDN N/A N/A EDP N/A EDW EDJ ZWC EBL/ EBW/ EBP/ EKL EKW EKP Fakro EL N/A EZ N/A EH N/A EP N/A /C N/A /C N/A /C N/A /C N/A EE Combi Flashings 18mm -
Tilcor-Installation-Manual-16-EN.Pdf
INSTALLATION MANUAL BOND / CLASSIC / TUDOR / SHAKE / ROYAL / ANTICA These installation details are provided to demonstrate the recommended installation methods for Tilcor products and accessories. The details and information in this document reflect current roofing practices used in New Zealand. Consult with Tilcor Roofing Systems for additional information. Ross Roof Group Ltd +64 9 299 9498 faks +64 9 298 4114 1c Inlet Road, Takanini 2112, PO Box 72062, Papakura 2244, e-mail: [email protected] web: www.tilcor.com New Zealand 1. General Information ................................................................................. 3 2. Recommended Tools ............................................................................... 9 3. Profile and Flashing Specifications .......................................................... 10 4. Preparation of The Roof Surface for Installation ................................... 14 5. Tile (BOND, CLASSIC, TUDOR, ANTICA) Installation ............................... 16 6. Tile Installation (SHAKE, ROYAL) .............................................................. 19 7. Eaves Flashing ........................................................................................... 20 8. Box Barge Installation (Bond, Classic, Tudor, Shake, Royal) ................. 21 9. Installation of Barrels at The Ridge and Hip ............................................ 22 10. Roof Window Installation ........................................................................ 23 11. Roof Ventilation, Extractor and Sanitary