Preliminary Design and Integration Studies
Total Page:16
File Type:pdf, Size:1020Kb
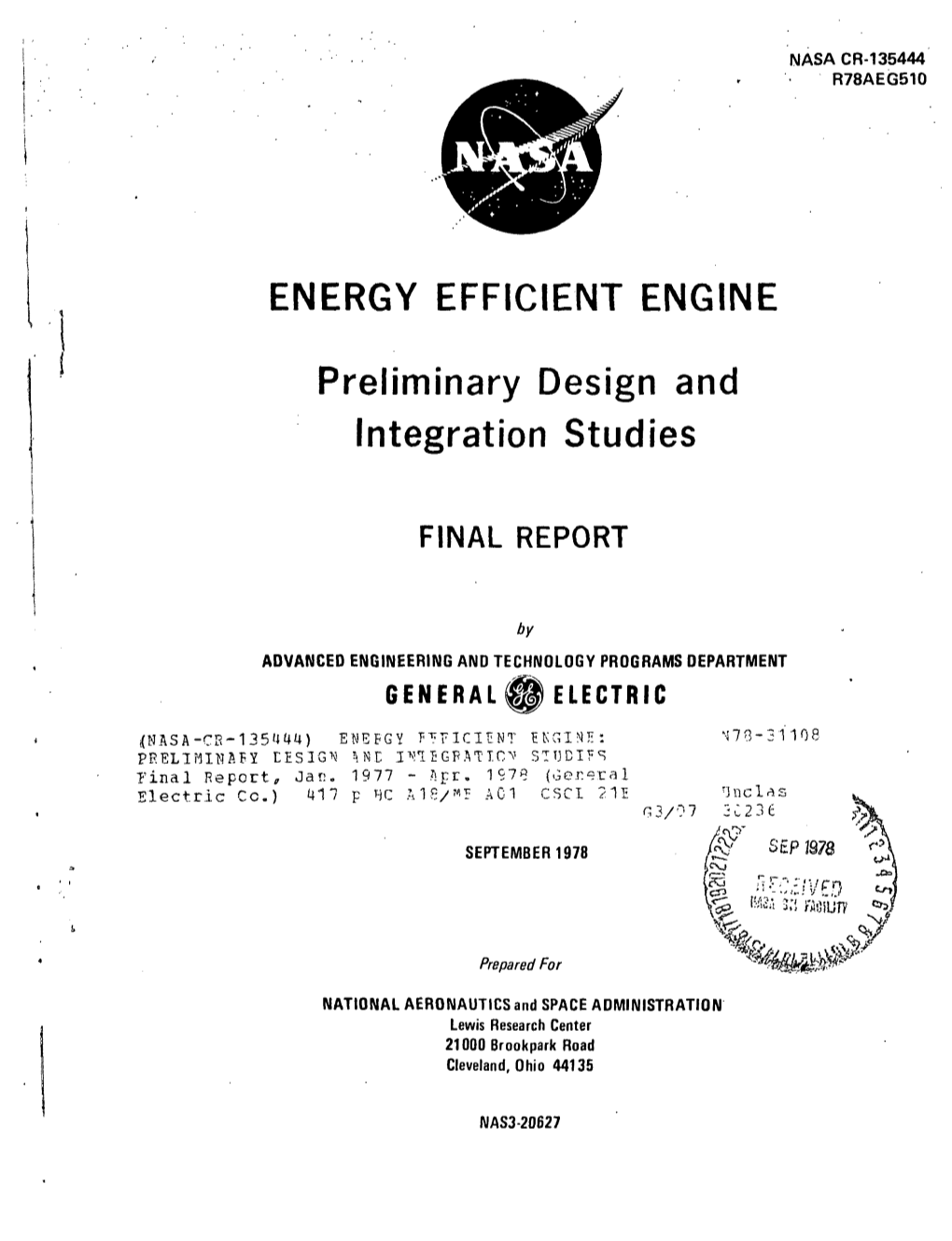
Load more
Recommended publications
-
Gallery of USAF Weapons Note: Inventory Numbers Are Total Active Inventory Figures As of Sept
Gallery of USAF Weapons Note: Inventory numbers are total active inventory figures as of Sept. 30, 2011. ■ 2012 USAF Almanac Bombers B-1 Lancer Brief: A long-range, air refuelable multirole bomber capable of flying intercontinental missions and penetrating enemy defenses with the largest payload of guided and unguided weapons in the Air Force inventory. Function: Long-range conventional bomber. Operator: ACC, AFMC. First Flight: Dec. 23, 1974 (B-1A); Oct. 18, 1984 (B-1B). Delivered: June 1985-May 1988. IOC: Oct. 1, 1986, Dyess AFB, Tex. (B-1B). Production: 104. Inventory: 66. Aircraft Location: Dyess AFB, Tex.; Edwards AFB, Calif.; Eglin AFB, Fla.; Ellsworth AFB, S.D. Contractor: Boeing, AIL Systems, General Electric. Power Plant: four General Electric F101-GE-102 turbofans, each 30,780 lb thrust. Accommodation: pilot, copilot, and two WSOs (offensive and defensive), on zero/zero ACES II ejection seats. Dimensions: span 137 ft (spread forward) to 79 ft (swept aft), length 146 ft, height 34 ft. B-1B Lancer (SSgt. Brian Ferguson) Weight: max T-O 477,000 lb. Ceiling: more than 30,000 ft. carriage, improved onboard computers, improved B-2 Spirit Performance: speed 900+ mph at S-L, range communications. Sniper targeting pod added in Brief: Stealthy, long-range multirole bomber that intercontinental. mid-2008. Receiving Fully Integrated Data Link can deliver nuclear and conventional munitions Armament: three internal weapons bays capable of (FIDL) upgrade to include Link 16 and Joint Range anywhere on the globe. accommodating a wide range of weapons incl up to Extension data link, enabling permanent LOS and Function: Long-range heavy bomber. -
The Aircraft Propulsion the Aircraft Propulsion
THE AIRCRAFT PROPULSION Aircraft propulsion Contact: Ing. Miroslav Šplíchal, Ph.D. [email protected] Office: A1/0427 Aircraft propulsion Organization of the course Topics of the lectures: 1. History of AE, basic of thermodynamic of heat engines, 2-stroke and 4-stroke cycle 2. Basic parameters of piston engines, types of piston engines 3. Design of piston engines, crank mechanism, 4. Design of piston engines - auxiliary systems of piston engines, 5. Performance characteristics increase performance, propeller. 6. Turbine engines, introduction, input system, centrifugal compressor. 7. Turbine engines - axial compressor, combustion chamber. 8. Turbine engines – turbine, nozzles. 9. Turbine engines - increasing performance, construction of gas turbine engines, 10. Turbine engines - auxiliary systems, fuel-control system. 11. Turboprop engines, gearboxes, performance. 12. Maintenance of turbine engines 13. Ramjet engines and Rocket engines Aircraft propulsion Organization of the course Topics of the seminars: 1. Basic parameters of piston engine + presentation (1-7)- 3.10.2017 2. Parameters of centrifugal flow compressor + presentation(8-14) - 17.10.2017 3. Loading of turbine blade + presentation (15-21)- 31.10.2017 4. Jet engine cycle + presentation (22-28) - 14.11.2017 5. Presentation alternative date Seminar work: Aircraft engines presentation A short PowerPoint presentation, aprox. 10 minutes long. Content of presentation: - a brief history of the engine - the main innovation introduced by engine - engine drawing / cross-section - -
The Power for Flight: NASA's Contributions To
The Power Power The forFlight NASA’s Contributions to Aircraft Propulsion for for Flight Jeremy R. Kinney ThePower for NASA’s Contributions to Aircraft Propulsion Flight Jeremy R. Kinney Library of Congress Cataloging-in-Publication Data Names: Kinney, Jeremy R., author. Title: The power for flight : NASA’s contributions to aircraft propulsion / Jeremy R. Kinney. Description: Washington, DC : National Aeronautics and Space Administration, [2017] | Includes bibliographical references and index. Identifiers: LCCN 2017027182 (print) | LCCN 2017028761 (ebook) | ISBN 9781626830387 (Epub) | ISBN 9781626830370 (hardcover) ) | ISBN 9781626830394 (softcover) Subjects: LCSH: United States. National Aeronautics and Space Administration– Research–History. | Airplanes–Jet propulsion–Research–United States– History. | Airplanes–Motors–Research–United States–History. Classification: LCC TL521.312 (ebook) | LCC TL521.312 .K47 2017 (print) | DDC 629.134/35072073–dc23 LC record available at https://lccn.loc.gov/2017027182 Copyright © 2017 by the National Aeronautics and Space Administration. The opinions expressed in this volume are those of the authors and do not necessarily reflect the official positions of the United States Government or of the National Aeronautics and Space Administration. This publication is available as a free download at http://www.nasa.gov/ebooks National Aeronautics and Space Administration Washington, DC Table of Contents Dedication v Acknowledgments vi Foreword vii Chapter 1: The NACA and Aircraft Propulsion, 1915–1958.................................1 Chapter 2: NASA Gets to Work, 1958–1975 ..................................................... 49 Chapter 3: The Shift Toward Commercial Aviation, 1966–1975 ...................... 73 Chapter 4: The Quest for Propulsive Efficiency, 1976–1989 ......................... 103 Chapter 5: Propulsion Control Enters the Computer Era, 1976–1998 ........... 139 Chapter 6: Transiting to a New Century, 1990–2008 .................................... -
Broad Specificationfuels on High B ,Passturbofan Engine Combustors
A/',d_*,,e'/_-/_2 _ Y/ 3 1176 00156 6455 NASA-CR-159641 19790025034 NASA CR-159641 R79AEG504 I,:. Analytical Evaluation of the Impact of " Broad SpecificationFuels on High B_,passTurbofan Engine Combustors FINAL REPORT August 1979 By J. R. Taylor General Electric Company Aircraft Engine Group Cincinnati., OH 45215 Ll_[1_.i[_!_,ll"_l'ti'lit_P7'll_i, ;:t! ,<::iY.ig LANGLEY RE.SEARCH CENTER LIBRARy,NASA HAMPTON,.VIRGINIA . " NATIONAL AERONAUTICS AND SPACEADMINISTRATION LEWISPrepRarEedSEARCHfor: CENTER -: ...... 21000 BROOKPARKROAD CLEVELAND, OHIO 44135 NAS3-20799 1. Report No. I 2. GovernmentA_:cessionNo. 3. Recipient'sCatalogNo. NASA CR-159641 I 4. Title and Subtitle 5. Report Date Analytical Evaluation of the Impact of Broad Specification Fuels August 1979 on High Bypass Turbofan Engine Combustors 6. PerformingOrganizationCode 7. Author{'s) 8. PerformingOrganizationReport No. J.R. Taylor R79AEG504 10. Work Unit No. 9. PerformingOrganizationName andAddress General Electric Company 11. Contractor Grant No. - Aircraft Engine Group Cincinnati, Ohlo 45215 NAS3-20799 13. Type of Report and PeriodCovered 12. SponsoringAgencyName and Address Contractor Report National Aeronautics and Space Administration 14. SponsoringAgency Code Washington, D.C. 20546 15. SupplementaryNotes Project Manager: A.L. Smith, NASA-Lewis Research Center, Cleveland, Ohlo 44135 16.Abstra_ An in-depth analysis of six conceptual combustor designs for the CF6-50 hlgh bypass turbofan engine and slx conceptual combustor designs for the NASA/GE E3 high bypass turbofan engine was performed to provide an assessment of the major problems anticipated in using broad specification fuels in these aircraft engine combustion systems. The conceptual eombustor designs are representative of both state-of-the-art and advanced state-of-the-art combustion systems. -
The Market for Aviation Turbofan Engines
The Market for Aviation Turbofan Engines Product Code #F640 A Special Focused Market Segment Analysis by: Aviation Gas Turbine Forecast Analysis 1 The Market for Aviation Turbofan Engines 2010-2019 Table of Contents Executive Summary .................................................................................................................................................2 Introduction................................................................................................................................................................2 Trends..........................................................................................................................................................................3 Market Focus .............................................................................................................................................................3 Competitive Environment.......................................................................................................................................4 Figure 1 - The Market for Aviation Turbofan Engines Unit Production 2010 - 2019 (Bar Graph) .................................................................................6 Figure 2 - The Market for Aviation Turbofan Engines Value of Production 2010 - 2019 (Bar Graph)...........................................................................6 Manufacturers Review.............................................................................................................................................7 -
Testing Down to the Last Detail
1/2010 Testing down to the last detail MTU Aero Engines Holding AG Customers + PartnersTechnology + Science MTU Global Dachauer Straße 665 80995 Munich • Germany Tel. +49 89 1489-0 Fax +49 89 1489-5500 Power for the Jumbo Jet Hardfaced tips for top MTU support for the [email protected] www.mtu.de and the Dreamliner efficiency “flying gas station” Contents Editorial Cover Story Dear Readers: Testing down to the last detail 4 – 7 Finally, yes finally, the bird is on the wing. However, the program highlights something Late last year, the new A400M military trans- else too—something we have witnessed re- Customers + Partners port aircraft successfully completed its long- peatedly in the past. Almost all the major Power for the Jumbo Jet and 8 – 11 awaited, eagerly anticipated maiden flight commercial and military aircraft programs the Dreamliner above the Spanish city of Seville. The relief that have ever been initiated in Europe and A boost for the MRJ 12 – 15 Testing down to the last detail was palpable throughout the industry; delays the United States have been subject to to the project had been creating too much delays, some of them massive. In this respect, Four TP400-D6 engines lift Europe’s new military transport, the A400M, up into turbulence all round. Now, the ongoing flight the A400M is no exception. As things stand the air—now almost an everyday occurrence at Seville airport. Since the maiden Technology + Science test program is demonstrating the superior at present, in pure economic terms, MTU flight in December 2009, flight testing has been in full swing. -
Shuttle/Progress in Aircraft Design Since 1903
197402:3386-002 -TABLE OF CONTENTS _. AIRCRAFT PAGE AIRCRAFT PAGE AeroncaC-2 28 Granville Bros.R-1 "Super Sportster" 33 BeechModel 18 42 GrummanF3F-2 36 Bell Model204 73 GrummanF4F-3 "Wildcat" 43 Bell P-59A "Airacomet" 57 GrummanF8F-1 "Bearcat" 60 • Bell XS-1 63 GrummanF-14A "Tomcat" 92 BldriotXI 5 HandleyPage0/400 7 BoeingModel40B 23 HawkerSiddeley"Harrier" 88 ; _. BoeingModel80A-1 27 Kellett YO-60 58 BoeingModel367-80 71 Lear Jet Model23 84 BoeingMode=377 "Stratocruiser" 64 Lockheed1049 "Super Constellation" 68 BoeingModel727 82 LockheedP-38F .ightning" 47 ; BoeingModel 737 89 LockheedP-80A "Shooting Star" 59 Bo_ingModel747 90 LockheedYF-12A 83 BoeingB-17F "Flying Fortress" 39 Lockheed"Vega" 25 BoeingB-29 "Superfortress" 56 Martin MB-2 18 BoeingB-47E 66 Martin PBM-3C "Mariner" 48 Bo_;ngB-52 "Stratofortress" 69 McDonnellF-4B "Phantom I1" 77 Boeing F4B-4 32 McDonnellDouglasF-15A"Eagle" 93 BoeingP-26A 31 MoraneSaulnierType N 6 CessnaModel421 87 Navy-CurtissNC-4 17 Cierva autogiro 20 Nieuport XVII C.1 9 ConsolidatedB-24D "Liberator" 49 NorthAmericanB.25H "Mitchell" 51 ConsolidatedPBY-5A'Catalina" 37 North AmericanF-86F "Sabre" 65 ConvairB-36D 62 North AmericanF-100D "Super Sabre" 70 Convair B-58A"Hustler" 74 North AmericanP-51B "Mustang" 52 , ConvairF-106A "Delta Dart" 75 NorthAmericanX-15 79 L Curtiss JN-4D"Jenny" 12 Piper J-3 "Cub" 44 CurtissP-6E "Hawk" 30 Piper "Cherokee140" 80 CurtissP-36A 38 Pitcairn PA-5"Mailwing" 24 : CurtissP-40B 46 Republic P-47D "Thunderbolt" 53 _ CurtissPW-8 19 RoyalAircraft FactoryR.E.8 8 De Havilland DH-4 13 RyanNYP "Spirit of St. -
Gallery of USAF Weapons Note: Inventory Numbers Are Total Active Inventory Figures As of Sept
Gallery of USAF Weapons Note: Inventory numbers are total active inventory figures as of Sept. 30, 2015. By Aaron M. U. Church, Senior Editor ■ 2016 USAF Almanac BOMBER AIRCRAFT B-1 Lancer Brief: Long-range bomber capable of penetrating enemy defenses and de- livering the largest weapon load of any aircraft in the inventory. COMMENTARY The B-1A was initially proposed as replacement for the B-52, and four proto- types were developed and tested before program cancellation in 1977. The program was revived in 1981 as B-1B. The vastly upgraded aircraft added 74,000 lb of usable payload, improved radar, and reduced radar cross section, but cut maximum speed to Mach 1.2. The B-1B first saw combat in Iraq during Desert Fox in December 1998. Its three internal weapons bays accommodate a substantial payload of weapons, including a mix of different weapons in each bay. Lancer production totaled 100 aircraft. The bomber’s blended wing/ body configuration, variable-geometry design, and turbofan engines provide long range and loiter time. The B-1B has been upgraded with GPS, smart weapons, and mission systems. Offensive avionics include SAR for tracking, B-2A Spirit (SSgt. Jeremy M. Wilson) targeting, and engaging moving vehicles and terrain following. GPS-aided INS lets aircrews autonomously navigate without ground-based navigation aids Dimensions: Span 137 ft (spread forward) to 79 ft (swept aft), length 146 and precisely engage targets. Sniper pod was added in 2008. The ongoing ft, height 34 ft. integrated battle station modifications is the most comprehensive refresh in Weight: Max T-O 477,000 lb. -
Etu – V Tulpar
2017-2018 Undergraduate Team Engine Candidate Engines for a Next Generation Supersonic Transport ETU – V TULPAR TEAM MEMBERS Veli Can ÜSTÜNDAĞ - 921399 Çağdaş Cem ERGİN - 920976 Baran İPER - 921398 Onur TAN - 921395 Faculty Advisor Asst. Prof. Sıtkı USLU SIGNATURES Faculty Advisor Asst. Prof. Sıtkı USLU TOBB University of Economics and Technology Team Leader Cagdas Cem ERGIN TOBB University of Economics and Technology Deparment of Mechanical Engineering AIAA Member Number: 920976 Team Member Veli Can USTUNDAG TOBB University of Economics and Technology Deparment of Mechanical Engineering AIAA Member Number: 921399 Team Member Baran IPER TOBB University of Economics and Technology Deparment of Mechanical Engineering AIAA Member Number: 921398 Team Member Onur TAN TOBB University of Economics and Technology Deparment of Mechanical Engineering AIAA Member Number: 921395 ii TABLE OF CONTENT LIST OF TABLES .................................................................................................................................................. v LIST OF FIGURES ............................................................................................................................................... vi NOMENCLATURE ............................................................................................................................................... ix 1. INTRODUCTION .......................................................................................................................................... 1 2. STATE OF THE -
Production Test Facilities for Turbojet and Turbofan Engines 1975-1995
LIBRARY „_.-,j TECHNICAL REPORT SECTION NAVAL POSTGRADUATE S< MONTEREY. CAL.FORN.A 93940 NPS-57Ba,To72061A NAVAL POSTGRADUATE SCHOOL Monterey, California PRODUCTION TEST FACILITIES FOR TUR BOJET AND TURBOFAN ENGINES - 1975 to 1995 D. L. Bailey LT, USN P. W. Tower LT, USN May 1972 Approved for public release; distribution unlimited, FEDDOCS D 208.14/2:NPS-57BA72061A NAVAL POSTGRADUATE SCHOOL Monterey, California Rear Admiral A. S. Goodfellow, Jr., USN Milton U. Clauser Superintendent Provost ABSTRACT: A review is made of test cell design options in order to identify characteristics of jet engine test facilities to be constructed in the 1970's and designed to be operable for a minimum of twenty years. The necessity of providing replacements for many current facilities is documented, and the factors which will ensure future production capability and economic feasibility are detailed. Present turbine engines are reviewed and projections of future engines and aircraft are made. A confidential supplement is included for qualified receivers. Experimental investigations of inlet flow patterns and engine exhaust-augmenter relationships are being carried out. Results will be published in thesis form in October 1972, by the Naval Postgraduate School, Monterey, California. ACKNOWLEDGMENT This work was funded in part by AIR TASK Number A33033OC/ 551B/2F00-432-302. The assistance and guidance of Dr. Allen E. Fuhs is gratefully acknowledged. TABLE OF CONTENTS PART TITLE PAGE I. INTRODUCTION 1 II. ENGINES 2 A. Present 2 B. Future 2 III. SUMMARY OF TEST FACILITY REQUIREMENTS . 8 IV. PRESENT TEST CELL DESIGNS 10 A. Inlets 10 B. Exhausts 14 C. General 18 V. -
National Air & Space Museum Technical Reference Files: Propulsion
National Air & Space Museum Technical Reference Files: Propulsion NASM Staff 2017 National Air and Space Museum Archives 14390 Air & Space Museum Parkway Chantilly, VA 20151 [email protected] https://airandspace.si.edu/archives Table of Contents Collection Overview ........................................................................................................ 1 Scope and Contents........................................................................................................ 1 Accessories...................................................................................................................... 1 Engines............................................................................................................................ 1 Propellers ........................................................................................................................ 2 Space Propulsion ............................................................................................................ 2 Container Listing ............................................................................................................. 3 Series B3: Propulsion: Accessories, by Manufacturer............................................. 3 Series B4: Propulsion: Accessories, General........................................................ 47 Series B: Propulsion: Engines, by Manufacturer.................................................... 71 Series B2: Propulsion: Engines, General............................................................ -
Gallery of USAF Weapons
Almanac USAF■ Gallery of USAF Weapons By Susan H.H. Young Note: Inventory numbers are Total Active Inventory figures as of Sept. 30, 1999. B-1B’s list of weapons, with fleet completion in FY02. The B-1B’s capability is being significantly enhanced by the ongoing Conventional Mission Upgrade Pro- gram (CMUP). This gives the B-1B greater lethality and survivability through the integration of precision and standoff weapons and a robust ECM suite. CMUP includes GPS receivers, a MIL-STD-1760 weapon in- terface, secure radios, and improved computers to support precision weapons, initially the JDAM, fol- lowed by the Joint Standoff Weapon (JSOW) and the Joint Air-to-Surface Standoff Missile (JASSM). The Defensive System Upgrade Program will improve air- crew situational awareness and jamming capability. B-2 Spirit Brief: Stealthy, long-range, multirole bomber that can deliver conventional and nuclear munitions any- where on the globe by flying through previously impen- etrable defenses. Function: Long-range heavy bomber. Operator: ACC. First Flight: July 17, 1989. Delivered: Dec. 17, 1993–present. B-1B Lancer (Ted Carlson) IOC: April 1997, Whiteman AFB, Mo. Production: 21. Inventory: 21. Unit Location: Whiteman AFB, Mo. Contractor: Northrop Grumman, with Boeing, LTV, and General Electric as principal subcontractors. Bombers Power Plant: four General Electric F118-GE-100 turbofans, each 17,300 lb thrust. B-1 Lancer Accommodation: two, mission commander and pi- Brief: A long-range multirole bomber capable of lot, on zero/zero ejection seats. flying missions over intercontinental range without re- Dimensions: span 172 ft, length 69 ft, height 17 ft.