US5357419.Pdf
Total Page:16
File Type:pdf, Size:1020Kb
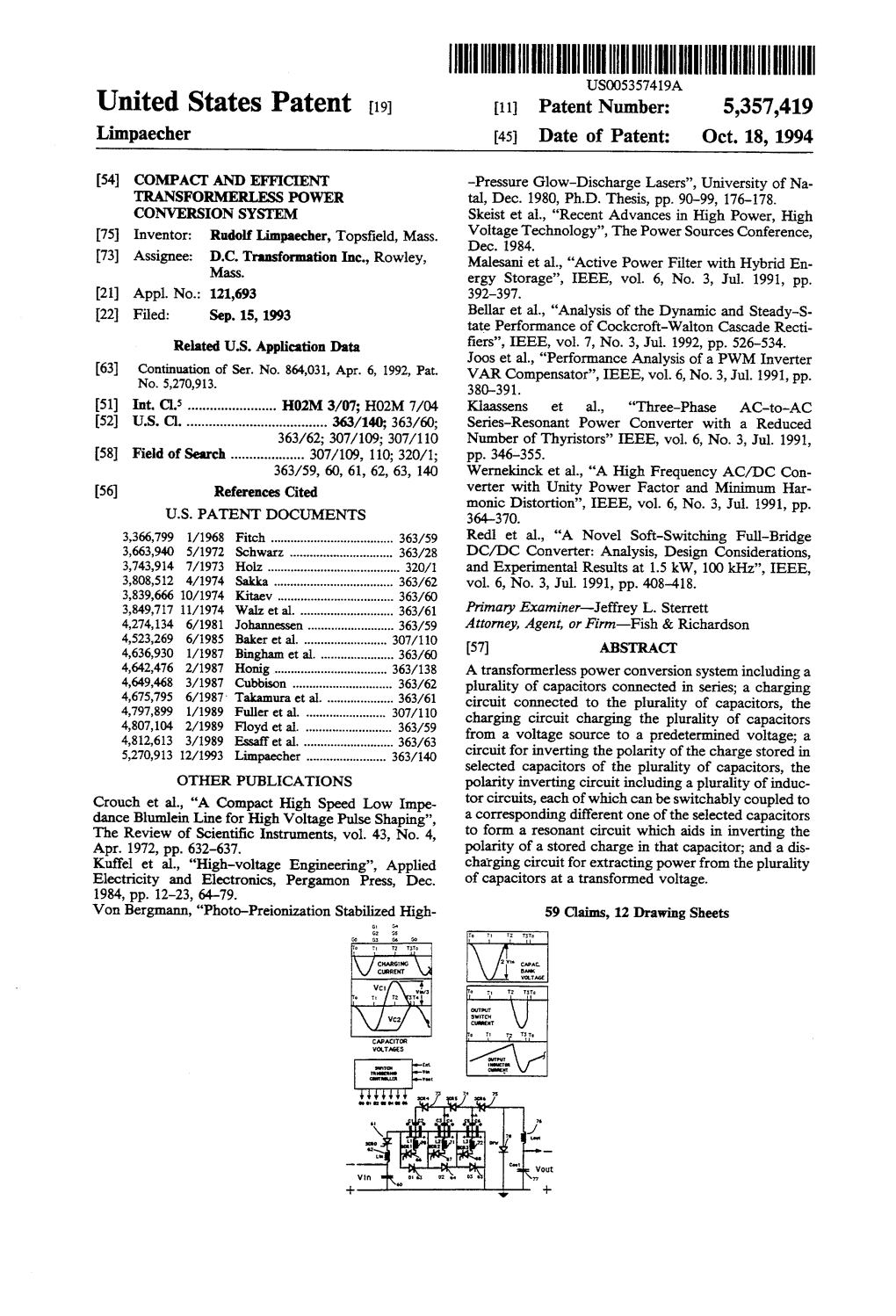
Load more
Recommended publications
-
A Real Distribution Network Voltage Regulation Incorporating Auto-Tap-Changer Pole Transformer Multiobjective Optimization
applied sciences Article A Real Distribution Network Voltage Regulation Incorporating Auto-Tap-Changer Pole Transformer Multiobjective Optimization Sayed Mir Shah Danish 1,* , Ryuto Shigenobu 2, Mitsunaga Kinjo 1, Paras Mandal 3 , Narayanan Krishna 4, Ashraf Mohamed Hemeida 5 and Tomonobu Senjyu 1 1 Faculty of Engineering, University of the Ryukyus, 1 Senbaru Nishihara-cho, Nakagami, Okinawa 903-0213, Japan 2 Department of Electrical and Electronics Engineering, University of Fukui, 3-9-1 Bunkyo, Fukui-shi, Fukui 910-8507, Japan 3 Department of Electrical and Computer Engineering, University of Texas at El Paso, El Paso, TX 79968, USA 4 Department of Electrical and Electronics Engineering, SASTRA Deemed University, Thanjavur, Tamil Nadu 613401, India 5 Department of Electrical Engineering, Faculty of Energy Engineering, Aswan University, Aswan 81528, Egypt * Correspondence: [email protected] Received: 11 June 2019; Accepted: 11 July 2019; Published: 14 July 2019 Abstract: A number of studies realized operation of power systems are unstable in developing countries due to misconfiguration of distribution systems, limited power transfer capability, inconsistency of renewable resources integration, paucity of control and protection measures, timeworn technologies, and disproportionately topology. This study underlines an Afghanistan case study with 40% power losses that is mainly pertinent from old distribution systems. The long length of distribution systems, low-power transfer capability, insufficient control and protection strategy, peak-demand elimination, and unstable operation (low energy quality and excessive voltage deviations) are perceived pre-eminent challenges of Afghanistan distribution systems. Some attainable solutions that fit challenges are remodeling (network reduction), networks reinforcement, optimum compensation strategy, reconfiguration options, improving, and transfer capability. -
Local Voltage Support by Distributed Generation
Do It Locally: Local Voltage Support by Distributed Generation – A Management Summary Management Summary of IEA Task 14 Subtask 2 – Recommendations Based on Research and Field Experience Report IEA-PVPS T14-08:2017 INTERNATIONAL ENERGY AGENCY PHOTOVOLTAIC POWER SYSTEMS PROGRAMME Do It Locally: Local Voltage Support by Distributed Generation – A Management Summary Management Summary of IEA Task 14 Subtask 2 – Recommendations Based on Research and Field Experience IEA PVPS Task 14, Subtask 2, Activity 2.8 IEA-PVPS T14-08:2017 January 2017 Authors: M. Kraiczy1, [email protected] L. Al Fakhri1, [email protected] T. Stetz2, [email protected] M. Braun1,3, [email protected] 1 Fraunhofer IWES, Germany 2 TH Mittelhessen University of Applied Sciences, Germany 3 University of Kassel, Germany Contents Contents ............................................................................................................................................................ ii Abbreviations and Acronyms ........................................................................................................................... iii Foreword .......................................................................................................................................................... iv Abstract ............................................................................................................................................................ vi 1. Introduction .............................................................................................................................................. -
Comparison of Voltage Regulation Between SST and Conventional Transformers in High Penetration PV Power Systems
Scholars' Mine Masters Theses Student Theses and Dissertations Summer 2017 Comparison of voltage regulation between SST and conventional transformers in high penetration PV power systems Gautham Ashokkumar Follow this and additional works at: https://scholarsmine.mst.edu/masters_theses Part of the Electrical and Computer Engineering Commons Department: Recommended Citation Ashokkumar, Gautham, "Comparison of voltage regulation between SST and conventional transformers in high penetration PV power systems" (2017). Masters Theses. 7680. https://scholarsmine.mst.edu/masters_theses/7680 This thesis is brought to you by Scholars' Mine, a service of the Missouri S&T Library and Learning Resources. This work is protected by U. S. Copyright Law. Unauthorized use including reproduction for redistribution requires the permission of the copyright holder. For more information, please contact [email protected]. COMPARISON OF VOLTAGE REGULATION BETWEEN SST AND CONVENTIONAL TRANSFORMERS IN HIGH PENETRATION PV POWER SYSTEMS by GAUTHAM ASHOKKUMAR A THESIS Presented to the Faculty of the Graduate School of the MISSOURI UNIVERSITY OF SCIENCE AND TECHNOLOGY In Partial Fulfillment of the Requirements for the Degree MASTER OF SCIENCE IN ELECTRICAL ENGINEERING 2017 Approved by Dr. Mariesa L. Crow, Advisor Dr. Mehdi Ferdowsi Dr. Pourya Shamsi iii ABSTRACT Solid state transformers (SST) are power electronic transformers combined with high-frequency conventional transformers and control circuitry capable of delivering high performance and flexible power control capabilities. This thesis focuses on analyzing the performance of SSTs in a distribution system with photovoltaic (PV) injection. In order to validate the performance of SSTs, average value models are used on the IEEE 34 bus distribution feeder network scaled to 12.47 kV. -
Fundamentals of Reactive Power and Voltage Regulation in Power Systems
Fundamentals of Reactive Power and Voltage Regulation in Power Systems Course No: E03-011 Credit: 3 PDH Boris Shvartsberg, Ph.D., P.E., P.M.P. Continuing Education and Development, Inc. 22 Stonewall Court Woodcliff Lake, NJ 07677 P: (877) 322-5800 [email protected] FUNDAMENTALS OF REACTIVE POWER AND VOLTAGE REGULATION IN POWER SYSTEMS Boris Shvartsberg, Ph.D., P.E., P.M.P. © 2011 Boris Shvartsberg Introduction One of the main goals that every electrical utility company has is transportation of electrical energy from generating station to the customer, meeting the following main criteria: • High reliability of power supply • Low energy cost • High quality of energy (required voltage level, frequency etc.) This course is concentrated on accomplishing the 2nd and 3rd goals through regulation of reactive power and voltage. Reliability of power supply is a subject of a different course. To better understand why the regulation of reactive power and voltage makes power systems more efficient, let’s start with discussion about the structure of the power systems and their main components. Power System Structure The typical power system structure is shown in Figure 1. Fig. 1 - Power System Structure and Main Components Where the numerical symbols represent the following components: (1) Generator (2) Generating station’s step-up transformer substation (3) Extra high voltage step-down transformer substation (4) High voltage step-down transformer substation (5) Distribution substation (6) Distribution Transformer (7) Transmission and Distribution -
Secondary Voltage Regulation Based on Average Voltage Control
TecnoLógicas ISSN: 0123-7799 ISSN: 2256-5337 [email protected] Instituto Tecnológico Metropolitano Colombia Secondary voltage regulation based on average voltage control Lopera-Mazo, Edwin H.; Espinosa, Jairo Secondary voltage regulation based on average voltage control TecnoLógicas, vol. 21, no. 42, 2018 Instituto Tecnológico Metropolitano, Colombia Available in: https://www.redalyc.org/articulo.oa?id=344255453005 DOI: https://doi.org/10.22430/22565337.779 Los artículos publicados por la revista TecnoLógicas son obras literarias y científicas protegidas por las leyes de Derecho de Autor. Con la firma de la Declaración de Originalidad, así como con la entrega de la obra para su consideración o posible publicación, los autor autorizan de forma gratuita, al INSTITUTO TECNOLÓGICO METROPOLITANO –ITM- para la publicación, reproducción, comunicación, distribución y transformación de la obra e igualmente declaran bajo la gravedad del juramento que la obra es original e inédita de exclusiva autoría de los remitentes. This work is licensed under Creative Commons Attribution 3.0 International. PDF generated from XML JATS4R by Redalyc Project academic non-profit, developed under the open access initiative Edwin H. Lopera-Mazo, et al. Secondary voltage regulation based on average voltage control Artículos de investigación Secondary voltage regulation based on average voltage control Regulación secundaria de voltaje basada en el control del voltaje promedio Edwin H. Lopera-Mazo DOI: https://doi.org/10.22430/22565337.779 Instituto Tecnológico Metropolitano, Colombia Redalyc: https://www.redalyc.org/articulo.oa? [email protected] id=344255453005 Jairo Espinosa Universidad Nacional de Colombia, Colombia [email protected] Received: 05 February 2018 Accepted: 20 April 2018 Abstract: is paper compares a conventional Secondary Voltage Regulation (SVR) scheme based on pilot nodes with a proposed SVR that takes into account average voltages of control zones. -
A Study of Voltage Regulation and Islanding Associated with Distributed Generation
UNLV Retrospective Theses & Dissertations 1-1-2007 A study of voltage regulation and islanding associated with distributed generation Chensong Dai University of Nevada, Las Vegas Follow this and additional works at: https://digitalscholarship.unlv.edu/rtds Repository Citation Dai, Chensong, "A study of voltage regulation and islanding associated with distributed generation" (2007). UNLV Retrospective Theses & Dissertations. 2763. http://dx.doi.org/10.25669/o1qk-cj6y This Dissertation is protected by copyright and/or related rights. It has been brought to you by Digital Scholarship@UNLV with permission from the rights-holder(s). You are free to use this Dissertation in any way that is permitted by the copyright and related rights legislation that applies to your use. For other uses you need to obtain permission from the rights-holder(s) directly, unless additional rights are indicated by a Creative Commons license in the record and/or on the work itself. This Dissertation has been accepted for inclusion in UNLV Retrospective Theses & Dissertations by an authorized administrator of Digital Scholarship@UNLV. For more information, please contact [email protected]. A STUDY OF VOLTAGE REGULATION AND ISLANDING ASSOCIATED WITH DISTRIBUTED GENERATION by Chensong Dai Bachelor of Electrical Engineering Tsinghua University, China 1997 Master of Electrical Engineering Nanjing Automation Research Institute, China 2000 A dissertation submitted in partial fulfillment of the requirements for the Doctor of Philosophy Degree in Electrical Engineering Department of Electrical and Computer Engineering Howard R. Hughes College of Engineering Graduate College University of Nevada Las Vegas December 2007 Reproduced with permission of the copyright owner. Further reproduction prohibited without permission. -
A Novel Control Strategy for the Frequency and Voltage Regulation of Distribution Grids Using Electric Vehicle Batteries †
energies Article A Novel Control Strategy for the Frequency and Voltage Regulation of Distribution Grids Using Electric Vehicle Batteries † Mohammadshayan Latifi 1, Reza Sabzehgar 1,* , Poria Fajri 2 and Mohammad Rasouli 3 1 Department of Electrical and Computer Engineering, San Diego State University, San Diego, CA 92182, USA; mlatifi@sdsu.edu 2 Department of Electrical and Biomedical Engineering, University of Nevada Reno, Reno, NV 89557, USA; [email protected] 3 Department of Electrical and Computer Engineering, Penn State Behrend, Erie, PA 16563, USA; [email protected] * Correspondence: [email protected]; Tel.: +1-619-594-7791 † This paper is an extended version of our paper published in 2019 IEEE Texas Power and Energy Conference (TPEC), College Station, TX, USA, 7–8 February 2019; pp. 1–6. Abstract: In this study, a double-loop control strategy is proposed for power grid frequency and voltage regulation using plug-in electric vehicles (PEVs) connected to the grid through a three-level capacitor clamped inverter. The frequency and voltage regulation problem is first formulated using vector space analysis and phasor diagrams to find the boundaries and constraints in terms of the system parameters. The derived formulas are then utilized to design a double-loop controller using an exclusive phase detector control loop and a novel pulse width modulation (PWM) scheme to effectively regulate the frequency and voltage of the grid. The effectiveness and feasibility of the Citation: Latifi, M.; Sabzehgar, R.; proposed control strategy are evaluated through simulation and experimental studies. This approach Fajri, P.; Rasouli, M. A Novel Control can benefit both the customers and the grid operator, as it facilitates utilizing the batteries of the Strategy for the Frequency and connected PEVs to supply a portion or all of the active and reactive power demand, hence regulating Voltage Regulation of Distribution the frequency and voltage of the grid. -
Voltage Regulation of Unbalanced Distribution Network with Distributed Generators Through Genetic Algorithm
University of Northern Iowa UNI ScholarWorks Dissertations and Theses @ UNI Student Work 2018 Voltage regulation of unbalanced distribution network with distributed generators through genetic algorithm Islam Ali University of Northern Iowa Let us know how access to this document benefits ouy Copyright ©2018 Islam Ali Follow this and additional works at: https://scholarworks.uni.edu/etd Part of the Electrical and Electronics Commons Recommended Citation Ali, Islam, "Voltage regulation of unbalanced distribution network with distributed generators through genetic algorithm" (2018). Dissertations and Theses @ UNI. 678. https://scholarworks.uni.edu/etd/678 This Open Access Dissertation is brought to you for free and open access by the Student Work at UNI ScholarWorks. It has been accepted for inclusion in Dissertations and Theses @ UNI by an authorized administrator of UNI ScholarWorks. For more information, please contact [email protected]. Copyright by ISLAM ALI 2018 All Rights Reserved VOLTAGE REGULATION OF UNBALANCED DISTRIBUTION NETWORK WITH DISTRIBUTED GENERATORS THROUGH GENETIC ALGORITHM An Abstract of a Dissertation Submitted in Partial Fulfillment of the Requirements for the Degree Doctor of Industrial Technology Approved: ____________________________________ Dr. Hong Nie, Committee Chair ____________________________________ Dr. Patrick Pease Interim Dean of the Graduate College Islam Ali University of Northern Iowa July, 2018 ABSTRACT Energy demand has rapidly increased since the manufacturing revolution in the 19th century. One of the higher energy demands is electricity. The great majority of devices in the manufacturing field run on electricity. The vertically integrated grid paradigm has to be changed to supply the increase in the electrical demand residentially and commercially. Distributed generators (DG) such as Photovoltic (PV) is used to supply the increase in the electrical demand. -
Electric Power Distribution Systems Operations
Naval Facilities Engineering Command 200 Stovall Street Alexandria, Virginia 22332-2300 Electric Power Distribution Systems Operations NAVFAC MO-201 April 1990 SN 0525-LP-320-1900 FOREWORD This manual on electric power distribution systems is one of a series developed to aid utility supervisory personnel at shore establishments in the performance of their duties. It includes information obtained from extensive research of current literature on the subject and preferred practices based on practical experience. The principles and procedures described are in accordance with national professional society, association, and institute codes. Additional information concerning procedures, suggestions, recommendations or modifications that will improve this manual are invited and should be submitted through appropriate channels to the Commander, Naval Facilities Engineering Command, (Attention: Code 165), 200 Stovall Street, Alexandria, VA 22332-2300. This publication has been reviewed and approved in accordance with the Secretary of the Navy Instruction 5600.16A and is certified as an official publication of the Naval Facilities Engineering Command. It cancels and supersedes Operation of Electric Power Distribution Systems, NAVFAC MO-201, November 1963, in its entirety. D. B. CAMPBELL Assistant Commander for Public Works Centers and Departments i PAGE ii INTENTIONALLY LEFT BLANK ABSTRACT Application principles and procedures for the operation of electric power distribution systems and associated major apparatus are presented. The contents include principles of power systems, cabling systems, electrical equipment, power system protection and coordination, instruments and meters, operational procedures, and electrical utilization systems. iii PAGE iv INTENTIONALLY LEFT BLANK CHANGE CONTROL SHEET Document all changes, page replacements, and pen and ink alterations posted in this manual. -
Approaches to Establishing Voltage Control Requirements for Distributed Generation Units
E3S Web o f Conferences 139, 010 06 (2019) https://doi.org/10.1051/e3sconf/20191390 1006 RSES 2019 Approaches to establishing voltage control requirements for distributed generation units Pavel Ilyushin1*, Petr Berezovskiy 2, and Sergey Filippov3 1Petersburg power engineering institute of professional development, Aviation str., 23, Saint-Petersburg, Russia 2Study committee C6 of CIGRE Russian national committee, Aviation str., 23, Saint-Petersburg, Russia 3Energy research institute of the Russian academy of sciences, Nagornaya str., 31, bld. 2, Moscow, Russia Abstract. Analysis of Russian national regulation and technical standards requirements for generating equipment participation in voltage and reactive power control in the power system carried out. Summary of some international experience in voltage control organization under conditions of distributed generation units’ deep integration in public grid is presented in article. Advantages of voltage and reactive power control automation over decentralized and poorly coordinated control are substantiated. Problematic aspects of distributed generation units (including RES) integration, as well as ENTSO-E approaches to voltage and reactive power control in the synchronous zone of continental Europe are considered. Technical requirements of Deutsch and Danish regulations, regarding participation of distributed generation facilities in voltage control are given. Approaches to establishing voltage control requirements for distributed generation units’ operation with national power system are presented. 1 Introduction electricity quality requirements are ever higher on the consumer bus side. The Russian business community certainly seems In this context, decentralized barely coordinated grid interested in distributed generation (DG), as businesses control based on «manual» adjustment of automatic seek cheaper energy, while DG is an effective tool to excitation controls (AEC) in electric machines, produce it. -
Impact of Photovoltaic System Penetration on the Operation of Voltage Regulator Equipment
IMPACT OF PHOTOVOLTAIC SYSTEM PENETRATION ON THE OPERATION OF VOLTAGE REGULATOR EQUIPMENT A Thesis presented to the Faculty of California Polytechnic State University, San Luis Obispo In Partial Fulfillment of the Requirements for the Degree Masters of Science in Electrical Engineering By Abesh S. Mubaraki June 2013 © 2013 Abesh Sorab Mubaraki ALL RIGHTS RESERVED ii COMMITTEE MEMBERSHIP TITLE: Impact of Photovoltaic System Penetration on the Operation of Voltage Regulator Equipment AUTHOR: Abesh Sorab Mubaraki DATE SUBMITTED: June 2013 COMMITTEE CHAIR: Dr. Taufik, Professor, Electrical Engineering COMMITTEE MEMBER: Dr. Dale Dolan, Professor, Electrical Engineering COMMITTEE MEMBER: Dr. Ali Shaban, Professor, Electrical Engineering iii ABSTRACT IMPACT OF PHOTOVOLTAIC SYSTEM PENETRATION ON THE OPERATION OF VOLTAGE REGULATOR EQUIPMENT Abesh Sorab Mubaraki The growing popularity of photovoltaic (PV) generation systems leads to an increase in the number of residential and commercial grid-tied PV systems that interconnect to the distribution circuit. This affects the characteristics of the distribution circuit; for example, the assumption that the voltage profile of a radial line decreases down-stream becomes invalid because of the addition of the PV system on the line. This poses new challenges when setting the parameters of voltage regulating devices. Add to that the fact that PV systems are intermittent, especially on cloudy days, which make the line even more difficult to regulate, and the number of switching occurrences of the regulating devices increases, thus accelerating wear-and-tear to the utility’s equipment. The objective of this thesis is to develop an index which qualitatively indicates the impact of PV system(s) on operation, efficiency, reliability, and lifetime of voltage regulation equipment. -
Use of Demand Response for Voltage Regulation in Power Distribution Systems with Flexible Resources
IET Generation, Transmission & Distribution Research Article ISSN 1751-8687 Use of demand response for voltage Received on 1st August 2019 Revised 13th November 2019 regulation in power distribution systems with Accepted on 19th December 2019 E-First on 31st January 2020 doi: 10.1049/iet-gtd.2019.1170 flexible resources www.ietdl.org Qiangqiang Xie1,2, Hongxun Hui1, Yi Ding1 , Chengjin Ye1, Zhenzhi Lin1, Peng Wang3, Yonghua Song1, Ling Ji4, Rong Chen5 1College of Electrical Engineering, Zhejiang University, Hangzhou, People's Republic of China 2College of Electronics and Information, Hangzhou Dianzi University, Hangzhou, People's Republic of China 3School of Electrical & Electronic Engineering, Nanyang Technological University, Singapore 4Guodian Nanjing Automation Co., LTD, Nanjing 211100, People's Republic of China 5State Grid Zhejiang Electric Power Co., LTD, Zhejiang 310007, People's Republic of China E-mail: [email protected] Abstract: In low-voltage power distribution systems with high penetration of photovoltaics (PVs) generation and electric vehicles (EVs), the over-voltage problem arises at times because of large PV generation, and under-voltage problem also arises sometimes because of simultaneous charging of massive EVs. Over- and under-voltage problems lead to more difficulties in achieving voltage regulation. Demand response (DR) is expected to be promising and cost-effective in promoting smart grids, and hence, the utilisation of flexible resources (FRs) through DR can be helpful for distribution system voltage regulation. This study introduces a hierarchical control structure of a community energy management system (CEMS) and multiple sub-CEMSs to apply an FR-based two-stage voltage regulation technique. In the first stage, i.e.