Pros and Cons of Various Automotive Materials And
Total Page:16
File Type:pdf, Size:1020Kb
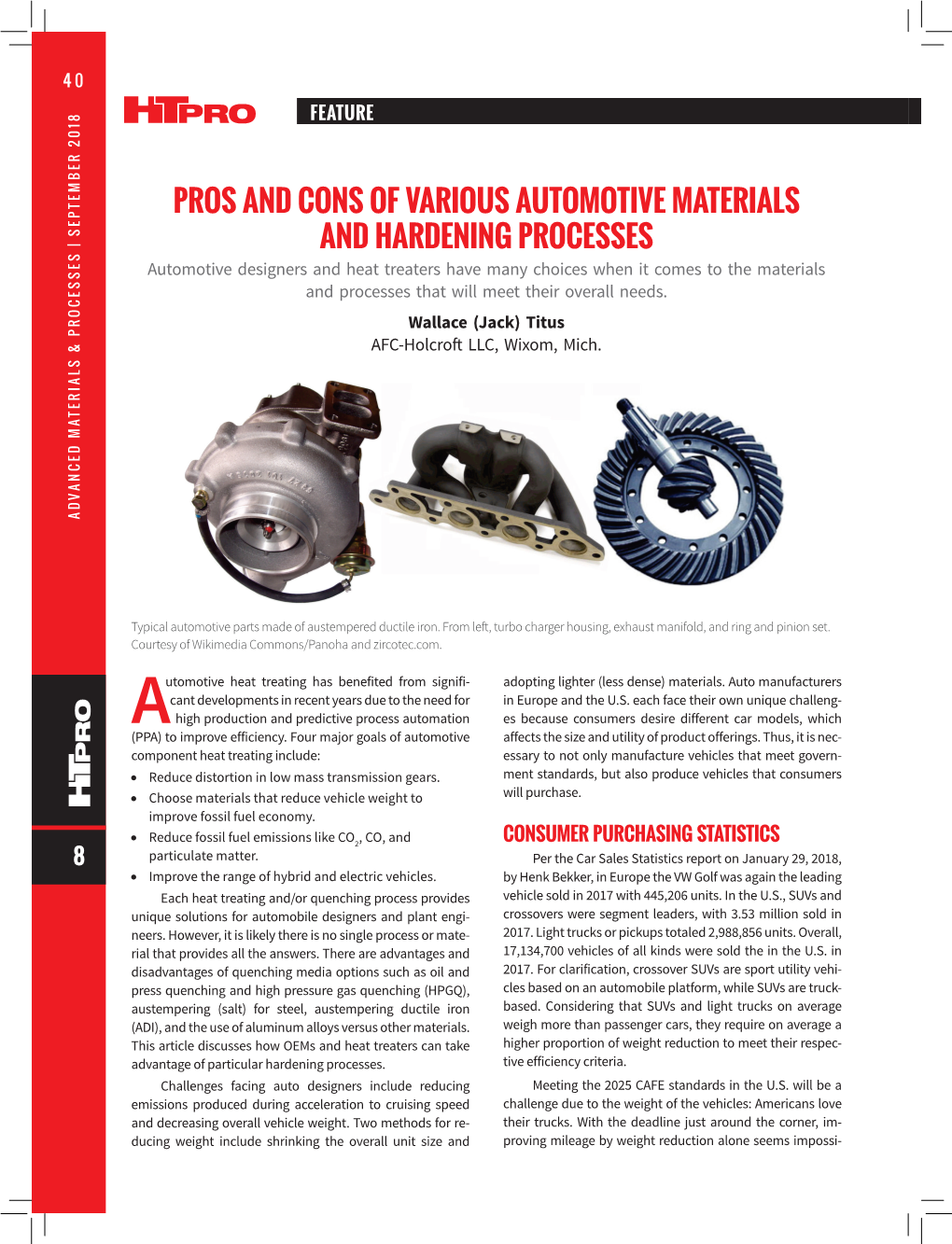
Load more
Recommended publications
-
Wear Behavior of Austempered and Quenched and Tempered Gray Cast Irons Under Similar Hardness
metals Article Wear Behavior of Austempered and Quenched and Tempered Gray Cast Irons under Similar Hardness 1,2 2 2 2, , Bingxu Wang , Xue Han , Gary C. Barber and Yuming Pan * y 1 Faculty of Mechanical Engineering and Automation, Zhejiang Sci-Tech University, Hangzhou 310018, China; [email protected] 2 Automotive Tribology Center, Department of Mechanical Engineering, School of Engineering and Computer Science, Oakland University, Rochester, MI 48309, USA; [email protected] (X.H.); [email protected] (G.C.B.) * Correspondence: [email protected] Current address: 201 N. Squirrel Rd Apt 1204, Auburn Hills, MI 48326, USA. y Received: 14 November 2019; Accepted: 4 December 2019; Published: 8 December 2019 Abstract: In this research, an austempering heat treatment was applied on gray cast iron using various austempering temperatures ranging from 232 ◦C to 371 ◦C and holding times ranging from 1 min to 120 min. The microstructure and hardness were examined using optical microscopy and a Rockwell hardness tester. Rotational ball-on-disk sliding wear tests were carried out to investigate the wear behavior of austempered gray cast iron samples and to compare with conventional quenched and tempered gray cast iron samples under equivalent hardness. For the austempered samples, it was found that acicular ferrite and carbon saturated austenite were formed in the matrix. The ferritic platelets became coarse when increasing the austempering temperature or extending the holding time. Hardness decreased due to a decreasing amount of martensite in the matrix. In wear tests, austempered gray cast iron samples showed slightly higher wear resistance than quenched and tempered samples under similar hardness while using the austempering temperatures of 232 ◦C, 260 ◦C, 288 ◦C, and 316 ◦C and distinctly better wear resistance while using the austempering temperatures of 343 ◦C and 371 ◦C. -
ITP Metal Casting: Advanced Melting Technologies
Advanced Melting Technologies: Energy Saving Concepts and Opportunities for the Metal Casting Industry November 2005 BCS, Incorporated 5550 Sterrett Place, Suite 306 Columbia, MD 21044 www.bcs-hq.com Advanced Melting Technologies: Energy Saving Concepts and Opportunities for the Metal Casting Industry Prepared for ITP Metal Casting by BCS, Incorporated November 2005 Acknowledgments This study was a collaborative effort by a team of researchers from University of Missouri–Rolla, Case Western Reserve University, and Carnegie Mellon University with BCS, Incorporated as the project coordinator and lead. The research findings for the nonferrous casting industry were contributed by Dr. Jack Wallace and Dr. David Schwam, while the ferrous melting technologies were addressed by Dr. Kent Peaslee and Dr. Richard Fruehan. BCS, Incorporated researched independently to provide an overview of the melting process and the U.S. metal casting industry. The final report was prepared by Robert D. Naranjo, Ji-Yea Kwon, Rajita Majumdar, and William T. Choate of BCS, Incorporated. We also gratefully acknowledge the support of the U.S. Department of Energy and Cast Metal Coalition (CMC) in conducting this study. Disclaimer This report was prepared as an account of work sponsored by an Agency of the United States Government. Neither the United States Government nor any Agency thereof, nor any of their employees, makes any warranty, expressed or implied, or assumes any legal liability or responsibility for the accuracy, completeness, or usefulness of any information, apparatus, product, or process disclosed, or represents that its use would not infringe privately owned rights. Reference herein to any specific commercial product, process, or service by trade name, trademark, manufacturer, or otherwise does not necessarily constitute or imply its endorsement, recommendation, or favoring by the United States Government or any Agency thereof. -
Effect of Melting Process and Aluminium Content on the Microstructure and Mechanical Properties of Fe–Al Alloys
ISIJ International, Vol. 50 (2010), No. 10, pp. 1483–1487 Effect of Melting Process and Aluminium Content on the Microstructure and Mechanical Properties of Fe–Al Alloys Shivkumar KHAPLE, R. G. BALIGIDAD, M. SANKAR and V. V. Satya PRASAD Defence Metallurgical Research Laboratory, Kanchanbagh, Hyderabad, 500058 India. E-mail: [email protected] (Received on January 4, 2010; accepted on July 1, 2010) This paper presents the effect of air induction melting with flux cover (AIMFC) versus vacuum induction melting (VIM) on the recovery of alloying element, reduction of impurities, workability and mechanical prop- erties of Fe–(7–16mass%)Al alloys. Three Fe–Al alloy ingots containing 7, 9 and 16 mass% Al were prepared by both AIMFC and VIM. All these ingots were hot-forged and hot-rolled at 1 373 K and were further charac- terized with respect to chemical composition, microstructure and mechanical properties. The recovery of aluminium as well as reduction of oxygen during both AIMFC and VIM is excellent. AIMFC ingots exhibit low level of sulphur and high concentration of hydrogen as compared to VIM ingots. VIM ingots of all the three alloys were successfully hot worked. However, AIMFC ingots of only those Fe–Al alloys containing lower concentration of aluminium could be hot worked. The tensile properties of hot-rolled Fe–7mass%Al alloy produced by AIMFC and VIM are comparable. The present study clearly demonstrates that it is feasible to produce sound ingots of low carbon Fe–7mass%Al alloy by AIMFC process with properties comparable to the alloy produced by VIM. KEY WORDS: air inducting melting with flux cover; vacuum induction melting; Fe–Al alloy; microstructure; mechanical properties. -
BAT Guide for Electric Arc Furnace Iron & Steel Installations
Eşleştirme Projesi TR 08 IB EN 03 IPPC – Entegre Kirlilik Önleme ve Kontrol T.C. Çevre ve Şehircilik Bakanlığı BAT Guide for electric arc furnace iron & steel installations Project TR-2008-IB-EN-03 Mission no: 2.1.4.c.3 Prepared by: Jesús Ángel Ocio Hipólito Bilbao José Luis Gayo Nikolás García Cesar Seoánez Iron & Steel Producers Association Serhat Karadayı (Asil Çelik Sanayi ve Ticaret A.Ş.) Muzaffer Demir Mehmet Yayla Yavuz Yücekutlu Dinçer Karadavut Betül Keskin Çatal Zerrin Leblebici Ece Tok Şaziye Savaş Özlem Gülay Önder Gürpınar October 2012 1 Eşleştirme Projesi TR 08 IB EN 03 IPPC – Entegre Kirlilik Önleme ve Kontrol T.C. Çevre ve Şehircilik Bakanlığı Contents 0 FOREWORD ............................................................................................................................ 12 1 INTRODUCTION. ..................................................................................................................... 14 1.1 IMPLEMENTATION OF THE DIRECTIVE ON INDUSTRIAL EMISSIONS IN THE SECTOR OF STEEL PRODUCTION IN ELECTRIC ARC FURNACE ................................................................................. 14 1.2 OVERVIEW OF THE SITUATION OF THE SECTOR IN TURKEY ...................................................... 14 1.2.1 Current Situation ............................................................................................................ 14 1.2.2 Iron and Steel Production Processes............................................................................... 17 1.2.3 The Role Of Steel Sector in -
Historic Lighthouse Preservation: IRON WPTC Photo Figure 1
Historic Lighthouse Preservation: IRON WPTC photo Figure 1. Cast-iron-and-steel skeletal 191-foot-tall tower at Cape Charles, Virginia Second to masonry, iron was the most Iron was also used for the production of common lighthouse construction material. architectural trim features such as gallery For lighthouse construction, iron was used deck brackets, entryway pilasters and in a variety of its commercially pediments, doors, and prefabricated lantern manufactured alloys: wrought iron, cast components. These iron features were used iron, steel, galvanized iron and steel, and on masonry and wood as well as iron stainless steel. In historic lighthouses the lighthouses. Other iron alloys such as steel, most widely used alloy was cast iron. The galvanized iron and steel, and stainless steel use of cast iron in lighthouse construction are mostly found in modern additions such ranged from simple prefabricated lanterns as handrails, equipment brackets, security to caisson-style foundations to 190-foot-tall doors, etc. first-order coastal towers. For more on the This section will discuss the preservation of variety of iron lighthouse construction types iron alloys used in lighthouse tower refer to Part II., History of the Lighthouse construction and decoration. Because of Service and Lighthouse Construction their similar properties, the various iron Types. alloys will be discussed together; special treatments concerning a specific alloy will Historic Lighthouse Preservation Handbook Part IV. B, Page 1 WPTC photo Figure 2. Example of a keeper's quarters fitted with a prefabricated cast-iron-and-steel lantern. WPTC photo Figure 4. Double-wall, cast-iron, first-order 163-foot-tall WPTC photo coastal tower at Cape Henry, Virginia. -
The Importance of Sic in the Process of Melting Ductile Iron with a Variable Content of Charge Materials
materials Article The Importance of SiC in the Process of Melting Ductile Iron with a Variable Content of Charge Materials Krzysztof Janerka 1 , Łukasz Kostrzewski 2, Marcin Stawarz 1 and Jan Jezierski 1,* 1 Department of Foundry Engineering, Silesian University of Technology, 7 Towarowa, 44-100 Gliwice, Poland; [email protected] (K.J.); [email protected] (M.S.) 2 LFP Ltd., 15 Fabryczna, 64-100 Leszno, Poland; [email protected] * Correspondence: [email protected]; Tel.: +48-32-338-5551 Received: 15 February 2020; Accepted: 6 March 2020; Published: 9 March 2020 Abstract: The article presents issues related to melting ductile iron grade EN-GJS-400-15, with different proportions of feedstock (steel scrap and pig iron). The main attention was paid to determining the impact of silicon carbide on the structure and properties of melted cast iron. In the conducted melts, carbon and silicon deficiencies were supplemented with a suitably chosen carburizer, ferrosilicon, and SiC metallurgical silicon carbide. The percentage of silicon carbide in the charge ranged from 0 to 0.91%. The basic condition for the planning of melts was to maintain the repeatability of the chemical composition of the output cast iron and cast iron after the secondary treatment of liquid metal with various charge compositions. Based on the tests, calculations, and analyses of the results obtained, it was concluded that the addition of SiC may increase the number and size of graphite precipitates. Increasing the SiC content in the charge also caused a change in the solidification nature of the alloy and the mechanism of growth of spheroidal graphite precipitates, causing their surface to form a scaly shell. -
Feasibility of Solid-State Steelmaking from Cast Iron -Decarburization of Rapidly Solidified Cast Iron
ISIJ International, Vol. 52 (2012), No. 1, pp. 26–34 Feasibility of Solid-state Steelmaking from Cast Iron -Decarburization of Rapidly Solidified Cast Iron- Ji-Ook PARK, Tran Van LONG and Yasushi SASAKI Graduate Institute of Ferrous Technology (GIFT), Pohang University of Science and Technology (POSTECH), Hyoja-dong, Pohang, 790-784 South Korea. (Received on September 6, 2011; accepted on September 29, 2011) To meet the unprecedented demand of environmental issues and tightened production cost, steel industry must develop the disruptively innovative process. In the present study, totally new steelmaking process of ‘Solid State Steelmaking’ (or S3 process) without BOF process or liquid state oxidation process is proposed. The overview of the new process is as follows: (1) High carbon liquid iron from the ironmak- ing processes is directly solidified by using a strip casting process to produce high carbon thin sheets. (2) Then, the produced cast iron sheet is decarburized by introducing oxidizing gas of H2O or CO2 in a con- tinuous annealing line to produce low carbon steel sheets. The most beneficial aspect of the S3 process is the elimination of several steps such as BOF, and secondary refinement processes and no formation of inclusions. To investigate the feasibility of S3 process, the cast iron strips with various high carbon content produced by a centrifugal slip casting method are decarburized at 1 248 K and 1 373 K by using H2O–H2 gas mixture and its kinetics of the decarburization is investigated. In the decarburization process, the car- bon diffusion through the decarburized austenite phase but not the decomposition of cementite is the rate controlling step of the decarburizing process. -
The Carburization Process Rates in Synthetic Cast Iron Production
VOLUME 18 ISSUE 1-2 of Achievements in Materials September–October and Manufacturing Engineering 2006 The carburization process rates in synthetic cast iron production K. Janerka, D. Bartocha*, J. Szajnar Division of Foundry, Institute of Engineering Materials and Biomaterials, Silesian University of Technology, ul. Konarskiego 18a, 44-100 Gliwice, Poland * Corresponding author: E-mail address: [email protected] Received 15.03.2006; accepted in revised form 30.04.2006 Manufacturing and processing AbstrAct Purpose: The aim of presented researches was determination of possibility of synthetic cast iron production on base of steel and process scrap as well as determination of carburization effectiveness, realized with three methods: addition of carburizer to charge in solid, addition of carburizer on surface of liquid metal, pneumatic injection of carburizer in stream of carrying gas to liquid metal. Design/methodology/approach: Each of these methods have a undoubted advantages but also have a number of disadvantages. In foundry engineering practice the most essential parameters of this process are to obtain as high as possible degree of carbon assimilation from carburizer, in as short as possible time, with high process repeatability. Findings: Decrease of share or elimination of the pig iron from charge materials causes significant reduction of cast iron melt costs. Working out the effective and repeatable crburization method is a very important issue. Research limitations/implications: The result of carburization in arc electric furnaces experiments carried out by the authors of this paper made possibility on application method of pneumatic carburization in a dozen of domestic foundries. Presented below researches concern inductive furnaces, which are a wide group of melting furnaces applied in foundry engineering. -
The Best Solution for Steel and Cast Iron Milling!
Keeping the Customer First Tungaloy Report No. 358-EE Screw-on type TAC Mills type The best solution for steel and cast iron milling! Exact simulation analysis provides light weight cutter with low cutting Exceptional rigidity improves performance ● Analysis of the load transmission route Need high rigidity and low cutting forces Area with low effect on rigidity This is an area for weight reduction Conventional face mill TAW13 type 20 to 30% lighter than competitors cutters. Lighter than conventional TAC mills by 5 to 10%. Features Low cutting forces and reliability for impact resistance Contributes to free cutting action with extremely high toughness levels. Competitor Large rake angle 27˚ 27° rake angle! Exceptionally low cutting forces! (In ML-type chipbreaker) Axial rake angle Double-relief geometry Competitor The peripheral cutting edges with utter two-step relief increase edge Rotating direction of c strength. Peripheral cutting edge Comparison of impact resistance ■ ■Comparison of cutting forces Work material : Carbon steel Work material : Carbon steel 10 (JIS S50C), 280HRC 2500 (JIS S55C), 280HB TAW13 type (MJ insert) Tangential Machine : BT50 Machine : BT50 force Competitor A Cutting speed : Vc = 150 m/min 8 Cutting speed : Vc = 150 m/min 2000 Ymax Competitor B Feed rate : fz = 0.05 ~ 0.3 mm/t Feed rate : fz = 0.3 mm/t Depth of cut : ap = 3.0 mm Depth of cut : ap = 2.0 mm 1500 6 (N) Cutting width : ae = 80 mm (m) Cutting width : ae = 50 mm Axial force YC 4 200 1000 Feed Zmax Feed 2 500 XC Cutting forces Cutting length 0 100 0 TAW13 Existing Competitor Competitor 0 0.05 0.1 0.15 0.2 0.25 0.3 0.35 type TAC mill A B (MJ insert) Feed per tooth fz (mm/t) ZC 2 a highly rigid, forces !! High productivity Bodies are available in coarse, close, and extra-close (made to order) pitch design. -
Effect of Tempering Temperature and Time on Strength and Hardness of Ductile Cast Iron
EFFECT OF TEMPERING TEMPERATURE AND TIME ON STRENGTH AND HARDNESS OF DUCTILE CAST IRON This thesis Submitted In Partial Fulfilment of The requirement For the Degree of Master of Technology ( DUAL DEGREE ) In Metallurgical and Materials Engineering By RAVINDRA KUMAR (Roll no. 710MM1165) Under the Guidance of Dr. Sudipta Sen 2015 1 CERTIFICATE This is to certify that the thesis qualified, “Effect of Tempering Temperature and Time on Strength and Hardness of Ductile Cast Iron” submitted by Ravindra Kumar (710MM1165) for requirements Master of Technology degree in metallurgical & Materials Engineering at National Institute of Technology, Rourkela is a genuine work carried out under my guidance and supervision. Dr. Sudipta Sen Associate professor Department of Metallurgical and Materials Engineering National Institute of Technology Rourkela-769008, Odisha 2 ACKNOWLEDGEMENT I would like to express my sincere gratitude to Dr. Sudipta Sen, Department of Metallurgical and Materials Engineering for assigning me the project “Effect of Tempering Temperature and Time on Strength and Hardness of Ductile Cast Iron” His positive behavior and regular guidance made it possible to understand this project better . It is not possible to acknowledge suitable his important contribution of our knowledge and time given selflessly in proceeding with my project work. I have received infinite support and good guidance from him. I am very grateful to our all professors of Metallurgical and materials engineering department. And Mr. Ranjan Kumar Behera, Ph.D. Scholar, and all my Classmate and my M.Tech friends to given excellent support for helping me throughout the project and providing me with lot of information and support as and when I required. -
Zcmi Cast Iron Facade Restoration
ZCMI CAST IRON FACADE RESTORATION FEATURED PRODUCTS Series 90-97 Tneme-Zinc Series 66 Hi-Build Epoxoline Series N69 Hi-Build Epoxoline II PROJECT INFORMATION Series 135 Chembuild Series 215 Surfacing Epoxy Series 1072 Fluoronar Series 1078 Fluoronar Metallic Series 1079-0762 Metallic Clearcoat Project Location Salt Lake City, Utah Although separated by more than 135 years, the first major department store in Salt Lake City, Utah, and the city’s newest retail destination share one thing in common - a Project Completion Date historic cast iron façade restored with an advanced fluoropolymer coating system from Spring 2011 Tnemec. “The amount of craftsmanship and handiwork that goes into restoring cast iron architecture like this is unbelievable,” Tnemec coating consultant Michelle Call explained. Owner “That’s why landmark projects require high-performance coating systems.” City Creek Reserve, Inc. Salt Lake City, Utah The iconic façade, which is listed on the National Register of Historic Places, belonged to Zion’s Cooperative Mercantile Institution (ZCMI) founded by Brigham Young in 1868. Engineer The 75-foot high by 140-foot long facade features cast iron colonnades with ornamental Historical Arts & Casting, Inc. castings and a cornice section made of galvanized metal. The façade is now part of the West Jordan, Utah new Macy’s department store in the downtown City Creek development. Applicator During restoration, original cast iron and replacement pieces re-cast in aluminum were Daniels Painting prepared by abrasive blast cleaning and shop-primed with an epoxy coating that doubled Salt Lake City, Utah as field-applied tie coat. Specified primers were Series 90-97 Tneme-Zinc, Series 66 Hi- Build Epoxoline and Series N69 Hi-Build Epoxoline II. -
Corrosion of Steel and Two Types of Cast Iron in Soil
Corrosion of Steel and Two Types of Cast Iron in Soil WILLIAM A. PENNINGTON Physical Scientist, Division of Research, Bureau of Reclamation, Denver, Colorado Of the three pipe materials, steel and gray and ductile cast irons, steel is the best for a given thickness where buried bare in soil, although gray cast iron in larger commercial sizes is the only one not requiring an external coating for a service life of 50 years. The underground pitting corrosion study subjected National Bureau of Standards data to an interpretive technique developed at the U.S. Bureau of Reclamation. Pit depth rela- tions given as two types of equations have been established for the three materials. Ductile cast iron, made according to manufacturer's schedule, has about the same service life as steel in "severely corrosive" soil, even though its pitting rate is greater than either steel or gray cast iron. •THROUGH years of experience in installing water-conveying metal pipes in soil, the Bureau of Reclamation has learned that plain carbon steel, properly coated externally, is the most economical of the wrought metals. Consequently, a very high percentage of such installations are steel. One of the main objectives in this study has been to examine the experimental soil corrosion data of the National Bureau of Standards (NBS) for wrought metals to ascertain whether these data can be employed to reach the same conclusion. Having demonstrated that reliable experimental data can be so used, simi lar data for gray and ductile cast irons have been compared with those for steel to pre dict the relative performance of these three materials.