Natural Fiber Composites for Space Applications
Total Page:16
File Type:pdf, Size:1020Kb
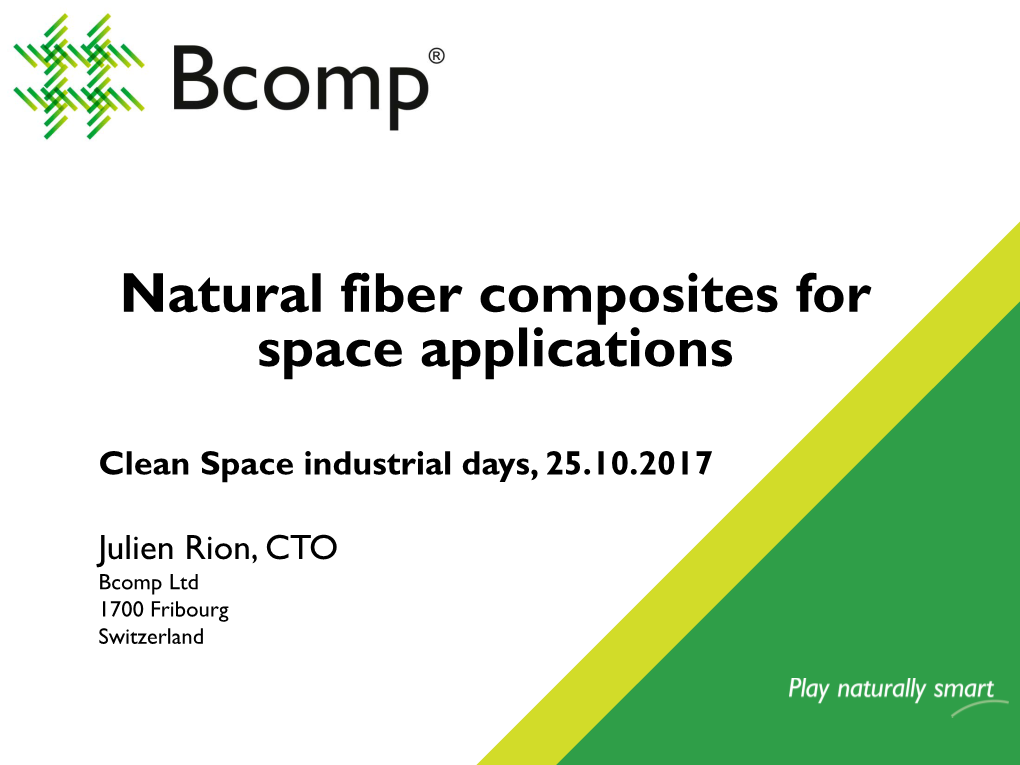
Load more
Recommended publications
-
Investigation of the Mechanical Properties of a Carbon Fibre-Reinforced Nylon Filament for 3D Printing
machines Article Investigation of the Mechanical Properties of a Carbon Fibre-Reinforced Nylon Filament for 3D Printing Flaviana Calignano 1,* , Massimo Lorusso 2 , Ignanio Roppolo 3 and Paolo Minetola 1 1 Department of Management and Production Engineering, Politecnico di Torino, Corso Duca degli Abruzzi 24, 10129 Turin, Italy; [email protected] 2 Istituto Italiano di Tecnologia, Center for Sustainable Future Technologies IIT@Polito, Corso Trento 21, 10129 Turin, Italy; [email protected] 3 Department of Applied Science and Technology, Politecnico di Torino, Corso Duca degli Abruzzi 24, 10129 Turin, Italy; [email protected] * Correspondence: fl[email protected]; Tel.: +39-011-090-7218 Received: 19 July 2020; Accepted: 2 September 2020; Published: 4 September 2020 Abstract: Additive manufacturing (i.e., 3D printing) has rapidly developed in recent years. In the recent past, many researchers have highlighted the development of in-house filaments for fused filament fabrication (FFF), which can extend the corresponding field of application. Due to the limited mechanical properties and deficient functionality of printed polymer parts, there is a need to develop printable polymer composites that exhibit high performance. This study analyses the actual mechanical characteristics of parts fabricated with a low-cost printer from a carbon fibre-reinforced nylon filament. The results show that the obtained values differ considerably from the values presented in the datasheets of various filament suppliers. Moreover, the hardness and tensile strength are influenced by the building direction, the infill percentage, and the thermal stresses, whereas the resilience is affected only by the building direction. Furthermore, the relationship between the mechanical properties and the filling factor is not linear. -
Natural Fibers and Fiber-Based Materials in Biorefineries
Natural Fibers and Fiber-based Materials in Biorefineries Status Report 2018 This report was issued on behalf of IEA Bioenergy Task 42. It provides an overview of various fiber sources, their properties and their relevance in biorefineries. Their status in the scientific literature and market aspects are discussed. The report provides information for a broader audience about opportunities to sustainably add value to biorefineries by considerin g fiber applications as possible alternatives to other usage paths. IEA Bioenergy Task 42: December 2018 Natural Fibers and Fiber-based Materials in Biorefineries Status Report 2018 Report prepared by Julia Wenger, Tobias Stern, Josef-Peter Schöggl (University of Graz), René van Ree (Wageningen Food and Bio-based Research), Ugo De Corato, Isabella De Bari (ENEA), Geoff Bell (Microbiogen Australia Pty Ltd.), Heinz Stichnothe (Thünen Institute) With input from Jan van Dam, Martien van den Oever (Wageningen Food and Bio-based Research), Julia Graf (University of Graz), Henning Jørgensen (University of Copenhagen), Karin Fackler (Lenzing AG), Nicoletta Ravasio (CNR-ISTM), Michael Mandl (tbw research GesmbH), Borislava Kostova (formerly: U.S. Department of Energy) and many NTLs of IEA Bioenergy Task 42 in various discussions Disclaimer Whilst the information in this publication is derived from reliable sources, and reasonable care has been taken in its compilation, IEA Bioenergy, its Task42 Biorefinery and the authors of the publication cannot make any representation of warranty, expressed or implied, regarding the verity, accuracy, adequacy, or completeness of the information contained herein. IEA Bioenergy, its Task42 Biorefinery and the authors do not accept any liability towards the readers and users of the publication for any inaccuracy, error, or omission, regardless of the cause, or any damages resulting therefrom. -
All About Fibers
RawRaw MaterialsMaterials ¾ More than half the mix is silica sand, the basic building block of any glass. ¾ Other ingredients are borates and trace amounts of specialty chemicals. Return © 2003, P. Joyce BatchBatch HouseHouse && FurnaceFurnace ¾ The materials are blended together in a bulk quantity, called the "batch." ¾ The blended mix is then fed into the furnace or "tank." ¾ The temperature is so high that the sand and other ingredients dissolve into molten glass. Return © 2003, P. Joyce BushingsBushings ¾The molten glass flows to numerous high heat-resistant platinum trays which have thousands of small, precisely drilled tubular openings, called "bushings." Return © 2003, P. Joyce FilamentsFilaments ¾This thin stream of molten glass is pulled and attenuated (drawn down) to a precise diameter, then quenched or cooled by air and water to fix this diameter and create a filament. Return © 2003, P. Joyce SizingSizing ¾The hair-like filaments are coated with an aqueous chemical mixture called a "sizing," which serves two main purposes: 1) protecting the filaments from each other during processing and handling, and 2) ensuring good adhesion of the glass fiber to the resin. Return © 2003, P. Joyce WindersWinders ¾ In most cases, the strand is wound onto high-speed winders which collect the continuous fiber glass into balls or "doffs.“ Single end roving ¾ Most of these packages are shipped directly to customers for such processes as pultrusion and filament winding. ¾ Doffs are heated in an oven to dry the chemical sizing. Return © 2003, P. Joyce IntermediateIntermediate PackagePackage ¾ In one type of winding operation, strands are collected into an "intermediate" package that is further processed in one of several ways. -
Carbon Fiber Supply and Demand
Carbon Fiber Supply and Demand Supply of PAN based carbon fiber New players could make all the difference San Diego, California, USA October 23 2007 The ongoing shortage of PAN based carbon fibers has seen the planning, development and realization of new carbon fiber manufacturing capacity in new countries. The start up of new plant faces many hurdles, especially in the face of competition that has been in the business for many decades. However these hurdles have been overcome and this process will enable carbon fiber to become truly a commodity product, available to the vast range of current and new composite applications. Latest News (Press releases in the last 4 weeks) Supply October 11, 2007 Capacity Expansion of Carbon Fiber “TENAX®” Toho Tenax Co., Ltd. (Head Office: Bunkyo-ku, Tokyo, President: Yoshikuni Utsunomiya), which is engaged in the business of carbon fibers within the Teijin Group, has decided to add a new carbon fiber production line at Toho Tenax Europe GmbH (located at Wuppertal, Germany. October 05, 2007 SGL Group plans to triple carbon fiber capacities SGL Group plans to triple carbon fiber capacities Capacity increase up to 12,000 metric tons by 2012 Demand September 27, 2007 British Airways Green light for aircraft orders British Airways has today placed an order for 12 Airbus A380 and 24 Boeing 787 aircraft with options for a further seven Airbus A380s and18 Boeing 787s. The British Airways Order The new aircraft will replace 34 of the airline's long haul fleet and will be delivered between 2010 and 2014. The order, including options, will give the airline the ability to grow its capacity by up to four per cent per year and the flexibility to tailor its future capacity growth in line with market conditions. -
Basic of Textiles
BASIC OF TEXTILES BFA(F) 202 CC 5 Directorate of Distance Education SWAMI VIVEKANAND SUBHARTI UNIVERSITY MEERUT 250005 UTTAR PRADESH SIM MOUDLE DEVELOPED BY: Reviewed by the study Material Assessment Committed Comprising: 1. Dr. N.K.Ahuja, Vice Chancellor Copyright © Publishers Grid No part of this publication which is material protected by this copyright notice may be reproduce or transmitted or utilized or store in any form or by any means now know or here in after invented, electronic, digital or mechanical. Including, photocopying, scanning, recording or by any informa- tion storage or retrieval system, without prior permission from the publisher. Information contained in this book has been published by Publishers Grid and Publishers. and has been obtained by its author from sources believed to be reliable and are correct to the best of their knowledge. However, the publisher and author shall in no event be liable for any errors, omission or damages arising out of this information and specially disclaim and implied warranties or merchantability or fitness for any particular use. Published by: Publishers Grid 4857/24, Ansari Road, Darya ganj, New Delhi-110002. Tel: 9899459633, 7982859204 E-mail: [email protected], [email protected] Printed by: A3 Digital Press Edition : 2021 CONTENTS 1. Fiber Study 5-64 2. Fiber and its Classification 65-175 3. Yarn and its Types 176-213 4. Fabric Manufacturing Techniques 214-260 5. Knitted 261-302 UNIT Fiber Study 1 NOTES FIBER STUDY STRUCTURE 1.1 Learning Objective 1.2 Introduction 1.3 Monomer, Polymer, Degree of polymerization 1.4 Student Activity 1.5 Properties of Fiber: Primary & Secondary 1.6 Summary 1.7 Glossary 1.8 Review Questions 1.1 LEARNING OBJECTIVE After studying this unit you should be able to: ● Describe the Natural Fiber. -
Flax, Jute, Hemp, Glass and Carbon Fibers
fibers Article Direct Comparison of the Structural Compression Characteristics of Natural and Synthetic Fiber-Epoxy Composites: Flax, Jute, Hemp, Glass and Carbon Fibers Mike R. Bambach Department of Civil Engineering, The University of Sydney, Sydney, NSW 2006, Australia; [email protected]; Tel.: +61-2-9351-2193 Received: 8 September 2020; Accepted: 25 September 2020; Published: 28 September 2020 Abstract: Recent decades have seen substantial interest in the use of natural fibers in continuous fiber reinforced composites, such as flax, jute and hemp. Considering potential applications, it is of particular interest how natural fiber composites compare to synthetic fiber composites, such as glass and carbon, and if natural fibers can replace synthetic fibers in existing applications. Many studies have made direct comparisons between natural and synthetic fiber composites via material coupon testing; however, few studies have made such direct comparisons of full structural members. This study presents compression tests of geometrically identical structural channel sections fabricated from fiber-epoxy composites of flax, jute, hemp, glass and carbon. Glass fiber composites demonstrated superior tension material coupon properties to natural fiber composites. However, for the same fiber mass, structural compression properties of natural fiber composite channels were generally equivalent to, or in some cases superior to, glass fiber composite channels. This indicates there is substantial potential for natural fibers to replace glass fibers in structural -
A Supertough Electro-Tendon Based on Spider Silk Composites
ARTICLE https://doi.org/10.1038/s41467-020-14988-5 OPEN A supertough electro-tendon based on spider silk composites Liang Pan1, Fan Wang2, Yuan Cheng 3, Wan Ru Leow1, Yong-Wei Zhang3, Ming Wang1, Pingqiang Cai 1, ✉ ✉ Baohua Ji4, Dechang Li 4 & Xiaodong Chen 1 Compared to transmission systems based on shafts and gears, tendon-driven systems offer a simpler and more dexterous way to transmit actuation force in robotic hands. However, 1234567890():,; current tendon fibers have low toughness and suffer from large friction, limiting the further development of tendon-driven robotic hands. Here, we report a super tough electro-tendon based on spider silk which has a toughness of 420 MJ/m3 and conductivity of 1,077 S/cm. The electro-tendon, mechanically toughened by single-wall carbon nanotubes (SWCNTs) and electrically enhanced by PEDOT:PSS, can withstand more than 40,000 bending- stretching cycles without changes in conductivity. Because the electro-tendon can simulta- neously transmit signals and force from the sensing and actuating systems, we use it to replace the single functional tendon in humanoid robotic hand to perform grasping functions without additional wiring and circuit components. This material is expected to pave the way for the development of robots and various applications in advanced manufacturing and engineering. 1 Innovative Centre for Flexible Devices (iFLEX), School of Materials Science and Engineering, Nanyang Technological University, 50 Nanyang Avenue, Singapore 639798, Singapore. 2 Biomechanics and Biomaterials Laboratory, Department of Applied Mechanics, Beijing Institute of Technology, Beijing 100081, China. 3 Institute of High Performance Computing, Agency for Science Technology and Research (A*STAR), 1 Fusionopolis Way, Singapore 138632, ✉ Singapore. -
Mechanical Properties of Flax Fibers and Their Composites
ISSN: 1402-1544 ISBN 978-91-86233-XX-X Se i listan och fyll i siffror där kryssen är DOCTORAL T H E SIS Department of Applied Physics and Mechanical Engineering Division of Polymer Engineering Edgars Sp ISSN: 1402-1544 ISBN 978-91-7439-025-4 Mechanical Properties of Flax Fibers Luleå University of Technology 2009 ā rniņš and Their Composites Mechanical Properties of Their Flax Composites Fibers and Edgars Spārniņš Mechanical properties of flax fibers and their composites by Edgars SpƗrniƼš Division of Polymer Engineering Department of Applied Physics and Mechanical Engineering Luleå University of Technology S-971 87 Luleå, SWEDEN October 2009 Printed by Universitetstryckeriet, Luleå 2009 ISSN: 1402-1544 ISBN 978-91-7439-025-4 Luleå www.ltu.se PREFACE The work presented in this thesis concerns flax fibers as a potential replacement of synthetic fibers in conventional polymer composites. The thesis consists of a general introduction and literature review and eight journal papers. Research nowadays often is a result of team work. Therefore there are a couple of persons that I would like to acknowledge. First, I thank my supervisors: Dr. Roberts Joffe, Dr. JƗnis Andersons, Prof. JƗnis VƗrna and Prof. Vitauts Tamužs. I would like to thank my co-authors Dr. Lennart Wallström, Ms. Evija PoriƷe, Dr. Kalle Nättinen and Ms. Johanna Lampinen as well. Further thanks go to Mr. Vilis Skruls and Mr. Uldis Vilks, research engineers from Institute of Polymer Mechanics, Riga, Latvia. They helped with experimental equipment setup for single fiber tensile tests. Mr. Rnjdolfs Livanoviþs is acknowledged for developing the code of fiber image analysis. -
Carbon Fiber Manufacture in Australia?
Carbon Fiber Manufacture in Australia? Vince Kelly, Consultant Engineer Carbon-Fiber Technology www.carbon-fiber.com The ongoing shortage of PAN based carbon fibers has seen the planning, development and realizationCarbon of newFiber carbon Manufacture fiber manufacturing in Australia? capacity in new countries. The start up of new plant faces many hurdles, especially in the face of competition that has been in the business forVince many Kelly, decades. Consultant Engineer Carbon-Fiber Technology However these hurdles have been overcome and this process will enable carbon fiber to become truly a commodity product, available to the vast range www.carbon-fiber.com of current and new composite applications Carbon Fiber Manufacture in Australia? URGENT NOTICE! Due to the severeVince global Kelly, shortage Consultant of carbon fiber,Engineer and in order to continue shipping SOME carbon fabric to our customers, Carbcom will be limiting purchase quantities Carbonand temporarily-Fiber Technologyeliminating bulk pricing. We deeply apologize than Carbcom cannot be the aggressive price leader we have been up until recently, and we hope in the future you will buy larger quantities again when we are able to secure the volume of fibers we need to serve you with www.carbonfull shipments-fiber.com at great pricing! Toll-free 1-888-CARBCOM / (888-227-2266) International call: 1-808-579-8000 The Big 2, Toho Tenax and Toray Global Structure of Toho Tenax Carbon Fiber Manufacture in Australia? PAN Precursor (raw material) Made in Japan and exported to their -
One Design Class Rules
2021 One-Design Section Class Rules The Following Class Rules Shall Apply for Approved One Design Sections: Beneteau 36.7 Beneteau First 36.7 North American One-Design Class Rules February 1, 2019 Beneteau 40.7 Lake Michigan Beneteau 40.7 Fleet Class Rules J/105 J/105 Class Association Rules January 1, 2020 J/105 Class Association Fleet 5, Lake Michigan (Fleet 5) Special Addenda: 2021 Chicago Yacht Club’s Race to Mackinac J/109 J/109 Class Rules February 1, 2020 J109 Amendments and Modifications to Class Rules for the 2020 Chicago to Mackinac Sailing Race as adopted by the J109 Great Lakes and Lake Champlain Fleet 11 J/111 J/111 Class Rules January 1, 2020 J111 Amendments and Modifications to J111 Class Rules for 2020 Chicago to Mackinac Race as adopted by the J111 Lake Michigan fleet #1 Tartan Ten T-10 (Tartan 10) Class Association Class Rules: version 2020.f The Local Rules of the Chicago T-10 Association 1 | P a g e February 1, 2019 Beneteau First 36.7 North American One-Design Class Rules 1. INTRODUCTION / OBJECTIVES 1.1 These rules, as adopted by the “Beneteau First 36.7 North American One Design Class Association” (Class), serve to maintain the First 36.7’s one-design standards and to ensure equal and fair racing among all boats in the class. Wherever possible, these rules will not compromise the First 36.7’s ease of handling, affordability, safety, comfort, and styling. These Rules can be interpreted in two very different ways: an Owner could make the assumption that the Beneteau First 36.7 is a boat that should be able to be continually optimized and modified with very little restriction, causing a further assumption that any changes an Owner chooses are acceptable unless specifically prohibited by these rules. -
E. Coli Derived Spider Silk Masp1 and Masp2 Proteins As Carbon Fiber
E. COLI DERIVED SPIDER SILK MASP 1 AND MASP 2 PROTEINS AS CARBON FIBER PRECURSORS P.I. Randolph V. Lewis Utah State University June 7, 2017 Project ID LM103 This presentation does not contain any proprietary, confidential, or otherwise restricted information Overview Timeline Barriers Start date: November 1, 2014 2.5.1. Lightweight Materials Technology (VTP MYPP 2011- End date: March 31, 2017 2015) Percent complete: 90+% Performance: Match carbon fiber using spider silk instead of PAN Budget • Total project funding Partners – DOE: $1,490,744 • U. of California, Riverside – Contractor share: $497,298 • Funding FY 2015: $997,758 • Oak Ridge Nat’l Laboratory • Funding FY 2016: $990,284 • Utah State University DOE June 7, 2017 1 Relevance Overall Project Objective Reduce the weight of vehicles thereby reducing green house gas emissions and the dependence on foreign oil through the use of carbon fibers produced from spider silk protein fibers Project Goals • Maximize protein production via E. coli while maintaining full-length protein • Develop a Scalable Fiber Spinning process • Improve spider silk fiber mechanical properties • Generate transgenic silkworms producing silk with much higher strength • Determine optimal stabilization conditions for spider silk protein fibers for conversion to carbon fibers • Conduct techno-economic analyses to estimate costs DOE June 7, 2017 Milestones Recipient Name: Randolph V. Lewis, Utah State University Project Title: Spider Silk MaSp1 and MaSp2 Proteins as Carbon Fiber Precursors Task # Task Title Milestone -
Production of Carbon Fibers from Acrylic Fibers
International Conference on Chemical, Civil and Environment engineering (ICCEE'2012) March 24-25, 2012 Dubai Production of Carbon Fibers from Acrylic Fibers R. Eslami Farsani matrix composites. ‘Stronger than steel, stiffer than titanium, Abstract—Carbon fibers are fabricated from different materials and lighter than aluminum’ has become a cliché for carbon such as acrylic fibers, cellulose fibers and pitch. But acrylic fibers are fiber composites and is now being realized in practice [4-7]. recognized as the most widely used precursor for the present-day At present, three precursors including acrylic-based, rayon- manufacture of carbon fibers. The process of fabrication carbon based, and pitch-based fibers are mainly used for the fibers from acrylic fibers is composed of two steps including oxidative stabilization at low temperature and carbonization at high production of carbon fibers. The majority of all carbon fibers temperatures in an inert atmosphere. Today carbon fibers are still used today are made from acrylic precursor [1,6]. Acrylic expensive because of the high price of their raw material. This study fibers manufactured presently are composed of at least 85% focuses on making carbon fibers from acrylic fibers (low price by weight of acrylonitrile (AN) units. The remaining 15% acrylic fibers used in textile industry). The results shows that in case consists of neutral and/or ionic comonomers which are added of conducting complete stabilization process, it is possible to produce to improve the properties of the fibers. Neutral comonomers desirable carbon fibers from commercial acrylic fibers. With some changes in conventional procedure of stabilization in terms of like methyl acrylate (MA), vinyl acetate (VA), or methyl temperature and time of operation, the desirable conditions of methacrylate (MMA) are used to modify the solubility of the complete stabilization are achieved.