(36,747/7%A?Eian M
Total Page:16
File Type:pdf, Size:1020Kb
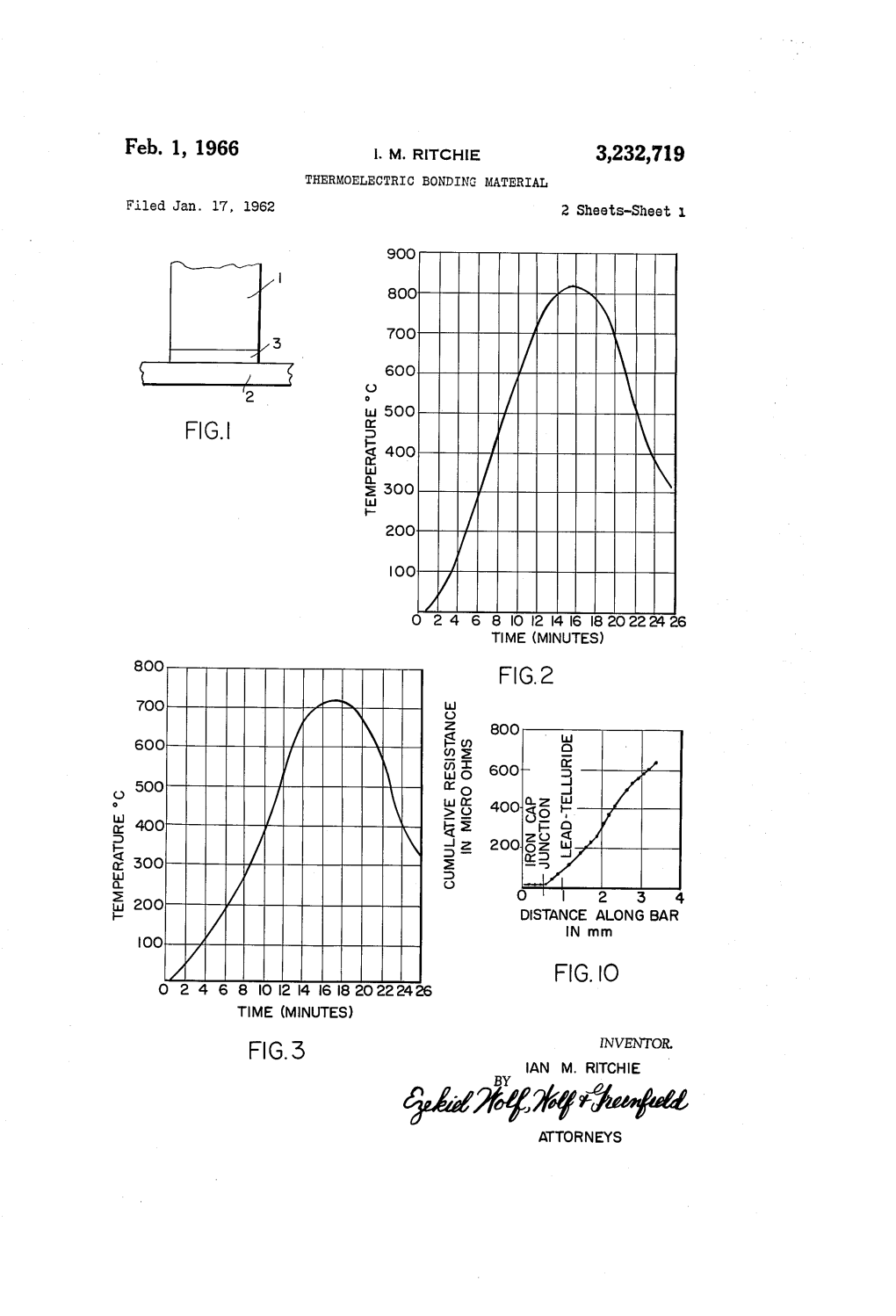
Load more
Recommended publications
-
Enhanced Thermoelectric Performance of Bulk Tin Telluride: Synergistic Effect of Calcium and Indium Co-Doping
Materials Today Physics 4 (2018) 12e18 Contents lists available at ScienceDirect Materials Today Physics journal homepage: https://www.journals.elsevier.com/ materials-today-physics Enhanced thermoelectric performance of bulk tin telluride: Synergistic effect of calcium and indium co-doping * ** D. Krishna Bhat a, , U. Sandhya Shenoy b, a Department of Chemistry, National Institute of Technology Karnataka, Surathkal, Mangalore 575025, India b Department of Chemistry, College of Engineering and Technology, Srinivas University, Mukka, Mangalore 574146, India article info abstract Article history: SnTe based materials are considered recently as a lead-free replacement of the well-known PbTe based Received 27 January 2018 thermoelectric (TE) materials in addressing the energy crisis worldwide. Herein we report both exper- Received in revised form imental and theoretical study on the effect of co-doping of calcium and indium on electronic structure 4 February 2018 and TE properties of SnTe. We show that the resonant levels introduced by indium and band gap opening Accepted 12 February 2018 caused by calcium, valence band convergence induced by both calcium and indium, synergistically in- creases the Seebeck coefficient for a wide range of temperatures. The co-doped SnTe with a high ZT of À À ~1.65 at 840 K and record high power factor of ~47 mWcm 1K 2 for SnTe based materials make it a Keywords: Thermoelectric promising material for TE applications. © Band degeneracy 2018 Published by Elsevier Ltd. Resonant levels Tin telluride Introduction similar crystal and electronic structure. Though safer than PbTe, SnTe suffers a drawback of low ZT due to high carrier concentration Exhaustion of non-renewable fossil fuel resources caused due to resulting out of inherent Sn vacancies, smaller band gap (~0.18 eV) its abuse has resulted in ever increasing energy crisis [1]. -
221 Gaas GRADED A
USOO6403874B1 (12) United States Patent (10) Patent No.: US 6,403,874 B1 Shakouri et al. (45) Date of Patent: *Jun. 11, 2002 (54) HIGH-EFFICIENCY HETEROSTRUCTURE OTHER PUBLICATIONS THERMONIC COOLERS N N. W. Ashcroft, et al., Solid State Physics, manual, 1976, pp. (75) Inventors: Ali Shakouri, Santa Cruz; John E. 318-319, 320-321, 362-363. Bowers, Santa Barbara, both of CA D. A. Broido et al., “Effect of Superlattice structure on the (US) th ermoelectriclectric fiIlgure OIf meril:t: , Theline Am erican PhPinySIca 1 Society (Physical Review B.), vol. 51, No. 19, May 15, (73) Assignee: The Regents of the University of 1995, pp. 13797-800. California, Oakland, CA (US) D. A. Broido et al., “Comment of Use of quantum well Superlattices to obtain high figure of merit from nonconven (*) Notice: Subject to any disclaimer, the term of this tional thermoelectric materials”, Appl. Phys. Lett. 63, 3230 patent is extended or adjusted under 35 (1993), Applied Physics Letters, vol. 67, No. 8, Aug. 21, U.S.C. 154(b) by 0 days. 1995, pp. 1170–1171. D. A. Broido et al., “Thermoelectric figure or merit of This patent is Subject to a terminal dis- quantum wire Superlattices”, Applied Physics Letters, Jul. 3, claimer. 1995, vol. 67, No. 1, 100-102. (21) Appl. No.: 09/441,787 (List continued on next page.) (22) Filed: Nov. 17, 1999 Primary Examiner—Bruce F. Bell ASSistant Examiner Thomas H Parsons Related U.S. Application Data (74) Attorney, Agent, or Firm-Gates & Cooper LLP (60) Pisional application No. 60/109,342, filed on Nov. -
PRAJNA - Journal of Pure and Applied Sciences ISSN 0975 2595 Volume 19 December 2011 CONTENTS
PRAJNA - Journal of Pure and Applied Sciences ISSN 0975 2595 Volume 19 December 2011 CONTENTS BIOSCIENCES Altered energy transfer in Phycobilisomes of the Cyanobacterium, Spirulina Platensis under 1 - 3 the influence of Chromium (III) Ayya Raju, M. and Murthy, S. D. S. PRAJNA Volume 19, 2011 Biotransformation of 11β , 17 α -dihydroxy-4-pregnene-3, 20-dione-21-o-succinate to a 4 - 7 17-ketosteroid by Pseudomonas Putida MTCC 1259 in absence of 9α -hydroxylase inhibitors Rahul Patel and Kirti Pawar Influence of nicking in combination with various plant growth substances on seed 8 - 10 germination and seedling growth of Noni (Morinda Citrifolia L.) Karnam Jaya Chandra and Dasari Daniel Gnana Sagar Quantitative analysis of aquatic Macrophytes in certain wetlands of Kachchh District, 11 - 13 Journal of Pure and Applied Sciences Gujarat J.P. Shah, Y.B. Dabgar and B.K. Jain Screening of crude root extracts of some Indian plants for their antibacterial activity 14 - 18 Purvesh B. Bharvad, Ashish R. Nayak, Naynika K. Patel and J. S. S. Mohan ________ Short Communication Heterosis for biometric characters and seed yield in parents and hybrids of rice 19 - 20 (Oryza Sativa L.) M. Prakash and B. Sunil Kumar CHEMISTRY Adsorption behavior and thermodynamics investigation of Aniline-n- 21 - 24 (p-Methoxybenzylidene) as corrosion inhibitor for Al-Mg alloy in hydrochloric acid V.A. Panchal, A.S. Patel and N.K. Shah Grafting of Butyl Acrylate onto Sodium Salt of partially Carboxymethylated Guar Gum 25 - 31 using Ceric Ions J.H. Trivedi, T.A. Bhatt and H.C. Trivedi Simultaneous equation and absorbance ratio methods for estimation of Fluoxetine 32 - 36 Hydrochloride and Olanzapine in tablet dosage form Vijaykumar K. -
Activity 8 How Atoms Interact with Each Other
CS_Ch7_PeriodicTbl 4/27/06 1:45 PM Page 442 The Periodic Table Activity 8 How Atoms Interact with Each Other GOALS What Do You Think? In this activity you will: You have learned that the chemical behavior of an atom is • Relate patterns in ionization determined by the arrangement of the atom’s electrons, energies of elements to specifically the valence electrons. The salt that you put on patterns in electron your food is chemically referred to as NaCl—sodium chloride. arrangements. • Use your knowledge of • How might the valence electrons of sodium (Na) and electron arrangements and chlorine (Cl) interact to create this bond? valence electrons to predict formulas for compounds Record your ideas about this question in your Active formed by two elements. Chemistry log. Be prepared to discuss your responses with • Contrast ionic bonding and your small group and the class. covalent bonding. • Draw electron-dot diagrams Investigate for simple molecules with 1. In Activity 3 you read that John Dalton assumed that covalent bonding. chemical compounds formed from two elements combined in the simplest possible combination—one atom of each element. In Activity 6 you began to see that an atom’s chemical behavior reflects its excess or deficiency of electrons relative to an atom of the closest noble gas on the periodic table. Use the list of ionization energies in Activity 6 to answer the following questions: 442 Active Chemistry CS_Ch7_PeriodicTbl 2/28/05 10:04 AM Page 443 Activity 8 How Atoms Interact with Each Other a) Which atoms have the smallest stable electron arrangement as neon. -
D. I. Bletskan "Phase Equilibrium in the Binary Systems a IV
Journal of Ovonic Research Vol. 1, No. 5, October 2005, p. 53 - 60 PHASE EQUILIBRIUM IN THE SYSTEMS AIV – BVI Part. II Systems Germanium-Chalcogen D. I. Bletskan* Uzhgorod University, Uzhgorod, Ukraine The phases in the system germanium – chalcogen are reviewed. The phase transitions are discussed. 1.4 System Ge-S The phase diagram T-x of the binary system Ge-S has been firstly built by A. V. Novoselova et al. [39] using the data of thermal and X-ray analysis. Thereafter, the regions of the phase diagrams of the system Ge-S in the neighborhood of GeS and GeS2 have been carefully determined in [40-44] and are represented in Fig. 1.4. In this system there were found two stable chemical compounds, whose stoichiometric compositions correspond to GeS and GeSe2. The temperature conditions of GeS and GeS2 synthesis, the melting character and melting temperature, given in the literature, are different. Thus, the melting temperature of GeS, after the data of various authors are 938 K [39, 42], 940 K [40], 931 K [41, 46]. Many research reports [39, 42-44] show that GeS compound melts congruently. Nevertheless, in the papers [40, 41, 46] is demonstrated that, during very slow heating, GeS melts incongruently, according to the peritectic reaction: GeS(solid) = Ge(solid) + Liq(53 at.% S) (1.4) In the system Ge-S, on the germanium side, there is a large domain (3÷45 at.% S) of layer separation in the liquid state (stratification) with one phase rich in germanium and a phase with the composition approaching GeS. -
Kohn Et Al. [45] Sept. 25, 1973
“9-25-73 i'XR 367616718. _ , UnIted States Patent 1191 ~ _ 1111 3,761,718 Kohn et al. [45] Sept. 25, 1973 [54] DETECTOR APPARATUS USING 2,949,498 8/1960 Jackson ........................ .. 250/212 x SEMICONDUCTOR LAMINAE 3,324,298 6/1967 Waer . _ . .. 250/211 ‘3,191,045 6/1965 c61man..... 250/211 [75] Inventors: Alan N- Kohn. Brookline; Jack K. 3,473,214 11/1969 Dillman ............................ .. 250/211 Lennard, Framingham', Jay ,1. ' ' Schlickman, Lexington; Robert A. FOREIGN PATENTS OR APPLICATIONS weagan" Chelmsford, 3“ of Mass- 629,924 10/1961 Canada ............................. .. 250/226 [73] Assignee: Honeywell Inc“ Minneapolis’ Minn. 1,043,662 4/l959 Germany .... .................... .. 250/226 [22] Filed: Sept- 7. 1972 OTHER PUBLICATIONS [21] Appl' No'i 287’l94 Marinace; IBM Technical Disclosure Bulletin; Vol. 1 1; Related US. Application Data No. 4; 9/68; p. 398. [63] Continuation-impart of Ser. No. 855,9l8, Sept. 8, 1969' abandoned‘ Primary Examiner-Walter Stolwein AtI0rney—Charles J. Ungemach et al. [521 U.s.c1 ........ ..250/211R,250/226,3l7/235 N, ‘ 356/99, 350/316 [51] Int. Cl. ............................................ ..G0lj3/34 , [581FieldofSearch ................... ..250/211J,211R, [571 ABSTRAQT 250/212’ 226; 317/235 N; 350/316; 356/99’ ‘00 A new multi-layer semiconductor photo detector ar rangement, and scienti?c instruments embodying the [56] References Cited underlying novel principle. UNITED STATES PATENTS 2,896,086 7/1959 Wunderman ..................... .. 250/211 14 Claims, 10 Drawing Figures 3,761,718 1 2 DETECTOR APPARATUS USING similarly illuminated, the output may appear as at B in SEMICONDUCTOR LAMINAE FIG. 2. _ If such a lamina 20 is overlaid with another identical ' BRIEF SUMMARY OF THE INVENTION lamina 23,‘ as shown in FIG. -
Preparation of Bismuth Telluride Specimens for TEM
Preparation of Bismuth Telluride Specimens for TEM Mark Homer1, Douglas L. Medlin2 1,2. Sandia National Laboratories, Energy Nanomaterials Dept., Livermore CA, USA Bismuth telluride (Bi2Te3) and its alloys are an important class of thermoelectric material. How well a thermoelectric material works is dependent on a variety of factors such as electrical and thermal conductivity and the Seeback coefficient. Because the electrical and thermal conductivity can be affected by defects in the material, there is much interest in the basic understanding the microstructures of these materials [1]. There are challenges in preparation of TEM specimens from telluride-based materials due to their sensitivity to ion-milling artifacts. For instance, nanoscale defect arrangements have been shown to form in lead telluride (PbTe) specimens prepared under aggressive ion milling conditions if cooling and power density is not suitably controlled [2]. In this presentation we discuss methods and conditions for preparing TEM specimens of Bi2Te3 specimens considering both ion-milling and electropolishing techniques. In all cases TEM specimens were mechanically pre-thinned using conventional mechanical dimpling and polishing techniques prior to final thinning to electron transparency. The ion-milled specimens were prepared with Ar+ ion sputtering using a Fischione Model 1010 ion mill with LN cooling. The electropolished specimens were prepared using a Fischione Model 120 electropolisher and an electrolyte consisting of 53% water, 38% glycerol, 5% sodium hydroxide, and 4% tartaric acid. The electrolyte was set in an ice bath and cooled to 2° C, and electropolished at 25V and 35mA. Figures 1 and 2 show dark-field TEM micrographs comparing ion milled and electropolished Bi2Te3 specimens. -
High-Throughput Physical Vapour Deposition Flexible Thermoelectric Generators
www.nature.com/scientificreports OPEN High-throughput physical vapour deposition fexible thermoelectric generators Received: 14 January 2019 Katrina A. Morgan 1, Tian Tang2, Ioannis Zeimpekis 1, Andrea Ravagli1, Chris Craig1, Accepted: 25 February 2019 Jin Yao1, Zhuo Feng1, Dmitry Yarmolich3, Clara Barker 2, Hazel Assender2 & Published: xx xx xxxx Daniel W. Hewak1 Flexible thermoelectric generators (TEGs) can provide uninterrupted, green energy from body-heat, overcoming bulky battery confgurations that limit the wearable-technologies market today. High- throughput production of fexible TEGs is currently dominated by printing techniques, limiting material choices and performance. This work investigates the compatibility of physical vapour deposition (PVD) techniques with a fexible commercial process, roll-to-roll (R2R), for thermoelectric applications. We demonstrate, on a fexible polyimide substrate, a sputtered Bi2Te3/GeTe TEG with Seebeck coefcient (S) of 140 μV/K per pair and output power (P) of 0.4 nW per pair for a 20 °C temperature diference. For the frst time, thermoelectric properties of R2R sputtered Bi2Te3 flms are reported and we demonstrate the ability to tune the power factor by lowering run times, lending itself to a high- speed low-cost process. To further illustrate this high-rate PVD/R2R compatibility, we fabricate a TEG using Virtual Cathode Deposition (VCD), a novel high deposition rate PVD tool, for the frst time. This Bi2Te3/Bi0.5Sb1.5Te3 TEG exhibits S = 250 μV/K per pair and P = 0.2 nW per pair for a 20 °C temperature diference. Termoelectric generators (TEGs) can provide constant power for fexible electronic platforms. Using the body’s warmth, they do not rely on solar power, unlike photovoltaic generators, or on the user’s ftness, unlike elec- tromagnetic induction generators. -
WO 2016/074683 Al 19 May 2016 (19.05.2016) W P O P C T
(12) INTERNATIONAL APPLICATION PUBLISHED UNDER THE PATENT COOPERATION TREATY (PCT) (19) World Intellectual Property Organization International Bureau (10) International Publication Number (43) International Publication Date WO 2016/074683 Al 19 May 2016 (19.05.2016) W P O P C T (51) International Patent Classification: (81) Designated States (unless otherwise indicated, for every C12N 15/10 (2006.01) kind of national protection available): AE, AG, AL, AM, AO, AT, AU, AZ, BA, BB, BG, BH, BN, BR, BW, BY, (21) International Application Number: BZ, CA, CH, CL, CN, CO, CR, CU, CZ, DE, DK, DM, PCT/DK20 15/050343 DO, DZ, EC, EE, EG, ES, FI, GB, GD, GE, GH, GM, GT, (22) International Filing Date: HN, HR, HU, ID, IL, IN, IR, IS, JP, KE, KG, KN, KP, KR, 11 November 2015 ( 11. 1 1.2015) KZ, LA, LC, LK, LR, LS, LU, LY, MA, MD, ME, MG, MK, MN, MW, MX, MY, MZ, NA, NG, NI, NO, NZ, OM, (25) Filing Language: English PA, PE, PG, PH, PL, PT, QA, RO, RS, RU, RW, SA, SC, (26) Publication Language: English SD, SE, SG, SK, SL, SM, ST, SV, SY, TH, TJ, TM, TN, TR, TT, TZ, UA, UG, US, UZ, VC, VN, ZA, ZM, ZW. (30) Priority Data: PA 2014 00655 11 November 2014 ( 11. 1 1.2014) DK (84) Designated States (unless otherwise indicated, for every 62/077,933 11 November 2014 ( 11. 11.2014) US kind of regional protection available): ARIPO (BW, GH, 62/202,3 18 7 August 2015 (07.08.2015) US GM, KE, LR, LS, MW, MZ, NA, RW, SD, SL, ST, SZ, TZ, UG, ZM, ZW), Eurasian (AM, AZ, BY, KG, KZ, RU, (71) Applicant: LUNDORF PEDERSEN MATERIALS APS TJ, TM), European (AL, AT, BE, BG, CH, CY, CZ, DE, [DK/DK]; Nordvej 16 B, Himmelev, DK-4000 Roskilde DK, EE, ES, FI, FR, GB, GR, HR, HU, IE, IS, IT, LT, LU, (DK). -
Alfa Laval Black and Grey List, Rev 14.Pdf 2021-02-17 1678 Kb
Alfa Laval Group Black and Grey List M-0710-075E (Revision 14) Black and Grey list – Chemical substances which are subject to restrictions First edition date. 2007-10-29 Revision date 2021-02-10 1. Introduction The Alfa Laval Black and Grey List is divided into three different categories: Banned, Restricted and Substances of Concern. It provides information about restrictions on the use of Chemical substances in Alfa Laval Group’s production processes, materials and parts of our products as well as packaging. Unless stated otherwise, the restrictions on a substance in this list affect the use of the substance in pure form, mixtures and purchased articles. - Banned substances are substances which are prohibited1. - Restricted substances are prohibited in certain applications relevant to the Alfa Laval group. A restricted substance may be used if the application is unmistakably outside the scope of the legislation in question. - Substances of Concern are substances of which the use shall be monitored. This includes substances currently being evaluated for regulations applicable to the Banned or Restricted categories, or substances with legal demands for monitoring. Product owners shall be aware of the risks associated with the continued use of a Substance of Concern. 2. Legislation in the Black and Grey List Alfa Laval Group’s Black and Grey list is based on EU legislations and global agreements. The black and grey list does not correspond to national laws. For more information about chemical regulation please visit: • REACH Candidate list, Substances of Very High Concern (SVHC) • REACH Authorisation list, SVHCs subject to authorization • Protocol on persistent organic pollutants (POPs) o Aarhus protocol o Stockholm convention • Euratom • IMO adopted 2015 GUIDELINES FOR THE DEVELOPMENT OF THE INVENTORY OF HAZARDOUS MATERIALS” (MEPC 269 (68)) • The Hong Kong Convention • Conflict minerals: Dodd-Frank Act 1 Prohibited to use, or put on the market, regardless of application. -
INVESTIGATIONS on STRUCTURE and PROPERTIES of Ge-As-Se CHALCOGENIDE GLASSES Ting Wang April 2017 a Thesis Submitted for the Degr
INVESTIGATIONS ON STRUCTURE AND PROPERTIES OF Ge-As-Se CHALCOGENIDE GLASSES Ting Wang April 2017 A thesis submitted for The degree of Doctor of Philosophy of The Australian National University The Laser Physics Centre Research School of Physics & Engineering The Australian National University STATEMENT I declare that the work presented in this thesis is, to the best of my knowledge, the result of original research. The thesis has not been submitted for a degree or diploma to any other university or institution. Part of the research included in this thesis has been performed jointly with Professor Pierre Lucas. Signed Ting Wang ACKNOWLEDGEMENTS I would like to sincerely thank my supervisor and advisors, Professor Barry Luther-Davis, Dr. Rongping Wang and Dr. Xin Gai for their guidance, advice and thoughtful comments throughout this work. I would like to express my thanks to Dr. Zhiyong Yang, Dr. Duk-Yong Choi, Dr. Steve Madden, Dr. Vu Khu for sharing their knowledge and expertise in glass science. I would also like to thank Professor Ian Jackson, Mr Sukanta Debbarma and Mrs Maryla Krolikowska for their help in experiments. Particularly thanks to Professor Pierre Lucas and Mr Ozgur Gulbiten for providing useful samples, valuable suggestions and great assistance on the interpretation of the thermal data. Thanks to all students who work in the laser physics center: Yi Yu, Pan Ma, Kunlun Yan, Joseph Sudhakar Paulraj and Yue Sun. Thanks to my parents, for their encouragement and great support during my PhD. I TABLE OF CONTENTS TABLE OF CONTENTS ................................................................................................. i LIST OF FIGURES........................................................................................................iii LIST OF TABLES ........................................................................................................viii LIST OF ABBREVIATIONS ....................................................................................... -
Electronic Properties of Lead Telluride Quantum Wells
Electronic Properties of Lead Telluride Quantum Wells Liza Mulder Smith College 2013 NSF/REU Program Physics Department, University of Notre Dame Advisors: Profs. Jacek Furdyna, Malgorzata Dobrowolska, and Xinyu Liu Thanks also to: Rich Pimpinella, Joseph Hagmann, and Xiang Li Abstract My research this summer has focused on measuring the electronic properties of quantum wells that combine two families of semiconductors, specifically Cadmium Telluride and Lead Telluride (CdTe/PbTe/CdTe), whose interfaces hold promise of Topological Crystalline Insulator (TCI) surface states. The samples used in my study are grown by Molecular Beam Epitaxy, and measured using Magneto Transport experiments. I have found that samples grown on higher temperature substrates have higher charge carrier mobilities and lower carrier concentrations, while the resistivity shows no significant change. These results will be used as a guide toward designing future structures for observing and characterizing TCI surface states. Introduction Semiconductors have many applications in electronic devices, and as these devices become smaller and smaller, so do their components. Hence the importance of understanding the complex surface states of semiconductors. Some of these surfaces are also possible examples of Topological Insulators (TIs) or Topological Crystalline Insulators (TCIs). By studying semiconductors in the form of thin films, quantum wells, nanowires, and quantum dots, researchers hope to better understand semiconductors in this form, to measure the electronic and magnetic properties of their surface states, and to discover new examples of TIs and TCIs. This summer I studied the electronic properties of Cadmium Telluride - Lead Telluride (CdTe/PbTe:Bi/CdTe) quantum well structures. The samples are grown by Molecular Beam Epitaxy, and measured using Magneto Transport.