3,356,456 Dec. 5, 1967
Total Page:16
File Type:pdf, Size:1020Kb
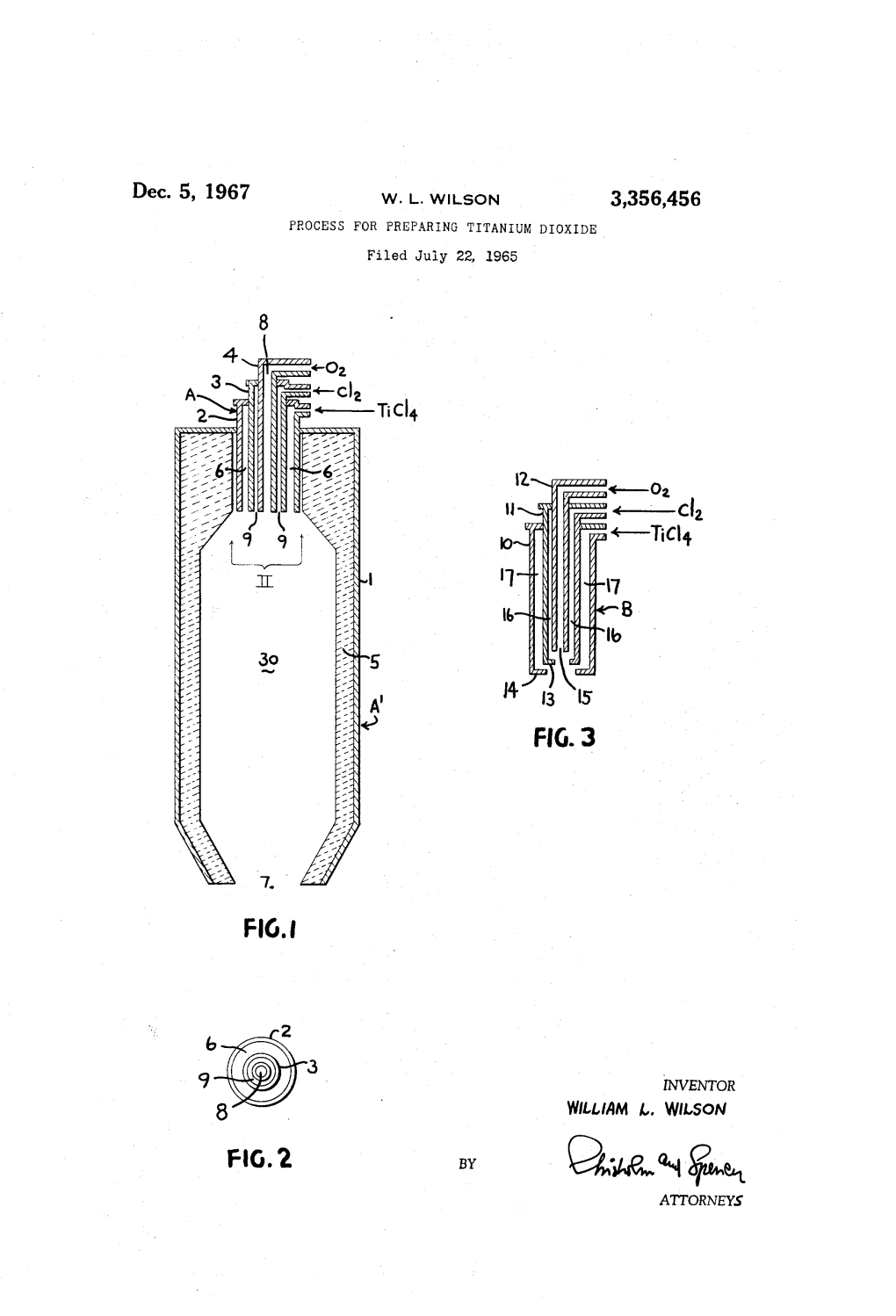
Load more
Recommended publications
-
Crown Chemical Resistance Chart
Crown Polymers, Corp. 11111 Kiley Drive Huntley, IL. 60142 USA www.crownpolymers.com 847-659-0300 phone 847-659-0310 facisimile 888-732-1270 toll free Chemical Resistance Chart Crown Polymers Floor and Secondary Containment Systems Products: CrownShield covers the following five (4) formulas: CrownShield 50, Product No. 320 CrownCote, Product No. 401 CrownShield 40-2, Product No. 323 CrownShield 28, Product No. 322 CrownPro AcidShield, Product No. 350 CrownCote AcidShield, Product No. 430 CrownPro SolventShield, Product No. 351 CrownCote SolventShield, Product No. 440 This chart shows chemical resistance of Crown Polymers foundational floor and secondary containment product line that would be exposed to chemical spill or immersion conditions. The chart was designed to provide general product information. For specific applications, contact your local Crown Polymers Floor and Secondary Containment Representative or call direct to the factory. ; Resistant to chemical immersion up to 7 days followed by wash down with water 6 Spillage environments that will be cleaned up within 72 hours after initial exposure. 9 Not Recommended Chemical CrownShield SolventShield AcidShield Chemical CrownShield SolventShield AcidShield 1, 4-Dichloro-2-butene 9 6 6 Aluminum Bromate ; ; ; 1, 4-Dioxane 9 6 6 Aluminum Bromide ; ; ; 1-1-1 Trichloroethane 9 ; ; Aluminum Chloride ; ; ; 2, 4-Pentanedione 6 ; 6 Aluminum Fluoride (25%) ; ; ; 3, 4-Dichloro-1-butene 6 6 6 Aluminum Hydroxide ; ; ; 4-Picoline (0-50%) 9 6 6 Aluminum Iodine ; ; ; Acetic Acid (0-15%) 9 6 6 -
Gasket Chemical Services Guide
Gasket Chemical Services Guide Revision: GSG-100 6490 Rev.(AA) • The information contained herein is general in nature and recommendations are valid only for Victaulic compounds. • Gasket compatibility is dependent upon a number of factors. Suitability for a particular application must be determined by a competent individual familiar with system-specific conditions. • Victaulic offers no warranties, expressed or implied, of a product in any application. Contact your Victaulic sales representative to ensure the best gasket is selected for a particular service. Failure to follow these instructions could cause system failure, resulting in serious personal injury and property damage. Rating Code Key 1 Most Applications 2 Limited Applications 3 Restricted Applications (Nitrile) (EPDM) Grade E (Silicone) GRADE L GRADE T GRADE A GRADE V GRADE O GRADE M (Neoprene) GRADE M2 --- Insufficient Data (White Nitrile) GRADE CHP-2 (Epichlorohydrin) (Fluoroelastomer) (Fluoroelastomer) (Halogenated Butyl) (Hydrogenated Nitrile) Chemical GRADE ST / H Abietic Acid --- --- --- --- --- --- --- --- --- --- Acetaldehyde 2 3 3 3 3 --- --- 2 --- 3 Acetamide 1 1 1 1 2 --- --- 2 --- 3 Acetanilide 1 3 3 3 1 --- --- 2 --- 3 Acetic Acid, 30% 1 2 2 2 1 --- 2 1 2 3 Acetic Acid, 5% 1 2 2 2 1 --- 2 1 1 3 Acetic Acid, Glacial 1 3 3 3 3 --- 3 2 3 3 Acetic Acid, Hot, High Pressure 3 3 3 3 3 --- 3 3 3 3 Acetic Anhydride 2 3 3 3 2 --- 3 3 --- 3 Acetoacetic Acid 1 3 3 3 1 --- --- 2 --- 3 Acetone 1 3 3 3 3 --- 3 3 3 3 Acetone Cyanohydrin 1 3 3 3 1 --- --- 2 --- 3 Acetonitrile 1 3 3 3 1 --- --- --- --- 3 Acetophenetidine 3 2 2 2 3 --- --- --- --- 1 Acetophenone 1 3 3 3 3 --- 3 3 --- 3 Acetotoluidide 3 2 2 2 3 --- --- --- --- 1 Acetyl Acetone 1 3 3 3 3 --- 3 3 --- 3 The data and recommendations presented are based upon the best information available resulting from a combination of Victaulic's field experience, laboratory testing and recommendations supplied by prime producers of basic copolymer materials. -
The Institute of Paper Chemistry
The Institute of Paper Chemistry Appleton, Wisconsin Doctor's Dissertation Reaction Products of Lignin Model Compounds and Sodium Hydrosulfide Thomas G. Zentner June, 1953 A STUDY OF THE REACTION PRODUCTS OF LIGNIN MODEL COMPOUNDS AND SODIUM HYDROSULFIDE A thesis submitted by Thomas G. Zentner B.S. 1948, Texas A & M College M.S. 1950, Lawrence College in partial fulfillment of the requirements of The Institute of Paper Chemistry for the degree of Doctor of Philosophy from Lawrence College, Appleton, Wisconsin June, 1952 TABLE OF CONTENTS INTRODUCTION 1 HISTORICAL REVIEW 2 PRESENTATION OF THE PROBLEM 8 EXPERIMENTAL PROCEDURES 10 Synthesis of Compounds 10 Synthesis of 1-(4-Hydroxy-3-methoxyphenyl)-l-propanol 10 Synthesis of 1-(4-Benzoxy-3-methoxyphenyl)-l-propanol 11 Reaction of 1-(4-Benzoxy-3-methoxyphenyl) l-propanol with Benzyl Chloride 12 Synthesis of Propiovanillone 14 Synthesis of (-(4-Acetyl-2-methoxyphenoxy)acetovanillone 17 Attempted Synthesis of a-(2-Methoxy-4-methylphehoxy)- propiovanillone 17 Attempted Synthesis of 4-[l-(2-Methoxy-4-methylphenoxy)- l-propyl]guaiacol 21 Synthesis of 2t,4-Dihydroxy-3-methoxychalcone 23 Synthesis of 4,4'-Dihydroxy-3,3 -dimethoxychalcone 24 Synthesis of 4-Propionylpyrocatechol 24 Synthesis of Bis[l-(4-hydroxy-3-methoxyphenyl)-1- propyl] Disulfide 26 Reaction of Isolated Native Lignin with Potassium Hydrosulfide 27 Sodium Hydrosulfide Cooks 28 Cooking Liquor 28 General Procedures 30 Propiovanillone' 32 iii 2 ,4-Dihydroxy-3-methoxychalcone 34 4,4'-Dihydroxy-3,3 '-methoxychalcohe 37 4'-Hydroxy-3t-methoxyflavanone 39 2-Vanillylidene-3-coumaranone 41 Vanillin 44 G- (4-Acetyl-2-methoxyphenoxy)acetovanillone 45 1-(4-Hydroxy-3-methoxyphenyl)-1-propanol 49 DISCUSSION 58 SUMMARY AND CONCLUSIONS 69 LITERATURE CITED 71 INTRODUCTION Although the kraft process has been in use for many years, there is no sound explanation of the role played by the sulfide ion in the cook. -
The Following List Contains the Material Safety Data Sheets You Requested
The following list contains the Material Safety Data Sheets you requested. Please scoll down to view the requested MSDS(s). Product MSDS Distributor Format Language Quantity 2882200 2802299 Hach Company OSHA English 1 2882200 2877336 Hach C ompany OSHA English 1 2882200 2105669 Hach Company OSHA English 1 2882200 2107169 Hach Company OSHA English 1 2882200 1406499 Hach Company OSHA English 1 ____________________________________________________________________________________ ______________________ Total Enclosures: 5 World Headquarters Hach Company P.O.Box 389 MSDS No: M01921 Loveland, CO USA 80539 (970) 669 -3050 MATERIAL SAFETY DATA SHEET _________________________________________________________________________ ____ 1. CHEMICAL PRODUCT AND COMPANY IDENTIFICATION Product Name: Monochlor F TM Reagent Catalog Number: 2802299 Hach Company Emergency Telephone Numbers: P.O.Box 389 (Medical and Transportation) Loveland, CO USA 80539 (303) 623 -5716 24 Hour Service (970) 669 -3050 (515)232 -2533 8am - 4pm CST MSDS Number: M01921 Chemical Name: Not applicable CAS No.: Not applicable Chemical Formula: Not applicable Chemical Family: Not applicable Hazard: Harmful if swallowed Causes burns. Date of MSDS Pre paration: Day: 09 Month: March Year: 2010 _____________________________________________________________________________ 2. COMPOSITION / INFORMATION ON INGREDIENTS Sodium Tartrate CAS No.: 6106 -24 -7 TSCA CAS Number: 868 -18 -8 Percent Range: < 30 Percent Range Units: weight / weight LD50: Oral rabbit LD50 = 5290 mg/kg LC50: None reported TLV: Not established PEL: Not established Hazard: May cause irritation. Sodium Nitroferricyanide CAS No.: 14402 -89 -2 TSCA CAS Number: 14402 -89 -2 Percent Range: < 5.0 Percent Range Units: weight / weight LD50: Oral rat LD 50 = 99 mg/kg (anhydrous). LC50: None reported. TLV: 5 mg/m³ as CN¯ PEL: 5 mg/m³ as CN¯ Hazard: Toxic. -
Chemical Resistance 100% SOLIDS EPOXY SYSTEMS
Chemical Resistance 100% SOLIDS EPOXY SYSTEMS CHEMICAL 8300 SYSTEM 8200 SYSTEM 8000 SYSTEM OVERKOTE PLUS HD OVERKOTE HD OVERKRETE HD BASED ON ONE YEAR IMMERSION TESTING –––––––––––––––––––––––––––––––––––––––––––––––––––––––––––––––––––––––––––– Acetic Acid (0-15%) G II Acetonitrile LLG L Continuous Immersion Acetone (0-20%) LLL Acetone (20-30%) Suitable for continuous immersion in that chemical (based on LLG Acetone (30-50%) L G I ONE YEAR testing) to assure unlimited service life. Acetone (50-100%) G II Acrylamide (0-50%) LLL G Short-Term Exposure Adipic Acid Solution LLL Alcohol, Isopropyl LLL Suitable for short-term exposure to that chemical such as Alcohol, Ethyl LLG secondary containment (72 hours) or splash and spill Alcohol, Methyl LLI (immediate clean-up). Allyl Chloride LLI Allylamine (0-20%) L L I Allylamine (20-30%) L G I I Not Suitable Allylamine (30-50%) GGI Not suitable for any exposure to that chemical. Aluminum Bromide LL– Aluminum Chloride L L – Aluminum Fluoride (0-25%) L L – This chart shows chemical resistance of our various Aluminum Hydroxide LLL 1 topping materials (90 mils – ⁄4"). These ratings are based on Aluminum Iodide LL– temperatures being ambient. At higher temperatures, chemical Aluminum Nitrate LL– resistance may be effected. When chemical exposure is Aluminum Sodium Chloride L L – minimal to non-existent, a 9000 System–FlorClad™ HD or Aluminum Sulfate LLL 4600 System– BriteCast™ HD may be used. Alums L L L 2-Aminoethoxyethanol Resistance data is listed with the assumption that the material GGG has properly cured for at least four days, at recommended Ammonia – Wet L L – temperatures, prior to any chemical exposure. -
Corrosion-2020) (461 Event of the European Federation of Corrosion)
European Federation of Corrosion National Academy of Sciences of Ukraine Ministry of Education and Science of Ukraine Ukrainian Association of Corrosionists Karpenko Physico-Mechanical Institute Ivan Franko Lviv National University Ivano-Frankivsk National Technical University of Oil and Gas ХV International Conference «Problems of corrosion and corrosion protection of materials» (Corrosion-2020) (461 event of the European Federation of Corrosion) ABSTRACT BOOK October 15–16, 2020 Lviv, Ukraine UДC 539.3, 620.193, 620.194, 620.179, 620.197, 621.181:669.018, 621.785. XV International Conference “Problems of Corrosion and Corrosion Protection of Materials“ (Corrosion-2020). October 15-16, 2020, Lviv, Ukraine: Book of Abstract / Karpenko Physico-Mechanical Institute of NAS of Ukraine; S. Korniy, М.-О. Danyliak, Yu. Maksishko (Eds.). – Lviv, 2020. – 121 p. XV International Conference “Problems of Corrosion and Corrosion Protection of Materials“ (Corrosion-2020) was held at Lviv Palace of Arts on October 15-16, 2020. This Book of Abstract contains the results of studies are devoted to fundamentals of corrosion and corrosion assisted mechanical fracture; hydrogen and gas corrosion; new corrosion resistant materials; thermal spray, electroplated and other coatings; inhibitor, biocidal and electrochemical protection; testing methods and corrosion control; corrosion protection of oil and gas industry and chemical equipment. In the authors edition. Editorial board: S. Korniy, М.-О. Danyliak, Yu. Maksishko ©Karpenko Physico-Mechanical Institute of NAS of Ukraine, Lviv, 2020 CONFERENCE TOPICS: fundamentals of corrosion and corrosion assisted mechanical fracture; hydrogen and gas corrosion; new corrosion resistant materials and coatings; inhibitor and biocidal protection; electrochemical protection; testing methods and corrosion control; corrosion protected equipment of the oil and gas, chemical and energy industries. -
Chemical Names and CAS Numbers Final
Chemical Abstract Chemical Formula Chemical Name Service (CAS) Number C3H8O 1‐propanol C4H7BrO2 2‐bromobutyric acid 80‐58‐0 GeH3COOH 2‐germaacetic acid C4H10 2‐methylpropane 75‐28‐5 C3H8O 2‐propanol 67‐63‐0 C6H10O3 4‐acetylbutyric acid 448671 C4H7BrO2 4‐bromobutyric acid 2623‐87‐2 CH3CHO acetaldehyde CH3CONH2 acetamide C8H9NO2 acetaminophen 103‐90‐2 − C2H3O2 acetate ion − CH3COO acetate ion C2H4O2 acetic acid 64‐19‐7 CH3COOH acetic acid (CH3)2CO acetone CH3COCl acetyl chloride C2H2 acetylene 74‐86‐2 HCCH acetylene C9H8O4 acetylsalicylic acid 50‐78‐2 H2C(CH)CN acrylonitrile C3H7NO2 Ala C3H7NO2 alanine 56‐41‐7 NaAlSi3O3 albite AlSb aluminium antimonide 25152‐52‐7 AlAs aluminium arsenide 22831‐42‐1 AlBO2 aluminium borate 61279‐70‐7 AlBO aluminium boron oxide 12041‐48‐4 AlBr3 aluminium bromide 7727‐15‐3 AlBr3•6H2O aluminium bromide hexahydrate 2149397 AlCl4Cs aluminium caesium tetrachloride 17992‐03‐9 AlCl3 aluminium chloride (anhydrous) 7446‐70‐0 AlCl3•6H2O aluminium chloride hexahydrate 7784‐13‐6 AlClO aluminium chloride oxide 13596‐11‐7 AlB2 aluminium diboride 12041‐50‐8 AlF2 aluminium difluoride 13569‐23‐8 AlF2O aluminium difluoride oxide 38344‐66‐0 AlB12 aluminium dodecaboride 12041‐54‐2 Al2F6 aluminium fluoride 17949‐86‐9 AlF3 aluminium fluoride 7784‐18‐1 Al(CHO2)3 aluminium formate 7360‐53‐4 1 of 75 Chemical Abstract Chemical Formula Chemical Name Service (CAS) Number Al(OH)3 aluminium hydroxide 21645‐51‐2 Al2I6 aluminium iodide 18898‐35‐6 AlI3 aluminium iodide 7784‐23‐8 AlBr aluminium monobromide 22359‐97‐3 AlCl aluminium monochloride -
Traumatic Shock. Ii. the Preparation of Cystine, Methionine, and Homocystine Containing Radioactive Sulfur
TRAUMATIC SHOCK. II. THE PREPARATION OF CYSTINE, METHIONINE, AND HOMOCYSTINE CONTAINING RADIOACTIVE SULFUR Arnold M. Seligman, … , Alexander M. Rutenburg, Henry Banks J Clin Invest. 1943;22(2):275-279. https://doi.org/10.1172/JCI101393. Research Article Find the latest version: https://jci.me/101393/pdf TRAUMATIC SHOCK. II. THE PREPARATION OF CYSTINE, METHIONINE, AND HOMOCYSTINE CONTAINING RADIOACTIVE SULFUR By ARNOLD M. SELIGMAN, ALEXANDER M. RUTENBURG, AND HENRY BANKS 1 (From the Surgical Research Department of the Beth Israel Hospital and the Department of Surgery, Harvard Medical School, Boston) (Received for publication November 12, 1942) In order to prepare, from radioactive sulfur, the benzyl mercaptan (I) (0.6 moles), reported by sulfur-containing amino acids of a high order of Wood and du Vigneaud (4) in 23 per cent yield, specific activity for biological experiments such was found to give a 21.5 per cent yield when 0.06 as those described in the foregoing publication, it mole was used. Reduction of benzylcysteine was necessary (owing to the cost of radioactive (VIII) to cysteine with sodium and butyl alcohol sulfur) to investigate the efficiency of utilization did not give good yields; therefore, sodium and of small amounts of sulfur. The synthetic meth- liquid ammonia were used. Since radioactive ods utilized are not novel, but are described be- benzyl mercaptan is necessary for the synthesis of low because of the data obtained on yields in all three amino acids, a method of preparation of numerous small scale preparations. Since pres- the mercaptan from hydrogen sulfide, other than ent methods of preparing radioactive sulfur from that described by Tarver and Schmidt, in 70 per neutron bombardment of carbon tetrachloride in- cent yield, was investigated. -
WO 2017/116773 Al 6 July 2017 (06.07.2017) W P O P C T
(12) INTERNATIONAL APPLICATION PUBLISHED UNDER THE PATENT COOPERATION TREATY (PCT) (19) World Intellectual Property Organization International Bureau (10) International Publication Number (43) International Publication Date WO 2017/116773 Al 6 July 2017 (06.07.2017) W P O P C T (51) International Patent Classification: 85008-3279 (US). SHULT, Nicholas S.; 2255 North 44th C23F 1/14 (2006.01) H05K 3/38 (2006.01) Street, Suite 300, Phoenix, Arizona 85008-3279 (US). C01B 15/08 (2006.01) C09G 1/00 (2006.01) GOLDSMITH, Adam T.; 2255 North 44th Street, Suite 300, Phoenix, Arizona 85008-3279 (US). (21) International Application Number: PCT/US20 16/0673 13 (74) Agent: ROSENFIELD, Susan Stone; Fennemore Craig, 2394 East Camelback Road, Suite 600, Phoenix, Arizona (22) International Filing Date: 85016 (US). 16 December 2016 (16. 12.2016) (81) Designated States (unless otherwise indicated, for every (25) Filing Language: English kind of national protection available): AE, AG, AL, AM, (26) Publication Language: English AO, AT, AU, AZ, BA, BB, BG, BH, BN, BR, BW, BY, BZ, CA, CH, CL, CN, CO, CR, CU, CZ, DE, DJ, DK, DM, (30) Priority Data: DO, DZ, EC, EE, EG, ES, FI, GB, GD, GE, GH, GM, GT, 62/273,389 30 December 201 5 (30. 12.2015) US HN, HR, HU, ID, IL, IN, IR, IS, JP, KE, KG, KH, KN, 15/380,702 15 December 201 6 (15. 12.2016) US KP, KR, KW, KZ, LA, LC, LK, LR, LS, LU, LY, MA, (71) Applicant: TESSENDERLO KERLEY, INC. [US/US]; MD, ME, MG, MK, MN, MW, MX, MY, MZ, NA, NG, 2255 North 44th Street, Suite 300, Phoenix, Arizona NI, NO, NZ, OM, PA, PE, PG, PH, PL, PT, QA, RO, RS, 85008-3279 (US). -
Tantaline® Surface Alloy Treatment Services
Solutions for Conquering Corrosion. Tantaline® Surface Alloy Treatment Services www.tantaline.com Tantaline® Technology Tantaline® treatment is a diffusion bonded protective desired deposit. CVD technology has proven itself to layer of tantalum formed by chemical vapor deposition be robust, economical, and scalable over many years (CVD) on the surface of common materials. The of service in semiconductor and other industries. resulting surface has the same properties of pure tantalum because it is tantalum. Tantalum is the most corrosion resistant metal commercially available due Tantaline CVD to its very dense surface oxide layer. Compatibility with Our proprietary process creates a dense tantalum concentrated high temperature acidic environments surface with all of the beneficial properties of pure has been well established in industrial applications. tantalum metal. The Tantaline® process is conducted Tantaline® treatment enables the highest level of in a sealed reaction chamber under highly controlled corrosion resistance for components used in a wide conditions. This CVD process is geometry independent range of aggressive atmospheres at a competitive which enables both internal and external surfaces of price. This treatment can be applied to stock parts as a complex shapes to be treated at the same time. direct substitute for specialty metals. The list includes Parts typically treated include valves, fittings, solid tantalum, tantalum cladding, titanium, zirconium autoclaves, process chambers, flow reactors, and nickel alloys like Hastelloy®*, Inconel® ** and Alloy fasteners, mixers, flowmeters, and medical devices. 20. Treatment of stock parts fabricated from common Specialty items can be evaluated for treatment upon base metals can significantly reduce the overall lead request. Base metal is typically standard grades of time for otherwise difficult to obtain special order stainless steel, but the treatment process has been items. -
3. Process Modeling of the Sulfur-Ammonia Cycle
UC San Diego UC San Diego Electronic Theses and Dissertations Title A Continuous Solar Thermochemical Hydrogen Production Plant Design Permalink https://escholarship.org/uc/item/98v9888g Author Luc, Wesley Wai Publication Date 2013 Peer reviewed|Thesis/dissertation eScholarship.org Powered by the California Digital Library University of California UNIVERSITY OF CALIFORNIA, SAN DIEGO A Continuous Solar Thermochemical Hydrogen Production Plant Design A Thesis submitted in partial satisfaction of the requirements for the degree Master of Science in Chemical Engineering by Wesley Wai Luc Committee in charge: Professor Jan Talbot, Chair Professor Richard Herz Professor Pao Chau 2013 Signature Page The Thesis of Wesley Wai Luc is approved and it is acceptable in quality and form for publication on microfilm and electronically: _____________________________________________________________________ _____________________________________________________________________ _____________________________________________________________________ Chair University of California, San Diego 2013 iii Dedicated to my friends and family iv TABLE OF CONTENTS Signature Page ................................................................................................................... iii Dedication .......................................................................................................................... iv Table of Contents ................................................................................................................ v List of -
Chemical Capabilities Listing Laboratory, R&D, Industrial and Manufacturing Applications
Page 1 of 3 Chemical Capabilities Listing Laboratory, R&D, Industrial and Manufacturing Applications Acacia, Gum Arabic Barium Oxide Chromium Trioxide Acetaldehyde Bentonite, White Citric Acid, Anhydrous Acetamide Benzaldehyde Citric Acid, Monohydrate Acetanilide Benzoic Acid Cobalt Oxide Acetic Acid Benzoyl Chloride Cobaltous Acetate Acetic Anhydride Benzyl Alcohol Cobaltous Carbonate Acetone Bismuth Chloride Cobaltous Chloride Acetonitrile Bismuth Nitrate Cobaltous Nitrate Acetyl Chloride Bismuth Trioxide Cobaltous Sulfate Aluminium Ammonium Sulfate Boric Acid Cottonseed Oil Aluminon Boric Anhydride Cupferron Aluminum Chloride, Anhydrous Brucine Sulfate Cupric Acetate Aluminum Chloride, Hexahydrate n-Butyl Acetate Cupric Bromide Aluminum Fluoride n-Butyl Alcohol Cupric Carbonate, Basic Aluminum Hydroxide tert-Butyl Alcohol Cupric Chloride Aluminum Nitrate Butyric Acid Cupric Nitrate Aluminum Oxide Cadmium Acetate Cupric Oxide Aluminum Potassium Sulfate Cadmium Carbonate Cupric Sulfate, Anhydrous Aluminum Sulfate Cadmium Chloride, Anhydrous Cupric Sulfate, Pentahydrate 1-Amino-2-Naphthol-4-Sulfonic Acid Cadmium Chloride, Hemipentahydrate Cuprous Chloride Ammonium Acetate Cadmium Iodide Cuprous Oxide, Red Ammonium Bicarbonate Cadmium Nitrate Cyclohexane Ammonium Bifluoride Cadmium Oxide Cyclohexanol Ammonium Bisulfate Cadmium Sulfate, Anhydrous Cyclohexanone Ammonium Bromide Cadmium Sulfate, Hydrate Devarda's Alloy Ammonium Carbonate Calcium Acetate Dextrose, Anhydrous Ammonium Chloride Calcium Carbide Diacetone Alcohol Ammonium Citrate