Synthesis and Properties of In-Situ Bulk High Impact Polystyrene Toughened by High Cis-1,4 Polybutadiene
Total Page:16
File Type:pdf, Size:1020Kb
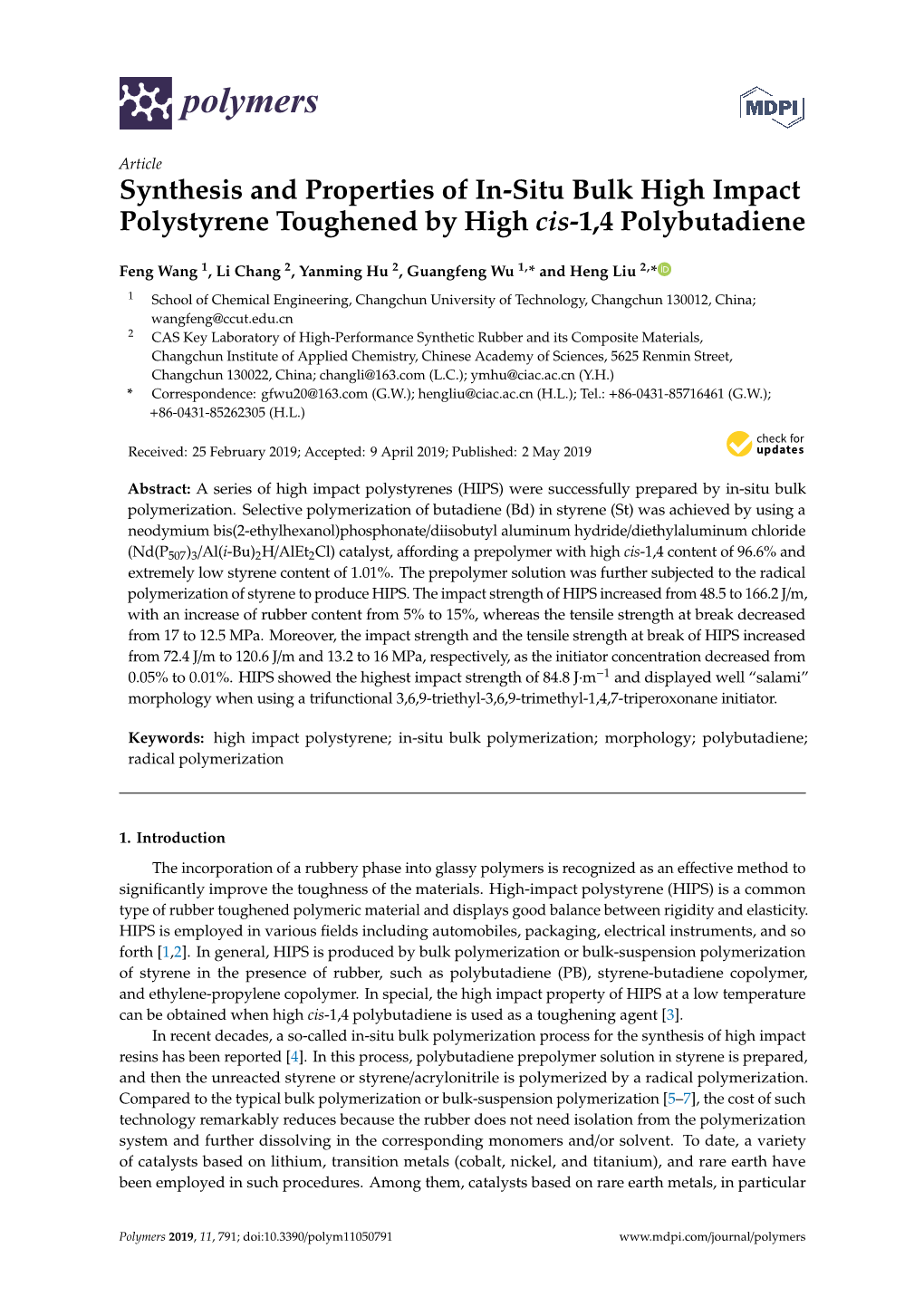
Load more
Recommended publications
-
Fracture of Polycarbonate/Abs Blends
FRACTURE OF POLYCARBONATE/ABS BLENDS PROEFSCHRIFT ter verkrijging van de graad van doctor aan de Universiteit Twente, op gezag van de rector magnificus, prof. dr. F.A. van Vught, volgens besluit van het College voor Promoties in het openbaar te verdedigen op vrijdag 27 april 2001 om 13.15 uur door Judith Pouwlien Frederika Inberg geboren op 27 juli 1972 te Britswerd Dit proefschrift is goedgekeurd door de promotor: Prof. L.C.E. Struik en de assistent-promotor: Dr. R.J. Gaymans ".... Het voornaamste probleem met die Tijdbesparingsobsessie ligt heel eenvoudig: tijd kun je niet besparen. Je kunt hem alleen besteden." Benjamin Hoff, in Tao van Poeh Fracture of polycarbonate/ABS blends J.P.F. Inberg Thesis, University of Twente, Enschede, The Netherlands April 2001 ISBN 90 365 1553x Cover: TEM picture of deformation zone ahead of an arrested crack in a co-continuous polycarbonate/ABS blend Ó J.P.F. Inberg Printed by: Grafisch Centrum Twente, Enschede Voorwoord Met dit proefschrift sluit ik mijn tijd binnen de onderzoeksgroep 'Synthese en Technologie van Engineering Plastics' (STEP) af, en komt er tevens een einde aan mijn tijd in Enschede. Het schrijven van een proefschrift mag dan een wat eenzaam karwei zijn, velen hebben bijgedragen aan het tot stand komen van dit proefschrift, waarvoor allen dank. Een aantal van hen wil ik hier met name noemen. Mijn mentor Reinoud Gaymans, voor het bieden van de mogelijkheid te promoveren binnen een gezellige groep, en de begeleiding van de afgelopen 4 jaar. Mijn promotor Professor Struik, voor de kritische maar altijd bijzonder waardevolle opmerkingen en aanwijzingen. -
Synthesis and Characterization of Liquid Natural Rubber As Impact Modifier for Epoxy Resin
Available online at www.sciencedirect.com ScienceDirect Physics Procedia 55 ( 2014 ) 129 – 137 Eight International Conference on Material Sciences (CSM8-ISM5) Synthesis And Characterization Of Liquid Natural Rubber As Impact Modifier For Epoxy Resin A.B. BEN SALEHa, Z.A. MOHD ISHAKb, A. S. HASHIMb, W.A. KAMILc, U.S. ISHIAKUd Faculty of education, Misurata University,Misurata, Libyaa, School of Material and Mineral Resourcesb School of Chemical Sciencec Universiti Sains Malaysia, Penang, Malaysia Kyoto Institute of Technology, Matsugasaki, Sakyo-kud Kyoto 606-8585, Japan Abstract Liquid natural rubber (LNR) with a molecular weight CMn =16×103 was prepared by the depolymerization of deproteinized natural rubber latex (DPNR). The liquid natural rubber (LNR) was characterized by FTIR and H’NMR spectroscopic analysis. LNR was premixed with the epoxy resin (EP) and cured with a diamine curing agent for 1 h at 100 °C and post cured at 110 °C, for 2 h in air oven. The modified EP containing different contents of LNR (5, 10, 15 and 20 phr) were evaluated. Thermal, mechanical and morphology properties were determined. The fracture toughness (KIC) of both unmodified and modified EPs were determined on static loaded single edge notched (SEN-B) specimens at room temperature. The glass transition temperatures (Tg) of the modified EPs were decreased with increasing LNR content. The strengths and modulus of EPs were slightly reduced with the incorporation of LNR. The effect was also reflected in the significant increase in the tensile strain of modified EP. Fracture toughness of the EP was observed to increase with the presence of LNR. -
Toughening Behaviour of Rubber-Modified Thermoplastic Polymers Involving Very Small Rubber Particles: 1
Toughening behaviour of rubber-modified thermoplastic polymers involving very small rubber particles: 1. A criterion for internal rubber cavitation D. Dompas and G. Groeninckx* Catholic University of Leuven, Laboratory of Macrornolecular Structural Chemistry, Celestijnenlaan 20OF, B-3001 Heverlee, Belgium (Received 26 January 1994) The criteria for internal cavitation of rubber particles have been evaluated. It is shown that internal rubber cavitation can be considered as an energy balance between the strain energy relieved by cavitation and the surface energy associated with the generation of a new surface. The model predicts that there exists a critical particle size for cavitation. Very small particles (100-200nm) are not able to cavitate. This critical-particle-size concept explains the decrease in toughening efficiency in different rubber-modified systems involving very small particles. (Keywords: rubber toughening; particle size; rubber cavitation) INTRODUCTION and associated matrix shear yielding is found in rubber-modified PC ~-7, PVC a-x°, poly(butylene tere- Many glassy polymers are brittle. For structural applica- phthalate (PBT) 11, nylon.612-1 s, nylon_6,616 and epoxy tions, this is clearly unwanted and it is well known that systems17 20. The matrix polymers in these rubber- the impact properties can be improved by the incorpora- modified systems are either crosslinked or have a high tion of a dispersed elastomeric phase Lz. The mechanism entanglement density, thus being polymers for which the by which the toughness is enhanced depends on the crazing mechanism is suppressed 21. This is not to say intrinsic ductility of the matrix material and on the that rubber cavitation can only appear in high-entangle- morphology of the blends 3. -
Polymer Chemistry Sem-6, Dse-B3 Part-3, Ppt-3
POLYMER CHEMISTRY SEM-6, DSE-B3 PART-3, PPT-3 Dr. Kalyan Kumar Mandal Associate Professor St. Paul’s C. M. College Kolkata Polymer Chemistry Part-3 Contents • Styrene Based Copolymers • Poly(Vinyl Chloride): A Thermoplastic Polymer Styrene Based Copolymers Styrene-Acrylonitrile (SAN) Copolymers and ABS Resins • To obtain a styrene-based polymer of higher impact strength and higher heat distortion temperature at the same time, styrene is copolymerized with 20-30% acrylonitrile. Such copolymers have better chemical and solvent resistance, and much better resistance to stress cracking and crazing while retaining the transparency of the homopolymer at the same time. In many respects SAN copolymers are also better than poly(methyl methacrylate) and cellulose acetate, two other transparent thermoplastics. • ABS resins are terpolymers of acrylonitrile, butadiene and styrene, prepared by interpolymerization (grafting) of styrene and acrylonitrile on polybutadiene or through blending of SAN copolymers with butadiene–acrylonitrile (Nitrile) rubber. Impact improvement is far better if the rubber in the blend is lightly cross-linked. The impact resistance of ABS resins may be as high as 6-7 ft lb. per inch of notch. This Lecture is prepared by Dr. K. K. Mandal, SPCMC, Kolkata Styrene-Acrylonitrile (SAN) Copolymers • Styrene acrylonitrile resin is a copolymer plastic consisting of styrene (Ph-CH=CH2) and acrylonitrile (CH2=CH-CN). It is also known as SAN. It is widely used in place of polystyrene owing to its greater thermal resistance. • The chains of between 70 and 80% by weight styrene and 20 to 30% acrylonitrile. Larger acrylonitrile content improves mechanical properties and chemical resistance, but also adds a yellow tint to the normally transparent plastic. -
And Micromechanics of Polymers
Sample Pages Goerg H. Michler, Francisco J. Baltá-Calleja Nano- and Micromechanics of Polymers Structure Modification and Improvement of Properties ISBN: 978-3-446-42767-9 For further information and order see http://www.hanser.de/978-3-446-42767-9 or contact your bookseller. © Carl Hanser Verlag, München 4 4 Crazing 4.1 The Phenomenon of „Craze“ As mentioned in the previous chapter, plastic deformation of polymers is a heterogeneous process, concentrated in local zones. Local plastic processes appear in form of shear bands, void formation with fibrillation, inter- and intra- spherulitic deformation, and formation of crazes. Crazing has been inten sively investigated over the last 60 years, with major reviews appearing regularly [1−8]. It is usually assumed that crazes are typical of amorphous, glassy polymers, such as PS, SAN, and PMMA, which are brittle at room temperature with elongation at break of a few percent. The reason is that crazes are visible in the amorphous, glassy polymers during mechanical loading with the eye in reflected light (see Fig. 4.1). Their macroscopic appearance of cracks left these zones with the name of craze. “Craze” is an old English word for hairline crack. Synonyms include “craquele” (from the pattern of cracks in the glaze of porcelain (china) or pottery, microcracks and “silver cracks” (from the Russian name). FIGURE 4.1 Tensile bars after loading in overview (left) and low optical magnifications of the bars (right); a) polystyrene; b) poly(methylmethacrylate) 120 4 Crazing Several crack-like zones The formation of crack-like zones in brittle materials under stress is a very general phenomenon, which is observed in very different materials: Inorganic glasses are typical examples of amorphous brittle materials with very fast crack propagation. -
Multiscale Behavior of Fused Deposition Additively Manufactured Thermoplastic Cellular Materials Kaitlynn Melissa Conway Clemson University, [email protected]
Clemson University TigerPrints All Theses Theses 8-2018 Multiscale Behavior of Fused Deposition Additively Manufactured Thermoplastic Cellular Materials Kaitlynn Melissa Conway Clemson University, [email protected] Follow this and additional works at: https://tigerprints.clemson.edu/all_theses Recommended Citation Conway, Kaitlynn Melissa, "Multiscale Behavior of Fused Deposition Additively Manufactured Thermoplastic Cellular Materials" (2018). All Theses. 2954. https://tigerprints.clemson.edu/all_theses/2954 This Thesis is brought to you for free and open access by the Theses at TigerPrints. It has been accepted for inclusion in All Theses by an authorized administrator of TigerPrints. For more information, please contact [email protected]. MULTISCALE BEHAVIOR OF FUSED DEPOSITION ADDITIVELY MANUFACTURED THERMOPLASTIC CELLULAR MATERIALS A Thesis Presented to the Graduate School of Clemson University In Partial Fulfillment of the Requirements for the Degree Master of Science Mechanical Engineering by Kaitlynn Melissa Conway August 2018 Accepted by: Dr. Garrett J. Pataky: Thesis Advisor, Committee Chair Dr. Joshua D. Summers Dr. Huijuan Zhao Abstract Cellular materials are known for being lightweight as well as deforming in unique ways. Cellular materials have become more viable due to additive manufacturing (AM). AM cellular materials are easier to fabricate compared to traditional cellular materials and AM cellular materials are not as limited in geometry as traditional fabrication methods were. AM materials were studied in this paper in a two-phase approach. Phase 1 focused on the global mechanical properties of AM cellular materials. Phase 2 focused on the crazing of AM thermoplastic glassy polymers and how additive manufacturing affects the behavior or cellular materials. Because cellular materials do not have a consistent cross sectional area throughout the material, there is not a standard cross sectional area to use for property calculations. -
Chapter 3 Rubber Elasticity
Chapter 23 Fracture and Toughening Fracture behavior Fracture testing Impact/Fatigue Toughening Failure or fracture Ch 23 sl 2 failure [破碎, 破斷] ~ rupture by exceedingly large stress fracture [破壞] ~ failure by crack propagation micromechanism of fracture Fig 23.4 p561 chain scission or slip? radical conc’n by ESR Upon stress, 1. chain slip (against Xtal, Xlinking, entangle) higher than ey 2a. crazing/yielding or lower than ef 2b. chain scission (early) when high Xc, low Mc, low Me 3. then chain scission 4. voiding crack fracture effect of MM (on strength) Fig 23.5 M = 6 – 8 Me? MM should be much higher than Me. Brittle fracture Ch 23 sl 3 theoretical (tensile) strength of solids (by Griffith) for interatomic separation pp557-558 st = tensile strength whiskers, su or sf ≈ E/10 su = ultimate stress sf = fracture stress polymer single crystals, su or sf ≈ E/40 sc = craze stress for (isotropic glassy unfilled) polymers, su = sf = sc if brittle sf < E/100 < stheo E = 1 – 3 GPa, sf < 100 MPa due to flaw [crack, notch, or inclusion], which cause stress concentration and plastic constraint Ch 23 sl 4 stress concentration Ahead of crack tip, stress is larger than the applied stress s0 s0 circular crack [a=b], s = 3 s0 crack-tip radius Fig 23.6 p562 Fracture mechanics Ch 23 sl 5 energy balance approach LEFM [linear elastic FM] specimen with crack length 2a Crack grows when released (elastic) strain energy by stress [s2pa2/2E] is greater than created surface energy [4ag] Griffith (brittle) fracture criterion plane s plane -
Toughening of Epoxy Resin Using Natural And
TOUGHENING OF EPOXY RESIN WITH MODIFIED LIQUID NATURAL RUBBERS AND ACRYLONITRILE-BUTADIENE LIQUID RUBBERS By ABDULALI BASHIR AHMED BEN SALEH Thesis submitted in fulfilment of the requirements for the degree of doctor of philosophy September 2005 [96:1-5] Read! In the name of your Lord who created - Created the human from something which clings. Read! And your Lord is Most Bountiful - He who taught (the use of) the Pen, Taught the human that which he knew not. Chapter 96: AL-ALAQ Acknowledgements By the name of Allah the beneficent and the merciful, all praise and thanks is due to Allah the indivisible creator and sustainer of the world, he can never be praised or thanked enough. I would like to extend my sincere gratitude to my big family (my parents, brothers and sisters) for their support, dedication and advice. Not forgetting my small family (my wife and daughters) who had constantly given me healthy weather in all aspects of my life study. I would like to thank my supervisors, Prof. Dr. Zainal Arifin .Mohmed Ishak, Associate Prof. Dr. Azanam Shah Hashim and Associate Prof. Dr. Wan Ahmed Kamil for their continuing support & mentorship in my study. The assistance of Prof. Dr. Umaru S. Ishiaku at the earlier stages of my research is also acknowledged. Acknowledgements are also due to staff and laboratory technician, School of Materials and Mineral Resource Engineering. My respect and thanks are due to all staff and laboratory technician, School of Chemical Science, Universiti Sains Malaysia for their tireless help and cooperation during my research. I would also like to extend my grateful appreciation and thanks to my colleagues, classmates and friends, for their friendship and support and all postgraduate students of polymer department are also acknowledged. -
Studies of Rubber-Toughened Poly(Methyl Methacrylate) : 1
Studies of rubber-toughened poly(methyl methacrylate) : 1. Preparation and thermal properties of blends of poly(methyl methacrylate) with multiple-layer toughening particles P. A. Lovell*, J. McDonald, D. E. J. Saunders and R. J. Young Polymer Science and Technology Group, Manchester Materials Science Centre, UMIST, Grosvenor Street, Manchester M1 7HS, UK (Received 9 March 1992) The use of sequential emulsion polymerization to prepare toughening particles which comprise two, three and four radially alternating rubbery and glassy layers is described. The conditions which lead to control of particle size and morphology are discussed. The particles were crosslinked during their formation in order to ensure that they retained their size and morphology during blending with poly(methyl methacrylate) (PMMA). In this way, rubber-toughened (RT) PMMA materials with rubbery phases of predefined particle size and morphology were produced, as confirmed by transmission electron microscopy. The glass transitions of the three types of RTPMMA materials were essentially identical because the matrix PMMA was common to each blend and because the rubbery and glassy phases of each of the types of toughening particle were identical in composition. (Keywords: poly(methyl methacrylate); thermal properties; blends) INTRODUCTION properties of the matrix PMMA, the composition, morphology, size of the dispersed rubbery phase and the Poly (methyl methacrylate) (PM MA) is a classic example level of inclusion of the toughening particles. Although of a brittle thermoplastic and for several decades efforts these improved materials have been commercialized have been made to improve its fracture resistance via successfully, in comparison to other toughened polymers rubber toughening L2. The earlier efforts focused upon there are relatively few reports of investigations into their use of suspension polymerization to produce composite preparation, properties and deformation behaviour. -
Glass Transition Temperature and Microhardness of Compatible and Incompatible Elastomer/Plastomer Blends M
15 GLASS TRANSITION TEMPERATURE AND MICROHARDNESS OF COMPATIBLE AND INCOMPATIBLE ELASTOMER/PLASTOMER BLENDS M. F. MINA Department of Physics, Faculty of Engineering, Bangladesh University of Engineering and Technology, Dhaka-1000, Bangladesh G. H. MICHLER Department of Material Science, Martin-Luther-University, Halle-Wittenberg, D-06099 Halle/S., Germany F. J. BALTA CALLEJA Institute for the Structure of Matter, CSIC, Serrano 119, 28006 Madrid, Spain ABSTRACT Glass transition temperature (Tg) of core-shell particles-toughened poly(methyl- methacrylate) (CSPTPMMA) and natural rubber-toughened PMMA (NRTPMMA), which are basically the PMMA/elastomer blends with different concentrations of elastomer heterogeneously distributed in the samples, was investigated by means of differential scanning calorimetry (DSC), dynamic mechanical analysis (DMA) and microindentation technique (MT). Microhardness (H) of the samples was measured using MT. Core-shell particles (CSP) with a rubbery shell and natural rubber (NR) were used as reinforcing materials for the production of compatible and incompatible blends, respectively. Results reveal a good correlation of the glass transition temperature (Tg) obtained from DSC and DMA, and that deduced from MT. The H–value of each sample is compared with its Tg–value. Increase of Tg with the increase of H, which is a general behavior of polymers, is not maintained in the both blends investigated. Contrary to expectation, H is shown to decrease with increasing glass transition temperature in case of CSP-toughened compatible blends while it decreases with the decrease of Tg-value only in case of NR-modified incompatible blends for lower NR concentration (<1 wt%) and does not depend on Tg for rubber content higher than 1 wt%. -
Distributed Crazing in Rubber-Toughened Polymers
1 Continuum-micromechanical modeling of 2 distributed crazing in rubber-toughened polymers a b c a1 3 M. Helbig , E. van der Giessen , A.H. Clausen , Th. Seelig a 4 Institute of Mechanics, Karlsruhe Institute of Technology, Kaiserstrasse 12, 76131 Karlsruhe, Germany b 5 Zernike Institute for Advanced Materials, University of Groningen, Nijenborgh 4, 9747 AG Groningen, 6 The Netherlands c 7 Structural Impact Laboratory (SIMLab), Department of Structural Engineering, Norwegian University of 8 Science and Technology (NTNU), Rich. Birkelandsvei 1A, NO-7491 Trondheim, Norway 9 Abstract 10 A micromechanics based constitutive model is developed that focuses on the effect 11 of distributed crazing in the overall inelastic deformation behavior of rubber-toughened 12 ABS (acrylonitrile-butadiene-styrene) materials. While ABS is known to exhibit craz- 13 ing and shear yielding as inelastic deformation mechanisms, the present work is meant 14 to complement earlier studies where solely shear yielding was considered. In order to 15 analyse the role of either mechanism separately, we here look at the other extreme and 16 assume that the formation and growth of multiple crazes in the glassy matrix between 17 dispersed rubber particles is the major source of overall inelastic strain. This notion is 18 cast into a homogenized material model that explicitly accounts for the specific (cohesive 19 zone-like) kinematics of craze opening as well as for microstructural parameters such as 20 the volume fraction and size of the rubber particles. Numerical simulations on single- 21 edge-notch-tension (SENT) specimens are performed in order to investigate effects of the 22 microstructure on the overall fracture behavior. -
(PHBV) Bioplastic for Food Packaging Applications Disse
Natural Rubber Toughened Poly (3-hydroxybutyrate-co-3-hydroxyvalerate) (PHBV) Bioplastic for Food Packaging Applications Dissertation Presented in Partial Fulfillment of the Requirements for the Degree Doctor of Philosophy in the Graduate School of The Ohio State University By Xiaoying Zhao Graduate Program in Food Science and Technology The Ohio State University 2018 Dissertation Committee Yael Vodovotz, Advisor Katrina Cornish, Advisor Dr. Kurt Koelling Dr. David Nagib 1 Copyrighted by Xiaoying Zhao 2018 2 Abstract The packaging industry is searching for bio-based alternatives. Poly-(β- hydroxybutyrate-co-valerate) (PHBV) is a promising bioplastic made from bacterial fermentation of renewable resources. It has mechanical properties similar to propylene (PP) but is more brittle. PHBV toughness and flexibility must be improved before it can be commercially used for packaging. An industrially viable and economically effective way to toughen PHBV is blending it with flexible and ductile materials. Natural rubber (NR) is a promising toughening material due to its unique combination of ductility, flexibility, and renewability. NR has various packaging applications such as films and tapes. Blends from rubber and thermoplastics, such as polyethylene and PP, with improved toughness, flexibility, and other properties have been used in packaging industry. Therefore, the objective of this work is to improve PHBV toughness and flexibility through NR incorporation, elucidate the reaction mechanism of the coagent- assisted peroxide-induced reactive extrusion of NR and PHBV, optimize the PHBV/NR blends, and evaluate their suitability for food packaging applications. In this study, 2-25 wt. %NR was incorporated into PHBV through reactive extrusion in the presence of peroxide to improve PHBV flexibility and toughness.