Use Style: Paper Title
Total Page:16
File Type:pdf, Size:1020Kb
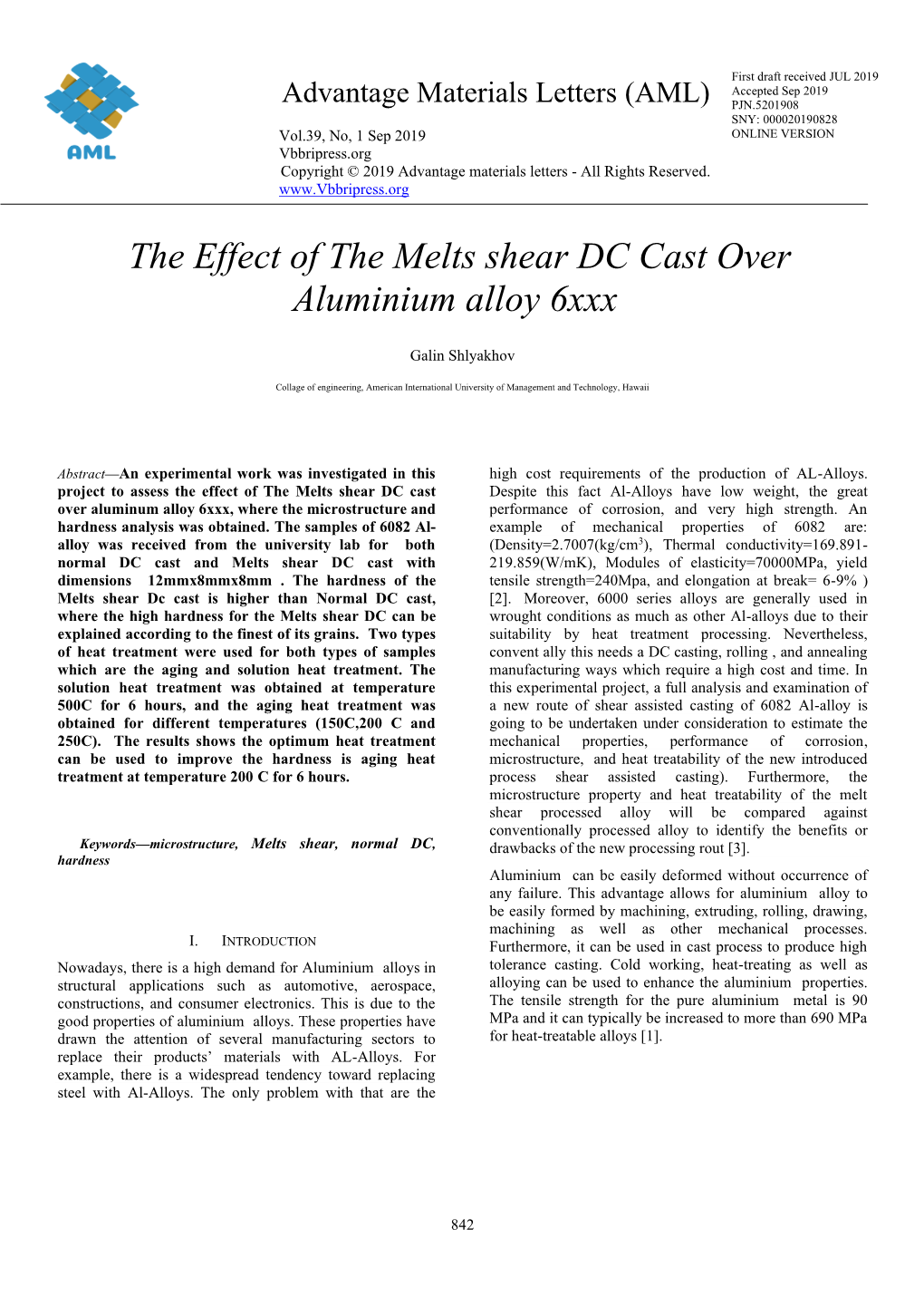
Load more
Recommended publications
-
Establishing a Correlation Between Interfacial Microstructures and Corro- Sion Initiation Sites in Al/Cu Joints by SEM-EDS and AFM-SKPFM
This may be the author’s version of a work that was submitted/accepted for publication in the following source: Sarvghad Moghaddam, Madjid, Parvizi, R., Davoodi, Ali, Haddad- Sabzevar, Mohsen, & Imani, Amin (2014) Establishing a correlation between interfacial microstructures and corro- sion initiation sites in Al/Cu joints by SEM-EDS and AFM-SKPFM. Corrosion Science, 79, pp. 148-158. This file was downloaded from: https://eprints.qut.edu.au/95930/ c Consult author(s) regarding copyright matters This work is covered by copyright. Unless the document is being made available under a Creative Commons Licence, you must assume that re-use is limited to personal use and that permission from the copyright owner must be obtained for all other uses. If the docu- ment is available under a Creative Commons License (or other specified license) then refer to the Licence for details of permitted re-use. It is a condition of access that users recog- nise and abide by the legal requirements associated with these rights. If you believe that this work infringes copyright please provide details by email to [email protected] License: Creative Commons: Attribution-Noncommercial-No Derivative Works 2.5 Notice: Please note that this document may not be the Version of Record (i.e. published version) of the work. Author manuscript versions (as Sub- mitted for peer review or as Accepted for publication after peer review) can be identified by an absence of publisher branding and/or typeset appear- ance. If there is any doubt, please refer to the published source. https://doi.org/10.1016/j.corsci.2013.10.039 Accepted Manuscript Establishing a Correlation between Interfacial Microstructures and Corrosion Initiation Sites in Al/Cu Joints by SEM-EDS and AFM-SKPFM M. -
191002 Knowledge: K1.02 [2.7/2.9] Qid: P6 (B1806)
NRC Generic Fundamentals Examination Question Bank--PWR May 2020 TOPIC: 191002 KNOWLEDGE: K1.02 [2.7/2.9] QID: P6 (B1806) Density input is normally used in steam flow instruments to convert __________ into __________. A. mass flow rate; volumetric flow rate B. volumetric flow rate; mass flow rate C. mass flow rate; differential pressure D. differential pressure; volumetric flow rate ANSWER: B. TOPIC: 191002 KNOWLEDGE: K1.02 [2.7/2.9] QID: P305 (B2906) If the steam pressure input to a density-compensated steam flow instrument fails high, the associated flow rate indication will... A. decrease, because the density input has decreased. B. increase, because the density input has decreased. C. decrease, because the density input has increased. D. increase, because the density input has increased. ANSWER: D. -1- Sensors and Detectors NRC Generic Fundamentals Examination Question Bank--PWR May 2020 TOPIC: 191002 KNOWLEDGE: K1.02 [2.7/2.9] QID: P406 (B1606) The density compensating input to a steam flow instrument is used to convert volumetric flow rate into… A. velocity flow rate. B. gallons per minute. C. mass flow rate. D. differential flow rate. ANSWER: C. -2- Sensors and Detectors NRC Generic Fundamentals Examination Question Bank--PWR May 2020 TOPIC: 191002 KNOWLEDGE: K1.02 [2.7/2.9] QID: P1212 If the steam pressure input to a density-compensated steam flow instrument fails low, the indicated flow rate will... A. increase, because the density input has increased. B. decrease, because the density input has increased. C. increase, because the density input has decreased. D. decrease, because the density input has decreased. -
Machining of Aluminum and Aluminum Alloys / 763
ASM Handbook, Volume 16: Machining Copyright © 1989 ASM International® ASM Handbook Committee, p 761-804 All rights reserved. DOI: 10.1361/asmhba0002184 www.asminternational.org MachJning of Aluminum and AlumJnum Alloys ALUMINUM ALLOYS can be ma- -r.. _ . lul Tools with small rake angles can normally chined rapidly and economically. Because be used with little danger of burring the part ," ,' ,,'7.,','_ ' , '~: £,~ " ~ ! f / "' " of their complex metallurgical structure, or of developing buildup on the cutting their machining characteristics are superior ,, A edges of tools. Alloys having silicon as the to those of pure aluminum. major alloying element require tools with The microconstituents present in alumi- larger rake angles, and they are more eco- num alloys have important effects on ma- nomically machined at lower speeds and chining characteristics. Nonabrasive con- feeds. stituents have a beneficial effect, and ,o IIR Wrought Alloys. Most wrought alumi- insoluble abrasive constituents exert a det- num alloys have excellent machining char- rimental effect on tool life and surface qual- acteristics; several are well suited to multi- ity. Constituents that are insoluble but soft B pie-operation machining. A thorough and nonabrasive are beneficial because they e,,{' , understanding of tool designs and machin- assist in chip breakage; such constituents s,~ ,.t ing practices is essential for full utilization are purposely added in formulating high- of the free-machining qualities of aluminum strength free-cutting alloys for processing in alloys. high-speed automatic bar and chucking ma- Strain-hardenable alloys (including chines. " ~ ~p /"~ commercially pure aluminum) contain no In general, the softer ailoys~and, to a alloying elements that would render them lesser extent, some of the harder al- c • o c hardenable by solution heat treatment and ,p loys--are likely to form a built-up edge on precipitation, but they can be strengthened the cutting lip of the tool. -
Corrosion Behaviour of Aluminum Alloys Weldments: a Literature Survey
6 III March 2018 http://doi.org/10.22214/ijraset.2018.3464 International Journal for Research in Applied Science & Engineering Technology (IJRASET) ISSN: 2321-9653; IC Value: 45.98; SJ Impact Factor: 6.887 Volume 6 Issue III, March 2018- Available at www.ijraset.com Corrosion Behaviour of Aluminum Alloys Weldments: A Literature Survey Vilas Hans1, Prabdeep Singh Bajwa2 1, 2 Department of Mechanical Engineering, LRIET, Solan, Himachal Pradesh, India Abstract: Aluminum alloys of 5xxx series and their welded joints show good resistance to corrosion in sea water. Metallic corrosion takes place in marine environments. In the ship manufacturing industries, welding is used to join the different aluminum parts of the ship structure, these weldments are generally remaining dip in saline water of sea or remain in salt foggy atmosphere, which gets eroded early when comes in contact with salt-water solution. A literature survey has been carried out to understanding of welding and corrosion of aluminum alloys. Keywords: 5xxx Aluminum alloys; marine corrosion; welding. I. INTRODUCTION Metallic corrosion takes place in wet environments when the chemical or electrochemical reaction between a metal and the surrounding environment results in the oxidation of the metal. For corrosion to occur, electrons are produced by the anodic oxidation of the metal must be consumed in a cathodic reaction. These two processes can take place on different parts of a metal structure providing that there is a conducting path for the electrons between the two, and a continuous electrolyte path for ion transport. Aluminium is highly reactive, with a negative standard electrode potential of - 1660mV, and is therefore unstable in the presence of water. -
Design of a Kite Controller for Airborne Wind Energy
Dissertation for Masters of Science in Engineering Design of a Kite Controller for Airborne Wind Energy Matteo Milandri February 2015 University of Cape Town University of Cape Town Faculty Engineering and the Built Environment Electrical Engineering Department The copyright of this thesis vests in the author. No quotation from it or information derived from it is to be published without full acknowledgement of the source. The thesis is to be used for private study or non- commercial research purposes only. Published by the University of Cape Town (UCT) in terms of the non-exclusive license granted to UCT by the author. University of Cape Town Supervised by Samuel Ginsberg Dr. Ian de Vries Declaration I know the meaning of plagiarism and declare that all the work in the document, save for that which is properly acknowledged, is my own. Matteo F. Milandri ___________________ i Abstract Airborne wind energy is a field of technology being developed to make use of the vast, renewable wind power resource which is above the reach of traditional wind turbines, without the need for a large tower. Much analytical research has been undertaken in recent years to better understand the problem space. However, there are relatively few working systems that demonstrate their functioning and can be compared with simulations and theory. Off-grid power systems still rely heavily on diesel generators, so devices that tap renewable energy sources with similar ease of deployment and lower cost of energy would help this sector to reduce its reliance on expensive, polluting, fossil fuels. The development of these systems is often performed by teams with business interests leaving little open access content available regarding the design process of such devices or the data that they provide. -
International Alloy Designations and Chemical Composition Limits for Wrought Aluminum and Wrought Aluminum Alloys
International Alloy Designations and Chemical Composition Limits for Wrought Aluminum and Wrought Aluminum Alloys 1525 Wilson Boulevard, Arlington, VA 22209 www.aluminum.org With Support for On-line Access From: Aluminum Extruders Council Australian Aluminium Council Ltd. European Aluminium Association Japan Aluminium Association Alro S.A, R omania Revised: January 2015 Supersedes: February 2009 © Copyright 2015, The Aluminum Association, Inc. Unauthorized reproduction and sale by photocopy or any other method is illegal . Use of the Information The Aluminum Association has used its best efforts in compiling the information contained in this publication. Although the Association believes that its compilation procedures are reliable, it does not warrant, either expressly or impliedly, the accuracy or completeness of this information. The Aluminum Association assumes no responsibility or liability for the use of the information herein. All Aluminum Association published standards, data, specifications and other material are reviewed at least every five years and revised, reaffirmed or withdrawn. Users are advised to contact The Aluminum Association to ascertain whether the information in this publication has been superseded in the interim between publication and proposed use. CONTENTS Page FOREWORD ........................................................................................................... i SIGNATORIES TO THE DECLARATION OF ACCORD ..................................... ii-iii REGISTERED DESIGNATIONS AND CHEMICAL COMPOSITION -
Effect of Tool Geometry and Welding Speed on Mechanical Properties and Microstructure of Friction Stir Welded Joints of Aluminium Alloys Aa6082-T6
A RCHIVE OFMECHANICAL ENGINEERING VOL. LXI 2014 Number 3 10.2478/meceng-2014-0026 Key words: FSW, aluminium alloys AA6082, tool pin geometry, weld speed, mechanical and metallurgical characterization HIRALAL SUBHASH PATIL ∗, SANJAY N. SOMAN ∗∗ EFFECT OF TOOL GEOMETRY AND WELDING SPEED ON MECHANICAL PROPERTIES AND MICROSTRUCTURE OF FRICTION STIR WELDED JOINTS OF ALUMINIUM ALLOYS AA6082-T6 Friction stir welding is a solid state innovative joining technique, widely being used for joining aluminium alloys in aerospace, marine automotive and many other applications of commercial importance. The welding parameters and tool pin profile play a major role in deciding the weld quality. In this paper, an attempt has been made to understand the influences of welding speed and pin profile of the tool on friction stir welded joints of AA6082-T6 alloy. Three different tool pin profiles (tapered cylin- drical four flutes, triangular and hexagonal) have been used to fabricate the joints at different welding speeds in the range of 30 to 74 mm/min. Microhardness (HV) and tensile tests performed at room temperature were used to evaluate the mechanical properties of the joints. In order to analyse the microstructural evolution of the ma- terial, the weld’s cross-sections were observed optically and SEM observations were made of the fracture surfaces. From this investigation it is found that the hexagonal tool pin profile produces mechanically sound and metallurgically defect free welds compared to other tool pin profiles. 1. Introduction Friction stir welding (FSW) is a solid-state joining process developed and patented by The Welding Institute (TWI) [1-2], and has emerged as a welding technique used in high strength alloys (2xxx, 6xxx, 7xxx and 8xxx series) for aerospace, automotive and marine applications [3] that were difficult to join with conventional techniques. -
6061 Aluminum
Alro Steel Metals Guide Aluminum Bar, Sheet, Plate, Structurals, Tube & Pipe Aluminum Cold Finished Bar ................. 6-2 thru 6-16 Aluminum CF Tolerances ..................... 6-17 thru 6-18 Aluminum Extruded Bar ....................... 6-19 thru 6-31 Aluminum Extruded Structurals .......... 6-32 thru 6-40 Aluminum Tube & Pipe ........................ 6-41 thru 6-51 Aluminum Extruded Tolerances .......... 6-52 thru 6-57 Aluminum Sheet & Plate ...................... 6-58 thru 6-65 Aluminum Cast Plate ............................ 6-66 thru 6-74 Aluminum Tread Plate .......................................... 6-75 Sheet & Plate Tolerances & Data ........ 6-76 thru 6-92 Comparative Characteristics .............. 6-93 thru 6-97 Specification Cross Reference .......... 6-98 thru 6-102 NOTE: Typical properties shown for alloys are not guaranteed by publication herein. In most cases, the values are averages for various sizes, product forms and manufacturing practices. The typical properties do not exactly represent particular products or sizes. The data is intended only as a basis for comparing alloys and tempers and should not be specified as engineering requirements or used for design purposes. Aluminum WARNING: These products can potentially expose you to chemicals including Nickel, Chromium, Lead, Cobalt, Mercury and Beryllium, which are known to the state of California to cause cancer and/or birth defects or other reproductive harm. For more information, visit www.P65Warnings.ca.gov 6-1 alro.com ® Alro Steel Metals Guide Aluminum Rod, Bar and Wire (Cold Finished) Rounds • Flats • Hexagons • Squares Alloy Descriptions and Applications 2011 – This free machining alloy compares favorably with free cutting brass. It is the most suitable alloy for machining on automatics, milling machines, lathes, planers, shapers and other machine tools, and is the most widely used alloy for all types of screw machine parts. -
The Effect of Fe Content on Intergranular Corrosion Behaviour
Turid Danbolt Turid 2019 thesis Master's NTNU Norwegian University of Science and Technology Master's thesis Faculty of Natural Sciences Department of Materials Science and Engineering June 2019 of a6005AluminiumAlloy Intergranular CorrosionBehaviour The EffectofFeContenton Turid Danbolt The Effect of Fe Content on Intergranular Corrosion Behaviour of a 6005 Aluminium Alloy Turid Danbolt Materials Science and Engineering Submission date: June 2019 Supervisor: Otto Lunder Co-supervisor: Trond Furu Norwegian University of Science and Technology Department of Materials Science and Engineering Preface This thesis is a continuation of the course TMT4500 Materials Technology, Specialization Project, and has been conducted at Department of Materials Engineering, Norwegian University of Science and Technology (NTNU) from January to June 2019. The work is a part of the FICAL project (Fundamentals of Intergranular Corrosion of Aluminium Alloys), a collaboration between NTNU, SINTEF, Hydro, Gränges, Benteler and Steertec. The author has performed all the experimental work as described in this thesis except for MTEX analysis of EBSD data and TEM sample preparation and analysis, which was conducted by Adrian Lervik (NTNU), and optical emission spectrometry, which was conducted by Trond Furu (Hydro). Trondheim, June 14, 2019 Turid Danbolt i Blank page ii Acknowledgements I would like to thank my supervisors, Otto Lunder1 and Trond Furu2, for their valuable input and guidance throughout this work. I also want to express my gratitude to Adrian Lervik3 for his help with EBSD analysis, TEM imaging and valuable insight which has been essential to completing this thesis. Yingda Yu4 deserves special recognition for his patience and indispensable help with SEM techniques. -
Alloy Designation, Processing, and Use of AA6XXX Series Aluminium Alloys
International Scholarly Research Network ISRN Metallurgy Volume 2012, Article ID 165082, 15 pages doi:10.5402/2012/165082 Review Article Alloy Designation, Processing, and Use of AA6XXX Series Aluminium Alloys Prantik Mukhopadhyay Electron Microscope Group, Defence Metallurgical Research Laboratory, Kanchanbagh, Hyderabad 500058, India Correspondence should be addressed to Prantik Mukhopadhyay, [email protected] Received 1 February 2012; Accepted 23 February 2012 Academic Editors: R. Hebert and Y. Yamabe-Mitarai Copyright © 2012 Prantik Mukhopadhyay. This is an open access article distributed under the Creative Commons Attribution License, which permits unrestricted use, distribution, and reproduction in any medium, provided the original work is properly cited. The strength-to-weight ratio offered by AA6XXX alloys and their enhanced mechanical properties have become crucial criteria for their use in light weight military vehicles, rockets, missiles, aircrafts, and cars, used for both defence and civil purpose. The focus of this review paper is to put together the latest knowledge available from various sources on alloy design, industrial processing, development of properties, and potential use of AA6XXX alloys. The direct chill (DC) cast AA6XXX wrought alloys which are subsequently processed by fabrication process like hot working, cold working, process annealing, and age hardening heat treatments are the foci of this review though designation section also contains the designations of cast alloys to provide the reader a broad overview on designation. World-wide accepted designations are briefly tabled along with their alloying elements. The effects of the alloying elements which are generally used for AA6XXX wrought alloys are discussed incorporating their interactions during wrought AA6XXX alloy fabrication. -
The Impact of the Casting Thickness on the Interfacial Heat Transfer And
The impact of the casting thickness on the interfacial heat transfer and solidification of the casting during permanent mold casting of an A356 alloy Anwar Hamasaiid, Matthew Dargusch, Gilles Dour To cite this version: Anwar Hamasaiid, Matthew Dargusch, Gilles Dour. The impact of the casting thickness on the interfacial heat transfer and solidification of the casting during permanent mold casting of anA356 alloy. Journal of Manufacturing Processes, Society of Manufacturing Engineers, 2019, 47, pp.229-237. 10.1016/j.jmapro.2019.09.039. hal-02320841 HAL Id: hal-02320841 https://hal-mines-albi.archives-ouvertes.fr/hal-02320841 Submitted on 8 Sep 2020 HAL is a multi-disciplinary open access L’archive ouverte pluridisciplinaire HAL, est archive for the deposit and dissemination of sci- destinée au dépôt et à la diffusion de documents entific research documents, whether they are pub- scientifiques de niveau recherche, publiés ou non, lished or not. The documents may come from émanant des établissements d’enseignement et de teaching and research institutions in France or recherche français ou étrangers, des laboratoires abroad, or from public or private research centers. publics ou privés. The impact of the casting thickness on the interfacial heat transfer and solidification of the casting during permanent mold casting of an A356 alloy A. Hamasaiida,b,c,d,⁎, M.S. Darguschb, G. Doura,e a Ecole des Mines d'Albi-Carmaux, CROMeP, now Institute Clement Ader, 81013, Albi Cedex 09, France b Centre for Advanced Materials Processing and Manufacturing, -
Aluminium SHEETS & PROFILES
CHAPAS y PERFILES de aluminio aluminium SHEETS & PROFILES www.alumisan.com ÍNDICE CHAPAS de aluminio aluminium SHEETS INDEX CHAPAS DE ALUMINIO 7 ALUMINIUM SHEETS BOBINAS DE ALUMINIO 16 ALUMINIUM COILS CHAPAS ESPECIALES 18 SPECIAL SHEETS ANTIDESLIZANTES GOFRADAS DE ALUMINIO CHAPAS SHEETSALUMINIUM NON-SLIP 18 EMBOSSED 19 SSL PERFORADAS SSL 20 PERFORATED 21 ESTAMPADAS DEPLOYÉ STAMPED 30 DEPLOYÉ 31 ANOLAC PANEL CELOSÍA ANOLAC 32 LATTICEWORK 34 FALSO TECHO SUELOS SUSPENDED CEILING 35 FLOOR 36 ALEACIONES 80 ALLOYS PERFILES de aluminio aluminium PROFILES PERFILES NORMALIZADOS PERFILES NORMALIZADOS PROFILES STANDARD 41 STANDARD PROFILES PERFILES PARA PORTALES 46 DOOR PROFILES PERFILES VARIOS 48 VARIOUS PROFILES ANCLAJES PARA FACHADAS 51 FACADE PROFILES ALEACIONES 84 ALLOYS perfi les de CARROCERÍA CHASSIS profi les PERFILES CARROCERÍA CHASSIS PROFILES PERFILES DE CARROCERÍA 55 CHASSIS PROFILES PANEL COMPOSITE COMPOSITE PANEL CARACTERÍSTICAS 62 CHARACTERISTICS COMPOSITE FR FACHADAS 64 BUILDING FR COMPOSITE COMPOSITE NIDO ABEJA 66 HONEYCOMB COMPOSITE PANEL COMPOSITE PANEL COMPOSITE PANEL COMPOSITE PE 68 PE COMPOSITE METACRILATO y POLICARBONATO METHACRYLATE & POLYCARBONATE METACRILATO 73 METHACRYLATE POLICARBONATO COMPACTO 74 COMPACT POLYCARBONATE POLICARBONATO ALVEOLAR 75 MULTIWALL POLICARBONATE POLICARBONATO PERFILADO Y POLICARBONATO METACRILATO & POLYCARBONATE METHACRYLATE 76 CORRUGATED POLYCARBONATE ALEACIONES de aluminio aluminium ALLOYS ALEACIONES CHAPAS 80 SHEETS ALLOYS ALEACIONES PERFILES ALEACIONES ALLOYS 84 PROFILE ALLOYS www.alumisan.com