Health and Safety Fundamentals and Hazards Within the Nuclear Fuel Cycle
Total Page:16
File Type:pdf, Size:1020Kb
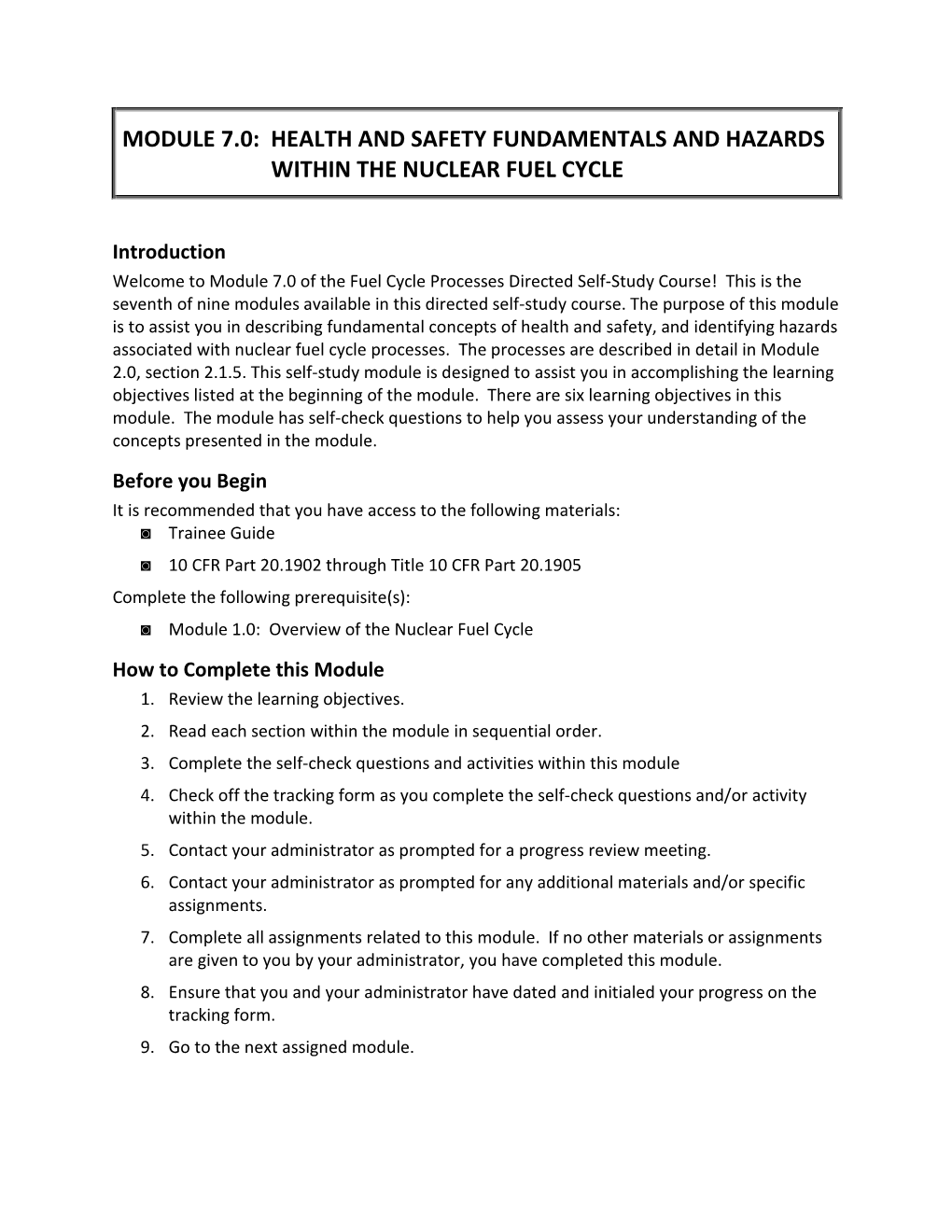
Load more
Recommended publications
-
Oct. 14, 1958 J. M. CARTER ET AL 2,856,263 PROCESS for the RECOVERY and PURIFICATION of URANIUM DEPOSITS Original Filed April 21, 1944 ‘7 Sheets-Sheet 1
Oct. 14, 1958 J. M. CARTER ET AL 2,856,263 PROCESS FOR THE RECOVERY AND PURIFICATION OF URANIUM DEPOSITS Original Filed April 21, 1944 ‘7 Sheets-Sheet 1 IN VEN TORS James M Car/‘er Mar?n D. ?ame/7 BY ATTORNEY Oct. 14, 1958 J. M. CARTER ET AL 2,856,263 PROCESS FOR THE RECOVERY AND PURIFICATION OF URANIUM DEPOSITS Original Filed April 21, 1944 7 Sheets-Sheet 55 QQOUMM,vRMmG w.9386mmE IN VEN TORS James M. Car fer By Marfin 0 Home/7 W4 W ATTORNEY Oct. 14,1958 J. M. CARTER ET AL 2,856,263 PROCESS FOR THE RECOVERY AND PURIFICATION _ OF URANIUM DEPOSITS Origlnal Filed April 21, 1944 7 Sheets-Sheet 4 SCRUBBYING. AND WASHING PARTS OF CALUTRON ' WITH HOT WATER Lf- WASH WATER :FCONDENSATE ' \WATERANDMAKE UP snevmc SOL/D IMPUR/ TIES — WASH WA TER -—p>- CONDENSING To DISCARD I OXIDIZING ORSALVAGE SOLUTION U02” Cu?! Few’! Cr!!! Ni“ FILTERING‘ - '3 PREC/P/TATE 0* |——‘———/ F/LTRA TE _ U024!- TO DISCARD __ EVAPORATING gel”,++ OR SALVAGE PRECIPITATING Z/VH OH AND F'LTER'NG gFlLTRA TE TO FURTHER T REATMENT Fig. 4 I INVENTORS ‘James M Cor fer, BY Mar/7'0 D. Kama/7 ' @ M A TTORNEY Oct. 14,1958 J. M. CARTER ET AL . 2,356,263 PROCESS FOR THE RECOVERY AND PURIFICATION 0F URANIUM DEPOSITS Original Filed April 21, 1944 7 Sheets-Sheet s DISSOLVING URANIUM METAL DEPOSITED ON COPPER COLLECTOR IN COLD HNo3 (8N) CONDENSATE I AND MAKE UP SOLUTION HNO3 U02" ' Cu ** 7—>— CONDENSING ' HN03 . EVAPORATI NG CONCENTRA TED \ soburj'o/v _ F/LTRA TE C35 cu {NHJLF H PRECIPITATING ‘ -[—-~’—NH4OH A ND F ILTERING ' f/RECIP/ TA TES *Cu/‘OHZH4 :0 01 ORTO SALVAGEDISCARD *Trace T__>_ DISSOLVING HN 0 3 ' - SOLUTION U02 +4 *cuvf *Tme F/LTRA TE PRECIPITATING _l—_'_NH OH AND FILTERING 4 { PREClP/TATE NH U 0 TO DISCARD ( ‘)2 2 ’ OR SALVAGE , r---‘“—? TO FURTHER TREATMENT 5 I N V EN TORS' James M Car/‘er ' Mar/"in D. -
ORGANOMETAT,T,TC CHEMISTRY of URANIUM a Thesis Submitted By
ORGANOMETAT,T,TC CHEMISTRY OF URANIUM A thesis submitted by R1TN R. SIGURDSON, B.Sc. for the DEGREE of DOCTOR of PHILOSOPHY of the UNIVERSITY of LONDON Royal College of Science Imperial College of Science and Technology London, SW7 ?AY August 1976 TO MY PARENTS 3 ACKNOWLEDGEMENTS I would like to express my gratitude to Professor Geoffrey Wilkinson, F.R.S. for his guidance and enthusiastic support throughout the course of this work. Many thanks are also extended to Drs. Dick Andersen, Ernesto Carmona-Guzman and David Cole-Hamilton for their suggestionS, encouragement and advice, and to Dr. Kostas Mertis for his patient help during the first months. I am indebted to the Canadian Research Council of Canada for financial support during the past three years. 4 CONTENTS ABSTRACT 6 INTRODUCTION I. The Chemistry of Uranium(IV) 8 .II. The Chemistry of Uranium(V) 15 III. The Chemistry of Uranium(VI) 16 CHAPTER I. DILITHIUMHEXAALKYLURANATE(IV) COMPLEXES I. Introduction 19 II. Results and Discussion 27 III. Experimental 35 CHAPTER II. TRILITHIUMOCTAALKYLURANATE(V) COMPLEXES I. Introduction 54 II. Results and Discussion 55 III. Experimental 60 CHAPTER III. ADDITION COMPOUNDS OF URANIUM(VI) HEXAISO-PROPDXIDE WITH LITHIUM, MAGNESIUM AND ALUMINIUM ALKYLS I. Introduction 70 II. Results and Discussion 71 III. Experimental 77 CHAPTER IV. ORGANOMETALLIC CHEMISTRY OF ADAMANTANE I. Introduction 84 II. Results and Discussion 85 III. Experimental 87 REFERENCES 92 5 ABBREVIATIONS Me - methyl Et - ethyl Prn- normal-propyl Pri- iso-propyl Bun- normal-butyl But- iso-butyl But- tertiary-butyl Ph - phenyl CP cyclopentadienyl DME - dimethoxyethane tmed - N,N,NI,N'-tetramethylethylenediamine pmdt - N,N,Nt,N",N"-pentamethyldiethylenetriamine g.l.c. -
1214 Final Report SF 10 03 06-CS
AN ASSESSMENT OF SOURCES, PATHWAYS, MECHANISMS AND RISKS OF CURRENT AND POTENTIAL FUTURE POLLUTION OF WATER AND SEDIMENTS IN GOLD-MINING AREAS OF THE WONDERFONTEINSPRUIT CATCHMENT Report to the WATER RESEARCH COMMISSION Compiled by Henk Coetzee Council for Geosience Reference to the whole of the publication should read: Coetzee, H. (compiler) 2004: An assessment of sources, pathways, mechanisms and risks of current and potential future pollution of water and sediments in gold-mining areas of the Wonderfonteinspruit catchment WRC Report No 1214/1/06, Pretoria, 266 pp. Reference to chapters/sections within the publication should read (example): Wade, P., Winde, F., Coetzee, H. (2004): Risk assessment. In: Coetzee, H (compiler): An assessment of sources, pathways, mechanisms and risks of current and potential future pollution of water and sediments in gold-mining areas of the Wonderfonteinspruit catchment. WRC Report No 1214/1/06, pp 119-165 WRC Report No 1214/1/06 ISBN No 1-77005-419-7 MARCH 2006 Executive summary 1. Introduction and historical background The eastern catchment of the Mooi River, also known as the Wonderfonteinspruit, has been identified in a number of studies as the site of significant radioactive and other pollution, generally attributed to the mining and processing of uraniferous gold ores in the area. With the establishment of West Rand Consolidated in 1887 gold mining reached the Wonderfonteinspruit catchment only one year after the discovery of gold on the Witwatersrand. By 1895 five more gold mines had started operations in the (non-dolomitic) headwater region of the Wonderfonteinspruit as the westernmost part of the West Rand goldfield. -
Química (2016) 27, 240---248
Educación Química (2016) 27, 240---248 educación Química www.educacionquimica.info REFLECTION Henry Enfield Roscoe Jaime Wisniak Department of Chemical Engineering, Ben-Gurion University of the Negev, Beer-Sheva 84105, Israel Received 14 July 2015; accepted 15 September 2015 Available online 1 June 2016 KEYWORDS Abstract Henry Enfield Roscoe (1833---1915), together with Robert Bunsen, his mentor, carried Photochemistry; on fundamental research in photochemistry, determining its laws and quantitative effects. His Vanadium; most important studies were on the chemistry of vanadium, uranium, tungsten, and molyb- Tungsten; denum, their oxides and oxychlorides, carrying on, for the first time, their synthesis and Niobium; separation. He also did important studies on public heath. His academic activities transformed Owens College (Victoria University) into the leading chemistry school in Britain. Public health; Education All Rights Reserved © 2016 Universidad Nacional Autónoma de México, Facultad de Química. This is an open access item distributed under the Creative Commons CC License BY-NC-ND 4.0. PALABRAS CLAVE Henry Enfield Roscoe Fotoquímica; Vanadio; Resumen Henry Enfield Roscoe (1833-1915), con la colaboración de Robert Bunsen, su men- Tungsten; tor, realizó estudios fundamentales sobre fotoquímica, fijando sus leyes, y la determinación Niobio; cuantitativa de sus efectos. Sus trabajos mas importantes fueron sobre la química del vanadio, uranio, tungsteno, y molibdeno, sus óxidos y oxicloruros, realizando, por primera vez, su sínte- Salud pública; Educación sis y separación. Asimismo, efectuó estudios importantes sobre salud pública. Sus actividades pedagógicas transformaron a Owens College (Victoria University) en la escuela líder de química en Inglaterra. Derechos Reservados © 2016 Universidad Nacional Autónoma de México, Facultad de Química. -
Identification of Potential Waste Processing and Waste Form Options for Molten Salt Reactors
Identification of Potential Waste Processing and Waste Form Options for Molten Salt Reactors Prepared for U.S. Department of Energy MSR Campaign B.J. Riley,(a) J. McFarlane,(b) G.D. DelCul,(b) J.D. Vienna,(a) C.I. Contescu,(b) L.M. Hay,(a) A.V. Savino,(a) H.E. Adkins,(a) (a)Pacific Northwest National Laboratory (b)Oak Ridge National Laboratory August 15, 2018 NTRD-MSR-2018-000379, PNNL-27723 Approved for public release. Distribution is unlimited. DISCLAIMER This information was prepared as an account of work sponsored by an agency of the U.S. Government. Neither the U.S. Government nor any agency thereof, nor any of their employees, makes any warranty, expressed or implied, or assumes any legal liability or responsibility for the accuracy, completeness, or usefulness, of any information, apparatus, product, or process disclosed, or represents that its use would not infringe privately owned rights. References herein to any specific commercial product, process, or service by trade name, trade mark, manufacturer, or otherwise, does not necessarily constitute or imply its endorsement, recommendation, or favoring by the U.S. Government or any agency thereof. The views and opinions of authors expressed herein do not necessarily state or reflect those of the U.S. Government or any agency thereof. Identification of Potential Waste Processing and Waste Form Options for Molten Salt Reactors iv August 15, 2018 SUMMARY The overall summary of the waste management envelope discussed in this report is represented by the diagram shown in Figure S1. The -
Lawrence Berkeley National Laboratory Recent Work
Lawrence Berkeley National Laboratory Recent Work Title THE KINETICS OF THE CHLORINATION OF UC14 BY Cl2 Permalink https://escholarship.org/uc/item/28x84687 Author Camahort, Jose Luis Publication Date 1965-05-20 eScholarship.org Powered by the California Digital Library University of California UCRL-11986 University of California Ernest 0. lawrence Radiation Laboratory THE KINETICS OF THE CHLORINATION OF UC1 BY C12 - TWO-WEEK LOAN COPY This is a library Circulating Copy which may be borrowed for two weeks. For a personal retention copy, call Tech. Info. Dioision, Ext. 5545 Berkeley, California DISCLAIMER This document was prepared as an account of work sponsored by the United States Government. While this document is believed to contain correct information, neither the United States Government nor any agency thereof, nor the Regents of the University of California, nor any of their employees, makes any warranty, express or implied, or assumes any legal responsibility for the accuracy, completeness, or usefulness of any information, apparatus, product, or process disclosed, or represents that its use would not infringe privately owned rights. Reference herein to any specific commercial product, process, or service by its trade name, trademark, manufacturer, or otherwise, does not necessarily constitute or imply its endorsement, recommendation, or favoring by the United States Government or any agency thereof, or the Regents of the University of California. The views and opinions of authors expressed herein do not necessarily state or reflect those of the United States Government or any agency thereof or the Regents of the University of California. DCl\L-llSJ36 UNIVERSITY OF CALIFORNIA Lal·rrence Radiation Laboratory Berkeley} California AEC Contract No. -
Uranium, Inorganic and Soluble Salts
Uranium, inorganic and soluble salts Evaluation of health hazards and proposal of a health based quality criteria for drinking water Environmental Project No. 1527, 2013 Title: Author: Uranium, inorganic and soluble salts Elsa Nielsen, Krestine Greve, Ole Ladefoged. Division of Toxicology and Risk Assessment. National Food Institute, Technical University of Denmark. Published by: The Danish Environmental Protection Agency Strandgade 29 1401 Copenhagen K Denmark www.mst.dk/english Year: ISBN no. Authored in 2008 978-87-93026-82-7 Published in 2013 Disclaimer: When the occasion arises, the Danish Environmental Protection Agency will publish reports and papers concerning research and development projects within the environmental sector, financed by study grants provided by the Danish Environmental Protection Agency. It should be noted that such publications do not necessarily reflect the position or opinion of the Danish Environmental Protection Agency. However, publication does indicate that, in the opinion of the Danish Environmental Protection Agency, the content represents an important contribution to the debate surrounding Danish environmental policy. Sources must be acknowledged. 2 Uranium, inorganic and soluble salts Content CONTENT 3 PREFACE 5 GENERAL DESCRIPTION 6 1.1 IDENTITY 6 1.2 PHYSICAL / CHEMICAL PROPERTIES 7 1.3 PRODUCTION AND USE 7 1.4 ENVIRONMENTAL OCCURRENCE AND FATE 8 1.4.1 Air 8 1.4.2 Water 8 1.4.3 Soil 10 1.4.4 Bioaccumulation 10 1.4.5 Foodstuffs 11 1.5 HUMAN EXPOSURE 11 2 TOXICOKINETICS 12 2.1 ABSORPTION, DISTRIBUTION -
SCIENTIFIC OPINION Uranium in Foodstuffs, in Particular Mineral Water
The EFSA Journal (2009) 1018, 1-59 SCIENTIFIC OPINION Uranium in foodstuffs, in particular mineral water1 Scientific Opinion of the Panel on Contaminants in the Food Chain (Question No EFSA-Q-2007-135) Adopted on 25 March 2009 This opinion, published on 29th May 2009, replaces the earlier version published on 28th April 20092. PANEL MEMBERS Jan Alexander, Diane Benford, Andrew Cockburn, Jean-Pierre Cravedi, Eugenia Dogliotti, Alessandro Di Domenico, María Luisa Férnandez-Cruz, Peter Fürst, Johanna Fink-Gremmels, Corrado Galli, Philippe Grandjean, Jadwiga Gzyl, Gerhard Heinemeyer, Niklas Johansson, Antonio Mutti, Josef Schlatter, Rolaf van Leeuwen, Carlos Van Peteghem, Philippe Verger. SUMMARY The European Food Safety Authority (EFSA) was asked to conduct a risk assessment on uranium at the European level because of the existence of differing regulations and also due to existing gaps in the knowledge base concerning the chronic toxicity of uranium. This opinion focuses on uranium‟s chemical toxicity, while the radiological risk will be addressed by the Group of Experts established under Article 31 of the European Atomic Energy Community (EURATOM) Treaty under the Directorate-General for Energy and Transport3. 1 For citation purposes: Scientific Opinion of the Panel on Contaminants in the Food Chain on a request from German Federal Institute for Risk Assessment (BfR) on uranium in foodstuff, in particular mineral water. The EFSA Journal (2009) 1018, 1-59. 2 After adoption of the opinion, EFSA was notified on the following two items: i) the Human Biomonitoring Commission is a commission of the German Federal Environment Agency (UBA) and not of the German Federal Institute for Risk Assessment (BfR). -
Aa-2A. at ATTORNEY
March 24, 1959 G. E. Macwood ET AL 2,879,130 PROCESS FOR RECOWERING URANIUM Filed Dec. ll, 1945 5 Sheets-Sheet 1 INVENTORS. GAOeGa f. A/40 WO22 CO/A/MAM/ A WAAA/ BY TA4//?o 4/7/M4// -aa-2a. AtATTORNEY. March 24, 1959 G. E. MACWOOD ETAL 2,879,130 PROCESS FOR RECOWERING URANIUM Filed Dec. ll, 1945 5 Sheets-Sheet 2 COWDAWSA7A scRUBBING AND WASHING 25.2% PARTS OF CALUTRON 24SA/ SOAV7/OW SOA/A /MAU/AP/7/AS MAAE UA h S E V N G --> Wa/AAR amaramates TO DSCARD CONDENSING WASA/ SOLU7/OM OR SALVAGE O X D Z N G Uttt --Uoatt SOL/A UO 2* - UO2' s /MAUAP/7/ES U(OH)4-e-UO2' FILTE R N G CUO -- Cutt navataras Cuc -- cut Cu2O -->CU Fett - - Fett TO DSCARD OR SALVAGE AARAC/A/747A C FILTER ING TO DSCARD - OR SALVAGE EVAPORATING EVAPORATING TO FURTHER TO FURTHER TREATMENT TREATMENT INVENTORS. GAOAOff A. W46 M/OOA s CO/AAW4W A). A1/AAAA A. y 2 BY Z4i/d 4/774W 4-16 at-1-ATTORNEY. March 24, 1959 G. E. MACWOOD ETAL 2,879,130 PROCESS FOR RECOVERING URANIUM Filed Dec, ll, 1945 5 Sheets-Sheet 3 DISSOLVING URANUM METAL DEPOSITED ON STANLESS STEEL COLLECTOR IN (i.) HOT SOLUTION HNO3 (12%) oR (2) SOLUTION HCI 2%8, H2O2 (0.5%) or (3)SOLUTION H2SO4 (8%)& H2O2 (0%) COWAAMSA 7A AWO MAAA UA //) A WO, or (2) AC/ & Aeole or (3)Al2SO & Ade O2 SOAV7/OAV CON DENS NG (1) At WO or (2) AC/ & Ale O2 (3) H2 SO & Aeole EVAPORATING . -
Experimental Equilibrium Data for the Uranium(IV) Thiocyanate System
Group 14 compounds and complexes 333 Table V.45: Experimental equilibrium data for the uranium(IV) thiocyanate system. t β(a) β◦(b) Method Ionic log10 q log10 q Reference Medium (◦C) U4+ +SCN− USCN3+ emf 0.6 M HClO4 20 1.49 ± 0.03 2.97 ± 0.06 [54AHR/LAR2] +0.4 MNaClO4 dis 1.00 M HClO4 10 1.78 [55DAY/WIL] (c) 1.00 M NaClO4 25 1.49 ± 0.20 2.97 ± 0.21 1.00 M NaClO4 40 1.30 ............................. 4+ − 2+ U + 2SCN U(SCN)2 emf 0.6 M HClO4 20 1.95 ± 0.17 4.20 ± 0.22 [54AHR/LAR2] +0.4 MNaClO4 dis 1.00 M HClO4 10 2.30 [55DAY/WIL] (c) 1.00 M NaClO4 25 2.11 ± 0.30 4.36 ± 0.30 1.00 M NaClO4 40 1.98 ............................. 4+ − + U + 3SCN U(SCN)3 emf 0.6 M HClO4 20 2.2 [54AHR/LAR2] +0.4 MNaClO4 β (a) log10 q refers to the equilibrium and the ionic strength given in the table. β◦ I (b) log10 q is the corresponding value corrected to = 0 at 298.15 K. (c) Uncertainty estimated by this review. H◦ q − ± · −1 ∆r m(V.176, = 1, 298.15 K) = (27 8) kJ mol H◦ q − ± · −1 ∆r m(V.176, = 2, 298.15 K) = (18 4) kJ mol These values are used to derive the enthalpies of formation of the two complexes 3+ 2+ USCN and U(SCN)2 : H◦ 3+, , . − . ± . · −1 ∆f m(USCN aq 298 15 K) = (541 8 9 5) kJ mol H◦ 2+, , . -
A Joint Photoelectron Spectroscopy and Theoretical Study on the Electronic À Structure of Ucl5 and Ucl5
FULL PAPER DOI: 10.1002/asia.201300627 A Joint Photoelectron Spectroscopy and Theoretical Study on the Electronic À Structure of UCl5 and UCl5 Jing Su,[a] Phuong Diem Dau,[b] Chao-Fei Xu,[a] Dao-Ling Huang,[b] Hong-Tao Liu,[b] Fan Wei,[c] Lai-Sheng Wang,*[b] and Jun Li*[a, d] Abstract: We report a combined photo- two unpaired electrons occupying two good agreement with the photoelectron electron spectroscopic and relativistic primarily U 5fz3 and 5fxyz based molec- spectra, providing insights into the quantum chemistry study on gaseous ular orbitals. The structures of both electronic structures and valence mo- À À À À UCl5 and UCl5. The UCl5 anion is UCl5 and UCl5 are theoretically opti- lecular orbitals of UCl5 and UCl5. We produced using electrospray ionization mized and confirmed to have C4v sym- also performed systematic theoretical and found to be highly electronically metry. The computational results are in studies on all the uranium pentahalide À stable with an adiabatic electron bind- complexes UX5 (X=F, Cl, Br, I). ing energy of 4.76Æ0.03 eV, which also Chemical bonding analyses indicate Keywords: ab initio calculations · represents the electron affinity of the that the UÀX interactions in UX À are actinides · density functional calcu- 5 neutral UCl molecule. Theoretical in- dominated by ionic bonding, with in- 5 lations · photoelectron spectrosco- vestigations reveal that the ground creasing covalent contributions for the À py · uranium state of UCl5 has an open shell with heavier halogen complexes. Introduction cies is important to understanding the actinide chemical spe- [4–7] À ciation and redox processes in molten salts. -
Aecresearchanddevelopment Report 26
". AECRESEARCHANDDEVELOPMENT REPORT 26 0R NL-3435 C-44a - Nuclear Technology - Ma !rials LABORATORY DEVELOPMENT OF A PROCESS FOR RECOVERING URANIUM FROM ROVER FUEL BY COMBUSTION, LIQUID-PHASE CHLORINATION WITH HEXACHLOROPROPENE, AND AQUEOUS EXTRACTION T. A. Gens T. B. Borne UNION CARBIDE CORPORATION for the U.S. ATOMIC ENERGY COMMISSION. ? Contract No. W- 7405- eng- 26 CHEMICAL TECHNOLOGY DIVISION Chemical Development Section B LABORATORY DEVELOPMENT OF A PROCESS FOR RECOVERING URANIUM FROM ROVER FUEL BY COMBUSTION, LIQUID-PHASE CHLORINATION WITH HEXACHLOROPROPENE, AND AQUEOUS EXTRACTION T. A. Gens T. B. Borne I Technician: E. R. Johns .d - RIDGE NATIONAL LABORATORY Oak Ridge, Tennessee 1' operated by UNION CARBIDE CORPORATION for the U. S. ATOMIC ENERGY COMMISSION P d I T . .iii CONTENTS 1. Introduction ......................... 1 2 . Flowsheet ........................... 3 2.1 Combustion ........................ 3 2.2 Chlorination and Preparation of Feed for the Solvent Extractionstep .................... 3 2.2.1 Results of Batch Solvent Extractions . 7 2.3 Major Operating Problems ................. 7 3 . Chemistry of the Chlorination Process ............. 8 4 . Laboratory Studies ...................... 9 4.1 Effect of Reflux Time and HCP-to-Ash Ratio ........ 10 4.2 Solvent Extraction .................... 14 4.3 Recycle of HCP ...................... 14 4.4 Possible Modifications in the HCP Process ........ 16 4.4.1 Separation of Uranium and Niobium by Differences in Solubility in HCP .............. 17 4.4.2 Evaporation of HCP and NbC15 with Chlorine or Argon Carrier Gas. and Aqueous Dissolution of the Residue ................... 18 4.4.3 Extraction of Chlorinated Products from HCP with Glycol ..................... 19 4.4.4 Chlorination with PC15 and POCl3 ......... 20 5 . Corrosion ........................... 21 6 .