Of Advanced Pulverized Coal Fired Power Plants …………………………………… 19
Total Page:16
File Type:pdf, Size:1020Kb
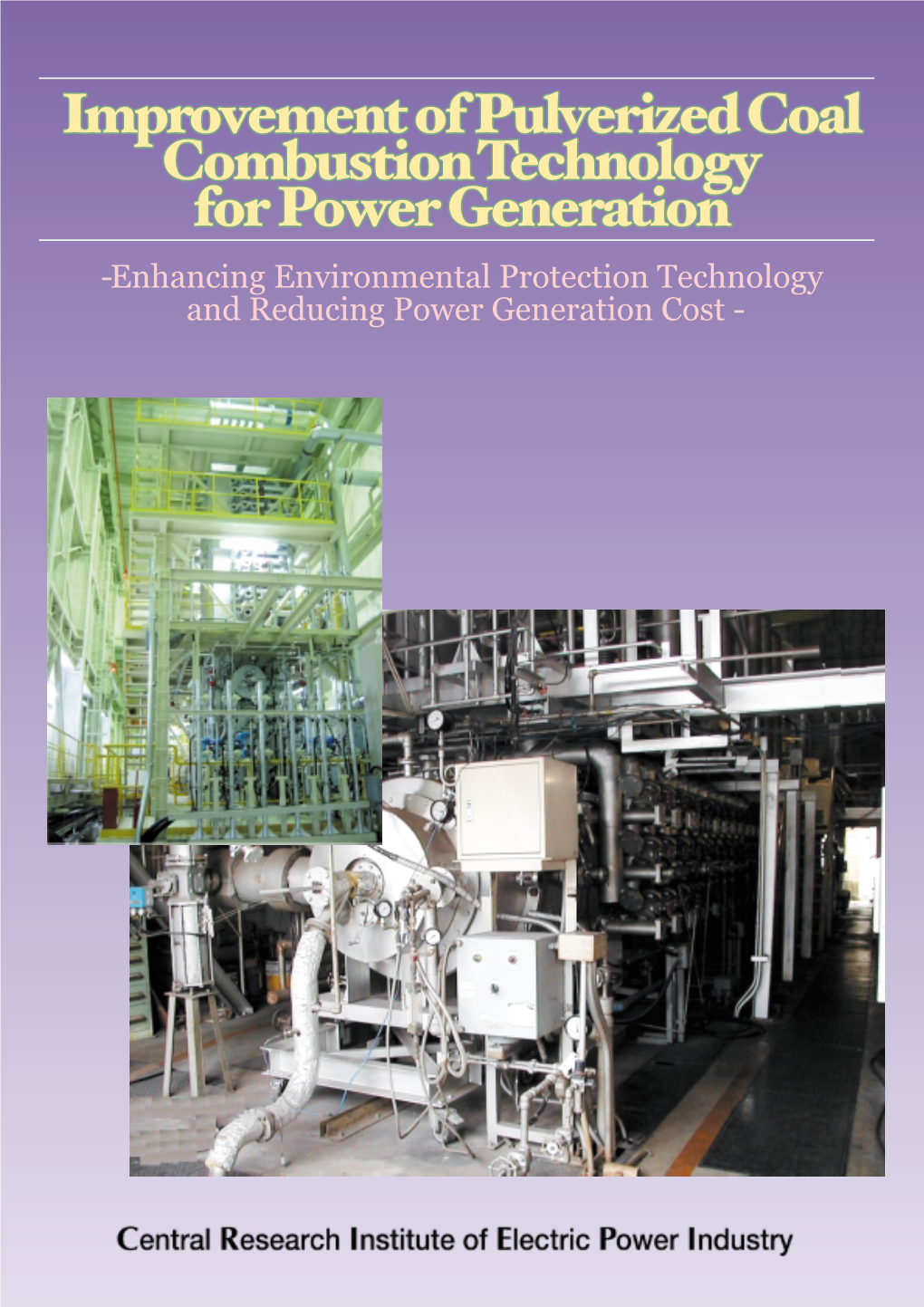
Load more
Recommended publications
-
Bullock70v.1.Pdf
CONTAINS PULLOUTS Spatial Adjustments in the Teesside Economy, 1851-81. I. Bullock. NEWCASTLE UNIVERSITY LIBRARY ---------------------------- 087 12198 3 ---------------------------- A Thesis Submitted to the University of Newcastle upon Tyne in Fulfilment of the Requirements for the Degree of PhD, Department of Geography 1970a ABSTRACT. This study is concerned with spatial change in a reg, - ional economy during a period of industrialization and rapid growth. It focuses on two main issues : the spatial pattl-rn of economic growth, and the locational adjustments induced and required by that process in individual sectors of the economy. Conceptually, therefore, the thesis belongs to the category of economic development studies, but it also makes an empirical contribution to knowledge of Teesside in a cru- cial period of the regionts history. In the first place, it was deemed necessary to estab- lish that economic growth did occur on Teesside between 1851 and 1881. To that end, use was made of a number of indirect indices of economic performance. These included population change, net migration, urbanization and changes in the empl. oyment structure of the region. It was found that these indicators provided evidence of economic growth, and evide- nce that growth was concentrated in and around existing urban centres and in those rural areas which had substantial mineral resources. To facilitate the examination of locational change in individual sectors of the economy - in mining, agriculture, manufacturing and the tertiary industries -, the actual spa- tial patterns were compared with theoretical models based on the several branches of location theory. In general, the models proved to be useful tools for furthering understand- ing of the patterns of economic activity and for predicting the types of change likely to be experienced during industr- ial revolution. -
Citywide Climate Change Strategy & Action Plan 2010
Citywide Climate Change Strategy & Action Plan 2010 - 2020 Delivering Newcastle’s Sustainable Community Strategy Foreword We realise the need for a citywide climate change strategy, one that provides a comprehensive response to the threats and opportunities that we face. We also recognise the urgent need to secure a low carbon future and prepare for a changing climate. I’m proud to say the strategy goes much further than before. It raises our ambitions and sets out how we plan to deliver against national and European commitments. At the heart of the strategy is our Sustainable Energy Action Plan that sets out a scenario to reduce our carbon emissions, and makes us confident enough to commit to our Newcastle Climate Change Declaration, adopted by the full Council in March 2010. The strategy also contains plans to adapt to the impacts of a changing climate. These will help us to seize the opportunities that a low carbon future presents, and to protect our heritage and citizens into a sustainable future. We all have a part to play, from our day-to-day actions and efforts to live in a low carbon future, to the development, delivery and uptake of physical measures to minimise our impact on the environment. This presents significant economic opportunities for our City. However, we cannot do this without understanding and preparing to live with the inevitable risks of a changing climate. Although the strategy lays the foundations for these actions, achieving our goals will not be easy. In this time of austerity we need to be bold in our choices and strong in our convictions, so that we make the decisions necessary for the future. -
Amy B. Dykstra Contact Email: [email protected]
DES Waste Management Division 29 Hazen Drive; PO Box 95 Concord, NH 03302-0095 ASTM Phase I Environmental Assessment Canaan Hydroelectric Station Stewartstown, NH NHDES Site #: 200609059 Project Number: 35945 Prepared For: Eversource Energy 780 North Commercial Street Manchester, NH 03101 Phone Number (603) 634-2851 RP Contact Name: William H. Smagula RP Contact Email: [email protected] Prepared By: Haley & Aldrich, Inc. 3 Bedford Farms Drive Bedford, NH 03110 Phone Number: (603) 625-5353 Contact Name: Amy B. Dykstra Contact Email: [email protected] Date of Report: 20 November 2015 File No. 60444-110 Cover Sheet for Reports Template - Revised January 2011 www.haleyaldrich.com REPORT ON ASTM PHASE I ENVIRONMENTAL SITE ASSESSMENT CANAAN HYDROELECTRIC STATION CANAAN, VERMONT by Haley & Aldrich, Inc. Bedford, New Hampshire for Eversource Energy Manchester, New Hampshire File No. 60444‐110 20 November 2015 HALEY & ALDRICH, INC. 3 Bedford Farms Drive Bedford, NH 03110 (603) 625.5353 20 November 2015 File No. 60444-110 Eversource Energy 780 North Commercial Street Manchester, New Hampshire 03101 Attention: Ms. Linda Landis Senior Counsel Subject: ASTM Phase I Environmental Site Assessment Canaan Hydroelectric Station Canaan, Vermont Ladies and Gentlemen: The enclosed report contains the results of a Phase I Environmental Site Assessment (Phase I) conducted at the Canaan Hydroelectric Station located at 108 Powerhouse Road in Canaan, Vermont (herein referred to as the “subject site”). This work was performed by Haley & Aldrich, Inc. (Haley & Aldrich), in accordance with our proposal to Eversource Energy dated 24 July 2015 (“Agreement”) as authorized via Purchase Order 02279342 dated 3 August 2015. -
Northeast England – a History of Flash Flooding
Northeast England – A history of flash flooding Introduction The main outcome of this review is a description of the extent of flooding during the major flash floods that have occurred over the period from the mid seventeenth century mainly from intense rainfall (many major storms with high totals but prolonged rainfall or thaw of melting snow have been omitted). This is presented as a flood chronicle with a summary description of each event. Sources of Information Descriptive information is contained in newspaper reports, diaries and further back in time, from Quarter Sessions bridge accounts and ecclesiastical records. The initial source for this study has been from Land of Singing Waters –Rivers and Great floods of Northumbria by the author of this chronology. This is supplemented by material from a card index set up during the research for Land of Singing Waters but which was not used in the book. The information in this book has in turn been taken from a variety of sources including newspaper accounts. A further search through newspaper records has been carried out using the British Newspaper Archive. This is a searchable archive with respect to key words where all occurrences of these words can be viewed. The search can be restricted by newspaper, by county, by region or for the whole of the UK. The search can also be restricted by decade, year and month. The full newspaper archive for northeast England has been searched year by year for occurrences of the words ‘flood’ and ‘thunder’. It was considered that occurrences of these words would identify any floods which might result from heavy rainfall. -
Development of a Methodology for Estimating Methane Emissions from Abandoned Coal Mines in the UK
1. Development of a Methodology for Estimating Methane Emissions from Abandoned Coal Mines in the UK thinking beyond construction 1. DEVELOPMENT OF A METHODOLOGY FOR ESTIMATING METHANE EMISSIONS FROM ABANDONED COAL MINES IN THE UK May 2005 Reference: REPORT/D5559/SK/May 2005/EMISSIONS/V3 Issue Prepared by: Verified by: Steven Kershaw Keith Whitworth V3 BSc, PhD BSc Associate Associate File Ref: I:\Projects D0000 to D9699\D5559 DEFRA IMC White Young Green Environmental Newstead Court, Little Oak Drive, Sherwood Business Park, Annesley, Nottinghamshire, NG15 0DR. Telephone: 01623 684550 Facsimile: 01623 684551 E-Mail: [email protected] Environmental Consultancy WHITE YOUNG GREEN ENVIRONMENTAL This report has been prepared for and on behalf of DEFRA in response to their particular instructions, and any duty of care to another party is excluded. Any other party using or intending to use this information for any other purpose should seek the prior written consent of IMC White Young Green Environmental. The conclusions reached are those which can reasonably be determined from sources of information, referred to in the report and from our knowledge of current professional practice and standards. Any limitations resulting from the data are identified where possible but both these and our conclusions may require amendment should additional information become available. The report is only intended for use in the stated context and should not be used otherwise. Where information has been obtained from third parties, IMC White Young Green Environmental have made all reasonable efforts to ensure that the source is reputable and where appropriate, holds acceptable quality assurance accreditation. -
In Maps and Pictures
Newcastle’s Outer West Newburn, Lemington, Bell’s Close and Sugley through the years in Maps and Pictures 1 Acknowledgments A Brief History of Newburn, Lemington, Sugley and Bell’s Close This book is published by St James’ Heritage & Environment Group but it was only possible with the help of many organisations and individuals who generously and freely contributed images, information and advice. The book was produced during the Covid pandemic which meant that the usual sources of information such as libraries and For seventy years the western border of Newcastle was marked by the navigable point of the Tyne. Here the river curved west in a meander before archives were not accessible and meetings were not allowed, so opportunities for fact-checking were limited. Any errors are ours and most of the credit must go to others. It Denton Burn which runs down from the West Road to join the Tyne at flowing east again towards the sea. It was a prime location until 1876 when is not possible to name everyone, but special thanks must go to West Newcastle Picture History Collection and Newcastle Libraries Local Studies who as usual responded Scotswood. After Scotswood and Benwell were absorbed into Newcastle major improvement works were carried out to alter the course of the river, promptly and without complaint to incessant requests for photographs from their wonderful collections. Newcastle Libraries Service also funded the printing costs of the in 1904 the new city boundary followed the line of the Dene, which had cutting a new channel to bypass the loop and creating the backwater known book. -
North East History
Jubilee North East Edition History North North East History Volume 48 East • Fifty Years of the North East Labour History Society History • Picketing, Photography and Memory: Easington 1984-85 North East History Volume 48 2017 • Jack Trevena: WEA District Secretary and Conscientious Objector • The Bagnalls of Ouseburn: Watermen, Publican, and a Sporting Hero • Trade Unionism and Methodism • Rose Lumsden, a Sunderland Nurse in the Great War • Gender and Social Transformation in the 1970s 48 2017 Community Development Projects • Commemorative Plaques and Monuments – some recent examples • Davey Hopper 1943 – 2016. A Personal Appreciation The north east labour history society holds regular meetings on a wide variety of subjects. The society welcomes new members. We have an increasingly busy web-site at www.nelh.net Supporters are welcome to contribute to discussions Journal of the North East Labour History Society Volume 48 http://nelh.net/ 2017 Journal of the North East Labour History Society north east history North East Volume 48 2017 History ISSN 14743248 © 2017 NORTHUMBERLAND Printed by Azure Printing Units 1 F & G Pegswood Industrial Estate Pegswood Morpeth TYNE & Northumberland WEAR NE61 6HZ Tel: 01670 510271 DURHAM TEESSIDE Journal of the North East Labour History Society Copyright reserved on behalf of the authors and the North East Labour History Society © 2017 www.nelh.net 1 north east history Contents Note from the Editors 5 How to submit articles 8 Notes on contributors 9 Articles: Fifty Years of the North East Labour History Society 13 Picketing, Photography and Memory: Leanne Carr 31 Easington 1984-85 Another Kind of Heroism: Jack Trevena, Kath Connolly 43 Workers’ Educational Association North and Jude Murphy East District Secretary 1914-1919 and Conscientious Objector Conscientious Objectors 1916-1956 Sue King 59 Oral History interviews with a Daughter and Widows in Newcastle The Bagnalls of Ouseburn: Watermen, Mike Greatbatch 65 Publican, and a Sporting Hero Easington Colliery: My Pathway To Politics Harry Barnes 81 Trade Unionism and Methodism. -
Newburn Manor: an Analysis of a Changing Medieval, Post-Medieval and Early Modern Landscape in Newcastle Upon Tyne
Durham E-Theses Newburn Manor: an analysis of a changing medieval, post-medieval and early modern landscape in Newcastle Upon Tyne Morrison, Jennifer How to cite: Morrison, Jennifer (2007) Newburn Manor: an analysis of a changing medieval, post-medieval and early modern landscape in Newcastle Upon Tyne, Durham theses, Durham University. Available at Durham E-Theses Online: http://etheses.dur.ac.uk/2924/ Use policy The full-text may be used and/or reproduced, and given to third parties in any format or medium, without prior permission or charge, for personal research or study, educational, or not-for-prot purposes provided that: • a full bibliographic reference is made to the original source • a link is made to the metadata record in Durham E-Theses • the full-text is not changed in any way The full-text must not be sold in any format or medium without the formal permission of the copyright holders. Please consult the full Durham E-Theses policy for further details. Academic Support Oce, Durham University, University Oce, Old Elvet, Durham DH1 3HP e-mail: [email protected] Tel: +44 0191 334 6107 http://etheses.dur.ac.uk 2 Newburn Manor - An Analysis Of A Changing Medieval, Post-Medieval And Early Modern Landscape In Newcastle Upon Tyne Volume One (of Two) Newburn Haugh on the River Tyne (copyright Newcastle City Council, City Repro. 1983) Jennifer Morrison Thesis submitted for degree of Master of Arts University of Durham Department of Archaeology 2007 1 8 APR 2008 Contents Contents Volume one Abstract 1 Declaration 2 Acknowledgements -
The Works Brass Band – a Historical Directory of the Industrial and Corporate Patronage and Sponsorship of Brass Bands
The works brass band – a historical directory of the industrial and corporate patronage and sponsorship of brass bands Gavin Holman, January 2020 Preston Corporation Tramways Band, c. 1910 From the earliest days of brass bands in the British Isles, they have been supported at various times and to differing extents by businesses and their owners. In some cases this support has been purely philanthropic, but there was usually a quid pro quo involved where the sponsor received benefits – e.g. advertising, income from band engagements, entertainment for business events, a “worthwhile” pastime for their employees, corporate public relations and brand awareness - who would have heard of John Foster’s Mills outside of the Bradford area if it wasn’t for the Black Dyke Band? One major sponsor and supporter of brass bands, particularly in the second half of the 19th century, was the British Army, through the Volunteer movement, with upwards of 500 bands being associated with the Volunteers at some time – a more accurate estimate of these numbers awaits some further analysis. However, I exclude these bands from this paper, to concentrate on the commercial bodies that supported brass bands. I am also excluding social, civic, religious, educational and political organisations’ sponsorship or support. In some cases it is difficult to determine whether a band, composed of workers from a particular company or industry was supported by the business or not. The “workmen’s band” was often a separate entity, supported by a local trade union or other organisation. For the purposes of this review I will be including them unless there is specific reference to a trade union or other social organisation. -
The Outer West the Outer West the Heritage of This Area
EXPLORING YOUR LOCAL HISTORY EXPLORING YOUR LOCAL HISTORY EXPLORINGA HeritageA HeritageYOUR Guide LOCAL Guide HISTORY EXPLORING YOUR LOCAL HISTORY A Heritage Guide A Heritage Guide EXPLORINGEXPLORING YOUR YOUR LOCAL LOCAL HISTORY HISTORY This heritage guide is an introduction to the history of Newcastle’s This heritage guide is an introduction to the history of Newcastle’s EXPLORING YOUR LOCAL HISTORY outer west villagesThis heritage of Newburn, guide is an Lemington, introduction Sugley to the andhistory Bell’s of Newcastle’s EXPLORING YOUR LOCAL HISTORY outer westThis heritage villages guide of Newburn, is an introduction Lemington, to theSugley history and of Bell’s Newcastle’s outer west villages of Newburn, Lemington, Sugley and Bell’s Close. It includesClose. outer It three includes west illustrated villages three illustratedof walkNewburn, trails walk Lemington, offering trails offering insights Sugley insightsand into Bell’s into Close. It includes three illustrated walk trails offering insights into the heritagethe of heritage thisClose. area. Itof includes this area. three illustrated walk trails offering insights into The Outer West The Outer West the heritage of this area. EXPLORING YOUR LOCAL HISTORY the heritage of this area. When this area became part of the City of Newcastle in 1974, it TheThe OuterOuter WestWest When this area became part of the City of Newcastle in 1974, it When this area became part of the City of Newcastle in 1974, it NEWBURNNEWBURN LEMINGTON LEMINGTON SUGLEY SUGLEY brought withbrought it aWhen long with this and it a area longfascinating became and fascinating part history. of the history. ItsCity strategic of Newcastle Its strategic in 1974, it NEWBURN LEMINGTON SUGLEY brought with it a long and fascinating history. -
4Es L3Q3 'It Is Questionable If All the Mechanical Inventions Yet Made Have Lightened the Day's Toil of Any Human Being'
University of Newcastle upon Tyne TECHNICAL CHANGE AND THE TRANSFORMATION OF WORK: THE CASE OF THE BRITISH COAL INDUSTRY John Tomaney Submitted In fulfilment of the requirements of the Degree of Doctor of Philosophy Centre for Urban and Regional Development Studies Department of Geography University of Newcastle upon Tyne Newcastle upon Tyne 1991 1.j\l •t. 1 I........ iF I:; t :?j. :L•Ii X 4es L3Q3 'It is questionable if all the mechanical inventions yet made have lightened the day's toil of any human being' - John Stuart Mill, Principles of Political Economy, 1888. 'What', asked the French lecturer on the Science of Metals and Mining, 'is the most important thing to come out of a coal-mine?' 'Coal', replied the students. 'No', said the lecturer, Frederic Le Play, 'the most important thing is the coal-miner'. - F.D. Gould 'Le Play', Sociological Review, (1927) 1 ABSTRACT This thesis examines the suggestion that dramatic changes are occurring in the organisation of work and production, and that these amount to the emergence of a new 'post-Fordist' industrial paradigm. In particular, the claim that introduction of new forms of microelectronic-based technologies is leading to the emergence of new forms of skilled work, and that, as a result, old forms of industrial conflict are ameliorated, is analysed. The value of this conceptualisation of contemporary workplace change is questioned. A critique of the 'post-Fordist' argument is offered. This stresses: that new tendencies in the organisation of work can be discerned but that generally these are occurring alongside enduring forms of hierarchy and control; that the new forms of work and production represent a reformulation of traditional capitalist concerns of efficiency and control through the extension of 'flow principles'; and that the pattern of change in reality is highly uneven and spatially differentiated. -
EWEA OFFSHORE 2013 Exhibitor List - Alphabetic Order, Sorted by Company Name Company Name Address 1 Address 2 Address 3 Postcode City Country Description Website
EWEA OFFSHORE 2013 exhibitor list - alphabetic order, sorted by company name company_name address 1 address 2 address 3 postcode city country description website Being properly informed with the best advice and information is mission critical to you and your business. 4C Offshore provides market intelligence and technical advice to a wide range of global clients in the energy markets, notably offshore wind and subsea power cables. A leading 4C Offshore Limited Orbis Energy Centre, Wilde Street NR32 1XH Lowestoft UK advisory to submarine grid owners. www.4coffshore.com The 8.2 Consulting AG offers a wide range of technical services and consulting regarding offshore wind. Relying on the best experts in wind energy and decades of experience, 8.2 is your reliable partner in rough times. Amongst others, our services include technical consulting, due diligence, manufacturing control and periodic 8.2 Consulting AG Brandstwiete 4 D-20457 Hamburg Germany inspections. www.8p2.de A2SEA – powered by know-how. A2SEA offers integrated installation and service solutions for the offshore wind industry. Since 2002, our fleet has installed more than 1000 turbines and 400 foundations. Powered by know- how and experience, our project teams complete every A2SEA A/S Kongens Kvarter 51 DK-7000 Fredericia Denmark installation safely, on time, and to budget. www.a2sea.com/ Aarsleff is a leading Danish contracting company. Our expertise is to devise, plan and implement large-scale projects within infrastructure, climate adaptation, the environment, energy etc. – from design to handing-over. Our point of departure is a strong position in Denmark and Aarsleff Lokesvej 15 DK-8230 Aabyhoej Denmark the Baltic Sea region, and we solve projects worldwide.