Life Cycle Inventory
Total Page:16
File Type:pdf, Size:1020Kb
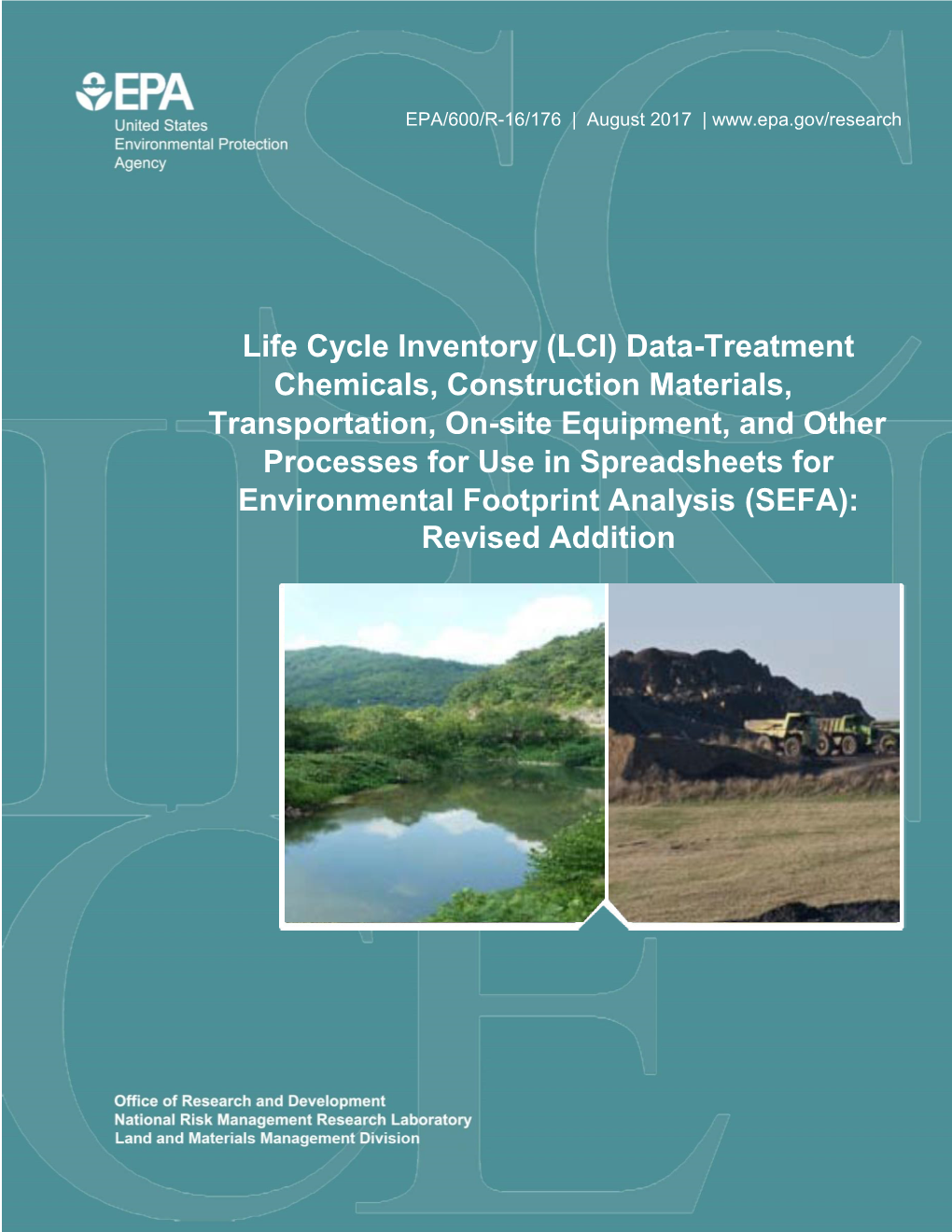
Load more
Recommended publications
-
Chemical Hygiene Plan Manual
CHEMICAL HYGIENE PLAN AND HAZARDOUS MATERIALS SAFETY MANUAL FOR LABORATORIES This is the Chemical Hygiene Plan specific to the following areas: Laboratory name or room number(s): ___________________________________ Building: __________________________________________________________ Supervisor: _______________________________________________________ Department: _______________________________________________________ Telephone numbers 911 for Emergency and urgent consultation 48221 Police business line 46919 Fire Dept business line 46371 Radiological and Environmental Management Revisied on: Enter a revision date here. All laboratory chemical use areas must maintain a work-area specific Chemical Hygiene Plan which conforms to the requirements of the OSHA Laboraotry Standard 29 CFR 19190.1450. Purdue University laboratories may use this document as a starting point for creating their work area specific CHP. Minimally this cover page is to be edited for work area specificity (non-West Lafayette laboratories are to place their own emergency, fire, and police telephone numbers in the space above) AND appendix K must be completed. This instruction and information box should remain. This model CHP is version 2010A; updates are to be found at www.purdue.edu/rem This page intentionally blank. PURDUE CHEMICAL HYGIENE PLAN AWARENESS CERTIFICATION For CHP of: ______________________________ Professor, building, rooms The Occupational Safety and Health Administration (OSHA) requires that laboratory employees be made aware of the Chemical Hygiene Plan at their place of employment (29 CFR 1910.1450). The Purdue University Chemical Hygiene Plan and Hazardous Materials Safety Manual serves as the written Chemical Hygiene Plan (CHP) for laboratories using chemicals at Purdue University. The CHP is a regular, continuing effort, not a standby or short term activity. Departments, divisions, sections, or other work units engaged in laboratory work whose hazards are not sufficiently covered in this written manual must customize it by adding their own sections as appropriate (e.g. -
Use of Bismuth Compounds for the Manufacture of Medicaments for The
Europäisches Patentamt *EP000805815B1* (19) European Patent Office Office européen des brevets (11) EP 0 805 815 B1 (12) EUROPEAN PATENT SPECIFICATION (45) Date of publication and mention (51) Int Cl.7: A61K 33/24, C07F 9/94, of the grant of the patent: A61K 49/04 10.04.2002 Bulletin 2002/15 (86) International application number: (21) Application number: 96901066.9 PCT/GB96/00183 (22) Date of filing: 26.01.1996 (87) International publication number: WO 96/22994 (01.08.1996 Gazette 1996/35) (54) Use of bismuth compounds for the manufacture of medicaments for the treatment of gastric disorders caused by Helicobacter pylori Verwendung von WISMUTVERBINDUNGEN zur Herstellung eines Arzneimittels zur Behandlung von Magenverstimmungen, die durch Helicobacter pylori verursacht werden Utilisation de COMPOSES DE BISMUTH pour la fabrication de médicaments pour le traitement de troubles gastriques associées avec Helicobacter pylori (84) Designated Contracting States: EP-A- 0 480 691 EP-A- 0 716 091 DE DK ES FR GB IE IT SE WO-A-91/03241 WO-A-93/02713 WO-A-95/06053 WO-A-96/16677 (30) Priority: 26.01.1995 GB 9501560 WO-A-96/16678 BE-A- 782 105 07.06.1995 US 486225 DE-A- 2 216 725 (43) Date of publication of application: • TETRAHEDRON LETT. (TELEAY,00404039);94; 12.11.1997 Bulletin 1997/46 VOL.35 (44); PP.8197-200, KYOTO UNIV.;FAC. SCI.; KYOTO; 606-01; JAPAN (JP), SUZUKI H ET (73) Proprietor: NYCOMED IMAGING A/S AL ’Ultrasonic reaction of triarylbismuthines 0401 Oslo (NO) and triarylstibines with iodosylbenzene. Mild oxidizing ability of the organobismuth oxide (72) Inventors: function for organic substrates’ • KLAVENESS, Jo • DATABASE CHEMABS CHEMICAL ABSTRACTS N-1166 Oslo (NO) SERVICE, COLUMBUS, OHIO, US ASTHANA A • BERG, Arne ’Reactions of triphenyl antimony, bismuth and N-1300 Sandvika (NO) their dibromides with pentachlorophenol and • ALMEN, Torsten pentachlorothiophenol’ & INDIAN J. -
Hydrite General Product Flyer
PRODUCT OFFERING forms, trade names and a variety of certifi cations. Please call us about your specifi c chemical requirements. PRODUCTS A-Z Acetic Acid Calcium Chloride Calcium Dioctyl Phthalate Glycol Ether DPM Reduction Chemicals Acetone Hydroxide (Lime) Calcium Dipotassium Phosphate Glycol Ether EB Liquid Inorganic Salts Aluminum Brite Dips Hypochlorite Calcium (DKP) Glycol Ether EE Magnesium Bisulfi te Aluminum Chlorhydrate Phosphates Dipropylene Glycol Glycol Ether EE-AC Magnesium Chloride Aluminum Sulfate (Alum) Carboxymethyl Cellulose Disodium Phosphate Glycol Ether EM Magnesium Hydroxide Ammonium Bicarbonate Caustic Potash Dodecylbenzenesulfonic Glycol Ether EP Magnesium Oxide Ammonium Bifl uor ide Caustic Soda Acid (DDBSA) Glycol Ether PM Magnesium Phosphate Ammonium Bisulfi te Chelants Dye Fixatives Glycol Ether PM-AC Magnesium Sulfate Ammonium Chloride Chlorine Epoxy Resins HAN, Heavy Aromatic Magnesium Sulfi te Ammonium Hydroxide Chromic Acid Ethyl Acetate Naphtha Metal Finishing Products (Aqua Ammonia) Citric Acid Ethyl Alcohol Heat Transfer Fluids Methanol Ammonium Persulfate Copper Carbonate Ethylene Diamine Tetra Heptane Methyl Amyl Ketone Ammonium Phosphates Copper Cyanide Acetic Acid (EDTA) Hexane Methyl Ethyl Ketone Ammonium Sulfate Copper Sulfate Ethylene Dichloride Hexylene Glycol Methyl Isobutyl Ketone Ammonium Sulfi te Cyclohexane Ethylene Glycol HTH Methylene Chloride Mineral Anhydrous Ammonia Cyclohexanone Felt & Wire Cleaners Hydrochloric Acid Fillers Anodizing Chemicals Dairy Cleaners Ferric Chloride Hydrofluoric Acid -
United States Patent (19) ’11) 4,095,037 Stapp 45) June 13, 1978
United States Patent (19) ’11) 4,095,037 Stapp 45) June 13, 1978 54 METHOD FOR THE oxIDATION OF A 56) References Cited CONJUGATED DOLEFN U.S. PATENT DOCUMENTS 3,238,225 3/1966 Brill................................ 260/346.1 (75) Inventor: Paul R. Stapp, Bartlesville, Okla. 3,432,558 3/1969 Ryland ................................. 260/604 3,670,014 6/1972 Fernholz .......................... 260/497 A 73 Assignee: Phillips Petroleum Company, 3,755,423 8/1973 Onoda .............................. 260/497 A. Bartlesville, Okla. 3,922,300 11/1975 Onoda .............................. 260/497. A Primary Examiner-James O. Thomas, Jr. 21 Appl. No.: 721,645 Assistant Examiner-Michael Shippen 22 Filed: Sep. 8, 1976 57 ABSTRACT A conjugated diolefin is reacted with a carboxylic acid, (51) Int, C.’......................... CO7C 67/05; B01J 23/16 a carboxylic acid anhydride, or a mixture thereof, in the (52) U.S.C. .................................... 560/246; 260/410; presence of oxygen and a catalyst comprising a com 260/410.6; 260/465.4; 560/1; 560/106; pound of bismuth, an alkali metal compound and a 560/112; 560/122; 560/228; 560/230; 252/438 source of nitrate ion. 58 Field of Search ........... 260/497 R, 497 A, 476 R, 260/410, 40.6, 465.4, 468 R, 487 11 Claims, No Drawings 4,095,037 1. METHOD FOR THE OXDATION OF A . R. R. R. 1) CONJUGATED DOLEFN C-CEC as R. BACKGROUND OF THE INVENTION The invention relates to a method suitable for the In said formula (1), R- is selected from the group oxidation of a conjugated diolefin. In another aspect, consisting of H-, F-, CL-, Br-, -, -CsN, the invention relates to a composition useful as a cata lyst. -
Toxicological Profile for Beryllium
BERYLLIUM 19 3. HEALTH EFFECTS 3.1 INTRODUCTION The primary purpose of this chapter is to provide public health officials, physicians, toxicologists, and other interested individuals and groups with an overall perspective on the toxicology of beryllium. It contains descriptions and evaluations of toxicological studies and epidemiological investigations and provides conclusions, where possible, on the relevance of toxicity and toxicokinetic data to public health. A glossary and list of acronyms, abbreviations, and symbols can be found at the end of this profile. 3.2 DISCUSSION OF HEALTH EFFECTS BY ROUTE OF EXPOSURE To help public health professionals and others address the needs of persons living or working near hazardous waste sites, the information in this section is organized first by route of exposure (inhalation, oral, and dermal) and then by health effect (death, systemic, immunological, neurological, reproductive, developmental, genotoxic, and carcinogenic effects). These data are discussed in terms of three exposure periods: acute (14 days or less), intermediate (15–364 days), and chronic (365 days or more). Levels of significant exposure for each route and duration are presented in tables and illustrated in figures. The points in the figures showing no-observed-adverse-effect levels (NOAELs) or lowest-observed-adverse-effect levels (LOAELs) reflect the actual doses (levels of exposure) used in the studies. LOAELS have been classified into "less serious" or "serious" effects. "Serious" effects are those that evoke failure in a biological system and can lead to morbidity or mortality (e.g., acute respiratory distress or death). "Less serious" effects are those that are not expected to cause significant dysfunction or death, or those whose significance to the organism is not entirely clear. -
Alphabetical Index of Substances and Articles
ALPHABETICAL INDEX OF SUBSTANCES AND ARTICLES - 355 - NOTES TO THE INDEX 1. This index is an alphabetical list of the substances and articles which are listed in numerical order in the Dangerous Goods List in Chapter 3.2. 2. For the purpose of determining the alphabetical order the following information has been ignored even when it forms part of the proper shipping name: numbers; Greek letters; the abbreviations “sec” and “tert”; and the letters “N” (nitrogen), “n” (normal), “o” (ortho) “m” (meta), “p” (para) and “N.O.S.” (not otherwise specified). 3. The name of a substance or article in block capital letters indicates a proper shipping name. 4. The name of a substance or article in block capital letters followed by the word “see” indicates an alternative proper shipping name or part of a proper shipping name (except for PCBs). 5. An entry in lower case letters followed by the word “see” indicates that the entry is not a proper shipping name; it is a synonym. 6. Where an entry is partly in block capital letters and partly in lower case letters, the latter part is considered not to be part of the proper shipping name. 7. A proper shipping name may be used in the singular or plural, as appropriate, for the purposes of documentation and package marking. - 356 - INDEX Name and description Class UN No. Name and description Class UN No. Accumulators, electric, see 4.3 3292 Acid mixture, nitrating acid, see 8 1796 8 2794 8 2795 Acid mixture, spent, nitrating acid, see 8 1826 8 2800 8 3028 Acraldehyde, inhibited, see 6.1 1092 ACETAL 3 1088 -
Hexafluorosilicic Acid
Sodium Hexafluorosilicate [CASRN 16893-85-9] and Fluorosilicic Acid [CASRN 16961-83-4] Review of Toxicological Literature October 2001 Sodium Hexafluorosilicate [CASRN 16893-85-9] and Fluorosilicic Acid [CASRN 16961-83-4] Review of Toxicological Literature Prepared for Scott Masten, Ph.D. National Institute of Environmental Health Sciences P.O. Box 12233 Research Triangle Park, North Carolina 27709 Contract No. N01-ES-65402 Submitted by Karen E. Haneke, M.S. (Principal Investigator) Bonnie L. Carson, M.S. (Co-Principal Investigator) Integrated Laboratory Systems P.O. Box 13501 Research Triangle Park, North Carolina 27709 October 2001 Toxicological Summary for Sodium Hexafluorosilicate [16893-85-9] and Fluorosilicic Acid [16961-83-4] 10/01 Executive Summary Nomination Sodium hexafluorosilicate and fluorosilicic acid were nominated for toxicological testing based on their widespread use in water fluoridation and concerns that if they are not completely dissociated to silica and fluoride in water that persons drinking fluoridated water may be exposed to compounds that have not been thoroughly tested for toxicity. Nontoxicological Data Analysis and Physical-Chemical Properties Analytical methods for sodium hexafluorosilicate include the lead chlorofluoride method (for total fluorine) and an ion-specific electrode procedure. The percentage of fluorosilicic acid content for water supply service application can be determined by the specific-gravity method and the hydrogen titration method. The American Water Works Association (AWWA) has specified that fluorosilicic acid contain 20 to 30% active ingredient, a maximum of 1% hydrofluoric acid, a maximum of 200 mg/kg heavy metals (as lead), and no amounts of soluble mineral or organic substance capable of causing health effects. -
Fluoride Inhibitor (BS1077-B) Ghsunitedstatessds En 2021-02-01
Page: 1/9 Safety Data Sheet according to OSHA HCS (29CFR 1910.1200) and WHMIS 2015 Regulations Revision: January 27, 2021 1 Identification · Product identifier · Trade name: Fluoride Inhibitor · Product code: BS1077-B · Recommended use and restriction on use · Recommended use: Laboratory chemicals · Restrictions on use: No relevant information available. · Details of the supplier of the Safety Data Sheet · Manufacturer/Supplier: AquaPhoenix Scientific, Inc. 860 Gitts Run Road Hanover, PA 17331 USA Tel +1 (717)632-1291 Toll-Free: (866)632-1291 [email protected] · Distributor: AquaPhoenix Scientific 860 Gitts Run Road, Hanover, PA 17331 (717) 632-1291 · Emergency telephone number: ChemTel Inc. (800)255-3924 (North America) +1 (813)248-0585 (International) 2 Hazard(s) identification · Classification of the substance or mixture Skin Sens. 1 H317 May cause an allergic skin reaction. Carc. 1B H350 May cause cancer. STOT RE 1 H372 Causes damage to organs through prolonged or repeated exposure. · Label elements · GHS label elements The product is classified and labeled according to the Globally Harmonized System (GHS). · Hazard pictograms: GHS07 GHS08 · Signal word: Danger · Hazard statements: H317 May cause an allergic skin reaction. H350 May cause cancer. H372 Causes damage to organs through prolonged or repeated exposure. · Precautionary statements: P201 Obtain special instructions before use. P202 Do not handle until all safety precautions have been read and understood. (Cont'd. on page 2) 50.1.3 Page: 2/9 Safety Data Sheet according to OSHA HCS (29CFR 1910.1200) and WHMIS 2015 Regulations Revision: January 27, 2021 Trade name: Fluoride Inhibitor (Cont'd. of page 1) P260 Do not breathe dust/fume/gas/mist/vapors/spray. -
United States Patent (19) 11 Patent Number: 6,117,412 Klaveness Et Al
USOO6117412A United States Patent (19) 11 Patent Number: 6,117,412 Klaveness et al. (45) Date of Patent: *Sep. 12, 2000 54) NON-CLUSTER TYPE BISMUTH 5,417,958 5/1995 Deutsch et al. ........................ 424/9.42 COMPOUNDS 5,482,669 1/1996 Shah. 5,482,700 1/1996 Deutsch et al.. 75 Inventors: Jo Klaveness, Oslo; Ame Berg, 5,730,953 3/1998 Suzuki et al. .......................... 424/9.42 Sandvika, both of Norway; Torsten 5,817,289 10/1998 Klaveness et al. .................... 424/1.11 Almen, Falstorbo, Sweden; Klaes FOREIGN PATENT DOCUMENTS Golman, Rungsted Kyst, Denmark; 809388 5/1974 Belgium. Michael Droege, Livermore; Shi-bao O O217 577 Yu, Campbell, both of Calif. A2 9/1986 European Pat. Off.. O 230 893 A2 1/1987 European Pat. Off.. 73 Assignee: Nycomed Imaging AS, Norway O 445 743 A2 9/1991 European Pat. Off.. 0 480 691 A2 4/1992 European Pat. Off.. * Notice: This patent is Subject to a terminal dis O OS33 281 claimer. A1 9/1992 European Pat. Off.. 0 716 091 A1 8/1994 European Pat. Off.. 21 Appl. No.: 08/875,305 2216725 10/1973 Germany. 63-225381 9/1988 Japan. 22 PCT Filed: Jan. 26, 1996 81/7456 4/1983 South Africa. 86 PCT No.: PCT/GB9600183 1003685 9/1965 United Kingdom. 1341331 12/1973 United Kingdom. S371 Date: Oct. 22, 1997 2 248 185 1/1992 United Kingdom. 2 262 036 6/1993 United Kingdom. S 102(e) Date: Oct. 22, 1997 WO 89/00557 1/1989 WIPO. WO 89/03219 4/1989 WIPO. -
WO 2016/074683 Al 19 May 2016 (19.05.2016) W P O P C T
(12) INTERNATIONAL APPLICATION PUBLISHED UNDER THE PATENT COOPERATION TREATY (PCT) (19) World Intellectual Property Organization International Bureau (10) International Publication Number (43) International Publication Date WO 2016/074683 Al 19 May 2016 (19.05.2016) W P O P C T (51) International Patent Classification: (81) Designated States (unless otherwise indicated, for every C12N 15/10 (2006.01) kind of national protection available): AE, AG, AL, AM, AO, AT, AU, AZ, BA, BB, BG, BH, BN, BR, BW, BY, (21) International Application Number: BZ, CA, CH, CL, CN, CO, CR, CU, CZ, DE, DK, DM, PCT/DK20 15/050343 DO, DZ, EC, EE, EG, ES, FI, GB, GD, GE, GH, GM, GT, (22) International Filing Date: HN, HR, HU, ID, IL, IN, IR, IS, JP, KE, KG, KN, KP, KR, 11 November 2015 ( 11. 1 1.2015) KZ, LA, LC, LK, LR, LS, LU, LY, MA, MD, ME, MG, MK, MN, MW, MX, MY, MZ, NA, NG, NI, NO, NZ, OM, (25) Filing Language: English PA, PE, PG, PH, PL, PT, QA, RO, RS, RU, RW, SA, SC, (26) Publication Language: English SD, SE, SG, SK, SL, SM, ST, SV, SY, TH, TJ, TM, TN, TR, TT, TZ, UA, UG, US, UZ, VC, VN, ZA, ZM, ZW. (30) Priority Data: PA 2014 00655 11 November 2014 ( 11. 1 1.2014) DK (84) Designated States (unless otherwise indicated, for every 62/077,933 11 November 2014 ( 11. 11.2014) US kind of regional protection available): ARIPO (BW, GH, 62/202,3 18 7 August 2015 (07.08.2015) US GM, KE, LR, LS, MW, MZ, NA, RW, SD, SL, ST, SZ, TZ, UG, ZM, ZW), Eurasian (AM, AZ, BY, KG, KZ, RU, (71) Applicant: LUNDORF PEDERSEN MATERIALS APS TJ, TM), European (AL, AT, BE, BG, CH, CY, CZ, DE, [DK/DK]; Nordvej 16 B, Himmelev, DK-4000 Roskilde DK, EE, ES, FI, FR, GB, GR, HR, HU, IE, IS, IT, LT, LU, (DK). -
Economic Commission for Europe Inland Transport
ECONOMIC COMMISSION FOR EUROPE INLAND TRANSPORT COMMITTEE INF.6 Working Party on the Transport of Dangerous Goods Joint Meeting of the RID Safety Committee and the Working Party on the Transport of Dangerous Goods (Geneva, 1-10 September 2003) Harmonization with the UN Recommendations on the Transport of Dangerous Goods Bulk containers Transmitted by the Government of the United Kingdom 1. Introduction New provisions for bulk containers from the UN Model Regulations are being proposed for inclusion in RID/ADR based on text prepared by the UN Secretariat and as discussed at the ad hoc Working Group on the Harmonization of RID/ADR/ADN with the UN Recommendations on the Transport of Dangerous Goods that met from 26-28 May 2003. The results of the discussions on this subject are recorded in paragraphs 39 to 46 of the report of the ad hoc Working Group TRANS/WP.15/AC.1/2003/56 and the proposed text for inclusion in RID/ADR in the relevant parts of Addendum 1 to 7 of 2003/56, in particular a new chapter 6.11 and a modified chapter 7.3. 2. Proposal and Justification A new chapter 6.11, reflecting UN chapter 6.8, is contained in 2003/56 Add 6 dealing with the requirements for the design, construction, inspection and testing of bulk containers and new UN chapter 4.3 dealing with the use of bulk containers has been integrated into a modified chapter 7.3 contained in 2003/56 Add 7. Now that there are comprehensive provisions for bulk containers developed at UN level, the UK believes as reflected in paragraph 43 of 2003/56, that these should now apply to carriage in bulk in RID/ADR rather than have two separate systems based on the provisions for bulk containers in UN and the existing provisions in RID/ADR. -
Standard Thermodynamic Properties of Chemical
STANDARD THERMODYNAMIC PROPERTIES OF CHEMICAL SUBSTANCES ∆ ° –1 ∆ ° –1 ° –1 –1 –1 –1 Molecular fH /kJ mol fG /kJ mol S /J mol K Cp/J mol K formula Name Crys. Liq. Gas Crys. Liq. Gas Crys. Liq. Gas Crys. Liq. Gas Ac Actinium 0.0 406.0 366.0 56.5 188.1 27.2 20.8 Ag Silver 0.0 284.9 246.0 42.6 173.0 25.4 20.8 AgBr Silver(I) bromide -100.4 -96.9 107.1 52.4 AgBrO3 Silver(I) bromate -10.5 71.3 151.9 AgCl Silver(I) chloride -127.0 -109.8 96.3 50.8 AgClO3 Silver(I) chlorate -30.3 64.5 142.0 AgClO4 Silver(I) perchlorate -31.1 AgF Silver(I) fluoride -204.6 AgF2 Silver(II) fluoride -360.0 AgI Silver(I) iodide -61.8 -66.2 115.5 56.8 AgIO3 Silver(I) iodate -171.1 -93.7 149.4 102.9 AgNO3 Silver(I) nitrate -124.4 -33.4 140.9 93.1 Ag2 Disilver 410.0 358.8 257.1 37.0 Ag2CrO4 Silver(I) chromate -731.7 -641.8 217.6 142.3 Ag2O Silver(I) oxide -31.1 -11.2 121.3 65.9 Ag2O2 Silver(II) oxide -24.3 27.6 117.0 88.0 Ag2O3 Silver(III) oxide 33.9 121.4 100.0 Ag2O4S Silver(I) sulfate -715.9 -618.4 200.4 131.4 Ag2S Silver(I) sulfide (argentite) -32.6 -40.7 144.0 76.5 Al Aluminum 0.0 330.0 289.4 28.3 164.6 24.4 21.4 AlB3H12 Aluminum borohydride -16.3 13.0 145.0 147.0 289.1 379.2 194.6 AlBr Aluminum monobromide -4.0 -42.0 239.5 35.6 AlBr3 Aluminum tribromide -527.2 -425.1 180.2 100.6 AlCl Aluminum monochloride -47.7 -74.1 228.1 35.0 AlCl2 Aluminum dichloride -331.0 AlCl3 Aluminum trichloride -704.2 -583.2 -628.8 109.3 91.1 AlF Aluminum monofluoride -258.2 -283.7 215.0 31.9 AlF3 Aluminum trifluoride -1510.4 -1204.6 -1431.1 -1188.2 66.5 277.1 75.1 62.6 AlF4Na Sodium tetrafluoroaluminate