Grayscale-To-Color: Single-Step Fabrication of Bespoke Multispectral Filter Arrays
Total Page:16
File Type:pdf, Size:1020Kb
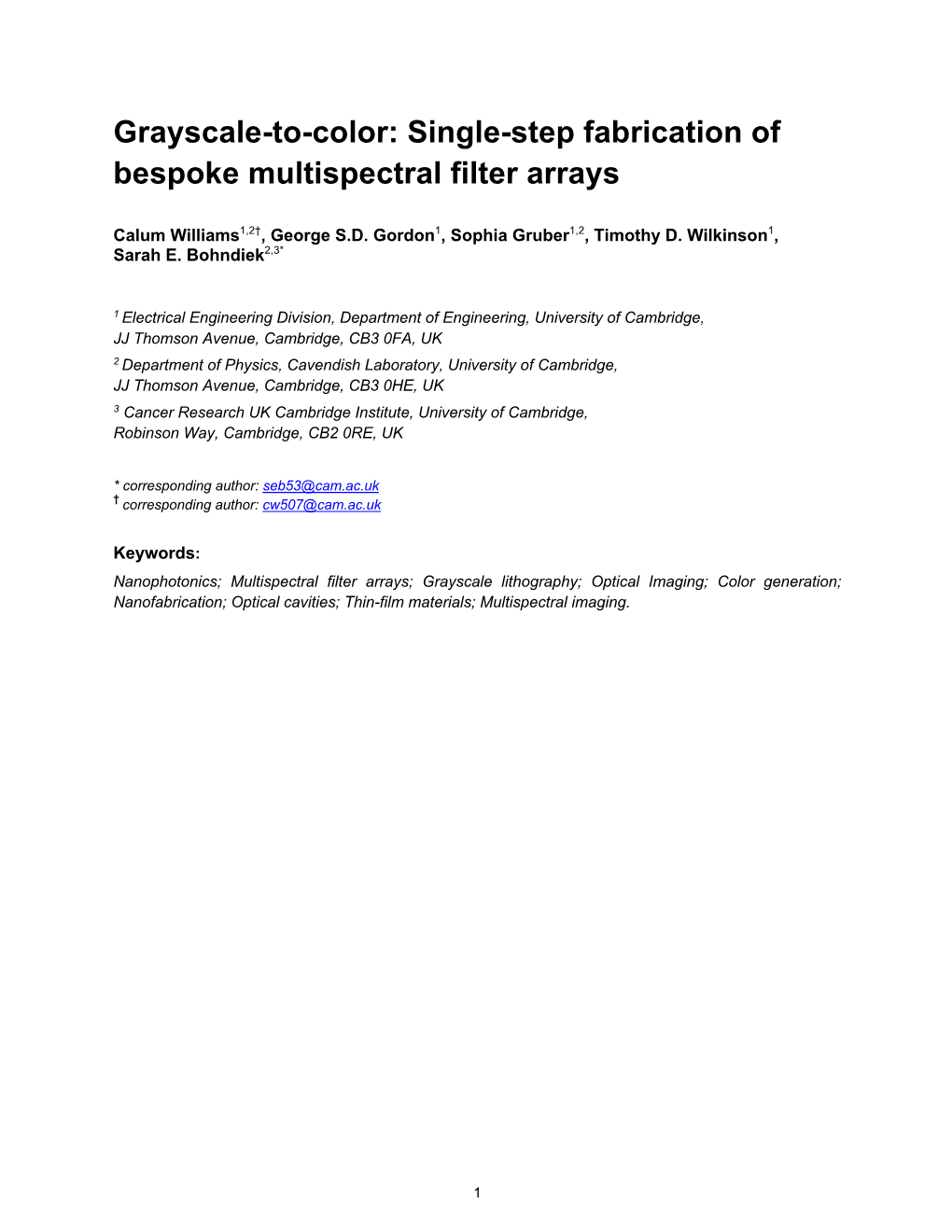
Load more
Recommended publications
-
Advanced Color Machine Vision and Applications Dr
Advanced Color Machine Vision and Applications Dr. Romik Chatterjee V.P. Business Development Graftek Imaging 2016 V04 - for tutorial 5/4/2016 Outline • What is color vision? Why is it useful? • Comparing human and machine color vision • Physics of color imaging • A model of color image formation • Human color vision and measurement • Color machine vision systems • Basic color machine vision algorithms • Advanced algorithms & applications • Human vision Machine Vision • Case study Important terms What is Color? • Our perception of wavelengths of light . Photometric (neural computed) measures . About 360 nm to 780 nm (indigo to deep red) . “…the rays are not coloured…” - Isaac Newton • Machine vision (MV) measures energy at different wavelengths (Radiometric) nm : nanometer = 1 billionth of a meter Color Image • Color image values, Pi, are a function of: . Illumination spectrum, E(λ) (lighting) λ = Wavelength . Object’s spectral reflectance, R(λ) (object “color”) . Sensor responses, Si(λ) (observer, viewer, camera) . Processing • Human <~> MV . Eye <~> Camera . Brain <~> Processor Color Vision Estimates Object Color • The formation color image values, Pi, has too many unknowns (E(λ) = lighting spectrum, etc.) to directly estimate object color. • Hard to “factor out” these unknowns to get an estimate of object color . In machine vision, we often don’t bother to! • Use knowledge, constraints, and computation to solve for object color estimates . Not perfect, but usually works… • If color vision is so hard, why use it? Material Property • -
Invention of Digital Photograph
Invention of Digital photograph Digital photography uses cameras containing arrays of electronic photodetectors to capture images focused by a lens, as opposed to an exposure on photographic film. The captured images are digitized and stored as a computer file ready for further digital processing, viewing, electronic publishing, or digital printing. Until the advent of such technology, photographs were made by exposing light sensitive photographic film and paper, which was processed in liquid chemical solutions to develop and stabilize the image. Digital photographs are typically created solely by computer-based photoelectric and mechanical techniques, without wet bath chemical processing. The first consumer digital cameras were marketed in the late 1990s.[1] Professionals gravitated to digital slowly, and were won over when their professional work required using digital files to fulfill the demands of employers and/or clients, for faster turn- around than conventional methods would allow.[2] Starting around 2000, digital cameras were incorporated in cell phones and in the following years, cell phone cameras became widespread, particularly due to their connectivity to social media websites and email. Since 2010, the digital point-and-shoot and DSLR formats have also seen competition from the mirrorless digital camera format, which typically provides better image quality than the point-and-shoot or cell phone formats but comes in a smaller size and shape than the typical DSLR. Many mirrorless cameras accept interchangeable lenses and have advanced features through an electronic viewfinder, which replaces the through-the-lens finder image of the SLR format. While digital photography has only relatively recently become mainstream, the late 20th century saw many small developments leading to its creation. -
Characteristics of Digital Fundus Camera Systems Affecting Tonal Resolution in Color Retinal Images 9
Characteristics of Digital Fundus Camera Systems Affecting Tonal Resolution in Color Retinal Images 9 ORIGINAL ARTICLE Marshall E Tyler, CRA, FOPS Larry D Hubbard, MAT University of Wisconsin; Madison, WI Wake Forest University Medical Center Boulevard Ken Boydston Winston-Salem, NC 27157-1033 Megavision, Inc.; Santa Barbara, CA [email protected] Anthony J Pugliese Choices for Service in Imaging, Inc. Glen Rock, NJ Characteristics of Digital Fundus Camera Systems Affecting Tonal Resolution in Color Retinal Images INTRODUCTION of exposure, a smaller or larger number of photons strikes his article examines the impact of digital fundus cam- each sensel, depending upon the brightness of the incident era system technology on color retinal image quality, light in the scene. Within the dynamic range of the sen- T specifically as it affects tonal resolution (brightness, sor, it can differentiate specific levels of illumination on a contrast, and color balance). We explore three topics: (1) grayscale rather than just black or white. However, that the nature and characteristics of the silicon-based photo range of detection is not infinite; too dark and no light is sensor, (2) the manner in which the digital fundus camera detected to provide pictorial detail; too bright and the sen- incorporates the sensor as part of a complete system, and sor “maxes out”, thus failing to record detail. (3) some considerations as to how to select a digital cam- This latter point requires further explanation. Sensels era system to satisfy your tonal resolution needs, and how have a fixed capacity to hold electrons generated by inci- to accept delivery and training on a new system.1 dent photons. -
Spatial Frequency Response of Color Image Sensors: Bayer Color Filters and Foveon X3 Paul M
Spatial Frequency Response of Color Image Sensors: Bayer Color Filters and Foveon X3 Paul M. Hubel, John Liu and Rudolph J. Guttosch Foveon, Inc. Santa Clara, California Abstract Bayer Background We compared the Spatial Frequency Response (SFR) The Bayer pattern, also known as a Color Filter of image sensors that use the Bayer color filter Array (CFA) or a mosaic pattern, is made up of a pattern and Foveon X3 technology for color image repeating array of red, green, and blue filter material capture. Sensors for both consumer and professional deposited on top of each spatial location in the array cameras were tested. The results show that the SFR (figure 1). These tiny filters enable what is normally for Foveon X3 sensors is up to 2.4x better. In a black-and-white sensor to create color images. addition to the standard SFR method, we also applied the SFR method using a red/blue edge. In this case, R G R G the X3 SFR was 3–5x higher than that for Bayer filter G B G B pattern devices. R G R G G B G B Introduction In their native state, the image sensors used in digital Figure 1 Typical Bayer filter pattern showing the alternate sampling of red, green and blue pixels. image capture devices are black-and-white. To enable color capture, small color filters are placed on top of By using 2 green filtered pixels for every red or blue, each photodiode. The filter pattern most often used is 1 the Bayer pattern is designed to maximize perceived derived in some way from the Bayer pattern , a sharpness in the luminance channel, composed repeating array of red, green, and blue pixels that lie mostly of green information. -
A High Full Well Capacity CMOS Image Sensor for Space Applications
sensors Article A High Full Well Capacity CMOS Image Sensor for Space Applications Woo-Tae Kim 1 , Cheonwi Park 1, Hyunkeun Lee 1 , Ilseop Lee 2 and Byung-Geun Lee 1,* 1 School of Electrical Engineering and Computer Science, Gwangju Institute of Science and Technology, Gwangju 61005, Korea; [email protected] (W.-T.K.); [email protected] (C.P.); [email protected] (H.L.) 2 Korea Aerospace Research Institute, Daejeon 34133, Korea; [email protected] * Correspondence: [email protected]; Tel.: +82-62-715-3231 Received: 24 January 2019; Accepted: 26 March 2019; Published: 28 March 2019 Abstract: This paper presents a high full well capacity (FWC) CMOS image sensor (CIS) for space applications. The proposed pixel design effectively increases the FWC without inducing overflow of photo-generated charge in a limited pixel area. An MOS capacitor is integrated in a pixel and accumulated charges in a photodiode are transferred to the in-pixel capacitor multiple times depending on the maximum incident light intensity. In addition, the modulation transfer function (MTF) and radiation damage effect on the pixel, which are especially important for space applications, are studied and analyzed through fabrication of the CIS. The CIS was fabricated using a 0.11 µm 1-poly 4-metal CIS process to demonstrate the proposed techniques and pixel design. A measured FWC of 103,448 electrons and MTF improvement of 300% are achieved with 6.5 µm pixel pitch. Keywords: CMOS image sensors; wide dynamic range; multiple charge transfer; space applications; radiation damage effects 1. Introduction Imaging devices are essential components in the space environment for a range of applications including earth observation, star trackers on satellites, lander and rover cameras [1]. -
Lecture Notes 3 Charge-Coupled Devices (Ccds) – Part II • CCD
Lecture Notes 3 Charge-Coupled Devices (CCDs) { Part II • CCD array architectures and pixel layout ◦ One-dimensional CCD array ◦ Two-dimensional CCD array • Smear • Readout circuits • Anti-blooming, electronic shuttering, charge reset operation • Window of interest, pixel binning • Pinned photodiode EE 392B: CCDs{Part II 3-1 One-Dimensional (Linear) CCD Operation A. Theuwissen, \Solid State Imaging with Charge-Coupled Devices," Kluwer (1995) EE 392B: CCDs{Part II 3-2 • A line of photodiodes or photogates is used for photodetection • After integration, charge from the entire row is transferred in parallel to the horizontal CCD (HCCD) through transfer gates • New integration period begins while charge packets are transferred through the HCCD (serial transfer) to the output readout circuit (to be discussed later) • The scene can be mechanically scanned at a speed commensurate with the pixel size in the vertical direction to obtain 2D imaging • Applications: scanners, scan-and-print photocopiers, fax machines, barcode readers, silver halide film digitization, DNA sequencing • Advantages: low cost (small chip size) EE 392B: CCDs{Part II 3-3 Two-Dimensional (Area) CCD • Frame transfer CCD (FT-CCD) ◦ Full frame CCD • Interline transfer CCD (IL-CCD) • Frame-interline transfer CCD (FIT-CCD) • Time-delay-and-integration CCD (TDI-CCD) EE 392B: CCDs{Part II 3-4 Frame Transfer CCD Light−sensitive CCD array Frame−store CCD array Amplifier Output Horizontal CCD Integration Vertical shift Operation Vertical shift Horizotal shift Time EE 392B: CCDs{Part II 3-5 Pixel Layout { FT-CCD D. N. Nichols, W. Chang, B. C. Burkey, E. G. Stevens, E. A. Trabka, D. -
CMOS Active Pixel Image Sensors for Highly Integrated Imaging Systems
IEEE JOURNAL OF SOLID-STATE CIRCUITS, VOL. 32, NO. 2, FEBRUARY 1997 187 CMOS Active Pixel Image Sensors for Highly Integrated Imaging Systems Sunetra K. Mendis, Member, IEEE, Sabrina E. Kemeny, Member, IEEE, Russell C. Gee, Member, IEEE, Bedabrata Pain, Member, IEEE, Craig O. Staller, Quiesup Kim, Member, IEEE, and Eric R. Fossum, Senior Member, IEEE Abstract—A family of CMOS-based active pixel image sensors Charge-coupled devices (CCD’s) are currently the dominant (APS’s) that are inherently compatible with the integration of on- technology for image sensors. CCD arrays with high fill-factor, chip signal processing circuitry is reported. The image sensors small pixel sizes, and large formats have been achieved and were fabricated using commercially available 2-"m CMOS pro- cesses and both p-well and n-well implementations were explored. some signal processing operations have been demonstrated The arrays feature random access, 5-V operation and transistor- with charge-domain circuits [1]–[3]. However, CCD’s cannot transistor logic (TTL) compatible control signals. Methods of be easily integrated with CMOS circuits due to additional on-chip suppression of fixed pattern noise to less than 0.1% fabrication complexity and increased cost. Also, CCD’s are saturation are demonstrated. The baseline design achieved a pixel high capacitance devices so that on-chip CMOS drive electron- size of 40 "m 40 "m with 26% fill-factor. Array sizes of 28 28 elements and 128 128 elements have been fabricated and ics would dissipate prohibitively high power levels for large characterized. Typical output conversion gain is 3.7 "V/e for the area arrays (2–3 W). -
A Guide to Smartphone Astrophotography National Aeronautics and Space Administration
National Aeronautics and Space Administration A Guide to Smartphone Astrophotography National Aeronautics and Space Administration A Guide to Smartphone Astrophotography A Guide to Smartphone Astrophotography Dr. Sten Odenwald NASA Space Science Education Consortium Goddard Space Flight Center Greenbelt, Maryland Cover designs and editing by Abbey Interrante Cover illustrations Front: Aurora (Elizabeth Macdonald), moon (Spencer Collins), star trails (Donald Noor), Orion nebula (Christian Harris), solar eclipse (Christopher Jones), Milky Way (Shun-Chia Yang), satellite streaks (Stanislav Kaniansky),sunspot (Michael Seeboerger-Weichselbaum),sun dogs (Billy Heather). Back: Milky Way (Gabriel Clark) Two front cover designs are provided with this book. To conserve toner, begin document printing with the second cover. This product is supported by NASA under cooperative agreement number NNH15ZDA004C. [1] Table of Contents Introduction.................................................................................................................................................... 5 How to use this book ..................................................................................................................................... 9 1.0 Light Pollution ....................................................................................................................................... 12 2.0 Cameras ................................................................................................................................................ -
(PPS) • CMOS Photodiode Active Pixel Sensor (APS) • Photoga
Lecture Notes 4 CMOS Image Sensors CMOS Passive Pixel Sensor (PPS) • Basic operation ◦ Charge to output voltage transfer function ◦ Readout speed ◦ CMOS Photodiode Active Pixel Sensor (APS) • Basic operation ◦ Charge to output voltage transfer function ◦ Readout speed ◦ Photogate and Pinned Diode APS • Multiplexed APS • EE 392B: CMOS Image Sensors 4-1 Introduction CMOS image sensors are fabricated in \standard" CMOS technologies • Their main advantage over CCDs is the ability to integrate analog and • digital circuits with the sensor Less chips used in imaging system ◦ Lower power dissipation ◦ Faster readout speeds ◦ More programmability ◦ New functionalities (high dynamic range, biometric, etc) ◦ But they generally have lower perofrmance than CCDs: • Standard CMOS technologies are not optimized for imaging ◦ More circuits result in more noise and fixed pattern noise ◦ In this lecture notes we discuss various CMOS imager architectures • In the following lecture notes we discuss fabrication and layout issues • EE 392B: CMOS Image Sensors 4-2 CMOS Image Sensor Architecture Word Pixel: Row Decoder Photodetector & Readout treansistors Bit Column Amplifiers/Caps Output Column Mux Readout performed by transferring one row at a time to the column • storage capacitors, then reading out the row, one (or more) pixel at a time, using the column decoder and multiplexer In many CMOS image sensor architectures, row integration times are • staggerred by the row/column readout time (scrolling shutter) EE 392B: CMOS Image Sensors 4-3 CMOS Image Sensor -
Micro* Color and Macro* Color RGB Tunable Filters for High-Resolution
PRODUCT NOTE RGB Tunable Filters Micro*Color and Macro*Color RGB Tunable Filters for High- Resolution Color Imaging Figure 1. High-resolution color image of pine cone stem at 10x magnification, taken with a Micro*Color™ slider and monochrome camera on a Zeiss Axioplan™ 2 microscope. Introduction Key Features Micro*Color™ RGB Tunable Filters turn your mono- • Solid-state design for rapid, vibrationless chrome camera into a high-resolution color imaging tuning system. The solid-state liquid crystal design allows • Better spatial resolution than conventional rapid, vibrationless switching between the red, “painted-pixel” CCD or CMOS cameras green, and blue color states, simulating the color- sensitivity curves of the human eye. The closer you • Variety of models for microscope or stand- look, the more you’ll notice that not only are images alone use taken with Micro*Color filter exceptionally accurate • Plug-and-play USB interface with simple in color rendition, but they also contain detail not serial command set reproducible using conventional color cameras. Figure 2. Left to right, Micro*Color sliders for Olympus BX/IX and Zeiss Axioskop™/ Axioplan, and Macro*Color 35 mm optics. True Color When You Need It Why is the Micro*Color Tunable RGB Filter with a The Micro*Color 0.65X coupler is designed for use on micro- Monochrome Camera Better Than a Conventional scopes with an available C-mount camera port. No other Color Camera? adapters are necessary. Micro*Color sliders fit into the analyzer Most digital color cameras utilize a single “painted-pixel” or similar slots on many common research microscope models. -
Digital Light Field Photography
DIGITAL LIGHT FIELD PHOTOGRAPHY a dissertation submitted to the department of computer science and the committee on graduate studies of stanford university in partial fulfillment of the requirements for the degree of doctor of philosophy Ren Ng July © Copyright by Ren Ng All Rights Reserved ii IcertifythatIhavereadthisdissertationandthat,inmyopinion,itisfully adequateinscopeandqualityasadissertationforthedegreeofDoctorof Philosophy. Patrick Hanrahan Principal Adviser IcertifythatIhavereadthisdissertationandthat,inmyopinion,itisfully adequateinscopeandqualityasadissertationforthedegreeofDoctorof Philosophy. Marc Levoy IcertifythatIhavereadthisdissertationandthat,inmyopinion,itisfully adequateinscopeandqualityasadissertationforthedegreeofDoctorof Philosophy. Mark Horowitz Approved for the University Committee on Graduate Studies. iii iv Acknowledgments I feel tremendously lucky to have had the opportunity to work with Pat Hanrahan, Marc Levoy and Mark Horowitz on the ideas in this dissertation, and I would like to thank them for their support. Pat instilled in me a love for simulating the flow of light, agreed to take me on as a graduate student, and encouraged me to immerse myself in something I had a passion for.Icouldnothaveaskedforafinermentor.MarcLevoyistheonewhooriginallydrewme to computer graphics, has worked side by side with me at the optical bench, and is vigorously carrying these ideas to new frontiers in light field microscopy. Mark Horowitz inspired me to assemble my camera by sharing his love for dismantling old things and building new ones. I have never met a professor more generous with his time and experience. I am grateful to Brian Wandell and Dwight Nishimura for serving on my orals commit- tee. Dwight has been an unfailing source of encouragement during my time at Stanford. I would like to acknowledge the fine work of the other individuals who have contributed to this camera research. Mathieu Brédif worked closely with me in developing the simulation system, and he implemented the original lens correction software. -
The Future Is Bright for CCD Sensors TELEDYNE IMAGING
The Future is Bright for CCD Sensors TELEDYNE IMAGING CCDs will Continue to Provide a Crucial Imaging Capability for Science omplementary metal-oxide- CMOS technology accounts for the semiconductor (CMOS) image majority of the visible wavelengths market, sensors now dominate the by revenue as highlighted by Yole Dévelop- Cimaging detector market, but pement Status of the CMOS Image Sensor there are industrial and scientific imaging (CIS) Industry 2018 report. applications where charge-coupled device However, while the economies of scale (CCD) imager sensors is still the preferred and sheer momentum behind CMOS sensor choice, from both technical and commer- development are huge — predominantly in cial perspectives. consumer applications — it is far too early According to market research company, to write off CCD sensors. Research and Markets, the global image As technologies and markets evolve, sensors market is expected to reach $23.2 what is technically feasible and what is billion by 2023 (as of April 2018). commercially viable also evolve, and many Continued market growth is mainly imaging applications in spectroscopy, driven by rising demand for dual-camera microscopy, medium to large ground mobile phones, the development of telescopes and space science will continue low-power and compact image sensors, to be better served by CCDs. and the increased use of image sensing devices in biometric applications. Teledyne e2v CCD Bruyères detector in handling jig for the ESA PLATO mission. 2 teledyneimaging.com THE FUTURE IS BRIGHT FOR CCD SENSORS Scientific applications include optical electron microscopy. 3 TELEDYNE IMAGING Teledyne e2v CIS120 Invented in 1969, Charge-coupled devices CCD AND CMOS BASICS CMOS general purpose where originally designed as a memory CCD and CMOS are both silicon based image sensor for space storage device in the United States at AT&T detector arrays: applications.