Transit Manual
Total Page:16
File Type:pdf, Size:1020Kb
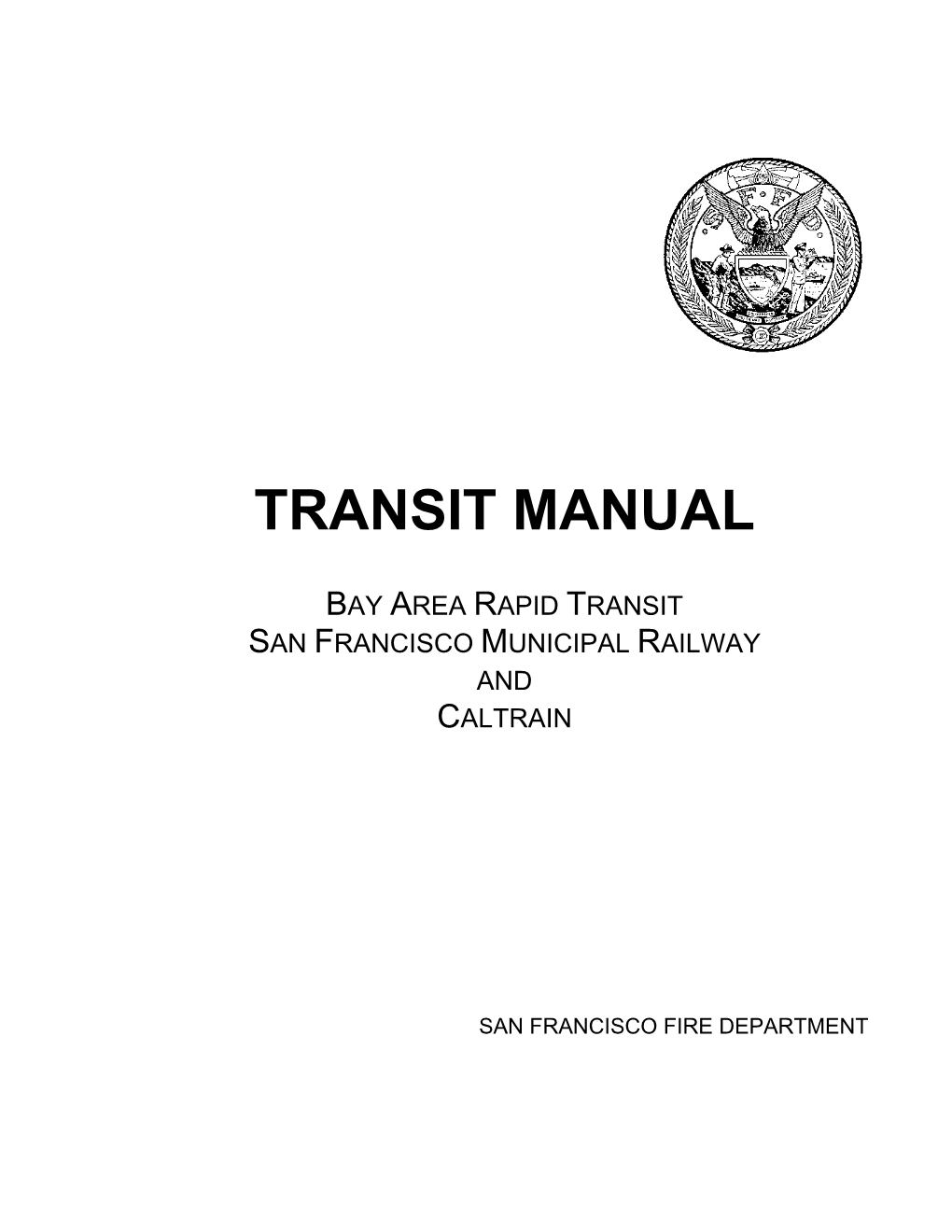
Load more
Recommended publications
-
Please Refrain from Wearing Scented Products (Perfume, Cologne
SAN FRANCISCO BAY AREA RAPID TRANSIT DISTRICT 300 Lakeside Drive, P. O. Box 12688, Oakland, CA 94604-2688 NOTICE OF MEETING AND AGENDA BOND OVERSIGHT COMMITTEE Wednesday, July 26, 2017 4:00 p.m. – 6:00 p.m. COMMITTEE MEMBERS: Marian Breitbart, Michael Day, Daren Gee, Christine D. Johnson, Michael McGill, Anu Natarajan, John Post Meeting of the Bond Oversight Committee on Wednesday, July 26, 2017, at 4:00 p.m. The Meeting will be held in the 1800 Conference Room, 300 Lakeside Dr., 18th Floor, Oakland, California. AGENDA 1. CALL TO ORDER A. Roll Call. 2. INTRODUCTION OF COMMITTEE MEMBERS 3. INTRODUCTION OF BART STAFF 4. COMMITTEE ROLE A. Controller-Treasurer’s Office is official point of contact for all matters B. Audio recording of meetings C. Meeting Agendas/Minutes D. Annual Report writing and approval process E. Request for photos and bio for website F. Clipper Card/Travel reimbursement G. Introduce process of selecting Committee Chair and Vice Chair 5. PRESENTATION: MEASURE RR OVERALL PROGRAM 6. PRESENTATION: STATUS OF BONDS SOLD 7. Q&A WITH STAFF 8. STAFF REQUEST TO PRESENT ASSET MANAGEMENT AT NEXT MEETING 9. SETTING NEXT MEETING DATE AND AGENDA 10. PUBLIC COMMENT Please refrain from wearing scented products (perfume, cologne, after-shave, etc.) to this meeting, as there may be people in attendance susceptible to environmental illnesses. BART provides services/accommodations upon request to persons with disabilities and individuals who are limited English proficient who wish to address BART Board matters. A request must be made within one and five days in advance of a Board or committee meeting, depending on the service requested. -
The Third Crossing
The Third Crossing A Megaproject in a Megaregion www.thirdcrossing.org Final Report, February 2017 Transportation Planning Studio Department of City and Regional Planning, University of California, Berkeley Acknowledgements The authors would like to acknowledge the Department of City and Regional Planning (DCRP) at the College of Environmental Design (CED) at UC Berkeley, the University of California Transportation Center and Institute of Transportation Studies (ITS), UC Berkeley for support. A special thanks also goes to the helpful feedback from studio instructor Karen Trapenberg Frick and UC Berkeley faculty and researchers including Jesus Barajas and Jason Corburn. We also acknowledge the tremendous support and insights from colleagues at numerous public agencies and non-profit organizations throughout California. A very special thanks goes to David Ory, Michael Reilly, and Fletcher Foti of MTC for their gracious support in running regional travel and land use models, and to Professor Paul Waddell and Sam Blanchard of UrbanSim, Inc. for lending their resources and expertise in land use modeling. We also thank our classmates Joseph Poirier and Lee Reis; as well as David Eifler, Teresa Caldeira, Jennifer Wolch, Robert Cervero, Elizabeth Deakin, Malla Hadley, Leslie Huang and other colleagues at CED; and, Alexandre Bayen, Laura Melendy and Jeanne Marie Acceturo of ITS Berkeley. About Us We are a team of 15 graduate students in City Planning, Transportation Engineering, and Public Health. This project aims to facilitate a conversation about the future of transportation between the East Bay and San Francisco and in the larger Northern California megaregion. We are part of the Department of City and Regional Planning in the UC Berkeley College of Environmental Design, with support from the University of California Transportation Center and The Institute of Transportation Studies at the University of California, Berkeley. -
SAN FRANCISCO 2Nd Quarter 2014 Office Market Report
SAN FRANCISCO 2nd Quarter 2014 Office Market Report Historical Asking Rental Rates (Direct, FSG) SF MARKET OVERVIEW $60.00 $57.00 $55.00 $53.50 $52.50 $53.00 $52.00 $50.50 $52.00 Prepared by Kathryn Driver, Market Researcher $49.00 $49.00 $50.00 $50.00 $47.50 $48.50 $48.50 $47.00 $46.00 $44.50 $43.00 Approaching the second half of 2014, the job market in San Francisco is $40.00 continuing to grow. With over 465,000 city residents employed, the San $30.00 Francisco unemployment rate dropped to 4.4%, the lowest the county has witnessed since 2008 and the third-lowest in California. The two counties with $20.00 lower unemployment rates are neighboring San Mateo and Marin counties, $10.00 a mark of the success of the region. The technology sector has been and continues to be a large contributor to this success, accounting for 30% of job $0.00 growth since 2010 and accounting for over 1.5 million sf of leased office space Q2 Q3 Q4 Q1 Q2 Q3 Q4 Q1 Q2 2012 2012 2012 2013 2013 2013 2013 2014 2014 this quarter. Class A Class B Pre-leasing large blocks of space remains a prime option for large tech Historical Vacancy Rates companies looking to grow within the city. Three of the top 5 deals involved 16.0% pre-leasing, including Salesforce who took over half of the Transbay Tower 14.0% (delivering Q1 2017) with a 713,727 sf lease. Other pre-leases included two 12.0% full buildings: LinkedIn signed a deal for all 450,000 sf at 222 2nd Street as well 10.0% as Splunk, who grabbed all 182,000 sf at 270 Brannan Street. -
A Year of Movement
A Year of Movement San Francisco Municipal Transportation Agency Fiscal Year 2017-2018 Annual Report VISION Excellent transportation choices for San Francisco. MISSION We connect San Francisco through a safe, equitable and sustainable transportation system. Table of Contents Letter from the DOT About the SFMTA SFMTA Strategic Plan Moving Muni Forward Improving Access to Transportation Making Streets Safer with Vision Zero Building Out the Bike Network Driving Innovation Protecting the Environment Our Workplace Connects to the Transportation System Working with Communities Completed Projects FY 2017-2018 Projects on the Horizon Financial Information Key Performance Indicators Acknowledgments This annual report shares milestones and data covering the fiscal year that began July 1, 2017 and closed June 30, 2018. This period comprises the final year of the Fiscal Year 2013–2018 SFMTA Strategic Plan. A Year of Movement San Francisco is the epicenter of transportation innovation. This was true a century ago, when our city introduced Muni as the first publicly owned transit system in the nation. San Francisco continues to be the home of transportation innovations, from the great strides we’ve made to embrace environmentally friendly transportation options and being the home of the greenest public transit system in North America, to proactively designing streets that prioritize your safety and well-being no matter how you move around the city. Our annual report describes the many ways that we work to manage, operate and regulate the city’s transportation system to ensure that it is safe, reliable and equitable. Thanks to historic investments to replace and expand the entire Muni fleet with state-of-the-art light rail vehicles and new coaches, trolleys and hybrid buses, Muni now generates less than 2 percent of the city’s greenhouse gas emissions. -
Draft Plan Bay Area 2050 Air Quality Conformity Analysis
DRAFT AIR QUALITY CONFORMITY AND CONSISTENCY REPORT JULY 2021 PBA2050 COMMISH BOARD DRAFT 06.14.21 Metropolitan Transportation Association of City Representatives Commission Bay Area Governments Susan Adams Alfredo Pedroza, Chair Jesse Arreguín, President Councilmember, City of Rohnert Park Napa County and Cities Mayor, City of Berkeley Nikki Fortunato Bas Nick Josefowitz, Vice Chair Belia Ramos, Vice President Councilmember, City of Oakland San Francisco Mayor's Appointee Supervisor, County of Napa London Breed Margaret Abe-Koga David Rabbitt, Mayor, City and County of San Francisco Cities of Santa Clara County Immediate Past President Tom Butt Supervisor, County of Sonoma Eddie H. Ahn Mayor, City of Richmond San Francisco Bay Conservation Pat Eklund and Development Commission County Representatives Mayor, City of Novato David Canepa Candace Andersen Maya Esparza San Mateo County Supervisor, County of Contra Costa Councilmember, City of San José Cindy Chavez David Canepa Carroll Fife Santa Clara County Supervisor, County of San Mateo Councilmember, City of Oakland Damon Connolly Keith Carson Neysa Fligor Marin County and Cities Supervisor, County of Alameda Mayor, City of Los Altos Carol Dutra-Vernaci Cindy Chavez Leon Garcia Cities of Alameda County Supervisor, County of Santa Clara Mayor, City of American Canyon Dina El-Tawansy Otto Lee Liz Gibbons California State Transportation Agency Supervisor, County of Santa Clara Mayor, City of Campbell (CalSTA) Gordon Mar Giselle Hale Victoria Fleming Supervisor, City and County Vice Mayor, City of Redwood City Sonoma County and Cities of San Francisco Barbara Halliday Dorene M. Giacopini Rafael Mandelman Mayor, City of Hayward U.S. Department of Transportation Supervisor, City and County Rich Hillis Federal D. -
Coherent, Inc. 5100 Patrick Henry Drive, Santa Clara, Ca 95054
COHERENT, INC. 5100 PATRICK HENRY DRIVE, SANTA CLARA, CA 95054 San Francisco International Airport (SFO) Mineta San Jose International Airport (SJC) – is approximately 30 miles north of Santa Clara – is approximately 6 miles south of Santa Clara Website: https://www.flysfo.com/ 1701 Airport Boulevard, San Jose, CA 95110 Website: http://www.flysanjose.com/fl/ Directions: Get on US-101 S from International Terminal Arrivals Directions: Level - 1.4 mi http://www.flysanjose.com/fl/travelers.php?page=map s/to_here&exp=7 Follow US-101 South Leaving the rental car area, follow the signs to CA-87 Merge onto US-101 S to Lawrence Expressway in and US-101 North Sunnyvale (Exit 394 from US 101) - 27.5 mi Use the right lane to turn right on to Skyport Drive (430 Use the 2nd from the right lane to take Exit 394 for ft.) Lawrence Expressway - 0.3 mi Use the right lane to merge onto CA-87 via the ramp Follow Lawrence Expressway and Tasman Drive to to Hwy 101 N – 0.8 mi Patrick Henry Drive in Santa Clara - 1.7 mi Use the left 3 lanes to take exit 9B to merge onto Turn left on Patrick Henry Drive – Coherent is on your US-101 N toward San Francisco – 2.7 mi immediate left ___________________________ Take exit 393 to merge on to Great America Parkway – 1.4 mi Keep right at the fork & merge onto Great America Parkway – 1.5 mi Taxi from/to SFO and/or SJC airports: Use the left 2 lanes to turn left onto Tasman Drive - 0.4 SFO – you can have a sedan arranged for your arrival mi SJC – you can take a taxi or have a sedan arranged for your arrival. -
AQ Conformity Amended PBA 2040 Supplemental Report Mar.2018
TRANSPORTATION-AIR QUALITY CONFORMITY ANALYSIS FINAL SUPPLEMENTAL REPORT Metropolitan Transportation Commission Association of Bay Area Governments MARCH 2018 Metropolitan Transportation Commission Jake Mackenzie, Chair Dorene M. Giacopini Julie Pierce Sonoma County and Cities U.S. Department of Transportation Association of Bay Area Governments Scott Haggerty, Vice Chair Federal D. Glover Alameda County Contra Costa County Bijan Sartipi California State Alicia C. Aguirre Anne W. Halsted Transportation Agency Cities of San Mateo County San Francisco Bay Conservation and Development Commission Libby Schaaf Tom Azumbrado Oakland Mayor’s Appointee U.S. Department of Housing Nick Josefowitz and Urban Development San Francisco Mayor’s Appointee Warren Slocum San Mateo County Jeannie Bruins Jane Kim Cities of Santa Clara County City and County of San Francisco James P. Spering Solano County and Cities Damon Connolly Sam Liccardo Marin County and Cities San Jose Mayor’s Appointee Amy R. Worth Cities of Contra Costa County Dave Cortese Alfredo Pedroza Santa Clara County Napa County and Cities Carol Dutra-Vernaci Cities of Alameda County Association of Bay Area Governments Supervisor David Rabbit Supervisor David Cortese Councilmember Pradeep Gupta ABAG President Santa Clara City of South San Francisco / County of Sonoma San Mateo Supervisor Erin Hannigan Mayor Greg Scharff Solano Mayor Liz Gibbons ABAG Vice President City of Campbell / Santa Clara City of Palo Alto Representatives From Mayor Len Augustine Cities in Each County City of Vacaville -
Conference Transportation Guide
Conference Transportation Guide February 12–15 San Francisco Think Venues Walking, shuttles, BART (Bay The best way to get around Connector Shuttle: Area Rapid Transit) — San Think venues is on foot. Check Moscone/Hilton Hours Francisco has it all. Think 2019 on distances between Think The Connector Shuttle will run Tuesday 7:30am–5:30pm is in a new city. To maximize your venues, suggested walking paths, between Moscone West and the Wednesday 7:30am–6:30pm time, ensure you know how to and wear comfortable shoes. Hilton San Francisco Union Square Thursday 7:30am–6:30pm get around. during the following times: Friday 7:30am–12:30pm Post St 2nd St Think Site Map 14 Market St Kearny St Kearny Grand St Grand Stockton St Stockton 1 Moscone West 6 Press Club Geary St New Montgomery St Registration & Information Desk (Sun–Tue am only) 7 Yerba Buena Forum Chairman’s Address General Session: Research 8 Yerba Buena Theater Science Slam Featured Sessions O’Farrell St 15 3rd St 2 Moscone North 9 AMC Metreon 13 Registration & Information Desk Breakout Sessions Code Yerba Buena Ln Minna St Think Theater (Featured Sessions) Powell St Powell Ellis St 6 Executive Meeting Center Business Partner Café 10 City View 7 Natoma St InnerCircle Lounge Market St 16 Mission St 3 Moscone South Mason St Registration & Information Desk 11 Tabletop Tap House Eddy St St Magnin Cyril Howard St Think Academy Code Café 5 8 9 Think Campus InterContinental Bookstore & Think Store 12 10 Registration 2 4 Think Park (Howard St.) Breakout Sessions Mason St Transportation Think Park Theater 11 (Featured Sessions) 13 Hilton Union Square Walking Path Mission St Be Equal Lounge Registration 4 1 3 Breakout Sessions Market St BART 5 Yerba Buena Gardens 5th St Westin St. -
EMMA Official Statement
NEW ISSUE – BOOK ENTRY ONLY RATINGS: Moody’s (2020 Bonds): Aaa Long Term Standard & Poor’s (2020C-1 Bonds): AAA Short Term Standard & Poor’s (2020C-2 Bonds): A-1+ See “Ratings” herein. In the opinion of Orrick, Herrington & Sutcliffe LLP, Bond Counsel to the District, based upon an analysis of existing laws, regulations, rulings and court decisions, and assuming, among other matters, the accuracy of certain representations and compliance with certain covenants, interest on the 2020C-1 Bonds is excluded from gross income for federal income tax purposes under Section 103 of the Internal Revenue Code of 1986. In the further opinion of Bond Counsel, interest on the 2020C-1 Bonds is not a specific preference item for purposes of the federal alternative minimum tax. Bond Counsel is also of the opinion that interest on the 2020 Bonds is exempt from State of California personal income taxes. Bond Counsel further observes that interest on the 2020C-2 Bonds is not excluded from gross income for federal income tax purposes under Section 103 of the Code. Bond Counsel expresses no opinion regarding any other tax consequences related to the ownership or disposition of, or the amount, accrual or receipt of interest on, the 2020 Bonds. See “TAX MATTERS.” $700,000,000 SAN FRANCISCO BAY AREA RAPID TRANSIT DISTRICT GENERAL OBLIGATION BONDS $625,005,000 $74,995,000 (ELECTION OF 2016), (ELECTION OF 2016), 2020 SERIES C-1 2020 SERIES C-2 (FEDERALLY TAXABLE) (GREEN BONDS) (GREEN BONDS) Dated: Date of Delivery Due: As shown on inside cover The San Francisco Bay Area Rapid Transit District General Obligation Bonds (Election of 2016), 2020 Series C-1 (Green Bonds) (the “2020C-1 Bonds”) and 2020 Series C-2 (Federally Taxable) (Green Bonds) (the “2020C-2 Bonds” and, together with the 2020C-1 Bonds, the “2020 Bonds”) are being issued to finance specific acquisition, construction and improvement projects for District facilities approved by the voters and to pay the costs of issuance of the 2020 Bonds. -
CPUC 2015 Triennial Audit Report
2015 TRIENNIAL SAFETY REVIEW OF SAN FRANCISCO MUNICIPAL TRANSPORTATION AGENCY (SFMTA) RAIL TRANSIT SAFETY BRANCH SAFETY AND ENFORCEMENT DIVISION CALIFORNIA PUBLIC UTILITIES COMMISSION 505 VAN NESS AVENUE SAN FRANCISCO, CA 94102 November 10, 2016 Final Report Elizaveta Malashenko, Director Safety and Enforcement Division 2015 TRIENNIAL SAFETY REVIEW OF SAN FRANCISCO MUNICIPAL TRANSPORTATION AGENCY (SFMTA) ACKNOWLEDGEMENT The California Public Utilities Commission’s Rail Transit Safety Branch (RTSB) staff conducted this system safety program review. Staff members directly responsible for conducting safety review and inspection activities include: Daren Gilbert – Program Manager Stephen Artus – Program & Project Supervisor Steve Espinal – Senior Utilities Engineer, Supervisor Jimmy Xia – Utilities Engineer – SFMTA Representative Raed Dwairi – Utilities Engineer – Joey Bigornia – Utilities Engineer Mike Borer –Supervisor Sherman Boyd – Signal Inspector Debbie Dziadzio –Operations Inspector Adam Freeman – Mechanical Inspector Robert Hansen – Utilities Engineer – AirTrain Representative Howard Huie – Utilities Engineer – LACMTA Representative Claudia Lam – Senior Utilities Engineer, Specialist David Leggett – Senior Utilities Engineer, Specialist John Madriaga –Track Inspector James Matus – Mechanical Inspector Kevin McDonald –Track Inspector Arun Mehta – Utilities Engineer Paul Renteria – Bridge Inspector Rupa Shitole – Utilities Engineer Yan Solopov – Regulatory Analyst Colleen Sullivan – Utilities Engineer Michael Warren – Utilities Engineer -
San Francisco Bay Area Regional Rail Plan, Chapter 7
7.0 ALTERNATIVES DEFINITION & Fig. 7 Resolution 3434 EVALUATION — STEP-BY-STEP Step One: Base Network Healdsburg Sonoma Recognizing that Resolution 3434 represents County 8 MTC’s regional rail investment over the next 25 Santa years as adopted first in the 2001 Regional Trans- Rosa Napa portation Plan and reaffirmed in the subsequent County Vacaville 9 plan update, Resolution 3434 is included as part Napa of the “base case” network. Therefore, the study Petaluma Solano effort focuses on defining options for rail improve- County ments and expansions beyond Resolution 3434. Vallejo Resolution 3434 rail projects include: Marin County 8 9 Pittsburg 1. BART/East Contra Costa Rail (eBART) San Antioch 1 Rafael Concord Richmond 2. ACE/Increased Services Walnut Berkeley Creek MTC Resolution 3434 Contra Costa 3. BART/I-580 Rail Right-of-Way Preservation County Rail Projects Oakland 4. Dumbarton Bridge Rail Service San 1 BART: East Contra Costa Extension Francisco 10 6 3 2 ACE: Increased Service 5. BART/Fremont-Warm Springs to San Jose Daly City 2 Pleasanton Livermore 3 South Extension BART: Rail Right-of-Way Preservation San Francisco Hayward Union City 4 Dumbarton Rail Alameda 6. Caltrain/Rapid Rail/Electrification & Extension San Mateo Fremont County 5 BART: Fremont/Warm Springs 4 to Downtown San Francisco/Transbay Transit to San Jose Extension 7 Redwood City 5 Center 6 & Extension to Downtown SF/ Mountain Milpitas Transbay Transit Center View Palo Alto 7. Caltrain/Express Service 7 Caltrain: Express Service Sunnyvale Santa Clara San San Santa Clara 8 Jose 8. SMART (Sonoma-Marin Rail) SMART (Sonoma-Marin Rail) Mateo Cupertino County 9 County 9. -
1999 Caltrain Short Term Service Study
Caltrain Short-Term Service and Fleet Study FINAL REPORT Prepared for the Peninsula Corridor Joint Powers Board By SYSTRA Consulting March 2000 Cal, TM Caltrain Short-Term Service and Fleet Study TABLE OF CONTENTS 1. Acknowledgements 1 2. Executive Summary 2 3. Introduction and Purpose 6 4. Service and Performance Standards 7 5. Ridership Trends 9 6. Dwell Time Reduction 13 7. Short Term Service Options 14 7.1 Service Option No.1: Schedule Optimization to Address Reverse Peak 14 7.2 Service Option NO.2: Selected Trains Turn at Millbrae Station 21 7.3 Service Option NO.3: Palo Alto to Gilroy Additional Train Service 28 7.4 Service Option NO.4: Medium-Term Schedule Optimization 34 7.5 Service Option NO.5: Medium-Term Schedule Optimization, Gilroy Service Extension 42 7.6 Service Option NO.6: Medium-Term Completely New Schedule, Repetitive Zone Patterns 49 7.7 Key Recommendations 57 8. Related Service Planning Issues 59 8.1 Yard and Terminal Capacity 59 8.2 Third Track Utilization and Capital Requirements 60 9. Source Documents 64 10. Appendix 65 LIST OF TABLES Table 1: Summary Table of Findings 5 Table 2: Factors Expected to Influence Ridership Increases 11 Table 3: County-to-County Commuting in the San Francisco Bay Area 1990-2020 12 Table 4: Service Options Matrix 15 Table 5: Conceptual Train-Equipment Cycles for Service Option No.1 19 Table 6: Annual Operating and Maintenance Cost Indices for Service Option No.1 20 Table 7: Conceptual Train-Equipment Cycles for Service Option No.2 25 Table 8: Annual Operating and Maintenance Cost Indices