To Formula One Systems and Specialists a MODERN RECIPE for HIGH-TECH ENGINEERING SUCCESS
Total Page:16
File Type:pdf, Size:1020Kb
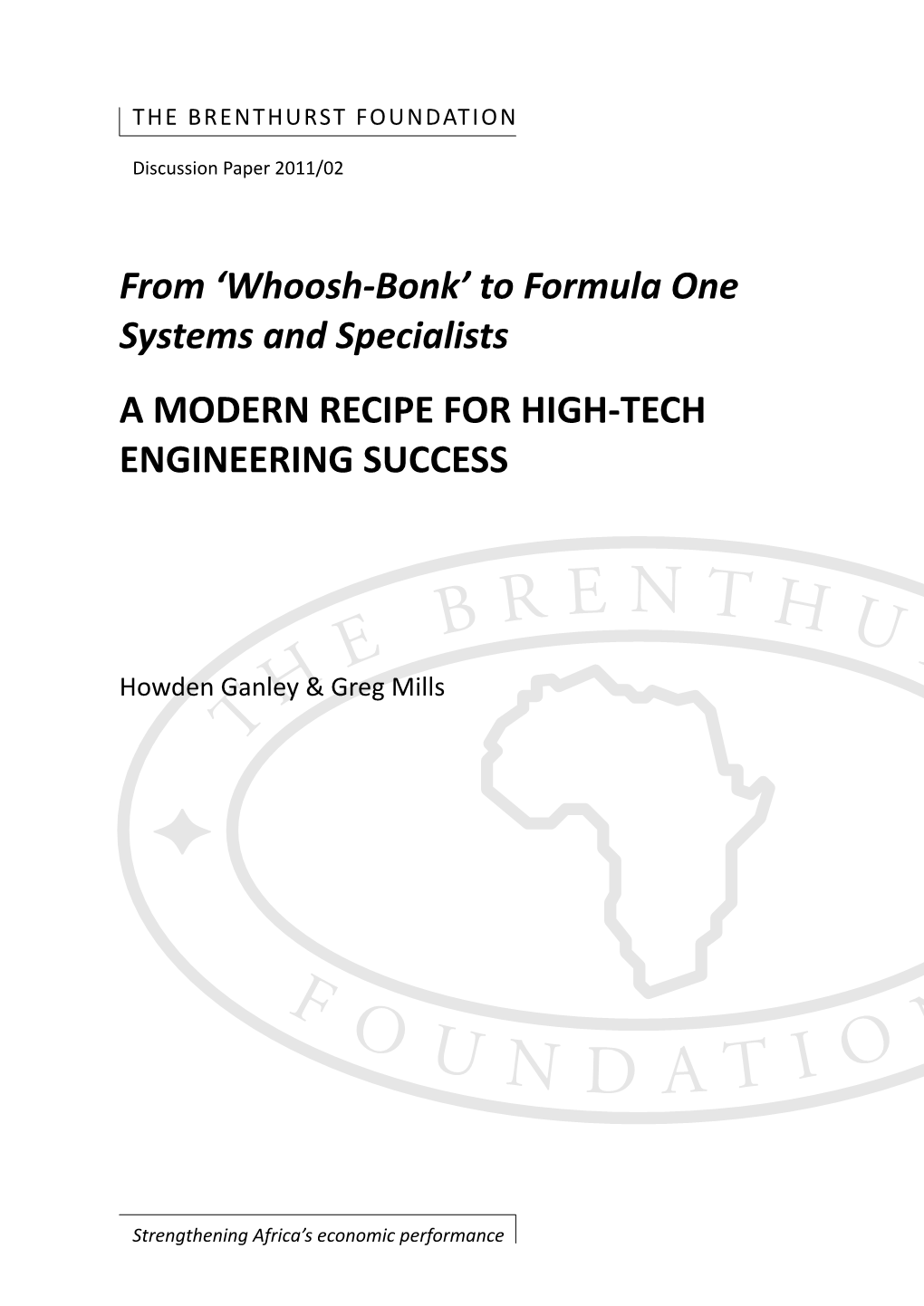
Load more
Recommended publications
-
President's Message
Published by the Golden Gate Lotus Club www.gglotus.org June 2003 President’s Message by Peter Richen Noni & I went to the Wine Country Classic the other day. Dave and Penny Elsebusch, who race a Lotus 7A (Dave drives, Penny is the mechanic), kindly provided me with a participant’s pass. It was a beautiful day. The Lotus marque was well represented with two 7A’s in the ’55 to ’62 GT & Production Car class; seven 23’s in the ’61 to ’65 Sport Racing Class; a super 7, and an Elan 26R in ’63 to ’66 GT and Produc- tion Cars; twelve 18’s, 20’s, 22’s and 27’s in the ’57 to ’63 Formula Car Class; and nine 11’s and one 15 in the ’55 to ’60 Sport Racing Class. In addition to the racing, there was a large tent devoted to wine tasting and other gourmet items from the Napa and Sonoma area. It cost an extra $15 each to get into the tent, but it went to Rich Kamp and a new Caterham 7, in his new shop charity, and it was worth it to be able to taste and nibble from a scenic area overlooking the course. We also took the opportunity to visit with Rich Kamp at his new shop, June Meeting which is right behind turn 10 (opposite the main grandstand). For those of you Friday, June 20th, 7:30 pm who remember his shop in South City, this new shop in huge in comparison Host: John Zender, aka Fusion Technology (~3000 SF). -
British American Racing British American Racing
BRITISH AMERICAN RACING BRITISH AMERICAN RACING Presents An Introduction to British American Racing and Formula One British American Racing - PO Box 5014, Brackley, Northants NN13 7YY, England Paul Jordan, Commercial Manager - Tel : (44) 1280 840 402 ; Fax: (44) 1280 840 403 British American Racing - Reynard Centre, Telford Road, Bicester, Oxfordshire OX6 OUY England Rick Gorne, Commercial Director - Tel : (44) 1869 244 397; Fax: (44) 1 869 324 575 C BRITISH AMERICAN ToBAcco C C May 1998 C To Whom It May Concern : After a period of extensive research and analysis, British American Tobacco confirmed its intention to enter the 1999 FIA Formula One World Championship . To obtain maximum Corporate Brand Value, this entry is formulated on a unique business configuration and a Brand Strategy which will be revolutionary to the Sport of Formula 1 . We believe that we are a leading World Package Goods Organisation and, as such, must set a leader profile with our business associates and consumers. British American Racing is a new FIA Formula One constructor and was established with the necessary resources, both human and financial, to compete effectively with the best in the world . On racing matters, we have complete confidence in our partners, Mr Craig Pollock and the Reynard Group : Mr Adrian Reynard, Mr Richard Gorne and Mr Malcolm Oastler, to be the Formula One Team of the future . L. Like you, our interests must relate to its effect on our business associates and consumers . I In this regard, we have formulated a commercial package which will ensure a heightened level of awareness and value to our brands and organisation. -
Le Mans (Not Just) for Dummies the Club Arnage Guide
Le Mans (not just) for Dummies The Club Arnage Guide to the 24 hours of Le Mans 2011 "I couldn't sleep very well last night. Some noisy buggers going around in automobiles kept me awake." Ken Miles, 1918 - 1966 Copyright The entire contents of this publication and, in particular of all photographs, maps and articles contained therein, are protected by the laws in force relating to intellectual property. All rights which have not been expressly granted remain the property of Club Arnage. The reproduction, depiction, publication, distr bution or copying of all or any part of this publication, or the modification of all or any part of it, in any form whatsoever is strictly forbidden without the prior written consent of Club Arnage (CA). Club Arnage (CA) hereby grants you the right to read and to download and to print copies of this document or part of it solely for your own personal use. Disclaimer Although care has been taken in preparing the information supplied in this publication, the authors do not and cannot guarantee the accuracy of it. The authors cannot be held responsible for any errors or omissions and accept no liability whatsoever for any loss or damage howsoever arising. All images and logos used are the property of Club Arnage (CA) or CA forum members or are believed to be in the public domain. This guide is not an official publication, it is not authorized, approved or endorsed by the race-organizer: Automobile Club de L’Ouest (A.C.O.) Mentions légales Le contenu de ce document et notamment les photos, plans, et descriptif, sont protégés par les lois en vigueur sur la propriété intellectuelle. -
Forgotten F1 Teams – Series 1 Omnibus Simtek Grand Prix
Forgotten F1 Teams – Series 1 Omnibus Welcome to Forgotten F1 Teams – a mini series from Sidepodcast. These shows were originally released over seven consecutive days But are now gathered together in this omniBus edition. Simtek Grand Prix You’re listening to Sidepodcast, and this is the latest mini‐series: Forgotten F1 Teams. I think it’s proBaBly self explanatory But this is a series dedicated to profiling some of the forgotten teams. Forget aBout your Ferrari’s and your McLaren’s, what aBout those who didn’t make such an impact on the sport, But still have a story to tell? Those are the ones you’ll hear today. Thanks should go to Scott Woodwiss for suggesting the topic, and the teams, and we’ll dive right in with Simtek Grand Prix. Simtek Grand Prix was Born from Simtek Research Ltd, the name standing for Simulation Technology. The company founders were Nick Wirth and Max Mosley, Both of whom had serious pedigree within motorsport. Mosley had Been a team owner Before with March, and Wirth was a mechanical engineering student who was snapped up By March as an aerodynamicist, working underneath Adrian Newey. When March was sold to Leyton House, Mosley and Wirth? Both decided to leave, and joined forces to create Simtek. Originally, the company had a single office in Wirth’s house, But it was soon oBvious they needed a Bigger, more wind‐tunnel shaped Base, which they Built in Oxfordshire. Mosley had the connections that meant racing teams from all over the gloBe were interested in using their research technologies, But while keeping the clients satisfied, Simtek Began designing an F1 car for BMW in secret. -
Formula E Finale Buemi Survives Clash to Take the Crown #%%'.'4#6' +0018#6+10
AUSTRIAN GP WHAT MERC CRASH TANAK DENIED SURPRISE 16-PAGE REPORT MEANS FOR FORMULA 1 WORLD RALLY VICTORY HAMILTON WINS… ROSBERG FUMES As Wolff threatens team orders “I don’t want contact anymore” FORMULA E FINALE BUEMI SURVIVES CLASH TO TAKE THE CROWN #%%'.'4#6' +0018#6+10 ÜÜܰ>Û°VÉÀ>V} 5+/7.#6' '0)+0''4 /#-' 6'56 4#%' AUSTRIAN GP WHAT MERC CRASH TANAK DENIED SURPRISE 16-PAGE REPORT MEANS FOR FORMULA 1 WORLD RALLY VICTORY HAMILTON WINS… ROSBERG FUMES COVER IMAGES As Wolff threatens team orders “I don’t want contact anymore” Etherington/LAT; FORMULA E FINALE Charniaux/XPB; BUEMI SURVIVES CLASH TO TAKE THE CROWN Rajan Jangda/e-racing.net COVER STORY 4 Austrian Grand Prix report and analysis PIT+PADDOCK 20 FIA aims to boost motorsport worldwide 22 New manufacturers for Formula E 25 Feedback: your letters 27 Ian Parkes: in the paddock REPORTS AND FEATURES XPB IMAGES 28 Buemi takes Formula E title as Prost wins 34 Heartache for Tanak in Rally Poland 40 Suzuki: the sleeping giant of MotoGP Nico still struggling to RACE CENTRE 46 GP2; GP3; Blancpain Sprint Cup; NASCAR Sprint Cup; Formula get the balance right Renault Eurocup; IMSA SportsCar NICO ROSBERG JUST CAN’T QUITE GET IT RIGHT. WHEN CLUB AUTOSPORT it comes to wheel-to-wheel battles, he is either too soft or overly 65 Will Palmer to race in BRDC F3 at Spa robust. He usually comes off worst too, particularly when fi ghting 66 Crack Mercedes squad for British GT Mercedes ‘team-mate’ and title rival Lewis Hamilton. -
Stock List Updated 28/09/2021
1:43 Formula 1 - Stock List Updated 28/09/2021 Limited Price Model Year Description Manufacturer Manuf # Edition (AUD) F o r m u l a 1 , 2 a n d 3 Alfa Romeo 158 1950 Race car (25) (Oro Series) Brumm R036 35.00 Alfa Romeo 158 1950 L.Fagioli (12) 2nd Swiss GP Brumm S055 5000 40.00 Alfa Romeo 159 1951 Consalvo Sanesi (3) 6th British GP Minichamps 400511203 55.00 Alfa Romeo Ferrari C38 2019 K.Raikkonen (7) Bahrain GP Minichamps 447190007 222 135.00 Alfa Romeo Ferrari C39 2020 K.Raikkonen (7) Turkish GP Spark S6492 100.00 Alpha Tauri Honda AT01 2020 D.Kvyat (26) Austrian GP Minichamps 417200126 400 125.00 Alpha Tauri Honda AT01 2020 P.Gasly (10) 1st Italian GP Spark S6480 105.00 Alpha Tauri Honda AT01 2020 P.Gasly (10) 7th Austrian GP Spark S6468 100.00 Andrea Moda Judd S921 1992 P.McCathy (35) DNPQ Monaco GP Spark S3899 100.00 Arrows BMW A8 1986 M.Surer (17) Belgium GP "USF&G" Last F1 race Minichamps 400860017 75.00 Arrows Mugen FA13 1992 A.Suzuki (10) "Footwork" Onyx 146 25.00 Arrows Hart FA17 1996 R. Rosset (16) European GP Onyx 284 30.00 Arrows A20 1999 T.Takagi (15) show car Minichamps 430990084 25.00 Australian GP Event car 2001 Qantas AGP Event car Minichamps AC4010300 3000 40.00 Auto Union Tipo C 1936 R.Gemellate (6) Brumm R110 38.00 BAR Supertec 01 2000 J.Villeneuve test car Minichamps 430990120 40.00 BAR Honda 03 2001 J.Villeneuve (10) Minichamps 400010010 35.00 BAR Honda 005 2003 T.Sato collection (16) Japan GP standing driver Minichamps 518034316 35.00 BAR Honda 006 2004 J. -
We Celebrate One of the Great Racing Car Constructors
LOLA AT 60 WE CELEBRATE ONE OF THE GREAT RACING CAR CONSTRUCTORS Including FROM BROADLEY TO BIRRANE GREATEST CARS LOLA’S SECRET WEAPON THE AUDI CHALLENGER The success of the Mk1 sports-racer, usually powered by the Coventry Climax 1100cc FWA engine, brought Lola Cars into existence. It overshadowed the similar e orts of Lotus boss Colin Chapman and remained competitive for several seasons. We believe it is one of designer Eric Broadleyʼs greatest cars, so turn to page 16 to see what our resident racer made of the original prototype at Donington Park. Although the coupe is arguably more iconic, the open version of the T70 was more successful. Developed in 1965, the Group 7 machine could take a number of di erent V8 engines and was ideal for the inaugural Can-Am contest in ʼ66. Champion John Surtees, Dan Gurney and Mark Donohue won races during the campaign, while Surtees was the only non-McLaren winner in ʼ67. The big Lola remains a force in historic racing. JEP/PETCH COVER IMAGES: JEP/PETCH IMAGES: COVER J BLOXHAM/LAT Contents 4 The story of Lola How Eric Broadley and Martin Birrane Celebrating a led one of racing’s greatest constructors 10 The 10 greatest Lolas racing legend Mk1? T70? B98/10? Which do you think is best? We select our favourites and Lola is one of the great names of motorsport. Eric Broadley’s track test the top three at Donington Park fi rm became one of the leading providers of customer racing cars and scored success in a diverse range of categories. -
Publications Dealing with Cfd Focused Principally Company Such As Tatuus to Use Them
TATUUS STORY: Thirty years of success PY 012: The Prototype of the future LUCA GHIOTTO: “I’m studying to become a champion” MAGAZINE n.1 - 2013 i THE HISTORY “That bet with Renault” 2 3 hirty years of racing, adventures and was Alberto Colombo, the owner of the historic Martini from France. The first year we showed up success. From Formula Monza to Sanremo Racing team. He noticed my with 3/4 cars, making very little headway: the Formula Renault 2000, from enthusiasm, that I was good in looking for teams weren’t interested in buying our models. Formula Ford to the new challenges sponsors, and offered me a job as team manager. However we learned to appreciate just how much in the world of prototypes. Tatuus It was a dream come true. When Alberto retired effort Renault Sport was putting in to promote Racing was founded by Artico from racing, I created a company providing teams the sport. They gave us a real break because, after TSandonà and Gianfranco De Bellis in 1980 and has with a complete range of services such as printed seeing our project, they bought the first car. built an international reputation in motorsports postcards, photographs, stickers and hospitality, Rather than cash, they paid us with 3/4 kits which based on passion, efficiency and the ability to together with another youngster from Monza were worth about 60 million Lire at the time». provide top‐quality products at competitive who followed Formula Monza as a photographer, This was just what we needed but once again it prices, together italian, or more specifically, and who is unfortunately no longer with us. -
Racing, Region, and the Environment: a History of American Motorsports
RACING, REGION, AND THE ENVIRONMENT: A HISTORY OF AMERICAN MOTORSPORTS By DANIEL J. SIMONE A DISSERTATION PRESENTED TO THE GRADUATE SCHOOL OF THE UNIVERSITY OF FLORIDA IN PARTIAL FULFILLMENT OF THE REQUIREMENTS FOR THE DEGREE OF DOCTOR OF PHILOSOPHY UNIVERSITY OF FLORIDA 2009 1 © 2009 Daniel J. Simone 2 To Michael and Tessa 3 ACKNOWLEDGMENTS A driver fails without the support of a solid team, and I thank my friends, who supported me lap-after-lap. I learned a great deal from my advisor Jack Davis, who when he was not providing helpful feedback on my work, was always willing to toss the baseball around in the park. I must also thank committee members Sean Adams, Betty Smocovitis, Stephen Perz, Paul Ortiz, and Richard Crepeau as well as University of Florida faculty members Michael Bowen, Juliana Barr, Stephen Noll, Joseph Spillane, and Bill Link. I respect them very much and enjoyed working with them during my time in Gainesville. I also owe many thanks to Dr. Julian Pleasants, Director Emeritus of the Samuel Proctor Oral History Program, and I could not have finished my project without the encouragement provided by Roberta Peacock. I also thank the staff of the Samuel Proctor Oral History Program. Finally, I will always be grateful for the support of David Danbom, Claire Strom, Jim Norris, Mark Harvey, and Larry Peterson, my former mentors at North Dakota State University. A call must go out to Tom Schmeh at the National Sprint Car Hall of Fame, Suzanne Wise at the Appalachian State University Stock Car Collection, Mark Steigerwald and Bill Green at the International Motor Racing Resource Center in Watkins Glen, New York, and Joanna Schroeder at the (former) Ethanol Promotion and Information Council (EPIC). -
Sample Download
KÁROLY MéHES GILLES VILLENEUVE HIS UNTOLD LIFE FROM BERTHIERVILLE TO ZOLDER 48 INTERVIEWS 1 GILLES VILLENEUVE Pitch Publishing Ltd A2 Yeoman Gate HIS UNTOLD LIFE Yeoman Way Durrington FROM BERTHIERVILLE TO ZOLDER BN13 3QZ Email: [email protected] Web: www.pitchpublishing.co.uk First published by VerArtis Nonprofit Kft., Felsőmalom u. 3/2., H-7621 Pécs, Hungary 48 INTERVIEWS © Károly Méhes, 2014 BY KÁROLY MÉHES Károly Méhes has asserted his rights in accordance with the Copyright, Designs and Patents Act 1988 to be identified as the author of this work. All rights reserved. No part of this publication may be reproduced, stored in a retrieval system, or transmitted in any form or by any means, electronic, mechanical, photocopying, recording or otherwise, without the prior permission in writing of the publisher and the copyright owners, or as expressly permitted by law, or under terms agreed with the appropriate reprographics rights organization. Enquiries concerning reproduction outside the terms stated here should be sent to the publishers at the UK address printed on this page. The publisher makes no representation, express or implied, with regard to the accuracy of the information contained in this book and cannot accept any legal responsibility for any errors or omissions that may be made. A CIP catalogue record for this book is available from the British Library. 13-digit ISBN: 978-963-12-0717-0 Design and typesetting by Olner Pro Sport Media. Printed in India. Manufacturing managed by Jellyfish Print Solutions Ltd. CONTENTS -
2017 SPANISH GRAND PRIX 12-14 May 2017
2017 SPANISH GRAND PRIX 12-14 May 2017 fter four opening ‘flyaway’ races, the 2017 FIA Formula CIRCUIT DE BARCELONA-CATALUNYA AOne World Championship sees teams return to the sport’s Length of lap: traditional heartland for a predominantly European leg of the 4.655km season, beginning with the Spanish Grand Prix at the Circuit de Lap record: 1:21.670 (Kimi Räikkönen, Ferrari, Barcelona-Catalunya. 2008) A favoured test venue for Formula One, Barcelona’s circuit Start line/finish line offset: 0.126km is perhaps the one the sport’s teams know best, with a Total number of race laps: wealth of data on this season’s new cars having already been 66 accumulated during two pre-season tests in February and Total race distance: March. 307.104km Pitlane speed limits: However, as the first ‘close-to-home’ race of the season, the 80km/h in practice, qualifying, and Spanish Grand Prix is also the event to which many teams the race bring their first major update of the season and that, allied to the development that has already taken place, means the CIRCUIT NOTES cars that will race on Sunday are likely to be quite different ► The artificial grass has been to those that made their track debut here 10 weeks ago. removed on the exit of Turns 10, 13 and 15. At each, 50mm-high Conditions, too, are also likely be very different to those kerbs have been installed. experienced in the winter, with track temperatures set to be ► The artificial grass has been much higher than in testing. -
Red Bull Racing 1:23.619 1:21.773 1:20.981 2 S
2017 FIA Formula One™ World Championship FORMULA 1 GRAN PREMIO DE ESPAÑA PIRELLI 2017 12 – 14 May 2017 TABLE OF CONTENTS Time Schedule FORMULA 1 GRAN PREMIO DE ESPAÑA PIRELLI 2017 Welcome to Circuit de Barcelona-Catalunya The Circuit de Barcelona-Catalunya in detail Recommendations to get to Circuit de Barcelona-Catalunya Media Centre Operation Formula One Press Conference Schedule 2011/2016 Spanish Grand Prix results Media Contacts FORMULA 1 GRAN PREMIO DE ESPAÑA PIRELLI 2017 Officials 2017 Circuit de Barcelona-Catalunya Race Calendar 2017 FIA Formula One World Championship™ Calendar 2017 FIA Formula One World Championship™ Entry list 2017 FIA Formula One World Championship™ Classification Drivers and Teams Statistics 2017 FIA Formula One World Championship™: Australia, China, Bahrain and Russia Appendix The Formula One Spanish Grand Prix 1913-2016 Circuit general map, grandstands and giant screens Red Zones map TIME SCHEDULE THURSDAY, 11th May 13.00 Gates and Ticket Offices Opening 16.00 - 18.30 Formula One Pit Lane Walk (with 3-day or Sunday ticket) 18:00-18:30 Go Karting Karting driver demo meet & greet F1 Drivers FRIDAY, 12th May 08.00 Gates and Ticket Offices Opening 10.00 - 11.30 Formula One 1st Practice Session 12.00 - 12.45 FIA Formula 2 Practice Session 14.00 - 15.30 Formula One 2nd Practice Session 15.55 - 16.25 FIA Formula 2 Qualifying Session 16.45 - 17.30 GP3 Series Practice Session 17.50 - 18.35 Porsche Mobil 1 Supercup Practice Session SATURDAY, 13th May 08.00 Gates and Ticket Offices Opening 09.45 - 10.15 GP3 Series Qualifying