Copper Interconnects: Surface State Engineering to Facilitate Specular Electron Scattering
Total Page:16
File Type:pdf, Size:1020Kb
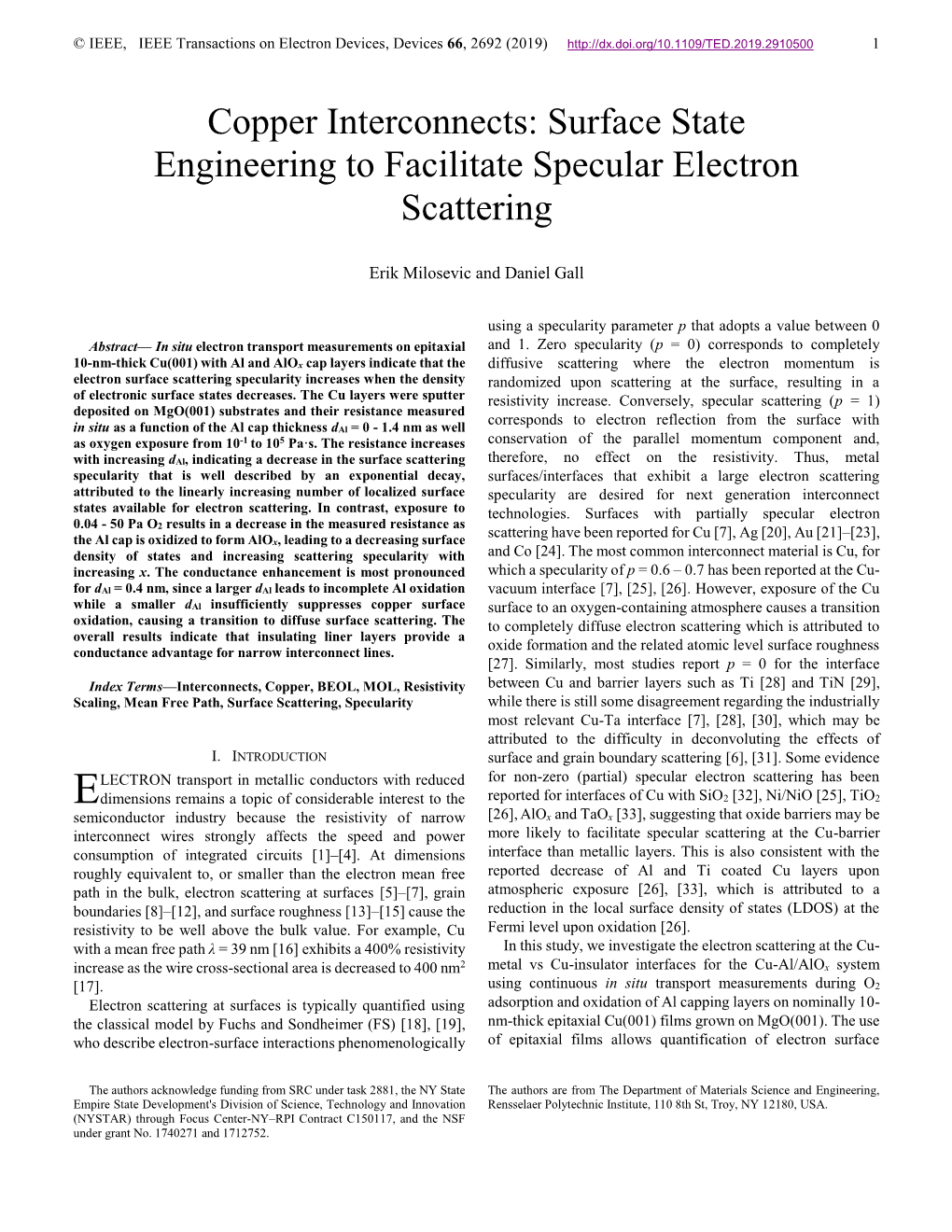
Load more
Recommended publications
-
Process Integration Issues of Low-Permittivity Dielectrics with Copper for High-Performance Interconnects
PROCESS INTEGRATION ISSUES OF LOW-PERMITTIVITY DIELECTRICS WITH COPPER FOR HIGH-PERFORMANCE INTERCONNECTS A DISSERTATION SUBMITTED TO THE DEPARTMENT OF ELECTRICAL ENGINEERING AND THE COMMITTEE ON GRADUATE STUDIES OF STANFORD UNIVERSITY IN PARTIAL FULFILLMENT OF THE REQUIREMENTS FOR THE DEGREE OF DOCTOR OF PHILOSOPHY Alvin Leng Sun Loke March 1999 © Copyright by Alvin Leng Sun Loke 1999 All Rights Reserved Prepared under the support of the Semiconductor Research Corporation, and Graduate Research Fellowships from the Natural Sciences and Engineering Research Council of Canada and Rockwell Semiconductor Systems Integrated Circuits Laboratory Center for Integrated Systems Stanford University, Stanford, CA 94305-4070 ii I certify that I have read this dissertation and that in my opinion it is fully adequate, in scope and quality, as a dissertation for the degree of Doctor of Philosophy. ___________________________ S. Simon Wong (Principal Advisor) I certify that I have read this dissertation and that in my opinion it is fully adequate, in scope and quality, as a dissertation for the degree of Doctor of Philosophy. ___________________________ Krishna C. Saraswat I certify that I have read this dissertation and that in my opinion it is fully adequate, in scope and quality, as a dissertation for the degree of Doctor of Philosophy. ___________________________ James S. Harris, Jr. Approved for the University Committee on Graduate Studies: ___________________________ Dean of Graduate Studies iii iv To Papa, Mummy, Alan, and Selene... v vi Abstract The relentless drive toward high-speed and high-density silicon-based integrated cir- cuits (IC’s) has necessitated significant advances in interconnect technology. In current process technologies, transistors are interconnected by multilevel aluminum and tungsten conductors encased in silicon dioxide (oxide) insulators. -
UNIVERSITY of CALIFORNIA, SAN DIEGO Optimization of the BEOL
UNIVERSITY OF CALIFORNIA, SAN DIEGO Optimization of the BEOL Interconnect Stack for Advanced Semiconductor Technology Nodes A thesis submitted in partial satisfaction of the requirements for the degree Master of Science in Electrical Engineering (Computer Engineering) by Pooja Pradeep Shah Committee in charge: Professor Andrew B. Kahng, Chair Professor Chung-Kuan Cheng Professor Bill Lin 2015 Copyright Pooja Pradeep Shah, 2015 All rights reserved. The thesis of Pooja Pradeep Shah is approved, and it is ac- ceptable in quality and form for publication on microfilm and electronically: Chair University of California, San Diego 2015 iii DEDICATION I dedicate this thesis to my loving husband Rakesh, my mother and my sister. This thesis would not have been possible without their encouragement and support. iv TABLE OF CONTENTS Signature Page . iii Dedication . iv Table of Contents . v List of Figures . vii List of Tables . ix Acknowledgments . x Vita ......................................... xi Abstract of the Thesis . xii Chapter 1 Introduction . 1 1.1 Motivation . 2 1.2 Our Contributions . 3 1.3 Limitations . 5 1.4 Outline of the Thesis . 5 Chapter 2 Previous Works . 7 2.1 Landmark Works . 8 2.2 Wire Optimization at System Level . 11 2.3 Wire Optimization Considering Layer Assignment . 13 2.4 Wire Sizing and Repeater Insertion . 14 2.5 Other Works . 16 2.6 Predictive Technology Models . 18 2.7 Reliability . 19 2.8 The ITRS BEOL Structure and Prediction . 20 2.9 Pitch Prediction . 22 2.10 Summary of Previous Works . 23 Chapter 3 Experiments for Interconnect Dimension Optimization and Vali- dation . 26 3.1 Our Flow . -
Preliminary Reliability Evaluation of Copper-Interconnect Metallization Technology
Preliminary Reliability Evaluation of Copper-Interconnect Metallization Technology Ashok K. Sharma NASA/Goddard Space Flight Center, Greenbelt, MD 20771 Alexander Teverovsky QSS Group, Inc., Goddard Space Flight Center, Greenbelt, MD 20771 1.0 Background The advantages of using copper for interconnection in microcircuits are mostly due to its lower resistance compared to the aluminum metallization. Copper-based metallization has specific resistance of less than 2 µΩ-cm compared to more than 3 µΩ-cm for aluminum metallization. In combination with a reduced susceptibility to electromigration failures, this enables designing of highly scaled devices with significantly reduced time delays. These features are mostly beneficial for high-performance microprocessors and fast static RAMs (FSRAM). In addition, copper interconnect process uses the dual damascene technology for deposition of copper, which can potentially reduce the manufacturing cost by eliminating some labor intensive steps of aluminum etching. This makes copper interconnect use quite attractive for semiconductor industry, and positions this technology as a standard interconnect process for the most high performance microcircuits in the future. Major problems with copper metallization are due to some specific physical/electrochemical properties. Copper does not create a passive oxide film (as aluminum does), has poor adhesion and high rate of diffusion through silicon and dielectric layers (organic and inorganic). This introduces new failure mechanisms such as poisoning of the P-N junctions, charge instability and formation of resistive shorts caused by copper electrochemical migration. The first on the market, copper-based FSRAM was manufactured by Motorola (the part is available since 1999). This part was used to gain experience with the copper-based interconnect design and technology, to analyze problems related to their evaluation and to obtain preliminary results of destructive physical analysis (DPA) of the parts. -
3-D Multilayer Copper Interconnects for High-Performance Monolithic Devices and Passives Ayad Ghannam, David Bourrier, Lamine Ourak, Christophe Viallon, Thierry Parra
3-D Multilayer Copper Interconnects for High-Performance Monolithic Devices and Passives Ayad Ghannam, David Bourrier, Lamine Ourak, Christophe Viallon, Thierry Parra To cite this version: Ayad Ghannam, David Bourrier, Lamine Ourak, Christophe Viallon, Thierry Parra. 3-D Multi- layer Copper Interconnects for High-Performance Monolithic Devices and Passives. Components, Packaging and Manufacturing Technology, 2013, 3 (6), pp.935-942. 10.1109/TCPMT.2013.2258073. hal-00920609 HAL Id: hal-00920609 https://hal.archives-ouvertes.fr/hal-00920609 Submitted on 19 Dec 2013 HAL is a multi-disciplinary open access L’archive ouverte pluridisciplinaire HAL, est archive for the deposit and dissemination of sci- destinée au dépôt et à la diffusion de documents entific research documents, whether they are pub- scientifiques de niveau recherche, publiés ou non, lished or not. The documents may come from émanant des établissements d’enseignement et de teaching and research institutions in France or recherche français ou étrangers, des laboratoires abroad, or from public or private research centers. publics ou privés. 1 3D Multi-layer Copper Interconnects for High Performance Monolithic Devices and Passives Ayad Ghannam, David Bourrier, Lamine Ourak, Christophe Viallon, and Thierry Parra suspended planar or 3D structures [9]-[12] are other Abstract—This paper presents a new and efficient low-cost technologies that enable direct above-IC integration of high-Q multi-layer 3D copper interconnect process for monolithic inductors. However, these approaches are either complex and devices and passives. It relies on the BPN and SU-8 photoresists, expensive or incompatible with standard silicon technologies associated with an optimized electroplating process to form which use low resistivity substrate. -
Chapter 2 Fundamentals of Electromigration
Chapter 2 Fundamentals of Electromigration Having shown in Chap. 1 that the future development of microelectronics will lead to more and more electromigration problems, let us now investigate in detail the actual low-level migration processes. A solid grounding in the physics of electro- migration (EM) and its specific effects on the interconnect will give us the knowledge to establish effective mitigation methods during the design of integrated circuits (ICs). We first explain the physical causes of EM (Sect. 2.1) and then present options to quantify the EM process (Sect. 2.2), which enable us to effectively characterize key aspects of the process and its effects. In Sect. 2.3, we introduce EM-influencing factors arising from the specific circuit technology, the environment, and the design. We then investigate detailed EM mechanisms with regard to circuit materials, frequencies, and mechanical stresses (Sect. 2.4). Since EM is closely related to other migration processes, such as thermal and stress migration that also occur in the conductors of electronic circuits, we examine their interdependencies (Sect. 2.5). IC designers must be especially aware of thermal and stress migration; both are introduced and described in their interaction with EM. Finally, Sect. 2.6 outlines the principles of a migration analysis through simu- lation. This honors the importance of finite element modeling (using the finite element method, FEM) in electromigration analysis and enables the reader to develop and apply similar modeling and simulation techniques. 2.1 Introduction The reliability of electronic systems is a central concern for developers, which is addressed by a variety of design measures that include, among others, the choice of materials to best suit an intended use. -
Electrochemical Atomic Layer Deposition of Metals for Applications in Semiconductor Interconnect Metallization
ELECTROCHEMICAL ATOMIC LAYER DEPOSITION OF METALS FOR APPLICATIONS IN SEMICONDUCTOR INTERCONNECT METALLIZATION by KAILASH VENKATRAMAN Submitted in partial fulfillment of the requirements for the degree of Doctor of Philosophy Thesis Advisor: Professor Rohan Akolkar Department of Chemical & Biomolecular Engineering CASE WESTERN RESERVE UNIVERSITY January, 2019 CASE WESTERN RESERVE UNIVERSITY SCHOOL OF GRADUATE STUDIES We hereby approve the dissertation of Kailash Venkatraman Candidate for the Doctor of Philosophy degree* (signed) Prof. Rohan Akolkar (chair of the committee) Prof. Uziel Landau Prof. Christine Duval Prof. Mark De Guire Date: October 22, 2018 *We also certify that written approval has been obtained for any proprietary material contained therein. 1 DEDICATION Dedicated to my grandparents, Late Shri. S. Krishnaswamy and Smt. S. Sundaresan. 2 TABLE OF CONTENTS DEDICATION .....................................................................................................................2 LIST OF TABLES ...............................................................................................................6 LIST OF FIGURES .............................................................................................................7 ACKNOWLEDGEMENTS ...............................................................................................13 LIST OF SYMBOLS .........................................................................................................14 CHAPTER 1. Introduction ........................................................................................... -
"Process Integration Issues of Low-Permittivity Dielectrics with Copper for High-Performance Interconnects", Chapter
PROCESS INTEGRATION ISSUES OF LOW-PERMITTIVITY DIELECTRICS WITH COPPER FOR HIGH-PERFORMANCE INTERCONNECTS A DISSERTATION SUBMITTED TO THE DEPARTMENT OF ELECTRICAL ENGINEERING AND THE COMMITTEE ON GRADUATE STUDIES OF STANFORD UNIVERSITY IN PARTIAL FULFILLMENT OF THE REQUIREMENTS FOR THE DEGREE OF Ph.D. CHAPTER 2 Alvin Leng Sun Loke March 1999 Chapter 2 Review of Interconnect Integration The investigations to be presented in subsequent chapters assume a basic command of interconnect process technologies. This chapter provides an overview of interconnect integration, emphasizing key features in both conventional Al and Damascene Cu technol- ogies. It is hoped that with this review, the less familiar reader will have acquired some relevant background information for comprehending the context of the work to follow. In conventional silicon IC technologies, the interconnects are incorporated after front- end processing. Frontend processing refers to the sequence of fabrication steps, typically at very high temperatures (700−1100°C), that form the MOS transistors in the active regions, the pockets of thick isolation in the field regions that separate adjacent transistors, and the silicidation of the transistor terminals for low-resistance contacts. The reader is directed to [38]−[40] for a representative flavor of manufacturable advanced frontend tech- nologies. The backend, referring to the interconnection of transistors, is subsequently formed by contacting the transistor terminals and then vertically stacking alternating layers of metal wires and vias encased in dielectric. Backend process temperatures typically do not exceed 450°C to avoid melting of the metals and to control stress. 17 Chapter 2: Review of Interconnect Integration 2.1 Conventional Technology The state-of-the-art 0.25-µm backend, shown in Figure 2-1, is revisited to illustrate the integration of conventional Al metallization. -
Exploration of Carbon Nanotube and Copper-Carbon Nanotube Composite for Next Generation On-Chip Energy Efficient Interconnect Applications Jie Liang
Exploration of carbon nanotube and copper-carbon nanotube composite for next generation on-chip energy efficient interconnect applications Jie Liang To cite this version: Jie Liang. Exploration of carbon nanotube and copper-carbon nanotube composite for next genera- tion on-chip energy efficient interconnect applications. Micro and nanotechnologies/Microelectronics. Université Montpellier, 2019. English. NNT : 2019MONTS022. tel-02378303 HAL Id: tel-02378303 https://tel.archives-ouvertes.fr/tel-02378303 Submitted on 25 Nov 2019 HAL is a multi-disciplinary open access L’archive ouverte pluridisciplinaire HAL, est archive for the deposit and dissemination of sci- destinée au dépôt et à la diffusion de documents entific research documents, whether they are pub- scientifiques de niveau recherche, publiés ou non, lished or not. The documents may come from émanant des établissements d’enseignement et de teaching and research institutions in France or recherche français ou étrangers, des laboratoires abroad, or from public or private research centers. publics ou privés. TH ESE` POUR OBTENIR LE GRADE DE DOCTEUR DE L’UNIVERSIT E´ DE MONTPELLIER En Micro´electronique Ecole´ doctorale : Information, Structures, Syst`emes Unit´ede recherche LIRMM Exploration of Carbon Nanotube and Copper-Carbon Nanotube Composite for Next Generation On-chip Energy Efficient Interconnect Applications Pr´esent´ee par Jie LIANG le 17 Juin 2019 Sous la direction de Aida TODRI-SANIAL Devant le jury compos´ede Pascal Nouet Professeur LIRMM, UMR CNRS / Universit´ede Montpellier Pr´esident du Jury Aida Todri-Sanial Directrice de Recherche LIRMM, CNRS / Universit´ede Montpellier Directricedeth`ese Ian O’Connor Professeur Ecole´ Centrale de Lyon Rapporteur Jacques-Olivier Klein Professeur Universit´eParis-Sud Rapporteur Cristell Maneux Professeur Universit´ede Bordeaux Examinatrice Jean Dijon Directeur de Recherche CEA-LITEN, Universit´ede Grenoble Invit´e I dedicate my dissertation work to my family and many friends. -
Interconnect Scaling.Pdf
EE 311 Notes/Prof Saraswat Scaling of Interconnections Scaling of Minimum Feature size and Chip Area 104 10 pr oduction 103 1 logic de velopment 102 0.1 memor y 1 0.01 10 1970 1980 1990 2000 2010 1970 1980 1990 2000 2010 Year Year Ref. A. Loke, PhD Thesis, Stanford Univ. 1999 Once the active devices and regions are fabricated they must be electrically connected to each other to make circuits. They must also be connected to the outside world through their inputs and outputs on bonding pads. Making these connections is the job of contacts, vias and interconnects. Separating the interconnects from each other is the job of dielectric layers. All of these components are part of the “metallization” or “backend” structure. The figure below is a schematic diagram showing these components in a typical integrated circuit structure. In recent times the relative importance of the backend structures has greatly increased, and will likely to continue as integrated circuit technology progresses. EE 311 / Saraswat Interconnect Scaling Fig. 2 Schematic cross-section of backend structure, showing interconnects, contacts and vias, separated by dielectric layers. Interconnects can either be global or local. In general, local interconnects are the first, or lowest, level of interconnects. They usually connect gates, sources and drains in MOS technology, and emitters, bases, and collectors in bipolar technology. In MOS technology a local interconnect, polycrystalline silicon, also serves as the gate electrode material. Silicided gates and silicided source/drain regions also act as local interconnects. In addition, TiN, a by-product of a silicided gate process, can be used as a local interconnect, and W is sometimes used as well. -
Copper–Titanium Thin Film Interaction
Microelectronic Engineering 76 (2004) 153–159 www.elsevier.com/locate/mee Copper–titanium thin film interaction L. Castoldi a, G. Visalli a, S. Morin a, P. Ferrari a, S. Alberici b, G. Ottaviani c,d,*, F. Corni c,d, R. Tonini c,d, C. Nobili c,d, M. Bersani e a ST Microelectronis, Cornaredo, Milano, Italy b Central R&D, Physics and Material Characterization Laboratory, ST Microelectronis, Via Olivetti 2, I-20041 Agrate Brianza, Milano, Italy c Dipartimento di Fisica, via Campi 213/a 41100 Modena, Italy d MASEM, Materiali Avanzati per Sistemi, lElettroMeccanici, via Vivaldi 70, 41100 Modena, Italy e ITC-irst, via Sommarive 18, 38050 Povo, Trento, Italy Available online 12 August 2004 Abstract Interaction between 5 lm thick copper and 50 nm thin titanium films was investigated as a function of annealing temperature and time using MeV 4He+ Rutherford backscattering, X-ray diffraction and dynamic Secondary Ion Mass Spectrometry. Samples were made by depositing 10 nm of titanium on a PECVD silicon oxynitride, followed by 50 nm of titanium nitride and 50 nm of titanium in the said order. In the same system 100 nm of copper were subsequently sputtered; finally 5 lm of copper were grown by electroplating. This complex structure was chosen in order to inves- tigate the possibility of using copper interconnects also in power devices. To investigate the composition and growth of Ti–Cu compound on the buried interface, it was necessary to develop a special procedure. The results of the investiga- tion show the formation of a laterally non-uniform layer of TiCu4, which is presumably preceded by the formation of CuTi. -
The Metal Resistivity Increase Is an Emerging Concern As the ITRS Projected Metal Widths Can Be Smaller Than the Mean Free Path
Proceedings of the 22nd Advanced Metallization Conference, Colorado Springs, CO, September 27-29, 2005. Interconnect Modeling and Analysis in the Nanometer Era: Cu and Beyond Kaustav Banerjee1, Sungjun Im2 and Navin Srivastava1 1Department of Electrical and Computer Engineering, University of California, Santa Barbara, CA 93106, U.S.A. 2Department of Materials Science and Engineering, Stanford University, Stanford, CA 94305, U.S.A. ABSTRACT This paper highlights key emerging issues in the domain of interconnect modeling and analysis. The implications of various nanoscale effects on VLSI interconnect performance, reliability, power dissipation and parasitic extraction are also presented. Finally, promising new technologies are outlined which have the potential to meet these interconnect challenges in the nanometer era. INTRODUCTION As VLSI technology has progressed to pack smaller, faster and increasing number of transistors (doubling every 1.8 years as per Moore’s Law) on a single chip than ever before, the demands from wires that connect these devices have increased tremendously. In fact, Copper/Low-k interconnect technologies for sub-100 nm CMOS ICs are impacting system performance through increased power dissipation, signal delay, and cross-talk. With clock frequencies increasing into the GHz regime, the parasitic resistance, capacitance and inductance associated with these wires often lead to performance bottlenecks which have led the semiconductor and the electronic design automation (EDA) industries to adopt several technological innovations. Furthermore, prevalent high chip temperatures (aggravated by large power dissipation of nanometer scale ICs) and increasing current densities in wires make electromigration in copper a constant threat to VLSI circuits. Moreover, variability issues at the nanometer scale are evident in interconnects as they are in devices. -
Advanced Copper Interconnects Application As an Adhesion
Chemical Vapor Deposition of Cobalt Nitride and its Application as an Adhesion-Enhancing Layer for Advanced Copper Interconnects Harish B. Bhandari, Jing Yang, Hoon Kim, Youbo Lin, Roy G. Gordon, Qing Min Wang, Jean-Sébastien M. Lehn, Huazhi Li and Deo Shenai ECS J. Solid State Sci. Technol. 2012, Volume 1, Issue 5, Pages N79-N84. doi: 10.1149/2.005205jss Email alerting Receive free email alerts when new articles cite this article - sign up service in the box at the top right corner of the article or click here To subscribe to ECS Journal of Solid State Science and Technology go to: http://jss.ecsdl.org/subscriptions © 2012 The Electrochemical Society ECS Journal of Solid State Science and Technology, 1 (5) N79-N84 (2012) N79 2162-8769/2012/1(5)/N79/6/$28.00 © The Electrochemical Society Chemical Vapor Deposition of Cobalt Nitride and its Application as an Adhesion-Enhancing Layer for Advanced Copper Interconnects Harish B. Bhandari,a,b Jing Yang,a Hoon Kim,a,c Youbo Lin,a,d Roy G. Gordon,a,∗,z Qing Min Wang,e Jean-Sebastien´ M. Lehn,e Huazhi Li,e and Deo Shenaie aHarvard University, Cambridge, Massachusetts, 02138, USA bRMD - Radiation Monitoring Devices, Inc, Watertown, Massachusetts, 02472, USA cAlbany NanoTech, Globalfoundries, Albany, New York 12203, USA dIBM East Fishkill, Globalfoundries, Hopewell Junction, New York 12533, USA eDow Electronic Materials, The Dow Chemical Company, North Andover, Massachusetts 01845, USA An interlayer of face centered cubic (fcc) Co4N has demonstrated significant improvements in adhesion between copper and diffusion barrier layers. This fcc phase of Co4N was prepared by chemical vapor deposition (CVD) using bis(N-tert-butyl-N -ethyl- ◦ propionamidinato)cobalt(II) and a reactant mixture of NH3 and H2 at substrate temperatures from 100 to 180 C.