3D Printed Micro-Channel Heat Sink Design Considerations
Total Page:16
File Type:pdf, Size:1020Kb
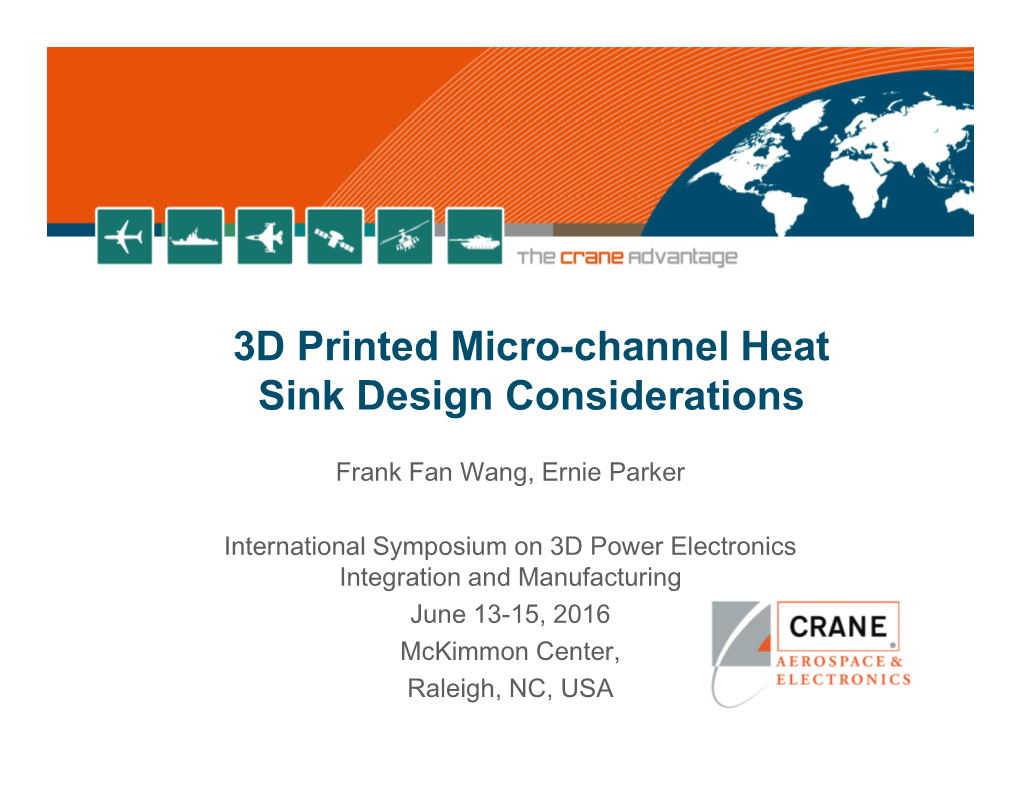
Load more
Recommended publications
-
7 Families of Additive Manufacturing According to ASTM F2792 Standards
7 Families of Additive Manufacturing According to ASTM F2792 Standards VAT Powder Bed Binder Material Photopolymerization Fusion (PBF) Jetting Jetting Alternative Names: Alternative Names: Alternative Names: Alternative Names: SLA™- Stereolithography Apparatus SLS™- Selective Laser Sintering; DMLS™- 3DP™- 3D Printing Polyjet™ DLP™- Digital Light Processing Direct Metal Laser Sintering; SLM™- Selective ExOne SCP™- Smooth Curvatures Printing 3SP™- Scan, Spin, and Selectively Photocure Laser Melting: EBM™- Electron Beam Melting; Voxeljet MJM - Multi-Jet Modeling CLIP™ – Continuous Liquid Interface Production SHS™- Selective Heat Sintering; Projet™ MJF™- Multi-Jet Fusion Description: Description: Description: Description: A vat of liquid photopolymer resin is cured Powdered materials is selectively consolidated Liquid bonding agents are selectively applied Droplets of material are deposited layer by layer through selective exposure to light (via a laser by melting it together using a heat source onto thin layers of powdered material to build up to make parts. Common varieties include jetting or projector) which then initiates polymerization such as a laser or electron beam. The powder parts layer by layer. The binders include organic a photcurable resin and curing it with UV light, and converts the exposed areas to a solid part. surrounding the consolidated part acts and inorganic materials. Metal or ceramic as well as jetting thermally molten materials that assupport material for overhanging features. powdered parts are typically fired in -
The Processing of Binder Jet Multi-Material 3D Printing to Improve Upon Material Properties
Clemson University TigerPrints All Theses Theses December 2019 The Processing of Binder Jet Multi-Material 3D Printing to Improve upon Material Properties Sara Mohammed Damas Clemson University, [email protected] Follow this and additional works at: https://tigerprints.clemson.edu/all_theses Recommended Citation Damas, Sara Mohammed, "The Processing of Binder Jet Multi-Material 3D Printing to Improve upon Material Properties" (2019). All Theses. 3224. https://tigerprints.clemson.edu/all_theses/3224 This Thesis is brought to you for free and open access by the Theses at TigerPrints. It has been accepted for inclusion in All Theses by an authorized administrator of TigerPrints. For more information, please contact [email protected]. THE PROCESSING OF BINDER JET MULTI-MATERIAL 3D PRINTING TO IMPROVE UPON MATERIAL PROPERTIES A Thesis Presented to the Graduate School of Clemson University In Partial Fulfillment of the Requirements for the Degree Master of Science Mechanical Engineering by Sara M. Damas December 2019 Accepted by: Dr. Cameron J. Turner, Committee Chair Dr. Gang Li Dr. Suyi Li ABSTRACT Additive manufacturing methods are becoming more prominent in the world of design and manufacturing due to their reduction of material waste versus traditional machining methods such as milling. As their demand rises, a need to improve their methodologies and produce higher quality products arises. The technology to 3D print has been in around since the 1970’s, and thanks to Scott Crump as of 1989, it is possible to 3D print in layers to obtain a solid component. In today’s present time, we now can multi- material 3D print. However, even though we have the technology for multi-material 3D printing, standards in this field are severely lacking. -
Numerical Modeling and Simulation of Selective Laser Sintering in Polymer Powder Bed Xin Liu
Numerical modeling and simulation of selective laser sintering in polymer powder bed Xin Liu To cite this version: Xin Liu. Numerical modeling and simulation of selective laser sintering in polymer powder bed. Thermics [physics.class-ph]. Université de Lyon, 2017. English. NNT : 2017LYSEI012. tel-01920677 HAL Id: tel-01920677 https://tel.archives-ouvertes.fr/tel-01920677 Submitted on 13 Nov 2018 HAL is a multi-disciplinary open access L’archive ouverte pluridisciplinaire HAL, est archive for the deposit and dissemination of sci- destinée au dépôt et à la diffusion de documents entific research documents, whether they are pub- scientifiques de niveau recherche, publiés ou non, lished or not. The documents may come from émanant des établissements d’enseignement et de teaching and research institutions in France or recherche français ou étrangers, des laboratoires abroad, or from public or private research centers. publics ou privés. N°d’ordre NNT : 2017LYSEI012 THESE de DOCTORAT DE L’UNIVERSITE DE LYON opérée au sein de (Institut National des Sciences Appliquées de Lyon) Ecole Doctorale N° ED162 (MEGA de Lyon) Spécialité/ discipline de doctorat : Thermique et Energétique Soutenue à huis clos le 28/02/2017, par : Xin LIU Numerical Modeling and Simulation of Selective Laser Sintering in Polymer Powder bed Devant le jury composé de : BARRES Claire Maître de conférences HDR INSA-Lyon Examinateur BERGHEAU Jean-Michel Professeur des Universités ENISE-St.Etienn Examinateur REGNIER Gilles Professeur des Universités ENSAM-Paris Rapporteur SCHMIDT Fabrice Professeur des Universités MINES-Albi Rapporteur BOUTAOUS M'hamed Maître de conférences HDR INSA-Lyon Directeur de thèse XIN Shihe Professeur des Universités INSA-Lyon Co-directeur de thèse 1 Cette thèse est accessible à l'adresse : http://theses.insa-lyon.fr/publication/2017LYSEI012/these.pdf © [X. -
Additive Manufacturing Is Changing the Way Manufacturing
Additive Manufacturing is changing the way manufacturing gets done, but what is it? How does it work? What are the benefits and limitations? What industries are benefiting the most? ITAMCO answers these questions and examines how 3D printing compares to traditional manufacturing. GUIDE TO ADDITIVE MANUFACTURING TABLE OF CONTENTS WHAT IS ADDITIVE MANUFACTURING?. 3 ADDITIVE MANUFACTURING PROCESSES . .4 MATERIAL TYPES. 9 ADDITIVE MANUFACTURING PROCESSES INFOGRAPHIC . 10 BENEFITS . 12 LIMITATIONS . .12 APPLICATIONS. .14 ADDITIVE MANUFACTURING VERSUS TRADITIONAL MANUFACTURING . 15 2 WHAT IS ADDITIVE MANUFACTURING? Additive manufacturing (AM) or 3D printing is layer-by-layer GROWING NEED FOR AM fabrication of three-dimensional (3D) objects. AM now meets a broad range of needs throughout many industries including: Traditional manufacturing is a subtractive process in which material is removed to produce the final shape. Examples include milling, cutting, • Visualization tool or parts in design turning, drilling, boring, etc. AM offers many advantages in the production • Means to create customized products of parts, but the key benefits are unparalleled design freedom, less hard • Industrial tooling tooling and assembly, and the ability to manufacture single or multiple • Small runs of production parts components from a wide range of materials. • Full-strength, rapid prototyping Surprisingly this seemingly modern technology has been around for nearly • Test complex geometries 40 years. In 1981 automatic methods for producing 3D models were detailed by Hideo Kodama. His published paper described techniques for forming 3D plastic models using ultraviolet (UV) cured layers of photopolymer material. In 1984 Chuck Hull filed a patent coining the term stereolithography, a technique utilizing UV light lasers and a bed or vat or photopolymer resin to produce 3D objects. -
A 3D Printing Handbook Table of Contents
EBOOK After the basics: a 3D printing handbook Table of Contents Introduction 3 When starting a 3D print lab, material choices matter 4 The 3D printing career matrix 10 Making desktop 3D printing more user-friendly 18 3D printing file format cage match: AMF vs. 3MF 24 Specialty filaments for 3D printing are on the rise 32 3D Printing Multi-Color Madness 41 Introduction Welcome to the first volume of 3D printing for intermediates. Welcome to all of you who kind of know what you’re doing. You are among friends here. When it comes to 3D printing, there is a giant gap between learning material for beginners and content meant for the extremely experienced. We’re here to help. We’ve set out to save you hours of googling and forum searching to bring you the intermediate 3D printing topics you’re craving - like when to use specialty filaments and tips for starting a print lab. As always, feel free to share your feedback. Are these topics useful? What should we cover in volume two? Let us know. Dennis Bella is a freelance writer with diverse range of experience in 3D printing, software, and technology. In his former life, he was a 15 year veteran in IT security sales, CAD quality assurance, and technology public relations. While offering his own 3D printed items, Dennis works with clients to create a variety of designs, from dimensioned parts to artistic sculptures. He is a graduate of Northeastern University in Mechanical Engineering Technology and received certification in Technical Communications from University of Massachusetts at Amherst. -
3D PRINTING Introduction Additive Manufacturing Or 3D Printing Is a Process of Making Three Dimensional Solid Objects from a Digital Model
3D PRINTING Introduction Additive manufacturing or 3D printing is a process of making three dimensional solid objects from a digital model. 3D printing is achieved using additive processes, where an object is created by laying down successive layers of material. 3D printing is considered distinct from traditional machining techniques (subtractive processes) which mostly rely on the removal of material by drilling, cutting etc. A 3D Printer A hyperboloid object print (made of PLA) using a RepRap “Prusa Mendel” 3D printer for molten polymer deposition. 3D printing is usually performed by a materials printer using digital technology. Since the start of the twenty-first century there has been a large growth in the sales of these machines, and their price dropped substantially. The technology is used in the fields of jewellery, footwear, industrial design, architecture, engineering and construction (AEC), automotive, aerospace, dental and medical industries, education, geographic information systems, civil engineering, and many others. History Early examples of 3D printing occurred in the 1980s, though the printers then were large, expensive and highly limited in what they could produce. • The term "3D printing" was coined at MIT in 1995 when then graduate students Jim Bredt and Tim Anderson modified an inkjet printer to extrude a binding solution onto a bed of powder, rather than ink onto paper. The ensuing patent led to the creation of modern 3D printing companies Z Corporation (founded by Bredt and Anderson) and ExOne. • SLS was developed and patented by Dr. Carl Deckard at the University of Texas at Austin in the mid-1980s, under sponsorship of DARPA. -
3D Printing 3D Printing Has Fallen from the Spotlight Somewhat, but That Doesn’T Mean Its Revolutionary Potential Has Faded
Edison Explains 3D printing 3D printing has fallen from the spotlight somewhat, but that doesn’t mean its revolutionary potential has faded. print heads, in a similar way to an inkjet printer, but in layers that harden on contact with UV light. What is the state of the 3D MJ uses plastics and some rubber-like and fully printing market? transparent materials as its feedstock. Following a surge in public What about 3D printing in metal? excitement in the early 2010s, the 3D printing market peaked in So far little has been said of technologies best suited for terms of consumer interest after a heavy price point and printing in metal rather than plastic polymers. It is here that heavier machines dissuaded most buyers from the powder bed fusion comes into its own. market. Used for printing metal, plastics and other materials, the That said, the use of 3D printing has continued to expand technology turns a bed of powdered material into a 3D in its core manufacturing-related fields, driven by a drift object by selectively fusing sections through the from plastic to metal feedstock, faster printing speeds and application of heat. To achieve this in plastic, selective maturing software/design platforms. In addition, with an laser sintering (SLS) uses lasers to heat powder increasingly advanced set of technologies to choose from, selectively and fuse it. 3D printing is still on the minds of many manufacturers. For metal, the same principle is used in direct metal laser How do 3D printers work? sintering (DMLS), selective laser melting (SLM) and selective heat sintering (SHS), with some slight variations. -
Concrete Casting Moulds with 3D-Printing Tech- Nology
Saimaa University of Applied Sciences Technology, Lappeenranta Mechanical Engineering and Production Technology Junjie He Concrete casting moulds with 3D-printing tech- nology Thesis 2019 Abstract Junjie He Concrete casting moulds with 3D-printing technology, 37 pages Saimaa University of Applied Sciences Technology Lappeenranta Mechanical Engineering and Production Technology Thesis 2019 Instructor: Mikko Ruotsalainen, Saimaa University of Applied Sciences This thesis aims to test the feasibility of adopting 3D printing technology in con- crete moulds manufacturing and formulate the advantages and limitations of 3D printing technology in casting mould making. This study was carried out in the laboratory of Saimaa University of Applied Sci- ences by conducting an experimental project. The background information was gathered from the Internet and the literatures in Lappeenranta Academic Library. In this study, the different additive manufacturing techniques and the testing equipment were introduced, then the procedure and results of the experimental project were elaborated and discussed, finally the conclusions of this study and the niche market of 3D printing casting moulds were summarized. This study is just a preliminary research to explore the possibilities of adopting 3D-printing technology in the manufacturing innovation. Further study is required to exploit the full potential of this technology. Keywords: 3D printing technology, concrete casting moulds, feasibility 2 Table of contents 1 Introduction ................................................................................................. -
991022180953403411.Pdf
Copyright Undertaking This thesis is protected by copyright, with all rights reserved. By reading and using the thesis, the reader understands and agrees to the following terms: 1. The reader will abide by the rules and legal ordinances governing copyright regarding the use of the thesis. 2. The reader will use the thesis for the purpose of research or private study only and not for distribution or further reproduction or any other purpose. 3. The reader agrees to indemnify and hold the University harmless from and against any loss, damage, cost, liability or expenses arising from copyright infringement or unauthorized usage. IMPORTANT If you have reasons to believe that any materials in this thesis are deemed not suitable to be distributed in this form, or a copyright owner having difficulty with the material being included in our database, please contact [email protected] providing details. The Library will look into your claim and consider taking remedial action upon receipt of the written requests. Pao Yue-kong Library, The Hong Kong Polytechnic University, Hung Hom, Kowloon, Hong Kong http://www.lib.polyu.edu.hk CREATION OF 3D DIGITAL PRINTED FASHION PROTOTYPE WITH INNOVATIVE SURFACE TEXTURE CHAN HIU SEN PhD The Hong Kong Polytechnic University 2019 The Hong Kong Polytechnic University Institute of Textiles and Clothing CREATION OF 3D DIGITAL PRINTED FASHION PROTOTYPE WITH INNOVATIVE SURFACE TEXTURE CHAN HIU SEN A thesis submitted in partial fulfillment of the requirements for the degree of Doctor of Philosophy June 2018 CERTIFICATE OF ORIGINALITY I hereby declare that this thesis is my own work and that, to the best of my knowledge and belief, it reproduces no material previously published or written, nor material that has been accepted for the award of any other degree or diploma, except where due acknowledgement has been made in the text. -
Der CAMSIZER XT
Creative Optimization with Additive Manufacturing Webinar - Additive Manufacturing with Particle Size and Shape Analysis Many Additive Manufacturing (also called 3D printing) techniques such as selective laser sintering (SLS), selective laser melting (SLM) and electro-beam melting (EBM) use metal particle powders as a raw material (Aluminum, Titanium, Steel, Nickel, Tungsten and many Alloys). The particle size, size distribution and shape have a strong effect on the manufacturing result. Therefore it is important for manufacturers and suppliers to control the particle size and shape of their powders used in this process. In order to control particle size and shape these parameters must be measured. We discuss how to use the CAMSIZER technology to improve additive manufacturing results by monitoring the incoming particles. Value of Dynamic Image Analysis in 3D additive manufacturing How does Dynamic Image Analysis work? Why two cameras can control and monitor dust and oversize? Check the manufacturing and production of Additive Manufacturing powders Check the incoming raw material and the recycled powder for reuse 1 CAMSIZER XT & CAMSIZER X2 Additive Manufacturing December 5th of 2017 Julie Chen HORIBA Scientific Gert Beckmann Retsch Technology GmbH Processes Classification Technology Description Materials Binder Jetting 3D Printing Creates objects by depositing a Metal, Polymer, Ink-Jetting binding agent to join powdered Ceramic S-Print material. M-Print Direct Energy Direct Metal Deposition Builds parts by using focused Metal powder, Deposition Laser Deposition thermal energy to fuse materials as Metal wire Laser Consolidation they are deposited on a substrate. Electron Beam Direct Melting Material Fused Deposition Modelling Creates objects by dispensing Polymer Extrusion material through a nozzle to build layers. -
To Read This Handbook
Advanced Additive Manufacturing Handbook Prepared by i Deliverable Datasheet Project Acronym: INEX-ADAM Grant Agreement number: 810708 Project title: Increasing Excellence on Advanced Additive Manufacturing Funding scheme: Horizon2020 Twinning Call: H2020-WIDESPREAD-05-2017-Twinning Type of action: CSA Start date of project: 1st September 2018 Duration: 36 months Project website: www.inex-adam.eu Deliverable number: D3.2 – V1.0 Deliverable title: Advanced Additive Manufacturing Handbook Work package: WP3- Raising Knowledge and Excellence on AM Lead beneficiary: UNIZAG FSB/LTH Dissemination level: Public Deliverable summary This handbook is a summary of the training material delivered to UNIZAG FSB by MUL (11-3- 2019 – 5-4-2019), UBRUN (3-6-2019 – 12-6-2019), AIDIMME (23-9-2019 – 4-10-2019) and LTH (4-11-2019 – 15-11-2019) and strategic research topics of all INEX-ADAM project partners. ii Contents Deliverable Datasheet ii Contents iii List of figures vii List of tables xiii Introduction 1 1.1. INEX-ADAM 1 Introduction to Additive Manufacturing 2 2.1. What is Additive Manufacturing 2 2.2. Why do we need Additive Manufacturing 3 2.3. Additive Manufacturing Classification 6 2.4. Vat polymerization 7 2.4.1. Stereolitography SLA 9 2.4.2. Digital Light Processing DLP 11 2.5. Material jetting 12 2.5.1. PolyJet 12 2.6. Binder jetting 16 2.6.1. 3D printing 3DP 17 2.7. Powder Bed Fusion Technologies 20 2.7.1. Introduction to Powder Bed Fusion (PBF) Technologies 20 2.7.2. Electron Beam Technology 22 2.7.3. Laser Melting Technology 25 2.7.4. -
Diseño Y Fabricación De Impresora 3D Basada En Robot Paralelo Tipo Delta – Ropar3d
TRABAJO FIN DE GRADO UNIVERSIDAD DE ALMERIA ESCUELATRABAJO FINSUPERIOR DE GRADO DE INGENIERÍA GRADO EN INGENIERÍA MECÁNICA “Diseño y fabricación de impresora 3D Diseñobasada eny robot paralelo tipo Delta – fabricaciónRoPar3D” de impresora 3D basada en robot paralelo tipo Delta – RoPar3D [Subtítulo del documento] UNIVERSIDAD DE ALMERÍA Curso 2019/2020 DiegoAlumno/a Miguel Parra: Martínez [Fecha] Diego Miguel Parra Martínez Director/es: Manuel Ángel Aguilar Torres Fernando José Aguilar Torres Diseño y fabricación de impresora 3D basada en robot paralelo tipo Delta – RoPar3D Autor Diego Miguel Parra Martínez Director Codirector Aguilar Torres, Manuel Ángel Aguilar Torres, Fernando José El presente Trabajo de Fin de Grado de la Escuela Superior de Ingeniería de la Universidad de Almería (UAL) se distribuye con licencia Creative Commons Reconocimiento-No comercial-Compartir Igual 4.0 International CC BY-NC-SA https://creativecommons.org/licenses/by-nc-sa/4.0/ A mis padres por su apoyo incondicional durante estos años ESCUELA SUPERIOR DE INGENIERÍA Contenido Agradecimientos 7 Relación de Figuras 8 Relación de Tablas 11 Glosario 12 Abreviaturas, Siglas y Acrónimos 16 1. Interés y objetivos 17 1.1. Introducción 17 1.2. Motivación personal 18 1.3. Justificación 19 1.4. Objetivos 20 2. MARCO TEÓRICO (I): ESTADO ACTUAL DE LA IMPRESIÓN 3D FDM 21 2.1 Definición y origen. 21 2.2 Prototipado Rápido vs Fabricación Aditiva. 22 2.3 Historia y evolución. 23 2.4 Movimiento RepRap, Movimiento Maker y DIY. 26 2.5 Ventajas de la impresión 3D. 27 2.6 Impresión 3D industrial vs. Impresión 3D doméstica. 30 2.7 Tecnologías de impresión 3D.