Charging Process Analysis of an Opposed-Piston Two-Stroke Aircraft Diesel Engine
Total Page:16
File Type:pdf, Size:1020Kb
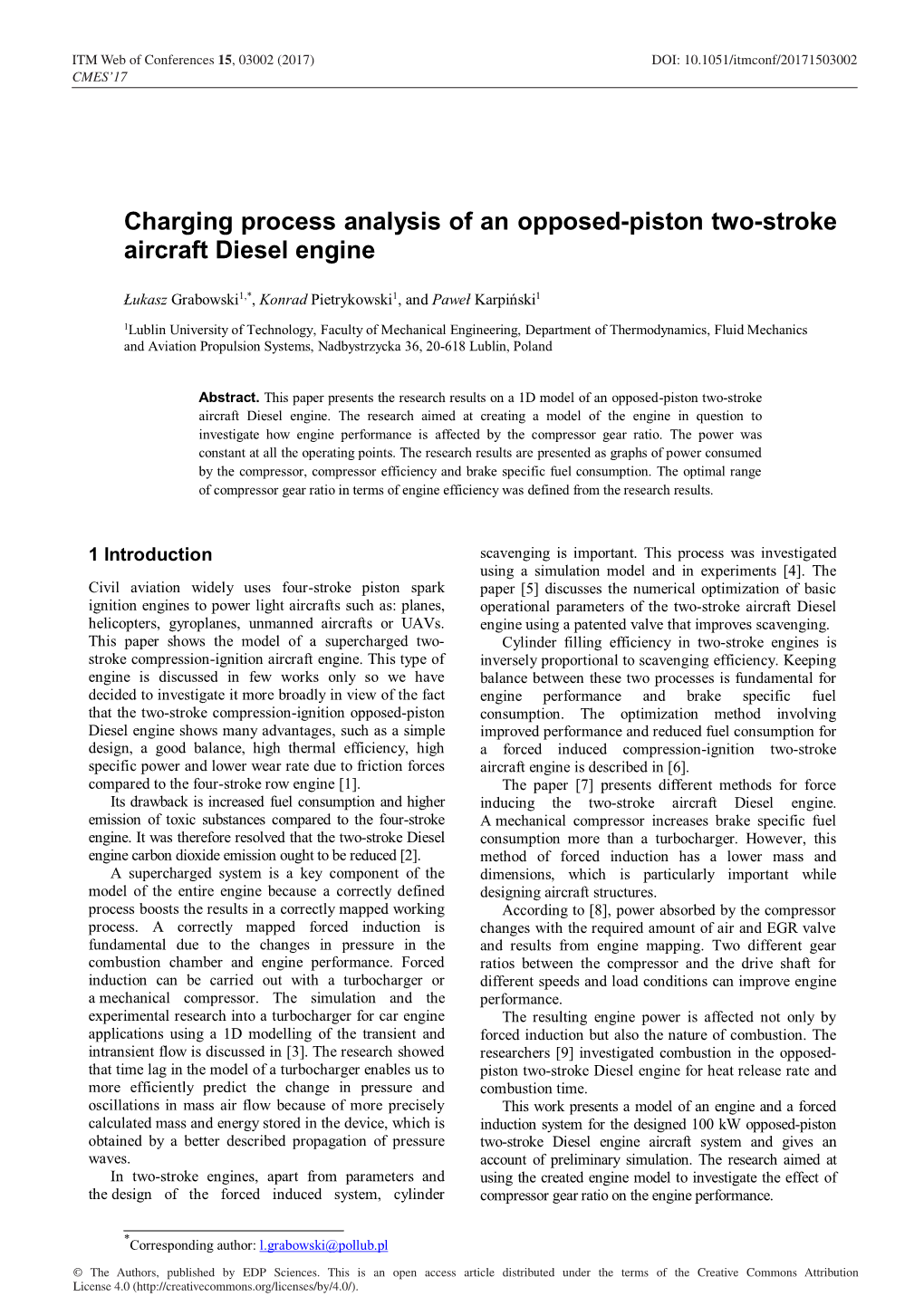
Load more
Recommended publications
-
General Electric Company Turbofan Engines
50320 Federal Register / Vol. 78, No. 160 / Monday, August 19, 2013 / Rules and Regulations 11. Markings and Placards— Vibration levels imposed on the DEPARTMENT OF TRANSPORTATION Miscellaneous Markings and Placards— airframe can be mitigated to an Fuel, and Oil, Filler Openings acceptable level by utilization of Federal Aviation Administration (Compliance With § 23.1557(c)(1)(ii) isolators, damper clutches, and similar Requirements) provisions so that unacceptable 14 CFR Part 39 Instead of compliance with vibration levels are not imposed on the [Docket No. FAA–2013–0195; Directorate § 23.1557(c)(1)(i), the applicant must previously certificated structure. Identifier 2013–NE–08–AD; Amendment 39– comply with the following: 14. Powerplant Installation—One 17553; AD 2013–16–15] Fuel filler openings must be marked Cylinder Inoperative RIN 2120–AA64 at or near the filler cover with— Tests or analysis, or a combination of For diesel engine-powered Airworthiness Directives; General methods, must show that the airframe airplanes— Electric Company Turbofan Engines can withstand the shaking or vibratory (a) The words ‘‘Jet Fuel’’; and forces imposed by the engine if a AGENCY: Federal Aviation (b) The permissible fuel designations, cylinder becomes inoperative. Diesel Administration (FAA), DOT. or references to the Airplane Flight engines of conventional design typically Manual (AFM) for permissible fuel ACTION: Final rule. have extremely high levels of vibration designations. when a cylinder becomes inoperative. SUMMARY: We are adopting a new (c) A warning placard or note that Data must be provided to the airframe airworthiness directive (AD) for all states the following or similar: installer/modifier so either appropriate General Electric Company (GE) model ‘‘Warning—this airplane is equipped design considerations or operating GEnx–2B67B turbofan engines with with an aircraft diesel engine; service procedures, or both, can be developed to booster anti-ice (BAI) air duct, part with approved fuels only.’’ prevent airframe and propeller damage. -
Military Vehicle Options Arising from the Barrel Type Piston Engine
Journal of Power Technologies 101 (1) (2021) 22–33 Military vehicle options arising from the barrel type piston engine Pawe l Mazuro1 and Cezary Chmielewski1,B 1Warsaw University of Technology B [email protected] Abstract in terms of efficiency, meaning that piston engines can deliver enhanced range and endurance. This is benefi- The article reviews knowledge about requirements for engines in cial in missions requiring a stopover for refueling and state-of-the-art unmanned aerial vehicles and tanks. Analysis of particularly useful for unmanned supply, observation design and operational parameters was carried out on selected and maritime missions. turboshaft and piston engines generating power in the range of 500 - 1500 kW (0.5 - 1.5 MW). The data was compared In contrast, land combat vehicles have significantly with the performance of innovative, barrel type piston engines, different drive unit requirements. High mobility en- which are likely to become an alternative drive solution in the ables the vehicle to rapidly change location after de- target vehicle groups. tection. To this end, the torque curve as a function of the rotational speed of the shaft is of decisive im- portance. Keywords: military UAV, tanks, turboshaft engines, piston engines, barrel type piston engines The complexity of tank engines adds an additional layer of requirements, impacting the reliability and durability of the power unit, and they come with re- 1 Introduction lated manufacturing and operating costs. In military land vehicles, the engine should be as small This article consolidates knowledge on options and as possible; the space saved can be used for other capabilities arising from use of the barrel type piston purposes. -
Federal Register/Vol. 78, No. 160/Monday, August 19, 2013
Federal Register / Vol. 78, No. 160 / Monday, August 19, 2013 / Rules and Regulations 50317 (3) The factor with wing flaps extended as 3A13 to include the new Model J182T model T182T. The regulations specified in CS–VLA 345. with the Societe de Motorisation incorporated by reference in the type (f) Kinds of operation. The kinds of Aeronautiques (SMA) Engines, Inc. certificate are commonly referred to as operation (day VFR or day and night VFR, SR305–230E–C1 which is a four-stroke, the ‘‘original type certification basis.’’ In whichever is applicable) in which the aeroplane may be used, must be stated. The air cooled, diesel cycle engine that uses addition, the J182T certification basis minimum equipment required for the turbine (jet) fuel. The Model No. J182T, includes special conditions and operation must be listed. which is a derivative of the T182 equivalent levels of safety. (g) Powerplant limitations. The following currently approved under Type If the Administrator finds that the information must be furnished: Certificate No. 3A13, is an aluminum, applicable airworthiness regulations (1) Limitation required by CS–VLA 1521. four place, single engine airplane with (i.e., 14 CFR part 23) do not contain (2) Information necessary for marking the a cantilever high wing, with the SMA adequate or appropriate safety standards instruments required by CS–VLA 1549 to 1553. SR305–230E–C1 diesel cycle engine and for the J182T because of a novel or (3) Fuel and oil designation. associated systems installed. unusual design feature, special (4) For two-stroke engines, fuel/oil ratio. In anticipation of the reintroduction conditions are prescribed under the (h) Placards. -
Vol. 76 Tuesday, No. 225 November 22, 2011 Pages 72081–72300
Vol. 76 Tuesday, No. 225 November 22, 2011 Pages 72081–72300 OFFICE OF THE FEDERAL REGISTER VerDate Mar 15 2010 20:07 Nov 21, 2011 Jkt 226001 PO 00000 Frm 00001 Fmt 4710 Sfmt 4710 E:\FR\FM\22NOWS.LOC 22NOWS mstockstill on DSK4VPTVN1PROD with FEDREGWS II Federal Register / Vol. 76, No. 225 / Tuesday, November 22, 2011 The FEDERAL REGISTER (ISSN 0097–6326) is published daily, SUBSCRIPTIONS AND COPIES Monday through Friday, except official holidays, by the Office of the Federal Register, National Archives and Records PUBLIC Administration, Washington, DC 20408, under the Federal Register Subscriptions: Act (44 U.S.C. Ch. 15) and the regulations of the Administrative Paper or fiche 202–512–1800 Committee of the Federal Register (1 CFR Ch. I). The Assistance with public subscriptions 202–512–1806 Superintendent of Documents, U.S. Government Printing Office, Washington, DC 20402 is the exclusive distributor of the official General online information 202–512–1530; 1–888–293–6498 edition. Periodicals postage is paid at Washington, DC. Single copies/back copies: The FEDERAL REGISTER provides a uniform system for making Paper or fiche 202–512–1800 available to the public regulations and legal notices issued by Assistance with public single copies 1–866–512–1800 Federal agencies. These include Presidential proclamations and (Toll-Free) Executive Orders, Federal agency documents having general FEDERAL AGENCIES applicability and legal effect, documents required to be published Subscriptions: by act of Congress, and other Federal agency documents of public interest. Paper or fiche 202–741–6005 Documents are on file for public inspection in the Office of the Assistance with Federal agency subscriptions 202–741–6005 Federal Register the day before they are published, unless the issuing agency requests earlier filing. -
N O T I C E This Document Has Been Reproduced From
N O T I C E THIS DOCUMENT HAS BEEN REPRODUCED FROM MICROFICHE. ALTHOUGH IT IS RECOGNIZED THAT CERTAIN PORTIONS ARE ILLEGIBLE, IT IS BEING RELEASED IN THE INTEREST OF MAKING AVAILABLE AS MUCH INFORMATION AS POSSIBLE CONTRACTORS REPORT NO. 995 NASA CR•165,170 LIGHTWEIGHT DIESEL ENGINE DESIGNS FOR COMMUTER TYPE AIRCRAFT (NASA-C8-165470) LIG BINEIGHT DIESEL ENGINE DiS1VNS FOR C ONMUTEi T y kE N82-11066 Coatiuenta^ AIRCRAFT (TelEdyne 10t0rs, nuskeyon, Micu^) 7U P hC: A04/&F A01 CSCL 21c Uncla., G3/J7 u8165 Alex P. Brouwers Teledyne Continental Motors General Products Division 76 Getty Street Muskegon, Michigan 49442 JULY 1981 ^^ NGV1S81 RECEIVED NASA Sn FACSftx Acm 01 PREPARED FOR: AMM NATIONAL AERONAUTICS AND SPACE ADMINISTRATION LEWIS RESEARCH CENTER 21000 BROOKPARK ROAD CLEVELAND, OHIO 44135 CONTRACT NAS3.22149 CONTRACTORS REPORT NO. 995 NASA CR•165470 LIGHTWEIGHT DIESEL ENGINE DESIGNS FOR COMMUTER TYPE AIRCRAFT Alex P. Bromers Teledyne Continental Motors General Products Division 76 Getty Street Muskegon, Michigan 49442 JULY 1981 PREPARED FOR: NATIONAL AERONAUTICS AND SPACE ADMINISTRATION LEWIS RESEARCH CENTER 21000 BROOKPARK ROAD CLEVELAND, OHIO 44135 CONTRACT NAS3.22149 .xTELEDYNE C *ff1NEN1AL Mc7 M. General Products Wslon 4244J7-81 U, TABLE OF CONTENTS Papa No. 1.0 Summary ................................................................1 2.0 Introduction .............................................................3 2.1 Purpose of the Study ..................................................3 2.2 Previous Large Aircraft Diesel Engines -
Aircraft Propulsion C Fayette Taylor
SMITHSONIAN ANNALS OF FLIGHT AIRCRAFT PROPULSION C FAYETTE TAYLOR %L~^» ^ 0 *.». "itfnm^t.P *7 "•SI if' 9 #s$j?M | _•*• *• r " 12 H' .—• K- ZZZT "^ '! « 1 OOKfc —•II • • ~ Ifrfil K. • ««• ••arTT ' ,^IfimmP\ IS T A Review of the Evolution of Aircraft Piston Engines Volume 1, Number 4 (End of Volume) NATIONAL AIR AND SPACE MUSEUM 0/\ SMITHSONIAN INSTITUTION SMITHSONIAN INSTITUTION NATIONAL AIR AND SPACE MUSEUM SMITHSONIAN ANNALS OF FLIGHT VOLUME 1 . NUMBER 4 . (END OF VOLUME) AIRCRAFT PROPULSION A Review of the Evolution 0£ Aircraft Piston Engines C. FAYETTE TAYLOR Professor of Automotive Engineering Emeritus Massachusetts Institute of Technology SMITHSONIAN INSTITUTION PRESS CITY OF WASHINGTON • 1971 Smithsonian Annals of Flight Numbers 1-4 constitute volume one of Smithsonian Annals of Flight. Subsequent numbers will not bear a volume designation, which has been dropped. The following earlier numbers of Smithsonian Annals of Flight are available from the Superintendent of Documents as indicated below: 1. The First Nonstop Coast-to-Coast Flight and the Historic T-2 Airplane, by Louis S. Casey, 1964. 90 pages, 43 figures, appendix, bibliography. Price 60ff. 2. The First Airplane Diesel Engine: Packard Model DR-980 of 1928, by Robert B. Meyer. 1964. 48 pages, 37 figures, appendix, bibliography. Price 60^. 3. The Liberty Engine 1918-1942, by Philip S. Dickey. 1968. 110 pages, 20 figures, appendix, bibliography. Price 75jf. The following numbers are in press: 5. The Wright Brothers Engines and Their Design, by Leonard S. Hobbs. 6. Langley's Aero Engine of 1903, by Robert B. Meyer. 7. The Curtiss D-12 Aero Engine, by Hugo Byttebier. -
150 and 300 Kw Lightweight Diesel Aircraft Engine Design Study
https://ntrs.nasa.gov/search.jsp?R=19800011788 2020-03-21T19:51:36+00:00Z NASA Contractor Report 3260 150 and 300 kW Lightweight Diesel Aircraft Engine Design Study Alex P. Brouwers Teledyne Continental Motors Muskegon, Michigan Prepared for Lewis Research Center under Contract NAS3-20830 N/ /X National Aeronautics and Space Administration Scientific and Technical Information Office 1980 TABLE OF CONTENTS PageNo. 1.0 Summary ...................................................... 1 2.0 Introduction ................................................... 4 2.1 Advantages of the Diesel Engine .................................. 4 2.2 Previous Aircraft Diesel Engines .................................. 5 2.3 Scope of the Project ............................................. 7 2.4 Relative Merit of this Project to the General Field .................... 7 2.5 Significance of the Project ....................................... 7 3.0 Engine Design Study ............................................. 8 3.1 Technology Analysis ............................................ 8 3.1.1 Literature Search ............................................... 8 3.1.2 Definition of the Technology Base ................................. 8 3.1.3 Definition of the Design Approaches ............................... 16 3.1.4 Criteria Attributes ............................................... 17 3.1.5 Ranking Priorities ................................................ 18 3.1.6 Rating of Criteria ............................................... 19 3.1.7 Logic of Ranking ............................................... -
GTP-19-1645 Final PDF Document.PDF
Citation for published version: Turner, J, Head, R, Wijetunge, R, Chang, J, Engineer, N, Blundell, D & Burke, P 2020, 'Analysis of different uniflow scavenging options for a medium-duty 2-stroke engine for a U.S. light-truck application', Journal of Engineering for Gas Turbines and Power, vol. 142, no. 10, 101011. https://doi.org/10.1115/1.4046711 DOI: 10.1115/1.4046711 Publication date: 2020 Document Version Peer reviewed version Link to publication Publisher Rights CC BY Turner, J. W. G., Head, R. A., Wijetunge, R., Chang, J., Engineer, N., Blundell, D. W., and Burke, P. (September 29, 2020). "Analysis of Different Uniflow Scavenging Options for a Medium-Duty 2-Stroke Engine for a U.S. Light-Truck Application." ASME. J. Eng. Gas Turbines Power. October 2020; 142(10): 101011. https://doi.org/10.1115/1.4046711 University of Bath Alternative formats If you require this document in an alternative format, please contact: [email protected] General rights Copyright and moral rights for the publications made accessible in the public portal are retained by the authors and/or other copyright owners and it is a condition of accessing publications that users recognise and abide by the legal requirements associated with these rights. Take down policy If you believe that this document breaches copyright please contact us providing details, and we will remove access to the work immediately and investigate your claim. Download date: 02. Oct. 2021 GTP-19-1645 ANALYSIS OF DIFFERENT UNIFLOW SCAVENGING OPTIONS FOR A MEDIUM-DUTY 2-STROKE ENGINE FOR A U.S. LIGHT-TRUCK APPLICATION J.W.G. -
Performance and Emission Characteristics of an Aircraft Turbo Diesel Engine Using JET-A Fuel
Performance and Emission Characteristics of an Aircraft Turbo Diesel Engine using JET-A Fuel by Sean Christopher Underwood B.S. Aerospace Engineering, Georgia Institute of Technology, 2005 B.S. Mathematics, Georgia Southwestern State University, 2005 Submitted to the Department of Aerospace Engineering and the Faculty of the Graduate School of Engineering at the University of Kansas in partial fulfillment of the requirements for the degree of Master of Science. Committee: ________________________________ Dr. Ray Taghavi, Committee Chairman ________________________________ Dr. Saeed Farokhi, Committee Member ________________________________ Dr. Mark Ewing, Committee Member ___________________ Date Thesis Defended The Thesis Committee for Sean Christopher Underwood certifies that this is the approved Version of the following thesis: Performance and Emission Characteristics of an Aircraft Turbo Diesel Engine using JET-A Fuel Committee: ________________________________ Dr. Ray Taghavi, Committee Chairman ________________________________ Dr. Saeed Farokhi, Committee Member ________________________________ Dr. Mark Ewing, Committee Member ___________________ Date Approved i Abstract Performance and emission data was acquired by testing an aircraft turbo diesel engine with JET-A at the Mal Harned Propulsion Laboratory of the University of Kansas. The performance data was analyzed and compared to the presented data of the manufacturer. The performance test data of the engine was similar to those reported in the handbook of the engine. The emission data was collected in percent of volume, mass, and part per million units. The different types of pollutants that were evaluated were NOx, CO, CO2, and HC. The emission investigation demonstrates that the aircraft turbo diesel emission data (g/kg fuel) was close to other turbine engines reported in the literature. -
Study on Effects of Combustible Gas on Helicopter Operations
Aviation Safety Support Services for the Bureau of Safety and Environmental Enforcement Task C.4.5: Study on Effects of Combustible Gas on Helicopter Operations August 31, 2015 Aviation Safety Support Services for BSEE Task C.4.5: Study on Effects of Combustible Gas on Helicopter Operations Table of Contents Abbreviations and Acronyms .................................................................................... 4 1. Introduction....................................................................................................... 6 1.1 Other Mishaps Consistent With APG Ingestion .............................................................7 2. Analysis ...........................................................................................................12 2.1 Subtask C.4.5.1 – review and assess helideck construction standards .........................12 2.2 Subtask C.4.5.2 (a) – conduct technical analysis ..........................................................32 2.3 Subtask C.4.5.2 (b) – identify and list each helicopter (make, model, and engine) used on OCS facilities under BSEE jurisdiction. ..........................................................34 2.4 Subtask C.4.5.2 (c) – (1) determine the vapor density for each flammable gas (lighter or heavier than air) to determine how the placement of vents would affect helicopter operations; and (2) determine the flammability limits for each flammable gas to determine the effect on helicopter operations...................................35 2.5 Subtask C.4.5.2 (d) – (1) determine -
Smithsonian Contributions
Frontispiece—President Herbert Hoover (in front of microphones) presenting the Collier Trophy to Alvan Macauley (nearest engine), President of the Packard Motor Car Co., on March 31, 1932 (although the award was for 1931). Also present were Hiram Bingham, U.S. Senator from Connecticut (nearest pillar), Clarence M. Young, Director of Aeronautics, U.S. Department of Commerce (between Macauley and Hoover), and Amelia Earhart, first woman to fly across the Atlantic Ocean (between Macauley and the engine). In the foreground is a cutaway Packard diesel aero nautical engine, and directly in front of Senator Bingham is the Collier Trophy, America's highest aviation award. (Smithsonian photo A48825.) SMITHSONIAN ANNALS OF FLIGHT VOLUME 1 • NUMBER 2 The First Airplane Diesel Engine: Packard Model DR-980 of 1928 ROBERT B. MEYER Curator of Flight Propulsion SMITHSONIAN INSTITUTION • NATIONAL AIR MUSEUM WASHINGTON, D.C. • 1964 The following microfilm prints are available at the Smithsonian Institution: "The Packard Diesel Aircraft Engine—A New Chapter in Trans portation Progress." An advertising brochure produced by the Packard Motor Car Company in 1930, illustrated, 17 pages. Fifty-Hour Test of the Engine by the Packard Company, 1930. Text and charts, 14 pages. Fifty-Hour Test of the Engine by the U.S. Navy in 1931: Text and charts, 26 pages. Packard Instructional Manual, 1931. Illustrated, 74 pages. "The Packard Diesel Engine," Aviation Institute of U.S.A. Pamphlet No. 21-A, 1930. Illustrated, 32 pages. For sale by the Superintendent of Documents, U.S. Government Printing Office Washington, D.C., 20402 Price 60 cents IV Contents Page ACKNOWLEDGMENTS vi FOREWORD vii INTRODUCTION 1 History 2 DESCRIPTION 11 Specifications 11 Operating Cycles 13 Weight-Saving Features 15 Diesel Cycle Features 20' Development 23 COMMENTS 27 ANALYSIS 33 Advantages 33 Disadvantages 35 APPENDIX 1. -
The Slipstream
VOLUME 22, ISSUE 6 THE SLIPSTREAM THE NEWSLETTER OF GREEN RIVER EAA CHAPTER 441 KENT, WA J U N E 2 0 2 0 PRESIDENTS COLUMN, P IETENPOL UPDATE: INSIDE THIS ISSUE: Presidents Column: in Chapter 441 is not Gaussian: our chapter is skewed slightly to the PRESIDENTS CO L- Brian was un-available for providing 1 "elder statesman" side. We have 3 UMN an input to the Newsletter. While we members with more than 50 years of PIETENPOL U P- 3 have had a couple of members DATE flying; only 2 with less than 20. I "Head West' during the last year or won't bother you with the plots. D A R I N S R V 3 two the information is interesting to KITFOX UPDATE 3 look at 6 years later. Please note I picked this year to point all of this GUESS THAT AI R- 4 that this is from June 2014 and the out, because it seemed like 40 is a PLANE timelines are now 6 years later. "milestone" anniversary. What I dis- GUESS THAT I N- 4 covered (besides the fact that I am of STRUMENT PANEL Local Trivia average experience and slightly less E A A N E W S 5 Last month, I celebrated the 40th than the median) is that there were a anniversary of my first solo: May of number of other members who have EDITORS CORNER 6 1974, in a Cherokee 140, N2884T. gone past "milestone" anniversaries MAY G A T H E R I N G 7 MINUTES This month, I get to celebrate the this year without even saying any- same anniversary of my private pilot thing.