Analysis of Hydroxylammonium Nitrate Burning Rates
Total Page:16
File Type:pdf, Size:1020Kb
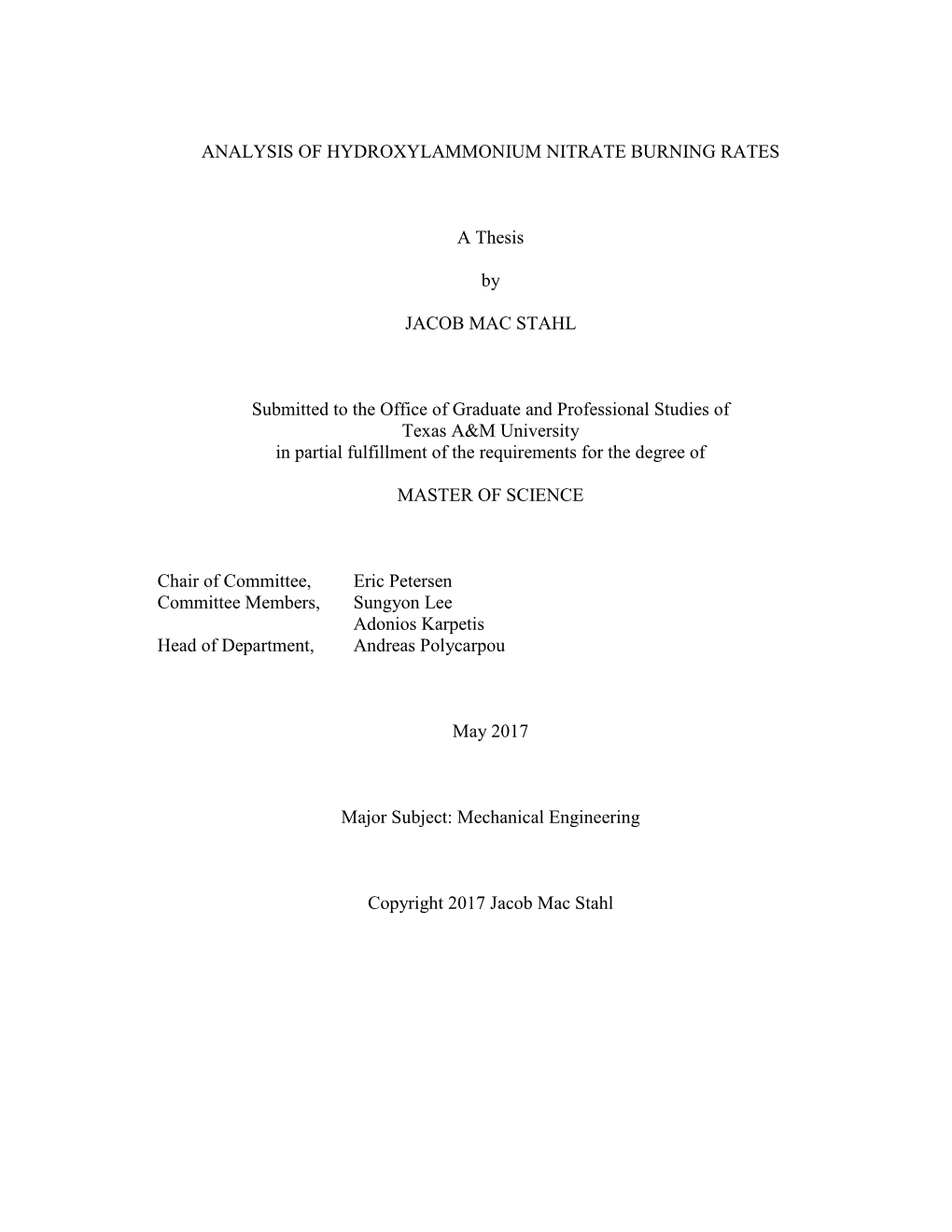
Load more
Recommended publications
-
Role of Electrodes in Ambient Electrolytic Decomposition of Hydroxylammonium Nitrate (HAN) Solutions
Propulsion and Power Research 2013;2(3):194–200 http://ppr.buaa.edu.cn/ Propulsion and Power Research www.sciencedirect.com ORIGINAL ARTICLE Role of electrodes in ambient electrolytic decomposition of hydroxylammonium nitrate (HAN) solutions Kai Seng Koha, Jitkai China,n, Tengku F. Wahida Ku Chikb aFaculty of Engineering, University of Nottingham Malaysia Campus, Semenyih, Selangor 52000, Malaysia bNational Space Agency Malaysia (ANGKASA), Putrajaya, Wilayah Persekuatuan 62570, Malaysia Received 13 April 2013; accepted 17 June 2013 Available online 27 August 2013 KEYWORDS Abstract Decomposition of hydroxylammonium nitrate (HAN) solution with electrolytic decomposition method has attracted much attention in recent years due to its efficiencies and Electrolytic decomposition; practicability. However, the phenomenon has not been well-studied till now. By utilizing Hydroxylammonium mathematical model currently available, the effect of water content and power used for nitrate (HAN); decomposition was studied. Experiment data shows that sacrificial material such as copper or Copper wire; aluminum outperforms inert electrodes in the decomposition of HAN solution. In the case of using Inert carbon rod; copper wire to electrolyse HAN solutions, approximately 10 seconds is required to reach 100 1C Electrode regardless of concentration of HAN. In term of power consumption, 100 W–300 W was found to be the range in which decomposition could be triggered effectively using copper wire as electrodes. & 2013 National Laboratory for Aeronautics and Astronautics. Production and hosting by Elsevier B.V. All rights reserved. 1. Introduction n Hydroxylammonium nitrate (HAN), with the chemical Corresponding author: Tel.: +60 173310400. formula NH OHNO , has been widely recognized as a E-mail address: [email protected] (Jitkai Chin). -
Characterization & Analysis On
CHARACTERIZATION & ANALYSIS ON ELECTROLYTIC DECOMPOSITION OF HYDROXYLAMMONIUM NITRATE (HAN) TERNARY MIXTURES IN MICROREACTORS CHAI WAI SIONG, BEng. Thesis submitted to the University of Nottingham For the degree of Doctor of Philosophy 2017 1 | P a g e Abstract Rapid development of micropropulsion systems arose from growing interest on micro- and nanosatellites. Utilization of liquid energetic materials such as hydrazine and hydrogen peroxide as propellant in propulsion yielded promising results. However, safety issue remains a great concern as hydrazine is highly toxic. This drives the development of propellants towards lower toxicity and more environmental friendly, namely green propellants. Hydroxylammonium nitrate (HAN) was selected among three green propellants due to its high energy density in addition to ease in storage and handling properties. In order to understand the effect of addition of fuel into HAN binary solution, electrolytic decomposition of zero oxygen balance HAN ternary mixture in thermal isolated beaker was performed at macroscale. Addition of a fuel to binary HAN solution generally has more stages of decomposition, as opposed to single stage in binary HAN solution. Rate of temperature increase in the first stage of decomposition (Ṫ1) was found to be directly proportional to electrical resistivity of the HAN ternary mixture, while maximum electrolytic decomposition temperature (Tmax) of HAN ternary mixture obtained was dependent on fuel added. Visualization of HAN decomposition was demonstrated using transparent PDMS microreactors. A novel DPST integration in triggering the power supply and high speed camera was proposed. Such 2 | P a g e integration greatly reduced the cost of using a DAQ system, and was shown to capture the decomposition successfully at 5000 fps. -
(12) United States Patent (10) Patent N0.: US 6,218,577 B1 Brand Et Al
US006218577B1 (12) United States Patent (10) Patent N0.: US 6,218,577 B1 Brand et al. (45) Date of Patent: Apr. 17, 2001 (54) ENEGETIC HYDRAZINIUM SALTS (58) Field Of Search ............................. .. 564/464; 149/36, 149/122 (75) Inventors: Adam J. Brand, Palmdale; Gregory W. Drake, Lancaster, both of CA (US) (56) References Cited (73) Assignee: The United States of America as US' PATENT DOCUMENTS represented by the Secretary of the 3,297,747 * 1/1967 Thornton et al. .................. .. 564/310 Air Force, Washington, DC (US) 3,314,837 * 4/1967 Heubusch . .. 525/410 4,310,696 * 1/1982 Hojo et al. ......................... .. 564/464 ( * ) Notice: Subject to any disclaimer, the term of this . * cited b examiner patent is extended or adJusted under 35 y U_S,C, 154(b) by 0 days, Primary Examiner—Johann Richter Assistant Examiner—Brian J. Davis (21) APPL NO; 09/356,227 (74) Attorney, Agent, or Firm—Thomas C. Stover (22) Filed: Jul. 16, 1999 (57) ABSTRACT Provided is a salt of hydroXyethylhydraZine of Related US. Application Data [HO—CH2—CH2—NH2—NH2+][X_] or [HO—CH2— (60) Provisional application No. 60/093,733, ?led on Jul. 20, 1998. CH2—NH2—NH32+][X_]2, Where X=NO3, c104, N(NO2)2 or C(NO2)3 and method of making same. (51) Int. Cl.7 ................................................. .. C07C 241/02 (52) US. Cl. ............................................................ .. 564/464 19 Claims, N0 Drawings US 6,218,577 B1 1 2 ENEGETIC HYDRAZINIUM SALTS HO—CH2—CH2—NH—NH2+m HXQ[HO—CH2— CH2—NH2—NH2+][X_] or [HO—CH2—CH2—NH2— This application claims priority from US. -
Annex XV Dossier PROPOSAL for IDENTIFICATION of a SUBSTANCE AS a CATEGORY 1A OR 1B CMR, PBT, Vpvb OR a SUBSTANCE of an EQUIVALEN
ANNEX XV – IDENTIFICATION OF HYDRAZINE AS SVHC Annex XV dossier PROPOSAL FOR IDENTIFICATION OF A SUBSTANCE AS A CATEGORY 1A OR 1B CMR, PBT, vPvB OR A SUBSTANCE OF AN EQUIVALENT LEVEL OF CONCERN Substance Name(s): Hydrazine EC Number(s): 206-114-9 CAS Number(s): 302-01-2 Submitted by: European Chemical Agency on request of the European Commission Version: February 2011 PUBLIC VERSION: This report does not include the Confidential Annexes referred to in Part II. 1 ANNEX XV – IDENTIFICATION OF HYDRAZINE AS SVHC CONTENTS PROPOSAL FOR IDENTIFICATION OF A SUBSTANCE AS A CATEGORY 1A OR 1B CMR, PBT, VPVB OR A SUBSTANCE OF AN EQUIVALENT LEVEL OF CONCERN ................................................................................7 PART I..........................................................................................................................................................................8 JUSTIFICATION .........................................................................................................................................................8 1 IDENTITY OF THE SUBSTANCE AND PHYSICAL AND CHEMICAL PROPERTIES .................................8 1.1 Name and other identifiers of the substance...................................................................................................8 1.2 Composition of the substance.........................................................................................................................9 1.3 Physico-chemical properties...........................................................................................................................9 -
Export Control Handbook for Chemicals
Export Control Handbook for Chemicals -Dual-use control list -Common Military List -Explosives precursors -Syria restrictive list -Psychotropics and narcotics precursors ARNES-NOVAU, X 2019 EUR 29879 This publication is a Technical report by the Joint Research Centre (JRC), the European Commission’s science and knowledge service. It aims to provide evidence-based scientific support to the European policymaking process. The scientific output expressed does not imply a policy position of the European Commission. Neither the European Commission nor any person acting on behalf of the Commission is responsible for the use that might be made of this publication. Contact information Xavier Arnés-Novau Joint Research Centre, Via Enrico Fermi 2749, 21027 Ispra (VA), Italy [email protected] Tel.: +39 0332-785421 Filippo Sevini Joint Research Centre, Via Enrico Fermi 2749, 21027 Ispra (VA), Italy [email protected] Tel.: +39 0332-786793 EU Science Hub https://ec.europa.eu/jrc JRC 117839 EUR 29879 Print ISBN 978-92-76-11971-5 ISSN 1018-5593 doi:10.2760/844026 PDF ISBN 978-92-76-11970-8 ISSN 1831-9424 doi:10.2760/339232 Luxembourg: Publications Office of the European Union, 2019 © European Atomic Energy Community, 2019 The reuse policy of the European Commission is implemented by Commission Decision 2011/833/EU of 12 December 2011 on the reuse of Commission documents (OJ L 330, 14.12.2011, p. 39). Reuse is authorised, provided the source of the document is acknowledged and its original meaning or message is not distorted. The European Commission shall not be liable for any consequence stemming from the reuse. -
Hydrocarbon-Seeded Ignition System for Small Spacecraft Thrusters Using Ionic Liquid Propellants
SSC13-VII-6 Hydrocarbon-Seeded Ignition System for Small Spacecraft Thrusters Using Ionic Liquid Propellants Stephen A. Whitmore, Daniel P. Merkley, and Shannon D. Eilers Mechanical and Aerospace Engineering Department, Utah State University 4130 Old Main Hill, UMC 4130; (435)-797-2951 [email protected] Terry L. Taylor Technology Development and Transfer Office, NASA Marshall Spaceflight Center, ZP-30, MSFC AL 35812; (256)-544-5916 [email protected] ABSTRACT "Green" propellants based on Ionic-liquids (ILs) like Ammonium DiNitramide and Hydroxyl Ammonium Nitrate have recently been developed as reduced-hazard replacements for hydrazine. Compared to hydrazine, ILs offer up to a 50% improvement in available density-specific impulse. These materials present minimal vapor hazard at room temperature, and this property makes IL's potentially advantageous for "ride-share" launch opportunities where hazards introduced by hydrazine servicing are cost-prohibitive. Even though ILs present a reduced hazard compared to hydrazine, in crystalline form they are potentially explosive and are mixed in aqueous solutions to buffer against explosion. Unfortunately, the high water content makes IL-propellants difficult to ignite and currently a reliable “cold-start” capability does not exist. For reliable ignition, IL-propellants catalyst beds must be pre-heated to greater than 350 C before firing. The required preheat power source is substantial and presents a significant disadvantage for SmallSats where power budgets are extremely limited. Design and development of a "micro-hybrid" igniter designed to act as a "drop-in" replacement for existing IL catalyst beds is presented. The design requires significantly lower input energy and offers a smaller overall form factor. -
Linear Burn Rate of Ionic Liquid Multimode Monopropellant
AIAA Propulsion and Energy Forum 10.2514/6.2019-4294 19-22 August 2019, Indianapolis, IN AIAA Propulsion and Energy 2019 Forum Linear Burn Rate of Ionic Liquid Multimode Monopropellant Nicolas Rasmont,1 Emil J. Broemmelsiek,1 Alex J. Mundahl,1 and Joshua L. Rovey2 University of Illinois Urbana-Champaign, Urbana IL, 61801 Multimode microthrusters are capable of both high specific impulse electrical operation and high thrust chemical operation, allowing a high degree of mission flexibility for small satellites. This technology requires a monopropellant capable of sustaining both modes of propulsion, through catalytic exothermic decomposition (chemical mode) and electrospray (electric mode). Previous research has identified a double-salt ionic liquid consisting of 41% wt. 1-ethyl-3-methylimidazolium ethyl sulfate and 59% wt. hydroxylammonium nitrate as a promising propellant candidate. The objective of this work is to measure its linear burn rate. The burn rate is measured through pressure-based and high-speed imaging methods in a fixed-volume pressurized reactor across a pressure range from 0.5 to 10 MPa. Its performance is compared to benchmarks 80% wt. hydroxylammonium nitrate-water and nitromethane propellants, both of which show good agreement with the literature. The burn rate of the ퟏ.ퟏퟏ푷 multimode monopropellant is found to follow an exponential law 풓풃 = ퟓ. ퟑퟓ풆 between 0.5 and 3 MPa and being approximately constant at 140 mm/s between 3 and 10 MPa. Nomenclature 푟푏 = Linear burn rate (mm/s) 퐷푐 = Diameter of propellant container (mm) 푉 = Volume of propellant (mL) 훥ℎ = Change in height (mm) 훥푡 = Change in time (s) 푃 = Pressure (MPa) 푎 = Burn rate coefficient (mm/s) 푛 = Burn rate exponent (unitless) I. -
The Decomposition of Hydroxylammonium Nitrate Under Vacuum Conditions
Western Michigan University ScholarWorks at WMU Master's Theses Graduate College 4-2016 The Decomposition of Hydroxylammonium Nitrate under Vacuum Conditions Gregory A. Neff Follow this and additional works at: https://scholarworks.wmich.edu/masters_theses Part of the Aerospace Engineering Commons, and the Mechanical Engineering Commons Recommended Citation Neff, Gregory A., "The Decomposition of Hydroxylammonium Nitrate under Vacuum Conditions" (2016). Master's Theses. 695. https://scholarworks.wmich.edu/masters_theses/695 This Masters Thesis-Open Access is brought to you for free and open access by the Graduate College at ScholarWorks at WMU. It has been accepted for inclusion in Master's Theses by an authorized administrator of ScholarWorks at WMU. For more information, please contact [email protected]. THE DECOMPOSITION OF HYDROXYLAMMONIUM NITRATE UNDER VACUUM CONDITIONS by Gregory A. Neff A thesis submitted to the Graduate College in partial fulfillment of the requirements for the degree of Master of Science in Engineering (Mechanical) Mechanical and Aerospace Engineering Western Michigan University April 2016 Thesis Committee: Kristina M. Lemmer, Ph.D., Chair Bade Shrestha, Ph.D. Ramakrishna Guda, Ph.D. THE DECOMPOSITION OF HYDROXYLAMMONIUM NITRATE UNDER VACUUM CONDITIONS Gregory A. Neff, M.S.E. Western Michigan University, 2016 This research investigates the decomposition of the ionic liquid: hydroxylammonium nitrate (HAN), under vacuum conditions. All research was conducted at the Aerospace Laboratory for Plasma Experiments (ALPE) at Western Michigan University. Hydroxylammonium nitrate solution 24% wt. in H2O was used consistently throughout this research. A variety of temperatures and pressures ranging from 23°C to 645°C and 6E-3 Torr to 4 Torr, respectively, were used to decompose HAN. -
Experimental Techniques to Study the Combustion of Aqueous
EXPERIMENTAL TECHNIQUES TO STUDY THE COMBUSTION OF AQUEOUS SOLUTIONS OF HYDROXYLAMMONIUM NITRATE WITH ADDITIVES A Thesis by GABRIEL DYLAN HOMAN-CRUZ Submitted to the Office of Graduate and Professional Studies of Texas A&M University in partial fulfillment of the requirements for the degree of MASTER OF SCIENCE Chair of Committee, Eric Petersen Committee Members, Timothy Jacobs Adonios Karpetis Head of Department, Andreas Polycarpou December 2015 Major Subject: Mechanical Engineering Copyright 2015 Gabriel Dylan Homan-Cruz ABSTRACT Aqueous solutions of hydroxylammonium nitrate (HAN) are promising as possible replacements for hydrazine as liquid rocket propellants. HAN-based propellants offer lower toxicity, higher density, and possibly higher specific impulse compared to hydrazine, but further research is needed to fully understand the combustion of HAN mixtures and to implement them in actual applications. The thesis presented here studies the combustion of HAN mixtures in a constant volume strand-burner over a pressure range between 3 and 20 MPa. A solution of 82.4 wt% HAN in water was used as a baseline from which other solutions were created. Silica and titania nanoparticles were added separately at concentrations of 1 wt% and 3 wt% in the baseline solution based on previous studies that have shown their effects on burning rates of other types of liquid propellants. A 14.9-wt% methanol mixture was examined based on previous studies that showed methanol’s effectiveness as a reducing agent in HAN-based propellants. A combination of 14.9 wt% methanol and 1 wt% silica was also studied. The preparation of these formulations is discussed in detail. -
Evaluation of Electric Solid Propellant Responses to Electrical Factors and Electrode Configurations
EVALUATION OF ELECTRIC SOLID PROPELLANT RESPONSES TO ELECTRICAL FACTORS AND ELECTRODE CONFIGURATIONS by ANDREW TIMOTHY HIATT A DISSERTATION Submitted in partial fulfillment of the requirements for the degree of Doctor of Philosophy in The Department of Mechanical & Aerospace Engineering to The School of Graduate Studies of The University of Alabama in Huntsville Huntsville, Alabama 2018 In presenting this dissertation in partial fulfillment of the requirements for a doctoral degree from The University of Alabama in Huntsville, I agree that the Library of this University shall make it freely available for inspection. I further agree that permission for extensive copying for scholarly purposes may be granted by my advisor or, in his/her absence, by the Chair of the Department or the Dean of the School of Graduate Studies. It is also understood that due recognition shall be given to me and to The University of Alabama in Huntsville in any scholarly use which may be made of any material in this dissertation. Andrew Timothy Hiatt (Date) ii DISSERTATION APPROVAL FORM Submitted by Andrew Timothy Hiatt in partial fulfillment of the requirements for the degree of Doctor of Philosophy in Mechanical Engineering and accepted on behalf of the Faculty of the School of Graduate Studies by the dissertation committee. We, the undersigned members of the Graduate Faculty of The University of Alabama in Huntsville, certify that we have advised and/or supervised the candidate on the work described in this dissertation. We further certify that we have reviewed the dissertation manuscript and approve it in partial fulfillment of the requirements for the degree of Doctor of Philosophy in Mechanical Engineering. -
Catalytic Decomposition of Hydroxylammonium Nitrate Monopropellant
2011 International Conference on Chemistry and Chemical Process IPCBEE vol.10 (2011) © (2011) IACSIT Press, Singapore Catalytic Decomposition of Hydroxylammonium Nitrate Monopropellant Charlie Oommen 1 +, Santhosh Rajaraman 1, R Arun Chandru 1 and R Rajeev 2 1 Department of Aerospace Engineering, Indian Institute of Science, Bangalore 2 Vikram Sarabhai Space Center, Thiruvananthapuram Abstract. Hydroxylammonium Nitrate (HAN) is being investigated as a promising substitute to hydrazine monopropellants. HAN propellants are less toxic and insensitive compared to conventional monopropellants. With the right combination of fuel and an active catalyst, HAN can be effectively used in propulsion systems. The current study focuses on developing a supported metal catalyst for HAN decomposition. An iridium supported catalyst was developed and characterized. The developed catalyst was found to be remarkably active even at very low concentration of HAN in HAN-water solutions. Keywords: Hydroxylammonium nitate, monopropellant, catalyst 1. Introduction Monopropellants are used extensively in reaction control systems (RCS) of satellites for orbital correction and attitude control. These are chemicals when passed through a catalytic bed decompose exothermically and produce large volume of gaseous products which can be expanded through a nozzle to get desired thrust. Propellant feed and control-system simplicity are of primary concern while choosing a propellant system. It must be easily decomposed and reactive to give good combustion properties. Among many systems that have been tried and tested over the years, hydrazine has remained as the most preferred mono propellant for over five decades due to its versatility and dependability. It offers substantially improved specific impulse over cold gas, and hydrazine systems require far less complex hardware compared to bi-propellant systems. -
Review of State-Of-The-Art Green Monopropellants: for Propulsion Systems Analysts and Designers
aerospace Review Review of State-of-the-Art Green Monopropellants: For Propulsion Systems Analysts and Designers Ahmed E. S. Nosseir 1,2,*, Angelo Cervone 1,* and Angelo Pasini 2 1 Department of Space Engineering, Faculty of Aerospace Engineering, Delft University of Technology (TU Delft), 2629 HS Delft, The Netherlands 2 Sede di Ingegneria Aerospaziale, Dipartimento di Ingegneria Civile e Industriale, Università di Pisa (UniPi), 56122 Pisa, Italy; [email protected] * Correspondence: [email protected] or [email protected] (A.E.S.N.); [email protected] (A.C.) Abstract: Current research trends have advanced the use of “green propellants” on a wide scale for spacecraft in various space missions; mainly for environmental sustainability and safety concerns. Small satellites, particularly micro and nanosatellites, evolved from passive planetary-orbiting to being able to perform active orbital operations that may require high-thrust impulsive capabilities. Thus, onboard primary and auxiliary propulsion systems capable of performing such orbital op- erations are required. Novelty in primary propulsion systems design calls for specific attention to miniaturization, which can be achieved, along the above-mentioned orbital transfer capabilities, by utilizing green monopropellants due to their relative high performance together with simplicity, and better storability when compared to gaseous and bi-propellants, especially for miniaturized systems. Owing to the ongoing rapid research activities in the green-propulsion field, it was necessary to extensively study and collect various data of green monopropellants properties and performance that would further assist analysts and designers in the research and development of liquid propulsion sys- tems.