Copper Production Technology CONTENTS Page Figure Page History
Total Page:16
File Type:pdf, Size:1020Kb
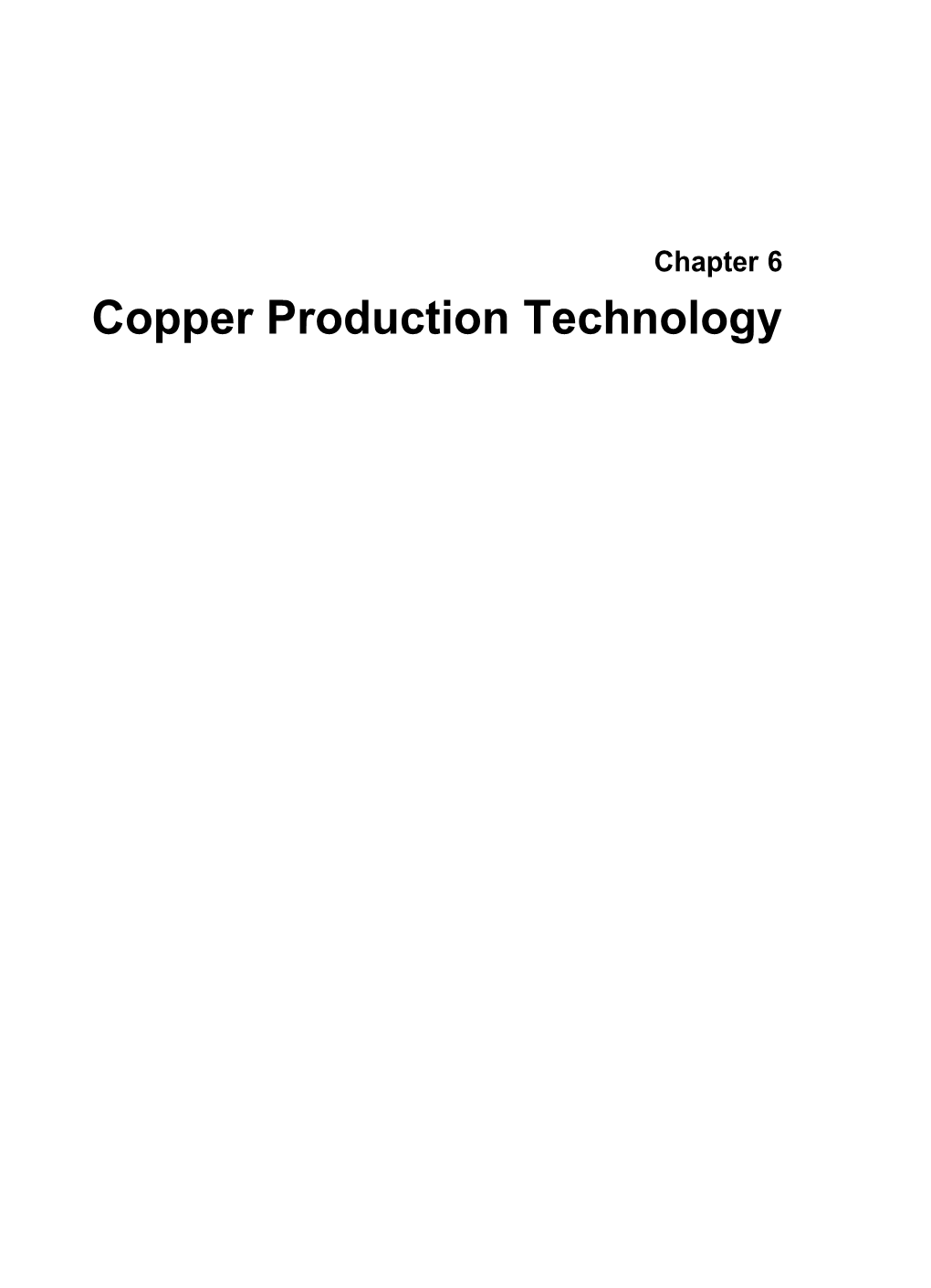
Load more
Recommended publications
-
A Review of Flotation Separation of Mg Carbonates (Dolomite and Magnesite)
minerals Review A Review of Flotation Separation of Mg Carbonates (Dolomite and Magnesite) Darius G. Wonyen 1,†, Varney Kromah 1,†, Borbor Gibson 1,† ID , Solomon Nah 1,† and Saeed Chehreh Chelgani 1,2,* ID 1 Department of Geology and Mining Engineering, Faculty of Engineering, University of Liberia, P.O. Box 9020 Monrovia, Liberia; [email protected] (D.G.W.); [email protected] (Y.K.); [email protected] (B.G.); [email protected] (S.N.) 2 Department of Electrical Engineering and Computer Science, University of Michigan, Ann Arbor, MI 48109, USA * Correspondence: [email protected]; Tel.: +1-41-6830-9356 † These authors contributed equally to the study. Received: 24 July 2018; Accepted: 13 August 2018; Published: 15 August 2018 Abstract: It is well documented that flotation has high economic viability for the beneficiation of valuable minerals when their main ore bodies contain magnesium (Mg) carbonates such as dolomite and magnesite. Flotation separation of Mg carbonates from their associated valuable minerals (AVMs) presents several challenges, and Mg carbonates have high levels of adverse effects on separation efficiency. These complexities can be attributed to various reasons: Mg carbonates are naturally hydrophilic, soluble, and exhibit similar surface characteristics as their AVMs. This study presents a compilation of various parameters, including zeta potential, pH, particle size, reagents (collectors, depressant, and modifiers), and bio-flotation, which were examined in several investigations into separating Mg carbonates from their AVMs by froth flotation. Keywords: dolomite; magnesite; flotation; bio-flotation 1. Introduction Magnesium (Mg) carbonates (salt-type minerals) are typical gangue phases associated with several valuable minerals, and have complicated processing [1,2]. -
Effects of Varied Process Parameters on Froth Flotation Efficiency: a Case Study of Itakpe Iron Ore
Nigerian Journal of Technology (NIJOTECH) Vol. 39, No. 3, July 2020, pp. 807 – 815 Copyright© Faculty of Engineering, University of Nigeria, Nsukka, Print ISSN: 0331-8443, Electronic ISSN: 2467-8821 www.nijotech.com http://dx.doi.org/10.4314/njt.v39i3.21 EFFECTS OF VARIED PROCESS PARAMETERS ON FROTH FLOTATION EFFICIENCY: A CASE STUDY OF ITAKPE IRON ORE S. Akande1, E. O. Ajaka2, O. O. Alabi3 and T. A. Olatunji4,* 1, 2, DEPARTMENT OF MINING ENGINEERING, FEDERAL UNIV. OF TECHNOLOGY, AKURE, ONDO STATE, NIGERIA 3, 4, DEPT. OF MET. & MATERIALS ENGINEERING, FEDERAL UNIV. OF TECHNOLOGY, AKURE, ONDO STATE, NIGERIA Email addresses: 1 [email protected], 2 [email protected], 3 [email protected], 4 [email protected] ABSTRACT The dire need for Itakpe iron ore concentrates of appreciable iron content meets for smelting operation necessitated this study. Core samples of the iron ore sourced from Itakpe, Kogi State, Nigeria were prepared for petrological analysis followed by chemical and particle size analyses. Froth flotation was done using different collectors at varying particle sizes and pH values. Characterization studies carried out revealed that Itakpe iron ore is a lean ore assaying 36.18% Fe2O3 and contains predominantly quartz, sillimanite, and haematite. Its liberation size lies favourably at 75 µm. Processing the ore by froth flotation yielded appreciable enrichment. Optimal recovery (~92%) was achieved using potassium amyl xanthate (PAX) at pH 11 for fine feed sizes (<125 µm) yielding iron concentrate assaying 67.66% Fe2O3. Thus, processing at this set-of- conditions is recommended for the industrial production of more enriched Itakpe iron ore concentrates. -
Petrology of Ore Deposits
Petrology of Ore Deposits An Introduction to Economic Geology Introductory Definitions Ore: a metalliferous mineral, or aggregate mixed with gangue that can me mined for a profit Gangue: associated minerals in ore deposit that have little or no value. Protore: initial non-economic concentration of metalliferous minerals that may be economic if altered by weathering (Supergene enrichment) or hydrothermal alteration Economic Considerations Grade: the concentration of a metal in an ore body is usually expressed as a weight % or ppm. The process of determining the grade is termed “assaying” Cut-off grade: after all economic and political considerations are weighed this is the lowest permissible grade that will mined. This may change over time. Example Economic Trends Economy of Scale As ore deposits are mined the high-grade zones are developed first leaving low-grade ores for the future with hopefully better technology Since mining proceeds to progressively lower grades the scale of mining increases because the amount of tonnage processed increases to remove the same amount of metal Outputs of 40,000 metric tons per day are not uncommon Near-surface open pit mines are inherently cheaper than underground mines Other factors important to mining costs include transportation, labor, power, equipment and taxation costs Classification of Ore bodies Proved ore: ore body is so thoroughly studied and understood that we can be certain of its geometry, average grade, tonnage yield, etc. Probable ore: ore body is somewhat delineated by surface mapping and some drilling. The geologists is reasonably sure of geometry and average grade. Possible Ore: outside exploration zones the geologist may speculate that the body extends some distance outside the probable zone but this is not supported by direct mapping or drilling. -
Metal Extraction Processes for Electronic Waste and Existing Industrial Routes: a Review and Australian Perspective
Resources 2014, 3, 152-179; doi:10.3390/resources3010152 OPEN ACCESS resources ISSN 2079-9276 www.mdpi.com/journal/resources Review Metal Extraction Processes for Electronic Waste and Existing Industrial Routes: A Review and Australian Perspective Abdul Khaliq, Muhammad Akbar Rhamdhani *, Geoffrey Brooks and Syed Masood Faculty of Science, Engineering and Technology, Swinburne University of Technology, Hawthorn, VIC 3122, Australia; E-Mails: [email protected] (A.K.); [email protected] (G.B.); [email protected] (S.M.) * Author to whom correspondence should be addressed; E-Mail: [email protected]; Tel.: +61-3-9214-8528; Fax: +61-3-9214-8264. Received: 11 December 2013; in revised form: 24 January 2014 / Accepted: 5 February 2014 / Published: 19 February 2014 Abstract: The useful life of electrical and electronic equipment (EEE) has been shortened as a consequence of the advancement in technology and change in consumer patterns. This has resulted in the generation of large quantities of electronic waste (e-waste) that needs to be managed. The handling of e-waste including combustion in incinerators, disposing in landfill or exporting overseas is no longer permitted due to environmental pollution and global legislations. Additionally, the presence of precious metals (PMs) makes e-waste recycling attractive economically. In this paper, current metallurgical processes for the extraction of metals from e-waste, including existing industrial routes, are reviewed. In the first part of this paper, the definition, composition and classifications of e-wastes are described. In the second part, separation of metals from e-waste using mechanical processing, hydrometallurgical and pyrometallurgical routes are critically analyzed. -
Principles of Extractive Metallurgy Lectures Note
PRINCIPLES OF EXTRACTIVE METALLURGY B.TECH, 3RD SEMESTER LECTURES NOTE BY SAGAR NAYAK DR. KALI CHARAN SABAT DEPARTMENT OF METALLURGICAL AND MATERIALS ENGINEERING PARALA MAHARAJA ENGINEERING COLLEGE, BERHAMPUR DISCLAIMER This document does not claim any originality and cannot be used as a substitute for prescribed textbooks. The information presented here is merely a collection by the author for their respective teaching assignments as an additional tool for the teaching-learning process. Various sources as mentioned at the reference of the document as well as freely available material from internet were consulted for preparing this document. The ownership of the information lies with the respective author or institutions. Further, this document is not intended to be used for commercial purpose and the faculty is not accountable for any issues, legal or otherwise, arising out of use of this document. The committee faculty members make no representations or warranties with respect to the accuracy or completeness of the contents of this document and specifically disclaim any implied warranties of merchantability or fitness for a particular purpose. BPUT SYLLABUS PRINCIPLES OF EXTRACTIVE METALLURGY (3-1-0) MODULE I (14 HOURS) Unit processes in Pyro metallurgy: Calcination and roasting, sintering, smelting, converting, reduction, smelting-reduction, Metallothermic and hydrogen reduction; distillation and other physical and chemical refining methods: Fire refining, Zone refining, Liquation and Cupellation. Small problems related to pyro metallurgy. MODULE II (14 HOURS) Unit processes in Hydrometallurgy: Leaching practice: In situ leaching, Dump and heap leaching, Percolation leaching, Agitation leaching, Purification of leach liquor, Kinetics of Leaching; Bio- leaching: Recovery of metals from Leach liquor by Solvent Extraction, Ion exchange , Precipitation and Cementation process. -
Profits from the Past
Reprocessing and tailings reduction.qxp_proof 29/04/2020 09:50 Page 1 REPROCESSING AND TAILINGS REDUCTION In Colombia, AuVert's technology is being combined with CDE's experience in dewatering Profits from the past and tailings management to extract the remaining precious metals existing in the ground, while removing up to 93% of residual mercury which has to date prevented this land from being used by the local population reasons why mining companies may be cautious about using tailings as backfill material or relocating current day ‘waste’ to an inaccessible area of the mine, according to Gerritsen. “As technology improves, the opportunity to recover more of the metals/minerals increases,” he said. “There are elements where that may not be the case – coal ash, for example, cannot be reprocessed but can be used to produce cement. While tailings dam liabilities and falling water resources are There are certainly opportunities with gold, affecting the ability of miners to start new mines, or expand copper and even coal, for instance.” The strategies companies ultimately pursue for existing ones, these issues are strengthening the case for these ‘waste streams’ depend on the technology reprocessing and retreating ‘waste’ sites or streams. Dan available and the safety of the facilities, Gerritsen Gleeson explores an increasingly diverse market focused on remarked. revenue generation and risk reduction “For instance, it may not be economically viable to reprocess the material currently in a ith improved transparency around recycling and thickening, or SART, plant from BQE tailings storage facility and, therefore, the owner tailings dams and waste stockpiles now Water will only bolster cash reserves through the may decide to close it or put it into a non-active Wpart and parcel of being a responsible recovery of a high-grade saleable copper sulphide state,” he said. -
Chapter 11: Beneficiation
CHAPTER 11 Beneficiation – Comminution Sponsored by: SPONSOR PROFILE Through pioneering the introduction of modern process • project controls and reporting plants and associated technologies to remote and logistically • contract management challenging locations, Lycopodium Minerals Pty Ltd has • procurement and logistics management developed a successful track record in developing and • inspection and expediting commissioning major resource projects worldwide. • quality assurance/quality control Since its establishment in 1992, Lycopodium has become a • financial evaluations leading international engineering and project management • client representation. consultancy, with an enviable reputation for providing Engineering technically innovative and cost-effective engineering solutions. They are focused on the evaluation and development of projects • Conceptual through to detailed design in the fields of minerals processing, materials handling and • across all disciplines: earthworks, civil infrastructure. • structural, mechanical, piping • electrical, instrumentation, control Lycopodium Minerals has undertaken studies and projects across a broad range of commodities including gold (free, • systems, automation and infrastructure. gravity, refractory, preg robbing), base metals (concentrators, Process hydrometallurgy), iron ore, uranium, rare earths and industrial minerals. Their resume of projects reflects diversity in not • Metallurgical test work design only commodity, but client background, technology, scale of • management and interpretation -
A History of Tailings1
A HISTORY OF MINERAL CONCENTRATION: A HISTORY OF TAILINGS1 by Timothy c. Richmond2 Abstract: The extraction of mineral values from the earth for beneficial use has been a human activity- since long before recorded history. Methodologies were little changed until the late 19th century. The nearly simultaneous developments of a method to produce steel of a uniform carbon content and the means to generate electrical power gave man the ability to process huge volumes of ores of ever decreasing purity. The tailings or waste products of mineral processing were traditionally discharged into adjacent streams, lakes, the sea or in piles on dry land. Their confinement apparently began in the early 20th century as a means for possible future mineral recovery, for the recycling of water in arid regions and/or in response to growing concerns for water pollution control. Additional Key Words: Mineral Beneficiation " ... for since Nature usually creates metals in an impure state, mixed with earth, stones, and solidified juices, it is necessary to separate most of these impurities from the ores as far as can be, and therefore I will now describe the methods by which the ores are sorted, broken with hammers, burnt, crushed with stamps, ground into powder, sifted, washed ..•. " Agricola, 1550 Introduction identifying mining wastes. It is frequently used mistakenly The term "tailings" is to identify all mineral wastes often misapplied when including the piles of waste rock located at the mouth of 1Presented at the 1.991. National mine shafts and adi ts, over- American. Society for Surface burden materials removed in Mining and Reclamation Meeting surface mining, wastes from in Durango, co, May 1.4-17, 1.991 concentrating activities and sometimes the wastes from 2Timothy c. -
Challenges Related to the Processing of Fines in the Recovery of Platinum Group Minerals (Pgms)
minerals Review Challenges Related to the Processing of Fines in the Recovery of Platinum Group Minerals (PGMs) Kirsten C. Corin 1,* , Belinda J. McFadzean 1, Natalie J. Shackleton 2 and Cyril T. O’Connor 1 1 Centre for Minerals Research, Chemical Engineering Department, University of Cape Town, P Bag X3, Rondebosch, Cape Town 7700, South Africa; [email protected] (B.J.M.); [email protected] (C.T.O.) 2 Minerals Expertise Tech Pty Ltd., Germiston 2007, South Africa; [email protected] * Correspondence: [email protected] Abstract: In order to increase the recovery of PGMs by flotation, it is necessary to optimise the liberation of the key minerals in which the platinum group elements (PGEs) are contained which include sulphides, arsenides, tellurides, and ferroalloys among others, while at the same time ensuring the optimal depression of gangue minerals. In order to achieve this, comminution circuits usually consist of two or three stages of milling, in which the first stage is autogeneous, followed by ball milling. Further liberation is achieved in subsequent stages using ultra-fine grinding. Each comminution stage is followed by flotation in the so-called MF2 or MF3 circuits. While this staged process increases overall recoveries, overgrinding may occur, hence creating problems associated with fine particle flotation. This paper presents an overview of the mineralogy of most of the more significant PGM ores processed in South Africa and the various technologies used in comminution circuits. The paper then summarises the methodology used in flotation circuits to optimise recovery Citation: Corin, K.C.; McFadzean, of fine particles in terms of the collectors, depressants, and frothers used. -
Sand, Gravel, and Crushed Stone On-The-Job Training Modules
SAND, GRAVEL, AND CRUSHED STONE ON-THE-JOB TRAINING MODULES Module 17 - “Primary Crushing Operation” UNITED STATES DEPARTMENT OF LABOR ELAINE L. CHAO SECRETARY MINE SAFETY AND HEALTH ADMINISTRATION DAVE D. LAURISKI ASSISTANT SECRETARY Originally Published AUGUST 2000 INSTRUCTION GUIDE SERIES MSHA IG 40 MODULE NUMBER 17 OF INSTRUCTION GUIDE NUMBER 40 ON-THE-JOB TRAINING FOR THE SAND, GRAVEL, AND CRUSHED STONE INDUSTRY PRIMARY CRUSHING OPERATION This module describes basic job steps, potential hazards and accidents, and recommended safe job procedures for primary crushing operations. This job is normally done by the crusher operator, but may be done by other occupations. Crusher operators must protect themselves, and other people in the area, from accidents and injuries resulting from operation of the crusher and associated equipment. There are several different types of primary crushers, however, there are many similarities in the job clxii procedures followed by crusher operators. Crushing is the first step in converting shot rock into usable products. Essentially, crushing is no more than taking large rocks and reducing them to small pieces. Crushing is sometimes continued until only fines remain. At some operations, all the crushing is accomplished in one step, by a primary crusher. At other operations, crushing is done in two or three steps, with a primary crusher that is followed by a secondary crusher, and sometimes a tertiary crusher. Raw material, of various sizes, is brought to the primary crusher by rear-dump haul units, or carried by a wheel front-end loader. Primary crushing reduces this run-of-mine rock to a more manageable size. -
Effect of Comminution Method on Particle Damage and Breakage Energy
EFFECT OF COMMINUTION METHOD ON PARTICLE DAMAGE AND BREAKAGE ENERGY Michael Moats, Jan Miller, Chen-Lun Lin and Raj Rajamani Department of Metallurgical Engineering University of Utah Outline • Our Department • High Pressure Grinding • Particle Damage Characterization • Breakage Energy • Application to Simulant Development Department of Metallurgical Engineering • University of Utah is located in Salt Lake City along the Wasatch Mtns. • Only stand alone Metallurgical Engineering department remaining in the U.S. • Traditional curriculum with critical mass of professors – Mineral Processing – Chemical Metallurgy – Physical Metallurgy High Pressure Grinding Rolls (HPGR) HPGR consists of a pair of counter rotating rolls, one fixed and the other floating. The feed is introduced to the gap in between the rolls and they compress the bed of particles. The grinding force applied to the crushing zone is controlled by a hydro-pneumatic spring on the floating roll. Speeds of the rolls are also adjustable to obtain optimum grinding conditions. Comparison of HPGR and AG/SAG Mills Aspect HPGR AG/SAG Mill Grinding Mechanism Inter-particle compression Impact, attrition and compression Residence Time Low-single pass High (feed migrates through length of mill) Wet/Dry Grinding Dry-Low moisture Predominantly wet milling Availability >90% -2-4 change outs pa >90% -1-2 change outs pa Size regulated feed Required Yes-strongly affects stud breakage AG-No, SAG-Sometimes Critical material size Not required Required Product particle Yes (beneficial for downstream Negligible micro-cracking processes Maximum Throughput 2000tph 4000tph Footprint Small Large Specific power 1-5kWh/t 5-12kWh/t Operating cost Overall plant 20% lower Overall plant 20% higher Capital Cost 25% lower 25% higher Delivery time Substantially faster Substantially longer Variation in feed hardness Single parameter variable High losses •Reference: Koenig, R.L. -
Mineral Engineering & Fuel Technology
MINERAL ENGINEERING & FUEL TECHNOLOGY (MME-203) 4th Semester B. Tech Dept. of Metallurgical and Materials Engineering V.S.S.university of Technology , Burla Sambalpur , odisha Person Name Designation Department involved And Email .id Course Gautam Assistant MME coordinator Behera professor [email protected] Course Co- Dinesh Assistant MME coordinator ku professor mishra , [email protected] Course Co- Avala Assistant MME coordinator Lava professor kumar [email protected] Goals of the subject 1-To impart knowledge about Mineral Processing [fundamental knowledge] 2-To teach you to “think” rather than “cook” 3-To encourage you to consider a career path in Mineral Processing Content Introduction to mineral processing(Engineering) Crushing and grinding Size separation methods Concentration methods Agglomeration techniques Fuel technology MODULE -I Introduction to mineral and mineral Engineering Mineral- a substance from which we get metal non metals or any valuables. Mineral Engineering ( branch of mme which deals with study of minerals and its processing )where the minerals is being processed to get a concentrate from which metals are extracted . Flow chat to show the relationship of mineral engineering with mining and extractive metallurgy engineering Subject covers Minerals definition MINERAL : Natural occur inorganic aggregate of metals and non metals . Or Inorganic compound having a definite chemical composition and crystal structure (atomic structure). Or minerals are the forms in which metals are found in the earth crust and as sea bed deposit depend on their reactivity with their environment, particular with oxygen , sulphur, and co2. Anything of economical value which is extracted from the earth. Characteristic of mineral 1-Minerals are homogeneous in physical and chemical composition.