Residual Gas Effects on Combustion in an Air-Cooled Utility Engine
Total Page:16
File Type:pdf, Size:1020Kb
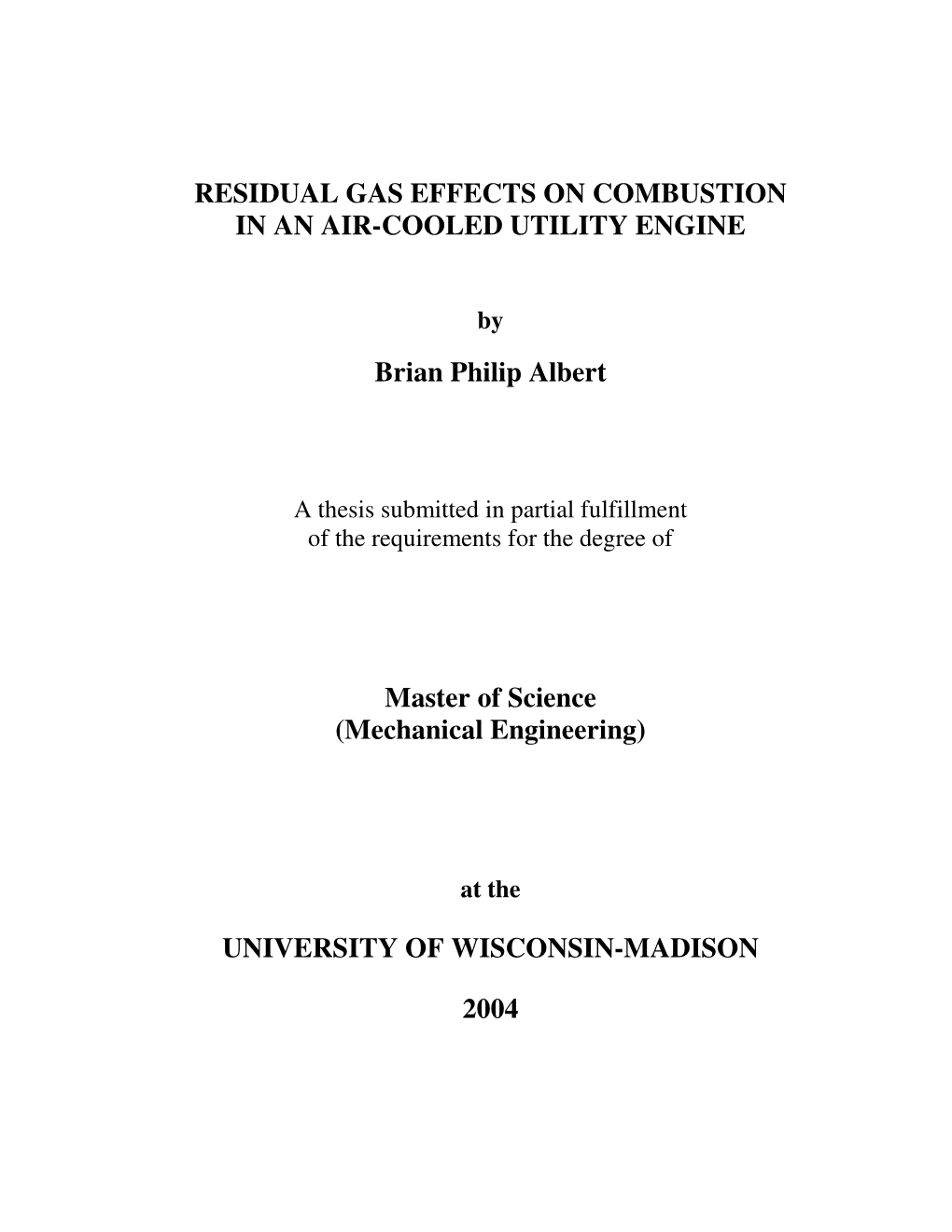
Load more
Recommended publications
-
Los Motores Aeroespaciales, A-Z
Sponsored by L’Aeroteca - BARCELONA ISBN 978-84-608-7523-9 < aeroteca.com > Depósito Legal B 9066-2016 Título: Los Motores Aeroespaciales A-Z. © Parte/Vers: 1/12 Página: 1 Autor: Ricardo Miguel Vidal Edición 2018-V12 = Rev. 01 Los Motores Aeroespaciales, A-Z (The Aerospace En- gines, A-Z) Versión 12 2018 por Ricardo Miguel Vidal * * * -MOTOR: Máquina que transforma en movimiento la energía que recibe. (sea química, eléctrica, vapor...) Sponsored by L’Aeroteca - BARCELONA ISBN 978-84-608-7523-9 Este facsímil es < aeroteca.com > Depósito Legal B 9066-2016 ORIGINAL si la Título: Los Motores Aeroespaciales A-Z. © página anterior tiene Parte/Vers: 1/12 Página: 2 el sello con tinta Autor: Ricardo Miguel Vidal VERDE Edición: 2018-V12 = Rev. 01 Presentación de la edición 2018-V12 (Incluye todas las anteriores versiones y sus Apéndices) La edición 2003 era una publicación en partes que se archiva en Binders por el propio lector (2,3,4 anillas, etc), anchos o estrechos y del color que desease durante el acopio parcial de la edición. Se entregaba por grupos de hojas impresas a una cara (edición 2003), a incluir en los Binders (archivadores). Cada hoja era sustituíble en el futuro si aparecía una nueva misma hoja ampliada o corregida. Este sistema de anillas admitia nuevas páginas con información adicional. Una hoja con adhesivos para portada y lomo identifi caba cada volumen provisional. Las tapas defi nitivas fueron metálicas, y se entregaraban con el 4 º volumen. O con la publicación completa desde el año 2005 en adelante. -Las Publicaciones -parcial y completa- están protegidas legalmente y mediante un sello de tinta especial color VERDE se identifi can los originales. -
US5507253.Pdf
|||||||||| USO05507253A United States Patent (19) 11 Patent Number: 5,507,253 Lowi, Jr. (45) Date of Patent: Apr. 16, 1996 54 ADABATIC, TWO-STROKECYCLE ENGINE ing,” SAE Paper 650007. HAVING PSTON-PHASING AND John C. Basiletti and Edward F. Blackburne, Dec. 1966, COMPRESSION RATO CONTROL SYSTEM "Recent Developments in Variable Compression Ratio Engines.” SAE Paper 660344. 76 Inventor: Alvin Lowi, Jr., 2146 Toscanini Dr., L. J. K. Setright, "Some Unusual Engines,” Dec. 1975, pp. Rancho Palos Verde, Calif. 90732 99-105, 109-111. R. Kamo, W. Bryzik and P. Glance Dec. 1987, "Adiabatic (21) Appl. No.: 311,348 Engine Trends-Worldwide,” SAE Paper 870018. (22 Filed: Sep. 23, 1994 S. G. Timony, M. H. Farmer and D. A. Parker, Dec. 1987, "Preliminary Experiences with a Ceramics Evaluation Related U.S. Application Data Engine Rig.” SAE Paper 870021. Paul and Humphrheys, Dec. 1952, SAE Transactions No. 6, 63 Continuation of Ser. No. 112,887, Aug. 27, 1993, Pat. No. 5,375,567. p. 259. (51) Int. Cl." ......................................... FO2B 75/26 Primary Examiner-Marguerite Macy I52 U.S. Cl. .................................... 123/S6.9 Attorney, Agent, or Firm-Bruce M. Canter 58) Field of Search .................................. 123/55.7, 56.1, 123/56.2, 56.8, 56.9, 51 B, 193.6 57) ABSTRACT An engine structure and mechanism that operates on various 56) References Cited combustion processes in a two-stroke-cycle without supple U.S. PATENT DOCUMENTS mental cooling or lubrication comprises an axial assembly of cylindrical modules and twin, double-harmonic cams that 1,127,267 2/1915 McElwain .............................. 123/56.8 operate with opposed pistons in each cylinder through fully 1,339,276 5/1920 Murphy ................................. -
Principles of an Internal Combustion Engine
Principles of an Internal Combustion Engine Course No: M03-046 Credit: 3 PDH Elie Tawil, P.E., LEED AP Continuing Education and Development, Inc. 22 Stonewall Court Woodcliff Lake, NJ 076 77 P: (877) 322-5800 [email protected] Chapter 2 Principles of an Internal Combustion Engine Topics 1.0.0 Internal Combustion Engine 2.0.0 Engines Classification 3.0.0 Engine Measurements and Performance Overview As a Construction Mechanic (CM), you are concerned with conducting various adjustments to vehicles and equipment, repairing and replacing their worn out broken parts, and ensuring that they are serviced properly and inspected regularly. To perform these duties competently, you must fully understand the operation and function of the various components of an internal combustion engine. This makes your job of diagnosing and correcting troubles much easier, which in turn saves time, effort, and money. This chapter discusses the theory and operation of an internal combustion engine and the various terms associated with them. Objectives When you have completed this chapter, you will be able to do the following: 1. Understand the principles of operation, the different classifications, and the measurements and performance standards of an internal combustion engine. 2. Identify the series of events, as they occur, in a gasoline engine. 3. Identify the series of events, as they occur in a diesel engine. 4. Understand the differences between a four-stroke cycle engine and a two-stroke cycle engine. 5. Recognize the differences in the types, cylinder arrangements, and valve arrangements of internal combustion engines. 6. Identify the terms, engine measurements, and performance standards of an internal combustion engine. -
Mathematical Modeling and Analysis of Gas Torque in Twinrotor Piston
J. Cent. South Univ. (2013) 20: 3536−3544 DOI: 10.1007/s117710131879y Mathematical modeling and analysis of gas torque in twinrotor piston engine DENG Hao(邓豪) 1, 2, PAN Cunyun(潘存云) 1, XU Xiaojun(徐小军) 1, ZHANG Xiang(张湘) 1 1. College of Mechatronic Engineering and Automation, National University of Defense Technology, Changsha 410073, China; 2. Naval Aeronautical Engineering Institute, Qingdao Branch, Qingdao 266041, China © Central South University Press and SpringerVerlag Berlin Heidelberg 2013 Abstract: The gas torque in a twinrotor piston engine (TRPE) was modeled using adiabatic approximation with instantaneous combustion. The first prototype of TRPE was manufactured. This prototype is intended for high power density engines and can produce 36 power strokes per shaft revolution. Compared with the conventional engines, the vector sum of combustion gas forces acting on each rotor piston in TRPE is a pure torque, and the combustion gas rotates the rotors while compresses the gas in the compression chamber at the same time. Mathematical modeling of gas force transmission was built. Expression for gas torque on each rotor was derived. Different variation patterns of the volume change of working chamber were introduced. The analytical and numerical results is presented to demonstrate the main characteristics of gas torque. The results show that the value of gas torque in TRPE falls to be less than zero before the combustion phase is finished; the time for one stroke is 30° in terms of the rotating angle of the output shaft; gas torque in one complete revolution of the output shaft has a period which is equal to 60° and it is necessary to put off the moment when gas torque becomes zero in order to export the maximum energy. -
ENRESO WORLD - Ilab
ENRESO WORLD - ILab Different Car Engine Types Istas René Graduated in Automotive Technologies 1-1-2019 1 4 - STROKE ENGINE A four-stroke (also four-cycle) engine is an internal combustion (IC) engine in which the piston completes four separate strokes while turning the crankshaft. A stroke refers to the full travel of the piston along the cylinder, in either direction. The four separate strokes are termed: 1. Intake: Also known as induction or suction. This stroke of the piston begins at top dead center (T.D.C.) and ends at bottom dead center (B.D.C.). In this stroke the intake valve must be in the open position while the piston pulls an air-fuel mixture into the cylinder by producing vacuum pressure into the cylinder through its downward motion. The piston is moving down as air is being sucked in by the downward motion against the piston. 2. Compression: This stroke begins at B.D.C, or just at the end of the suction stroke, and ends at T.D.C. In this stroke the piston compresses the air-fuel mixture in preparation for ignition during the power stroke (below). Both the intake and exhaust valves are closed during this stage. 3. Combustion: Also known as power or ignition. This is the start of the second revolution of the four stroke cycle. At this point the crankshaft has completed a full 360 degree revolution. While the piston is at T.D.C. (the end of the compression stroke) the compressed air-fuel mixture is ignited by a spark plug (in a gasoline engine) or by heat generated by high compression (diesel engines), forcefully returning the piston to B.D.C. -
Aircraft Propulsion C Fayette Taylor
SMITHSONIAN ANNALS OF FLIGHT AIRCRAFT PROPULSION C FAYETTE TAYLOR %L~^» ^ 0 *.». "itfnm^t.P *7 "•SI if' 9 #s$j?M | _•*• *• r " 12 H' .—• K- ZZZT "^ '! « 1 OOKfc —•II • • ~ Ifrfil K. • ««• ••arTT ' ,^IfimmP\ IS T A Review of the Evolution of Aircraft Piston Engines Volume 1, Number 4 (End of Volume) NATIONAL AIR AND SPACE MUSEUM 0/\ SMITHSONIAN INSTITUTION SMITHSONIAN INSTITUTION NATIONAL AIR AND SPACE MUSEUM SMITHSONIAN ANNALS OF FLIGHT VOLUME 1 . NUMBER 4 . (END OF VOLUME) AIRCRAFT PROPULSION A Review of the Evolution 0£ Aircraft Piston Engines C. FAYETTE TAYLOR Professor of Automotive Engineering Emeritus Massachusetts Institute of Technology SMITHSONIAN INSTITUTION PRESS CITY OF WASHINGTON • 1971 Smithsonian Annals of Flight Numbers 1-4 constitute volume one of Smithsonian Annals of Flight. Subsequent numbers will not bear a volume designation, which has been dropped. The following earlier numbers of Smithsonian Annals of Flight are available from the Superintendent of Documents as indicated below: 1. The First Nonstop Coast-to-Coast Flight and the Historic T-2 Airplane, by Louis S. Casey, 1964. 90 pages, 43 figures, appendix, bibliography. Price 60ff. 2. The First Airplane Diesel Engine: Packard Model DR-980 of 1928, by Robert B. Meyer. 1964. 48 pages, 37 figures, appendix, bibliography. Price 60^. 3. The Liberty Engine 1918-1942, by Philip S. Dickey. 1968. 110 pages, 20 figures, appendix, bibliography. Price 75jf. The following numbers are in press: 5. The Wright Brothers Engines and Their Design, by Leonard S. Hobbs. 6. Langley's Aero Engine of 1903, by Robert B. Meyer. 7. The Curtiss D-12 Aero Engine, by Hugo Byttebier. -
Engine Modeling of an Internal Combustion Engine
Engine Modeling of an Internal Combustion Engine With Twin Independent Cam Phasing THESIS Presented in Partial Fulfillment of the Requirements for Graduation with Distinction at The Ohio State University By Jason Meyer * * * * * The Ohio State University 2007 Defense Committee: Approved by Professor Yann Guezennec, Advisor Professor James Schmiedeler Adviser Undergraduate Program in Mechanical Engineering Copyright Jason Meyer 2007 Table of Contents Table of Contents .............................................................................................................. 1 Table of Figures................................................................................................................. 3 Acknowledgements ........................................................................................................... 5 Abstract.............................................................................................................................. 6 Chapter 1: Introduction ................................................................................................... 7 Chapter 2: Literature Review.......................................................................................... 9 2.1. Variable Valve Actuation Introduction ............................................................... 9 2.2 Types of Variable Valve Actuation ..................................................................... 12 2.2.1 Discretely-Stage Cam Systems...................................................................... 12 2.2.2 -
FAILURE Engine Analysis Booklet
FAILURE Engine Analysis Booklet © 2013 ECHO Incorporated – 400 Oakwood Road. Lake Zurich, IL 60047-1564 INTRODUCTION The best way to analyze an engine failure is by investigating what caused the fail- ure. This is very similar to a detective looking for evidence at a crime scene. It’s important not just to look at engine damage. Instead, look for clues outside the engine, test some components and then pull the cylinder to look for more clues inside the engine. The most accurate cause of an engine failure can be determined once all the available facts are assembled. Table of Contents INTRODUCTION .....................................................................2 2-STROKE ENGINE FUNDAMENTALS ..........................................3 ENGINE FAILURE BASICS ........................................................4 SPECIAL TOOLS ....................................................................8 SERVICE INFORMATION ..........................................................9 OUTSIDE ENGINE CHECKS & TESTS ........................................ 10 INSIDE ENGINE CHECKS ........................................................ 16 RAW GAS FAILURES ............................................................ 19 DIRT INGESTION FAILURES ...................................................20 LEAN SEIZE FAILURES ..........................................................22 OVERHEATING FAILURES ......................................................24 DETONATION / PRE-IGNITION .................................................27 STALE FUEL FAILURES -
A Review of Variable Valve Timing Devices Paul Shelton University of Arkansas, Fayetteville
View metadata, citation and similar papers at core.ac.uk brought to you by CORE provided by ScholarWorks@UARK University of Arkansas, Fayetteville ScholarWorks@UARK Mechanical Engineering Undergraduate Honors Mechanical Engineering Theses 5-2008 A Review of Variable Valve Timing Devices Paul Shelton University of Arkansas, Fayetteville Follow this and additional works at: http://scholarworks.uark.edu/meeguht Part of the Applied Mechanics Commons, Electrical and Electronics Commons, and the Electro- Mechanical Systems Commons Recommended Citation Shelton, Paul, "A Review of Variable Valve Timing Devices" (2008). Mechanical Engineering Undergraduate Honors Theses. 17. http://scholarworks.uark.edu/meeguht/17 This Thesis is brought to you for free and open access by the Mechanical Engineering at ScholarWorks@UARK. It has been accepted for inclusion in Mechanical Engineering Undergraduate Honors Theses by an authorized administrator of ScholarWorks@UARK. For more information, please contact [email protected]. A REVIEW OF VARIABLE VALVE TIMING DEVICES A thesis submitted in partial fulfillment of the requirements for the Honors Program, for the degree of Bachelor of Science in Mechanical Engineering by P. Blair Shelton, Mechanical Engineering Thesis Advisor – Dr. Larry Roe Dr. Adam Huang May 2008 University of Arkansas 2 Acknowledgements I would like to thank Dr. Roe and Huang for their continued support and guidance of my automotive research, Vanessa for bringing me food on those long nights of research, Aaron for helping with the formatting -
A Space Cam Mechanism for Power Transmission of an Opposite
MATEC Web of Conferences 22, 03003 (2015) DOI: 10.1051/matecconf/2015220300 3 C Owned by the authors, published by EDP Sciences, 2015 A Space Cam Mechanism for Power Transmission of an Oppo- site-cylinder Piston Engine Haoyue Zhang*, Xiaojun Xu, Lei Zhang, Faliang Zhou College of Mechatronics Engineering and Automation, National University of Defense Technology, Changsha, Hunan, China ABSTRACT: For the purpose of improving the engine’s power density, we put forward a new type of power transmission mechanism which is used for opposed-cylinder engine. The gas pressure acts on the cam through the piston and push rod, and the spindle rotation of external is driven by the cam. The design of spatial cam work surface is completed by using the enveloping theory of a family of space curves, the force between roller and cam is analyzed using dynamic analysis software. Under the condition of equal number, size and stroke of piston, the new one with larger power density is more compact in structure than the traditional power transmission mechanism, and the reaction force on either side of the main shaft and the acting force between pistons and cyl- inders are smaller than those in traditional one, which prolongs the service life of the pistons. Keywords: power transmission; space cam; supercharge; stress 1 INTRODUCTION 2 THE COMPOSITION AND THE PRESSURIZA- TION THEORY OF NOVEL POWER TRANS- The special space mechanism internal combustion MISSION MECHANISM engine has been widely applied in military fields, and familiar ones are cam-type, swash plate-type and New power transmission mechanism transforms the wobble plate-type (Peng et al. -
Master's Thesis
Potential Future Engine Cycles for Improved Thermal Efficiency Analysis of Various Internal Waste Heat Recovery Cycles with Minimal Deviation From Common Engine Architectures MICHAEL J. DENNY Department of Applied Mechanics Combustion Division Chalmers University of Technology Gothenburg, Sweden 2014 Master's Thesis 2014:32 Potential Future Engine Cycles for Improved Thermal Efficiency Analysis of Various Internal Waste Heat Recovery Cycles with Minimal Deviation From Common Engine Architectures MICHAEL J. DENNY © MICHAEL J. DENNY, 2014 Master's Thesis 2014:32 ISSN 1652-8557 Department of Applied Mechanics Combustion Division Chalmers University of Technology SE-412 96 G¨oteborg Sweden Telephone: + 46 (0)31-772 1000 Thesis performed at: Volvo Car Corporation Advanced Engine Engineering Dept. 97624 PO Box PV4B SE-405 31 G¨oteborg Sweden Printed by: Chalmers Reposervice G¨oteborg, Sweden 2014 Abstract A comparative 1-D analysis is undertaken between a baseline internal combustion engine (ICE) and several ICE operating cycle concepts which are intended to produce higher brake efficiencies than the baseline which runs on an Otto cycle. The baseline is a spark ignition gasoline engine representative of modern naturally aspirated automotive engines in its architecture and implemented technologies. Engine models are created and compared in the 1-D engine simulation software program GT-Power created by Gamma Technologies. After calibrating the performance of each model with the same resolution and tuning strategies, the result is that all of the concepts are less efficient than the base- line engine. Each engine concept requires additional hardware to separate the processes of the cycle within the engine. These components add to the mechanical friction, flow, and heat losses within the engine, and in some cases manage only to transfer exergy into different forms, not reduce it in a positive way. -
Rotary Combustion Engine
ROTARY COMBUSTION ENGINE This article is about internal combustion engines that do not use conventional pistons. See also rotary engine for the World War I aircraft engines by that name. A rotary engine is an internal combustion engine that does not use pistons in the way a reciprocating enginedoes, but instead uses one or more rotors, sometimes called rotary pistons. Further clarification The term rotary combustion engine has been suggested as an alternative name for these engines to distinguish them from the obsolete aircraft engines also known as rotary engines. However both continue to be called rotary engines and only the context determines which type is meant. In particular, the only commercial producer of (pistonless) rotary engines as of 2005, Mazda, consistently refers to their Wankel engines asrotary engines. The basic concept of a (pistonless) rotary engine is to avoid the reciprocating motion of the piston with its inherent vibration and rotational-speed-related mechanical stress. As of 2005 the Wankel engine is the only successful pistonless rotary engine, but many similar concepts have been proposed and are under various stages of development. There are countless other examples of rotary engines varying in rotor design, size and many other categories. Notable examples include: The quasiturbine. The Sarich orbital engine. A rotary engine developed by Texas machinist Frank Turner which was licensed by Malcolm Bricklin for use in place of the V8 powering the Bricklin SV- 1 vehicle, but never used. The Rand Cam engine Advantages All such engines have the potential to improve on the piston engine in the areas of: Higher power-to-weight ratios.