Electromagnetic and Magnetic Suspension
Total Page:16
File Type:pdf, Size:1020Kb
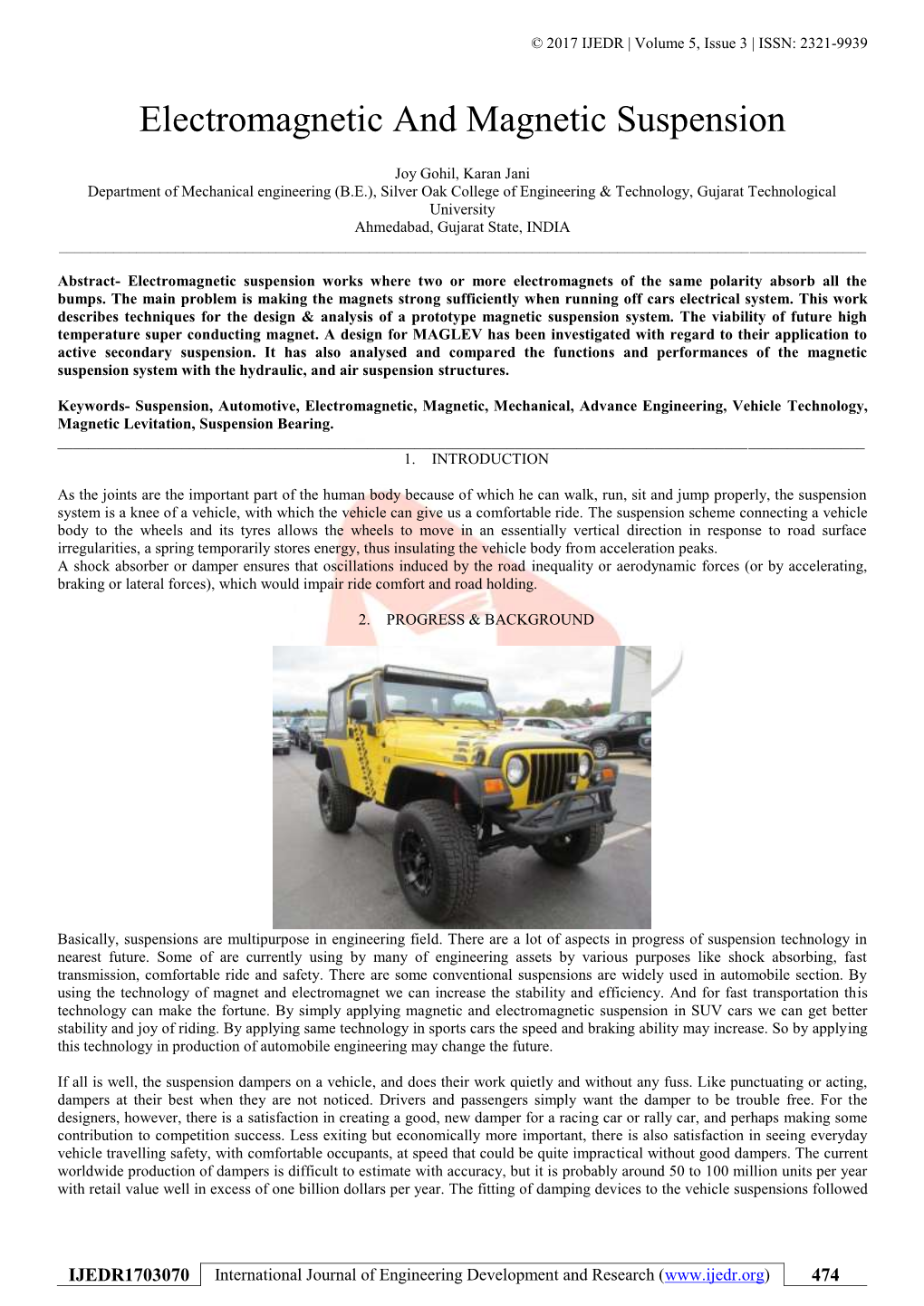
Load more
Recommended publications
-
Development and Testing of an Axial Halbach Magnetic Bearing
NASA/TM—2006-214357 Development and Testing of an Axial Halbach Magnetic Bearing Dennis J. Eichenberg, Christopher A. Gallo, and William K. Thompson Glenn Research Center, Cleveland, Ohio July 2006 NASA STI Program . in Profile Since its founding, NASA has been dedicated to the • CONFERENCE PUBLICATION. Collected advancement of aeronautics and space science. The papers from scientific and technical NASA Scientific and Technical Information (STI) conferences, symposia, seminars, or other program plays a key part in helping NASA maintain meetings sponsored or cosponsored by NASA. this important role. • SPECIAL PUBLICATION. Scientific, The NASA STI Program operates under the auspices technical, or historical information from of the Agency Chief Information Officer. It collects, NASA programs, projects, and missions, often organizes, provides for archiving, and disseminates concerned with subjects having substantial NASA’s STI. The NASA STI program provides access public interest. to the NASA Aeronautics and Space Database and its public interface, the NASA Technical Reports Server, • TECHNICAL TRANSLATION. English- thus providing one of the largest collections of language translations of foreign scientific and aeronautical and space science STI in the world. technical material pertinent to NASA’s mission. Results are published in both non-NASA channels and by NASA in the NASA STI Report Series, which Specialized services also include creating custom includes the following report types: thesauri, building customized databases, organizing and publishing research results. • TECHNICAL PUBLICATION. Reports of completed research or a major significant phase For more information about the NASA STI of research that present the results of NASA program, see the following: programs and include extensive data or theoretical analysis. -
Dynamic Suspension Modeling of an Eddy-Current Device: an Application to Maglev
DYNAMIC SUSPENSION MODELING OF AN EDDY-CURRENT DEVICE: AN APPLICATION TO MAGLEV by Nirmal Paudel A dissertation submitted to the faculty of The University of North Carolina at Charlotte in partial fulfillment of the requirements for the degree of Doctor of Philosophy in Electrical Engineering Charlotte 2012 Approved by: Dr. Jonathan Z. Bird Dr. Yogendra P. Kakad Dr. Robert W. Cox Dr. Scott D. Kelly ii c 2012 Nirmal Paudel ALL RIGHTS RESERVED iii ABSTRACT NIRMAL PAUDEL. Dynamic suspension modeling of an eddy-current device: an application to Maglev. (Under the direction of DR. JONATHAN Z. BIRD) When a magnetic source is simultaneously oscillated and translationally moved above a linear conductive passive guideway such as aluminum, eddy-currents are in- duced that give rise to a time-varying opposing field in the air-gap. This time-varying opposing field interacts with the source field, creating simultaneously suspension, propulsion or braking and lateral forces that are required for a Maglev system. In this thesis, a two-dimensional (2-D) analytic based steady-state eddy-current model has been derived for the case when an arbitrary magnetic source is oscillated and moved in two directions above a conductive guideway using a spatial Fourier transform technique. The problem is formulated using both the magnetic vector potential, A, and scalar potential, φ. Using this novel A-φ approach the magnetic source needs to be incorporated only into the boundary conditions of the guideway and only the magnitude of the source field along the guideway surface is required in order to compute the forces and power loss. -
Universidade Federal Do Rio De Janeiro 2017
Universidade Federal do Rio de Janeiro RETROSPECTIVA DOS MÉTODOS DE LEVITAÇÃO E O ESTADO DA ARTE DA TECNOLOGIA DE LEVITAÇÃO MAGNÉTICA Hugo Pelle Ferreira 2017 RETROSPECTIVA DOS MÉTODOS DE LEVITAÇÃO E O ESTADO DA ARTE DA TECNOLOGIA DE LEVITAÇÃO MAGNÉTICA Hugo Pelle Ferreira Projeto de Graduação apresentado ao Curso de Engenharia Elétrica da Escola Politécnica, Universidade Federal do Rio de Janeiro, como parte dos requisitos necessários à obtenção do título de Engenheiro. Orientador: Richard Magdalena Stephan Rio de Janeiro Abril de 2017 RETROSPECTIVA DOS MÉTODOS DE LEVITAÇÃO E O ESTADO DA ARTE DA TECNOLOGIA DE LEVITAÇÃO MAGNÉTICA Hugo Pelle Ferreira PROJETO DE GRADUAÇÃO SUBMETIDO AO CORPO DOCENTE DO CURSO DE ENGENHARIA ELÉTRICA DA ESCOLA POLITÉCNICA DA UNIVERSIDADE FEDERAL DO RIO DE JANEIRO COMO PARTE DOS REQUISITOS NECESSÁRIOS PARA A OBTENÇÃO DO GRAU DE ENGENHEIRO ELETRICISTA. Examinada por: ________________________________________ Prof. Richard Magdalena Stephan, Dr.-Ing. (Orientador) ________________________________________ Prof. Antonio Carlos Ferreira, Ph.D. ________________________________________ Prof. Rubens de Andrade Jr., D.Sc. RIO DE JANEIRO, RJ – BRASIL ABRIL de 2017 RETROSPECTIVA DOS MÉTODOS DE LEVITAÇÃO E O ESTADO DA ARTE DA TECNOLOGIA DE LEVITAÇÃO MAGNÉTICA Ferreira, Hugo Pelle Retrospectiva dos Métodos de Levitação e o Estado da Arte da Tecnologia de Levitação Magnética/ Hugo Pelle Ferreira. – Rio de Janeiro: UFRJ/ Escola Politécnica, 2017. XVIII, 165 p.: il.; 29,7 cm. Orientador: Richard Magdalena Stephan Projeto de Graduação – UFRJ/ Escola Politécnica/ Curso de Engenharia Elétrica, 2017. Referências Bibliográficas: p. 108 – 165. 1. Introdução. 2. Princípios de Levitação e Aplicações. 3. Levitação Magnética e Aplicações. 4. Conclusões. I. Stephan, Richard Magdalena. II. Universidade Federal do Rio de Janeiro, Escola Politécnica, Curso de Engenharia Elétrica. -
Non-Dimensional Design Approach for Electrodynamic Bearings
View metadata, citation and similar papers at core.ac.uk brought to you by CORE provided by PORTO Publications Open Repository TOrino Non-dimensional design approach for Electrodynamic Bearings F. Impinna* J. Detoni N. Amati Department of Mechanical and Department of Mechanical and Department of Mechanical and Aerospace Engineering, Aerospace Engineering, Aerospace Engineering, Politecnico di Torino Politecnico di Torino Politecnico di Torino Torino, Italy Torino, Italy Torino, Italy A. Tonoli Department of Mechanical and Aerospace Engineering, Politecnico di Torino Torino, Italy Abstract Electrodynamic bearings (EDBs) are passive magnetic bearings that exploit the interaction between eddy currents developed in a rotating conductor and a static magnetic field to generate forces. Similar to other types of magnetic suspensions, EDBs provide contactless support, thus avoiding problems with lubrication, friction and wear. The most interesting aspect of EDBs is that levitation can be obtained by passive means, hence, no electronic equipment, such as power electronics or sensors, are necessary. Despite their promising characteristics, rotors running on EDBs are still lacking a design procedure; furthermore, at present the static behavior of a bearing can only be defined by means of finite element analyses. The aim of the present paper is to present a methodology that allows performing a first approximation design without resorting to detailed FE analyses. The methodology is based on the use of non-dimensional parameters, similar to the analysis of fluid bearings (Sommerfeld number). The non-dimensional quantities are derived using dimensional analysis, and contain the main geometrical and physical parameters determining the EDBs' performance. The relation between the non-dimensional quantities characterizing the static performance of the EDB is derived using FE simulations and is presented in the form of graphs. -
Superconducting Magnetic Bearings Simulation Using an H-Formulation Finite Element Model
Superconducting Magnetic Bearings Simulation using an H-formulation Finite Element Model Loïc Quéval1, Kun Liu2, Wenjiao Yang2, Víctor M. R. Zermeño3, Guangtong Ma2* 1Group of electrical engineering - Paris (GeePs), CNRS UMR 8507, CentraleSupélec, UPSud, UPMC, Gif-sur- Yvette, France. Phone: +33-169851534, e-mail address: [email protected] 2Applied Superconductivity Laboratory (ASCLab), State Key Laboratory of Traction Power, Southwest Jiaotong University, Chengdu, Sichuan 610031, China. Phone: +86-28-87603310, e-mail address: [email protected], [email protected], [email protected] 3Karlsruhe Institute of Technology, Hermann-von-Helmholtz Platz 1, 76344 Eggenstein-Leopoldshafen, Germany Phone: +49-72160828582, e-mail address: [email protected] * Author to whom correspondence should be addressed Abstract The modeling of superconducting magnetic bearing (SMB) is of great significance for predicting and optimizing its levitation performance before construction. Although lots of efforts have been made in this area, it still remains some space for improvements. Thus the goal of this work is to report a flexible, fast and trustworthy H-formulation finite element model. First the methodology for modeling and calibrating both bulk-type and stack-type SMB is summarized. Then its effectiveness for simulating SMBs in 2-D, 2-D axisymmetric and 3-D is evaluated by comparison with measurements. In particular, original solutions to overcome several obstacles are given: clarification of the calibration procedure for stack-type and bulk-type SMBs, details on the experimental protocol to obtain reproducible measurements, validation of the 2-D model for a stack-type SMB modeling the tapes real thickness, implementation of a 2-D axisymmetric SMB model, implementation of a 3-D SMB model, extensive validation of the models by comparison with experimental results for field cooling and zero field cooling, for both vertical and lateral movements. -
Magnetic Guidance for Linear Drives
Magnetic Guidance for Linear Drives Vom Fachbereich Elektrotechnik und Informationstechnik der Technischen Universität Darmstadt zur Erlangung des akademischen Grades eines Doktor-Ingenieurs (Dr.-Ing.) genehmigte Dissertation von Phong C. Khong, M.Sc. Geboren am 10. April 1978 in Hanoi, Vietnam Referent: Prof. Dr.-Ing. Peter Mutschler Korreferent: Prof. Dr.-Ing. Mario Pacas Tag der Einreichung: 11. 04. 2011 Tag der mündlichen Prüfung: 29. 08. 2011 D17 Darmstadt 2011 Erklärung laut §9 PromO Erklärung laut §9 PromO Ich versichere hiermit, dass ich die vorliegende Dissertation allein und nur unter Verwendung der angegebenen Literatur verfasst habe. Die Arbeit hat bisher noch nicht zu Prüfungszwecken gedient. ______________ Darmstadt, den 08. April 2011. Phong C. Khong I Preface Preface This dissertation is the results of my 4-years study and research in the Department of Power Electronics and Control of Drives - Darmstadt University of Technology. Besides the personal works, the results are achieved by the contributed help directly or indirectly from many people to the dissertation. Therefore, I would like to give here my thanks to them. Firstly, I would like to give my thanks to Prof. Dr.-Ing. Peter Mutschler, the supervisor and director of the Department. I would thank for his greatest support throughout my thesis with his supervision, inspiration and wonderful working plan during the 4-years. I would thank for his support in formalities and finance for my study in Germany. To Prof. Dr.-Ing. Mario Pacas, I thank for his interest and for acting as the co-advisor. I thank the DFG Deutsche Forschungsgemeinschaft for financially supporting my projects MU 1109. -
Test and Theory of Electrodynamic Bearings Coupled to Active Magnetic Dampers
CORE Metadata, citation and similar papers at core.ac.uk Provided by PORTO Publications Open Repository TOrino Politecnico di Torino Porto Institutional Repository [Proceeding] Test and Theory of Electrodynamic Bearings Coupled to Active Magnetic Dampers Original Citation: Impinna F., Detoni J.G., Tonoli A., Amati N. (2014). Test and Theory of Electrodynamic Bearings Coupled to Active Magnetic Dampers. In: 14th International Symposium on Magnetic Bearings, Linz, Austria, 11-14 August 2014. pp. 263-268 Availability: This version is available at : http://porto.polito.it/2561348/ since: September 2014 Terms of use: This article is made available under terms and conditions applicable to Open Access Policy Article ("Public - All rights reserved") , as described at http://porto.polito.it/terms_and_conditions. html Porto, the institutional repository of the Politecnico di Torino, is provided by the University Library and the IT-Services. The aim is to enable open access to all the world. Please share with us how this access benefits you. Your story matters. (Article begins on next page) Test and theory of electrodynamic bearings coupled to active magnetic dampers Fabrizio Impinna, Joaquim G. Detoni, Andrea Tonoli, Nicola Amati, Maria Pina Piccolo Department of Mechanical and Aerospace Engineering, Mechatronics Laboratory, Politecnico di Torino, Corso Duca degli Abruzzi, 24, 10129 Torino Abstract— Electrodynamic bearings (EDBs) are passive AMDs. It requires studying the effect of the combination of magnetic bearings that exploit the interaction between electrodynamic and AMD forces both analytically and eddy currents developed in a rotating conductor and a experimentally. This is aimed at developing an analytical static magnetic field to generate forces. -
Design of a Lorentz, Slotless Self-Bearing Motor for Space Applications
ABSTRACT OF THESIS DESIGN OF A LORENTZ, SLOTLESS SELF-BEARING MOTOR FOR SPACE APPLICATIONS The harsh conditions of space, the stringent requirements for orbiting devices, and the increasing precision pointing requirements of many space applications demand an actuator that can provide necessary force while using less space and power than its predecessors. Ideally, this actuator would be able to isolate vibrations and never fail due to mechanical wear, while pointing with unprecedented accuracy. This actuator has many space applications from satellite optical communications and satellite appendage positioning to orbiting telescopes. This thesis presents the method of design of such an actuator – a self-bearing motor. The actuator uses Lorentz forces to generate both torque and bearing forces. It has a slotless winding configuration with four sets of three-phase currents. A stand-alone software application, LFMD, was written to automatically optimize and configure such a motor according to a designer’s application requirements. The optimization is done on the bases of minimum powerloss, minimum motor outer diameter, minimum motor mass, and minimum length. Using that program, two sample space applications are analyzed and applicable motor configurations are presented. KEYWORDS: Self-bearing Motor, Precision Pointing, Lorentz, Space, Magnetic Bearing Author: Barrett Alan Steele Date: December 13, 2002 Copyright Barrett A. Steele, 2002 DESIGN OF A LORENTZ, SLOTLESS SELF-BEARING MOTOR FOR SPACE APPLICATIONS By Barrett Alan Steele Director of Thesis: Dr. L. Scott Stephens Director of Graduate Studies: Dr. George Huang Date: December 13, 2002 RULES FOR THE USE OF THESIS Unpublished theses submitted for the Master’s degree and deposited in the University of Kentucky Library are as a rule open for inspection, but are to be used only with due regard to the rights of the authors. -
Analysis and Design of a Maglev Permanent Magnet Synchronous Linear Motor to Reduce Additional Torque in Dq Current Control
energies Article Analysis and Design of a Maglev Permanent Magnet Synchronous Linear Motor to Reduce Additional Torque in dq Current Control Feng Xing 1 ID , Baoquan Kou 1,*, Lu Zhang 1, Tiecheng Wang 1 and Chaoning Zhang 2 1 School of Electrical Engineering and Automation, Harbin Institute of Technology, Harbin 150001, China; [email protected] (F.X.); [email protected] (L.Z.); [email protected] (T.W.) 2 School of Electrical Engineering, KAIST, Daejeon 34141, Korea; [email protected] * Correspondence: [email protected]; Tel.: +86-451-8640-3771 Received: 21 January 2018; Accepted: 28 February 2018; Published: 5 March 2018 Abstract: The maglev linear motor has three degrees of motion freedom, which are respectively realized by the thrust force in the x-axis, the levitation force in the z-axis and the torque around the y-axis. Both the thrust force and levitation force can be seen as the sum of the forces on the three windings. The resultant thrust force and resultant levitation force are independently controlled by d-axis current and q-axis current respectively. Thus, the commonly used dq transformation control strategy is suitable for realizing the control of the resultant force, either thrust force and levitation force. However, the forces on the three windings also generate additional torque because they do not pass the mover mass center. To realize the maglev system high-precision control, a maglev linear motor with a new structure is proposed in this paper to decrease this torque. First, the electromagnetic model of the motor can be deduced through the Lorenz force formula. -
Superconducting Magnetic Bearings
Superconducting Magnetic Bearings L. Quéval GeePs, CentraleSupélec, University of Paris-Saclay, France EASISchool2 CEA Paris-Saclay [email protected] Superconducting magnetic bearings 2019-10-01 1 Overview I. A (short) introduction to superconductivity II. Superconducting maglev vehicles III. Measurement of the performances of a (stack-type) SMB IV. Modeling of a (stack-type) SMB V. Simulation of a stack-type SMB • Calibration • Validation VI. Conclusions VII. Bonus: Comsol vs. Comsol Jr. [email protected] Superconducting magnetic bearings 2019-10-01 2 I. A (short) introduction to superconductivity [email protected] Superconducting magnetic bearings 2019-10-01 3 What is a superconductor ? Type II Type I • Perfect conductivity = Zero resistance Video 1 from “BBC Story of Electricity - Superconductivity”, (47s – 1m40s), © BBC. • Meissner effect Video 2 from “How superconducting magnetic levitation works ?”, (1m25s – 3m25s), © I.G. Chen. • Flux trapping effect [email protected] Superconducting magnetic bearings 2019-10-01 4 What is a superconductor ? Hc H [1] B.B. Jensen, A.B. Abrahamsen, M.P. Sørensen, J.B. Hansen, “A course on applied superconductivity shared by four departments ,” US-China Education Review A, vol. 3, no. 3, 141-152, 2013. [email protected] Superconducting magnetic bearings 2019-10-01 5 Superconductors development history © Wikipedia 0 K = -273.15°C [email protected] Superconducting magnetic bearings 2019-10-01 6 Conductors 1962 1986 Discovery of high temperature 1987 superconductors (HTS) 1988 2001 © Adapted from X. Obradors and T. Izumi. [email protected] Superconducting magnetic bearings 2019-10-01 7 Bulks YBCO bulk [1] GdBCO bulk [2] 40 x 40 x 15 mm D = 41 mm Bi-2223 [3] D = 59 mm, L = 100 mm [1] Y. -
Effects of Operational Losses in Active Magnetic Bearing Designs
Prince Owusu-Ansah.et al.Int. Journal of Engineering Research and Applicationwww.ijera.com ISSN: 2248-9622, Vol. 6, Issue 4, (Part - 7) April 2016, pp.01-04 RESEARCH ARTICLE OPEN ACCESS Effects of Operational Losses in Active Magnetic Bearing Designs. Prince Owusu-Ansah1, Alex Frimpong Justice2,Philip Kwabena Agyeman3, Ahwah Tettey Francis4Rhoda Afriyie Mensah5 1School ofMechanical andElectronic Engineering, Wuhan University OfTechnology, P.R China, 430070 Mechanical Engineering Department, Kumasi Polytechnic, P.O Box 854, Kumasi Ghana, West Africa. 2Mechanical Engineering Department, Kumasi Polytechnic, P.O Box 854, Kumasi Ghana, West Africa 3School ofMechanical andElectronic Engineering, Wuhan University OfTechnology, P.R China, 430070 Mechanical Engineering Department Kwame Nkrumah University Of Technology, Kumasi Ghana. West Africa 4School ofMechanical andElectronic Engineering, Wuhan University Of Technology, P.R China, 430070 5School ofAutomotive Engineering, Wuhan University Of Technology, P.R China, 430070 ABSTRACT This paper studies the effects of different forms of operational losses that are associated with active magnetic bearing designs.Active magnetic bearings are generally considered as having much lower frictional losses as compared to fluid and roller bearings, however AMBs are considered as more complex mechatronic systems, associated with various potential power loss mechanisms during it cycle of operation. Minimizing of losses consist of various measures and depends largely on the requirements of the application,among all these losses, aerodynamic losses are classified as been the more dominant in modern high speed applications and turbomachinery especially in expanders and compressors where its working gases are considered to be under very high pressures and temperaturesVarious forms of losses such as hysteresis, eddy current, iron, aerodynamic have been discussed. -
Hyperloop Integration to Reach the NOAH Concept
Tesi Magistrale Ing. Energetica e Nucleare Innovazione nella produzione energetica High-speed trains comparison to Hyperloop: energy and sustainability Hyperloop safety analysis and integrations to reach the NOAH concept Candidate Matteo Riviera Relators Andrea Carpignano Giacomo Bersano 2 Riviera M. –Innovazione nella produzione energetica – A.A. 2017/18 3 Acknowledgments Tanks to my family, for all you do to make me a better man, for all your support, for your gratitude and your teachings. I always keep you in my heart. Thanks to Polito staff, you can be proud of your work. Even if sometimes I felt like there was a wall between the world of teachers and the world of scholars. Thanks to my friends, always helpful and ready to show me other points of view in adverse situations. Thanks to Ikos staff, even if it was for a short time, it was a beautiful internship. Thanks to Carpene family, to host me like one of the family in your beautiful Beresina. Thank you all, if I can walk straight is because I found you in my way. Mostly thanks to my mother, that embolden myself from the very beginning and she will never stop to coach her little children. Riviera M. –Innovazione nella produzione energetica – A.A. 2017/18 4 Executive summary In a time of global changes, where humanity wakes up after a period of indiscriminate exploitation of resources and uncontrolled pollution of air, ground and sea, every chance to reduce damages to the environment must be taken on the fly. Transportation sector consumes, in Europe, one third of total end use energy relying for 90% over fossil fuels, a problem from environmental point of view.