Table of Contents
Total Page:16
File Type:pdf, Size:1020Kb
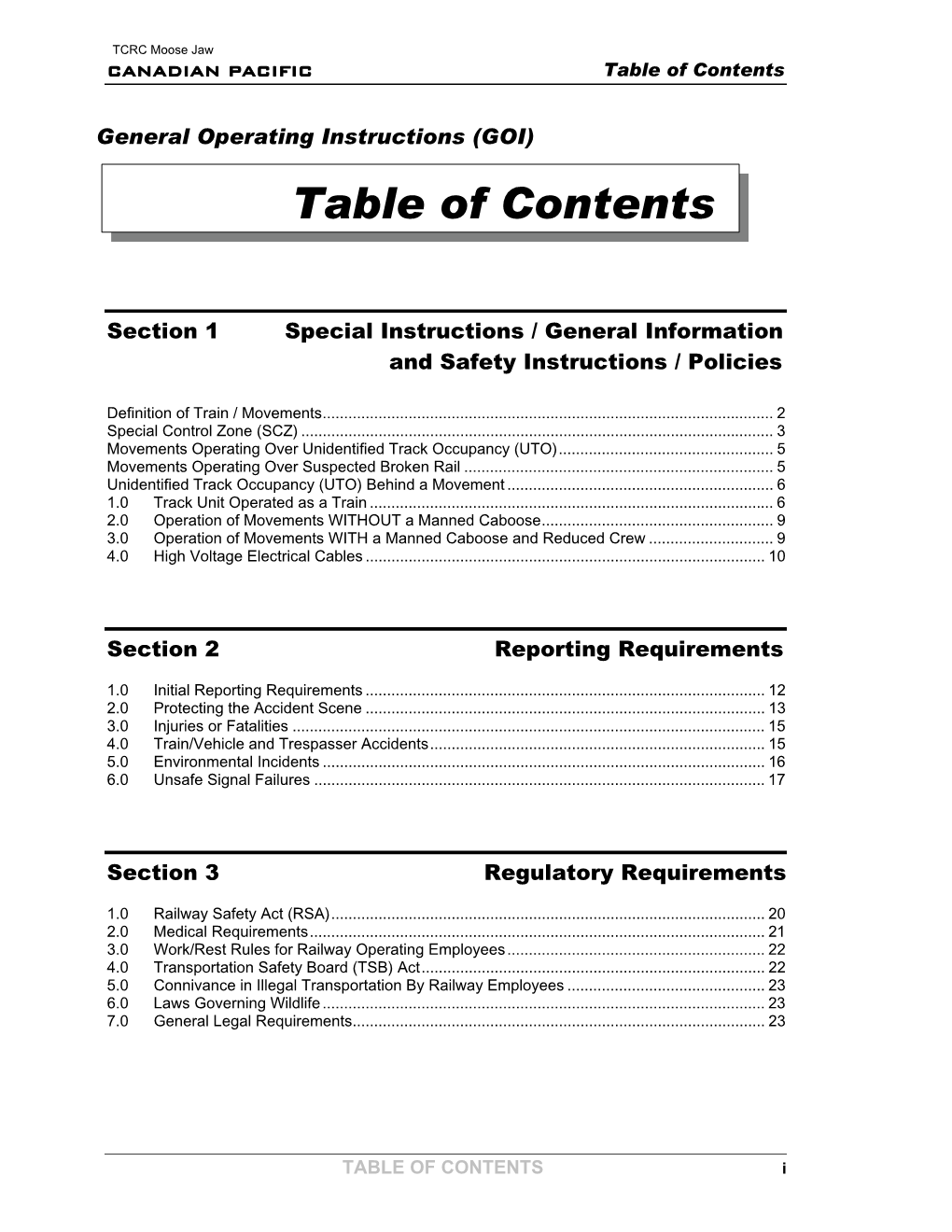
Load more
Recommended publications
-
Midnight Train to Georgemas Report Final 08-12-2017
Midnight Train to Georgemas 08/12/2017 Reference number 105983 MIDNIGHT TRAIN TO GEORGEMAS MIDNIGHT TRAIN TO GEORGEMAS MIDNIGHT TRAIN TO GEORGEMAS IDENTIFICATION TABLE Client/Project owner HITRANS Project Midnight Train to Georgemas Study Midnight Train to Georgemas Type of document Report Date 08/12/2017 File name Midnight Train to Georgemas Report v5 Reference number 105983 Number of pages 57 APPROVAL Version Name Position Date Modifications Claire Mackay Principal Author 03/07/2017 James Consultant Jackson David Project 1 Connolly, Checked Director 24/07/2017 by Alan Director Beswick Approved David Project 24/07/2017 by Connolly Director James Principal Author 21/11/2017 Jackson Consultant Alan Modifications Director Beswick to service Checked 2 21/11/2017 costs and by Project David demand Director Connolly forecasts Approved David Project 21/11/2017 by Connolly Director James Principal Author 08/12/2017 Jackson Consultant Alan Director Beswick Checked Final client 3 08/12/2017 by Project comments David Director Connolly Approved David Project 08/12/2017 by Connolly Director TABLE OF CONTENTS 1. INTRODUCTION 6 2. BACKGROUND INFORMATION 6 2.1 EXISTING COACH AND RAIL SERVICES 6 2.2 CALEDONIAN SLEEPER 7 2.3 CAR -BASED TRAVEL TO /FROM THE CAITHNESS /O RKNEY AREA 8 2.4 EXISTING FERRY SERVICES AND POTENTIAL CHANGES TO THESE 9 2.5 AIR SERVICES TO ORKNEY AND WICK 10 2.6 MOBILE PHONE -BASED ESTIMATES OF CURRENT TRAVEL PATTERNS 11 3. STAKEHOLDER CONSULTATION 14 4. PROBLEMS/ISSUES 14 4.2 CONSTRAINTS 16 4.3 RISKS : 16 5. OPPORTUNITIES 17 6. SLEEPER OPERATIONS 19 6.1 INTRODUCTION 19 6.2 SERVICE DESCRIPTION & ROUTING OPTIONS 19 6.3 MIXED TRAIN OPERATION 22 6.4 TRACTION & ROLLING STOCK OPTIONS 25 6.5 TIMETABLE PLANNING 32 7. -
CP's North American Rail
2020_CP_NetworkMap_Large_Front_1.6_Final_LowRes.pdf 1 6/5/2020 8:24:47 AM 1 2 3 4 5 6 7 8 9 10 11 12 13 14 15 16 17 18 Lake CP Railway Mileage Between Cities Rail Industry Index Legend Athabasca AGR Alabama & Gulf Coast Railway ETR Essex Terminal Railway MNRR Minnesota Commercial Railway TCWR Twin Cities & Western Railroad CP Average scale y y y a AMTK Amtrak EXO EXO MRL Montana Rail Link Inc TPLC Toronto Port Lands Company t t y i i er e C on C r v APD Albany Port Railroad FEC Florida East Coast Railway NBR Northern & Bergen Railroad TPW Toledo, Peoria & Western Railway t oon y o ork éal t y t r 0 100 200 300 km r er Y a n t APM Montreal Port Authority FLR Fife Lake Railway NBSR New Brunswick Southern Railway TRR Torch River Rail CP trackage, haulage and commercial rights oit ago r k tland c ding on xico w r r r uébec innipeg Fort Nelson é APNC Appanoose County Community Railroad FMR Forty Mile Railroad NCR Nipissing Central Railway UP Union Pacic e ansas hi alga ancou egina as o dmon hunder B o o Q Det E F K M Minneapolis Mon Mont N Alba Buffalo C C P R Saint John S T T V W APR Alberta Prairie Railway Excursions GEXR Goderich-Exeter Railway NECR New England Central Railroad VAEX Vale Railway CP principal shortline connections Albany 689 2622 1092 792 2636 2702 1574 3518 1517 2965 234 147 3528 412 2150 691 2272 1373 552 3253 1792 BCR The British Columbia Railway Company GFR Grand Forks Railway NJT New Jersey Transit Rail Operations VIA Via Rail A BCRY Barrie-Collingwood Railway GJR Guelph Junction Railway NLR Northern Light Rail VTR -
CRO 0209.Pdf
www.canadianrailwayobservations.com Updated 04/02/2009 CANADIAN NATIONAL CN Locomotives retired since last issue: (Previous retirement October 30th) GTW GP9r 4635 on January 28th (*Sold to MNNR January 19th … see below) On January 2nd 2009, Walter Pfefferle caught GODERICH-EXETER (GEXR) GP40 4019 pulling out of the EMCC plant in London, Ontario with these fully painted and brand new CN SD70M-2’s: 8852, 8854, 8856 and 8858. As well CN 8850-8867 were released in early January 2009. http://railfan.thegrebs.com/CN/GEXR_4019_EMD_London_Ont_1_2_09 (GEXR GP40) http://railfan.thegrebs.com/CN/CN_8854_London_1_2_09 3/4 http://railfan.thegrebs.com/CN/CN_8858_London_1_2_09 3/4 http://railfan.thegrebs.com/CN/CN_8856_London_1_2_09 3/4 http://railfan.thegrebs.com/CN/CN_8852_London_1_2_09 3/4 http://railfan.thegrebs.com/CN/CN_8852a_London_1_2_08 Rear shot. New CN Power: The following new SD70M-2 sightings came from several CRO readers this month: On January 14th, CN Intermodal 194 (which is a very lucrative UPS contracted train and operates between Chicago-Memphis-Jackson-New Orleans), departed Markham with brand new CN 8853, CN 5513, CN 9543, 150 cars, 7141 tons and 9845-feet of train. On January 13th at Chappel Jct, (near Saskatoon, SK), CN 104 had CN 8865 leading. On January 13th, CN 198 had CN 8855-2643 for power at Chappel Jct. January 11th, CN train Q120 with 2525-5698 and new CN SD70M-2 8863 with 9823-feet of train at 8767 tons enroute to Halifax, NS and arrived on the 12th. While on the Montmagny Subdivision, SD70M-2 8863 reportedly had a minor mechanical issue that was resolved while in transit. -
Stronger Ties: a Shared Commitment to Railway Safety
STRONGER TIES: A S H A R E D C O M M I T M E N T TO RAILWAY SAFETY Review of the Railway Safety Act November 2007 Published by Railway Safety Act Review Secretariat Ottawa, Canada K1A 0N5 This report is available at: www.tc.gc.ca/tcss/RSA_Review-Examen_LSF Funding for this publication was provided by Transport Canada. The opinions expressed are those of the authors and do not necessarily reflect the views of the Department. ISBN 978-0-662-05408-5 Catalogue No. T33-16/2008 © Her Majesty the Queen in Right of Canada, represented by the Minister of Transport, 2007 This material may be freely reproduced for non-commercial purposes provided that the source is acknowledged. Photo Credits: Chapters 1-10: Transport Canada; Appendix B: CP Images TABLE OF CONTENTS 1. INTRODUCTION ...............................................................1 1.1 Rationale for the 2006 Railway Safety Act Review . .2 1.2 Scope . 2 1.3 Process ....................................................................................3 1.3.1 Stakeholder Consultations . .4 1.3.2 Research . 6 1.3.3 Development of Recommendations .......................................6 1.4 Key Challenges for the Railway Industry and the Regulator.................7 1.5 A Word of Thanks .................................................................... 10 2. STATE OF RAIL SAFETY IN CANADA ...................................11 2.1 Accidents 1989-2006 ................................................................. 12 2.2 Categories of Accidents . 13 2.2.1 Main Track Accidents...................................................... 14 2.2.2 Non-Main Track Accidents ............................................... 15 2.2.3 Crossing and Trespasser Accidents . 15 2.2.4 Transportation of Dangerous Goods Accidents and Incidents . 17 2.3 Normalizing Accidents . 18 2.4 Comparing Rail Safety in Canada and the U.S. -
Financial Highlights
Financial Highlights (in thousands, except per share data) Years Ended December 31 1999 1998 Income Statement Data Operating revenues $175,586 $147,472 Operating income $22,368 $19,568 Net income $12,533 $11,434 Diluted earnings per common share $2.76 $2.19 Weighted average number of shares of common stock–diluted 4,540 5,229 Balance sheet data as of period end Total assets $301,940 $216,760 Total debt $108,376 $65,690 Stockholders’ equity $81,829 $74,537 GWI is a holding company whose subsidiaries own and operate regional freight railroads and provide related rail services. The Company generates revenues primarily from the movement of freight over track owned or operated by its railroads. The Company also generates nonfreight revenues primarily by providing freight car switching and rail-related services to industrial companies with extensive railroad facilities within their complexes. Revenues, Operating and Net Income Revenue Sources By Business Segment $180 by 1999 revenues $160 North American Railroad (68.9%) $30 $140 Industrial Switching (6.5%) $120 $20 Australian Railroad (24.6%) $100 $15 $80 (in millions) $60 $10 (in millions) Income Revenues $40 $5 $20 $0 $0 1995 1996 1997 1998 1999 (in thousands) Revenues $53,387 $77,795 $103,643 $147,472 $175,586 Operating Income 6,572 13,994 16,443 19,568 22,368 Net Income 1,657 5,905 7,998 11,434 12,533 Letter to the Shareholders Our financial performance in 1999, our centennial year, was the best in the Company’s history. Income after taxes increased 9.7 percent to $12.5 million from $11.4 million in 1998. -
How Railways Can Be Part of Canada's Climate Change Solution
How railways can be part of Canada’s climate change solution A submission by the Railway Association of Canada July 1, 2016 (originally submitted on May 31) Version 2 – update Version 2 – update Submission to Environment and Climate Change Canada Table of Contents 1 Canada’s railway sector .......................................................................................... 4 Climate change policy in the transportation sector ................................................................... 5 2 How railways can be part of Canada’s climate change solution ......................... 6 3 Policy considerations for the future ...................................................................... 9 4 Railway emissions management programs and performance .......................... 10 5 Our recommendations .......................................................................................... 12 Modal shift is a mitigation opportunity for Canada .................................................................. 12 Revenues collected from carbon pricing strategies should be reinvested into rail ................... 12 The Government needs to support clean technology and innovation in the rail sector ............ 13 6 Concluding remarks .............................................................................................. 13 Appendix A: List of RAC Members 2 Submission to Environment and Climate Change Canada Acronym Table AMT Agence métropolitaine de transport CO2e CO2 equivalent COP Conference of Parties CDP Carbon Disclosure -
2008 Corporate Profile + Fact Book
2008 corporate profile + fact book 2008 corporate profile + fact book table of contents 4 Financial summary 44 Integrated Operating Plan (IOP) 6 Key metrics 45 Interline management 10 System map (density) 46 Co-production 11 Corporate history 48 Information technology 12 Recent acquisition: DM&E 49 Safety 13 Company overview 51 Environment 14 Network 55 Community relations 17 Markets 57 Human resources i. Bulk 58 Labour relations ii. Merchandise iii. Intermodal 61 Governance 36 Canadian Pacific Logistics Solutions (CPLS) 63 Executive profiles 37 Motive power 65 Board of Directors 38 Freight car fleet 66 Financial data 40 Rail yards and intermodal terminals 70 Glossary 42 Repair facilities TSX / NYSE | CP forward-looking information This Corporate Profile and Fact Book contains certain forward-looking statements within the meaning of the Private Securities Litigation Reform Act of 1995 (United States) and other relevant securities legislation relating but not limited to Canadian Pacific’s (CP) operations, anticipated financial performance, business prospects and strategies. Forward-looking information typically contains statements with words such as “anticipate”, “believe”, “expect”, “plan” or similar words suggesting future outcomes. Readers are cautioned to not place undue reliance on forward-looking information because it is possible that we will not achieve predictions, forecasts, projections and other forms of forward-looking information. In addition, except as required by law, we undertake no obligation to update publicly or otherwise -
2014 Maine State Rail Plan
Maine State Rail Plan TABLE OF CONTENTSview Chapter 1 Framework of the Maine State Rail Plan 1.1 Purpose of the State Rail Plan 1.1 1.2 Visions, Goals, Objectives of the Maine State Rail Plan 1.3 1.3 Transportation and Rail Planning in Maine 1.6 . Figure 1-1: MaineDOT Organizational Chart 1.7 . Figure 1-2: Maine’s MPO Areas 1.10 . Figure 1-3: Regional Planning and Development Councils 1.11 1.4 Public and Stakeholder Involvement 1.12 1.5 Review of Freight and Passenger Rail Planning Studies 1.17 1.6 Evaluation Criteria 1.18 Chapter 2 Freight Rail System 2.1 Overview 2.1 . Figure 2-1: North American Class I Rail Connections 2.2 . Figure 2-2: Map of MM&A Abandonment 2.6 . Figure 2-3: State of Maine Owned Rail Status 2.10 2.2 Freight Rail Industry Development 2.10 2.3 Maine’s Freight Railroad Facilities 2.12 2.4 International, National and Regional Context 2.21 . Figure 2-4: Canadian Class I Connections to Maine System 2.21 . Figure 2-5: Northeast U.S. Rail Freight System 2.22 . Figure 2-6: NS, CP, PAS and PAR Corridors 2.23 . Figure 2-7: Railroad Return on Investment and Cost of Capital 2.24 2.5 Freight Rail Issues and System Constraints 2.24 . Figure 2-8: Estimated National Highway System Peak-Period Congestion 2.25 . Figure 2-9: Estimated Rail Freight Service Levels, 2035 2.25 . Figure 2-10: Rail Clearance and Weight Constraints 2.28 . -
2018 Rail Trends
RAIL TRENDS 2018 www.railcan.ca TM Yukon Territory Northwest Territories Nunavut C a n a d a Hay River British Columbia KR Schefferville Churchill Newfoundland and Labrador Alberta Labrador City Prince QIO Rupert CN HBRY QNSL Saskatchewan CFRR CN KCR CFA Quebec AMIC Sept-Îles Edmonton Manitoba SCFG PPrincerince CTRW EEdwarddward Moosonee IIslandsland CP BRRBRR CN SSaskatoonaskatoon RS New Ontario Brunswick Moncton CCalgaryalgary CN CBNS LLMRMR CN ONR Vancouver NBSR CN BCR BSR RReginaegina QQuébecuébec SRY KFR CEMR Halifax BNSF CMQ Nova CP CP CP NCR CFQG WinnipegWinnipeg CFL SLQ Scotia GWR EEXOXO BTCR Montréal Sherbrooke Thunder Bay SSudburyudbury HCRY OVR CSX Class 1 railways BCRY Shortline railways Toronto Passenger railways OBRY TTR GEXR PCHR CSX SOR OSR Detroit STER Windsor ETR RAC members as of Dec. 31, 2017 ISBN: 978-1-927520-09-3 Yukon Territory Northwest Territories Nunavut C a n a d a Hay River British Columbia KR Schefferville Churchill Newfoundland and Labrador Alberta Labrador City Prince QIO Rupert CN HBRY QNSL Saskatchewan CFRR CN KCR CFA Quebec AMIC Sept-Îles Edmonton Manitoba SCFG PPrincerince CTRW EEdwarddward Moosonee IIslandsland CP BRRBRR CN SSaskatoonaskatoon RS New Ontario Brunswick Moncton CCalgaryalgary CN CBNS LLMRMR CN ONR Vancouver NBSR CN BCR BSR RReginaegina QQuébecuébec SRY KFR CEMR Halifax BNSF CMQ Nova CP CP CP NCR CFQG WinnipegWinnipeg CFL SLQ Scotia GWR EEXOXO BTCR Montréal Sherbrooke Thunder Bay SSudburyudbury HCRY OVR CSX Class 1 railways BCRY Shortline railways Toronto Passenger railways OBRY TTR GEXR -
XXXV December 2009
mini-SITREP XXXV Edited and Printed by the Kenya Regiment Association (KwaZulu-Natal) – December 2009 KRA/EAST AFRICA SCHOOLS DIARY OF EVENTS: 2010 KRA (Australia) Sunshine Coast Curry Lunch, Power Boat Club, Caloundra Sun 14th Mar Curry Lunch, Oxley Golf Club Sun 21st Aug (TBC) KRA Boat Cruise 10th to 16th April Contact: Giles Shaw. 07-3800 6619 <[email protected]> Sydney’s Gold Coast. Ted Downer. 02-9769 1236 <[email protected]> Sat 28th Nov (TBC) East Africa Schools - Australia Annual Picnic. Lane Cove River National Park, Sydney Sun 24th Oct Contact: Dave Lichtenstein 01-9427 1220 <[email protected]> KRAEA Remembrance Sunday and Curry Lunch at Nairobi Clubhouse Nov (TBC) Contact: Dennis Leete <[email protected]> KRAENA - England Curry Lunch: St Cross Cricket Ground, Winchester Jul (TBC) AGM and Lunch: The Rifles London Club, Davies St Nov (TBC) Contact: John Davis. 01628-486832 <[email protected]> SOUTH AFRICA Cape Town: Lunch at Mowbray Golf Course. 12h30 for 13h00 TBA Contact: Jock Boyd. Tel: 021-794 6823 <[email protected]> Johannesburg: Lunch at Rivonia Recreation Club Apr & Oct (TBC) Contact: Keith Elliot. Tel: 011-802 6054 <[email protected]> KwaZulu-Natal: Saturday quarterly lunches: Venue TBA - 13 Mar, 12 Jun; 11 Sep; 11 Dec Contact: Anne/Pete Smith. Tel: 033-330 7614 <[email protected]> or Jenny/Bruce Rooken-Smith. Tel: 033-330 4012 <[email protected]> EA Schools’ Lunch: Stonehaven Castle, Shongweni Oct (TBC) Contact: Dave Leslie. Mob: 084-544 0419 <[email protected]> KRA (New Zealand) Curry Lunch, Brigham Restaurant, Auckland Feb/Mar (TBC) Spring Lunch at Soljans Winery, Auckland Sep/Oct (TBC) Contact Brian McCabe. -
Escorted Holidays by Rail
Escorted Holidays By Rail March 2021 – February 2022 Offering the best in rail travel Since 1998 “One of the world’s best and most innovative rail touring companies” – The Daily Mail Enjoy the freedom of travel with THE PTG TOURS TRAVEL EXPERIENCE GROUP TRAVEL Let us guide you through unfamiliar territory in the most In today’s world the group tour has become an opportunity comfortable and relaxing way possible. We journey on some to travel with other likeminded people who share common of the most scenic routes in the world. Simply enjoy the world interests. At PTG Tours our itineraries further enhance the passing you by as you travel in comfort to your destination. experience by visiting places not on the itineraries of other tour Your trusted guide will be traveling with you to make sure you groups. However, our itineraries are designed to give you the get the best and most unique experiences. We make sure your choice of having your independence from the group by giving trip is relaxed and problem free. you the option to take time out to enjoy your own Our guides have a passion for travel and extensive tour day or evening experience. experience over many years but from time to time we join up HOTELS with local guides, in addition to our tour guide, who have local We aim to provide stays at good hotels and these will vary insights and take your experience to another level that might depending on the type of tour. Generally the hotels we will use be missed if travelling without a guide. -
50764 Service Date – May 17, 2021 Eb Surface
50764 SERVICE DATE – MAY 17, 2021 EB SURFACE TRANSPORTATION BOARD DECISION Docket No. FD 36514 CANADIAN NATIONAL RAILWAY COMPANY, GRAND TRUNK CORPORATION, AND CN’S RAIL OPERATING SUBSIDIARIES —CONTROL— KANSAS CITY SOUTHERN, THE KANSAS CITY SOUTHERN RAILWAY COMPANY, GATEWAY EASTERN RAILWAY COMPANY, AND THE TEXAS MEXICAN RAILWAY COMPANY Digest:1 The Board determines that this proposed transaction will be subject to the agency’s current merger regulations and denies a motion to approve a proposed voting trust agreement, without prejudice, as incomplete. Decision No. 3 Decided: May 17, 2021 Canadian National Railway Company (CNR), Grand Trunk Corporation (GTC), and their rail operating subsidiaries (collectively, with CNR and GTC, CN)2 have notified the Surface Transportation Board (Board) of their intent to file an application seeking authority for the acquisition of control by CNR, through its wholly owned subsidiary Brooklyn Merger Sub, Inc. (Brooklyn Merger Sub), of Kansas City Southern, and through it, of The Kansas City Southern Railway Company (KCSR), Gateway Eastern Railway Company, and The Texas Mexican Railway Company (collectively, KCS), in the event that Kansas City Southern accepts 1 The digest constitutes no part of the decision of the Board but has been prepared for the convenience of the reader. It may not be cited to or relied upon as precedent. See Pol’y Statement on Plain Language Digs. in Decisions, EP 696 (STB served Sept. 2, 2010). 2 CN’s rail operating subsidiaries in the United States include Illinois Central Railroad Company; Wisconsin Central Ltd.; Grand Trunk Western Railroad Company; Bessemer and Lake Erie Railroad Company; Chicago, Central & Pacific Railroad Company; Cedar River Railroad Company; The Pittsburgh & Conneaut Dock Company; Sault.