Development of New Methods for Characterizing Uniformity of Yankee Coatings
Total Page:16
File Type:pdf, Size:1020Kb
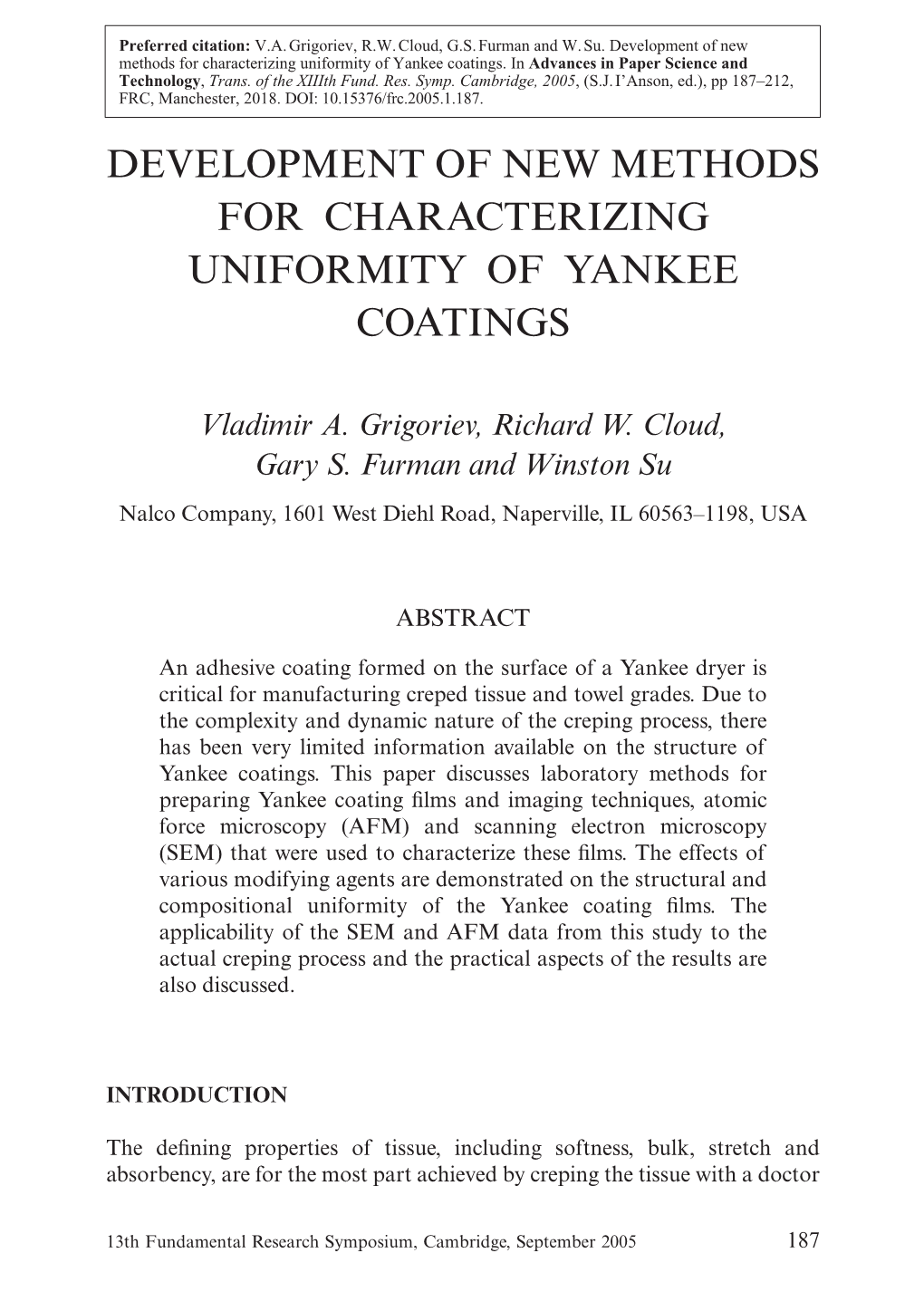
Load more
Recommended publications
-
Hazards in Paper and Pulp Industries – from an Engineering Insurance Perspective
Hazards in paper and pulp industries – from an engineering insurance perspective. IMIA WGP 49 (06) By Aki Ahonen Pohjola Ingvar Bodin Zurich Milan Dinets Ingosstrakh Mats Gådin If P&C Chairman Felix Staub Swiss Re Thomas Åström Pohjola Presented at the IMIA Conference in Boston, 12 September 2006. 1 Table of Contents 1 Introduction 4 1.1 General trends in the pulp and paper industry in the world. 4 1.2 Content of this paper 5 1.3 References 6 2 Technical descriptions and development 6 2.1 Pulp 6 2.1.1 Sulphate pulping (“Kraft” pulping) 6 2.1.1.1 Risks related to Kraft pulping 6 2.1.1.1.1 New chemicals for bleaching processes 6 2.1.1.1.2 Size increase of key machinery 7 2.1.2 Sulphite pulping 8 2.1.2.1 Special risk of sulphite pulping 8 2.1.3 Recycled pulping and deinked pulps 9 2.1.4 Mechanical pulp 9 2.2 Energy and chemical recovery 9 2.2.1 Kraft recovery boiler 10 2.2.1.1 General 10 2.2.1.2 Description 10 2.2.1.3 Special considerations 12 2.2.1.4 Trends in designing new recovery boilers 13 2.2.2 Black liquor gasification combined cycle 14 2.3 Paper Machine 14 2.3.1 Paper and board production in general 14 2.3.2 Contemporary technology and trends of paper and board machines 15 2.3.2.1 Dilution controlled head-box 15 2.3.2.2 Shoe press 16 2.3.2.3 Impingement drying 17 2.3.3 Tissue paper production 18 2.3.4 Technical trends and risks in general 19 2.4 Environmental aspects 20 2.4.1 Water treatment 20 2.4.2 Air purification 21 2.5 References 22 3 Loss prevention 23 3.1 General considerations 23 3.2 The most frequently used machine diagnostic methods 23 3.3 Critical components 24 3.3.1 Conveyors 24 3.3.2 Chippers 24 3.3.3 Digesters 25 3.3.4 Diffusers 25 3.3.5 Black liquor recovery boiler 26 3.3.6 Boiler fans 28 3.3.7 Lime kiln 29 3.3.8 Steam turbo sets 29 3.3.9 Main transformers 30 3.3.10 Paper machine 31 3.3.11 Yankee Dryers 31 2 3.4 References 32 4 EML / PML estimation. -
Introduction to Process and Properties of Tissue Paper
Introduction to process and properties of tissue paper enrico galli, 2017 Enrico Galli self-presentation • I was born in Viareggio (Lucca county or “the so called tissue valley”) Tuscany - Italy • Graduated in Chemical Engineering at University of Pisa in 1979 • Process and project engineer and then technical manager in oil industry (oil refineries and spent lube oil re-refining) in GULF, API, AGIP in Italy • Technical manager in chemical and consumer products company (soap, detergents, derivate from fatty acids, sanitary gloves, tissue paper) in Italy. • Since 1984 in paper and tissue business: • Italy: Tissue (PM, PBD, CON), Newspaper (PM), Cardboard paper (PM, MM) • Estónia: Tissue (PM, CEO) • France: Tissue (PM) • Hungary: Tissue (CON) • Nigéria: Tissue (CON) • Romania: Tissue (PM, PBM, MM, CON), Writing paper (PBM) • Rússia: Tissue (PM) • Spain: Tissue (PBM) • UK: Tissue (PBM) • Cooperation with following main European Tissue Companies: Annunziata (now WEPA – Italy), GP (now Lucart – Italy), Horizon Tissue (Estonia), Imbalpaper (now Sofidel – Italy), Kartogroup (now WEPA – Italy, France, Spain), Montebianco (Romania), Pehartec (Romania), Perini (now Sofidel – Romania, UK), Siktyvkar Tissue Group (Russia), Vaida Papir (Hungary)… and now proudly NAVIGATOR in Portugal! • I have been supporting Sales and Marketing Teams for strategic planning as well as for products development in Baltic Countries, BENELUX, Denmark, Finland, France, Germany, Hungary, Ireland, Italy, Norway, Poland, Romania, Russia, Spain, Sweden, UK. • Since 1998 I have -
Energy Audit Uncovers Major Energy Savings for Paper Mill
Energy Audit Uncovers Major Energy Savings for Paper Mill Jerry L. Aue, Aue Energy Consulting Sue Pierce, Johnson Corporation ABSTRACT Energy and financial savings are presented through the results of a recent Stora Enso North America – Stevens Point Paper Machine No. 34 (PM34) dryer section feasibility study and rebuild. The project, funded partially by the Wisconsin Focus on Energy program, increased the effectiveness of the paper machine’s dryer section through an improved dryer drainage system, the reduction of uncondensed steam and the addition of differential pressure controls. Improvements in energy efficiency were carefully documented to demonstrate significant reduction of energy use and increases in production achieved during each phase of the rebuild. This paper tracks the results from the dryer section feasibility study through the installation of the Dryer Management System™ control software. The four-step approach is discussed as follows: • Dryer Section Feasibility Study. This audit quantified the potential energy savings and outlined a plan to upgrade the dryer section. • Phase 1 – After Section Rebuild. Steam system modifications and equipment upgrades were made to the after section. • Phase 2 – Pre-dryer Section Rebuild. Modifications similar to those made to the after section were continued in the pre-dryer section. • Phase 3 - Dryer Section Rebuild. The final stages of the project included the installation of new valves, transmitters and a complete supervisory control system. The paper describes the upgrade and details the benefits of each phase. The energy use and paper production in March of 2005 are compared to the same information from March of 2004. Observed benefits include energy savings of 4,500 pounds per hour of steam and improvements in machine production, runnability and paper quality. -
Surface Temperature Measurement on a Yankee Cylinder During Operation
Faculty of Technology & Science Department of Physics and Electrical Engineering Henrik Jackman Surface temperature measurement on a Yankee cylinder during operation Engineering Physics Master Thesis Date/Term: 2009-06-10 Supervisors: Prof. Kjell Magnsson, Jonas Cederlöf, Hans Ivarsson, Karl-Johan Tolfsson Examiner: Prof. Lars Johansson Serial Number: X-XX XX XX Karlstads universitet 651 88 Karlstad Tfn 054-700 10 00 Fax 054-700 14 60 [email protected] www.kau.se Abstract The Yankee cylinder is used in most of Metso Paper's machines. It is used in the drying and creping process. Since the outcome of these processes largely aect the paper's nal quality it is important that the Yankee cylinder behaves in a controlled fashion. One important parameter aecting the behaviour of the Yankee cylinder is its surface temperature. The objective of this thesis was to search for and evaluate methods for measuring the surface temperature of a Yankee cylinder during operation. Metso Paper is looking for a method having an accuracy of ∆T = 1◦C, a response time of t < 10 ms, and being portable. Three dierent instruments were tested during the thesis: • Thermophone, a contact measurement device currently used by Metso Paper. • RAYNGER MX4, a pyrometer from Raytek. • FLIR P640, a thermographic camera with a 640x480 focal plane array from FLIR. The instruments were tested by performing measurements on Metso Paper's pilot machine in Karlstad during operation. The measurements revealed drawbacks for all three instruments. The biggest drawbacks of the Thermophone was its response time, t ≈ 5 min, and its dependence on the frictional heating of the teon cup. -
Paper Glossary
PAPER GLOSSARY A Abrasion Resistance Alcohol/Alcohol Substitutes The level at which paper can withstand continuous scuffing or Liquids added to the fountain solution of a printing press to rubbing. reduce the surface tension of water. Absorption Aluminum Plate The properties within paper that cause it to absorb liquids A metal press plate used for moderate to long runs in offset (inks, water, etc.) which come in contact with it. lithography to carry the image. Announcement Cards Accordion Fold Cards of paper with matching envelopes generally used for A binding term describing a method of folding paper. When social stationery, announcements, weddings, greetings, etc. unfolded it looks like the folds of an accordion. Antique Finish Acetate Proof A paper finish, usually used in book and cover papers, that has A transparent, acetate printing proof used to reproduce a tactile surface. Usually used in natural white or creamwhite anticipated print colors on a transparent acetate sheet. Also colors. called color overleaf proof. Apron Acid Free Extra space at the binding edge of a foldout, usually on Paper made in a neutral pH system, usually buffered with a French fold, which allows folding and tipping without calcium carbonate. This increases the longevity of the paper. interfering with the copy Acidity Archival Degree of acid found in a given paper substance measured by Acid free or neutral paper that includes a minimum of 2% pH level. From 0 to 7 is classified acid as opposed to 7 to 14, calcium carbonate to increase the longevity of the paper. which is classified alkaline. Artificial Parchment Against the Grain Paper produced with poorly formed formation. -
Papermaking Support
PAPERMAKING SUPPORT Process and Papermaking Capabilities For nearly 100 years, Solenis has helped pulp and paper mills all over the world optimize performance and efficiency with a wide array of innovative specialty chemicals and monitoring and control equipment. Our customers rely on our deep expertise, our on-site management approach, and our seasoned team of application experts and research scientists to remain competitive in increasingly challenging environments. The Customer Applications Laboratories, which include Papermaking Support, serve as hubs of our application expertise, ensuring that Solenis is prepared to meet the needs of our customers today and into the future. Comprehensive services. Global reach. The Global Customer Applications Laboratories, serve as hubs for our application expertise. We work closely with our sales, application, and research teams to understand our customers’ systems and problems as well as assist in the development of new treatment technologies. This ensures that Solenis is prepared to address the current and future needs of our customers. Solenis’ Applications Labs support our customers globally with laboratories located in Wilmington, Delaware; Paulínia, Brazil; Krefeld, Germany; Barendrecht, the Netherlands; Drammen, Norway; Terrassa, Spain; and Shanghai, China. They are staffed with experienced scientists and technicians, who use process simulation tools and methods to recommend effective improvements with the goal to enhance our customers’ papermaking productivity and product quality. Retention and Drainage Unique techniques used to recommend customized A thorough understanding of pulp, wet end chemistry, additives, treatments are: and operating conditions allows optimization of balanced retention • System surveys including count/particle size distribution/ and drainage/dewatering performance leading to improved paper area, image and charge analysis and board machine productivity, efficiency, and quality. -
Advantage Yankee Valmet Yankee Dryer Solutions World’S Only Complete Range of Yankee Solutions
Advantage Yankee Valmet Yankee dryer solutions World’s only complete range of Yankee solutions More than a century after it was invented, the Yankee is still the heart of the tissue machine. Nothing has surpassed it. Of course, technical development has been extensive. Modern Yankee cylinders are safe and reliable, and offer great performance along with energy efficiency. Customer needs have evolved, too, and not all tissue-making is the same. That’s why we believe in providing the ability to choose: offering both steel and cast iron Yankee cylinders. And we are the only manufacturer that can do so. We also offer the most complete range of machines and solutions for tissue, paper and board manufacturing. Our experience. Uncompromising safety Your advantage. and quality control More than 600 successful deliveries of As a central part of the tissue making customers in every phase. Combining Yankee dryers for different applications process, the Yankee cylinder must be your knowledge about the character- have given us tremendous experience in good condition for the rest of the istics required for the end product with and knowledge. We continuously body to perform at its best. Safety, our expertise in Yankee technology develop designs, materials and availability and performance in all yields profitable results to move your manufacturing methods, as well as areas from drying and pressing to business performance forward. the Yankee drying and paper-making creping are priority. Before delivery, processes themselves. The key to success we confirm and document the quality Smart logistics for is the combination of experience, and properties via extensive material flawless delivery craftsmanship, modern technology testing and non-destructive testing – all We believe it is vital to have full control and well-controlled processes. -
Basic Glossary of Papermaking Terms
Basic Glossary of Papermaking Terms ABRASION RESISTANCE Ability of paper product to withstand abrasion. Measured by determining degree and rate that a sample loses weight under specific rubbing action of an abrading substance, such as an eraser. ABSORBENCY Property of pulp, paper, and its constituents and products that permits the entrainment and retention of other materials it contacts, such as liquid, gaseous and solid substances. ACCEPTS Stock after it has been subjected to some cleaning processes. AFTER DRYERS The bank of dryers positioned after intermediate or sizing rolls. AGITATOR (1) Propeller or agitating shaft for stirring the pulp suspension in a chest or tank. (2) A rotating device for mixing fluids and fluid suspension in a tank or chest. AIR DRY (a.d.) Weight of moisture-free pulp or paper plus a nominal 10% moisture based on traditional assumption that this amount of moisture exists when they come into equilibrium with the atmosphere. AIR DRYING A method of drying the paper web on the paper machine by blowing air along the direction of the web. ALUM Papermaking chemical commonly used for precipitating rosin size onto pulp fibres to impart water- resistant properties (when used for water treatment) to the paper. Also, used for pitch control. More correctly called aluminium sulphate. ANTI-TARNISH PAPER Term originally applied to higher weight tissues used for wrapping silverware, but now used for all papers so prepared that they will not rust of discolour razor blades, needles, silverware etc. APPARENT DENSITY Weight (mass) per unit volume of a sheet of paper obtained by dividing the basis weight (or grammage) by the caliper (thickness). -
5-4144-00004/00027 Effective Date: 11/05/2014 Expiration Date: 11/04/2024
Facility DEC ID: 5414400004 PERMIT Under the Environmental Conservation Law (ECL) IDENTIFICATION INFORMATION Permit Type: Air State Facility Permit ID: 5-4144-00004/00027 Effective Date: 11/05/2014 Expiration Date: 11/04/2024 Permit Issued To:Essity Professional Hygiene North America LLC 1451 McMahon Dr Neenah, Wi 54956 Contact: Andrea Simmons 1 River St South Glens Falls, NY 12803 (518) 742-5674 Facility: SCA TISSUE N A 1 River St South Glens Falls, NY 12803 Description: The river street mill is an integrated paper mill meaning that both pulping and paper making are performed on-site. Each of these operations, along with certain "support operations" are discussed in greater detail below. The paper mill has a maximum production capacity of approximately 270 tons per day (tpd). Most paper produced is converted on-site (i.e.-cut to size, embossed as required, and wrapped and boxed for shipment. Brief descriptions of individual emitting units, operations that either do not or are believed not to potentially emit air contaminants, and identified mill support operations are given below. In some instances, regulatory applicability with respect to select operation is also discussed. Boiler house: the SCA SGF co-generation facility that used to supply steam to the SCA SGF facility was demolished but the Auxiliary boiler (#CBN03) still remains. This source is a 95 MMBtu/hr natural gas fired boiler (Combustion Engineering Tampella design) and is the primary provider of steam to the SCA facility. Additionally, the mill has two (2) boilers each of which has its own stack. One of these is a natural gas fired keeler package boiler with a maximum rated heat input of 72 MMBtu/hr. -
Synthesis and Application of a Cationic Polyamine As Yankee Dryer Coating Agent for the Tissue Paper-Making Process
polymers Article Synthesis and Application of a Cationic Polyamine as Yankee Dryer Coating Agent for the Tissue Paper-Making Process Cesar Valencia 1 , Yamid Valencia 1 and Carlos David Grande Tovar 2,* 1 Área de Investigación, Desarrollo e Innovación, Disproquin S.A.S., Calle 93 Número 7u-2a, Vía Cali-Juanchito 760021, Colombia; [email protected] (C.V.); [email protected] (Y.V.) 2 Grupo de Investigación de Fotoquímica y Fotobiología, Universidad del Atlántico, Carrera 30 Número 8-49, Puerto Colombia 081008, Colombia * Correspondence: [email protected] Received: 25 November 2019; Accepted: 6 January 2020; Published: 9 January 2020 Abstract: Tissue paper is of high importance worldwide and, continuously, research is focused on improvements of the softening and durability properties of the paper which depend specifically on the production process. Polyamide-amine-epichlorohydrin (PAE) resins along with release agents are widely used to adhere the paper to the yankee dryer (creping cylinder) in paper manufacture. Nevertheless, these resins are highly cationic and they normally adhere in excess to the paper which negatively affects the creping process and the quality of the paper. For this reason, a low cationic polyamine-epichlorohydrin coating (Polycoat 38®) was synthesized from a diamine supplied by Disproquin S.A.S. and epichlorohydrin. The analysis of the synthesized polymer was carried out by Fourier transform infrared spectroscopy (FTIR) and nuclear magnetic resonance (1H-NMR). The molecular weight of the polymer was obtained by gel permeation chromatography (GPC), physical-chemical properties such as kinematic viscosity, percentage of solids, density, charge density were measured and compared with a commercial PAE resin (Dispro620®) Thermal stability of the Polycoat 38® and glass transition temperature in presence of a release agent (Disprosol 17®) were also evaluated by thermogravimetric analysis (TGA) and differential scanning calorimetry (DSC), respectively. -
Critical Level Measurement of Hydraulic
Pulp & Paper Plants Application 420-22-057 Critical level measurement of Hydraulic Oil in the Paper Industry - Keep those Rollers Rollin’ Before paper becomes paper there are a series of steps that involve taking the wet pulp, forming it into a long continuous sheet, drying it, pressing it flat and putting it onto a roll. The entire process requires a reliable and uninterruptible supply of hydraulic oil for hydraulic motors and roller and carriage movement lubrication oil - or it’s “Stop the Presses”. Conveying a long continuous sheet of wet and fragile paper requires a series of rollers that guide and support the paper through this process. As the wet paper is moved forward through the forming process and drying process, in a modern paper mill, it’s speeds can reach over of 6,000 feet per minute (2100 m / min.). As the wet pulp leaves the Head Box it is evenly distributed on a continuously moving loop of a fine wire mesh screen called a “Fourdrinier wire” (named after its inventor), which allows the wet, soupy, pulp to be de-watered by gravity. Rollers and vacuum also help in removing additional water and form the paper surface. The wet sheet of paper is then lifted from the wire mesh screen to an endless “looped” belt of heavy woolen fabric that sends the paper through a series of presses where it is sandwiched between two woolen felts and compressed to remove additional water. Hydraulic oil is additionally used in this stage of the process to keep “just the right amount of pressure” on the rollers to delicately squeeze out any excess water prior to further drying. -
Kiattisak Roonprasang Thermal Analysis of Multi-Cylinder Drying
Verarbeitungstechnik Kiattisak Roonprasang Thermal Analysis of Multi-Cylinder Drying Section with variant Geometry Thermal Analysis of Multi-Cylinder Drying Section with Variant Geometry Kiattisak Roonprasang Thermische Analyse von Mehrzylinder Trockenpartien mit variabler Geometrie An der Fakultät Maschinenwesen der Technischen Universität Dresden zur Erlangung des akademischen Grades Doktoringenieur (Dr.-Ing.) angenommene Dissertation Kiattisak Roonprasang, M. Eng. geb. am 02. Juni 1972 in Suratthani, Thailand Tag der Einreichung: 28. Mai 2008 Tag der Verteidigung: 25. November 2008 Gutachter: Prof. Dr. -Ing. J. –P. Majschak Prof. Dr. -Ing. H. Großmann Asst. Prof. Dr. J. Tiansuwan Dr. -Ing. R. Wilken Vorsitzender der Promotionskomission: Prof. Dr. -Ing. habil. W. Richter Danksagung Ich möchte meine Dankbarkeit gegenüber all denen zum Ausdruck bringen, die mir die Möglichkeit und Unterstützung gaben meine Dissertation in Deutschland zu bearbeiten und abzuschließen. Zuerst möchte ich der Königlichen Thailändischen Regierung für das Bewilligen meines Stipendiums danken, dass es mir möglich gemacht hat am Lehrstuhl für Verarbeitungsmaschinen/ Verarbeitungstechnik an der Technischen Universität Dresden zu studieren und meine Forschungsarbeit durchzuführen. Außerdem bin ich dem ehemaligen Leiter des Lehrstuhls, Herrn Prof. Dr. - Ing. habil. Horst Goldhahn, zu Dank verpflichtet, dass er mir die Gelegenheit gegeben hat an seiner Professur zu studieren. Er begleitete meine fachliche Arbeit während meiner ersten Zeit in Deutschland und blieb auch nach seinem Eintritt in den Ruhestand mit mir in Kontakt. Meine tiefe und aufrichtige Dankbarkeit gilt meinem Doktorvater Herrn Prof. Dr. -Ing. Jens-Peter Majschak. Sein breites Wissen und seine logische Denkweise waren von hohem Wert für mich. Sein Verständnis, seine aufmunternde und persönliche Anleitung waren für mich eine gute Basis für den Aufbau und den Abschluss meiner Dissertation.