Photolithography
Total Page:16
File Type:pdf, Size:1020Kb
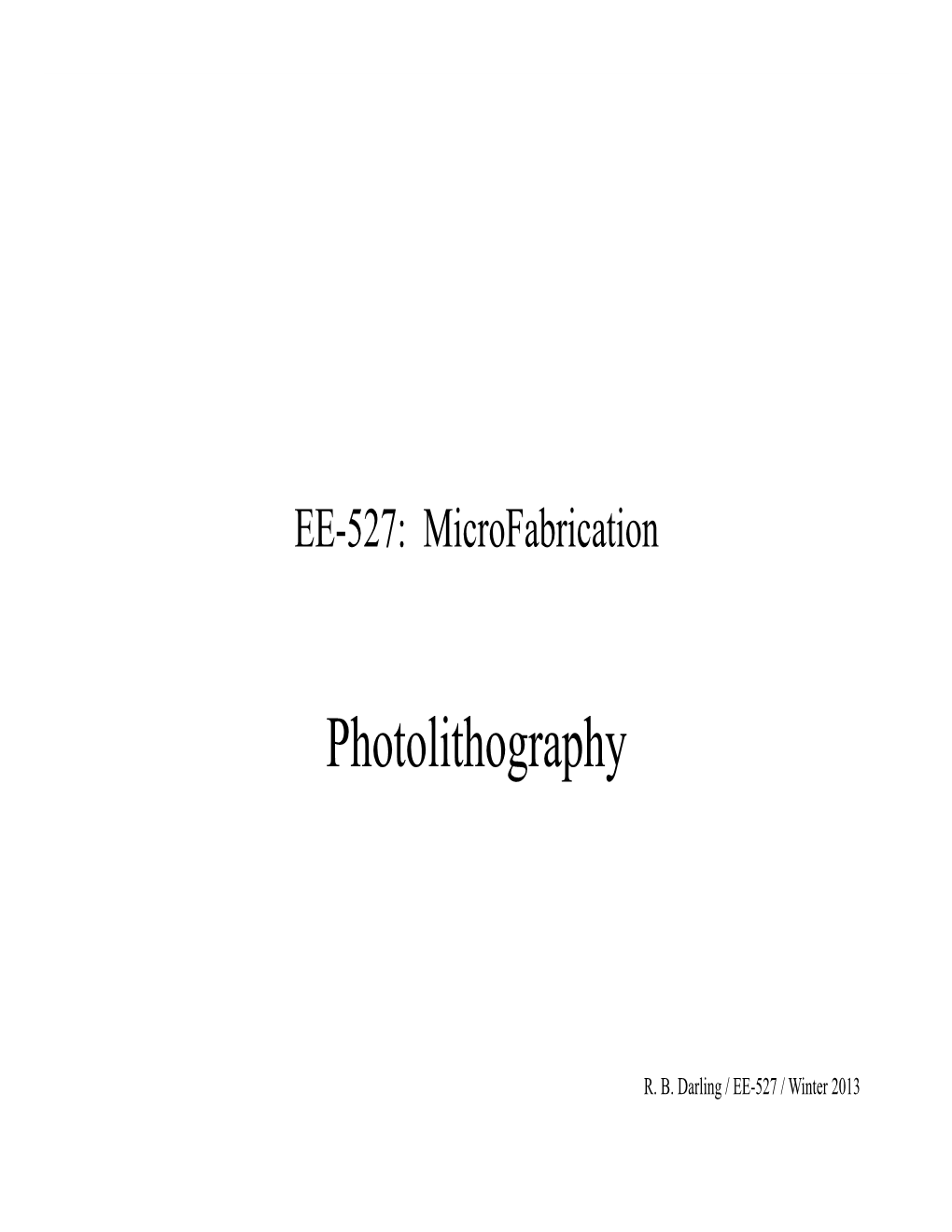
Load more
Recommended publications
-
China's Progress in Semiconductor Manufacturing Equipment
MARCH 2021 China’s Progress in Semiconductor Manufacturing Equipment Accelerants and Policy Implications CSET Policy Brief AUTHORS Will Hunt Saif M. Khan Dahlia Peterson Executive Summary China has a chip problem. It depends entirely on the United States and U.S. allies for access to advanced commercial semiconductors, which underpin all modern technologies, from smartphones to fighter jets to artificial intelligence. China’s current chip dependence allows the United States and its allies to control the export of advanced chips to Chinese state and private actors whose activities threaten human rights and international security. Chip dependence is also expensive: China currently depends on imports for most of the chips it consumes. China has therefore prioritized indigenizing advanced semiconductor manufacturing equipment (SME), which chip factories require to make leading-edge chips. But indigenizing advanced SME will be hard since Chinese firms have serious weaknesses in almost all SME sub-sectors, especially photolithography, metrology, and inspection. Meanwhile, the top global SME firms—based in the United States, Japan, and the Netherlands—enjoy wide moats of intellectual property and world- class teams of engineers, making it exceptionally difficult for newcomers to the SME industry to catch up to the leading edge. But for a country with China’s resources and political will, catching up in SME is not impossible. Whether China manages to close this gap will depend on its access to five technological accelerants: 1. Equipment components. Building advanced SME often requires access to a range of complex components, which SME firms often buy from third party suppliers and then assemble into finished SME. -
American Semiconductor Equipment Technologies
t, f • American Semiconductor Equipment Technologies American Semiconductor Equipment Technologies 6110 Variel Avenue Woodland Hills, California 91367 Telephone: (818) 884-5050 (Thousands of Dollars) Balance Sheet (Fiscal year ending 3/31/86) Working Capital $4,375 Long-Term Debt $2,000 Net Worth $3,446 Current Liability to Net Worth 183.75% Current Liability to Inventory 131.89% Total Liability to Net Worth 241.79% Fixed Assets to Net Worth 241.79% Total Employees 150 Operating performance data are not available Source: Dun & Bradstreet SEMS Industry Econometrics © 1987 Dataquest Incorporated May American Semiconductor Equipment Technologies (Material in this section has been compiled from Dun & Bradstreet financials, Dataquest's SEMS data base, and company literature supplied by ASET. For more information on this start-up company, Dataguest clients are invited to use their inquiry privileges.) > ir THE COMPAMY Background American Semiconductor Equipment Technologies (ASET) was formed in February 1986 to pursue both ongoing and newly developing markets for lithographic systems. The Company was organized by Greg Reyes and Ralph Miller with funding of $3.9 million from four venture capital firms. ASET's product line includes i-line wafer steppers, g-line wafer steppers, substrate steppers, standalone image repeaters and pattern generators, and combination systems. 0perat,^7"g aT«d Strategy ASET Corporation currently serves the semiconductor equipment markets in the image patterning area. The Company also looks to develop business in alternate industries, including laser cards, flat panel displays, and hybrid substrates. ASET maintains research efforts directed toward expanding micro- lithographic technology. ASET acquired the assets of TRE Corporation's wafer stepper and pattern generation manufacturing unit early in 1986. -
Paper 73-3 Has Been Designated As a Distinguished Paper at Display Week 2018
Distinguished Student Paper 73-3 / T. Ji Paper 73-3 has been designated as a Distinguished Paper at Display Week 2018. The full- length version of this paper appears in a Special Section of the Journal of the Society for Information Display (JSID) devoted to Display Week 2018 Distinguished Papers. This Special Section will be freely accessible until December 31, 2018 via: http://onlinelibrary.wiley.com/page/journal/19383657/homepage/display_week_2018.htm Authors that wish to refer to this work are advised to cite the full-length version by referring to its DOI: https://doi.org/10.1002/jsid.640 SID 2018 DIGEST Distinguished Student Paper 73-3 / T. Ji Tingjing Ji- Full Color Quantum Dot Light-Emitting Diodes Patterned by Photolithography Technology Full Color Quantum Dot Light-Emitting Diodes Patterned by Photolithography Technology Tingjing Ji (student), Shuang Jin, Bingwei Chen, Yucong Huang, Zijing Huang, Zinan Chen, Shuming Chen*, Xiaowei Sun Department of Electrical and Electronic Engineering, Southern University of Science and Technology, Shenzhen, PR China, 518055 *Corresponding author: [email protected] Abstract the traditional patterning processes. The QLED device achieved Photolithography is a high resolution and mature patterning maximum electroluminescence intensity of 23 770 cd/m2. [13] technique which has been widely used in semiconductor industry. For display application, a pixel consists of red (R), green (G) and In this work, we use photolithography to fine pattern the QD blue (B) side-by-side sub-pixels, which thereby requires a high layers. Because it is difficult to etch the QD layer, lift-off is used resolution patterning of the light-emission layers. -
Patterning of Quantum Dots by Dip-Pen and Polymer Pen Nanolithography
Nanofabrication 2015; 2: 19–26 Research Article Open Access Soma Biswas*, Falko Brinkmann, Michael Hirtz, Harald Fuchs Patterning of Quantum Dots by Dip-Pen and Polymer Pen Nanolithography Abstract: We present a direct way of patterning CdSe/ lithography and photolithography, these direct techniques ZnS quantum dots by dip-pen nanolithography and do not rely on resist layers and multi-step processing, but polymer pen lithography. Mixtures of cholesterol and allow the precise deposition of ink mixtures. Spot sizes in phospholipid 1,2-dioleoyl-sn-glycero-3 phosphocholine commercially widespread inkjet printing and other related serve as biocompatible carrier inks to facilitate the transfer spotting techniques are usually in the range of 50 to 500 of quantum dots from the tips to the surface during µm [5–7], while high resolution approaches (µCP, DPN and lithography. While dip-pen nanolithography of quantum PPL) reach sub-µm features. dots can be used to achieve higher resolution and smaller Microcontact printing utilises a predesigned pattern features (approximately 1 µm), polymer pen poly(dimethylsiloxane) (PDMS) stamp that is first coated lithography is able to address intermediate pattern scales with ink and subsequently pressed onto the surface in the low micrometre range. This allows us to combine manually. A total area up to cm2 can be patterned retaining the advantages of micro contact printing in large area and a lateral resolution of approximately 100 nm [8]. Dip-pen massive parallel patterning, with the added flexibility in nanolithography (Figure 1a) employs an atomic force pattern design inherent in the DPN technique. microscopy tip (AFM) as a quill pen. -
From Sand to Circuits
From sand to circuits By continually advancing silicon technology and moving the industry forward, we help empower people to do more. To enhance their knowledge. To strengthen their connections. To change the world. How Intel makes integrated circuit chips www.intel.com www.intel.com/museum Copyright © 2005Intel Corporation. All rights reserved. Intel, the Intel logo, Celeron, i386, i486, Intel Xeon, Itanium, and Pentium are trademarks or registered trademarks of Intel Corporation or its subsidiaries in the United States and other countries. *Other names and brands may be claimed as the property of others. 0605/TSM/LAI/HP/XK 308301-001US From sand to circuits Revolutionary They are small, about the size of a fingernail. Yet tiny silicon chips like the Intel® Pentium® 4 processor that you see here are changing the way people live, work, and play. This Intel® Pentium® 4 processor contains more than 50 million transistors. Today, silicon chips are everywhere — powering the Internet, enabling a revolution in mobile computing, automating factories, enhancing cell phones, and enriching home entertainment. Silicon is at the heart of an ever expanding, increasingly connected digital world. The task of making chips like these is no small feat. Intel’s manufacturing technology — the most advanced in the world — builds individual circuit lines 1,000 times thinner than a human hair on these slivers of silicon. The most sophisticated chip, a microprocessor, can contain hundreds of millions or even billions of transistors interconnected by fine wires made of copper. Each transistor acts as an on/off switch, controlling the flow of electricity through the chip to send, receive, and process information in a fraction of a second. -
Part III. Functional Polymers for Semiconductor Applications Outline
Functional Polymer/1st Semester, 2006 _________________________________________ Part III. Functional Polymers for Semiconductor Applications Outline of Part Photoresist for Semiconductor Applications Introduction of photolithography Photoresist Materials for Exposure at 193 nm Wavelength Chemically Amplified Resists for F2 Excimer laser Lithography Prof. Jin-Heong Yim Motivations Creation of integrated circuits, which are a major component in computer technology An extension of photolithography processes are used to create standard semiconductor chips Play a key role in the production of technically demanding components of advanced microsensors Used to make adhesives in electronics Prof. Jin-Heong Yim History Historically, lithography is a type of printing technology that is based on the chemical repellence of oil and water. Photo-litho-graphy: latin: light-stone-writing In 1826, Joseph Nicephore Niepce, in Chalon, France, takes the first photograph using bitumen of Judea on a pewter plate, developed using oil of lavender and mineral spirits In 1935 Louis Minsk of Eastman Kodak developed the first negative photoresist In 1940 Otto Suess developed the first positive photoresist. In 1954, Louis Plambeck, Jr., of Du Pont, develops the Dycryl polymeric letterpress plate Prof. Jin-Heong Yim Microlithography A process that involves transferring an integrated circuit pattern into a polymer film and subsequently replicating that pattern in an underlying thin conductor or dielectric film Prof. Jin-Heong Yim How Small Can We Print ? SEM picture of typical lithographic pattern Comparison of the dimensions of lithographic images and familiar objects Thompson, L. F.; Willson, C. G.; Bowden, M. J. Introduction to Microlithography; 2nd Ed; ACS Professional Reference Book; American Chemical Society; Washington, DC, 1994 Prof. -
Biocompatibility of SU-8 and Its Biomedical Device Applications
micromachines Review Biocompatibility of SU-8 and Its Biomedical Device Applications Ziyu Chen and Jeong-Bong Lee * Department of Electrical and Computer Engineering, The University of Texas at Dallas, Richardson, TX 75080, USA; [email protected] * Correspondence: [email protected]; Tel.: +1-972-883-2893; Fax: +1-972-883-5842 Abstract: SU-8 is an epoxy-based, negative-tone photoresist that has been extensively utilized to fabricate myriads of devices including biomedical devices in the recent years. This paper first reviews the biocompatibility of SU-8 for in vitro and in vivo applications. Surface modification techniques as well as various biomedical applications based on SU-8 are also discussed. Although SU-8 might not be completely biocompatible, existing surface modification techniques, such as O2 plasma treatment or grafting of biocompatible polymers, might be sufficient to minimize biofouling caused by SU-8. As a result, a great deal of effort has been directed to the development of SU-8-based functional devices for biomedical applications. This review includes biomedical applications such as platforms for cell culture and cell encapsulation, immunosensing, neural probes, and implantable pressure sensors. Proper treatments of SU-8 and slight modification of surfaces have enabled the SU-8 as one of the unique choices of materials in the fabrication of biomedical devices. Due to the versatility of SU-8 and comparative advantages in terms of improved Young’s modulus and yield strength, we believe that SU-8-based biomedical devices would gain wider proliferation among the biomedical community in the future. Keywords: SU-8; biocompatibility; biosensing; biomedical; implantable Citation: Chen, Z.; Lee, J.-B. -
Projection Photolithography-Liftoff Techniques for Production of 0.2-Pm Metal Patterns
IEEE TRANSACTIONS ON ELECTRON DEVICES, VOL. ED-28, NO. 11, NOVEMBER 1981 1375 Projection Photolithography-Liftoff Techniques for Production of 0.2-pm Metal Patterns MARK D. FEUER AND DANIEL E. PROBER, MEMBER, IEEE GLASS FILTER Abstract-A technique whichallows the useof projection photo- \ yPHOTORESIST lithography with the photoresist liftoff process, for fabrication of sub- micrometer metal patterns, is described. Through-the-substrate (back- \II a projection) exposure of the photoresist produces the undercut profiles necessary forliftoff processing. Metal lines andsuperconducting microbridges of 0.2-pm width have been fabricated with this technique. I Experimental details and process limits are discussed. II OBJECTIVE IMMERSION OIL ECENT DEVELOPMENTS inmicrolithography have SUBSTRATE - (d) R made possible the production ofa variety of devices with PHOTORESIST %- I-l submicrometer (submicron) dimensions [ 11 , [2] , offering the (a) advantages of higherspeed and packing density.For many Fig. 1. Schematicdiagram of back-projectionand metal-liftoff pro- Josephson-effect devices in particular, submicron dimensions cedure. (a) Exposure system, employing a Zeiss optical microscope. Image of the mask is projected through the substrate, which is shown are essential for achieving optimalperformance over awide in sideview. (b) Schematic contours of constant exposure intensity. range of operatingconditions [3] . Forsubmicron pattern (c) After photoresist development and metallization. (d) After liftoff. transfer, liftoff processing [ 11 generally -
Silicon Valley Group
Silicon Valley Group ANNUAL REPORT AND FORM 10-K Silicon Valley Group Enabling integrated circuit manufacturers to win the productivity race by providing leading-edge technology products that maximize yield through innovative design is the driving force of Silicon Valley Group. Our mission is fulfilled when products are delivered and installed on time and top-of-the-line service and support are provided to help customers achieve their productivity objectives. SILICON VALLEY GROUP TECHNOLOGY LEADER We are prepared for growth. a letter to our shareholders AS THE SEMICONDUCTOR GROWTH CYCLE GAINS MOMENTUM, SVG IS WELL POSITIONED FOR THE FUTURE. As the semiconductor industry goes, so too does SVG. The recent industry downturn, which started in 1998 and continued into 1999, presented major hurdles for Silicon Valley Group and its customers. It particularly impacted SVG at a time when our lithography manufacturing capacity and other capabilities had been increased to take advantage of what had been predicted to be a period of unprecedented growth. Managing a downturn is no easy feat. Although our return to profitability in the fourth quarter of the fiscal year was not as vigorous as we would have liked, I am pleased to say that SVG has risen to the challenge. We focused on the long-term health of the Company with cash preservation and investments in research and development (R&D). Our business is cyclical in nature, and I believe that the current upward momentum we are experiencing in the industry is a very positive indicator for the future. This was a very difficult year for SVG. -
And Nanolithography Techniques and Their Applications
Review on Micro- and Nanolithography Techniques and their Applications Alongkorn Pimpin* and Werayut Srituravanich** Department of Mechanical Engineering, Faculty of Engineering, Chulalongkorn University, Pathumwan, Bangkok 10330, Thailand E-mail: [email protected]*, [email protected]** Abstract. This article reviews major micro- and nanolithography techniques and their applications from commercial micro devices to emerging applications in nanoscale science and engineering. Micro- and nanolithography has been the key technology in manufacturing of integrated circuits and microchips in the semiconductor industry. Such a technology is also sparking revolutionizing advancements in nanotechnology. The lithography techniques including photolithography, electron beam lithography, focused ion beam lithography, soft lithography, nanoimprint lithography and scanning probe lithography are discussed. Furthermore, their applications are summarized into four major areas: electronics and microsystems, medical and biotech, optics and photonics, and environment and energy harvesting. Keywords: Nanolithography, photolithography, electron beam lithography, focused ion beam lithography, soft lithography, nanoimprint lithography, scanning probe lithography, dip-pen lithography, microsystems, MEMS, nanoscience, nanotechnology, nano-engineering. ENGINEERING JOURNAL Volume 16 Issue 1 Received 18 August 2011 Accepted 8 November Published 1 January 2012 Online at http://www.engj.org DOI:10.4186/ej.2012.16.1.37 DOI:10.4186/ej.2012.16.1.37 1. Introduction For decades, micro- and nanolithography technology has been contributed to the manufacturing of integrated circuits (ICs) and microchips. This advance in the semiconductor and IC industry has led to a new paradigm of the information revolution via computers and the internet. Micro- and nanolithography is the technology that is used to create patterns with a feature size ranging from a few nanometers up to tens of millimeters. -
Techniques and Considerations in the Microfabrication of Parylene C Microelectromechanical Systems
micromachines Review Techniques and Considerations in the Microfabrication of Parylene C Microelectromechanical Systems Jessica Ortigoza-Diaz 1, Kee Scholten 1 ID , Christopher Larson 1 ID , Angelica Cobo 1, Trevor Hudson 1, James Yoo 1 ID , Alex Baldwin 1 ID , Ahuva Weltman Hirschberg 1 and Ellis Meng 1,2,* 1 Department of Biomedical Engineering, University of Southern California, Los Angeles, CA 90089, USA; [email protected] (J.O.-D.); [email protected] (K.S.); [email protected] (C.L.); [email protected] (A.C.); [email protected] (T.H.); [email protected] (J.Y.); [email protected] (A.B.); [email protected] (A.W.H.) 2 Ming Hsieh Department of Electrical Engineering, University of Southern California, Los Angeles, CA 90089, USA * Correspondence: [email protected]; Tel.: +1-213-740-6952 Received: 31 July 2018; Accepted: 18 August 2018; Published: 22 August 2018 Abstract: Parylene C is a promising material for constructing flexible, biocompatible and corrosion- resistant microelectromechanical systems (MEMS) devices. Historically, Parylene C has been employed as an encapsulation material for medical implants, such as stents and pacemakers, due to its strong barrier properties and biocompatibility. In the past few decades, the adaptation of planar microfabrication processes to thin film Parylene C has encouraged its use as an insulator, structural and substrate material for MEMS and other microelectronic devices. However, Parylene C presents unique challenges during microfabrication and during use with liquids, especially for flexible, thin film electronic devices. In particular, the flexibility and low thermal budget of Parylene C require modification of the fabrication techniques inherited from silicon MEMS, and poor adhesion at Parylene-Parylene and Parylene-metal interfaces causes device failure under prolonged use in wet environments. -
Fundimentals of Photolithography
FUNDIMENTALS OF PHOTOLITHOGRAPHY One of the most widely used methods for creating nanoscale circuit components is Photolithography. The word lithography is derived from the Greek words lithos (stone) and graphein (to write) and finds its roots in a process invented by Aloys Senefelder in 1796. By treating a piece of limestone with certain chemicals, Senefelder was then able to transfer an image carved into the stone onto a piece of paper. This was done by coating certain parts of the porous limestone with a water repellant substance. When ink was applied to the stone it would only adhere to the untreated hydrophilic areas, and hence the image carved into the rock could be transferred repeatedly onto paper. Senefelder's technique is still used in some artistry applications today. As time progressed and technology improved, lithography methods evolved. In the 1820's a French scientist by the name of Nicephore Niepce developed the first photoresist, a component fundamental to photolithography. A photoresist is a substance that undergoes a chemical reaction when it is eXposed to light. Niepce's photoresist was a material known as Bitumen of Judea, a kind of naturally occurring asphalt. A sheet of stone, metal, or glass was coated with a thin layer of this bitumen, which became less soluble where it was eXposed to light. Areas that were uneXposed could then be removed using a solvent, and the resultant exposed areas of the sheet were etched using a chemical bath. After the remaining photoresist was removed, the sheet could then be used as a printing plate. Photolithography today is in many ways similar to the original process invented by Niepce.