US5349077.Pdf
Total Page:16
File Type:pdf, Size:1020Kb
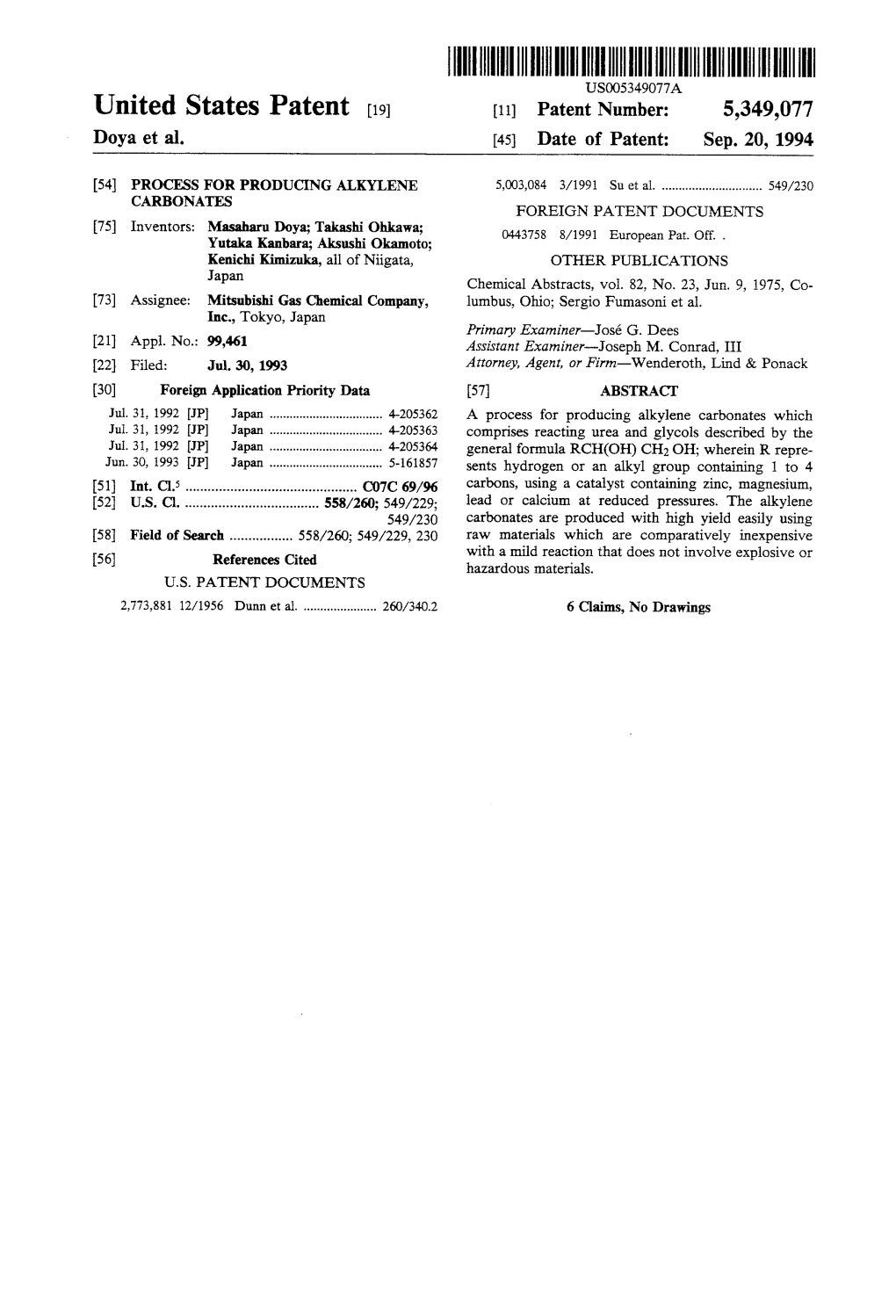
Load more
Recommended publications
-
Catalysis Science & Technology
Catalysis Science & Technology Accepted Manuscript This is an Accepted Manuscript, which has been through the Royal Society of Chemistry peer review process and has been accepted for publication. Accepted Manuscripts are published online shortly after acceptance, before technical editing, formatting and proof reading. Using this free service, authors can make their results available to the community, in citable form, before we publish the edited article. We will replace this Accepted Manuscript with the edited and formatted Advance Article as soon as it is available. You can find more information about Accepted Manuscripts in the Information for Authors. Please note that technical editing may introduce minor changes to the text and/or graphics, which may alter content. The journal’s standard Terms & Conditions and the Ethical guidelines still apply. In no event shall the Royal Society of Chemistry be held responsible for any errors or omissions in this Accepted Manuscript or any consequences arising from the use of any information it contains. www.rsc.org/catalysis Page 1 of 10 Catalysis Science & Technology Catalysis Science & Technology RSC Publishing ARTICLE Carbonates as reactants for the production of fine chemicals: the synthesis of 2-phenoxyethanol Cite this: DOI: 10.1039/x0xx00000x P. Ziosi a,b , T. Tabanelli a, G. Fornasari, a S. Cocchi a, F. Cavani a,b,* , P. Righi a,b,* Manuscript Received, The solventless and heterogeneously catalysed synthesis of 2-phenoxyethanol (ethylene glycol monophenyl ether) via the reaction between phenol and ethylene carbonate was investigated DOI: 10.1039/x0xx00000x using Na-mordenite catalysts, as an alternative to the industrial process using ethylene oxide and homogeneous basic conditions. -
Kinetic Modeling and Mechanistic Investigations of Transesterification of Propylene Carbonate with Methanol Over Fe-Mn Double Metal Cyanide Catalyst
Reaction Chemistry & Engineering Kinetic Modeling and Mechanistic Investigations of Transesterification of Propylene Carbonate with Methanol over Fe-Mn Double Metal Cyanide Catalyst Journal: Reaction Chemistry & Engineering Manuscript ID RE-ART-09-2019-000372.R1 Article Type: Paper Date Submitted by the 21-Oct-2019 Author: Complete List of Authors: Song, Ziwei; Yanshan University, Subramaniam, Bala; University of Kansas, Center for Environmentally Beneficial Catalysis Chaudhari, Raghunath; University of Kansas, Chemical & Petroleum Engineering Page 1 of 23 Reaction Chemistry & Engineering Kinetic Modeling and Mechanistic Investigations of Transesterification of Propylene Carbonate with Methanol over Fe-Mn Double Metal Cyanide Catalyst Ziwei Song, a,b,c Bala Subramaniam, a,b and Raghunath V. Chaudhari* a,b aCenter for Environmentally Beneficial Catalysis, University of Kansas, 1501 Wakarusa Dr. Lawrence, KS 66047, United States bDepartment of Chemical & Petroleum Engineering, University of Kansas, 1503 W 15th St. Lawrence, KS 66045, United States cDepartment of Chemical Engineering, College of Environmental and Chemical Engineering, Yanshan University, Qinhuangdao 066004, China *Corresponding author: [email protected] KEYWORDS: double metal cyanide, transesterification, dimethyl carbonate, microkinetic modeling 1 Reaction Chemistry & Engineering Page 2 of 23 Abstract Kinetic modeling of transesterification of propylene carbonate with methanol using Fe-Mn double metal cyanide catalyst has been investigated based on experimental data obtained under kinetically controlled conditions in a batch slurry reactor in the 140-200 °C range. A simple two-step power law model was found to represent the experimental data well. In addition, a detailed kinetic model based on a molecular level description of the reaction mechanism is also evaluated to provide better insight into the reaction mechanism. -
Ethylene Glycol
Ethylene glycol Ethylene glycol (IUPAC name: ethane-1,2-diol) is an organic Ethylene glycol compound with the formula (CH2OH)2. It is mainly used for two purposes, as a raw material in the manufacture of polyester fibers and for antifreeze formulations. It is an odorless, colorless, sweet-tasting, viscous liquid. Contents Production Industrial routes Biological routes Historical routes Uses Coolant and heat-transfer agent Antifreeze Precursor to polymers Other uses Dehydrating agent Hydrate inhibition Applications Chemical reactions Toxicity Environmental effects Names Notes Preferred IUPAC name References Ethane-1,2-diol External links Other names Ethylene glycol 1,2-Ethanediol Production Ethylene alcohol Hypodicarbonous acid Monoethylene glycol Industrial routes 1,2-Dihydroxyethane Ethylene glycol is produced from ethylene (ethene), via the Identifiers intermediate ethylene oxide. Ethylene oxide reacts with water to CAS Number 107-21-1 (http produce ethylene glycol according to the chemical equation: s://commonche mistry.cas.org/d C2H4O + H2O → HO−CH2CH2−OH etail?cas_rn=10 7-21-1) 3D model (JSmol) Interactive This reaction can be catalyzed by either acids or bases, or can occur image (https://ch at neutral pH under elevated temperatures. The highest yields of emapps.stolaf.e ethylene glycol occur at acidic or neutral pH with a large excess of du/jmol/jmol.ph water. Under these conditions, ethylene glycol yields of 90% can be p?model=OCC achieved. The major byproducts are the oligomers diethylene glycol, O) triethylene glycol, and tetraethylene glycol. The separation of these oligomers and water is energy-intensive. About 6.7 million tonnes 3DMet B00278 (http://w are produced annually.[4] ww.3dmet.dna.af frc.go.jp/cgi/sho A higher selectivity is achieved by use of Shell's OMEGA process. -
Propylene Carbonate Extraction for Recovery of Poly-3-Hydroxybutryate
1 Propylene Carbonate Extraction for Recovery of Poly-3-hydroxybutryate Abstract Propylene Carbonate Distillation Poly -3-hydroxybutryate (PHB) is a biopolymer produced Propylene Carbonate is an organic solvent produced as a storage molecule for energy and carbon under • Waste solution recovered after PHB by combining propylene oxide with carbon dioxide. It is poor growth conditions in certain organisms. PHB is a precipitation consisted of Propylene considered a polar aprotic solvent (no proton to donate) class of polyhydroxyalkanoates (PHAs), which have Carbonate and Ethanol Due to its characteristics (low vapor pressure, stability, similar properties to plastics derived from petroleum. PHB provides an environmentally friendly alternative to and high polarity) it is used in many applications. These include • Through distillation, both the Ethanol production of fibers and textiles, dyeing, personal care agents petroleum -based plastics due to its biodegradability and and Propylene Carbonate have been and cosmetics, and a component of some adhesives. It is also method of production. It can be produced by recovered. considered non-toxic making it more suitable to use at larger recombinant Escherichia coli, harvested from the cell, scales. and recovered. One of the major expenses of • Recovered 70% Propylene producing PHB is the extraction of the PHB from the Carbonate and nearly all Ethanol biomass. This study focused on evaluating different methods of PHB extraction for their ability to effectively • Preliminary experiments show no extract PHB from E. coli biomass and the feasibility of Propylene Carbonate Extraction Procedure Distillation apparatus to recover Propylene difference in the yield of PHB scaling up those processes. These processes provide a Carbonate and Ethanol from waste stream extracted with distilled Propylene 125 L Bioreactor way to produce PHB from growing E. -
Safety Data Sheet According to 1907/2006/EC, Article 31 Printing Date 01.04.2020Version Number 4 Revision: 01.04.2020
Page 1/8 Safety data sheet according to 1907/2006/EC, Article 31 Printing date 01.04.2020Version number 4 Revision: 01.04.2020 * SECTION 1: Identification of the substance/mixture and of the company/undertaking 1.1 Product identifier Trade name: 1mol/L Lithium hexafluorophosphate in (1:1:3 vol.%) Ethylene carbonate : Propylene carbonate : Dimethyl carbonate with 1wt.% Vinylene carbonate - 99,9% Article number: E020 UFI: TH30-W082-000P-86TG 1.2 Relevant identified uses of the substance or mixture and uses advised against No other important information available. Application of the substance / the mixture This product is intended for the exclusive use of Research and Development 1.3 Details of the supplier of the safety data sheet Manufacturer/Supplier: Solvionic SA 195 route d'Espagne 31036 TOULOUSE FRANCE Phone number: +33 (0)5.34.63.35.35 Further information obtainable from: HSE Department 1.4 Emergency telephone number: ORFILA (INRS): +33 (0)1.45.42.59.59 CCHST: 1-800-668-4284 (Canada & U.S.A) SECTION 2: Hazards identification 2.1 Classification of the substance or mixture Classification according to Regulation (EC) No 1272/2008 GHS02 Flam. Liq. 3 H226 Flammable liquid and vapour. GHS08 STOT RE 1 H372 Causes damage to organs through prolonged or repeated exposure. GHS05 Skin Corr. 1B H314 Causes severe skin burns and eye damage. Eye Dam. 1 H318 Causes serious eye damage. GHS07 Acute Tox. 4 H302 Harmful if swallowed. Skin Sens. 1 H317 May cause an allergic skin reaction. 2.2 Label elements Labelling according to Regulation (EC) No 1272/2008 The product is classified and labelled according to the CLP regulation. -
Green Chemistry
Green Chemistry View Article Online PAPER View Journal | View Issue The greening of peptide synthesis† Cite this: Green Chem., 2017, 19, Stefan B. Lawrenson, Roy Arav and Michael North* 1685 The synthesis of peptides by amide bond formation between suitably protected amino acids is a funda- mental part of the drug discovery process. However, the required coupling and deprotection reactions are routinely carried out in dichloromethane and DMF, both of which have serious toxicity concerns and generate waste solvent which constitutes the vast majority of the waste generated during peptide syn- thesis. In this work, propylene carbonate has been shown to be a green polar aprotic solvent which can be used to replace dichloromethane and DMF in both solution- and solid-phase peptide synthesis. Solution-phase chemistry was carried out with Boc/benzyl protecting groups to the tetrapeptide stage, no epimerisation occurred during these syntheses and chemical yields for both coupling and de- Received 20th January 2017, protection reactions in propylene carbonate were at least comparable to those obtained in conventional Accepted 1st March 2017 solvents. Solid-phase peptide synthesis was carried out using Fmoc protected amino acids on a DOI: 10.1039/c7gc00247e ChemMatrix resin and was used to prepare the biologically relevant nonapeptide bradykinin with compar- Creative Commons Attribution 3.0 Unported Licence. rsc.li/greenchem able purity to a sample prepared in DMF. Introduction methane mixtures.8 These issues are amplified in solid-phase peptide synthesis7,9 where large excesses of reagents are used Peptides are central compounds in the pharmaceutical indus- and resins are washed multiple times with toxic solvents. -
Comparative Study of Ethylene Carbonate-Based Electrolyte Decomposition at Li, Ca, and Al Anode Interfaces Joshua Young,* Peter M
Article Cite This: ACS Appl. Energy Mater. XXXX, XXX, XXX−XXX www.acsaem.org Comparative Study of Ethylene Carbonate-Based Electrolyte Decomposition at Li, Ca, and Al Anode Interfaces Joshua Young,* Peter M. Kulick, Taylor R. Juran, and Manuel Smeu* Department of Physics, Binghamton University, Binghamton, New York 13902, United States *S Supporting Information ABSTRACT: One of the major bottlenecks to the develop- ment of alternatives to existing Li ion battery technology, such as Li metal or multivalent ion (Mg, Ca, Zn, or Al) batteries, has to do with the layer of inorganic and organic compounds that forms at the interface between the metallic anode and electrolyte via solvent and salt decomposition (the solid− electrolyte interphase or SEI). In Li metal batteries the growth of dendrites causes continual formation of new SEI, while in multivalent ion batteries the SEI does not allow for the diffusion of the ions. Finding appropriate electrolytes for such systems and gaining an understanding of SEI formation is therefore critical to the development of secondary Li metal and multivalent ion cells. In this work, we use ab initio molecular dynamics simulations to investigate the initial stages of decomposition of organic electrolytes based on ethylene carbonate (EC) and formation of the SEI on Li, Ca, and Al metal fi fi 2− surfaces. We rst nd that pure EC only decomposes to CO and C2H4O2 species on each type of surface. However, when a salt 2− molecule is introduced to form an electrolyte, a second EC decomposition route resulting in the formation of CO3 and C2H4 begins to occur; furthermore, a variety of different inorganic compounds, depending on the chemical composition of the salt, form on the surfaces. -
Polyhydroxyalkylation of Urea with Ethylene Carbonate and Application of Obtained Products As Components of Polyurethane Foams
http://www.e-polymers.org e-Polymers 2008, no. 166 ISSN 1618-7229 Polyhydroxyalkylation of urea with ethylene carbonate and application of obtained products as components of polyurethane foams Iwona Zarzyka-Niemiec* *Rzeszów University of Technology, Department of Organic Chemistry, Al. Powstańców Warszawy 6, 35-959 Rzeszów, Poland; e-mail: [email protected] (Received: 17 March, 2008; published: 27 December, 2008) Abstract: The reaction between urea and ethylene carbonate occur with partial release of CO2 and partial incorporation of carbonate groups into products. The carbonate groups were found to be attached both to nitrogen of urea and to oxyethylene chain. The most effective catalyst of the synthesis was potassium carbonate. The hydroxyethyl and hydroxyethoxy groups of urea derivatives undergo partial dimerization to form carbamate groups in the products. The products of reaction between urea and ethylene carbonate have good thermal stability, they start to decompose at 200 0C. The obtained products can be used as polyol components for polyurethane foams. Polyurethane foams obtained from hydroxyethoxy derivatives of urea (EC8) are rigid products of low water uptake, good stability of dimensions, low mass loss on 30 days heating at 150 C, enhanced thermal stability and good compressive strength. Introduction Hydroxyalkyl derivatives of urea can be obtained by reaction of urea with corresponding aminoalcohols (I, y = 1) [1, 2]: O O 2H N CH O H+H N C NH H O CH HN C NH CH O H+2NH (1) 2 2 n y 2 2 2 n y 2 n y 3 (I) where: n = 2-5, y = 1, 2 or 3. -
Recent Advances in Non-Flammable Electrolytes for Safer Lithium-Ion Batteries
Review Recent Advances in Non-Flammable Electrolytes for Safer Lithium-Ion Batteries Neha Chawla1,*, Neelam Bharti 2 and Shailendra Singh 1 1 Environmental, Health and Safety, Carnegie Mellon University, Pittsburgh, PA 15213, USA; [email protected] 2 Mellon Institute Library, Carnegie Mellon University, Pittsburgh, PA 15213, USA; [email protected] * Correspondence: [email protected] Received: 19 December 2018; Accepted: 17 January 2019; Published: 1 February 2019 Abstract: Lithium-ion batteries are the most commonly used source of power for modern electronic devices. However, their safety became a topic of concern after reports of the devices catching fire due to battery failure. Making safer batteries is of utmost importance, and several researchers are trying to modify various aspects in the battery to make it safer without affecting the performance of the battery. Electrolytes are one of the most important parts of the battery since they are responsible for the conduction of ions between the electrodes. In this paper, we discuss the different non- flammable electrolytes that were developed recently for safer lithium-ion battery applications. Keywords: lithium-ion battery; non-flammable; electrolyte; safety; battery fire 1. Introduction Rechargeable lithium-ion (Li-ion) batteries are widely used in portable electronic devices and are considered as the most potential power source for electric vehicles due to their high energy density and long cycle life. A Li-ion battery consists of a positively charged cathode, negatively charged anode, separator, electrolyte, and positive and negative current collectors. While discharging, the lithium ions travel from the anode to the cathode through the electrolyte, thus generating an electric current, and, while charging the device, lithium ions are released by the cathode and then go back to the anode. -
A Study of Electrochemical Reduction of Ethylene and Propylene Carbonate
A Study of Electrochemical Reduction of Ethylene and Propylene Carbonate Electrolytes on Graphite Using ATR-FTIR Spectroscopy Guorong V. Zhuanga,*,z Hui Yangb,*, Berislav Blizanaca, and Philip N. Ross, Jr.a,* Materials Sciences Divisiona and Environmental Energy Technologies Divisionb Lawrence Berkeley National Laboratory Berkeley, CA 94720 Abstract We present results testing the hypothesis that there is a different reaction pathway for the electrochemical reduction of PC versus EC-based electrolytes at graphite electrodes with LiPF6 as the salt in common. We examined the reduction products formed using ex-situ Fourier Transform Infrared (FTIR) spectroscopy in attenuated total reflection (ATR) geometry. The results show the pathway for reduction of PC leads nearly entirely to lithium carbonate as the solid product (and presumably propylene gas as the co-product) while EC follows a path producing a mixture of organic and inorganic compounds. Possible explanations for the difference in reaction pathway are discussed. ________________________________________________________________________ * Electrochemical Society Active Member Z Corresponding author e-mail: [email protected] 1 It is well known in the literature that there is a considerable imbalance of cathodic versus anodic total charge for the carbon/graphite negative electrode in a Li-ion battery during the first few (formation) cycles1. This charge imbalance or irreversible capacity has been attributed to solvent co-intercalation, electrolyte reduction, SEI layer formation, and other side reactions accompanying intercalation and deintercalation of carbon/graphite electrodes2. Most of this irreversible capacity occurs in the potential region > 0.5 V (vs. Li/Li+), and in the case of graphite can be distinguished from the charge for intercalation/deintercalation which produces three well-defined sharp peaks in the differential capacity curve < 0.5 V (vs. -
Hydrothermal Conversion of Ethylene Carbonate to Ethylene Glycol
international journal of hydrogen energy 41 (2016) 9118e9122 Available online at www.sciencedirect.com ScienceDirect journal homepage: www.elsevier.com/locate/he Hydrothermal conversion of ethylene carbonate to ethylene glycol Jun Fu a, Naimeng Jiang c, Dezhang Ren a, Zhiyuan Song a,LuLia, * Zhibao Huo a,b, a School of Environmental Science and Engineering, Shanghai Jiao Tong University, 800 Dongchuan Road, Shanghai 200240, China b State Key Laboratory of Fine Chemicals, Dalian University of Technology, Dalian 116024, China c School of Chemistry and Chemical Engineering, Guangxi University, 100 University Road, Nanning 530004, China article info abstract Article history: A novel process for the conversion of ethylene carbonate (EC) to ethylene glycol (EG) in high Received 13 October 2015 temperature water was investigated. As a result, even there is no external catalyst and Received in revised form additive, the reaction of EC proceeded well and provided the desired EG in 99% yield with 13 December 2015 25% water filling at 250 C for 2 h. Moreover, only CO2 as by-product was observed in the Accepted 14 December 2015 process. High temperature water exhibits an unique merits and plays an catalytic role for Available online 6 January 2016 EC conversion. From viewpoint of practice, this work provides a simple, environmentally benign, catalyst/additive-free process for the production of ethylene glycol from ethylene Keywords: carbonate. Carbon dioxide © 2015 Hydrogen Energy Publications LLC. Published by Elsevier Ltd. All rights reserved. Ethylene carbonate Ethylene glycol High temperature water No catalyst/additive production from petroleum-derived ethylene via hydration of Introduction the intermediate ethylene oxide [2]. -
Process for Cosynthesis of Ethylene Glycol and Dimethyl Carbonate
~" ' MM II II II Ml Ml II I Ml I II II I II J European Patent Office _ _ _ _ _ © Publication number: 0 255 252 B1 Office_„. europeen des brevets © EUROPEAN PATENT SPECIFICATION © Date of publication of patent specification: 16.09.92 © Int. CI.5: C07C 68/06, C07C 69/96 © Application number: 87306054.5 @ Date of filing: 08.07.87 © Process for cosynthesis of ethylene glycol and dimethyl carbonate. ® Priority: 31.07.86 US 891093 © Proprietor: TEXACO DEVELOPMENT CORPO- RATION @ Date of publication of application: 2000 Westchester Avenue 03.02.88 Bulletin 88/05 White Plains, New York 10650(US) © Publication of the grant of the patent: @ Inventor: Knlfton, John Frederick 16.09.92 Bulletin 92/38 10900 Catsklll Trail Austin Texas 78750(US) © Designated Contracting States: BE DE FR GB NL © Representative: Ben-Nathan, Laurence Albert © References cited: et al EP-A- 0 000 880 Urquhart-Dykes & Lord 91 Wlmpole Street EP-A- 0 001 082 London W1M 8AH(GB) EP-A- 0 001 083 DE-A- 3 445 555 DE-B- 2 740 242 PATENT ABSTRACTS OF JAPAN, vol. 3, no. 87 (C-53) 25 July 1979 & JP-A-63023 METHODEN DER ORGANISCHEN CHEMIE vol. ^_ (HOUBEN-WEYL), 8, part 3, Georg (Q Thleme Verlag, 1952, EUGEN MUELLER et al CM m CM m m CM Note: Within nine months from the publication of the mention of the grant of the European patent, any person Q_ may give notice to the European Patent Office of opposition to the European patent granted. Notice of opposition LLI shall be filed in a written reasoned statement.