Thesis Edzard Scherpbier 20180816
Total Page:16
File Type:pdf, Size:1020Kb
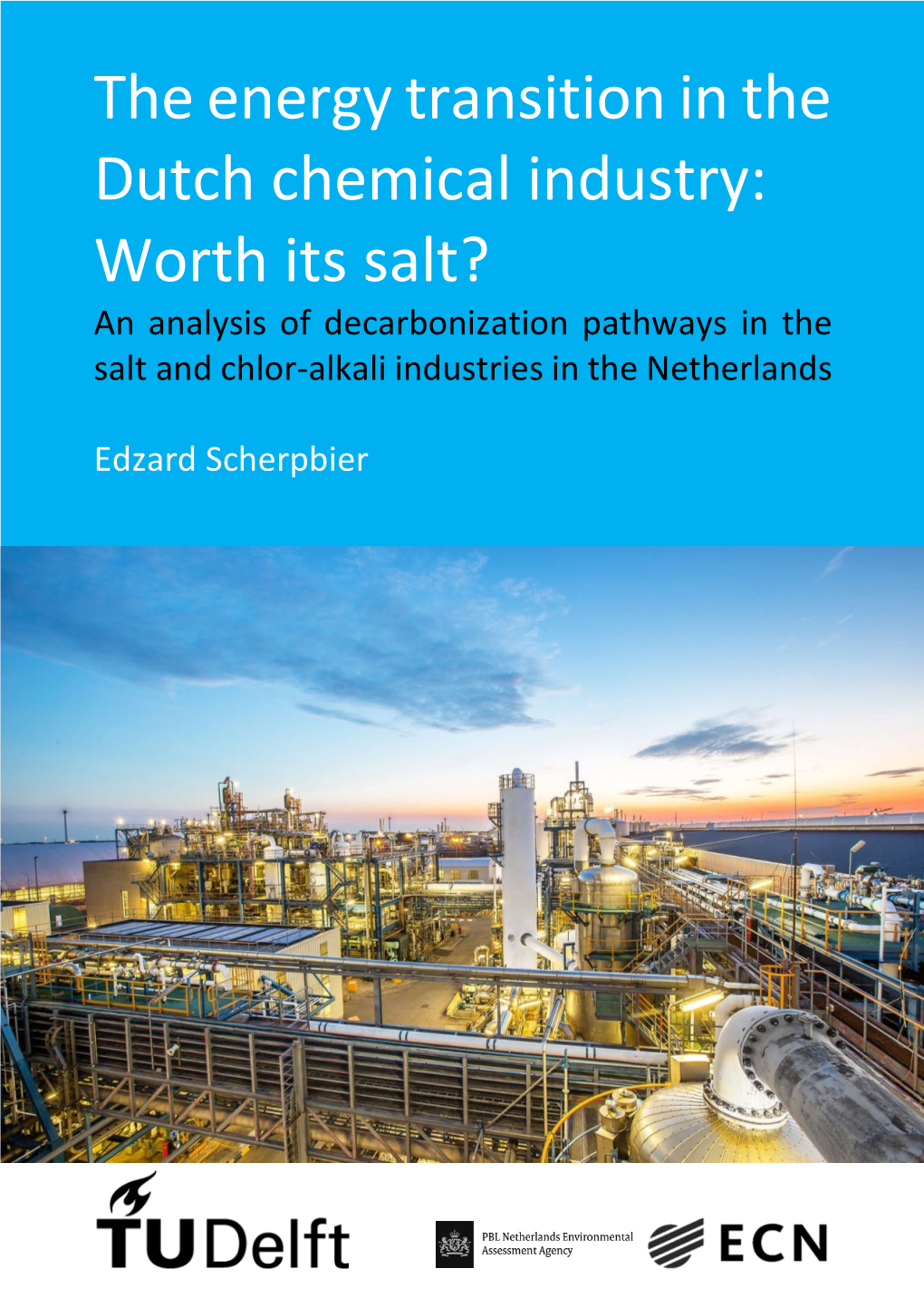
Load more
Recommended publications
-
Sodium Chloride Or Rock Salt | Peters Chemical Company
MSDS Sheet – Sodium Chloride or Rock Salt | Peters Chemical Company Call Now - 1-973-427-8844 Home Contact Us Deicers Airport Runway Deicers Deicing Articles Lime & Limestone Misc. Print This Page MATERIAL SAFETY DATA SHEET Product Name: Sodium Chloride – Rock Salt – Halite EPA Reg. No: N/A 1. PRODUCT IDENTIFICATION Product Name: Sodium Chloride – Rock Salt UN/MA#: N/A DOT Hazard Class: N/A 2. INGREDIENTS & RECOMMENDED OCCUPATIONAL EXPOSURE LIMITS TLV See Addendum 1 10 MG/M3 as nuisance dust. 3. PHYSICAL DATA Density: 40 – 70 lb/ft Boiling Point: N/A dry solid Melting Point: Partially decomposes at 12o F Vapor Pressure: N/A Vapor Density: N/A pH: 6-8 Solubility in Water: 100% Evaporation Rate: N/A Appearance and Odor: White Crystals and mild aromatic odor 4. FIRE AND EXPLOSION HAZARD DATA Flash Point: N/A Flammable Limits: N/A Fire Extinguishing Media: Considered non-combustible. Dry chemical. Foam, CO2, Water, Spray or Fog. Special Fire Fighting Procedures: Use self-contained breathing apparatus and full protective clothing. Fight fire from upwind side. Avoid run-off. Keep non-essential personnel away from immediate fire area, and out of any fall-out or run-off areas. Unusual Fire and Explosion Hazards: None 5. REACTIVITY DATA Stability: Stable Incompatibility: None Hazardous Decomposition or By-Products: None Conditions to Avoid: None Hazardous Polymerization: Will not occur http://www.peterschemical.com/sodium-chloride/msds-sheet-sodium-chloride-or-rock-salt/[1/8/2014 2:35:52 PM] MSDS Sheet – Sodium Chloride or Rock Salt | Peters Chemical Company 6. SPILL OR LEAK PROCEDURES Steps to be taken in case material is released: In case of release to the environment, report spills to the National Response Center 1-800-424-8802. -
Final Feasibility and Cost Analysis Findings and Recommendations Report
Final FEASIBILITY AND COST ANALYSIS FINDINGS AND RECOMMENDATION REPORT PARADOX VALLEY UNIT BYPRODUCTS DISPOSAL STUDY Submitted to: Wastren Advantage, Inc. 1571 Shyville Road Piketon, Ohio 45661 Submitted by: Amec Foster Wheeler Environment & Infrastructure, Inc. San Diego, California January 2017 Amec Foster Wheeler Project No. 1655500023 ©2016 Amec Foster Wheeler. All Rights Reserved. January 2017 Dave Sablosky Wastren Advantage, Inc. 1571 Shyville Road Piketon, Ohio 45661 Re: Final Feasibility, Cost Analysis, Findings, and Recommendation Report for Paradox Valley Unit Byproducts Disposal Study Dear Dave: The report included here satisfies the deliverable for the Paradox Valley Unit Evaporation Ponds Study 3: Final Feasibility, Cost Analysis, Findings, and Recommendations for Byproducts Disposal Report. As agreed with you and with Reclamation, this is a single combined report for the Byproducts Disposal Study that includes all elements anticipated from the Feasibility and Cost Analysis study, and the Findings and Recommendations report. This is a final version including all the information collected for Study 3 combined into a single report. It also includes the responses to the final comment matrix submitted by Reclamation. If you have any questions or concerns regarding this report, please contact Carla Scheidlinger at 858-300-4311 or by email at [email protected]. Respectfully submitted, Amec Foster Wheeler Environment & Infrastructure, Inc. Carla Scheidlinger Project Manager Amec Foster Wheeler Environment & Infrastructure, Inc. 9210 Sky Park Court, Suite 200 San Diego, California Tel: (858) 300-4300 Fax: (858) 300-4301 www.amecfw.com Wastren Advantage, Inc. Final Combined Findings and Recommendation Report Paradox Valley Unit Byproducts Disposal Study Amec Foster Wheeler Project No. -
SPR-691: Development of ADOT Application Rate Guidelines For
e SPR 691 OCTOBER 2015 Development of ADOT Application Rate Guidelines for Winter Storm Management of Chemical Additives through an Ambient Monitoring System Arizona Department of Transportation Research Center Development of ADOT Application Rate Guidelines for Winter Storm Management of Chemical Additives through an Ambient Monitoring System SPR‐691 October 2015 Prepared by: Ed Latimer, Richard Bansberg, Scott Hershberger, Theresa Price, Don Thorstenson, and Phil Ryder AMEC Environmental & Infrastructure 4600 E. Washington St., Suite 600 Phoenix, AZ 85034 Published by: Arizona Department of Transportation 206 S. 17th Ave. Phoenix, AZ 85007 In cooperation with U.S. Department of Transportation Federal Highway Administration Disclaimer This report was funded in part through grants from the Federal Highway Administration, U.S. Department of Transportation. The contents of this report reflect the views of the authors, who are responsible for the facts and the accuracy of the data, and for the use or adaptation of previously published material, presented herein. The contents do not necessarily reflect the official views or policies of the Arizona Department of Transportation or the Federal Highway Administration, U.S. Department of Transportation. This report does not constitute a standard, specification, or regulation. Trade or manufacturers’ names that may appear herein are cited only because they are considered essential to the objectives of the report. The U.S. government and the State of Arizona do not endorse products or manufacturers. Technical Report Documentation Page 1. Report No. 2. Government Accession No. 3. Recipient's Catalog No. FHWA‐AZ‐15‐691 4. Title and Subtitle 5. Report Date Development of ADOT Application Rate Guidelines for Winter Storm October 2015 Management of Chemical Additives through an Ambient Monitoring 6. -
Environmental Management Plan Salt Mining
Gecko Salt (Pty) Ltd –Environmental Management Plan for Mile 68 Salt Pan, Erongo Region, Namibia – November 2020 Environmental Management Plan Salt Mining - Mile 68 Salt Pan November 2020 Gecko Salt (Pty) Ltd –Environmental Management Plan for Mile 68 Salt Pan, Erongo Region, Namibia – November 2020 Author Philip Hooks Version 01 Reviewer Werner Petrick Date 04.11.2020 Reference Hooks, P., 2020. Environmental Management Plan for Mining Salt at Mile 68 Salt Pan. Assessed for Gecko Salt (Pty) Ltd. Gecko Salt (Pty) Ltd –Environmental Management Plan for Mile 68 Salt Pan, Erongo Region, Namibia – November 2020 ABREVIATIONS DWA Department of Water Affairs EA Environmental Audit EAP Environmental Assessment Practitioner ED Environmental Control Officer ECP Environmental Control Procedure EIA Environmental Impact Assessment EMP Environmental Management Plan ERP Emergency Response Plan MEFT Ministry of Environment, Forestry & Tourism ML Mining License MME Ministry of Mines & Energy MSDS Materials Safety Data Sheet PM Project Manager RA Roads Authority Gecko Salt (Pty) Ltd –Environmental Management Plan for Mile 68 Salt Pan, Erongo Region, Namibia – November 2020 1. Introduction 1.1 Project background Gecko Salt (Pty) Ltd (Gecko) plans to develop a solar salt production facility at the Mile 68 salt pan. The saline pan lies within the Dorob National Park along the central coastline north of the town of Henties Bay. Gecko was granted an exploration licence (EPL4426) over this pan and its surrounding in 2015. The company intends to apply for a mining licence over the area for producing salt on the saline pan. The envisaged development includes a 13-kilometre-long brine pipeline from Gecko’s Mining Licence at Cape Cross (ML210) to the future solar salt production facility at Mile 68. -
Operating Instructions Lab Washers PLW 6011 PLW 6111
Operating instructions Lab washers PLW 6011 PLW 6111 Read the operating instructions carefully before installing and using the machine. This will help en – UK protect users from personal injury and help prevent damage to the machine. CONTENTS Contents 1. GENERAL RULES ..................................................................................................... 6 1.1 Limitation of liability ............................................................................................................... 6 1.2 Validity, content and storage ................................................................................................ 6 2. PRODUCT INFORMATION ....................................................................................... 7 2.1 Appropriate use ...................................................................................................................... 8 2.2 Safety instructions and warnings ......................................................................................... 9 Appropriate use .................................................................................................................... 9 Risk of injury ......................................................................................................................... 9 Quality assurance ............................................................................................................... 11 Safety with children ........................................................................................................... -
Road Salt and Water Quality Fact Sheet WMB-4
WMB-4 2021 Road Salt and Water Quality Snowfall in New Hampshire and the necessity to travel on roads require winter snow and ice management by the state, municipalities and the private sector. Deicing materials are often used in order to keep the public safe during these winter weather events. The most commonly used de-icing chemical is sodium chloride (NaCl), commonly known as road salt. Road salt is readily available, and it is easy to handle, store and spread. Its purpose is to reduce the adherence of snow and ice to the pavement, preventing the formation of hard pack. Once hard pack forms, it is difficult to remove by plowing alone. In the United States from 2005-2009 an average of 23 million tons of salt were applied to our roads, parking lots, sidewalks and driveways each year.1 Studies have shown that, in urbanized areas, about 95% of the chloride inputs to a watershed are from road and parking lot deicing. In four chloride impaired watersheds in the southern I-93 corridor of New Hampshire, road salt sources were 10% to 15% from state roads, 30% to 35% from municipal roads, and 45% to 50% from private roads and parking lots. How Salt Works Pounds of Ice Melted per Pound of Salt The first step in melting ice is to lower its freezing point. This is done through the formation of brine where salt 50 crystals pull water molecules out of ice formation. Once 40 the brine is formed, melting is greatly accelerated. The rate 30 at which melting occurs is dependent on the temperature. -
Exotic Salts
Guide #1 - Exotic Salts Exotic Salts typically refer to naturally occurring mineral salts or Himalayan Pink Mineral Salt salts collected from bodies of water through evaporation. The Himalayan It’s one of the purest salts available on earth. Mined from deep in the Pink Salt is an example of mineral salt, while Fleur de Sel is an example Himalayan Mountains, this salt crystallized more than 200 million years of evaporated salt. Mineral salts are actually a type of sedimentary rock, ago and remains protected from modern-day pollution. It contains more than 84 trace minerals with none of the additives or aluminum com- and are mined. They often have high mineral content, and a unique set pounds found in refined salts. Uses: Grilling or roasting meat, fish or of flavors. Salts collected from bodies of water are done so through the chicken, and the coarse grain size can be used with a salt grinder. evaporation of rivers, oceans, ponds, etc. The flavor, texture, color, etc. of these salts will differ depending on the water type, the region where the Hawaiian Black Sea Salt water is collected, the time of year, and the evaporation process used. Characterized by a stunning black color and silky texture. Solar evapo- rated Pacific sea salt is combined with activated charcoal. The charcoal Alaea Hawaiian Sea Salt compliments the natural salt flavor and adds numerous health benefits. Harvested reddish Hawaiian clay enriches the salt with Iron Oxide. Savor Uses: Finishing, salads, meats, and seafood. a unique and pleasant flavor while roasting or grilling meats. It is the traditional and authentic seasoning for native Hawaiian dishes such as Kala Namak Indian Black Mineral Salt Kailua Pig, Hawaiian Jerky and Poke. -
A Grain of Salt
Illinois Wesleyan University Digital Commons @ IWU The Kemp Foundation's Teaching Honorees for Teaching Excellence Excellence Award Ceremony 7-27-2020 A Grain of Salt Timothy Rettich Illinois Wesleyan University Follow this and additional works at: https://digitalcommons.iwu.edu/teaching_excellence Part of the Higher Education Commons Recommended Citation Rettich, Timothy, "A Grain of Salt" (2020). Honorees for Teaching Excellence. 53. https://digitalcommons.iwu.edu/teaching_excellence/53 This Article is protected by copyright and/or related rights. It has been brought to you by Digital Commons @ IWU with permission from the rights-holder(s). You are free to use this material in any way that is permitted by the copyright and related rights legislation that applies to your use. For other uses you need to obtain permission from the rights-holder(s) directly, unless additional rights are indicated by a Creative Commons license in the record and/ or on the work itself. This material has been accepted for inclusion by faculty at Illinois Wesleyan University. For more information, please contact [email protected]. ©Copyright is owned by the author of this document. Kemp Award Address 2020 Timothy Rettich “A Grain of Salt” April 8! The theme of this talk was written with this date for Honors Convocation in mind. It was intended to be not only timely, but also somewhat light-hearted. The times have changed, but I decided to keep the same talk, thinking that light-heartedness, like toilet paper, is now in short supply. But by keeping the same talk you will note some anachronisms. Those of you playing along at home can keep track of how many temporal mistakes I make. -
Annual Report 2019
Annual Report 2019 www.kpluss.com With its mineral products, K+S helps farmers secure the world’s food supply, keeps industries running, enriches consumers’ daily live’s and ensures safety in winter. The focus is on the customer and their needs. In order to position our- selves successfully on a global scale in the long term, we are increasingly acting on the basis of innovative future concepts with which we can develop products and growth markets. This transformation phase is supported by our experience of more than 130 years. It allows us to navigate safely through the challenges of the reorganization: K+S is versatile. K+S worldwide We meet the growing demand for mineral products mainly from production sites in Europe, North and South America, and through a global distribution network. 39 6 32 4 13 Number of sites ten-yeAr SummAry K+S group 1 2010 2011 2012 2013 2014 2015 2016 2017 2018 2019 Profit and Loss Revenues € million 4,632.7 3,996.8 3,935.3 3,950.4 3,821.7 4,175.5 3,456.6 3,627.0 4,039.1 4,070.7 EBITDA 2 € million 953.0 1,146.0 1,033.3 907.2 895.5 1,057.5 519.1 576.7 606.3 640.4 EBITDA-Margin % 20.6 28.7 26.3 23.0 23.4 25.3 15.0 15.9 15.0 15.7 Depreciation 3 238.5 239.8 229.2 251.3 254.3 275.9 289.8 305.9 379.1 431.9 Group earnings from continued operations, adjusted 4 € million 453.8 625.6 538.1 437.1 366.6 542.3 130.5 145.0 85.4 77.8 Earnings per share from continued operations, adjusted 4 € 2.37 3.27 2.81 2.28 1.92 2.83 0.68 0.76 0.45 0.41 Cash flow Operating Cash flow € million 826.4 633.4 607.2 755.7 719.1 669.4 445.4 306.8 308.7 639.8 Capital expenditure 5 € million 188.6 293.1 465.5 742.5 1,153.2 1,278.8 1,170.8 810.8 443.2 493.3 Adjusted Free Cash flow € million 667.3 216.6 199.1 48.7 -306.3 -635.9 -776.8 -389.8 -206.3 139.7 Balance Sheet Balance sheet total € million 5,573.7 6,056.9 6,596.6 7,498.2 7,855.2 8,273.6 9,645.5 9,754.4 9,966.2 10,592.2 Equity € million 2,651.6 3,084.6 3,393.9 3,396.6 3,974.5 4,295.6 4,552.2 4,160.7 4,144.1 4,495.1 Equity ratio % 47.6 50.9 51.4 45.3 50.6 51.9 47.2 42.7 41.6 42.4 Net financial liabilities as of Dec. -
Decarbonisation Options for the Dutch Salt Industry
DECARBONISATION OPTIONS FOR THE DUTCH SALT INDUSTRY E.L.J. Scherpbier, H.C. Eerens 31 March 2021 Manufacturing Industry Decarbonisation Data Exchange Network Decarbonisation options for the Dutch salt industry © PBL Netherlands Environmental Assessment Agency; © TNO The Hague, 2021 PBL publication number: 3477 TNO project no. 060.33956 / TNO publication no. TNO 2021 P11186 Authors E.L.J. Scherpbier and H.C. Eerens Acknowledgements Prof.dr.ir. C.A. Ramirez Ramirez (Delft University of Technology) Dr.ir. J.H. Kwakkel (Delft University of Technology) J.R. Ybema (Nouryon Specialty Chemicals) Prof.dr.ir. S.A Klein (Nouryon Specialty Chemicals) Helen Roesink (Nedmag) MIDDEN project coordination and responsibility The MIDDEN project (Manufacturing Industry Decarbonisation Data Exchange Network) was initiated and is also coordinated and funded by PBL and TNO EnergieTransitie. The project aims to support industry, policymakers, analysts, and the energy sector in their common efforts to achieve deep decarbonisation. Correspondence regarding the project may be addressed to: D. van Dam (PBL), [email protected], or S. Gamboa Palacios (TNO), [email protected]. Erratum An earlier version of this report was published in 2019, but contained errors in relation to the description of the magnesium salt production. This version also includes a number of minor updates. This publication is a joint publication by PBL and TNO and can be downloaded from: www.pbl.nl/en. Parts of this publication may be reproduced, providing the source is stated, in the form: E.L.J. Scherpbier and H.C. Eerens (2021), Decarbonisation options for the Dutch salt industry. PBL Netherlands Environmental Assessment Agency and TNO, The Hague. -
1A Trobada Internacional D'arqueologia Envers L'explotació
Alfons Fíguls – Olivier Weller (Editors) 1a Trobada internacional d'arqueologia envers l'explotació de la sal a la prehistòria i protohistòria Cardona,Alfons Fíguls6, 7 i 8– deOlivier desembre Weller del (Editors) 2003 1a Trobada internacional d'arqueologia envers l'explotació de la sal a la prehistòria i protohistòria Cardona, 6, 7 i 8 de desembre del 2003 Alfons Fíguls i Alonso – Olivier Weller (Editors) 1a Trobada internacional d'arqueologia envers l'explotació de la sal a la prehistòria i protohistòria Cardona, 6-8 de desembre del 2003 www.saltmeeting.ajcardona.info [email protected] 3 Alfons Fíguls – Olivier Weller (Editors) 1a Trobada internacional d'arqueologia envers l'explotació de la sal a la prehistòria i protohistòria Cardona,Alfons Fíguls 6, 7 –i 8Olivier de desembre Weller (Editors) del 2003 1a Trobada internacional d'arqueologia envers l'explotació de la sal a la prehistòria i protohistòria Cardona, 6, 7 i 8 de desembre del 2003 Alfons Fíguls i Alonso i Olivier Weller (Editors) 1a Trobada internacional d'arqueologia envers l'explotació de la sal a la prehistòria i protohistòria Cardona, 6-8 de desembre del 2003 Archæologia Cardonensis I Institut de recerques envers la Cultura (IREC) www.saltmeeting.ajcardona.info [email protected] Director de la col·lecció Archaeologia Cardonensis: Alfons Fíguls i Alonso Comissió històrica assessora: Rosa M. Lanaspa i Cuadrench, Agustín Fuentes Martínez i Alfons Fíguls i Alonso Col·laboradors: Jorge Bonache Albacete, Joan González Huertas i M. Dolores Bonache Alabecte Assessora lingüística: Loreto Serena i Davins Són prohibides, sense autorització escrita dels editors, la reproducció total o parcial d’aquesta obra per a qualsevol procediment, incloent-hi la reprografia i el tractament informàtic. -
Property Auction Catalogue This Sale Will Be a Live Online Only Auction, Pre-Registration Is Required
Monday 7th September 2020 6.30pm start Property auction catalogue This sale will be a live online only auction, pre-registration is required. Property auctions The Moat House Hotel, Stoke-on-Trent, ST1 5BQ Auction Dates Closing Date For Entries 20th April 13th March 1st June 24th April 13th July 5th June 7th September 24th July 5th October 28th August 9th November 25th September 7th December 30th October All auctions start at 6.30pm Freehold & Leasehold Lots offered in conjunction with... 02 View property auction results at buttersjohnbee.com The region’s number 1 property auctioneer John Hand Donna Fern Rob Oulton Auction Manager Auction Negotiator Auctioneer Here at butters john bee we have over 150 years’ experience of selling property at auction. Welcome aboard our next auction catalogue, once again as is becoming the norm it will be an ONLINE ONLY SALE. We are doing our utmost to keep things on track, and we had a great deal of success with our July sale. We have always offered remote bidding at all our auctions, and I’m pleased to say that we are now working in partnership with EIG (Essential Information Group) who will be hosting our live sale as well as the Legal Pack page, streamlining the service we are able to offer and making it much easier for you to register to bid. This sale will run in exactly the same format Our next scheduled sale is 5th October, as as usual, as in we will have our auctioneer of yet we are still unsure if this will be online on the podium offering each Lot in turn, but or we can have live sale (obviously with there will be no live audience just internet some measures put in place) we will update bidders, people on the phone and no doubt you as soon as we can get confirmation some proxy bids.