CNC Production Routing Guide
Total Page:16
File Type:pdf, Size:1020Kb
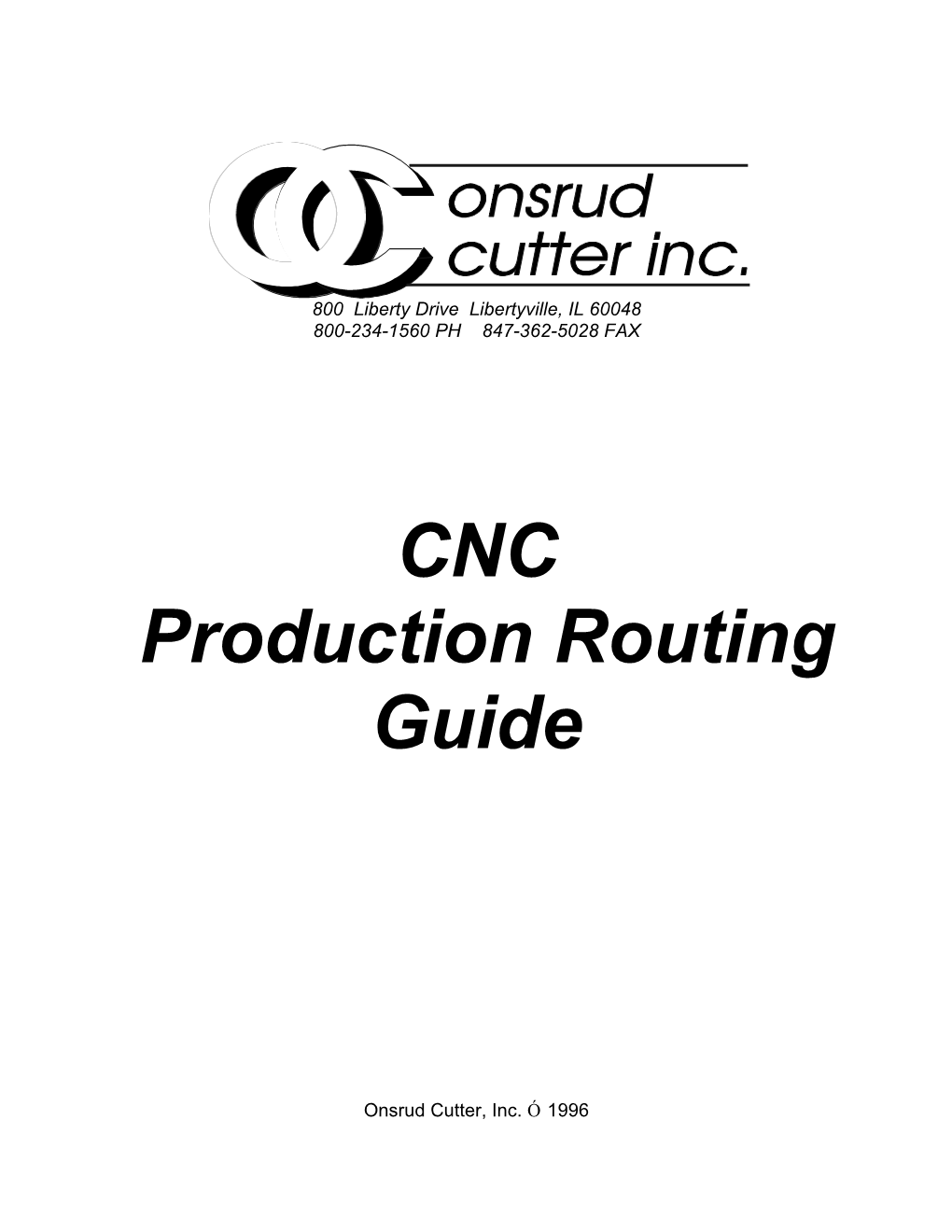
Load more
Recommended publications
-
2018 Line Card
H.D. Chasen Company Inc. H. D. CHASEN TOOL GROUP INVENTORY SOLUTIONS LOGISTICS www.steelerectortools.com “OTHERS TALK... WE STOCK.” 2018 LINE CARD 40 Lake Street|Somerville, MA|02143 P|617.666.9090 www.hdchasen.com INDEX OF PRODUCTS INDEX OF PRODUCTS A B Abrasive Back Stand Idler Units Abrasives - Abrasive Mounted Points Back Support Systems Abrasives - Bristle Discs - Roloc / Cup Wheel Bags - Tool Bags Abrasives - Cartridge Rolls Balldriver Hex Screwdrivers Abrasives - Cloth Sanding Rolls Balldriver Insert Bits Abrasives - Coated Abrasives Balldriver L-Wrench / Sets Abrasives - Combiwheels Abrasive / Scotchbrite Balldriver Power Bits Abrasives - Diamond Lapping Film Discs Balldriver T-Handle - Sets & Singles Abrasives - Diamond Lapping Film Sheets Bandsaws - Electric Abrasives - Diamond Products Bars - Boring Abrasives - Disc Pad Holder Bars - Breaker 3/8,1/2,3/4 Drive Abrasives - Discs PSA Cloth / Paper, Resin Fibre Bars - Claw Bar 5' Abrasives - Discs Quick Change Bars - Connecting Bars Abrasives - Discs Resin Fibre Bars - Diamond Point 5' Abrasives - Discs Roloc A/O, Regalite Polycut Bars - Grizzly Bar Abrasives - Discs Velcro S/C, Gold Bars - Jimmy Bars Abrasives - Flap Wheels Bars - Offset Pinch Bars - 14" - 48" Abrasives - Lapping Film Discs Bars - Pinch Bars 13-1/2" - 48" Abrasives - Lapping Film Sheets Bars - Pinch Point Crow Bar / 3' - 5-1/2' Abrasives - Microfinishing Film Discs Bars - Pry Abrasives - Microfinishing Film Sheets Bars - San Angelo Digging 5' - 7' Abrasives - Mounted Points / Cotton Abrasive Bars - Telegraph Lining -
Atla Fibre Co Article Fabricating Cutting Thermoset
SpecialFocus Fabricating and Cutting Thermoset Materials Plastics Fabrication by Mark Mush s the machining of plastic materials cannot be mastered in one diameter run at 3,000-3,600 rpm will give good results cutting dry with a setting, the same can be said, probably more so, of thermosets good exhaust system. Material feed should be as fast possible without forcing A(FR4/G-10, G-11, phenolics). Glass epoxies and phenolics have the saw. Idling creates friction and heat, which cause excessive dulling and traditionally been unfairly characterized as materials that many machine burning. A flood of water or water-soluble coolants on the work and wheel shops or fabricators avoid due to their dust, wear and tear on equipment can be used when necessary to prevent overheating. Abrasive wheel cutting and tools and the overall toughness of the material. To the contrary, with under water is also recommended. a little bit of practice and patience, most fabricators can master the art of thermosets. What follows is a guide to get you started in that process. Turning Mastering these suggestions will not immediately make you an expert Paper and fabric grades machinist of these materials but should significantly improve your skills. Ordinary high-speed tool steel can be used in finishing operations for all Paper and fabric grades thermoset grades. However, carbide-tipped tools may prove more economi- cal and will hold sizes more accurately from piece to piece. About .010" stock Thermoset materials machine well with proper techniques. As a rule, they should be left for finishing. Thermosets can be turned at 400 surface feet per machine more readily than metals with standard machine tools such as minute with high-speed tools and about twice as fast with carbides. -
ROUTER BIT GEOMETRY Feed the Router Bit in Such a Manner So That in Moving Through the Terms Work It Has a Chance to Bite Or Cut Its Way Freely
Compression Spiral ROUTER BIT GEOMETRY Feed the router bit in such a manner so that in moving through the Terms work it has a chance to bite or cut its way freely. If the feedrate is too Helix Angle- Angle of the cutting flute, it is measured relative to the axis fast, strain and deflection will occur. If it is too slow, friction and of the cutting toot. burning will occur. Both too fast and too slow will decrease its life and cause breakage. Flute Fadeout- The length between the end of the cutting length and the begin of the shank length The router mechanism must be well maintained for any cutting tool to perform properly. Check the collet for wear regularly. Inspect tools for CEL- Cutting edge length. collet marks indicating slipping due to wear or dust build up. Check Shank Length- The length of the cutter shank that can be inserted into spindle on a dial indicator for run-out. Collet and run-out problems cause the collet. premature toot failure and associated production difficulties. Do not use OAL- Overall cutter length. adaptor bushings to reduce size of the collet on a routing or production basis. Tools will not perform properly in bushings over an extended CED- Cutting edge diameter. period of time. Bushings are for prototype, experimentation, test and Shank Diameter- The diameter of the shank to be inserted into the collet. evaluation and not for production. Single Flute Wherever possible, use a coolant when routing. Heat caused by Use for faster feed rates in softer materials. -
Carbide Tipped Annular Cutters Are Engineered for Cutting 3” and 4” Thick Steel, Pipe, and Square Channel
Innovative Cutting Tool Solutions 2011 Product Catalog Your Productivity Partner Professional Grade Products Champion has been dedicated to servicing professionals with industrial grade products and services since 1897. Our product range includes twist drills, end mills, taps, dies, cutters, power tools, and masonry tools that are engineered for peak performance. Our distribution network serves cutting tool users in all fifty U.S. States, and is expanding internationally. Our commitment to same-day shipping and superior technical support give you, our customer, the Champion Edge. Innovative Cutting Tool Solutions Our CT5 Carbide tipped hole cutter has been completely redesigned. The result is faster hole penetration, and longer tool life. The design enhancements include a new carbide tip pocket for faster chip evacuation, improved carbide tips, stepped pilot drill for smoother penetration, and stiffer spring for positive slug ejection. The new CM95X series of SDS-Plus hammer bits features a “solid-tip” which penetrates rebar-imbedded concrete. These state of the art SDS-Plus bits penetrate the toughest aggregates including Vermont granite. Champion’s iPac system provides professional grade cutting tools in individual and combination packs. The iPac range includes twist drills, taps, and screw extractors. DT22HEX combination drill and taps create a hole and thread in one application. Available in NC/NF, and metric sizes, these industrial quality tools are available from 6-32 machine screw size to 1/2-13. Perfect for industrial, MRO and electrical professions. Champion’s CT9 was designed in conjunction with locksmiths whose work requires the installation of locksets in steel doors. CT9 hole cutters enable quick drilling of 1-1/2” and 2-1/8” holes in steel doors. -
Planing and Profiling
Anpassung der Rückenstärke für Druck noch nicht ausgeführt Planing and profiling Leitz Lexicon Edition 7 Version 2 Explanation of abbreviations A = dimension A LH = left hand rotation ae = cutting thickness (radial) ap = cutting depth (axial) M = metric thread ABM = dimension MBM = minimum order quantity APL = panel raising length MC = multi-purpose steel, coated APT = panel raising depth MD = thickness of knife AL = working length min-1 = revolutions per minute (RPM) AM = number of knives MK = morse taper AS = anti sound (low noise design) m min-1 = metres per minute m s-1 = metres per second b = overhang B = width n = RPM BDD = thickness of shoulder nmax. = maximum permissible RPM BEM = note NAL = position of hub BEZ = description ND = thickness of hub BH = tipping height NH = zero height BO = bore diameter NL = cutting length NLA = pinhole dimensions CNC = Computerized Numerical Control NT = grooving depth d = diameter P = profile D = cutting circle diameter POS = cutter position D0 = zero diameter PT = profile depth DA = outside Diameter PG = profile group DB = diameter of shoulder DFC = Dust Flow Control (optimised chip clearance) QAL = cutting material quality DGL = number of links DIK = thickness R = radius DKN = double keyway RD = right hand twist DP = polycrystalline diamond RH = right hand rotation DRI = rotation RP = radius of cutter FAB = width of rebate S = shank dimension FAT = depth of rebate SB = cutting width FAW = bevel angle SET = set FLD = flange diameter SLB = slotting width fz = tooth feed SLL = slotting length fz eff = effective tooth feed SLT = slotting depth SP = tool steel GEW = thread ST = Cobalt-basis cast alloys, GL = total length e.g. -
Milling Speeds & Feeds
MADE IN USA MILLING SPEEDS & FEEDS Carbide Tipped Speeds & feeds are starting recommendations only. Factors such as machine, fixture and tooling rigidity, horsepower available, coolant application and others will affect the performance significantly. Please read machine operators instructions and use all safety shields and glasses before performing these operations. Use these charts for carbide tipped milling cutters. IPT = Inches Per Tooth IPM = Inches Per Minute RPM = Rotations Per Minute SFPM = Surface Feet Per Minute Cutter Diameter = Diameter of the cutter in inches RPM=SFPM*3.82/CUTTER DIAMETER IPM=IPT*RPM*#TEETH APPLICATION - MILLS AND SAWS CLASS OF MATERIAL SURFACE FEET INCHES PER MATERIALS BRINELL PER MINUTE TOOTH (SFPM) (IPT) 30-150* ALUMINUM ALLOY - WROUGHT 1000-2000 .004-.008 (500kg) MAGNESIUM ALLOY 50-90* 750-1500 .004-.008 NON-FERROUS (SOFT) LEAD ALLOY 10-20* 300-1000 .004-.008 NON-METAL AND PLASTIC – 1500-3000 .004-.008 ZINC ALLOY - DIE CAST 80-100 750-1500 .005-.010 ALUMINUM BRONZE 40-175 200-600 .003-.006 BRASS ALLOY - LEADED AND 10-100Rb 400-800 .004-.008 NON-FERROUS FREE CUTTING (HARD) NICKEL SILVER 10-100Rb 200-400 .003-.006 COPPER ALLOY - TOUGH 40-200* 200-500 .004-.008 DUCTILE CAST IRON - AUSTENITIC 120-275 75-150 .002-.004 DUCTILE CAST IRON - FERRITIC 140-270 250-400 .003-.006 DUCTILE CAST IRON - MARTENSITIC 270-400 200-300 .003-.006 CAST IRON GRAY - PEARLITIC 220-320 120-300 .002-.004 GRAY - FERRITIC 110-240 250-425 .003-.006 MALLEABLE CAST IRON - 200-320 130-225 .002-.004 MARTENSITIC LOW AND MEDIUM CARBON STEEL -
Caddo Archeology Journal
CCaddoaddo AArcheologyrcheology JJournalournal Volume 16 Spring 2007 CADDO ARCHEOLOGY JOURNAL P.O. Box 8419 Austin, TX 78712-8419 EDITORIAL BOARD TIMOTHY K. PERTTULA 10101 Woodhaven Dr. Austin, TX 78753 e-mail: [email protected] CHESTER P. W ALKER 5309 DUVAL STREET AUSTIN, TX 78751 e-mail: [email protected] GREGORY VOGEL Center for American Archeology P.O. Box 366 Kampsville, IL 62053 [email protected] T. CLAY SCHULTZ 507 Franklin San Marcos, TX 78666 [email protected] LIASON WITH THE CADDO NATION OF OKLAHOMA ROBERT CAST Tribal Historic Preservation Offi cer Caddo Nation of Oklahoma P.O. Box 487 Binger, OK 73009 e-mail: [email protected] ISSN 1522-0427 Printed in the United States of America at Morgan Printing in Austin, Texas 2007 2 ◆ Spring 2007 Table of Contents Proposal For A 2007 Caddo Archaeology Summit Meeting . 5 Timothy K. Perttula Byram Ferry (16BO17): A Middle to Late Caddo Period Mound Site in the Red River Floodplain, Northwest Louisiana. 9 Jeffery S. Girard Archaeological Investigations of the Lang Pasture (41AN38) Midden Deposits on private property west of the SH 155 Right-of-Way, Anderson County, Texas . 27 Timothy K. Perttula, Bo Nelson, Mark Walters, and LeeAnna Schniebs Remote Sensing at the Horace Cabe Site (41BW14). 37 Chester P. Walker and Timothy K. Perttula The History of Archaeological Investigations at the Jamestown Mound Site (41SM54), An Archaeological Concervancy Preserve in Smith County, Texas . 45 Timothy K. Perttula Leaning Rock Site (41SM325) Lithics . 57 Harry J. Shafer The Organization of Novaculite Tool Production: Quarry-Workshop Debitage Comparisons . 71 Mary Beth Trubitt CADDO ARCHEOLOGY JOURNAL ◆ 3 PROPOSAL FOR A 2007 CADDO ARCHAEOLOGY SUMMIT MEETING Timothy K. -
Machining of Aluminum and Aluminum Alloys / 763
ASM Handbook, Volume 16: Machining Copyright © 1989 ASM International® ASM Handbook Committee, p 761-804 All rights reserved. DOI: 10.1361/asmhba0002184 www.asminternational.org MachJning of Aluminum and AlumJnum Alloys ALUMINUM ALLOYS can be ma- -r.. _ . lul Tools with small rake angles can normally chined rapidly and economically. Because be used with little danger of burring the part ," ,' ,,'7.,','_ ' , '~: £,~ " ~ ! f / "' " of their complex metallurgical structure, or of developing buildup on the cutting their machining characteristics are superior ,, A edges of tools. Alloys having silicon as the to those of pure aluminum. major alloying element require tools with The microconstituents present in alumi- larger rake angles, and they are more eco- num alloys have important effects on ma- nomically machined at lower speeds and chining characteristics. Nonabrasive con- feeds. stituents have a beneficial effect, and ,o IIR Wrought Alloys. Most wrought alumi- insoluble abrasive constituents exert a det- num alloys have excellent machining char- rimental effect on tool life and surface qual- acteristics; several are well suited to multi- ity. Constituents that are insoluble but soft B pie-operation machining. A thorough and nonabrasive are beneficial because they e,,{' , understanding of tool designs and machin- assist in chip breakage; such constituents s,~ ,.t ing practices is essential for full utilization are purposely added in formulating high- of the free-machining qualities of aluminum strength free-cutting alloys for processing in alloys. high-speed automatic bar and chucking ma- Strain-hardenable alloys (including chines. " ~ ~p /"~ commercially pure aluminum) contain no In general, the softer ailoys~and, to a alloying elements that would render them lesser extent, some of the harder al- c • o c hardenable by solution heat treatment and ,p loys--are likely to form a built-up edge on precipitation, but they can be strengthened the cutting lip of the tool. -
BAND SAW BLADES Welcome to ARNTZ Your Cutting Expert for the Entire World of Metals
2021 Edition FactBook BAND SAW BLADES Welcome to ARNTZ Your cutting expert for the entire world of metals. 225 years of manufacturing, 225 years of tools, 225 years of passion: We are proudly looking back on a long tradition while facing the future with excitement. Complex materials are opening up new markets and alloys are developing along with higher requirements of their products behind. This requires new and innovative cutting solutions. Our specialists are being challenged with the demands of many different markets – daily. We are familiar with the materials and their cross sections – over all industries and down to the detail. Our operational structures allow us to quickly and indivi- dually address the individual need of our customers and develop optimal solutions close to you. We will assist you from the first question up to fine-tuning. Even at your site if required. Saw blades from ARNTZ are high-performance tools – economical, precise and perfectly matched to the relevant application. Our actions are guided by our high quality standards and our passion for what we do. We deliver sawing technology „Made in Germany“ that you can depend on worldwide – promised ! Innovative cutting technology. Optimized operating processes and certified quality Our experienced service technicians provide in-depth expert controls are the foundation of ARNTZ’s high-end saw knowledge that has been adapted to fit your exact require- blades. Every single step in the production process goes ments. Alongside telephone assistance and on-site support, through our multilayered control system to guarantee we also offer training modules targeted to your require- our quality standards. -
Dimar Dado Set Instructions
Carbide Tipped Dado Sets - General Purpose Carbide Tipped Dado Sets - General Purpose Tool number Description Dia. Teeth Kerf Bore Tool number Description Dia. Teeth Kerf Bore 8-24 DADO Complete Set 8" 24 13/16" 5/8" 6-18 DADO CL Complete Set 6" 18 13/16" 5/8" 8-1/16 Dado Chipper 8" 2 1/16" 5/8" 6-1/16 Dado Chipper 6” 2 1/16" 5/8" 8-1/8 Dado Chipper 8" 2 1/8" 5/8" 6-1/8 Dado Chipper 6" 2 1/8" 5/8" 8-1/4 Dado Chipper 8" 2 1/4" 5/8" 6-1/4 Dado Chipper 6" 2 1/4" 5/8" 8-24R Saw Blade R 8" 24 1/8" 5/8" 6-18R Saw Blade R 6" 18 1/8" 5/8" 8-24L Saw Blade L 8" 24 1/8" 5/8" 6-18L Saw Blade L 6” 18 1/8" 5/8" Negative Hook Tooth Design Suitable for Wood & Melamine Chip Limiter - will prevent kickback Tool number Description Dia. Teeth Kerf Bore Tool number Description Dia.Teeth Kerf Bore www.dimarcanada.com 8-24 DADO-1 Complete Set 8" 24 13/16" 1" 8-24 DADO-CL Complete Set 8" 24 13/16" 5/8" 8-1/16-1 Dado Chipper 8" 2 1/16" 1" 8-1/16 Dado Chipper 8" 2 1/16" 5/8" 8-1/8-1 Dado Chipper 8" 2 1/8" 1" 8-1/8 Dado Chipper 8" 2 1/8" 5/8" 8-1/4-1 Dado Chipper 8" 2 1/4" 1" 8-1/4 Dado Chipper 8" 2 1/4" 5/8" 8-24R-1 Saw Blade R 8" 24 1/8" 1" 8-24RC Saw Blade R 8" 24 1/8" 5/8" 8-24L-1 Saw Blade L 8" 24 1/8" 1” 8-24LC Saw Blade L 8" 24 1/8" 5/8” DADO SET Negative Hook Tooth Design Suitable for Wood & Melamine Chip Limiter - will prevent kickback INSTRUCTIONS Carbide Tipped Dado Sets - For Melamine Tool number Description Dia. -
Antares, Inc. Fact Sheets Surface Engraving © 2011 - Antares, Inc
Antares, Inc. Fact Sheets Surface Engraving © 2011 - Antares, Inc. Section One - Burnishing Description Burnishing is a surface marking technique intended for coated metals - usually lacquered brass - where the coating is removed to expose the bare metal. It is a method of rotary engraving on metals that tends to bridge the gap between diamond drag (scratch engraving) and routing. The biggest advantage of burnishing is that it enables the engraver to produce wider line widths than are obtainable with a diamond graver with- out having to cut deeply into the metal. Burnishers can be used with single and multiple line fonts, and are excellent for producing detailed line and logo work on metal. Burnishing offers the ability to create enhanced effects on both lettering and graphics and is relatively simple process. Rotating Tools Non-Rotating Point Variable Tip Sizes Tip Only Cutting with Depth Surface Marking Only Application The most common application is on the brass plates on trophies and plaques. This “trophy brass” is a rela- tively hard material that yields excellent burnishing results. It is available in various gold tones with clear or colored lacquer coatings. When burnishing the gold material, the lacquer is removed exposing the bare metal. The burnished areas can then be oxidized or blackened resulting in a gold plate with contrasting black letters. (See “Color Filling Fact Sheet”). When burnishing the colored materials, the result is a colored plate with contrasting gold letters without the need for further treatment. Burnishing can also be done on materials other than brass. However, much of the success or failure de- pends on the hardness of the material. -
Helical's Machining Guidebook
Helical MACHINING GUIDEBOOK Quick Reference eBook for CNC Milling Practices & Techniques 1 | Machining Guidebook | © 2016 Helical Solutions, LLC Helical Contents Milling Techniques & Strategies Terminology & Common Calculations 01 | Milling Techniques . 3 04 | End Mill Construction . 37 Types of Tool Entry . 4 Geometry Definitions . 38 Ramping . 6 End Mill Construction . 40 Thin Wall Milling . 8 End Mill Anatomy . 42 Deep Pocket Milling . 10 05 | Common Calculations . 51 Finishing . 11 Decimal Conversion Chart . 52 Ball Nose Strategy . 13 Common Milling Calculations . 53 Corner Engagement . 17 Speeds & Feeds . 54 Angle Engagement . 19 Conventional vs Climb Milling . 20 06 | Tool Holding . 55 Chip Thinning . 22 Tool Holding . 56 Preventing Tool Pull Out . 58 02 | High Efficiency Milling . 23 High Efficiency Milling . 24 HEM Tooling . 25 Troubleshooting 03 | Depth of Cut . 26 07 | Troubleshooting . 60 Depth of Cut . 27 Troubleshooting Chart . 61 Depth of Cut - Peripheral . 28 Tool Wear . 65 Depth of Cut - Slotting . 34 Tool Deflection . 69 Copyright © 2016 by Helical Solutions, LLC . All rights reserved . This book or any portion thereof may not be reproduced or used in any manner whatsoever without the express written permission of Helical Solutions . 2 | Machining Guidebook | © 2016 Helical Solutions, LLC Helical 01 Milling Techniques Types of Tool Entry . 4 Ball Nose Strategy . 13 Ramping . 6 Corner Engagement . 17 Thin Wall Milling . 8 Angle Engagement . 19 Deep Pocket Milling . 10 Conventional vs Climb Milling . 20 Finishing . 11 Chip Thinning . 22 3 | Machining Guidebook | © 2016 Helical Solutions, LLC Helical Types of Tool Entry The type of part entry that is programmed has a lot of influence on the tool’s success and is one of the most punishing Theoperations type of part for entry a cutter programmed .