Microwave Uv: a New Wave of Tertiary Disinfection
Total Page:16
File Type:pdf, Size:1020Kb
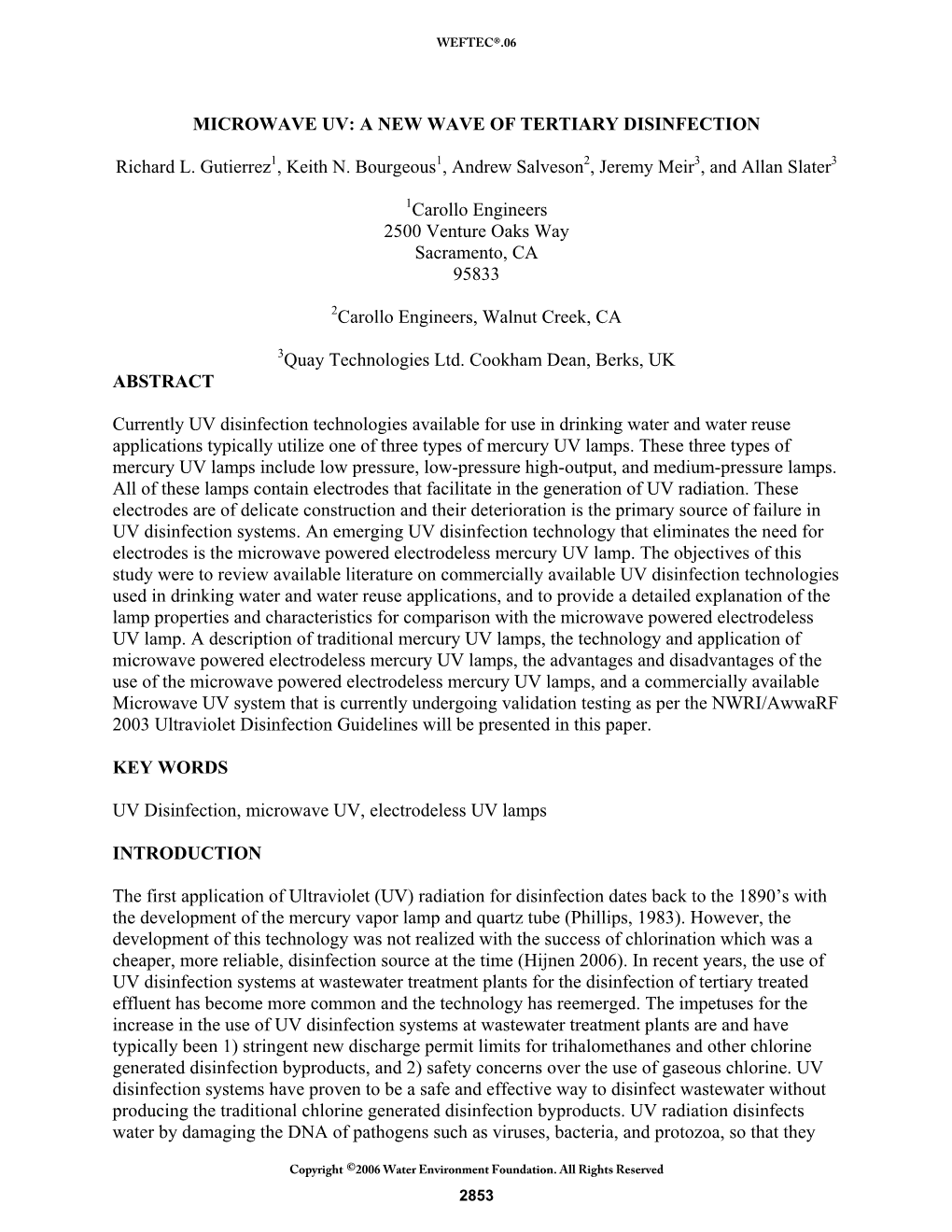
Load more
Recommended publications
-
Effective Application of Plasma Lighting Facility Based on Electrodeless Sulfur Lamp for Electrical Regeneration
EFFECTIVE APPLICATION OF PLASMA LIGHTING FACILITY BASED ON ELECTRODELESS SULFUR LAMP FOR ELECTRICAL REGENERATION Tetyana I. Frolova Kharkiv National University of Radio Electronics, 14 Nauky Ave., Kharkiv, 61166 UKRAINE Today, due to the intensive depletion of fossil resources on Earth, there is a need to use renewable energy sources. The most interesting is the photoelectric conversion of solar energy into electrical energy. Although the Sun is the largest source of energy on Earth and supplies 99.98% of the total energy of our planet, however, the intensity and spectral distribution of its radiation depends on geographical location, climatic, weather, and seasonal conditions, etc. Therefore, in the process of our life, artificial light sources are often used. Modern light sources must satisfy a number of parameters, combining high luminous efficiency and efficiency of generated radiation (a wide range of spectral distribution and color rendering), durability and environmental friendliness with low cost and variety of applications fields. The plasma lighting facility with a sulfur lamp is a powerful light source having a quasi-solar emission spectrum and providing light fluxes of 140 klm, and a color temperature of about 6400 K. Also the electrodeless lamp with microwave excitation has the ability to control the radiation power, which allows imitating the modes of sunrise and sunset. Electrodeless sulfur lamps can be used together with other electronic devices for creating the power energy-efficient lighting systems. It is proposed to use a lighting facility based on an electrodeless sulfur lamp with microwave excitation combine with solar batteries that are located indoors (for example, greenhouses). -
Apparatus for Producing Light by Exciting An
Europäisches Patentamt *EP000819317B1* (19) European Patent Office Office européen des brevets (11) EP 0 819 317 B1 (12) EUROPEAN PATENT SPECIFICATION (45) Date of publication and mention (51) Int Cl.7: H01J 65/04, F21S 2/00, of the grant of the patent: H05B 41/24 14.11.2001 Bulletin 2001/46 (86) International application number: (21) Application number: 96908743.6 PCT/US96/03262 (22) Date of filing: 11.03.1996 (87) International publication number: WO 96/28840 (19.09.1996 Gazette 1996/42) (54) APPARATUS FOR PRODUCING LIGHT BY EXCITING AN ELECTRODELESS LAMP WITH MICROWAVE ENERGY AND APPARATUS FOR PRODUCING HIGH INTENSITY VISIBLE LIGHT APPARAT ZUR ERZEUGUNG SICHTBAREN LICHTS MITTELS ERREGUNG EINER ELEKTRODENLOSEN LAMPE DURCH MIKROWELLENENERGIE UND APPARAT ZUR ERZEUGUNG SICHTBAREN LICHTS HOHER INTENSITÄT APPAREIL POUR PRODUIRE DE LA LUMIERE PAR EXCITATION D’UNE LAMPE SANS ELECTRODE AU MOYEN D’ ENERGIE HYPERFREQUENCE ET APPAREIL POUR PRODUIRE DE LA LUMIERE VISIBLE A HAUTE INTENSITE (84) Designated Contracting States: • TURNER, Brian AT BE CH DE DK ES FI FR GB GR IE IT LI LU MC Damascus, Maryland 20782 (US) NL PT SE (74) Representative: (30) Priority: 09.03.1995 US 402065 Schwepfinger, Karl-Heinz, Dipl.-Ing. Prinz & Partner GbR (43) Date of publication of application: Manzingerweg 7 21.01.1998 Bulletin 1998/04 81241 München (DE) (73) Proprietor: FUSION LIGHTING, INC. (56) References cited: Rockville, MD 20855 (US) EP-A- 0 450 131 DE-A- 4 307 946 JP-A- 56 126 250 US-A- 4 749 915 (72) Inventors: US-A- 4 887 192 US-A- 4 975 625 • SIMPSON, James, E. -
Innovative Solutions for Acoustic Resonance Characterization in Metal Halide Lamps
En vue de l'obtention du DOCTORAT DE L'UNIVERSITÉ DE TOULOUSE Délivré par : Institut National Polytechnique de Toulouse (INP Toulouse) Discipline ou spécialité : Génie Électrique Présentée et soutenue par : Mme FANG LEI le mercredi 24 janvier 2018 Titre : Innovative Solutions for Acoustic Resonance Characterization in Metal Halide Lamps Ecole doctorale : Génie Electrique, Electronique, Télécommunications (GEET) Unité de recherche : Laboratoire Plasma et Conversion d'Energie (LAPLACE) Directeur(s) de Thèse : M. PASCAL MAUSSION M. GEORGES ZISSIS Rapporteurs : M. BABAK NAHID-MOBARAKEH, UNIVERSITÉ LORRAINE M. MOUNSIF ECH CHERIF EL KETTANI, UNIVERSITE DU HAVRE Membre(s) du jury : Mme BETTY SEMAIL, UNIVERSITE LILLE 1, Président M. GEORGES ZISSIS, UNIVERSITE TOULOUSE 3, Membre M. PASCAL DUPUIS, UNIVERSITE TOULOUSE 3, Membre M. PASCAL MAUSSION, INP TOULOUSE, Membre Abstract Metal halide lamp is one kind of the most compact high-performance light sources. Because of their good color rendering index and high luminous efficacy, these lamps are often preferred in locations where color and efficacy are important, such as supermarkets, gymnasiums, ice rinks and sporting arenas. Unfortunately, acoustic resonance phenomenon occurs in metal halide lamps and causes light flicker, lamp arc bending and rotation, lamp extinction and in the worst case, arc tube explosion, when the lamps are operated in high-frequency bands. This thesis takes place in the context of developing electronic ballasts with robust acoustic resonance detection and avoidance mechanisms. To this end, several envelope detection methods such as the multiplier circuit, rectifier circuit, and lock-in amplifier, are proposed to characterize fluctuations of acoustic resonance. Furthermore, statistical criteria based on the standard deviation of these fluctuations are proposed to assess acoustic resonance occurrence and classify its severity. -
5 Lighting Technologies
5LIGHTINGTECHNOLOGIES Chapter5:Lightingtechnologies Topicscovered 5 Lightingtechnologies................................................................................................................ 93 5.1 Introduction.................................................................................................................... 93 5.2 Lightsources.................................................................................................................. 94 5.2.1 Overview........................................................................................................... 94 5.2.2 Lampsinuse ..................................................................................................... 96 5.2.3 Lamps................................................................................................................ 98 Incandescentlamp............................................................................................. 98 Tungstenhalogenlamp..................................................................................... 99 Fluorescentlamps ........................................................................................... 100 Compactfluorescentlamps(CFL).................................................................. 101 HighIntensityDischargelamps(HighPressure)............................................ 103 MercuryLamps............................................................................................... 103 Metalhalidelamps......................................................................................... -
Worldwide Light Sources and Fluorescent Light Market
Presentation on Worldwide Light sources and Fluorescent light Presented by: M. M. Ahtashom market Contents • Introduction • Classification of light source • Lighting efficiency comparison • Fluorescent lamp • History background • How light produced • Types of Fluorescent lamp • About Ballast • Operating Charecteristic • Applications • Advantages and Disadvantages • Commercial Prospect • CFL Recycling project • Reference Introduction A typical "light source" emits electromagnetic radiation in the visible spectrum. The list is oriented towards visible light: nearly everything emits photons through blackbody radiation. Classification of Light sources 1. Combustion 2. Natural 2.1 Celestial and atmospheric light 2.2 Terrestrial 3. Direct Chemical 4. Electric Powered 4.1 Electron simulated 4.2 Incandescent lamp 4.3 Electroluminescent (EL) lamp 4.4 Gas discharge lamps 4.4.1 High-intensity discharge lamp 5. Other 1. Combustion •Fire 2. Natural 2.1 Celestial and atmospheric light • Astronomical objects – Sun (Sunlight (solar radiation)) – Starlight (Stars forming groups such as Star clusters and galaxies and indirectly lighting nebulae) • Lightning (Plasma) – Sprite (lightning) – Ball lightning – Upper-atmospheric lightning – Dry lightning • Aurorae • Cherenkov radiation (from cosmic rays hitting atmosphere) • 2.2 Terrestrial • Bioluminescence – Luciferase - found in glowworms, fireflies, and certain bacteria – Aequorea victoria (a type of jellyfish) – Antarctic krill – Parchment worm (Chaetopterus), which exhibits blue bioluminescence despite -
Electrodeless High Intensity Discharge Lamp Having a Boron Sulfide Fill
Patentamt Europaisches |||| ||| 1 1|| ||| ||| ||| || || || ||| ||| || || || (19) J European Patent Office Office europeen des brevets (11) EP 0 788 1 40 A2 (12) EUROPEAN PATENT APPLICATION (43) Date of publication:ation: (51) |nt. CI.6: H01 J 61/16, H01 J 65/04 06.08.1997 Bulletin 1997/32 (21) Application number: 97100888.3 (22) Date of filing : 21 .01 .1 997 (84) Designated Contracting States: • Butler, Scott J. BE DE FR GB IT NL North Oxford, MA 01 537 (US) • Bochinski, Jason R. (30) Priority: 01.02.1996 US 595475 Springfield, OR 97477 (US) (71) Applicant: OSRAM SYLVANIA INC. (74) Representative: Pokorny, Gerd Danvers, MA 01 923 (US) OSRAM GmbH, Postfach 2216 34 (72) Inventors: 80506 Munchen (DE) • Lapatovich, Walter P. Marlborough, MA 01752 (US) (54) Electrodeless high intensity discharge lamp having a boron sulfide fill (57) An electrodeless high intensity discharge lamp including a sealed light-transmissive lamp envelope, a volatilizable chemical fill and inert an gas or nitrogen 12 within the envelope. The primary active component of the fill is boron sulfide. The inert gas or nitrogen within the envelope assists in starting the lamp, and is at sub- f KJ atmospheric pressure. The lamp envelope is coupled to | applicator | — rj a high frequency source to produce a light emit- \\ power ^ ting plasma discharge within the envelope. V\ \ FIG. I CM < O CO CO o Q_ LU Printed by Rank Xerox (UK) Business Services 2.14.11/3.4 1 EP 0 788 140 A2 2 Description amount of a metal halide and emitting light over a broad spectral range. -
Fluorescent Induction
Green Light Induction Lighting “Saving the Earth and Creating a Better Bottom Line.” We Can Reduce Your Electric Light Bill by 50% Minimum! When Replacing HID lighting www.GreenLightInduction.com 620 Newport Center Drive, Suite 1100 Contact:949•429•3435 1 Email: [email protected] Newport Beach, CA 92660 HOW IT WORKS http://www.indolamp.com/technologyhowitworks.html •Electromagnetic transformers, constructed from rings of metal coils and powered by a high frequency electronic ballast, create an electromagnetic field around a glass tube which contains the gas. The discharge path, induced by the coils, forms a closed loop allowing acceleration of free electrons, which collide with mercury atoms and excite the electrons. As the excited electrons from these atoms fall back from this higher energy level to a lower stable state, they emit ultraviolet radiation. This UV energy is converted to visible light as it passes through a phosphor coating on the surface of the tube. The unusual shape of an induction lamp maximizes the efficiency of the electromagnetic fields that are generated. Contact:949•429•3435 2 Email: [email protected] WHAT IS INDUCTION LIGHTING Uses wireless technology to Induction lamps do not use produce light - using simple electrodes. magnetism Instead of a ballast, the Principle of Induction is the system uses a high-frequency transmission of energy by generator with a power way of a magnetic field. coupler . Fluorescent lamps use The generator produces a electrodes to strike the arc and radio frequency magnetic initiate the flow of current field to excite gas fill. through the lamp, which excites the gas fill. -
Pros and Cons Controversy on Molecular Imaging and Dynamic
Open Access Archives of Biotechnology and Biomedicine Research Article Pros and Cons Controversy on Molecular Imaging and Dynamics of Double- ISSN Standard DNA/RNA of Human Preserving 2639-6777 Stem Cells-Binding Nano Molecules with Androgens/Anabolic Steroids (AAS) or Testosterone Derivatives through Tracking of Helium-4 Nucleus (Alpha Particle) Using Synchrotron Radiation Alireza Heidari* Faculty of Chemistry, California South University, 14731 Comet St. Irvine, CA 92604, USA *Address for Correspondence: Dr. Alireza Abstract Heidari, Faculty of Chemistry, California South University, 14731 Comet St. Irvine, CA 92604, In the current study, we have investigated pros and cons controversy on molecular imaging and dynamics USA, Email: of double-standard DNA/RNA of human preserving stem cells-binding Nano molecules with Androgens/ [email protected]; Anabolic Steroids (AAS) or Testosterone derivatives through tracking of Helium-4 nucleus (Alpha particle) using [email protected] synchrotron radiation. In this regard, the enzymatic oxidation of double-standard DNA/RNA of human preserving Submitted: 31 October 2017 stem cells-binding Nano molecules by haem peroxidases (or heme peroxidases) such as Horseradish Peroxidase Approved: 13 November 2017 (HPR), Chloroperoxidase (CPO), Lactoperoxidase (LPO) and Lignin Peroxidase (LiP) is an important process from Published: 15 November 2017 both the synthetic and mechanistic point of view. Copyright: 2017 Heidari A. This is an open access article distributed under the Creative -
Chapter 2 Incandescent Light Bulb
Lamp Contents 1 Lamp (electrical component) 1 1.1 Types ................................................. 1 1.2 Uses other than illumination ...................................... 2 1.3 Lamp circuit symbols ......................................... 2 1.4 See also ................................................ 2 1.5 References ............................................... 2 2 Incandescent light bulb 3 2.1 History ................................................. 3 2.1.1 Early pre-commercial research ................................ 4 2.1.2 Commercialization ...................................... 5 2.2 Tungsten bulbs ............................................. 6 2.3 Efficacy, efficiency, and environmental impact ............................ 8 2.3.1 Cost of lighting ........................................ 9 2.3.2 Measures to ban use ...................................... 9 2.3.3 Efforts to improve efficiency ................................. 9 2.4 Construction .............................................. 10 2.4.1 Gas fill ............................................ 10 2.5 Manufacturing ............................................. 11 2.6 Filament ................................................ 12 2.6.1 Coiled coil filament ...................................... 12 2.6.2 Reducing filament evaporation ................................ 12 2.6.3 Bulb blackening ........................................ 13 2.6.4 Halogen lamps ........................................ 13 2.6.5 Incandescent arc lamps .................................... 14 2.7 Electrical -
Photo-Catalytic Degradation of Rhodamine B Using Microwave Powered Electrodeless Discharge Lamp
Korean J. Chem. Eng., 27(2), 672-676 (2010) DOI: 10.1007/s11814-010-0060-7 RAPID COMMUNICATION Photo-catalytic degradation of rhodamine B using microwave powered electrodeless discharge lamp Jeong-Seok Chae*, Dong-Suk Jung*, Yeong-Seon Bae*, Sung Hoon Park*, Do-Jin Lee**, Sun-Jae Kim***, Byung Hoon Kim****, and Sang-Chul Jung*,† *Department of Environmental Engineering, **Department of Agricultural Education, Sunchon National University, Sunchon 540-742, Korea ***Department of Nano Science and Technology, Sejong University, Seoul 143-747, Korea ****Department of Dental Materials, School of Dentistry, MRC Center, Chosun University, Gwangju 501-759, Korea (Received 19 June 2009 • accepted 28 July 2009) Abstract−A microwave discharge electrodeless lamp (MDEL) was used as the light source for microwave assisted TiO2 photo-catalysis to degrade rhodamine B. A MDEL filled with low pressure mercury gas has been developed for the photo-catalytic treatment of water pollutants over TiO2 balls. TiO2 balls produced by the chemical vapor deposition method were used. The degradation reaction rate was shown to be higher with higher microwave intensity and with a larger amount of O2 gas addition. The effect of addition of H2O2 was not significant when photo-catalysis was used without additional microwave irradiation or when microwave was irradiated without the use of photo-catalysts. When H2O2 was added under simultaneous use of photo-catalysis and microwave irradiation, however, considerably higher degradation reaction rates were observed. This result suggests that there is a synergy effect when the constituent tech- niques are applied together. Key words: Photo-catalyst, Microwave, UV, Dye, Chemical Vapor Deposition INTRODUCTION ever, in application of TiO2 photo-catalyst in the treatment of non- biodegradable materials. -
New Induction and Plasma Lighting Technologies Proven Superior to LED for Streetlighting and High Lumen Applications
New Induction and Plasma Lighting Technologies proven Superior to LED for Streetlighting and High Lumen Applications Both Induction lamp and LEP (Light Emitting Plasma) technologies offer significant advantages over LED fixtures for streetlighting and high lumen applications with superior cost savings, longevity and performance Cities and muncipalities across the U.S. are seeking to replace inefficient lighting for streetlighting and public buildings to save energy and reduce operating costs. Similarly, commercial businesses, factories, large retail stores, warehouses, airports, convention centers, and parking facilities are looking to upgrade or replace their lighting systems for energy and maintenance savings. Typically 40% or more of the energy usage for municipalities, businesses and institutions is consumed by lighting. While the popularity of LED lighting increases for many applications, LED is not the best solution when high light levels are needed. Decline of the Realm of HID Lighting For decades, applications requiring high light levels have been the realm of high intensity discharge (HID) lighting fixtures. Street and highway lighting, parking lots, bridges & tunnels, stadiums, transportation facilities and other large outdoor areas are typically illuminated with HID fixtures. Warehouses, factories, parking garages, shopping malls, and high ceiling indoor applications also typically use HID lighting. Generally, high pressure sodium (HPS) lamps are utilized for streetlighting and industrial applications due to their efficiency and 24,000 hour life. But HPS exhibits poor color with a yellowish cast. Metal halide lamps, with whiter color rendering are used for most HID applications, but possess shorter lamp life, usually around 10,000 hours. All HID lamps employ an electrode to ignite gasses contained within the bulb envelope, and require a ballast for start-up and voltage regulation. -
United States Patent (19) 11 Patent Number: 5,363,015 Dakin Et Al
USOO5363015A United States Patent (19) 11 Patent Number: 5,363,015 Dakin et al. (45. Date of Patent: Nov. 8, 1994 (54) LOW MERCURY ARC DISCHARGE LAMP 3,906,274 9/1975 Silver et al.......................... 313/228 CONTAINING PRASEODYMUM 4,422,011 12/1983 Bruninx-Poesen et al. ........ 313/642 4,801,846 l/1989 Kramer et al. .............. ... 313/641 75 Inventors: James T. Dakin, Shaker Heights; 4,810,938 3/1989 Johnson et al. ... 315/248 Tommie Berry, Jr., East Cleveland; 4,812,702 3/1989 Johnson .......... ... 313/153 Mark E. Duffy, Shaker Heights; 4,959,584 9/1990 Anderson ... 33/160 Timothy D. Russell, Cleveland 4,972, 120 11/1990 Witting ... 313/638 Heights, all of Ohio 5,039,903 8/1991 Farrall ................................. 313/160 73 Assignee: General Electric Company, Primary Examiner-Donald J. Yusko Schenectady, N.Y. Assistant Examiner-Ashok Patel Attorney, Agent, or Firm-Stanley C. Corwin; Edward (21) Appl. No.: 927,041 M. Corcoran 22 Filed: Aug. 10, 1992 57 ABSTRACT 52511 U.S.C.Int. Cl. ............................................................ H01J 17/20;313/638; H01J 313/641. 61/12 A high- - intensity- electrodeless metal halide arc dis 313/642; 313/571; 313/161; 315/248; 315/344 charge lamp wherein RF energy is coupled to the arc 58) Field of Search ............... 313/638, 642,643, 640, discharge, contains a halide of praseodymium alone or 313/570, 161,571, 641; 315/248, 344 in combination with other metals such as one or more rare earth metals, Na and Cs and is essentially mercury 56) References Cited free (i.e., < 1 mg per cc of arc chamber volume).