6A/.444/ Patented Apr
Total Page:16
File Type:pdf, Size:1020Kb
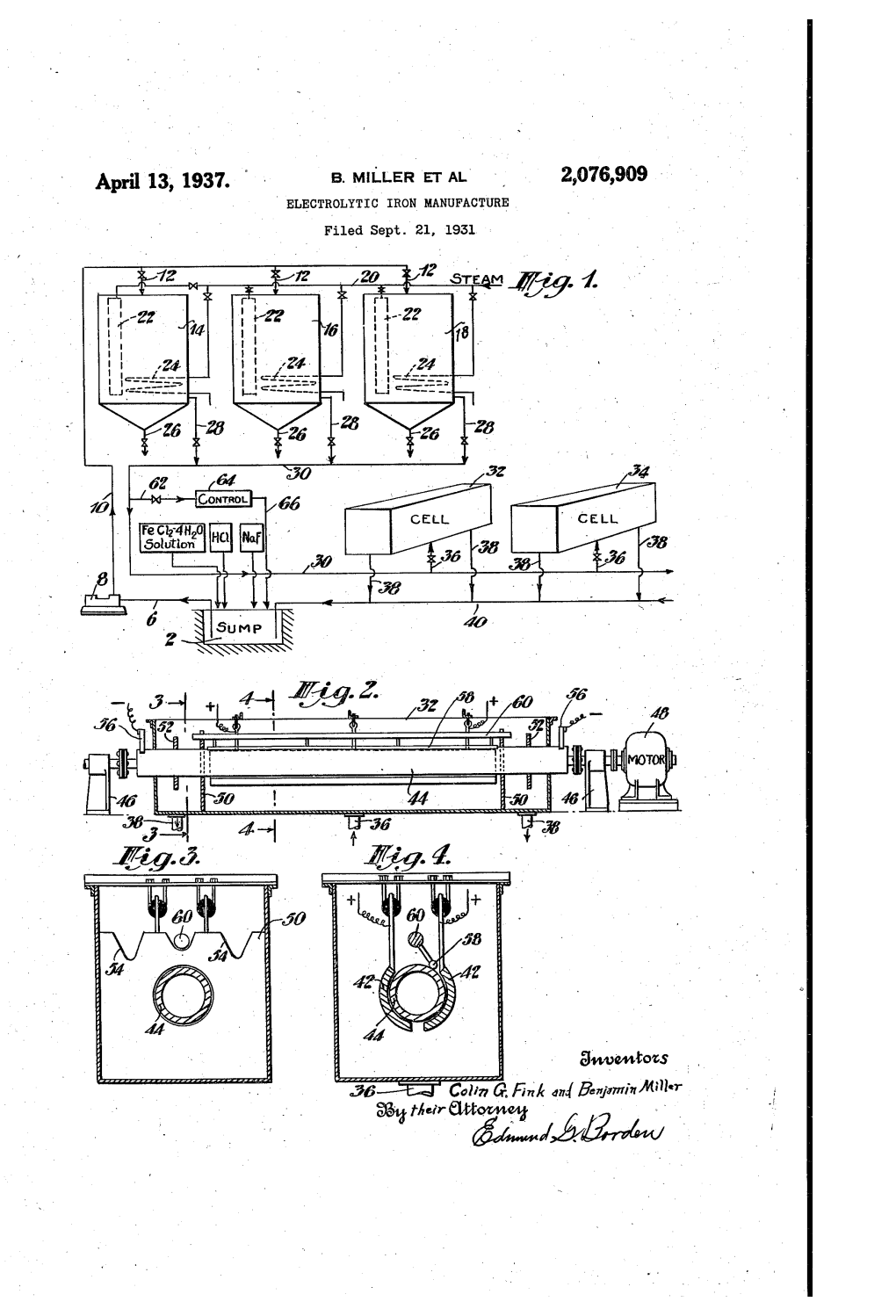
Load more
Recommended publications
-
Fortificants
GFF5.qxd 14/11/06 16:44 Page 93 PA RT I I I Fortificants: physical characteristics, selection and use with specific food vehicles GFF5.qxd 14/11/06 16:44 Page 94 GFF5.qxd 14/11/06 16:44 Page 95 Introduction By providing a critical review of the fortificants that are currently available for fortification purposes, Part III of these guidelines is intended to assist pro- gramme managers in their choice of firstly, a suitable food vehicle and secondly, a compatible fortificant. Having established – through the application of appro- priate criteria – that the nature of the public health risk posed by a micronutri- ent deficiency justifies intervention in the form of food fortification, the selection of a suitable combination of food vehicle and fortificant(s), or more specifically, the chemical form of the micronutrient(s) that will added to the chosen food vehicle, is fundamental to any food fortification programme. Subsequent chap- ters (Part IV) cover other important aspects of food fortification programme planning, including how to calculate how much fortificant to add to the chosen food vehicle in order to achieve a predetermined public health benefit (Chapter 7), monitoring and impact evaluation (Chapters 8 and 9), marketing (Chapter 10) and regulatory issues (Chapter 11). In practice, the selection of a food vehicle–fortificant combination is governed by range of factors, both technological and regulatory. Foods such as cereals, oils, dairy products, beverages and various condiments such as salt, sauces (e.g. soy sauce) and sugar are particularly well suited to mandatory mass fortifica- tion. These foods share some or all of the following characteristics: • They are consumed by a large proportion of the population, including (or especially) the population groups at greatest risk of deficiency. -
Standard Reference Materials Price and Availability List IMPORTANT NOTICE to PURCHASERS and USERS of NBS STANDARD REFERENCE MATERIALS
o A UNITED STATES NBS SPECIAL PUBLICATION DEPARTMENTucrnn 1 ivitii 1 urOF COMMERCE PUBLICATION 260 [ A SUPPLEMENT JANUARY, 1972 Standard Reference Materials Price and Availability List IMPORTANT NOTICE TO PURCHASERS AND USERS OF NBS STANDARD REFERENCE MATERIALS The Office of Standard Reference Materials no longer issues the Quarterly Insert Sheets to update the current issue of the SRM Catalog. Instead a Standard Reference Material Availability and Price List is issued semiannually. The format has been changed to improve readability and the List is organized as follows: Section I - A list of all classes of materials currently available arranged by Standard Reference Material (SRM), Research Material (RM), and General Material (GM) numbers, together with type, unit of issue, and current price. Section Ila — A list of all classes of materials that have been issued since the Catalog (July 1970) was published, arranged by SRM, RM, and GM numbers together with catalog category. Section lib — A short description, arranged by catalog category, of all SRM's issued since the Catalog (July 1970) was published and therefore not contained therein. For ease of reproduction, tables have been condensed and are, in general, not in the same format used in the catalog. (Please note that the values shown are nominal values. The actual values certified are given on the Certificate which accompanies the material.) The unit of issue and price are given after the description of each SRM. Section llla — A list, arranged by SRM numbers, of recently issued certificates (final or revised versions). Section Illb — A list, arranged by SRM, RM, and GM numbers, of all items that have gone out of stock since the effective date of the current catalog. -
Electrolytic Iron
ELECTROLYTIC IRON ; DEPOSITED BY T H E COMMI T T E E O N (Brafcmate StuMes. 1 x ACC. No DATE ELECTROLYTIC IRON.. A STUDY OF THE PRODUCTION OF IRON BY ELECTROLYSIS, WITH SPECIAL REFERENCE TO ITS RECOVERY FROM SULPHIDE ORES.. THESIS Submitted by WILLIAM RAYMOND MoCLELLAND As Part of the Requirements for the Degree of Master of Soienoe. MAY L925. MoOILL UNIVERSITY, MONTREAL, CANADA. ELECTROLYTIC IRON. A Study of the Production of Iron by Electrolysis, with Special: Reference to its Recovery from Sulphide Ores.- PART I. Introduction Historical Outline and Descriptive* Physical Properties of Electrolytic Iron. PART II Theoretioal Considerations. A. Leaohing. B. Electrolysis. PART III. Experimental Research. A. Ore Body and Treatment of Ore. B. Leaching. C. Electro-deposition. General Summary and Conclusion. PART IV. Appendix. References. Sample Calculations. Bibliography. (1) PART I. INTRODUCTION. Iron, is the oommonest, most widely used, and at the same time the most vitally important of all the base metals. In the growth and developementr of modern civilization it assumes a dominant position.. Iron was not unknown to the anoients,nor were they unaware of its uses. As early as 1500 B.C.. the inhabitants of India; fashioned swords and spear heads. They even recognized, its qualities: for purpose* of construotion. Wrought1: iron beams measuring twenty feet in length have been found in the temple of Kanaruk dating from 1250 B.C. The metallurgy of iron at this period was extremely primative and continued so for many hundreds of year.s. It v;as notr until the sixteenth century that the introduction of-the air blast into the furnaoff made the progress of iron manufacture comparatively rapid.From thi'a period on, tha production increase-d. -
The Preparation of High-Purity Iron (99.987%) Employing a Process of Direct Reduction–Melting Separation–Slag Refining
materials Article The Preparation of High-Purity Iron (99.987%) Employing a Process of Direct Reduction–Melting Separation–Slag Refining Bin Li 1,2, Guanyong Sun 1,2, Shaoying Li 1,2, Hanjie Guo 1,2,* and Jing Guo 1,2 1 School of Metallurgical and Ecological Engineering, University of Science and Technology Beijing, Beijing 100083, China; [email protected] (B.L.); [email protected] (G.S.); [email protected] (S.L.); [email protected] (J.G.) 2 Beijing Key Laboratory of Special Melting and Preparation of High-End Metal Materials, Beijing 100083, China * Correspondence: [email protected]; Tel.: +86-138-0136-9943 Received: 9 March 2020; Accepted: 9 April 2020; Published: 14 April 2020 Abstract: In this study, high-purity iron with purity of 99.987 wt.% was prepared employing a process of direct reduction–melting separation–slag refining. The iron ore after pelletizing and roasting was reduced by hydrogen to obtain direct reduced iron (DRI). Carbon and sulfur were removed in this step and other impurities such as silicon, manganese, titanium and aluminum were excluded from metallic iron. Dephosphorization was implemented simultaneously during the melting separation step by making use of the ferrous oxide (FeO) contained in DRI. The problem of deoxidization for pure iron was solved, and the oxygen content of pure iron was reduced to 10 ppm by refining with a high basicity slag. Compared with electrolytic iron, the pure iron prepared by this method has tremendous advantages in cost and scale and has more outstanding quality than technically pure iron, making it possible to produce high-purity iron in a short-flow, large-scale, low-cost and environmentally friendly way. -
Preparation of Pure Iron and Iron-Carbon Alloys
. PREPARATION OF PURE IRON AND IRON-CARBON ALLOYS By J. R. Cain, E. Schramm, and H. E. Cleaves CONTENTS Page I. Introduction 2 II. Making the electrolytic iron 4 III. Melting the electrolytic iron 7 1. Ftimaces 8 (a) Electric furnaces 8 (6) Gas furnaces 11 2. Crucibles 13 IV. Procedure in making alloys 16 V. Discussion of the sources of contamination 19 1. Silicon 19 2. Sulphur 20 3 Manganese and phosphorus 20 4. Copper 21 5 Nickel and cobalt 21 6. Magnesium 21 7. Oxygen 21 VI. Spectroscopic examination 22 VII. Methods of chemical analysis 22 1. Carbon 23 2. Sulphtir 23 3. Silicon 23 4. Phosphorus 24 5. Manganese 24 6. Copper 24 7. Magnesium 24 8. Nickel and cobalt 25 VIII. Summary '. 25 Bibliography 26 I 2 Bulletin of the Bureau of Standards [Voi 13 I. INTRODUCTION The fundamental importance of the iron-carbon thermal equi- librium diagram in the scientific metallurgy of iron and steel and its utility to practical workers have long been realized, and accord- ingly this subject has received attention from many points of view and from many investigators during the past two decades. In view of this fact, it might seem superfluous to add to the existing literature except for the following considerations : Earlier workers have for the most part confined their attention to special portions of the diagram or to disputed questions of theory. Their thermal studies have not been carried out with the degree of accuracy now attainable. They have practically without ex- ception employed commercial materials of varying degrees of purity. -
PDF File Generated From
OCCASION This publication has been made available to the public on the occasion of the 50th anniversary of the United Nations Industrial Development Organisation. DISCLAIMER This document has been produced without formal United Nations editing. The designations employed and the presentation of the material in this document do not imply the expression of any opinion whatsoever on the part of the Secretariat of the United Nations Industrial Development Organization (UNIDO) concerning the legal status of any country, territory, city or area or of its authorities, or concerning the delimitation of its frontiers or boundaries, or its economic system or degree of development. Designations such as “developed”, “industrialized” and “developing” are intended for statistical convenience and do not necessarily express a judgment about the stage reached by a particular country or area in the development process. Mention of firm names or commercial products does not constitute an endorsement by UNIDO. FAIR USE POLICY Any part of this publication may be quoted and referenced for educational and research purposes without additional permission from UNIDO. However, those who make use of quoting and referencing this publication are requested to follow the Fair Use Policy of giving due credit to UNIDO. CONTACT Please contact [email protected] for further information concerning UNIDO publications. For more information about UNIDO, please visit us at www.unido.org UNITED NATIONS INDUSTRIAL DEVELOPMENT ORGANIZATION Vienna International Centre, P.O. Box 300, 1400 Vienna, Austria Tel: (+43-1) 26026-0 · www.unido.org · [email protected] UNITED NATIONS INDUSTRIAL DEVELOPMENT C'riG,.\NIZATION Advances in Materials Techno!ogy: MONITOR Issue Number 4 Hay l9b) LJear Reader, This is the fourth issue of UNIDu's state-of-the-art series in the field ot materials entitled Advances in Hat~rials Iechnology: Monitor. -
Magnetic and Other Properties of Electrolytic Iron Melted in Vacuo, by Trygve D
H I LLIN S UNIVERSITY OF ILLINOIS AT URBANA-CHAMPAIGN PRODUCTION NOTE University of Illinois at Urbana-Champaign Library Large-scale Digitization Project, 2007. B<, <~: SIk 1g xS 1,·' ~FS I K; -S- 'A· -i 3· - C:55 I UNIVERSITY OF ILLINOIS ENGINEERING EXPERIMENT STATION BULLETIN NO. 72 MARCH, 1914 MAGNETIC AND OTHER PROPERTIES OF ELECTROLYTIC IRON MELTED IN VACUO BY TRYGVE D. YENSEN, ASSISTANT, ELECTRICAL ENGINEERING DEPART- MENT, ENGINEERING EXPERIMENT STATION CONTENTS PAGE I. INTRODUCTION ....................................... 3 1. Scope of Bulletin ............................ 3 2. Historical Review .................. ......... 4 3. Early Experiences ........................... 11 4. Acknowledgments ............................ 12 II. MATERIAL AND APPARATUS ............................. 13 5. Electrolytic Iron ............................. 13 6. Crucibles ................................... 13 7. Vacuum Furnace ............................ 13 8. Reheating Furnace ........................... 13 9. Pyrom eter .................................. 14 10. Permeameter ................................ 14 11. Conductivity Bridge ......................... 17 III. DETAILS OF TIE EXPERIMENTS .......................... 17 12. Cleaning the Iron................... ......... 17 13. M elting the Iron ............................. 17 14. Forging the Ingots into Rods................... 18 15. Preparing the Test-pieces ..................... 18 16. Annealing and Quenching..................... 19 17. M agnetic Tests .............................. 20 18. -
General Disclaimer One Or More of the Following Statements May Affect
General Disclaimer One or more of the Following Statements may affect this Document This document has been reproduced from the best copy furnished by the organizational source. It is being released in the interest of making available as much information as possible. This document may contain data, which exceeds the sheet parameters. It was furnished in this condition by the organizational source and is the best copy available. This document may contain tone-on-tone or color graphs, charts and/or pictures, which have been reproduced in black and white. This document is paginated as submitted by the original source. Portions of this document are not fully legible due to the historical nature of some of the material. However, it is the best reproduction available from the original submission. Produced by the NASA Center for Aerospace Information (CASI) first Quarterly Technical Nar y eve Report r^gust 25 Through November 30, 1980 CAST Fe-EASE CYLINDER/FEE ENEHATOR HOUSING ALLOY PO-17602 lr^ December 10, 1980 (NASA -CR-1(,9474) CA I FF.- IAEE CYLI '^ ;,1^ b /hcGEi^cFA;(;' ti.^^J ^ll(. ALLCY -Ic4, kjurti rIy I. - "L''Lc^l n ^cra*iv. [eECCt, 2 Aug;. - 3C ^ ;.CV. 1 )"?G (nih: ^^,iich ''a_tiu^ Co. ) 3) P If A,.3^,;I A11 U'LCiaa CSC[ I IF G3 u J o 2 Preparamv: F. LArson . Kindlimann Prepared for SA search Center CI !H 414135 Contract No. DEN 3-234 A!7 AIRESEARCN CASTING COMPANY TORQ.ANCE Cn' 1FnoIVIA. First Quarterly Technical Narrative Report August 25 Through November 30, 1980 CAST Fe-BASE CYLINDER / R EG E N E RATO R HOUSING ALLOY 80-17602 December 10, 1980 Prepared by: fl F. -
Letter Circular 192: Corrosion Resistance of Iron and Steel
• - - Letter HWG : MGL : LTQ DEPARTMENT OF COMMERCE " " ' \ BDREAU- -Op’S OTfDARDS Circular : •..- ~ ™ • 1&2 ’ ' • ' v • 7 • April 1336 ' • v ; yc-^s. ' COFRQSIQN- RESISTANCE ~CF "IRON AND STEEL . ; : • • •. V ; -a; . The /Lett-er- C.iTC.uliars are designed to answer .specific in- ; quiries and at the same.; t irae- to-'obylate .the necessity "for pre^ paratlon.-of a large number. of letters- on. .the same, subject There Is" no guarantee- it hat .the. 'Information .given In- the Letter r Circulars- ls , correct except as of .the date of issue,. - ilat-erlal of a permanent value appears in- the printed publications of the-, ^ -j ;.- • Bureah. r f 1 r:- 5 r Iv-rmc v. -. Letter. Circulars are not' available sin' the Government Print- ing Office, and the supply at the Bureau of -Standards Is- -limited Many inquiries' are- received- by- this. Bureau -in (regard to the resistance to corrosion of- ."cas.t iron, and of . steel, wrought iron, commercially pure-/ open-hearth iron. 'and copper-bearing -. iron or* steel in sheet - -pipe;,; wir.e-;..;andrsther forms both bare , : . and zinc : coat ed dr otherwise, trust' propled-t, : : Some inquirers request opinions on the suitability of specif - in makes or brands of these -materials , for specific uses. "It -is not the policy .of the -.Bur eau to recommend or. -de- cry specific mates or brands .of any article; Its .tests and. investi gallons deal with ..types of material, not- with, the merits or demerits of a .particular .maker* s product. ;--Thls . Letter - Circular is prepared to put those making such inquiries on types of material in touch with -published data -and opinions on the 'subject. -
Electrolytic Iron Production from Alkaline Suspensions of Solid Oxides
Electrolytic iron production from alkaline suspensions of solid oxides: compared cases of hematite, iron ore and iron-rich Bayer process residues Abdoulaye Maihatchi, Marie-Noëlle Pons, Quentin Ricoux, Frederic Goettmann, François Lapicque To cite this version: Abdoulaye Maihatchi, Marie-Noëlle Pons, Quentin Ricoux, Frederic Goettmann, François Lapicque. Electrolytic iron production from alkaline suspensions of solid oxides: compared cases of hematite, iron ore and iron-rich Bayer process residues. Journal of Electrochemical Science and Engineering, IAPC Publishing, 2020, 10 (2), pp.95. 10.5599/jese.751. hal-02519552 HAL Id: hal-02519552 https://hal.univ-lorraine.fr/hal-02519552 Submitted on 12 Jun 2020 HAL is a multi-disciplinary open access L’archive ouverte pluridisciplinaire HAL, est archive for the deposit and dissemination of sci- destinée au dépôt et à la diffusion de documents entific research documents, whether they are pub- scientifiques de niveau recherche, publiés ou non, lished or not. The documents may come from émanant des établissements d’enseignement et de teaching and research institutions in France or recherche français ou étrangers, des laboratoires abroad, or from public or private research centers. publics ou privés. Electrolytic iron production from alkaline suspensions of solid oxides: compared cases of hematite and iron-rich Bayer process residues. Ab. Maihatchi 1,2, M.N. Pons 1, Q. Ricoux 2, F. Goettmann 2 and F. Lapicque 1* 1 Reaction and Chemical Engineering Laboratory, CNRS-University of Lorraine, 1 rue Grandville, 54000 Nancy, France 2 Extracthive, Centre de Recherche CEA, Bat. 51, 30591 Marcoule, France Abstract: Iron can be produced by the direct electrochemical reduction of hematite particles suspended in hot, concentrated NaOH solutions. -
Electrolytic Deposition of Iron Irving M
Montana Tech Library Digital Commons @ Montana Tech Bachelors Theses and Reports, 1928 - 1970 Student Scholarship 5-1-1943 Electrolytic Deposition of Iron Irving M. Kenoffel Follow this and additional works at: http://digitalcommons.mtech.edu/bach_theses Part of the Ceramic Materials Commons, Environmental Engineering Commons, Geology Commons, Geophysics and Seismology Commons, Metallurgy Commons, Other Engineering Commons, and the Other Materials Science and Engineering Commons Recommended Citation Kenoffel, Irving M., "Electrolytic Deposition of Iron" (1943). Bachelors Theses and Reports, 1928 - 1970. 192. http://digitalcommons.mtech.edu/bach_theses/192 This Bachelors Thesis is brought to you for free and open access by the Student Scholarship at Digital Commons @ Montana Tech. It has been accepted for inclusion in Bachelors Theses and Reports, 1928 - 1970 by an authorized administrator of Digital Commons @ Montana Tech. For more information, please contact [email protected]. Electrolytic Deposition of Iron by Irving M. Kenoffel A Thesis Submitted tc the Department of Metallurgy In Partial Fulfillment of the Requirements for the Degree of Bachelor of ~ci ence in Letallurg ical Eng meering Montana School of Mines Butte, Montana. May 1, 1943 Electrolytic Deposition of Iron by Irving M. Kenoffel A Thesis Submitted to the Department of Metallurgy In Partial Fulfillment of the Requirements for the Degree of Bachelor of SCience in Metallurgical Engineering MOntana School of Mines Butte, Montana May 1, 1943 10,.;15 - Contents Page 1-- Abstract .Introduction Page 4-- Pur-th er Uses of Electrolytic Iron Page 7-- Researcn. Qn the Electrodeposition of Iron Page 17-- Tests. perfoJmled in Laboratory Page 22-- Test for Carb on Oonclusions Page 23-- Acknowledgment Page 24-- Bibliography ,> Abstract In this thesis the purpose was to obtain a good iron deposit from a relatively simple bath. -
Preparation and Properties of Pure Iron Alloys. I. Effects of Carbon And
PREPARATION AND PROPERTIES OF PURE IRON ALLOYS: I. EFFECTS OF CARBON AND MANGANESE ON THE MECHANICAL PROPERTIES OF PURE IRON. By Robert P. Neville and John R. Cain. ABSTRACT. This paper describes the preparation and mechanical properties of an extensive series of very pure alloys of electrolytic iron, carbon, and manganese whose composi- tions were so chosen as to bring out the specific effects on pure iron of additions of manganese, additions of carbon, and additions of carbon and manganese together in varying relative proportions. The maximum content each of carbon and manganese in each series is about 1.6 per cent; the minimum, o per cent, or pine iron. Three-pound ingots of the alloys were made by melting electrolytic iron under vac- utim in an electric furnace in a crucible of ptwe magnesia to which the carbon and man- ganese were added after fusion of the iron. From these ingots tensile specimens were made and tested in the annealed state. The data were tabulated in the order of in- creasing carbon for comparison and interpretation of results. The effects of carbon are shown by grouping the specimens according to manganese contents and plotting exudes for each group, with values from tests for ordinates and carbon contents for ab- scissas. The effects of manganese are shown in a similar manner by regrouping the specimens according to carbon contents. CONTENTS. Page. I. Introduction 412 II. Investigations of the effects of carbon and manganese on the mechanical properties of steel 413 III. Preparation of the alloys 418 1. Fusion in vacuo 418 2.