Feasibility and Design of Miniaturized Control Moment Gyroscope for a 3-Axis Stabilized Micro Satellite
Total Page:16
File Type:pdf, Size:1020Kb
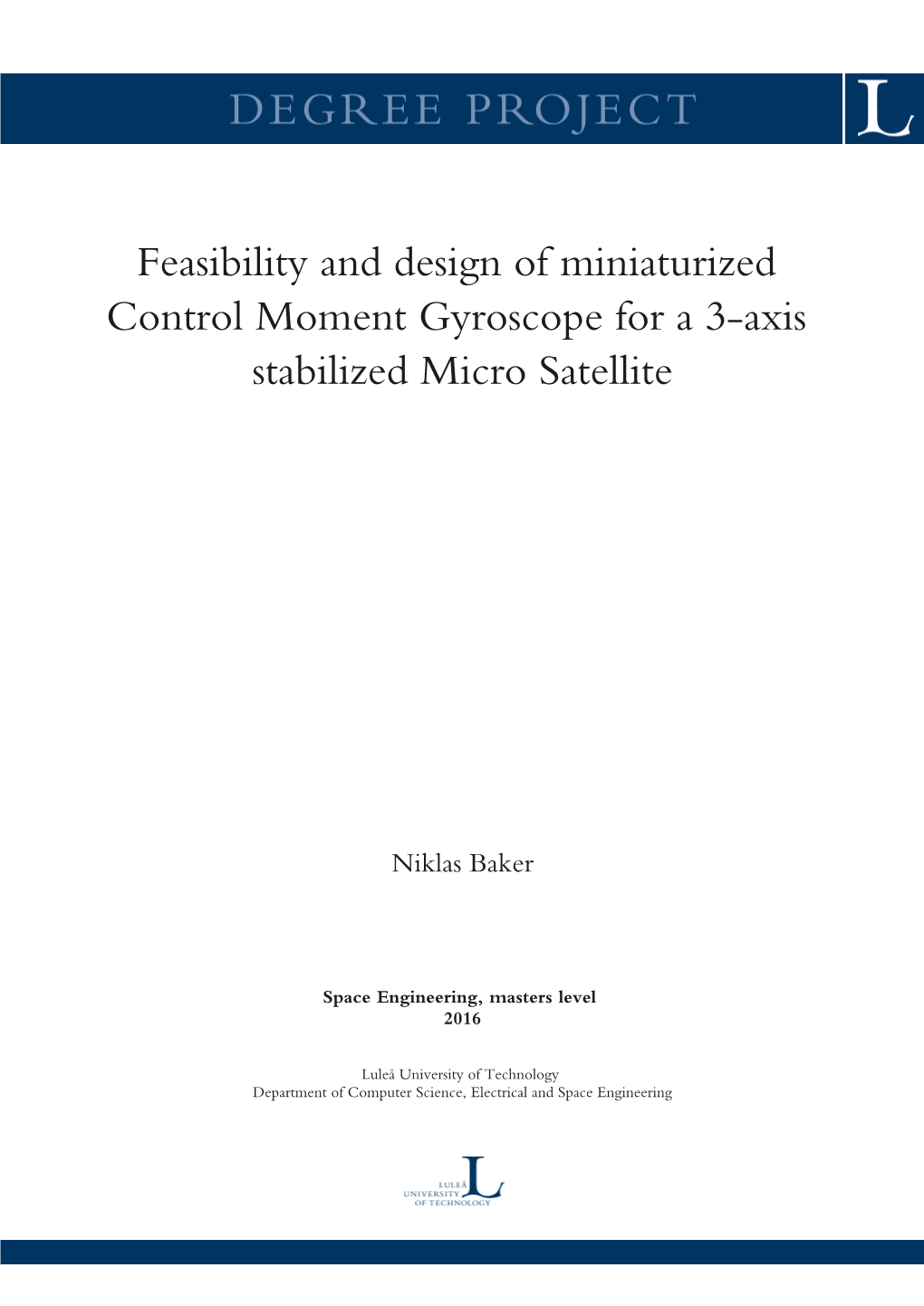
Load more
Recommended publications
-
I a COMPARISON STUDY on CONTROL MOMENT GYROSCOPE ARRAYS and STEERING LAWS CHITIIRAN KRISHNA MOORTHY a THESIS SUBMITTED to the F
A COMPARISON STUDY ON CONTROL MOMENT GYROSCOPE ARRAYS AND STEERING LAWS CHITIIRAN KRISHNA MOORTHY A THESIS SUBMITTED TO THE FACULTY OF GRADUATE STUDIES IN PARTIAL FULFILMENT OF THE REQUIREMENTS FOR THE DEGREE OF MASTER OF SCIENCE GRADUATE PROGRAM IN EARTH AND SPACE SCIENCE YORK UNIVERSITY TORONTO, ONTARIO DECEMBER 2019 ©CHITIIRAN KRISHNA MOORTHY, 2019 i Abstract Current reaction wheels and magnetorquers for microsatellite are limited by low slew rate and heavily depends on orbital parameters for coverage area. Control moment gyroscope (CMG) clusters offer an alternative solution for high slew rates and rapid retargeting. Though CMGs are often used in large space missions, their use in microsatellites is limited due to the stringent mass budget. Most literature reports only on pyramid configuration, and there are no definite cross comparison studies between various CMG clusters and steering laws. In this research, a generic tool in Matlab and Simulink is developed to further understand CMG configurations and steering laws for a microsat mission. Various steering laws necessary for mitigating singularities in CMG clusters are compared in two distinct missions. The simulation results were evaluated based on the pointing accuracy, platform jitter, and pointing stability achieved by the spacecraft for each combination of CMG clusters, steering laws and trajectories. The simulation results demonstrate that the pyramid cluster is marginally better than the rooftop cluster in pointing accuracy. The comparison of steering laws shows that, counterintuitively, Singularity Robust steering law, which passes through singularities, outperforms both Moore-Penrose and Local Gradient methods for almost all evaluation criteria for the two missions it was tested on. -
Appendix International Space Station Guide Appendix Image Sources 94
~~~~~~~~~~~~~~~~~~~~~~~~~~~~~~~~~~~~~~~~~~~~ appendix INTERNATIONAL SPACE STATION GUIDE APPENDIX IMAGE SOURCES 94 NASA wishes to acknowledge the use of images provided by: Canadian Space Agency European Space Agency Japan Aerospace Exploration Agency Roscosmos, the Russian Federal Space Agency INTERNATIONAL SPACE STATION GUIDE INTERNATIONAL SPACE STATION GUIDE APPENDIX APPENDIX IMAGE SOURCES 94 95 ACRONYM LIST Acronym List 1P Progress flight DLR German Aerospace Center HTV H-II Transfer Vehicle [JAxA] 1S Soyuz flight DMS Data Management System IBMP Institute for Biomedical Problems AC Assembly Complete DOS Long-Duration Orbital Station ICC Integrated Cargo Carrier [Russian] ACU Arm Control Unit ICS Internal Communications System EADS European Aeronautic Defence ARC Ames Research Center IEA Integrated Equipment Assembly and Space Company ARIS Active Rack Isolation System IRU In-flight Refill Unit ECLSS Environmental Control and Life ATCS Active Thermal Control System Support System ISPR International Standard Payload Rack atm Atmospheres ECS Exercise Countermeasures System ISS International Space Station ATV Automated Transfer Vehicle, ECU Electronics Control Unit ITA Integrated Truss Assembly launched by Ariane [ESA] EDR European Drawer Rack ITS Integrated Truss Structure ATV-CC Automated Transfer Vehicle EDV Water Storage Container [Russian] IV-CPDS Intravehicular Charged Particle Control Centre Directional Spectrometer EF Exposed Facility BCA Battery Charging Assembly JAXA Japan Aerospace Exploration Agency EHS Environmental Health System -
Final 2013.Indd
SPECULATION ON ARCHITECTURE IN THE ABSENCE OF GRAVITY Speculation on Architecture in the absence of Gravity. How might architectural elements and design strategies function in outer space? Hermann Matamu 132 8392 Master Thesis explanatory document: Jeanette Budgett Abstract The evolution of architecture has been driven by a combination of elements such as style, context, materiality, aesthetic and technology. The development of materials and the technological advancements of the human race are conveyed through architecture; from the technical expertise of the ancient Egyptians in pyramid construction, to the engineering feats of the Eiffel Tower in Paris, to the physical realisation of Gehry’s Guggenheim through computer modelling. Architecture is a continuous evolution which revolves around the progression of the human race in all fields of life. Space habitation presents the next step in this architectural evolution, in which Space tourism acts as the stepping stone for the transition of architectural design beyond Earth. Space design has been produced largely without architectural input. The aim of this project is to introduce an architectural sensibility, and to investigate the impact an absence of gravitational force has on architecture. The research follows the transition of architectural design from an environment of gravity to one without, by reviewing both current literature and precedent case studies. i Acknowledgements As this chapter in my life comes to an end, I would like to thank all those who made it a memorable one. Firstly, I would like to thank my supervisor, Jeanette Budgett. Thank you for your patience, support and constant encouragement throughout my research, your knowledge and time have been instrumental in the development of this project. -
Dynamical Study of a Control Moment Gyroscope
Explicit solution of the ODEs describing the 3 DOF Control Moment Gyroscope M. van Berkel DCT 2008.104 Traineeship report Coach(es): dr. N. Sakamoto Supervisor: Prof. dr. H. Nijmeijer Technische Universiteit Eindhoven Department Mechanical Engineering Dynamics and Control Group Eindhoven, October, 2008 Contents Contents 3 1 Introduction 4 2 Theory of Hamiltonian and Integrable systems 5 2.1 Lagrangian and Hamiltonian .............................. 5 2.2 Liouville integrability .................................. 6 2.3 Cyclic coordinates and conserved quantities ...................... 6 2.4 Poisson bracket ...................................... 6 3 Control Moment Gyroscope 7 3.1 Description of the Control Moment Gyroscope .................... 7 3.2 Lagrangian ........................................ 8 3.3 Hamiltonian and conjugate momenta ......................... 9 3.4 CMG’s first integrals ................................... 9 3.5 Solution in Integral form ................................ 9 4 Dynamics of the CMG-system 11 4.1 Equilibrium points of the unperturbed system ..................... 11 4.2 Libration ......................................... 12 4.3 Rotation .......................................... 14 4.4 Transition from libration to rotation .......................... 14 4.5 Change of motion .................................... 15 4.6 Special case of the equilibrium point .......................... 15 4.7 Summary of the different kind of motions ....................... 16 5 Construction of the solution 17 5.1 Constant q2 ....................................... -
Spring 2021 Midterm Report
Human Spaceflight Graduate Project Midterm Report For the Crewed and Uncrewed Semi-autonomous Habitat for the Exploration of Deep Space (CU SHEDS) In Support of HOME and the NASA Exploration Program Document Number: CU BIOASTRO 2021-Spring-007 March 18, 2021 This Document is for Educational Purposes Only Prepared for: University of Colorado 3100 Marine St, 572 UCB Boulder CO 80309 Bioastronautics Group Department of Aerospace Engineering Sciences College of Engineering and Applied Science University of Colorado 3775 Discovery Drive Boulder Colorado 80303 1 REVISIONS ISSUE DESCRIPTION DATE BY Notes / Major Changes 1.0 Initial Issue March 18, 2021 Rydell Stottlemyer, Colin Claytor, Kaitlyn Olson, Conner McLeod, Sam Schrup, Alex Liem, Marta Stepanyuk, Aaron Stirk, Neil Banerjee 2 Table of Contents 1. INTRODUCTION............................................................................................................ 5 2. PROJECT OVERVIEW ................................................................................................. 5 2.0 SCOPE ............................................................................................................................ 5 2.1 INDUSTRY PARTNER INFORMATION ............................................................................... 5 3. STATEMENT OF WORK AND REQUIREMENTS INFO ....................................... 6 3.0 GROUND RULES ............................................................................................................ 6 3.1 ASSUMPTIONS .............................................................................................................. -
ASCMG-JGCD-Final
JOURNAL OF GUIDANCE,CONTROL, AND DYNAMICS Vol. , No. , Adaptive Singularity-Free Control Moment Gyroscopes V. Sasi Prabhakaran∗ Akrobotix LLC, Syracuse, New York 13202 and Amit Sanyal† Syracuse University, Syracuse, New York 13244 DOI: 10.2514/1.G003545 Design considerations of agile, precise, and reliable attitude control for a class of small spacecraft and satellites using adaptive singularity-free control moment gyroscopes (ASCMG) are presented. An ASCMG differs from that of a conventional control moment gyroscopes (CMG) because it is intrinsically free from kinematic singularities and so does not require a separate singularity avoidance control scheme. Furthermore, ASCMGs are adaptive to the asymmetries in the structural members (gimbal and rotor) as well as misalignments between the center of mass of the gimbal and rotors. Moreover, ASCMG clusters are highly redundant to failure and can function as variable- and constant-speed CMGs without encountering singularities. A generalized multibody dynamics model of the spacecraft–ASCMG system is derived using the variational principles of mechanics, relaxing the standard set of simplifying assumptions made in prior literatureonCMG. The dynamics model so obtained shows the complex nonlinearcoupling between the internal degrees of freedom associated with an ASCMGand the spacecraft attitude motion.The general dynamics model is then extended to include the effects of multiple ASCMG, called the ASCMG cluster, and the sufficient conditions for nonsingular cluster configurations are obtained. The adverse effects of the simplifying assumptions that lead to the intricate design of the conventional CMG, and how they lead to singularities, become apparent in this development. A bare-minimum hardware prototype of an ASCMG using low-cost commercial off-the-shelf components is developed to show the design simplicity and scalability. -
Space Station Control Moment Gyroscope Lessons Learned
Space Station Control Moment Gyroscope Lessons Learned Charles Gurrisi*, Raymond Seidel*, Scott Dickerson*, Stephen Didziulis∗∗, Peter Frantz** and Kevin Ferguson∗∗∗ Abstract Four 4760 Nms (3510 ft-lbf-s) Double Gimbal Control Moment Gyroscopes (DGCMG) with unlimited gimbal freedom about each axis were adopted by the International Space Station (ISS) Program as the non-propulsive solution for continuous attitude control. These CMGs with a life expectancy of approximately 10 years contain a flywheel spinning at 691 rad/s (6600 rpm) and can produce an output torque of 258 Nm (190 ft-lbf)1. One CMG unexpectedly failed after approximately 1.3 years and one developed anomalous behavior after approximately six years. Both units were returned to earth for failure investigation. This paper describes the Space Station Double Gimbal Control Moment Gyroscope design, on-orbit telemetry signatures and a summary of the results of both failure investigations. The lessons learned from these combined sources have lead to improvements in the design that will provide CMGs with greater reliability to assure the success of the Space Station. These lessons learned and design improvements are not only applicable to CMGs but can be applied to spacecraft mechanisms in general. Introduction 2 The International Space Station (ISS) is currently the largest man-made object to ever orbit the Earth and represents one of the greatest engineering and integration efforts the National Aeronautics and Space Administration (NASA) has ever undertaken. The Guidance, Navigation, and Control (GN&C) system is composed of both a US non-propulsive attitude control system and a Russian thruster attitude control system. -
Highlights in Space 2010
International Astronautical Federation Committee on Space Research International Institute of Space Law 94 bis, Avenue de Suffren c/o CNES 94 bis, Avenue de Suffren 75015 Paris, France 2 place Maurice Quentin 75015 Paris, France UNITED NATIONS Tel: +33 1 45 67 42 60 75039 Paris Cedex 01, France E-mail: : [email protected] Fax: +33 1 42 73 21 20 Tel. + 33 1 44 76 75 10 URL: www.iislweb.com E-mail: [email protected] Fax. + 33 1 44 76 74 37 OFFICE FOR OUTER SPACE AFFAIRS URL: www.iafastro.com E-mail: [email protected] URL: http://cosparhq.cnes.fr Highlights in Space 2010 Prepared in cooperation with the International Astronautical Federation, the Committee on Space Research and the International Institute of Space Law The United Nations Office for Outer Space Affairs is responsible for promoting international cooperation in the peaceful uses of outer space and assisting developing countries in using space science and technology. United Nations Office for Outer Space Affairs P. O. Box 500, 1400 Vienna, Austria Tel: (+43-1) 26060-4950 Fax: (+43-1) 26060-5830 E-mail: [email protected] URL: www.unoosa.org United Nations publication Printed in Austria USD 15 Sales No. E.11.I.3 ISBN 978-92-1-101236-1 ST/SPACE/57 V.11-80947—March*1180947* 2011—475 UNITED NATIONS OFFICE FOR OUTER SPACE AFFAIRS UNITED NATIONS OFFICE AT VIENNA Highlights in Space 2010 Prepared in cooperation with the International Astronautical Federation, the Committee on Space Research and the International Institute of Space Law Progress in space science, technology and applications, international cooperation and space law UNITED NATIONS New York, 2011 UniTEd NationS PUblication Sales no. -
ISS Systems Engineering Case Study
International Space Station Systems Engineering Case Study Dr. Bill Stockman InternationalJoe SpaceBoyle Station Systems EngineeringDr. John Bacon Case Study Air Force Center for Systems Engineering Approved for Public Release; Distribution Unlimited The views expressed in this Case Study are those of the author(s) and do not reflect the official policy or position of NASA, the United States Air Force, the Department of Defense, or the United States Government. FOREWORD One of the objectives of the Air Force Center for Systems Engineering (AFCSE) is to develop case studies focusing on the application of systems engineering principles within various aerospace programs. The intent of these case studies is to examine a broad spectrum of program types and a variety of learning principles using the Friedman-Sage Framework to guide overall analysis. In addition to this case, the following studies are available at the AFCSE website. ■ Global Positioning System (space system) ■ Hubble Telescope (space system) ■ Theater Battle Management Core System (complex software development) ■ F-111 Fighter (joint program with significant involvement by the Office of the Secretary of Defense) ■ C-5 Cargo Airlifter (very large, complex aircraft) ■ A-10 Warthog (ground attack) ■ Global Hawk ■ KC-135 Simulator These cases support practitioners of systems engineering and are also used in the academic instruction in systems engineering within military service academies and at both civilian and military graduate schools. Each of the case studies comprises elements of success as well as examples of systems engineering decisions that, in hindsight, were not optimal. Both types of examples are useful for learning. Plans exist for future case studies focusing on various space systems, additional aircraft programs, munitions programs, joint service programs, logistics-led programs, science and technology/laboratory efforts, and a variety of commercial systems. -
Energetics of Control Moment Gyroscopes As Joint Actuators
JOURNAL OF GUIDANCE,CONTROL, AND DYNAMICS Vol. 32, No. 6, November–December 2009 Energetics of Control Moment Gyroscopes as Joint Actuators Daniel Brown∗ and Mason Peck† Cornell University, Ithaca, New York 14850 DOI: 10.2514/1.42313 This work compares the power and energy used by a robotic linkage actuated by either joint motors or scissored pairs of control moment gyroscopes. The objectives are to establish straightforward sizing equations that provide a basis for deciding on a system architecture and to validate them with detailed models. The resulting parallels between joint motor and control moment gyroscope actuation increase intuition for and inform the design of control moment gyroscopes on a single-body satellite. Control moment gyroscopes are chosen as an energy-efficient means of reactionless actuation that reduce nonlinearities and coupling between the robot and the spacecraft attitude control system. Scissored-pair control moment gyroscopes are well suited for robotics applications because the output torque acts only along the joint axis, eliminating undesirable gyroscopic reaction torques. Both analysis and simulation of a single-link robot demonstrate that the control moment gyroscope power is equal to the equivalent joint motor power for a large range of gimbal inertias and maximum gimbal angles. The transverse rate of the link does not affect this result. A two-link robot with orthogonal joint axes gives results similar to the single-link system unless momentum is not conserved about the joint. For a two-link robot with parallel joint axes, control moment gyroscopes outperform joint motors in power required when the joints rotate with opposite sign; the reverse is true when the joints act in unison. -
Document Title Second Line and Third Line
PROJECT MANAGER TREVOR JAHN THURSDAY LAB 2/11/2016 Semester Schedule and Updated Requirements MIKE YOUNG SYSTEMS/APM STORYBOARD 2 STORYBOARD 2 BACKUP SLIDES MISSION ARCHITECTURE DOCUMENT (SAMPLE) 1. Washington-1 (2018) Deploy and test an XM module (Bigelow BA330 inflatable habitat) in orbit around the earth. Power will be provided by a solar panels and an experimental SAFE 400 nuclear reactor. Launched by a Falcon heavy, the module will achieve LEO, deploy, and inflate remotely. 12 Mg, 16 m^3, X kW Technology goals: Test deployment of BA330 system via remote operation Test of custom control systems and telecoms Raise TRL of BA330 from 7 to 8 Raise TRL of SAFE 400 from 7 to 8 BACKUP SLIDES STORYBOARD INFO/MVP TRACKER (BY KATY O’CONNOR) (SAMPLE) SYSTEMS KYLE BUSH ISRU Technology Readiness ISRU Requirements and Recommendations 2/11/2016 NASA’S ISRU RESOURCE PROSPECTOR MISSION • RESOLVE Payload • Currently TRL 4 • Will be TRL 8 in 2020 • Utilizes CSA’s Artemis Jr. rover • OVEN instrument is of interest • Cannot collect and process resources in desired capacity • Mission • Tested on Mauna Kea in Hawaii • Planned Lunar mission in 2020 Rough Sketch of RESOLVE System • Planned to test in Cabeus • Will be tested during Lunar day Kyle Bush WHAT IS NEEDED • What the ISRU needs to produce per year: • About 0.56 Mg of water if using HydraLOX lander • About 0.46 Mg of water and 24 Mg of methane if using MethaLOX lander • Methane can also be made from hydrogen and carbon dioxide • Electrolysis would most likely be best for separating H2 and O2 • Can produce 0.786 Mg of water, 0.004509 Mg of methane and 0.01501 Mg of carbon dioxide from one rover trip. -
Characterization and Modeling of a Control Moment Gyroscope Dylan R
Air Force Institute of Technology AFIT Scholar Theses and Dissertations Student Graduate Works 3-26-2015 Characterization and Modeling of a Control Moment Gyroscope Dylan R. Penn Follow this and additional works at: https://scholar.afit.edu/etd Part of the Space Vehicles Commons Recommended Citation Penn, Dylan R., "Characterization and Modeling of a Control Moment Gyroscope" (2015). Theses and Dissertations. 179. https://scholar.afit.edu/etd/179 This Thesis is brought to you for free and open access by the Student Graduate Works at AFIT Scholar. It has been accepted for inclusion in Theses and Dissertations by an authorized administrator of AFIT Scholar. For more information, please contact [email protected]. Characterization and Modeling of a Control Moment Gyroscope THESIS 2d Lt, Dylan Penn, B.S. AFIT-ENY-MS-15-M-235 DEPARTMENT OF THE AIR FORCE AIR UNIVERSITY AIR FORCE INSTITUTE OF TECHNOLOGY Wright-Patterson Air Force Base, Ohio DISTRIBUTION STATEMENT A APPROVED FOR PUBLIC RELEASE; DISTRIBUTION UNLIMITED. The views expressed in this document are those of the author and do not reflect the official policy or position of the United States Air Force, the United States Department of Defense or the United States Government. This material is declared a work of the U.S. Government and is not subject to copyright protection in the United States. AFIT-ENY-MS-15-M-235 CHARACTERIZATION AND MODELING OF A CONTROL MOMENT GYROSCOPE THESIS Presented to the Faculty Department of Aeronautical and Astronautical Engineering Graduate School of Engineering and Management Air Force Institute of Technology Air University Air Education and Training Command in Partial Fulfillment of the Requirements for the Degree of Master of Science in Astronautical Engineering 2d Lt, Dylan Penn, B.S., B.S.