Orbital Maneuvering Vehicle (OMV) Missions Applications and Systems Requirements
Total Page:16
File Type:pdf, Size:1020Kb
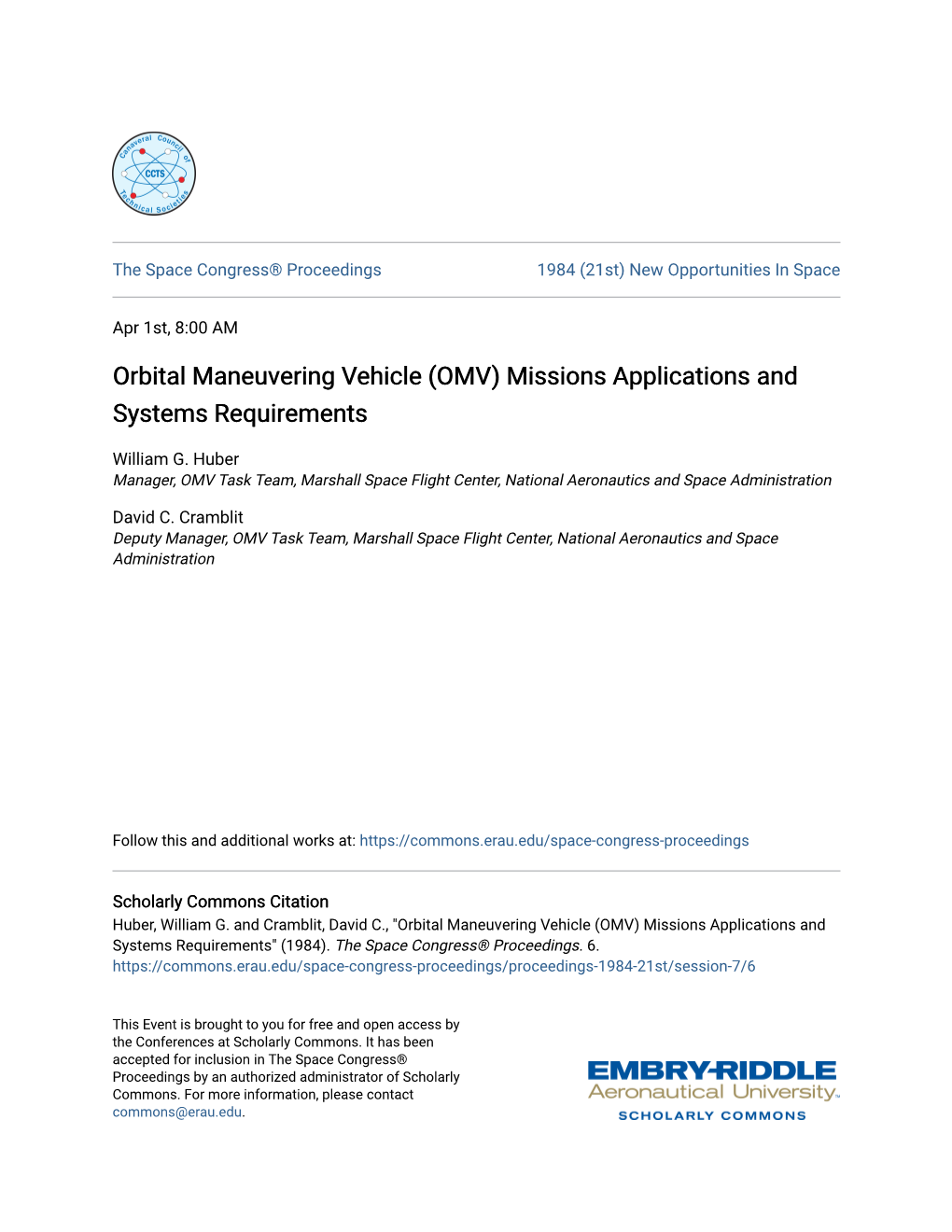
Load more
Recommended publications
-
Preface Patrick Besha, Editor Alexander Macdonald, Editor in The
EARLY DRAFT - NASAWATCH.COM/SPACEREF.COM Preface Patrick Besha, Editor Alexander MacDonald, Editor In the next decade, NASA will seek to expand humanity’s presence in space beyond the International Space Station in low-Earth orbit to a new habitation platform orbiting the moon. By the late 2020’s, astronauts will live and work far deeper in space than ever before. The push to cis-lunar orbit is part of a stepping-stone approach to extend our reach to Mars and beyond. This decision to explore ever farther destinations is a familiar pattern in the history of American space exploration. Another major pattern with historical precedent is the transition from public sector exploration to private sector commercialization. After the government has developed and demonstrated a capability in space, whether it be space-based communications or remote sensing, the private sector has realized its market potential. As new companies establish a presence, the government withdraws from the market. In 2015, we are once again at a critical stage in the development of space. The most successful long-term human habitation in space, orbiting the Earth continuously since 1998, is the International Space Station. Currently at the apex of its capabilities and the pinnacle of state-of-the-art space systems, it was developed through the investments and labors of over a dozen nations and is regularly re-supplied by cargo delivery services. Its occupants include six astronauts and numerous other organisms from Earth’s ecosystems from bacteria to plants to rats. Research is conducted on the spacecraft from hundreds of organizations worldwide ranging from academic institutions to large industrial companies and from high-tech start-ups to high-school science classes. -
Preparation of Papers for AIAA Technical Conferences
DUKSUP: A Computer Program for High Thrust Launch Vehicle Trajectory Design & Optimization Spurlock, O.F.I and Williams, C. H.II NASA Glenn Research Center, Cleveland, OH, 44135 From the late 1960’s through 1997, the leadership of NASA’s Intermediate and Large class unmanned expendable launch vehicle projects resided at the NASA Lewis (now Glenn) Research Center (LeRC). One of LeRC’s primary responsibilities --- trajectory design and performance analysis --- was accomplished by an internally-developed analytic three dimensional computer program called DUKSUP. Because of its Calculus of Variations-based optimization routine, this code was generally more capable of finding optimal solutions than its contemporaries. A derivation of optimal control using the Calculus of Variations is summarized including transversality, intermediate, and final conditions. The two point boundary value problem is explained. A brief summary of the code’s operation is provided, including iteration via the Newton-Raphson scheme and integration of variational and motion equations via a 4th order Runge-Kutta scheme. Main subroutines are discussed. The history of the LeRC trajectory design efforts in the early 1960’s is explained within the context of supporting the Centaur upper stage program. How the code was constructed based on the operation of the Atlas/Centaur launch vehicle, the limits of the computers of that era, the limits of the computer programming languages, and the missions it supported are discussed. The vehicles DUKSUP supported (Atlas/Centaur, Titan/Centaur, and Shuttle/Centaur) are briefly described. The types of missions, including Earth orbital and interplanetary, are described. The roles of flight constraints and their impact on launch operations are detailed (such as jettisoning hardware on heating, Range Safety, ground station tracking, and elliptical parking orbits). -
555/Of 474- 70
555/of 474- 70/ A PERSPECTIVE ON THE USE OF STORABLE PROPELLANTS FOR FUTURE SPACE VEHICLE PROPULSION William C. Boyd and Warren L. Brasher NASA, Johnson Space Center 0 O"0 Houston, Texas 0 ABSTRACT Propulsion system configurations for future NASA and DOD space initiatives are driven by the continually emerging new mission requirements. These initiatives cover an extremely wide range of mission scenarios, from unmanned planetary pro- grams, to manned lunar and planetary programs, to Earth-oriented ('Mission to Planet Earth) programs, and they are in addition to existing and future require- ments for near-Eirth missions such as to geosynchronous earth orbit (GEO). Increasing space transportation costs, and anticipated high costs associated with space-basing of future vehicles, necessitate consideration of cost-effective and easily maintainable configurations which maximize the use of ex-Isting technologies and assets, and use budgetary resources effectively. System design considerations associated with the use of storable propellants to fill these needs are presented. Comparisons in areas such as ccrrplexity, performance, flexibility, maintainabili- ty, and technology status are made for earth and space storable propellants, cluding nitrogen tetroxide/monomethylhydrazine and LOX/monomethylhydrazine. INTRODUCTION As the nation approaches the next century, some very harsh realities mist be faced, and some equally important decisions will be made. The economic and progranrnatic realities of space flight, and of space vehicle development and oper- ation, have been forced home. We have learned that space systems are expensive and conplex, require a long time to develop, and are allowed very little margin for error. In spite of these realities, however, we know that doing business in space in the future is going to require significant advances in orbital capability over what is currently available. -
COMMERCIALIZING the TRANSFER ORBIT STAGE Michael W. Miller
COMMERCIALIZING THE TRANSFER ORBIT STAGE Michael W. Miller Orbital Sciences Corporation Vienna, Virginia 22 180 ABSTRACT Orbital Sciences Corporation (OSC), a technically-based management, marketing, and financial corporation, was formed in 1982 to provide economical space transportation hardware and services to commercial and government users. As its first project, OSC is developing a new medium-capacity upper stage for use on NASA’s Space Shuttle, called the TOS. Before the TOS project successfully entered the development stage, many obstacles for a new company operat- ing in the established space industry had to be overcome. This paper describes key milestones necessary to establish this new commercial space endeavor. Historical milestones began with the selection of the project concept and synthesis of the company. This was followed by venture capital support which led to early discussions with NASA and the selection of a major aerospace company as prime contractor. A landmark agree- ment with NASA sanctioned the commercial TOS concept and provided the critical support necessary to raise the next round of venture capital. Future challenges including project management and customer commitments are also discussed. BACKGROUND Orbital Sciences Corporation (OSC), a technically-based management, marketing, and financial corporation, was formed in 1982 to provide economical space transportation hardware and services to commercial and government users. As its first project, OSC is developing a new medium-capacity upper stage-for use on NASA’s Space Shuttle,called the Transfer Orbit Stage (TOS). The TOS project represents an evolutionary milestone in the nation’s attempts to com- mercialize space. Responding to the Reagan administration’s mandate and to Congressional guidelines, NASA is encouraging private-sector initiatives in space activities. -
INTEGRATED SPACE PLAN (Preliminary)
CRITICAL PATH AMERICAN SPACE SHUTTLE PROGRAM INTEGRATED SPACE PLAN Space Transportation (NSTS) Systems Division FIRST INTERNATIONAL RMS GENERATION EXPENDABLE LAUNCH (INTERNATIONAL) OF VEHICLE FLEET (Preliminary) IUS UNITED STATES LAUNCH VEHICLE CAPABILITES REUSABLE SPACECRAFT PRIVATE LAUNCH VERSION 1.1 FEBRUARY, 1989 VEHICLE # TO LEO # TO GEO GEO-CIRCULAR FIRST FLIGHT VEHICLES ALS 200,000 1998 * THE AMERICAN SPACE SHUTTLE (ELV’S) EMU SHUTTLE C 150,000 20,000 (CENTAUR) 1994 1983 PRODUCED BY RONALD M. JONES D/385-210 SPACE 55,000 5,500 (IUS) 1981 1983 * CHALLENGER OV-099 SHUTTLE 6,500 (TOS) * COLUMBIA OV-102 ABOUT THIS DIAGRAM: TITAN 4 40,000 12,500 10,000 (CENTAUR) 1989 OV-103 * DISCOVERY GOVERNMENT - The Rockwell Integrated Space Plan (ISP) is a very long range systematic perspective of America’s and the TITAN 3 33,000 8,600 4,200 (IUS) 1965 MMU * ATLANTIS OV-104 COMMERCIAL SATELLITE Western World’s space program. Its 100-plus-year vision was created from the integration of numerous NASA ATLAS 2 14,400 5,200 2,500 1991 EARTH-TO-ORBIT * TBD OV-105 DEPLOYMENT long-range studies including the project Pathfinder case studies, recommendations from the National ATLAS 1 12,300 1959 AND IN-SPACE Commission on Space’s report to the President, the Ride report to the NASA Administrator, and the new DELTA 2 11,100 3,190 1,350 (PAM-D) 1988 SATELLITE RETRIEVAL * THE SOVIET SPACE SHUTTLE TRANSPORTATION SYSTEMS National Space Policy Directive. Special initiatives such as the four Pathfinder scenarios or those described in DELTA 7,800 1960 AND SERVICING * BURAN the Ride Report (i.e., Mission To Planet Earth, Exploration of the Solar System, Outpost on the Moon, and TITAN 2 5,500 1965 DEFENSE SATELLITES Humans to Mars) are integral parts of the ISP. -
Spacecraft Chemical Propulsion Systems at NASA Marshall Space Flight Center: Heritage and Capabilities
Spacecraft Chemical Propulsion Systems at NASA Marshall Space Flight Center: Heritage and Capabilities Patrick S. McRight*, Jeffrey A. Sheehyt, and John A. Blevins' NASA George C. Marshall Space Flight Center, Huntsville, AL 35812 NASA Marshall Space Flight Center (MSFC) is well known €or its contributions to large ascent propulsion systems such as the Saturn V and the Space Shuttle. This paper highlights a lesser known but equally rich side of MSFC - its heritage in spacecraft chemical propulsion systems and its current capabilities for in-space propulsion system development and chemical propulsion research. The historical narrative describes the efforts associated with developing upper-stage main propulsion systems such as the Saturn S-IVB as well as orbital maneuvering and reaction control systems such as the S-IVB auxiliary propulsion system, the Skylab thruster attitude control system, and many more recent activities such as Chandra, the Demonstration of Automated Rendezvous Technology, X-37, the X-38 de-orbit propulsion system, the Interim Control Module, the US Propulsion Module, and several technology development activities. Also discussed are MSFC chemical propulsion research capabilities, along with near- and long-term technology challenges to which MSFC research and system development competencies are relevant. I. Introduction N the days following the launch of Sputnik I on 4 October 1957, the American public eagerly awaited the Isuccessful launch of an American rocket. Weeks later. on 6 December 1957, the US Navy Vanguard rocket exploded on its launch pad at Cape Canaveral. Attention shifted toward the United States backup rocket program, based on the Army Jupiter-C rocket developed by the Army Ballistic Missile Agency (ABMA) at Redstone Arsenal in Huntsville, Alabama under the direction of Dr. -
SPACE TRANSPORTATION Contents
Chapter 5 SPACE TRANSPORTATION Contents Page Introduction. ..............103 The Space Transportation Industry . ................103 The providers of Space Transportation Services . .. ...103 Buyers of Space Transportation Services . ................122 Competition in Space Transportation . ......125 Development of Competition . ............125 Assessment of Demand . .................126 Nature of Competition . .. ...128 Effects of Competition . .. ....134 Cooperation in Space Transportation . ..............137 Current Policies. ........................138 Future Policy Options.. .. ....140 List of Tables Table No. Page 5-1. Ariane Flights . ..........115 5-2. Transportation Costs to Geosynchronous Orbit . ......................132 5-3. NASA vs. Arianespace Financing . ..............133 5-4. Companies That Contribute to Manufacturing Japanese Launch Vehicles ..139 List of Figures Figure No. Page 5-1. U.S. Launch vehicles . ..............104 5-2.The Hermes Spaceplane . ..................116 5-3. Foreign National Comparative Launch Vehicle Development. ..........118 5-4. Projection of Future Space Shuttle Demand Rockwell International. ...127 5-5. Outside Users Payload Model Battelle’s Columbus Laboratories . .......,128 5-6. Low Model Market Share by Launch Vehicle . ...............129 5-7. High Model Market Share by Launch Vehicle . .......................130 5-8. Arianespace Financing . ..133 5-9. Rockwell International Estimates That the Shuttle is Most Economical Over ELVs at High-Volume Operations. ............................135 -
General Disclaimer One Or More of the Following Statements May Affect This Document
General Disclaimer One or more of the Following Statements may affect this Document This document has been reproduced from the best copy furnished by the organizational source. It is being released in the interest of making available as much information as possible. This document may contain data, which exceeds the sheet parameters. It was furnished in this condition by the organizational source and is the best copy available. This document may contain tone-on-tone or color graphs, charts and/or pictures, which have been reproduced in black and white. This document is paginated as submitted by the original source. Portions of this document are not fully legible due to the historical nature of some of the material. However, it is the best reproduction available from the original submission. Produced by the NASA Center for Aerospace Information (CASI) f , 0 44)Y^ R'I (NA$A --C 4 -1737 65) EXCESS SCIENCE N84-;18882 IiCLU4i'lUlitlT,Ut CAPABILITIES ANC EXCESS PE1t2uL4ANCE CAPABIL,1TIES ASSLSSMEN1 FOR MARS UL0jC16iiLE AND (L ,I.PIA`1'ULW Y ORBIT L;11: U1XC-Ld 3 .,X'r.jNI)Jll STUDY F ival Hoport (ACA Government; GJ/1l 17782 Excess Science Accommodation Capabilities and Excess Performance Capabilities Assessment for Mars Geoscience and Climatology Orbiter Extended Study - Final Report Prepared for Jet Propulsion Laboratory m California Institute of Technology Sponsored by the National Aeronautics and Space Administration under Contract NAS7-918 'r, s 4 Prepared by RCA Government Systemb Division Astro•Electronics Princeton, New Jersey Authors K. Clark, A. Placco, ^^ 3,{ P. Kaskiewicz, and ti ` K. Lebsock 1 k4Sgs„1P^i^ Q Contract No. -
International Cooperation and Competition in Civilian Space Activities
International Cooperation and Competition in Civilian Space Activities June 1985 NTIS order #PB87-136842 Recommended Citation: International Cooperation and Competition in Civilian Space Activities (Washington, DC: U.S. Congress, Office of Technology Assessment, OTA-ISC-239, July 1985). Library of Congress Catalog Card Number 84-601087 For sale by the Superintendent of Documents U.S. Government Printing Office, Washington, DC 20402 Foreword The nature of global space activities has changed radically over the last decade. No longer are the United States and the Soviet Union the only countries capable of placing satellites into Earth orbit or sending interplanetary probes into deep space. Europe and Japan now have substantial space programs and have developed commercially competitive space systems. Several newly industrialized countries are well along in building their own space programs. In addition, the U.S. private sector has recently expanded its interest and investment in space technology. As this report makes clear, these changes have strong policy implications for the U.S. Government space program and for the U.S. private sector. This report presents the major findings of an assessment requested by the House Committee on Science and Technology and the Joint Economic Committee, on inter- national cooperation and competition in civilian space activities. The United States still enjoys a strong competitive position in most space technologies and in space science. There continues to be broad support for a long-term public commitment to civilian space activities. But precisely because of our achievements—and those of other space-far- ing nations—the number of opportunities (and associated costs) that lie before us re- quire a thoughtful articulation of space goals and objectives. -
Classification of Geosynchrono
ESA UNCLASSIFIED - Limited Distribution ! esoc European Space Operations Centre Robert-Bosch-Strasse 5 D-64293 Darmstadt Germany T +49 (0)6151 900 F +31 (0)6151 90495 www.esa.int TECHNICAL NOTE Classification of Geosynchronous objects. Prepared by ESA Space Debris Office Reference GEN-DB-LOG-00270-OPS-SD Issue/Revision 21.0 Date of Issue 19 July 2019 Status Issued ESA UNCLASSIFIED - Limited Distribution ! Page 2/234 Classification of Geosynchronous objects. Issue Date 19 July 2019 Ref GEN-DB-LOG-00270-OPS-SD ESA UNCLASSIFIED - Limited Distribution ! Abstract This is a status report on (near) geosynchronous objects as of 1 January 2019. Based on orbital data in ESA’s DISCOS database and on orbital data provided by KIAM the situation near the geostationary ring is analysed. From 1578 objects for which orbital data are available (of which 14 are outdated, i.e. the last available state dates back to 180 or more days before the reference date), 529 are actively controlled, 831 are drifting above, below or through GEO, 195 are in a libration orbit and 21 are in a highly inclined orbit. For 2 object the status could not be determined. Furthermore, there are 60 uncontrolled objects without orbital data (of which 55 have not been catalogued). Thus the total number of known objects in the geostationary region is 1638. Finally, there are 130 rocket bodies crossing GEO. If you detect any error or if you have any comment or question please contact: Stijn Lemmens European Space Agency European Space Operations Center Space Debris Office (OPS-GR) Robert-Bosch-Str. -
555/Of Provided474- by NASA Technical Reports Server 70
https://ntrs.nasa.gov/search.jsp?R=19900009157 2020-03-20T00:02:33+00:00Z View metadata, citation and similar papers at core.ac.uk brought to you by CORE 555/of provided474- by NASA Technical Reports Server 70/ A PERSPECTIVE ON THE USE OF STORABLE PROPELLANTS FOR FUTURE SPACE VEHICLE PROPULSION William C. Boyd and Warren L. Brasher NASA, Johnson Space Center 0 O"0 Houston, Texas 0 ABSTRACT Propulsion system configurations for future NASA and DOD space initiatives are driven by the continually emerging new mission requirements. These initiatives cover an extremely wide range of mission scenarios, from unmanned planetary pro- grams, to manned lunar and planetary programs, to Earth-oriented ('Mission to Planet Earth) programs, and they are in addition to existing and future require- ments for near-Eirth missions such as to geosynchronous earth orbit (GEO). Increasing space transportation costs, and anticipated high costs associated with space-basing of future vehicles, necessitate consideration of cost-effective and easily maintainable configurations which maximize the use of ex-Isting technologies and assets, and use budgetary resources effectively. System design considerations associated with the use of storable propellants to fill these needs are presented. Comparisons in areas such as ccrrplexity, performance, flexibility, maintainabili- ty, and technology status are made for earth and space storable propellants, cluding nitrogen tetroxide/monomethylhydrazine and LOX/monomethylhydrazine. INTRODUCTION As the nation approaches the next century, some very harsh realities mist be faced, and some equally important decisions will be made. The economic and progranrnatic realities of space flight, and of space vehicle development and oper- ation, have been forced home. -
Cambridge University Press 978-0-521-77300-3
Cambridge University Press 978-0-521-77300-3 — The Cambridge Encyclopedia of Space Fernand Verger , Isabelle Sourbès-Verger , Raymond Ghirardi , With contributions by Xavier Pasco , Foreword by John M. Logsdon , Translated by Stephen Lyle , Paul Reilly Index More Information Index Bold face entries refer to figures and figure Advanced Land Imager (ALI) 169, 232, 237 Agila 54, 297, 315 captions. resolution 274 chronology 291 Advanced Land Observation Satellite (ALOS) 163, position 291 169, 270 spectral bands 289 A sensors 232, 237, 270, 274 AGN AAD VSAR 237, 274 see active galactic nucleus see Acquisition, Archiving and Distribution Advanced Land Remote Sensing System (ALRSS) agriculture 241 AATSR 252 Airborne Laser (ABL) 356, 358 see Advanced Along Track Scanning Advanced Landsat 252 air braking 174, 204 Radiometer Advanced Microwave Scanning Radiometer Air Density Explorer (ADE) 170 ABL (AMSR) 174, 262 Air Launch Aerospace Corporation 111, 126, 128 see Airborne Laser Advanced Microwave Sounding Unit (AMSU) 174 AIRS ABM METOP 243 see Atmospheric Infrared Sounder see antiballistic missile systems Advanced Orion 54 Akebono 175, 176, 177, 178, 178 ABM Treaty (1972) 355 Advanced Satellite for Cosmology and Akjuit Aerospace Company 104, 110 accidents in space 48–49, 195, 362–363 Astrophysics (ASCA) 186 Alaska Aerospace Development Corp. 134 ACE Advanced Satellite Launch Vehicle (ASLV) 156, Alcantara space base 104, 108, 110, 157 see Advanced Composition Explorer 157 Alcatel Space 94, 294, 305, 308 see Atmospheric Chemistry Explorer payload