Stepper Motors
Total Page:16
File Type:pdf, Size:1020Kb
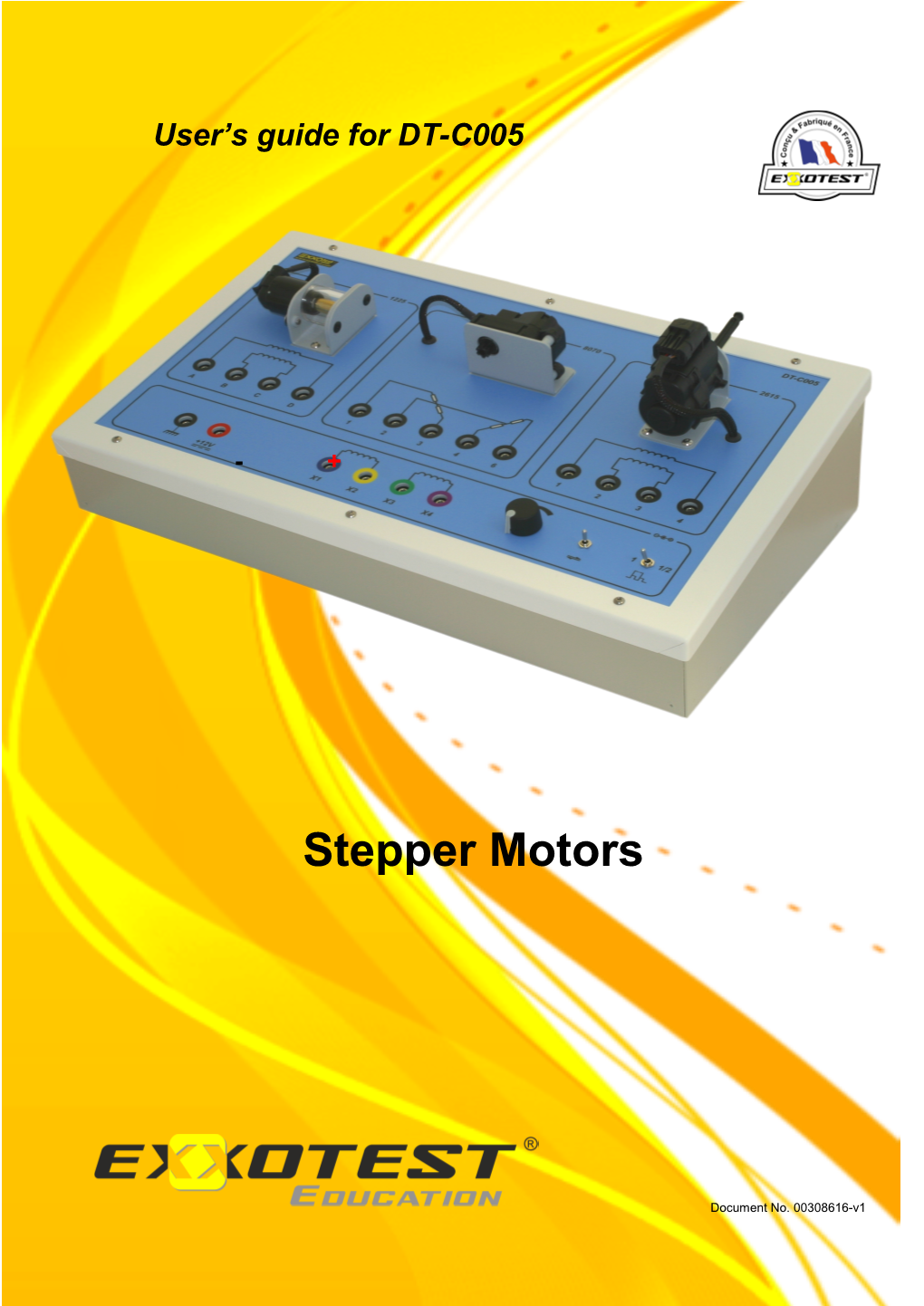
Load more
Recommended publications
-
Stepping Motors Fundamentals
AN907 Stepping Motors Fundamentals Author: Reston Condit TYPES OF STEPPING MOTORS Microchip Technology Inc. There are three basic types of stepping motors: Dr. Douglas W. Jones permanent magnet, variable reluctance and hybrid. University of Iowa This application note covers all three types. Permanent magnet motors have a magnetized rotor, while variable reluctance motors have toothed soft-iron rotors. Hybrid INTRODUCTION stepping motors combine aspects of both permanent Stepping motors fill a unique niche in the motor control magnet and variable reluctance technology. world. These motors are commonly used in measure- The stator, or stationary part of the stepping motor ment and control applications. Sample applications holds multiple windings. The arrangement of these include ink jet printers, CNC machines and volumetric windings is the primary factor that distinguishes pumps. Several features common to all stepper motors different types of stepping motors from an electrical make them ideally suited for these types of point of view. From the electrical and control system applications. These features are as follows: perspective, variable reluctance motors are distant 1. Brushless – Stepper motors are brushless. The from the other types. Both permanent magnet and commutator and brushes of conventional hybrid motors may be wound using either unipolar motors are some of the most failure-prone windings, bipolar windings or bifilar windings. Each of components, and they create electrical arcs that these is described in the sections below. are undesirable or dangerous in some environments. Variable Reluctance Motors 2. Load Independent – Stepper motors will turn at Variable Reluctance Motors (also called variable a set speed regardless of load as long as the switched reluctance motors) have three to five load does not exceed the torque rating for the windings connected to a common terminal. -
Difference Between Bipolar Drives and Unipolar Drives for Stepper Motors
WHITE PAPER DIFFERENCE BETWEEN BIPOLAR DRIVES AND UNIPOLAR DRIVES FOR STEPPER MOTORS orking on a motorized development requires some knowledge about motors and controllers. This article Wis focused on the stepper motors which is a type of brushless DC motor with a high number of poles. This technology is generally driven in open loop without any feedback sensor, meaning the current is typically applied on the phases without knowing the rotor position. The rotor moves to be aligned with the stator magnetic flux, then the current can be supplied to the next phase. We will consider two ways to supply current in the coil: bipolar way and unipolar way. In this article, we will explain the differences of bipolar and unipolar motors and driving methods. We will show the advantages and limits of both technologies. Let’s take an example of a four step, permanent magnet stepper motor (see figure 1). The rotor is made with a one pole pair magnet, and the stator is composed of two phases, Phase A and Phase B. • In unipolar: the current always flows in the same direction. Each coil is dedicated to one current direction, meaning either the coil A+ or the coil A- is powered. The coils A+ and A- are never powered together. • In bipolar: the current can flow in both directions in all coils. The phases A+ and A- are powered together. A bipolar motor requires one coil minimum per phase and unipolar motor Figure 1. 4-Step Stepper Motor requires two coils minimum per phase. Let’s review both options in more detail. -
Motor Actuators Basics
Motor Actuators Basics - 1 - Note: All specifications and other information are not guaranteed and are subject to change without notice. Prior to any new usage of JE motor actuators it is recommended to contact Johnson Electric. All information below and content of links are subject to the disclaimer of the Johnson Electric website - 2 - Contents Overview ....................................................................................................................................................................... 4 Classification ............................................................................................................................................................. 5 DC Motors ................................................................................................................................................................. 6 Universal Motors ....................................................................................................................................................... 7 BLDC Motors ............................................................................................................................................................. 8 Synchronous Motors ................................................................................................................................................. 9 Stepper Motors ........................................................................................................................................................ 10 Shaded -
Stepper Motor Basics
Industrial Circuits Application Note Stepper Motor Basics A stepper motor is an electromechanical Disadvantages device which converts electrical pulses into 15° discrete mechanical movements. The shaft 1. Resonances can occur if not A or spindle of a stepper motor rotates in properly controlled. D' discrete step increments when electrical 2. Not easy to operate at extremely B command pulses are applied to it in the high speeds. 1 proper sequence. The motors rotation has 6 several direct relationships to these applied 2 C' C input pulses. The sequence of the applied Open Loop Operation 5 pulses is directly related to the direction of One of the most significant advantages 3 motor shafts rotation. The speed of the of a stepper motor is its ability to be 4 B' motor shafts rotation is directly related to accurately controlled in an open loop D the frequency of the input pulses and the system. Open loop control means no length of rotation is directly related to the feedback information about position is A' number of input pulses applied. needed. This type of control eliminates the need for expensive Figure 1. Cross-section of a variable- sensing and feedback devices such as reluctance (VR) motor. Stepper Motor Advantages optical encoders. Your position is and Disadvantages known simply by keeping track of the input step pulses. Advantages 1. The rotation angle of the motor is Stepper Motor Types proportional to the input pulse. There are three basic stepper motor types. They are : 2. The motor has full torque at stand- N N S N S N still (if the windings are energized) • Variable-reluctance 3. -
Motor Actuators Basics
Motor Actuators Basics - 1 - Note: All specifications and other information are not guaranteed and are subject to change without notice. Prior to any new usage of JE motor actuators it is recommended to contact Johnson Electric. All information below and content of links are subject to the disclaimer of the Johnson Electric website - 2 - Contents Overview ....................................................................................................................................................................... 4 Classification ............................................................................................................................................................. 5 DC Motors ................................................................................................................................................................. 6 Universal Motors ....................................................................................................................................................... 7 BLDC Motors ............................................................................................................................................................. 8 Synchronous Motors ................................................................................................................................................. 9 Stepper Motors ........................................................................................................................................................ 10 Shaded -
Simple Discussion on Stepper Motors for the Development of Electronic
International Journal of Scientific & Engineering Research, Volume 5, Issue 1, January-2014 1089 ISSN 2229-5518 Simple Discussion on Stepper Motors for the Development of Electronic Device Tanu Shree Roy, Humayun Kabir, Md A. Mannan Chowdhury Abstract— This paper is designed and developed to have the general as well as basic knowledge about the modern electronic device named ‘Stepper motor’. A step motor can be viewed as a synchronous AC motor with the number of poles (on both rotor and stator) in- creased, taking care that they have no common denominator. Additionally, we have discussed about its characteristics, classification, oper- ation, advantages and electric magnetic effects. Index Terms— Electronic device, stepper motor, synchronous, rotor, stator, electric and magnetic effects. —————————— —————————— 1 INTRODUCTION Stepper motors can be viewed as electric motors without trol. Stepper systems are economical to implement, intuitive to commentators. Typically all windings in the motor are part control, and have good low speed torque, making them ideal of the stator and the rotor is permanent magnet or in the case for many low power, computer-controlled applications. They of variable reluctance motors, a toothed block of some magneti- can be for example interfaced to computer using few transistors cally soft material. All of the commutation must be handled and made to rotate using a small piece of software. Stepper mo- externally by the motor controller, and typically, the motors and tors provide good position repeatability. Stepper motors are controllers are designed so that the motor may be held in any used in robotics control and in computer accessories (disk fixed position as well as being rotated one way or the other [1, drives, printers, scanners etc.). -
Introduction to Stepper Motors Part 1: Types of Stepper Motors
Introduction to Stepper Motors Part 1: Types of Stepper Motors © 2007 Microchip Technology Incorporated. All Rights Reserved. Introduction to Stepper Motors Slide 1 Hello, my name is Marc McComb, I am a Technical Training Engineer here at Microchip Technology in the Security, Microcontroller and Technology Division. Thank you for downloading Introduction to Stepper Motors. This is Part 1 in a series of webseminars related to Stepper Motor Fundamentals. The following webseminar will focus on some of the stepper motors available for your applications. So let’s begin. 1 Agenda z Topics discussed in this WebSeminar: − Main components of a stepper motor − How do these components work together − Types of stepper motors © 2007 Microchip Technology Incorporated. All Rights Reserved. Introduction to Stepper Motors Slide 2 During this webseminar I will discuss the main components of a stepper motor and how these components work together to actually turn the rotor. We will also explore three types of stepping motors as well as two sub categories. 2 Stepper Motor Basics © 2007 Microchip Technology Incorporated. All Rights Reserved. Introduction to Stepper Motors Slide 3 So let’s start off with some stepper motor basics 3 What is a Stepper Motor? z Motor that moves one step at a time − A digital version of an electric motor − Each step is defined by a Step Angle Start Position Step 1 Step 2 © 2007 Microchip Technology Incorporated. All Rights Reserved. Introduction to Stepper Motors Slide 4 First, what is a stepper motor? As the name implies, the stepper motor moves in distinct steps during its rotation. Each of these steps is defined by a Step Angle. -
Electric Motor Handbook
Motor Handbook Authors: Institute for Power Electronics and Electrical Drives, RWTH Aachen University Fang Qi Daniel Scharfenstein Claude Weiss Infineon Technologies AG Dr. Clemens Müller Dr. Ulrich Schwarzer Version: 2.1 Release Date: 12.03.2019 Motor Handbook 2 Preface This motor handbook was created by Infineon Technologies AG together with Institute for Power Electronics and Electrical Drives, RWTH Aachen University/ Germany. It was originally released in its first version in 2016. Based on the feedback, which has been received in the meantime, a new version with further improved motor images and updated diagrams has been developed. Dr. Clemens Müller Infineon Technologies AG IFAG IPC ISD Munich/Germany, March 2019 Motor Handbook 3 Contents Preface ..................................................................................................... 2 Contents ................................................................................................... 3 Introduction............................................................................................... 5 Induction machine (IM) ............................................................................... 7 Structure and functional description ........................................................... 9 Motor characteristics and motor control ...................................................... 9 Notable features and ratings ................................................................... 22 Strengths and weaknesses .................................................................... -
A UNIPOLAR INVERTER DRIVE for a CAGE INDUCTION MOTOR By
A UNIPOLAR INVERTER DRIVE FOR A CAGE INDUCTION MOTOR by PATRICK REGINALD PALMER B.Sc.(Eng.), A.C.G.I., A.M.I.E.E. Thesis submitted to the University of London for the degree of Doctor of Philosophy and for the Diploma of Imperial College Department of Electrical Engineering Imperial College of Science and Technology September 1985 1 ABSTRACT # This thesis describes a novel pulse-width-modulated, voltage fed, unipolar inverter drive scheme for a squirrel-cage induction motor, which enables effective shoot through protection. Standard PWM techniques were employed. The proposed scheme was tested using standard ♦ two pole, totally enclosed, fan cooled, three phase induction motors, rated at 4 kW and 415 Vac. Simple alterations are required to the motor windings, and these were made by the manufacturer. * A review of inverter technology covers the principal categories of inverters, switching devices and detail circuitry. The modes of operation of unipolar schemes are discussed and their advantages and disadvantages # identified. A description of the experimental drive and its operating details follows, reference being made to measured current waveforms. Measured torque-speed and efficiency-speed * graphs are presented and discussed. For a more detailed examination of the performance a theoretical model of the entire inverter-induction motor scheme is developed. The model for the motor is based on a # mutually coupled coils approach. The predictions confirm the explanation of the operation given previously. Theoretical comparisons are made between the proposed 2 unipolar drive and equivalent conventional inverter ^ drives. There is then an extensive study of the inverter under fault conditions, where it is shown that the behaviour of the inverter under fault conditions is predictable and ^ controllable. -
Technical Reference 227 Step Motors & Drives
Step Motors & Drives The typical step motor system consists Step Motor Construction Permanent Magnet Step of a step motor and a drive package The three most popular types of step Motors that contains the control electronics motors are the variable reluctance and a power supply. The drive receives The permanent magnet (PM) step (VR), permanent magnet and the hy- step and direction signals from an in- motor is shown in Figure 14. Perma- brid. The hybrid step motor is by far dexer or programmable motion con- nent magnet motors differ from VR’s the most popular. While a variety of troller, which may be an integrated part by having a permanent magnet rotor step angles are available, the most of the drive. The drive logic determines with no teeth, which is magnetized common and popular is the 200 step the correct current level for each phase perpendicular to its axis. The stator per revolution, which is commonly re- of the motor and the power amplifiers consists of two stamped steel cups ferred to as a 1.8 degree step motor. generate and maintain the proper cur- with diagonally shaped teeth facing the rent loads. The power supply provides rotor. Coils of wire are wrapped the necessary voltages from the AC Variable Reluctance Step around each of the stator cups. or DC power source. Motors By energizing the phases in sequence, The general construction for a variable the rotor will rotate as it follows the Advantages of step motor reluctance step motor is shown in Fig- changing magnetic field. In this ex- ure 13. -
Fundamentals of Electric Motors and Transformers
Short Course on Energy Efficiency ISBN : 984-32-1803-6 15 Fundamentals of Electric Motors and Transformers Rajib Mikail Lecturer Department of Electrical and Electronic Engineering Bangladesh University of Engineering and Technology Dhaka e-mail: [email protected] Introduction Motors and transformers are the key driving force for industrial and residential appliances. We can’t even imagine an industry without motors and transformers. In industry all types of linear or rotational force, movement, torque, etc are applied by motors. Industries are getting automated day by day, hence the use of motors are increasing with the same pace. The power supply to any medium or large scale industry comes through transformer as the utilities prefer to supply at higher grid voltage. Maximum portion of power that is consumed in any industry is by motors. So the efficiency is a great issue for an industry owner to think about. The efficiency of the major consumer, the motor must be of as high as possible. The efficiency of the transformer, through which all the power is consumed, must also be near 100 percent. So every personnel related to the decision making in industry must have the knowledge regarding the energy efficiency issue for motors and transformers. Operation To discuss about the operation of motors and transformers we must know the basic principles of Faraday’s Law of Electromagnetic induction. According to Faraday if there is any rate of change of flux incorporated inside a conducting loop then there will be an EMF, hence voltage induced in the loop. If the loop is shorted or connected end to end, then a current will flow through the conductor. -
Stepper Motors Tech Talk Nov 2010
What is a stepper motor? 1. A stepper motor (or step motor) is a brushless, synchronous electric motor that can divide a full rotation into a large number of steps. The motor's position can be controlled precisely without any feedback mechanism (see Open-loop controller), as long as the motor is carefully sized to the application. Stepper motors are similar to switched reluctance motors (which are very large stepping motors with a reduced pole count, and generally are closed-loop commutated. 2. Stepper motors operate differently from DC brush motors, which rotate when voltage is applied to their terminals. Stepper motors, on the other hand, effectively have multiple "toothed" electromagnets arranged around a central gear-shaped piece of iron. The electromagnets are energized by an external control circuit, such as a microcontroller. To make the motor shaft turn, first one electromagnet is given power, which makes the gear's teeth magnetically attracted to the electromagnet's teeth. When the gear's teeth are thus aligned to the first electromagnet, they are slightly offset from the next electromagnet. So when the next electromagnet is turned on and the first is turned off, the gear rotates slightly to align with the next one, and from there the process is repeated. Each of those slight rotations is called a "step", with an integer number of steps making a full rotation. In that way, the motor can be turned by a precise angle. 3. Stepper motor characteristics 1. Stepper motors are constant power devices. 2. As motor speed increases, torque decreases. (most motors exhibit maximum torque when stationary, however the torque of a motor when stationary 'holding torque' defines the ability of the motor to maintain a desired position while under external load).