Bid Form for Fabrication of Ordinary District Type Bus Bodies
Total Page:16
File Type:pdf, Size:1020Kb
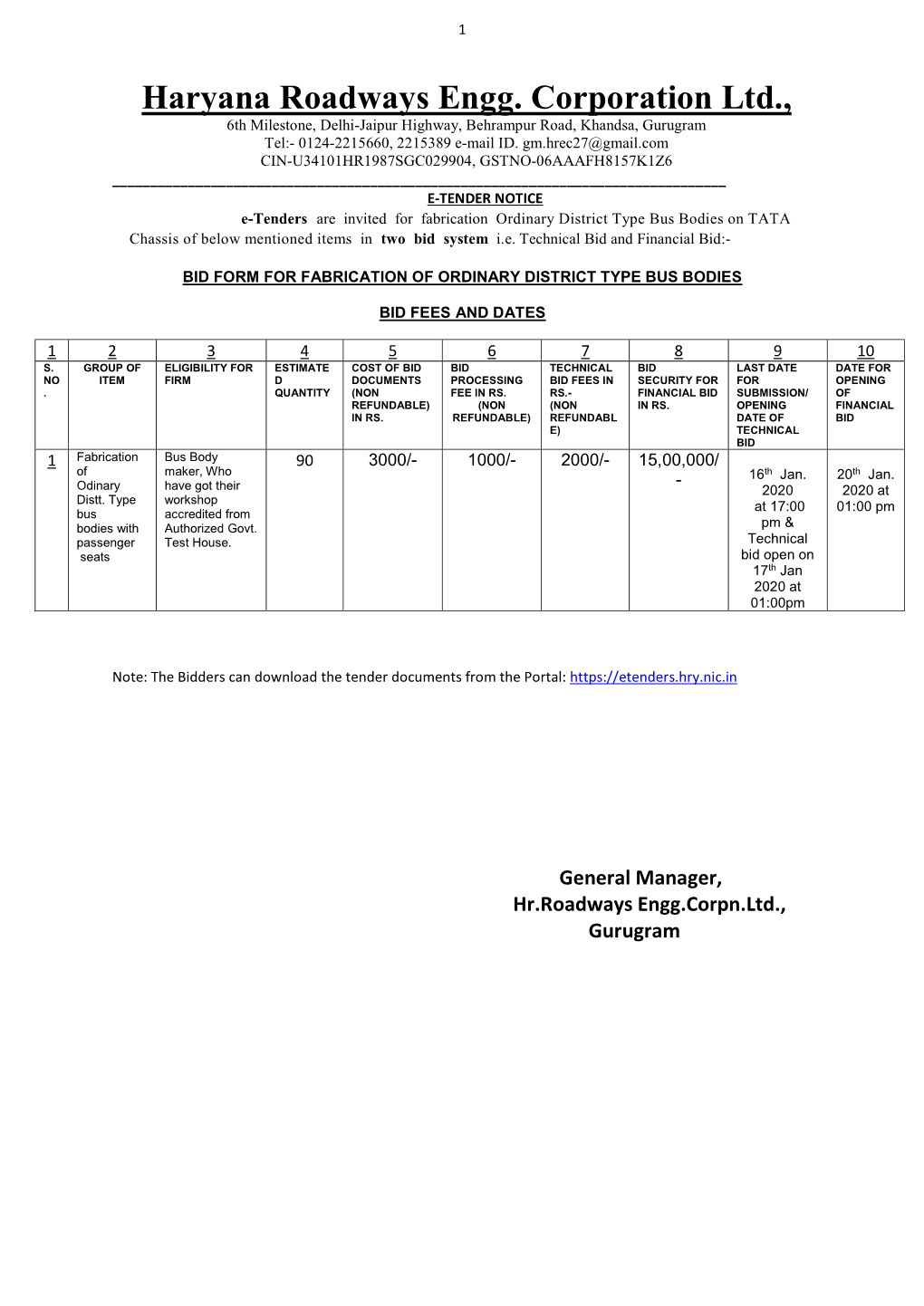
Load more
Recommended publications
-
Directorate of State Transport, Haryana Spo/He Dated: /5
Directorate of State Transport, Haryana 30-Bays Building, 2no FIoor, Sector_17, Chandigarh DTC (Storcs) 0172-2709809; E_Mail tD: _ d([email protected] To l. Senior Mechanical Engineer, Govt. central workshop, chandigarh. 2, All General Managers, Haryana Roadways. 3. Deputy Transport Controllers, Haryana Roadways Central Workshop, Hisar& Karnal. 4. Flying Squad officer, Haryana Roadways, Inter State Bus Terminal, Delhi. 5. General Manager, Driver Training lnstitute, Murthal (Sonipat). Memo No. SpO/He Dated: /5 - tz ^Ie Subject: Promoting of Digital payment - cashless Transactions. As you are aware that the Govt. of India I Haryana have resolved to make the financial transactions in State Transport Department, Haryana cashless and a few steps have already been initiated at different level of Covt. Authorities. In orderto promote cashless transaction in the department, the,following proposals of the office have been approved by competent authorities which are as under:- I' An online application for Driving Training Fees Payment has been developed to make payment online on e-Gras. All concerned officers are advised to accept Driving Training Fee payment through online payment system only i.e. epqv.hrtransporl.in. No physical cash transaction is allowed. 2. College / Institutes / Schools, General and Employees Bus Pass Payments to be processed online only on web addressi.e, epav.hrtransport.in. No physical cash transaction is allowed. 3. The collection of rented shops and other rented facilities at bus stands to be processed only on web address i.e. epov.hrtransport.in. No physical cash transaction is allowed. 1"he cornpliance report must be conveyed to this office within three days from the c1ate of this letter. -
Congress Participants
CONGRESS PARTICIPANTS "COMPAGNIA TRASPORTI LAZIALI" SOCIETÀ REGIONALE S.P. A. Italy 9292 - REISINFORMATIEGROEP B.V. Netherlands AB STORSTOCKHOLMS LOKALTRAFIK - STOCKHOLM PUBLIC TRANSPORT Sweden AB VOLVO Sweden ABB SCHWEIZ AG Switzerland ABG LOGISTICS Nigeria ABU DHABI DEPARTMENT OF TRANSPORT United Arab Emirates ACCENTURE Germany ACCENTURE Finland ACCENTURE Canada ACCENTURE Singapore ACCENTURE BRAZIL Brazil ACCENTURE BRISBANE Australia ACCENTURE SAS France ACTIA AUTOMOTIVE France ACTV SOCIETÀ PER AZIONI Italy ADDAX- ASSESORIA FINANCEIRA Brazil ADNKRONOS Italy ADV SPAZIO SRL Italy AESYS - RWH INTL. LTD Germany AGENCE BELGA Belgium AGENCE FRANCE PRESSE France AGENCE METROPOLITAINE DE TRANSPORT Canada AGENZIA CAMPANA PER LA MOBILITÀ SOSTENIBILE Italy AGENZIA ESTE NEWS Italy AGENZIA MOBILITA E AMBIENTE E TERRITORIO S.R.L. Italy AGENZIA PER LA MOBILITÀ ED IL TRASPORTO PUBBLICO LOCALE DI MODENA S.P.A. Italy AGETRANSP Brazil AIT AUSTRIAN INSTITUTE OF TECHNOLOGY GMBH Austria AJUNTAMENT DE BARCELONA Spain AKERSHUS FYLKESKOMMUNE - AKERSHUS COUNTY COUNCIL Norway AL AHRAME Egypt AL FAHIM United Arab Emirates AL FUTTAIM MOTORS United Arab Emirates AL RAI MEDIA GROUP-AL RAI NEWSPAPER Kuwait ALBERT - LUDWIGS - UNIVERSITÄT FREIBURG INSTITUT FÜR VERKEHRSWISSENSCH Germany ALCOA WHEEL AND TRANSPORTATION PRODUCTS Hungary ALEXANDER DENNIS LIMITED United Kingdom ALEXANDER DENNIS Ltd United Kingdom ALLINNOVE Canada ALMATY METRO Kazakhstan ALMATYELECTROTRANS Kazakhstan ALMAVIVA SPA Italy ALSTOM France ALSTOM MAROC S.A. Morocco AMBIENTE EUROPA Italy AMERICAN PUBLIC TRANSPORTATION ASSOCIATION USA ANDHRA PRADESH STATE ROAD TRANSPORT CORPORATION India APAM ESERCIZIO S.P.A. Italy ARAB UNION OF LAND TRANSPORT Jordan AREA METROPOLITANA DE BARCELONA Spain AREP VILLE France ARIA TRANSPORT SERVICES USA ARRIVA (ESSA ALDOSARI) United Arab Emirates ARRIVA ITALIA S.R.L. -
Haryana Roadways Engineering Corporation.Ltd., Gurgaon
Haryana Roadways Engineering Corporation.Ltd., Gurgaon 6th Milestone Delhi-Jaipur Highway Behrampur road Khandsa, Gurgaon Phone - 0124-2215660, 2215389 E-mail: [email protected] NOTICE INVITING E-TENDER Online E-tenders are hereby invited for the following store materials for fabrication of bus bodies: Sr. Name of Group/Item Approx value EMD Value Sources of Purchase No. (Rs. In lacs) (Rs. In lacs) 1 Mig Wire 0.8mm 25.00 0.50 M/s ESAB India Ltd. or M/s Ador Welding or their authorized dealer or distributors, M/s Maruti Weld, M/s Varun Electrodes Pvt. Ltd., M/s GEE Ltd. 2 Perforated Polythene etc. 04.00 0.08 Manufacturer/General Supplier 3 . Mig Welding Spare Parts 03.00 0.06 M/s L& T Ltd. OR their authorized of L & T make. deal ers/distri butors. 4 Synthetic Based Rubber 03.00 0.06 M/s Piddilite Industries Ltd./M/s Adhesive. Polygel Technologies India Pvt. Ltd. OR their authorized dealers/RC firms with ASRTU. 5 Tinted Toughened 16.00 0.32 Firm should have current rate Glass 5mm thickness contract with ASRTU or Dark Green and manufacture having in house Toughened Glass clear facility of Horizontal Toughening 5 mm. Plant and ISO 9001 meeting specification No.. IS;2553:1992 tt i' axirli 6 Water Proof Paper and 05.00 • 0.10 Authorized dealers/distributors of M/s Sandor'Disc etc. ' Carborandum Universal/Mico Bosch make. 7 Electric Welding Rod 09.50 0.19 M/s ESAB India Ltd. or M/s Ador 3.15mm'x 350mm Welding or their, authorized dealer or distributors, M/s Maruti Weld, M/s Varun Electrodes Pvt. -
Chapter VI BANKING, TRADE and COMMERCE
Chapter VI BANKING, TRADE AND COMMERCE INDIG ENOU S BA NKING Indigenous banking, as elsewhere, is done by individual bankers in towns and money-lenders (sahukars) in villages. The former receive de - posits , deal in hundis and also finance trade and industry against the security of goods. They are quite particular about the purpose s for which they advance lo ans . The money-lenders in villages mainly finance con sumption . Despite thi s difference, their operations are very similar . Functioning in an un- organised manner , they have adapted themselves to the customs, habits and needs of their local clients . Their business, being hereditary, is often carried on as a family concern. They generally rely on their own resources and, if necessary, borrow money from one another and even from joint-stock banks by re-discounting hundis. As the banks impose rigid conditions , these indigenous agencies do not often resort to them . The bazaar hundis rate (i .e. the rate at which indigenous bankers discount hundis) is invariably different from the bank rate. The village economy being traditionally controlled by the sahukar, the poor peasantry was at his mercy for all their financial needs. As a shopkeeper the sahukar preferred to have a lien on the agricultural produce . He could in this way profit twice, once by buying cheaply from the producer to whom he had lent money , and then by selling it at a higher rate to indi- vidual consumers or in a mandi . After 1870, when land became a profitable investment, the sahukar began to tighten his financial hold in such a way as eventually to oust the rural debtors from their lands. -
Download Full Length Paper
International Journal of Research in Social Sciences Vol. 11 Issue 03, March 2021 ISSN: 2249-2496 Impact Factor: 7.081 Journal Homepage: http://www.ijmra.us, Email: [email protected] Double-Blind Peer Reviewed Refereed Open Access International Journal - Included in the International Serial Directories Indexed & Listed at: Ulrich's Periodicals Directory ©, U.S.A., Open J-Gate as well as in Cabell’s Directories of Publishing Opportunities, U.S.A Performance Analysis of State Transport Undertaking: A Study of Haryana Devinder S Hooda NitishaSehrawat Abstract Haryana Roadways bus transport has been operated by the Haryana Government to meet the need of Public Road Transport in Haryana. The mission of Haryana Roadways is to surpass and robustness for public transportation services for rural and urban areas in state. The important objective of the study is to assess the performance of Haryana Roadways by firstly performance indicators are classified into categories and evaluate the overall performance and Depot- wise performance of Haryana Roadways.This study has taken some important indicators to measure the performance of depot, through these indictors it has been found that which area need more work. The accident rate was -3.28 in Haryana, which indicates that due to development of roads, trained staff, newly buses on road and proper maintenance of old buses the number of accident has been reduced. In Haryana the consumption of fuel has been growing only by 0.12% rate. This is also a very good sign for the performance. No significant fluctuations in consumption of fuel have been spotted among Haryana Roadways buses.Out of the 20 depots Bhiwani depot performed best, total receipts have shown highest growth rate and the total expenditure was lowest for this depot, in contrary to Ambala depot whose performance was worst. -
Rain Carts of the Canal Villages of Sonipat
CHAPTER vn COMMUNICATIQNS ROAD AND ROAD TRANSPORT ROADS A cross road line of importance runs from. Kharkhoda. going eastward . to Bhagpat. Some of the heaviest traffic of'the country.side.Iay.in.the cotton, gUT, and grain carts of the canal villages of Sonipat. The cross-country lines of road in that part of tahsil were often soft andtutt¥ ;often eut"lltY by wrong-headed water-courses and it was very difficult to. cress, them during the rainy season. Besides Grand Trunk Road (Sher Shah SUJ'iMilrgfrom Delhi towards Sonipat), the following table shows the important means of communicatioris (roads/routes) in the Sonipat area :- Route Halting Place ltemarks '\ \ Delhi to 1~ Rai Police bungalow and. enaamping Karnal ground Larsauli Ditto Rai to i Sonipat j Sonip3;.t Police bungalow Besides, a small list of unmetalled (roads ·l883-84)in tbeSonipattarea is given below-r-> Un metalled roads 'uttgtli (Miles) 1. Sonipat to Maniarpur ferry 11 2. Kharkhoda via Thana KaJan to Bhagpat 18 3. Sonipat to Bhagpat 12 4. Badli to Zafarpur via Sonipat 29 By 1912, there was some improvement in the roads. In addition to G.T. Road. Delhi city was also connected by a metalled road -Sonipat- Khar khoda. The position of the metalled roads in the Gohana area was not so satisfactory. The metalled roads were .Gohana-Rohtak (20 miles); Sampla- Kharkhoda-Sonipat (I8 miles); Rohtak-Kharkhoda and from Gohana to Mcham Kharkhoda and Safidon. 1. Delhi District Gazetteer, 1883-84, p. 144. 186 COMMUNICATIONS 1 187 All 'the roads were usually in-very faiJ'06ooitioo'aoo easy fQt' the traffic '~'OOurrtry carts-exaepttUter heavy- rain. -
HARYANA MASS RAPID TRANSPORT CORPORATION LIMITED Regd. Office
HARYANA MASS RAPID TRANSPORT CORPORATION LIMITED Regd. Office: C-3 Sector 6, PANCHKULA –134109. E-mail: [email protected] Website: www.hmrtc.org.in AGENDA FOR 41st MEETING (CONFIDENTIAL) DATE FEBRUARY 24TH, 2020 TIME 11:00 AM VENUE Main Committee Room, 4th floor, Haryana Civil Secretariat, Chandigarh. AGENDA FOR THE 41st MEETING OF THE BOARD OF DIRECTORS OF HMRTC. Day & Date Monday, February 24th, 2020 Time 11:00 AM th Venue Main Committee Room, 4 floor, Haryana Civil Secretariat, Chandigarh. INDEX Agenda Subject Page No. Item No. 1. To grant leave of absence to the Directors. 3 2. Confirmation of minutes of the 40th Board Meeting of HMRTC held 4-8 on 30.10.2019. 3. Follow up action on the decisions taken in the 40th Board Meeting 9-12 of HMRTC held on 30.10.2019. 4. Cessation of Sh. Devender Singh, IAS the then Additional Chief 13 Secretary to Govt. of Haryana, Industries & Commerce. 5. Appointment of Sh.Varinder Singh Kundu, IAS, Chief Executive 14 Officer, Gurugram Metropolitan Development Authority as Director of HMRTC. 6. Appointment of Sh.Siddhi Nath Roy, IAS, Additional Chief 15 Secretary to govt. of Haryana Urban Local Bodies as Director of HMRTC. 7. Appointment of Sh.Rajeev Arora, IAS, Additional Chief Secretary 16 PW(B&R) Department as Director of HMRTC. 8. Appointment of Sh.Anurag Aggarwal, IAS, HSIIDC Department as 17 Director of HMRTC 9. Appointment of Sh.Pankaj Yadav, IAS, Chief Administrator, HSVP- 18 cum-MD, HMRTC as Director of HMRTC. 10. Adoption of CAG report for the Financial year ending 31st March, 19-22 2019. -
Need of Public Transport in Gurugram
MID TERM REVIEW URBAN MOBILITY INDIA CONFERENCE PUBLIC TRANSPORT IN GURUGRAM City Bus Service Usha Kiran, Senior Town Planner, Urban Local Bodies Department, Haryana, Panchkula Public TransPorT in GuruGram - backGround Gurugram is a glaring example of urban growth. It has experienced growth spurt both spatially and demographically. With this sharp spurt in its population and Urban Sprawl there is need to introduce Public Transport. Planning perspective: Population Growth of Gurugram City The first Development Plan for the Gurugaon was notified in 1600000 the year 1995 for the year of 2001. 1400000 In year 2007 the Development Plan for the year 2021 was 1200000 notified 1000000 In year 2011 the Development Plan for the year 2025 was notified 800000 In year 2012 the Development Plan for the year 2031 was 600000 notified 400000 Since there is a rapid increase in the population growth as well as 200000 VisionAeral growth& Missionof Gurugram: from 1995 to 2011 and to cater the 0 demand in the planned manner, the development plans were 1961 1971 1981 1991 2001 2011 To move the people through Public Transport and decrease notified at different interval. the number of private vehicle from the road. Year Population To provide High Level of Infrastructure to the citizen. Goals and Objectives: To provide better and reliable source of Public Transport in terms of City bus and Metro. To change the mode of travel from private vehicle to Public Transport. Areal Growth of Gurugram 300 250 Kms 200 150 100 50 Area in Sq. Area 0 1981 1991 2001 2011 Public TransPorT in GuruGram - ciTy imaGes IT- Hub- Gurugram Industrial Estate- Manaser Water logging on roads of Gurugram and unsafe, overcrowded informal public transport Public TransPorT in GuruGram – exisTinG siTuaTion As already mentioned in the previous slide that Gurugram has experienced high rate of population as well as areal growth. -
Comparative Study Between Rajasthan State Road Transport Corporation and Haryana Roadways: Exploring Reason for Loss of Rajasthan State Road Transport Corporation
Volume 3, Issue 2, February– 2018 International Journal of Innovative Science and Research Technology ISSN No:-2456 –2165 Comparative Study between Rajasthan State Road Transport Corporation and Haryana Roadways: Exploring Reason for Loss of Rajasthan State Road Transport Corporation A. Harshit Jalan1 1Student, B.A. Honors (Economics), Manipal University Jaipur IJISRT18FB59 www.ijisrt.com 184 Volume 3, Issue 2, February – 2018 International Journal of Innovative Science and Research Technology ISSN No:-2456 –2165 SUMMARY Road Transport plays a vital role in development of any economy. In developing countries like India having a road, rail network is about 468882 km and 115000 km respectively shows the importance of road network in India.Rajasthan State Road Transport Undertakings and Haryana State Road Transport Undertakings are providing mobility to passenger in Rajasthan and Haryana by offering Various Services. But competition in these services itself makes these projects loss making. There are various variables for which people prefer one service over another. Haryana Roadways is profit making where as Rajasthan Roadways is making huge losses. As these are government undertaking so they remains backward as compared with private ones. Services like regular maintenance and up gradation are not possible in government undertaking so people prefer private ones. Haryana Roadways has given freedom to its drivers to decrease level in daily management. In this study a public opinion survey is carried out for finding service quality of both -
Government of Haryana Revenue & Disaster Management Department
Government of Haryana Revenue & Disaster Management Department DISTRICT DISASTER MANAGEMENT PLAN FARIDABAD 2017 Table of Contents 1 Introduction .................................................................................................................................. 1 1.1 History .............................................................................................................................................1 1.2 General Information .........................................................................................................................1 1.3 Administration .................................................................................................................................1 1.4 Location ...........................................................................................................................................2 1.5 Area..................................................................................................................................................2 1.6 Topography ......................................................................................................................................2 1.7 Drainage ...........................................................................................................................................2 1.8 Soil ...................................................................................................................................................2 1.9 Ground Water...................................................................................................................................2 -
Urban Mobility Regulatory Reforms in India April 2019
URBAN MOBILITY REGULATORY REFORMS IN INDIA APRIL 2019 SUSTAINABLE ENERGY FOUNDATION MP Ensystems Advisory Private Limited Shakti Sustainable Energy Foundation Report on “Urban Mobility Regulatory Reform in India”. Citation: Mahesh Patankar, Ira Prem, MP Ensystems Advisory (2019) About MP Ensystems MP Ensystems Advisory Private Limited (www.mpensystems.com) is a niche energy and environmental sector consultancy and advisory firm providing a bridge between policy-making and clean energy project implementation About Shakti Sustainable Energy Foundation Shakti Sustainable Energy Foundation works to strengthen the energy security of India by aiding the design and implementation of policies that support renewable energy, energy efficiency and sustainable transport solutions. Disclaimer The views and analysis expressed in this report do not necessarily reflect the views of Shakti Sustainable Energy Foundation. The Foundation also does not guarantee the accuracy of any data included in this publication nor does it accept any responsibility for the consequences of its use. Contents Executive Summary .................................................................................................................... 4 Project Team .............................................................................................................................. 5 Acknowledgements .................................................................................................................... 5 Abbreviations ............................................................................................................................ -
Free Travelling 28 02 2018.Pdf
gfj;k.kk jkT; ifjogu dh clksa esa eq¶r rFkk fj;k;rh ;k=k dh lqfo/kk dh Js.kh vuqlkj lwph d- e qQr ;k=k lqfo/kk dh Js.kh Øa- Js.kh Lohd`fr la[;k vkSj la- fnukad 1 LorU=rk lsukuh 2/SPL/CA2/L&B/Supdt lkaln ,oa HkwriwoZ lkaln dt.25.04.1986 2 2/86/97-POI(IP) dt.23.11.1987 3 fo/kk;d ,oa HkwriwoZ fo/kk;d 2142/CA2/L&B dt.28.4.1986 LorU=rk lsukfu;ksa dh fo/kok;sa 4. 14/11/84-3T(II) dt. 28.02.94 14/11/89-4T dt. 29.09.1989 5. vU/ks O;fDr dks lEcfU/kr mik;qDr }kjk tkjh 1913-1924/CA-4/L&B DT. dt.12.10.1982 igpku i= ds vk/kkj ij 6 laokn~nkrk @i=dkj & ftudh ;k=k ,d o’kZ esa dt. 26.04.93 19-07-2007 ls 2500 ls 4000 fdyksehVj rd c<+k nh xbZ gS 7 19-07-2007 ls 285 MSDl i=dkj o izSl “kk[kk ds dt. 30.04.2001 30 deZpkjh dh ;k=k 1500 ls 2500 fdyksehVj rd c<+k nh xbZ gS 8 Okg lHkh ys[kd ftUgsa gfj;k.kk jkT; }kjk mnqZ] 19/1/97-2T(II) dt. 5.02.2002 fgUnh] laLd`r ,oa iatkch lkfgR; ds fy;s lEekfur fd;k x;k gSA 9 lEekfur QksYd dykdkj dt. 21.03.2002 10 FkSyhf”kfea;k jksxh ,d lgk;d ds lkFk dt.