Also in This Issue
Total Page:16
File Type:pdf, Size:1020Kb
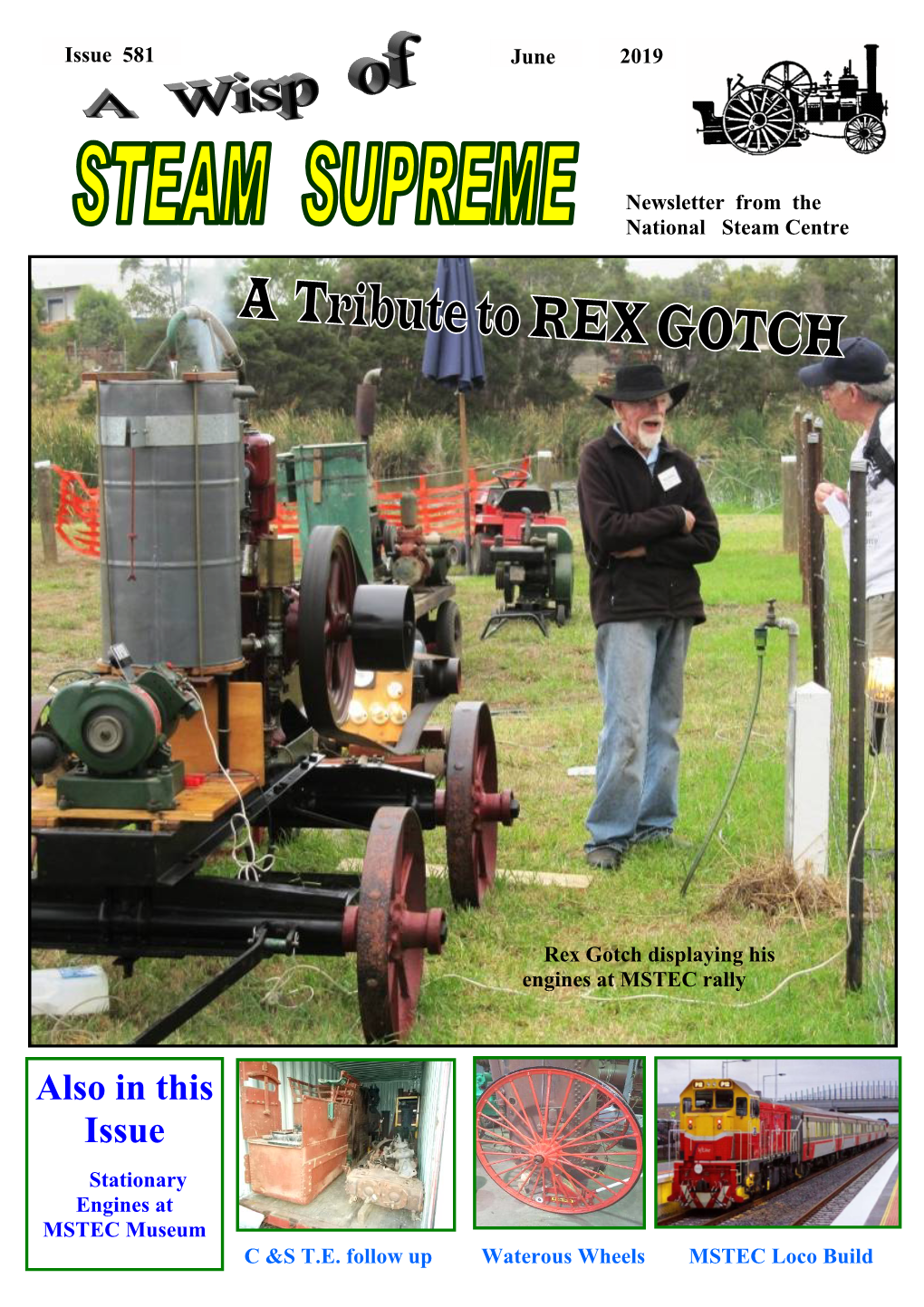
Load more
Recommended publications
-
Diesel and Fuel-Oil Engines
HdiiUiiat uuioTAt* VI i nPicrence moK not to do AUG 2 ^ : , CuKCH JlUili lilO L, iDi slil CS102E-42 Jf' Engines, Diese! and fuei-oil (export classifications) U. S. DEPARTMENT OF COMMERCE JESSE H. JONES, Secretary NATIONAL BUREAU OF STANDARDS LYMAN J. BRIGGS, Director DIESEL AND FUEL-OIL ENGINES (Export Classifications) COMMERCIAL STANDARD CS102E-42 Effective Date for New Production from October 30, 1942 A RECORDED VOLUNTARY STANDARD OF THE TRADE UNITED STATES GOVERNMENT PRINTING OFFICE WASHINGTON : 1942 For sale by the Superintendent of Documents, Washington, D. C. Price 10 cents . U. S. Department of Commerce National Bureau of Standard? PROMULGATION of COMMERCIAL STANDARD CS102E-42 for DIESEL AND FUEL-OIL ENGINES (Export Classifications) On January 30, 1942, at the instance of the Diesel Engine Manu- facturers’ Association, a conference of representative manufacturers adopted a recommended commercial standard for Diesel and fuel -oil engines (export classifications). Those concerned have since accepted and approved the standard as shown herein for promulgation by the U. S. Department of Commerce, through the National Bureau of Standards. The standard is effective for new production from October 30, 1942. Promulgation recommended I. J. Fairchild, Chieff Division of Trade Standards, Promulgated. Lyman J. Briggs, Director^ National Bureau of Standards, Promulgation approved. Jesse H. Jones, Secretary of Commerce. II DIESEL AND FUEL-OIL ENGINES (Export Classifications) COMMERCIAL STANDARD CS102E-42 PARTS Page 1. Nomenclature and definitions.. ' 1 2. Slow- and medium-speed stationary Diesel engines 7 3. Slow- and medium-speed marine Diesel engines 13 4. Small, medium- and high-speed stationary, marine, and portable Diesel engines 19 5. -
Absolute Auction Complete Liquidation by Order of Trustee
ABSOLUTE AUCTION COMPLETE LIQUIDATION BY ORDER OF TRUSTEE `04 BERCO RTM225A-BS WEDNESDAY, DECEMBER 5, 2012 9:00 AM Altoona-Beasley Altoona, Pennsylvania Manufacturing, Inc. 1440 COWPATH RD. • HATFIELD, PA 19440 `00 BERCO 225A-40 `03 SERDI 100HD `04 FORD F-550XL SUPER DUTY 215/361-9099 • Fax: 215/361-9212 www.hunyady.com PRE-SORTED FIRST CLASS MAIL US POSTAGE PAID HAVERTOWN, PA PERMIT #45 ABSOLUTE AUCTION Altoona-Beasley Manufacturing, Inc. Notice: Pursuant to U.S. Bankruptcy Court Case #10-71091 and by Order of Trustee all equipment assets formerly owned and operated by Altoona-Beasley Manufacturing, Inc. shall be liquidated. All items must sell to the highest bidder without minimums, reserves, or buyer’s premiums! Location: The auction will be held at the Altoona-Beasley facility at 210 East Plank Road, Altoona, Pennsylvania 16602 Dismantlement and Loadout: Certain machines will be required to be dismantled and loaded out by a qualified rigger for safety purposes. Loadout fees will be added to the purchaser’s invoice. One rigger will be selected and must be used. No other contractors will be permitted. Individual fees will be published in the sale day catalog. Items not requiring professional rigging will be loaded by the auction company at no charge! Sale Site Directions: FROM INTERSTATE 99 SOUTH BOUND: Exit #32 (Frankstown Road) End of ramp at traffic light turn left onto Frankstown Road. Proceed to second traffic light and turn left onto Plank Road. Sale site will be on immediate right. FROM INTERSTATE 99 NORTH BOUND: Exit #32 (Frankstown Road) End of ramp at traffic light turn right onto Frankstown Road. -
Portable Diesel IC Engine
SAN DIEGO AIR POLLUTION CONTROL DISTRICT 10124 OLD GROVE ROAD, SAN DIEGO, CA 92131-1649 PHONE (858) 586-2600 • FAX (858) 586-2601 CERTIFICATE OF COMPLIANCE & San Diego APCD Use Only CERTIFICATE OF REGISTRATION APP/Reg. No.: RULE 12.1 ID No.: BEC/FS: APCD2019-CON-001560/34X Existing P/O No.: Portable Diesel Internal Combustion (New) for Emergency or Low Use Only Name of Owner (DBA): Legal Owner (if different from DBA): Equipment Description: Year: Manufacturer: Model No.: Serial No.: HP Rating: Type of Fuel: : Engine Use: ☐Emergency Engine or ☐Low-Use Engine (less than 200 hours per year) I, ________________________ , certify that I will be in compliance with all applicable District Rules and Regulations and the following conditions: (Print or type name) 1. If designated as an Emergency Engine in the above equipment description, the engine shall be operated exclusively in emergency applications except for up to 50 hours per year for maintenance and testing. If designated as a Low-Use Engine in the above equipment description, the engine shall be operated 200 hours or less each calendar year. (17CCR 93116) 2. Emissions from each registered engine shall not exceed 100 pounds of oxides of nitrogen (NOx) during any one day. [Rule 12.1(d)(1)] 3. An engine or equipment unit shall be configured and operated so as to meet the definition of a portable emission unit as defined in Rule 12.1. An engine's and/or equipment unit's certificate of registration shall be invalid when such equipment is used as an integral part of the operation of a stationary source or to supplement or expand the stationary source's operation. -
16425- Portable Generators
MDWASD 12/2006 SECTION 16425 PORTABLE ENGINE-GENERATOR SETS PART 1 - GENERAL 1.01 REQUIREMENT Furnish and install a portable engine-generator system for use during periods of interruption of normal electrical service. 1.02 SUBMITTALS The Contractor shall submit all applicable submittals listed in Section 16420. 1.03 QUALITY ASSURANCE A. In the best interest of the Miami-Dade Water and Sewer Department, the supplier of this equipment shall maintain a full-time "in-house" parts and service organization within 50 miles of the job site. Equipment offered by those who do not have an "in house" parts and service organization and who depend on others to provide services shall not be considered. This supplier shall have his name, address and telephone number clearly and visibly located on all equipment. Service shall be available on a 24-hour/7-day a week basis. B. The supplier of the equipment shall provide information and/or supervision required for the proper installation of the equipment, testing of equipment and training of operating personnel. C. All components shall bear UL labels. D. The stand-by system, including the generator set and associated controls shall be designed, fabricated, tested and furnished by one manufacturer to assure one source of responsibility. The manufacturer shall have been regularly engaged in the production of engine-alternator sets and associated controls for a minimum of five years and shall manufacture either the engine, or the generator or both. 1.04 GUARANTEE The equipment furnished under this Specification shall be new, unused, of the latest design. The generator set, associated controls, and automatic load transfer switch shall be warranted for a minimum of five years or 1,500 operating hours whichever comes first. -
PORTABLE ENGINE INFORMATION Portable Means Designed and Capable of Being Carried Or Moved from One Location to Another
110 Maple Street, Auburn, CA 95603 (530) 745-2330 Fax (530) 745-2373 www.placer.ca.gov/apcd Erik C. White, Air Pollution Control Officer APPLICATION FOR CERTIFICATE OF REGISTRATION COMPRESSION IGNITION ENGINES USED IN AGRICULTURAL OPERATIONS FORM 3 – PORTABLE ENGINE INFORMATION Portable means designed and capable of being carried or moved from one location to another. Indicia of portability include, but are not limited to, wheels, skids, carrying handles, dolly, trailer, or platform. For purposes of registration, a portable engine must be used exclusively at agricultural sources under common ownership. Engines not considered portable include engines that operate at one location on a seasonal basis and engines that will remain at one location for more than 12 (twelve) months. For engines that are not considered portable, please complete FORM 2 – Stationary Engine Information Note: Tractor and truck engines used to drive / propel mobile equipment and vehicles are not subject to District registration requirements. Owner/Operator/Company Name: Engine Manufacturer: Model Number: Serial Number: Year of Engine Manufacture: ( or approximate age of engine) : Years Old Maximum Brake Horsepower Rating: Date of Installation: Tier “0” (non-certified / pre-1996) Tier 1 Tier 2 Tier 3 Tier 4 Engine Designation: ⃞ ⃞ ⃞ ⃞ ⃞ EPA/CARB Engine Family Number: ___________________________________________ Estimated Annual Hours of Operation: ⃞ CARB Diesel _______________ Gallons / Year Fuel Used and Estimated Amount: ⃞ Biodiesel (specify blend): ______________ -
Guide to Off-Road Vehicle & Equipment Regulations
Guide to Off-Road Vehicle & Equipment Regulations The California Air Resources Board (CARB) is actively enforcing off-road diesel and large spark-ignition engine vehicle and equipment regulations in support of California’s clean air goals. Enforcement of clean off-road vehicle rules provides a level playing field for those who have already done their part and are in compliance. If your fleet does not meet state clean air laws, you could be subject to fines. This booklet provides basic information and resources to help take the guesswork out of California’s clean off-road vehicle and equipment requirements. This booklet is not comprehensive of all CARB regulations that an off-road fleet may be subject to, but provides basic information specific to the following: • Regulation for In-Use Off-Road Diesel-Fueled Fleets • Large Spark-Ignition Engine Fleet Requirements Regulation • Portable Equipment Registration Program DISCLAIMER While this booklet is intended to assist vehicle owners with their compliance efforts, it is the sole responsibility of fleets to ensure compliance with applicable regulations. For more information or assistance with compliance options, visit arb.ca.gov/offroadzone, call the toll-free hotline at (877) 59DOORS (877-593-6677), or email at [email protected]. Table of Contents What off-road vehicle and equipment rules may apply to you? 1 Regulation for In-Use Off-Road Diesel-Fueled Fleets 2 Basic Reporting 3 Reporting – Initial & Annual 3 Labeling 3 Emission Performance Compliance Options 4 Meeting the Fleet Average Target -
Steam Engines of Which We Have Any Knowledge Were
A T H OROUGH AND PR ACT I CAL PR ESENT AT I ON OF MODER N ST EAM ENGI NE PR ACT I CE LLEWELLY DY N . I U M . E . V i P O F S S O O F X P M L G G P U DU U V S Y R E R E ERI ENTA EN INEERIN , R E NI ER IT AM ERICAN S O CIETY O F M ECH ANI C A L EN G INEERS I LL US T RA T ED AM ER ICA N T ECH N ICA L SOCIET Y C H ICAGO 19 17 CO PY GH 19 12 19 17 B Y RI T , , , AM ER ICA N T ECH N ICAL SOCIET Y CO PY RIG H TE D IN G REAT B RITAI N A L L RIGH TS RE S ERV E D 4 8 1 8 9 6 "GI. A INT RO DUCT IO N n m n ne w e e b e the ma es o ss H E moder stea e gi , h th r it j tic C rli , which so silently o pe rates the m assive e le ctric generators in f r mun a owe an s o r the an o o mo e w one o ou icip l p r pl t , gi t l c tiv hich t m es an o u omman s our uns n e pulls the Limited a sixty il h r , c d ti t d n And t e e m o emen is so f ee and e fe in admiratio . -
Steam Engine Collection
STEAM ENGINE COLLECTION The New England Museum of Wireless And Steam Frenchtown Road ~ East Greenwich, R.I. International Mechanical Engineering Heritage Collection Designated September 12, 1992 The American Society of Mechanical Engineers INTRODUCTION It has been said that an operating steam engine is ‘visual music’. The New England Museum of Wireless and Steam provides the steam engine enthusiast, the mechanical engineer and the public at large with an opportunity to experience the ‘music’ when the engines are in steam. At the same time they can appreciate the engineering skills of those who designed the engines. The New England Museum of Wireless and Steam is unusual among museums in its focus on one aspect of mechanical engineering history, namely, the history of the steam engine. It is especially rich in engines manufactured in Rhode Island, a state which has had an influence on the history of the steam engine in the United States out of all proportion to its size and population. Many of the great names in the design and manufacture of steam engines received their training in Rhode Island, most particularly in the shops of the Corliss Steam Engine Co. in Providence. George H. Corliss, an important contributor to steam engine technology, founded his company in Providence in 1846. Engines that used his patent valve gear were built in large numbers by the Corliss company, and by others, both in the United States and abroad, either under license or in various modified forms once the Corliss patent expired in 1870. The New England Museum of Wireless and Steam is particularly fortunate in preserving an example of a Corliss engine built by the Corliss Steam Engine Company. -
A Handbook on the Steam Engine, with Especial Reference to Small And
ADVERTlSEMElfTS. i+t\\i JD, 3.E. YS. (YS, Tl sPOUS U ^rcacuteb to PI nd), of I tt of Toronto id). Professor E.A.Allcut AL. Is. Castings in Bronze, Brass and Gun and White Metals, Machined if required. ROLLED PHOSPHOR BRONZE, Strip and Sheet, for Air Pump Valves, Eccentric Strap Liners, etc. HIKE find TELEPHONE WIRE. AD VER TISEMENTS. THE PHOSPHOR BRONZE CO, LIMITED, 87, Sumner Street, Southwark, London, S.E. And at BIRMINGHAM. r "COG WHEEL" and Sole Makers of the j3S %jg "VULCAN" iSPI^flfiC Brands of The best and most durable Alloys for Slide Valves, Bearings, Bushes, Eccentric Straps, and other parts of Machinery exposed to friction and Piston Motor wear ; Pump Rods, Pumps, Rings, Pinions, Worm Wheels, Gearing, etc. "DURO METAL" (REGISTERED TRADE MARK). Alloy B, specially adapted for BEARINGS for HOT-NECK ROLLS. CASTINGS In BRONZE, BRASS, GUN and WHITE METALS, in the Rough, or Machined, if required. ROLLED AND DRAWN BRONZE, GERMAN SILVER, GUN METAL, TIN, WHITE METALS AND ALUMINIUM BRONZE ALLOYS PHOSPHOR TIN & PHOSPHOR COPPER, "Cog-Wheel" Brand. Please specify the Manufacture of THE PHOSPHOR BRONZE CO., Ltd., of Southwark, London. lii ADVERTISEMENTS, ROBEY & Co GLOBE WORKS, LINCOLN. Mod Compound Horizontal Fixed Engine, it.- 1 iiii I'.ii.-nt Ti-ip Kxitiimioii (ic:ir. tolnijthe limpl >nUit ml miTrt economical at uuv in tin- market, and working ;.|iei to the Newcastle-nil -Tvm .tit Station (MX large engines), also St. Helens mint lam. BrUbane Electric Tram- Open-front High-speed Vertical e, for electric lighting. All thete Engine* are specially Dengned and Adapted for Electric Lighting. -
The Newcomen Society
The Newcomen Society for the history of engineering and technology Welcome! This Index to volumes 1 to 32 of Transactions of the Newcomen Society is freely available as a PDF file for you to print out, if you wish. If you have found this page through the search engines, and are looking for more information on a topic, please visit our online archive (http://www.newcomen.com/archive.htm). You can perform the same search there, browse through our research papers, and then download full copies if you wish. By scrolling down this document, you will get an idea of the subjects covered in Transactions (volumes dating from 1920 to 1960 only), and on which pages specific information is to be found. The most recent volumes can be ordered (in paperback form) from the Newcomen Society Office. If you would like to find out more about the Newcomen Society, please visit our main website: http://www.newcomen.com. The Index to Transactions (Please scroll down) GENERAL INDEX Advertising puffs of early patentees, VI, 78 TRANSACTIONS, VOLS. I-XXXII Aeolipyle. Notes on the aeolipyle and the Marquis of Worcester's engine, by C.F.D. Marshall, XXIII, 133-4; of Philo of 1920-1960 Byzantium, 2*; of Hero of Alexandria, 11; 45-58* XVI, 4-5*; XXX, 15, 20 An asterisk denotes an illustrated article Aerodynamical laboratory, founding of, XXVII, 3 Aborn and Jackson, wood screw factory of, XXII, 84 Aeronautics. Notes on Sir George Cayley as a pioneer of aeronautics, paper J.E. Acceleration, Leonardo's experiments with Hodgson, 111, 69-89*; early navigable falling bodies, XXVIII, 117; trials of the balloons, 73: Cayley's work on airships, 75- G.E.R. -
Associated Engines Brief History of the Feature Tractors
August 2019 Greetings from the Board, Our 2018 show was another great success! A huge, heartfelt thanks to everyone who volunteered their time helping us set up for the show. Thank you to everyone who brought out displays and especially to those who had running displays. We had over 25 Massey tractors in our feature area, 14 steam engines running around, dozens of models in the office and a huge showing of Economy engines, over 200 I’ve been told! We moved the tractor pull to Saturday afternoon and ran up to dark. Great work everyone! This year our 49th annual show will feature the White family of tractors, which includes Oliver and Minneapolis- Moline. Our 2019 show will highlight Associated engines as well. We will again be hosting model engines, and due to their great success, they will be in building 17 to give them more room to expand. We will continue to hold the tractor pull on Saturday afternoon and along with the Lorain County Farm Bureau, we will be having a kiddie tractor pull on Sunday. We are pleased to announce that for 2020, our 50th Anniversary show, we will be having “Red vs. Green” for the featured tractors and equipment. This showing of International and John Deere should make for a great event. For the first time ever, we are going to have a feature in the steam engine area. “Ohio-built” engines will be taking center stage for our Golden Anniversary. And in our engine area, the Baker Manufacturing Company will be the headliner. We are currently looking for some ideas to make our 50th a memorable one. -
Portable Equipment Frequently Asked Questions
Portable Equipment Frequently Asked Questions Note: This document contains interpretations of the regulations applicable to portable engines in California Code of Regulations, title 13, division 3, chapter 9, article 5, section 2450, et seq., and title 17, division 3, chapter 1, subchapter 7.5, section 93100, et seq. These interpretations were prepared by CARB staff working in the Statewide Portable Equipment Registration Program (PERP), and is subject to change at any time. The interpretations provided in this document are, by necessity, general in nature and may not be applicable in all situations. This document is provided for the convenience of the regulated community and is not a regulation. In all circumstances, these interpretations are CARB’s staff’s reasonable construction of the text of the regulations, and in the event of any differences the regulatory text controls over this document. PERP Forms are provided for the convenience of the regulated community. Applicability 1. What is the Portable Equipment Registration Program (PERP)? The Portable Equipment Registration Program (PERP) is a voluntary statewide program to register portable equipment such as air compressors, generators, concrete pumps, tub grinders, wood chippers, water pumps, drill rigs, pile drivers, rock drills, abrasive blasters, aggregate screening and crushing plants, and concrete batch plants. With certain limited exceptions, including a determination by a local air district that a permit is required for operation at a given location, portable equipment registered in PERP may operate throughout the state without obtaining permits from any of California's 35 air quality management or air pollution control districts (air districts). 2. What types of equipment must be registered in PERP? Nothing is required to be registered in PERP.