RFP-NR-4850 Fire Pumper
Total Page:16
File Type:pdf, Size:1020Kb
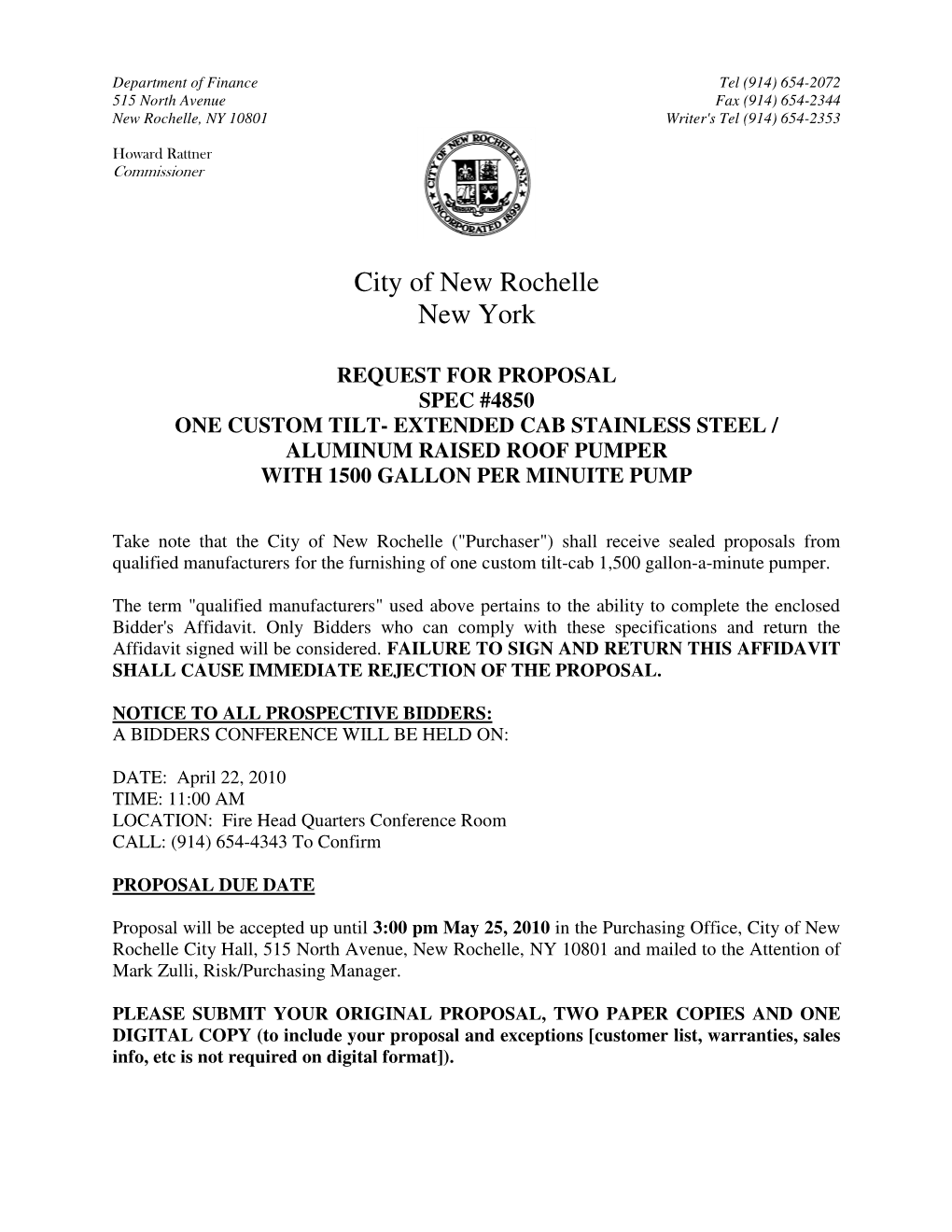
Load more
Recommended publications
-
Pdf Fire Services Final Report (1.74
To: Kelliann Dean, Deputy Minister, Department of Municipal Affairs Deputy Mayor Laurie Murley, President, UNSM Marie Walsh, President, AMANS Rod Nielsen President, Fire Services Association From: Fire Services Study Steering Committee Date: August 3, 2017 Re: Municipal Review of Fire Services in Nova Scotia As you are aware, the Union of Nova Scotia Municipalities and the Association of Municipal Administrators of Nova Scotia, with the financial support of the Province of Nova Scotia, engaged a consultant to facilitate a frank and open discussion on fire services. The consultant was asked to meet with representative stakeholders to ascertain and prioritize key issues at the local level, to consider opportunities to address these issues, and to facilitate the sharing of best practices, lessons learned and possible areas for collaboration. The work of the consultant was overseen by a Project Steering Committee comprised of representatives from UNSM, AMANS, the Fire Services Association and the Fire Marshal’s Office. The task of the Project Steering Committee was to select the consultant, to ensure the terms of reference were met and to facilitate the work of the consultant. Pomax Consulting was engaged to undertake the review. Their report is attached in Appendix B. Project Steering Committee Observations The Consultant has fulfilled the terms of reference. The Project Steering Committee recognizes the hard work of the consultant in documenting stakeholders’ views and concerns. The recommendations of the consultant make sense, in that the issues are complex and not solved by one group alone. The need to work together is paramount. During the stakeholder consultations, it became evident that there were varying degrees of understanding with respect to fire services in Nova Scotia, particularly around authority and areas of responsibility. -
One Year Later... Fire Fighters Honored at Memorial Service
November 2002 Vol 4, Issue 11 One Year Later... Fire Fighters Honored at Memorial Service Editor’s Note: With the memories of September 11, 2001 still vivid in Special Interest: our minds, Michigan’s fallen fire fighters were honored at the annual Michigan State Firemen’s Memorial in Roscommon on September 21. CPSC - Overfill Prevention Captain Mark Dougovito, State Fire Marshal, spoke at this year’s Devices ............................ 3 memorial service. His words so clearly illustrated what we all felt, and still feel, that we wanted to reprint his speech for those who did not NFPA Reports Drop in Home have an opportunity to attend the memorial. Fire Deaths ...................... 5 One year ago, many of you years from now, will see that MAPC Juvenile Arson stood on these hallowed same blank stare on their Capt. Mark A. Dougovito Conference ...................... 8 grounds, wondering what the children’s faces as they remember future would bring for our where they were and what they know that whatever happens, if MFFTC Web Site Links ... 11 nation, our state, and our were doing when the towers anything happens, the citizens of VIP Classes Offered ........ 11 families. The attack we all came down. this state are in good hands witnessed left us with an I know that’s going to happen, because of your dedication and emotional loss of such magni- because everybody standing devotion to duty. tude that we may never fully here today probably had a Last year, Captain Ed Burke recover. I know we will never flashback as I was just talking stood behind this same micro- forget. -
Jf R,}1/O)~ Iuty ·
FRANK T. MARTINEZ TY OF LOS ANGEL. Office of the City Clerk CALIFORNIA CITY CLERK Council and Public Services KAREN E. KALFAYAN Room 395, City Hall Executive Officer Los Angeles, CA 90012 Council File Information - (213) 978-1043 General Information - (213) 978-1133 When malting inquiries Fax: (213) 978-1040 relative to this matter refer to File No. HELEN GINSBURG ANTONIO R. VILLARAIGOSA Chief', Council and Public Services Division MAYOR 03-0814 November 9, 2005 City Administrative Officer Chief Legislative Analyst Information Technology Agency Fire Department RE: LOS ANGELES FIRE DEPARTMENT AMBULANCE BILLING PROCESS REVIEW AND OUTSOURCING ASSESSMENT BY BEARINGPOINT INC. At the meeting of the Council held October 26, 2005, the following action was taken: Attached reports adopted....................................... X Attached motion adopted() .......................... ············------ Attached resolution adopted() .................................. ______ Ordinance adopted .............................................. _______ Motion adopted to approve attached report ...................... ______ Motion adopted to approve attached communication ............... _______ To the Mayor FORTHWITH. X Ordinance Number ............................................... ------- Publication date .............................................. ·---~-- Effective date ................................................. ______ Mayor concurred. 11-0 7 - O5 Mayor failed to act - deemed approved .......................... ______ Findings adopted .............................................. -
2022 Revolving Loan Program
2022 Revolving Loan Program Ohio Department of Commerce Division of State Fire Marshal An Equal Opportunity Employer and Service Aug. 1, 2021 Re: 2022 Revolving Loan Program Dear Fire Chief, The Ohio Department of Commerce Division of State Fire Marshal is pleased to announce we are now accepting applications for the 2022 Revolving Loan Program. Loan applications must be postmarked no later than September 30, 2021 to be considered with an anticipated disbursement of January 2022. Please review the 2022 Revolving Loan Program Application package in its entirety. We have included helpful information to assist with completing the 2022 Revolving Loan Application and Approved Loan Worksheet. If you have any questions or require additional assistance, please contact Ashley Campbell, Program Administrator, at (800) 515-0023 or [email protected]. Complete information and forms can be found at: http://www.com.ohio.gov/fire Sincerely, Sheryl Maxfield Kevin Reardon Director, Ohio Department of Commerce State Fire Marshal Ohio State Fire Marshal 614 | 752 7161 8895 East Main Street Fax 614 | 752 7213 Reynoldsburg, OH 43068 U.S.A. TTY/TDD 800 | 750 0750 An Equal Opportunity Employer and Service Provider www.com.ohio.gov 2 Table of Contents 1. 2022 Revolving Loan Program Overview 4 2. Instructions for Completing 2022 Revolving Loan Application 7 3. 2022 Revolving Loan Program Application 10 4. Instructions for Completing Approved 2022 Loan Worksheet 14 5. Approved 2022 Loan Worksheet 15 6. 2022 Revolving Loan Program Scoring 16 7. Appendix A: OAC §1301:7-7-01(S), Ohio Fire Code 119, 17 Small Government Fire Department Services Revolving Loan Program 8. -
Annex F Fire Rescue Plan
ANNEX F Fire/Rescue and Hazardous Materials Table of Contents ANNEX F Fire/Rescue and Hazardous Materials Page I. Purpose F-3 II. Situation and Assumptions F-3 III. Concepts of Operation F-3 IV. Organization and Assignments of Responsibilities F-6 V. Direction and Control F-7 VI. Continuity of Government F-8 VII. Administration and Logistics F-8 VIII. Plan Development and Maintenance F-9 IX. Authorities and References F-10 X. Addendums F-10 MAY 2018, REVISED F-1 ANNEX F Fire/Rescue and Hazardous Materials Tabs Content Page Tab 1 Fire Departments in Trumbull County. F-11 Tab 2 Call Down List F-12 Tab3 Fire Operation Plan F-13 Tab 4 Ongoing Incident Assessment F-16 Tab 5 Levels of Response F-20 Tab 6 Levels of Protection F-22 Tab 7 Decontamination Procedures F-25 Tab 8 Operational Response Procedures F-28 Tab 9 Trumbull County Emergency Units F-30 Tab 10 Active Shooter Matrixes F-32 Tab 11 Bomb Threat/Incident Matrixes F-33 Tab 12 Fire Incident/Alarm Matrixes F-34 MAY 2018, REVISED F-2 ANNEX F Fire/Rescue and Hazardous Materials FIRE AND RESCUE I. PURPOSE This annex provides an organized presentation of Trumbull County’s firefighting, rescue, and hazardous materials response capabilities in the event of an emergency. Responsibilities for radiological defense are also addressed. Hazardous materials response is addressed in the Trumbull County Local Emergency Planning Committee in accordance with SARA, Title III Planning Criteria. II. SITUATION AND ASSUMPTIONS A. Situation 1. Fire, Rescue, and HAZMAT organizations in Trumbull County establish a primary command center when dealing with on-going emergencies. -
EMS in Illinois Inside This Special Issue
THE Winter 2015 IREIRE ALLALL FFan official Publication of the IllinoisCC Association of Fire Protection Districts Representing Fire Protection Districts throughout Illinois EMS in Illinois Inside this Special Issue: n Amicus Files to support Public Duty Rule n Rural Emergency Response HB 4523 n Roadway Safety Task Force SJR 0062 n Grain Bin Rescue Update Think you can’t aord a Horton? Think again. Too often do we hear potential customers say that they “can’t aord aHorton.” Based on a preconceived price notion, many reject Horton as an option before any detailed quote is actually provided. The quality, design, engineering and safety characteristics of a Horton have caused many to believe that our ambulance may be out of their budget. But with the introduction of our newest Pre-Engineered model, you “can’t aord NOT to own a Horton.” The Pre-Engineered series oers a unique opportunity for our customers to purchase a well-equipped Horton vehicle at an attractive price-point. All Pre-Engineered vehicles are tested to the same Horton standards and supported by an extensive service network. And because we believe safety shouldn't be an "upgrade option," our Pre-Engineered models come fully-equipped with HOPS. This exclusive safety system leverages airbags, 3-point seatbelts and progressive resistant foam to protect occupants during rollover crashes. Call today to learn more about a Horton Pre-Engineered model. See for yourself why you simply “can’t aord NOT to own a Horton!” FOSTERCOACH.COM 800.369.4215 IN THIS ISSUE FEA T URES THE Senate Joint Resolution Calls for Roadway FIRE CALL Safety Task Force ............................................... -
Information on Burning Within The
O K L A H O M A WILDLAND FIRE NOTES BURNING WITHIN THE OKLAHOMA LAW Oklahoma encompasses multiple fire-dependent ecosystems that rely on wildland fire effects to sustain native habitats and ecosystems. Careful application of fire enhances the vigor and resiliency of the varied ecosystems that support wildlife, agricultural grazing, hay production, wood products and water quality. Native Americans utilized fire to manage their environment for many of the same reasons to perpetuate the health of the land that sustained them. A longstanding trend of removing fire from fire-dependent ecosystems has left many areas in Oklahoma with suppressed habitat quality, change in cover type, declining environmental health and heightened risk of catastrophic wildfire. Utilization of fire can be a powerful, cost effective land management practice when properly implemented. Improperly applied fire can be a devastating force that destroys property and, in the worst case threatens both lives and livelihoods. Oklahoma Forestry Services promotes the responsible use of lawful burning to effectively manage wildlands across Oklahoma. Lawfully Burning in Oklahoma Open burning laws are detailed in Oklahoma Statutes Title 2, Section 16 which is known as the Oklahoma Forestry Code. To begin with, the following must be taken into consideration: 1. You are legally entitled to burn the property as an owner, authorized tenant or agent of the owner/authorized tenant. Statutory Reference: O.S. Title 2 § 16-24.1 2. You shall provide adequate firelines, sufficient manpower and firefighting equipment to contain your fire to the property you are authorized to burn and stay with the fire until it is extinguished. -
Canyon County, Idaho, All Hazards Mitigation Plan Volume II
Canyon County, Idaho, All Hazards Mitigation Plan Including the municipalities of Nampa, Caldwell, Middleton, Notus, Parma, Wilder, Greenleaf, & Melba 222000000666 UUUpppdddaaattteee Volume II Canyon County Wildland-Urban Interface Wildfire Mitigation Plan FFFEEEMMMAAA PPPrrreee---AAAdddoooppptttiiiooonnn RRReeevvviiieeewww JJJuuunnneee 222666,,, 222000000666 Vision: Promote a countywide hazard mitigation ethic through leadership, professionalism, and excellence, leading the way to a safe, sustainable Canyon County. This plan was developed by the Canyon County Wildland-Urban Interface Wildfire Mitigation Plan Committee and All Hazard Mitigation Plan Committee in cooperation with Northwest Management, Inc., 233 E. Palouse River Dr. P.O. Box 9748, Moscow, Idaho 83843, Phone: (208) 883-4488, Fax: (208) 883-1098, www.Consulting-Foresters.com Acknowledgments This Wildland Urban Interface Wildfire Mitigation Plan represents the efforts and cooperation of a number of organizations and agencies, through the commitment of people working together to improve preparedness for wildfire events while reducing factors of risk. Southwest Idaho Resource Canyon County Commissioners USDI Bureau of Land Management Conservation and Development and the employees of Canyon County Council, Inc. Idaho Bureau of Homeland Federal Emergency Management USDI Bureau of Reclamation Security Agency USDA Forest Idaho Transportation USDI Fish and Idaho Department Idaho Fish and Game Service Department Wildlife Service of Lands City of Notus City of Greenleaf City of Wilder -
Chemung County Fire Services Study
CHEMUNG COUNTY, NEW YORK COUNTY-WIDE FIRE SERVICES STUDY FEBRUARY 2010 THIS DOCUMENT WAS PREPARED WITH FUNDS PROVIDED BY THE NEW YORK STATE DEPARTMENT OF STATE MUNICIPAL SERVICES INCENTIVE GRANT PROGRAM. MMA CONSULTING GROUP, INC. 1330 BEACON STREET BROOKLINE, MASSACHUSETTS 02446 CHEMUNG COUNTY, NEW YORK CONTENTS I. EXECUTIVE SUMMARY 1 II. SCOPE OF THE STUDY 19 III. BACKGROUND AND DEMAND FOR SERVICES 22 IV. COUNTY-WIDE FIRE AND RESCUE COORDINATION 41 V. MEASURING CAPABILITY AND PERFORMANCE 54 VI. RESPONSE CAPABILITY, COMPUTER MAPPING & RESPONSE OBJECTIVES 62 VII. REORGANIZING FIRE DEPARTMENT DISTRICTS 73 VIII. ADMINISTRATIVE SUPPORT SERVICES 101 IX. APPARATUS FLEET AND REPLACEMENT GUIDELINES 105 X. IMPLEMENTATION OF RECOMMENDATIONS 110 XI. FUTURE FIRE/RESCUE PROTECTION NEEDS IN CHEMUNG COUNTY 123 MMA CONSULTING GROUP, INC. CHEMUNG COUNTY, NEW YORK I. EXECUTIVE SUMMARY This County-Wide Fire Services Study was conducted by MMA Consulting Group, Inc., and assesses current services and identifies methods to improve service delivery. There are 20 fire departments in Chemung County; one fire department has recently deactivated. Eighteen of the remaining 19 fire departments are volunteer fire departments; the City of Elmira has a career fire department. Several volunteer fire departments supplement their volunteer response by employing part-time personnel or a small number of full-time personnel. In addition to the city fire department, there are village fire departments, fire districts and fire protection districts in the County. The fire departments respond to approximately 6,500 calls for service annually. Approximately eight percent of calls are fire calls (building, vehicle, and other fires); 62 percent are emergency medical services (EMS) calls; and 30 percent are other types of calls. -
Firefighters: Feeling the Heat — Fabienne Scandella Researcher, European Trade Union Institute Acknowledgements
Firefighters: feeling the heat — Fabienne Scandella Researcher, European Trade Union Institute Acknowledgements Sincere thanks go out to the European firefighters’ union reps for their knowledgeable input to the conferences held in Vienna in 2010 and Elewijt in 2011 which informed this booklet. Special thanks go to Ronald Plasman, Adjutant with the Braine-L'Alleud (Belgium) Fire Service and representative of the Free Trade Union of Public Employees. His commitment to his fellow firefighters’ health and safety, his expertise, experience and engagement with this project, have been invaluable resources in writing this booklet. Finally, our thanks to our colleagues in the ETUI’s Working Conditions, Health and Safety Department for proofreading those parts of the manuscript within their fields of expertise – in alphabetical order: Stefano Boy, Marianne De Troyer, Tony Musu and Laurent Vogel. EPSU/ETUI: co-publication © European Trade Union Institute, 2012 ISBN 978-2-87452-222-2 Contents 05 Preface 07 Part 1 Employment and working conditions in European fire services 07 How fire services work 16 Financing 19 Tasks: more diverse everywhere 21 Part 2 Health and safety risks of firefighting 22 Heat risks 25 The risks of smoke 27 Physical hazards 28 Psychosocial risks 31 Part 3 Union strategies and recommendations 31 Risk assessment and management: ways to make operations safer 33 Personal protective equipment and other equipment 40 The importance of drilling and specific training 42 Rethinking health surveillance at work 47 Conclusion 49 Bibliography 53 Annexe List of seminar participants 05 Preface Most of us give little thought to firefighters’ working conditions. The head-turning sights and sounds of "blues and twos" as scarlet engines rush high visibility-clad crews to fires tend to overshadow what they do before, during and after. -
Applying Drone Swarms to Improve Firefighters' Efficiency And
applied sciences Article A Survey on Robotic Technologies for Forest Firefighting: Applying Drone Swarms to Improve Firefighters’ Efficiency and Safety Juan Jesús Roldán-Gómez 1,* , Eduardo González-Gironda 2 and Antonio Barrientos 2 1 Departamento de Ingeniería Informática, Escuela Politécnica Superior, Universidad Autónoma de Madrid, Francisco Tomás y Valiente, 11, 28049 Madrid, Spain 2 Centro de Automática y Robótica (UPM-CSIC), Universidad Politécnica de Madrid, José Gutiérrez Abascal, 2, 28006 Madrid, Spain; [email protected] (E.G.-G.); [email protected] (A.B.) * Correspondence: [email protected] Abstract: Forest firefighting missions encompass multiple tasks related to prevention, surveillance, and extinguishing. This work presents a complete survey of firefighters on the current problems in their work and the potential technological solutions. Additionally, it reviews the efforts performed by the academy and industry to apply different types of robots in the context of firefighting missions. Fi- nally, all this information is used to propose a concept of operation for the comprehensive application of drone swarms in firefighting. The proposed system is a fleet of quadcopters that individually are only able to visit waypoints and use payloads, but collectively can perform tasks of surveillance, map- ping, monitoring, etc. Three operator roles are defined, each one with different access to information and functions in the mission: mission commander, team leaders, and team members. These operators take advantage of virtual and augmented reality interfaces to intuitively get the information of the scenario and, in the case of the mission commander, control the drone swarm. Citation: Roldán-Gómez, J.J.; Keywords: robotics; multi-robot systems; swarms; drones; firefighting González-Gironda, E.; Barrientos, A. -
Photovoltaics and Firefighters' Operations: Best Practices
Photovoltaics and Firefighters’ Operations: Best Practices in Selected Countries Report IEA-PVPS T12-09:2017 1 IEA-PVPS-TASK 12 Photovoltaics and Firefighters’ Operations: Best Practices in Selected Countries INTERNATIONAL ENERGY AGENCY PHOTOVOLTAIC POWER SYSTEMS PROGRAM Photovoltaics and Firefighters’ Operations: Best Practices in Selected Countries IEA PVPS Task 12 Report IEA-PVPS T12-09:2017 April 2017 ISBN 978-3-906042-60-2 Authors: Shohei Namikawa Contributors: Geoffrey Kinsey, Garvin Heath, Andreas Wade, Parikhit Sinha, Keiichi Komoto The compilation of this report is supported by New Energy and Industrial Technology Development Organization (NEDO), Japan CONTENTS Executive Summary .......................................................................................................................2 Foreword .........................................................................................................................................5 1. Introduction .............................................................................................................................6 1.1. Objective ...............................................................................................................................6 1.2. Cases of fires involving PV systems.................................................................................6 1.3. Potential hazards in PV systems .......................................................................................8 1.4. Categories to mitigate hazards and components of this