Galley and Overhead Compartment Experiment Results- Full-Scale
Total Page:16
File Type:pdf, Size:1020Kb
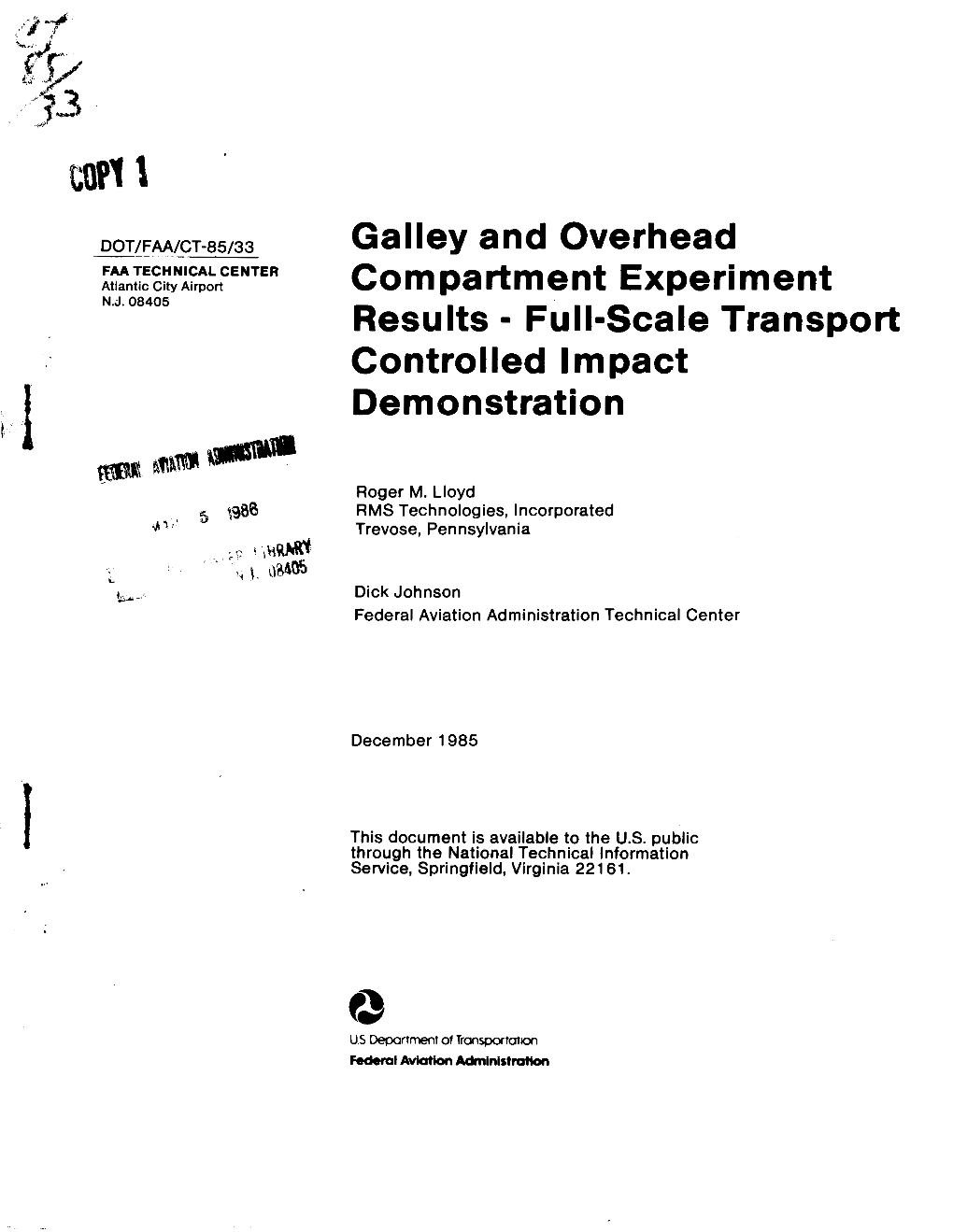
Load more
Recommended publications
-
FOOD SAFETY in AVIATION Presented by Brig Gen(Retd) Md Abdur Rab Miah
WELCOME TO CAA, BANGLADESH DECRALATION OF WORLD HEALTH ASSEMBLY In 1974, the 27th world health Assembly stressed, “ the need for each member state to shoulder the responsibilities for the Safety of food Wat e r , and proper handling of waste disposal in international traffic.” FOOD SAFETY IN AVIATION Presented by Brig Gen(Retd) Md Abdur Rab Miah CAPSCA Focal Person & Aviation Public Health Inspector and consultant Civil Aviation Authority, Bangladesh POINTS OF DISCUSSION Introduction Standards of Flight catering Premises Water Supply Storage of Food Food Handlers Food Preparation Staff Cloakroom Crew Meals Transportation of food to the aircraft Waste Disposal Flight Catering Laboratory Flight Catering Inspection , Conclusion INTRODUCTION Food safety in Aviation ensures hygiene, wholesomeness and soundness of food from its production to its final consumption by the passengers and crew. So, the air operators are to provide contaminants free ,hygienic , safe, attractive, palatable and high quality food to the consumers. Because the passengers assess an airline by the quality of the meals it serves on board. STANDARD OF FLT CAT PREMISES 1) Flight catering premises - spacious (2) Protection against rodents & insects 3) Lighting and ventilation (4) Located at or in the vicinity of airport 5) No projections or ledges on the wall (6) Floor- smooth but not slippery (7) Walls to be tiles fitted with min partition (8) or, Washable/Glossy paint PROTECTION AGAINST INSECTS & RODENTS All doors, windows and other openings should be insect-proof • Plastic insect-proof screening is recommended Kitchen entrances should have self-closing, double doors, opening outwards. EXCLUSION OF DOMESTIC ANIMALS Dogs, cats and other domestic animals should be excluded from all parts of the food premises. -
Cabin Crew Safety January-February 2000
F L I G H T S A F E T Y F O U N D A T I O N CABIN CREW SAFETY Vol. 35 No. 1 For Everyone Concerned with the Safety of Flight January–February 2000 Working in, Around Aircraft Cabins Requires Awareness of Fall Prevention The availability of limited data on slips, trips and falls during normal aircraft operations complicates efforts to improve the prevention of injury to crewmembers and passengers in the cabin environment. Nevertheless, airlines periodically should review fall-prevention strategies and related training of flight attendants and other workers. FSF Editorial Staff In most contexts, being injured by a fall simply study by the U.S. Bureau of Labor Statistics said means that the force of gravity caused a person’s that falls were the most common “injury and downward motion and injury occurred when illness cases by event or exposure” for pilots, most the moving person suddenly decelerated by striking involving walkways, stairs and vehicles. Falls were a surface or an object. When aircraft are in flight the third most common such event for flight or in motion on the ground, a variety of factors attendants, most involving walkways and stairs.1 can contribute to falls. For example, accident/ incident reports have identified factors such as In the early 1990s, researchers attempting to study turbulence, autopilot malfunctions, aircraft fatal falls in the workplace encountered difficulty upsets, sudden evasive maneuvers by flight crews, identifying such occurrences in most industries.2 aircraft collisions with airport structures, collisions Researchers have found that the available data do between ground vehicles and aircraft, and sudden not specify the circumstances for a large proportion braking while a flight crew is taxiing the of falls.3 Similarly, little public data and few studies aircraft. -
Aircraft Accident Report: American Airlines, Inc., Mcdonnell Douglas
Explosive decompression, American Airlines, Inc., McDonnell Douglas DC-10-10, N103AA, Near Windsor, Ontario, Canada, June 12, 1972 Micro-summary: On climb, this McDonnell Douglas DC-10-10 experienced an opening of a cargo door, explosive decompression, and a main cabin floor collapse, disrupting the flight control system. Event Date: 1972-06-12 at 1925 EST Investigative Body: National Transportation Safety Board (NTSB), USA Investigative Body's Web Site: http://www.ntsb.gov/ Cautions: 1. Accident reports can be and sometimes are revised. Be sure to consult the investigative agency for the latest version before basing anything significant on content (e.g., thesis, research, etc). 2. Readers are advised that each report is a glimpse of events at specific points in time. While broad themes permeate the causal events leading up to crashes, and we can learn from those, the specific regulatory and technological environments can and do change. Your company's flight operations manual is the final authority as to the safe operation of your aircraft! 3. Reports may or may not represent reality. Many many non-scientific factors go into an investigation, including the magnitude of the event, the experience of the investigator, the political climate, relationship with the regulatory authority, technological and recovery capabilities, etc. It is recommended that the reader review all reports analytically. Even a "bad" report can be a very useful launching point for learning. 4. Contact us before reproducing or redistributing a report from this anthology. Individual countries have very differing views on copyright! We can advise you on the steps to follow. -
6 Fuselage Design
6 - 1 6 Fuselage design In conventional aircraft the fuselage serves to accommodate the payload. The wings are used to store fuel and are therefore not available to accommodate the payload. The payload of civil aircraft can consist of passengers, baggage and cargo. The passengers are accommodated in the cabin and the cargo in the cargo compartment. Large items of baggage are also stored in the cargo compartment, whereas smaller items are taken into the cabin as carry-on baggage and stowed away in overhead stowage compartments above the seats. The cockpit and key aircraft systems are also located in the fuselage. 6.1 Fuselage cross-section and cargo compartment Today’s passenger aircraft have a constant fuselage cross-section in the central section. This design reduces the production costs (same frames; simply instead of doubly curved surfaces, i.e. a sheet of metal can be unwound over the fuselage) and makes it possible to construct aircraft variants with a lengthened or shortened fuselage. In this section we are going to examine the cross-section of this central fuselage section. In order to accommodate a specific number of passengers, the fuselage can be long and narrow or, conversely, short and wide. As the fuselage contributes approximately 25% to 50 % of an aircraft's total drag, it is especially important to ensure that it has a low-drag shape. A fuselage 1 fineness ratio ldFF/ of approximately 6 provides the smallest tube drag . However, as a longer fuselage leads to a longer tail lever arm, and therefore to smaller empennages and lower tail drag, a fineness ratio of 8 is seen as the ideal according to [ROSKAM III]. -
Cabin Safety Subject Index
Cabin Safety Subject Index This document is prepared as part of the FAA Flight Standards Cabin Safety Inspector Program. For additional information about this document or the program contact: Donald Wecklein Pacific Certificate Management Office 7181 Amigo Street Las Vegas, NV 89119 [email protected] Jump to Table of Contents Rev. 43 Get familiar with the Cabin Safety Subject Index The Cabin Safety Subject Index (CSSI) is a reference guide to Federal Regulations, FAA Orders, Advisory Circulars, Information for Operators (InFO), Safety Alerts for Operators (SAFO), legal interpretations, and other FAA related content related to cabin safety. Subscribe to updates If you would like to receive updates to the Cabin Safety Subject Index whenever it’s revised, click here: I want to subscribe and receive updates. This is a free service. You will receive an automated response acknowledging your request. You may unsubscribe at any time. Getting around within the CSSI The CSSI structure is arranged in alphabetical order by subject, and the document has direct links to the subject matter, as well as links within the document for ease of navigation. The Table of Contents contains a hyperlinked list of all subjects covered within the CSSI. • Clicking the topic brings you to the desired subject. • Clicking the subject brings you back to the Table of Contents. • Next to some subjects you will see (also see xxxxxxxx). These are related subjects. Click on the “also see” subject and it will bring you directly to that subject. • Clicking on hyperlinked content will bring you directly to the desired content. -
Download This Article
A compre hensive systems-level approach in cabin design minimizes fire potential and helps ensure passenger safety. 18 AERO QUARTERLY QTR_04 | 11 Fire Protection: Passenger Cabin The cabins on all Boeing airplanes incorporate comprehensive fire-protective features and materials to minimize the potential for a fire and help ensure the safety of passengers. By Arthur L. Tutson, Boeing Organization Designation Authorization, Authorized Representative, Fire Protection; Douglas E. Ferguson, Technical Safety Chief, Fire Protection, Technical Services and modifications; and Mike Madden, Deputy Pressurized Compartment Fire Marshal, Payloads Design This article is the third in a series exploring approach that goes beyond ensuring This article describes how Boeing the implementation of fire protection on individual parts meet fire property require- incorporates fire protection features and transport category airplanes. ments by looking at the integration of all materials into the airplane cabin that meet those parts on the airplane. This approach or exceed fire protection standards defined Two types of fires can affect an airplane uses the principles of material selection, by U.S. Federal Aviation Regulations (FAR). and its occupants: in-flight and post-crash. separation, isolation, detection, and control. an in-flight fire usually occurs as a result of These principles involve separating the a system or component failure or mainte- FIRE-PROTECTIVE MATERIALS three contributory factors to a fire (fuel, nance issue. A post-crash fire usually ignition source, and oxygen), isolating results from ignition of fuel released during Most materials used in the construction potential fires from spreading to other parts a crash landing. Boeing considers both of passenger compartment interiors are of the airplane, and controlling a fire should types of fires when designing for airplane required by the U.S. -
American Airlines
AMERICAN AIRLINES FLIGHT ATTENDANT AGREEMENT Between AMERICAN AIRLINES, INC. and THE ASSOCIATION OF PROFESSIONAL FLIGHT ATTENDANTS DECEMBER 13, 2014 TABLE OF CONTENTS Section 1 Recognition and Scope .......................................... 1-1 Section 2 Definitions………………………………………..2-1 Section 3 Compensation ........................................................ 3-1 Section 4 Expenses ................................................................ 4-1 Section 5 Moving Expenses .................................................. 5-1 Section 6 Crew Accommodations ........................................ 6-1 Section 7 Uniforms ............................................................... 7-1 Section 8 Vacation ............................................................... 8-1 Section 9 Sick Leave ............................................................ 9-1 Section 10 Scheduling .......................................................... 10-1 Section 11 Hours of Service ................................................. 11-1 Section 12 Reserve Duty ...................................................... 12-1 Section 13 Temporary Duty Assignment (TDY) .................. 13-1 Section 14 International Flying ............................................ 14-1 Section 15 Foreign Language Speaker ................................. 15-1 Section 16 Deadheading ....................................................... 16-1 Section 17 Co-Terminals ...................................................... 17-1 Section 18 Charters .............................................................. -
The American Airlines Bankruptcy
University of Tennessee, Knoxville TRACE: Tennessee Research and Creative Exchange Chapter 11 Bankruptcy Case Studies College of Law Student Work 4-28-2017 How to Get Away with Merger: The American Airlines Bankruptcy Kelsey Cunningham Osborne Christopher K. Coleman Follow this and additional works at: https://trace.tennessee.edu/utk_studlawbankruptcy Part of the Bankruptcy Law Commons Recommended Citation Cunningham Osborne, Kelsey and Coleman, Christopher K., "How to Get Away with Merger: The American Airlines Bankruptcy" (2017). Chapter 11 Bankruptcy Case Studies. https://trace.tennessee.edu/utk_studlawbankruptcy/46 This Article is brought to you for free and open access by the College of Law Student Work at TRACE: Tennessee Research and Creative Exchange. It has been accepted for inclusion in Chapter 11 Bankruptcy Case Studies by an authorized administrator of TRACE: Tennessee Research and Creative Exchange. For more information, please contact [email protected]. How To Get Away with Merger: The American Airlines Bankruptcy By: Kelsey Cunningham Osborne & Christopher K. Coleman Table of Contents Cast of Characters ...................................................................................................... 4 I. Introduction ............................................................................................................. 6 II. The Debtor’s Business .......................................................................................... 7 III. Events Leading to Filing for Chapter 11 ..................................................... -
National Transportation Safety Board
b NATIONAL TRANSPORTATION SAFETY BOARD WASHINGTON, D.C. 20594 AIRCRAFT ACCIDENT REPORT SCANDINAVIAN AIRLINES SYSTEM FLIGHT 901 McDONNELL DOUGLAS DC- 10-30 JOHN F. KENNEDY INTERNATIONAL AIRPORT JAMAICA, NEW YORK FEBRUARY 28, 1984 NTSB/AAR-84/ 15 UNITED STATES GOVERNMENT NTSB/AkR-84/15 PB84-910415 4. Ti t le end Subt i t le Aircraft Accident Report-- 5.Report Date Scandinavian Airlines System Flight 901 MdDonnell Douglas November 15, 1984 DC-10-3d Norwegian Registry LN-RKB John F. Kennedy Inter- 6.Performi ng Organization national Aimort Jamaica. New York, Februarv 28. 1984 Code 7. Author(s) 8.Performing Organization Report No. 9. Performing Organization Name and Address 10.Work Unit No. National Transportation Safety Board 3894-A Bureau of Accident Investigation 11.Contract or Grant No. Washington, D.C. 20594 1 13.Type of Report and Period Covered 12.Sponsdring Agency Name and Address Aircraft Accident Report February 28, 1984 NATIONAL TRANSPORTATION SAFETY BOARD Washington, D. C. 20594 1 .Sponsoring Agency Code 1 15.Supplementary Notes 1.8bstract On February 28, 1984, Scandinavian Airlines System Flight 901, a McDonnell Douglas DC-10-30, was a regularly scheduled international passenger flight from Stockholm, Sweden, to New York City, New York, with an en route stop at Oslo, Norway. Following an approach to runway 4 right at New York's John F. Kennedy International Airport, the airplane touched down about 4,700 ft (1,440 meters) beyond the threshold of the 8,400-foot (2,560-meter) runway and could not be stopped on the runway. The airplane was steered to the right to avoid the approach light pier at the departure end of the runway and came to rest in Thurston Basin, a tidal waterway located about 600 ft from the departure end of runway 4R. -
FDA Could Better Communicate with Airlines to Encourage Voluntary Construction Inspections of Aircraft Galleys and Lavatories
United States Government Accountability Office Report to Congressional Committees September 2020 AVIATION SANITATION FDA Could Better Communicate with Airlines to Encourage Voluntary Construction Inspections of Aircraft Galleys and Lavatories GAO-20-612 September 2020 AVIATION SANITATION FDA Could Better Communicate with Airlines to Encourage Voluntary Construction Inspections of Highlights of GAO-20-612, a report to Aircraft Galleys and Lavatories congressional committees Why GAO Did This Study What GAO Found Voluntary construction inspections are Most commercial aircraft undergo voluntary inspections to ensure that galleys the primary mechanism by which FDA and lavatories are constructed and assembled to meet the Food and Drug oversees compliance with its required Administration’s (FDA) sanitation standards, according to industry sanitation standards for the representatives. Twenty-seven percent of the inspections FDA conducted construction of aircraft galleys and between fiscal years 2015 and 2019 found objectionable conditions. But in nearly lavatories. all of these instances, the conditions identified, such as the need for additional A report accompanying the House sealant in areas where there was a gap or seam, were corrected by the airline or 2019 Agriculture, Rural Development, aircraft manufacturer during the inspection. However, some regional airline Food and Drug Administration, and representatives told GAO that their aircraft do not receive these construction Related Agencies Appropriations bill inspections, either because larger airlines with which they have contracts told included a provision for GAO to review them the inspections were unnecessary or because they did not believe the FDA’s process for ensuring proper inspections were relevant to them. FDA provides these inspections free of sanitation in aircraft galleys and charge, upon request of aircraft manufacturers or airlines, and aircraft passing lavatories. -
1995 Gulfstream GIVSP S/N 1262 (N432HC)
1995 Gulfstream GIVSP s/n 1262 (N432HC) Specifications subject to verification upon inspection and 35 Waterview Blvd. 2nd FL. Parsippany, NJ 07054 aircraft is subject to prior sale or withdrawal from the market. [email protected] | 201.891.0881 | LEAS.COM 1995 Gulfstream GIVSP s/n 1262 Airframe: 15,651 Hours 7,582 Landings Date of Manufacture (CofA): March 1995 Entry into Service: December 1995 Engines: Rolls-Royce TAY 611-8 (MSG-3) Engines are Hard-Time & Enrolled on Rolls-Royce CorporateCare Left (Eng #1): S/N: 16663 15,002 Eng. Hrs. Since New 7,280 Eng. Cycles Mid-Life c/w May 2019 at 14,654 Hrs. & 7,136 Cycles (348 Hrs TSMLI) Overhaul c/w May 2019 at 14,654 Hrs. & 7,136 Cycles (348 Hrs TSOH) Right (Eng #2): S/N: 16664 15,054 Eng. Hrs. Since New 7,309 Eng. Cycles Mid-Life c/w May 2019 at 14,707 Hrs. & 7,165 Cycles (348 Hrs TSMLI) Overhaul c/w May 2019 at 14,707 Hrs. & 7,165 Cycles (348 Hrs TSOH) APU: Enrolled on MSP & On Condition GTCP36-150G S/N: P-789C 9,323 Hrs 1995 Gulfstream GIVSP s/n 1262 Avionics: Honeywell 6-Tube EFIS Enrolled on Honeywell HAPP Dual Honeywell SPZ-8400 Digital Auto Pilot Dual Honeywell FZ-820 Flight Guidance Computers Dual Honeywell NZ-2010 LR NAV/FMS w/ 6.1 Software Dual Collins VHF-422B COMM (8.33 Spacing) Dual Collins VIR-432 NAV w/ FM Immunity Dual Collins ADF-462 Dual Collins DME-442 Dual Honeywell AA-300 Radio Altimeter Dual Collins HF-9000 w/ Selcal HF COMM Honeywell Primus 870 Weather Radar Dorne & Margolin ELT Dual Honeywell 12-Channel GPS Dual Collins TDR-94D Mode S Transponder w/ Flight ID & -
Basics of the Aircraft Cabin Environment Enable a Hygienic Environment and Contaminant Control
Use Tab 'Insert - Header & Footer' for Presentation Title - Siglum - Reference Month 200X CAPSCA-Europe Meeting, Bern 18-21 June 2013 Basics of the aircraft cabin environment Enable a hygienic environment and contaminant control Presented by Dr Joerg CREMERS from Airbus Operations GmbH Expert Cabin Aeromedicine, Health & Comfort Overview Cabin Environment in relation to Hygiene Cabin Environment Air Supply Water/Waste Galley/Food System Potable water System Design & architecture supply Interfaces Contamination Food cooling control Waste water requirements & technologies Disposal Pandemics Page 2 © AIRBUS Operations GmbH. All rights reserved. Confidential and proprietary document. Air Supply System Architecture The Air supply system has three main functions: supply air and pollutant removal; pressurization of the aircraft; temperature control and cooling of technical equipment Page 3 © AIRBUS Operations GmbH. All rights reserved. Confidential and proprietary document. Air Purity and Contaminant Control Outside air Ozone (during cruise) VOC Odours (during ground operation) Converter + Catalytic converters for depletion of Ozone / VOC Ozone Pathogens outside air: adiabatic compression in engine Remover Pure Air Pure Pathogens inside: HEPA filters, also odours PACKs = Conditioned, filtered, pure air = Passenger well-being Air conditioning HEPA* Particles free Gaseous** Cabin air no odour Filter air Filter * HEPA : High Efficiency Particulate Air filter * VOC : Volatile Organic Compounds; ** Option on A330/A340 only Page 4 © AIRBUS Operations GmbH. All rights reserved. Confidential and proprietary document. Use Tab 'Insert - Header & Footer' for Presentation Title - Siglum - Reference Air Ventilation aspects in Relation to Pandemics Risk of virus transmission is minimized by avoiding longitudinal flow, use of HEPA filters, low humidity of cabin air (5-15 %). Studies [1], [2] indicate that proximity, specifically in the few rows in front of the index case, is a major factor in the transmission.