Selenium Mineral Commodity Profile
Total Page:16
File Type:pdf, Size:1020Kb
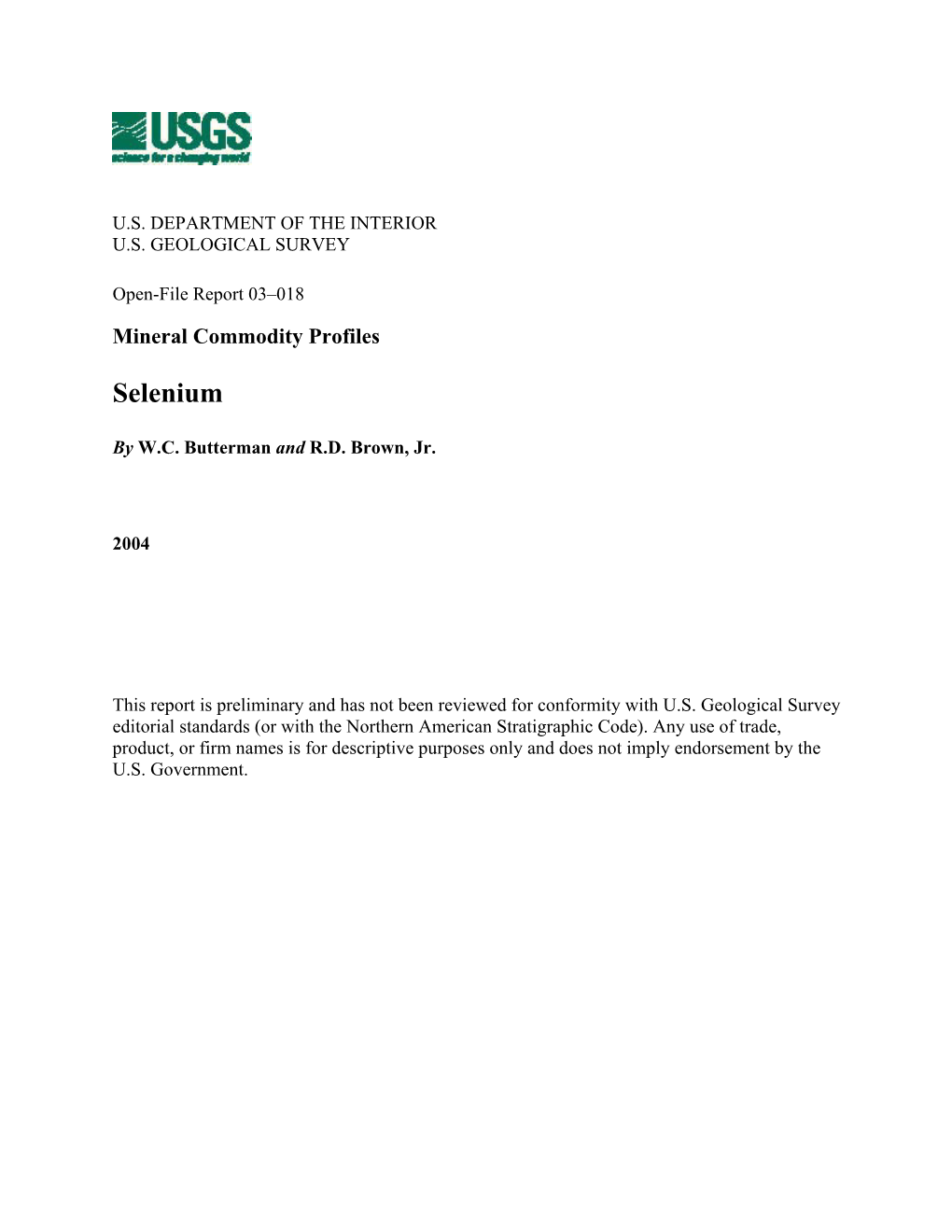
Load more
Recommended publications
-
Selenium Nutritional, Toxicologic, and Clinical Aspects ANNA M
160 Articles Selenium Nutritional, Toxicologic, and Clinical Aspects ANNA M. FAN, PhD, Berkeley, and KENNETH W. KIZER, MD, MPH, Sacramento, California This is one ofa series ofarticles from western state public health departments. Despite the recent findings ofenvironmental contamination, selenium toxicosis in humans is exceedingly rare in the United States, with the few known cases resulting from industrial accidents and an episode involving the ingestion of superpotent selenium supplements. Chronic selenosis is essentially unheard of in this country because of the typical diversity of the American diet. Nonetheless, because ofthe growing public interest in selenium as a dietary supplement and the occurrence ofenvironmental selenium contamination, medical practitioners should be familiar with the nutritional, toxicologic, and clinical aspects of this trace element. (Fan AM, Kizer KW: Selenium-Nutritional, toxicologic, and clinical aspects. West J Med 1990 Aug; 153:160-167) Since the recognition of the nutritional essentiality of and other parts of the world.4 Highly seleniferous soils selenium (Se) in animals in 1957, there has been ever- yielding selenium-toxic plants (such as Astragalus bisulca- increasing interest in this trace element. This interest has tus) are widespread in South Dakota, Wyoming, Montana, heightened in the past decade concomitant with the recog- North Dakota, Nebraska, Kansas, Colorado, Utah, Arizona, nition of selenium's essential nutritional role in humans and New Mexico. Soil containing high selenium concentra- and reports of selenium toxicity among humans. Interest in tions but not yielding toxic plants is found in Hawaii. selenium has been further aroused recently by the findings of elevated levels of this compound in certain soils and wa- Chemical Forms ter sources in the western United States, leading to adverse Selenium is a nonmetallic element chemically related to effects on fish and wildlife (T. -
The Electronic and Optical Properties of Close Packed Cadmium Selenide Quantum Dot Solids
The Electronic and Optical Properties of Close Packed Cadmium Selenide Quantum Dot Solids by Cherie Renee Kagan B. S. E. Materials Science and Engineering B. A. Mathematics University of Pennsylvania, Philadelphia, PA 1991 Submitted to the Department of Materials Science and Engineering in Partial Fulfillment of the Requirements for the Degree of DOCTOR OF PHILOSOPHY at the MASSACHUSETTS INSTITUTE OF TECHNOLOGY September 1996 0 1996 Massachusetts Institute of Technology All rights reserved Signature of the Author Departmenf of Materials Science and Engineering August 9, 1996 Certified by_ Moungi G. Bawendi Professor of Chemistry Thesis Supervisor Accepted by Linn W. Hobbs John F. Elliott Professor of Materials Science and Engineering Chair, Department Committee on Graduate Students AROHIvES ()F Tac(.!-otodY SEP 2 71996 Room 14-0551 77 Massachusetts Avenue Cambridge, MA 02139 Ph: 617.253.2800 MITLbries Email: [email protected] Document Services http://Iibraries.mit.eduldocs DISCLAIMER OF QUALITY Due to the condition of the original material, there are unavoidable flaws in this reproduction. We have made every effort possible to provide you with the best copy available. If you are dissatisfied with this product and find it unusable, please contact Document Services as soon as possible. Thank you. The images contained in this document are of the best quality available. 2 3 The Electronic and Optical Properties of Close Packed Cadmium Selenide Quantum Dot Solids by Cherie Renee Kagan - Submitted to the Department of Materials Science and Engineering on August 9, 1996 in Partial Fulfillment of the Requirements for the Degree of Doctor of Philosophy in Materials Science and Engineering Abstract The synthesis, structural characterization, optical spectroscopy, and electronic characterization of close packed solids prepared from CdSe QD samples tunable in size from 17 to 150 A in diameter (a<4.5%) are presented. -
Transport of Dangerous Goods
ST/SG/AC.10/1/Rev.16 (Vol.I) Recommendations on the TRANSPORT OF DANGEROUS GOODS Model Regulations Volume I Sixteenth revised edition UNITED NATIONS New York and Geneva, 2009 NOTE The designations employed and the presentation of the material in this publication do not imply the expression of any opinion whatsoever on the part of the Secretariat of the United Nations concerning the legal status of any country, territory, city or area, or of its authorities, or concerning the delimitation of its frontiers or boundaries. ST/SG/AC.10/1/Rev.16 (Vol.I) Copyright © United Nations, 2009 All rights reserved. No part of this publication may, for sales purposes, be reproduced, stored in a retrieval system or transmitted in any form or by any means, electronic, electrostatic, magnetic tape, mechanical, photocopying or otherwise, without prior permission in writing from the United Nations. UNITED NATIONS Sales No. E.09.VIII.2 ISBN 978-92-1-139136-7 (complete set of two volumes) ISSN 1014-5753 Volumes I and II not to be sold separately FOREWORD The Recommendations on the Transport of Dangerous Goods are addressed to governments and to the international organizations concerned with safety in the transport of dangerous goods. The first version, prepared by the United Nations Economic and Social Council's Committee of Experts on the Transport of Dangerous Goods, was published in 1956 (ST/ECA/43-E/CN.2/170). In response to developments in technology and the changing needs of users, they have been regularly amended and updated at succeeding sessions of the Committee of Experts pursuant to Resolution 645 G (XXIII) of 26 April 1957 of the Economic and Social Council and subsequent resolutions. -
The Management of Common Skin Conditions in General Practice
Management of Common Skin Conditions In General Practice including the “red rash made easy” © Arroll, Fishman & Oakley, Department of General Practice and Primary Health Care University of Auckland, Tamaki Campus Reviewed by Hon A/Prof Amanda Oakley - 2019 http://www.dermnetnz.org Management of Common Skin Conditions In General Practice Contents Page Derm Map 3 Classic location: infants & children 4 Classic location: adults 5 Dermatology terminology 6 Common red rashes 7 Other common skin conditions 12 Common viral infections 14 Common bacterial infections 16 Common fungal infections 17 Arthropods 19 Eczema/dermatitis 20 Benign skin lesions 23 Skin cancers 26 Emergency dermatology 28 Clinical diagnosis of melanoma 31 Principles of diagnosis and treatment 32 Principles of treatment of eczema 33 Treatment sequence for psoriasis 34 Topical corticosteroids 35 Combination topical steroid + antimicrobial 36 Safety with topical corticosteroids 36 Emollients 37 Antipruritics 38 For further information, refer to: http://www.dermnetnz.org And http://www.derm-master.com 2 © Arroll, Fishman & Oakley, Department of General Practice and Primary Health Care, University of Auckland, Tamaki Campus. Management of Common Skin Conditions In General Practice DERM MAP Start Is the patient sick ? Yes Rash could be an infection or a drug eruption? No Insect Bites – Crop of grouped papules with a central blister or scab. Is the patient in pain or the rash Yes Infection: cellulitis / erysipelas, impetigo, boil is swelling, oozing or crusting? / folliculitis, herpes simplex / zoster. Urticaria – Smooth skin surface with weals that evolve in minutes to hours. No Is the rash in a classic location? Yes See our classic location chart . -
List of Union Reference Dates A
Active substance name (INN) EU DLP BfArM / BAH DLP yearly PSUR 6-month-PSUR yearly PSUR bis DLP (List of Union PSUR Submission Reference Dates and Frequency (List of Union Frequency of Reference Dates and submission of Periodic Frequency of submission of Safety Update Reports, Periodic Safety Update 30 Nov. 2012) Reports, 30 Nov. -
A 1 Case-PR/ }*Rciofft.;Is Report
.A 1 case-PR/ }*rciofft.;is Report (a) This eruption site on Mauna Loa Volcano was the main source of the voluminous lavas that flowed two- thirds of the distance to the town of Hilo (20 km). In the interior of the lava fountains, the white-orange color indicates maximum temperatures of about 1120°C; deeper orange in both the fountains and flows reflects decreasing temperatures (<1100°C) at edges and the surface. (b) High winds swept the exposed ridges, and the filter cannister was changed in the shelter of a p^hoehoc (lava) ridge to protect the sample from gas contamination. (c) Because of the high temperatures and acid gases, special clothing and equipment was necessary to protect the eyes. nose, lungs, and skin. Safety features included military flight suits of nonflammable fabric, fuil-face respirators that are equipped with dual acidic gas filters (purple attachments), hard hats, heavy, thick-soled boots, and protective gloves. We used portable radios to keep in touch with the Hawaii Volcano Observatory, where the area's seismic activity was monitored continuously. (d) Spatter activity in the Pu'u O Vent during the January 1984 eruption of Kilauea Volcano. Magma visible in the circular conduit oscillated in a piston-like fashion; spatter was ejected to heights of 1 to 10 m. During this activity, we sampled gases continuously for 5 hours at the west edge. Cover photo: This aerial view of Kilauea Volcano was taken in April 1984 during overflights to collect gas samples from the plume. The bluish portion of the gas plume contained a far higher density of fine-grained scoria (ash). -
United States Patent (19) 11, 3,989,755 Mccoy Et Al
United States Patent (19) 11, 3,989,755 McCoy et al. (45) Nov. 2, 1976 54 PRODUCTION OF OXIMES BY THE (56) References Cited REACTION OF CARBON MONOXDE WITH UNITED STATES PATENTS NTROCOMPOUNDS 2,945,065 7/1960 Donaruma...................... 260/566 A 75) Inventors: John J. McCoy, Media; John G. 3,480,672 11/1969 Kober et al..................... 260/566 A Zajacek, Strafford, both of Pa.; Karl 3,734,964 5/1973 Knifton........................... 260/566. A E. Fuger, Therwil, Switzerland (73) Assignee: Atlantic Richfield Company, Los Primary Examiner-Gerald A. Schwartz Angeles, Calif. Attorney, Agent, or Firm-Delbert E. McCaslin 22 Filed: Feb. 20, 1975 (21) Appl. No.: 551,487 57) ABSTRACT Related U.S. Application Data Production of oximes (and ketones) by contacting at 63) Continuation-in-part of Ser. No. 372,457, June 21, elevated temperatures and pressures, a primary or sec 1973, abandoned. ondary saturated aliphatic nitrocompound with carbon monoxide in the presence of a catalyst comprising me 52 U.S. C. ........................ 260/566 A; 260/586 C; tallic selenium or inorganic selenium compounds and 260/586 R; 260/593 R a base. (51 int. Cl”........................................ C07C 131/04 58) Field of Search........ 260/566 A, 586 A, 586 R, 20 Claims, No Drawings 260/593 R 3,989,755 2 cycloaliphatic nitrocompound is contacted with carbon PRODUCTION OF OXIMES BY THE REACTION OF monoxide at temperatures in the range of from 50° to 200 C. under pressures in the range of from 10 atmo CARBON MONOXIDE WITH NITROCOMPOUNDS spheres to 200 atmospheres in the presence of a sele nium catalyst and a base. -
Organic Chemistry. T
View Article Online / Journal Homepage / Table of Contents for this issue i. 369 Organic Chemistry. Nature of the Kolbe Electrochemical Synthesis of Hydrocarbons. FH. FICHTERand EDUARDKRUMMENAUHEH (Helvetica Chim. A cia, 1918, 1, 146-166).-The authors discuss the two theories put forward to explain the' mechanism of the Kolbe hydrocarbon synthesis, and draw the conclusion that the oxidation thsory is more in accord with fact than the theory based on the ionic hypothesis. It is shown that peroxides are produced by electrochemical oxidation, on platinum anodes, of solutions of saturated fatty acids and their salts. Since them peroxides may be produced by the action of hydrogen peroxide on aci6 anhydrides, it is to be assumed that the separation of the anhydride is the first step in the hydrocarbon synthesis. The anhydride is then anodic- ally oxidised, with the formation of a very unstable peroxide. The peroxide is then decomposed by the relatively high tempera- ture of the anode, with the formation of the hydrocarbon, thus: R*CO,Na + (RCO),-0 + 0 + (RCO),*O = 0 + R*R+ 2CO,, or a side reaction may also occur, thus: (R*CO),O=O 4 R-CO,*R + CO,. When th? peroxides are decomposed by heat, there is also a considerable amount of methane produced in addition to the expected hydrocarbon. These considerations are adapted to the formation and decom- position of organic peracids. Organic peracids m:by be prepared by the action of hydrogen peroxide on both acids and anhydrides, consequently the formation of these substances electrolytically on the, anode does not necessarily demand the intermediary formation Published on 01 January 1918. -
Treatment of Diseases and Conditions Mediated By
(19) TZZ_ ___T (11) EP 1 572 115 B1 (12) EUROPEAN PATENT SPECIFICATION (45) Date of publication and mention (51) Int Cl.: of the grant of the patent: A61K 38/07 (2006.01) A61K 38/08 (2006.01) 21.01.2015 Bulletin 2015/04 A61K 38/17 (2006.01) A61K 38/38 (2006.01) (21) Application number: 03799853.1 (86) International application number: PCT/US2003/037901 (22) Date of filing: 25.11.2003 (87) International publication number: WO 2004/050023 (17.06.2004 Gazette 2004/25) (54) TREATMENT OF DISEASES AND CONDITIONS MEDIATED BY INCREASED PHOSPHORYLATION BEHANDLUNG VON ERKRANKUNGEN UND ZUSTÄNDEN,DIE DURCH ERHÖHTE PHOSPHORYLIERUNG VERMITTELT WERDEN TRAITEMENT DE MALADIES ET D’ETATS A MEDIATION DE PHOSPHORYLATION ACCRUE (84) Designated Contracting States: • JIANG B ET AL: "Phosphopeptides derived from AT BE BG CH CY CZ DE DK EE ES FI FR GB GR hen egg yolk phosvitin: effect of molecular size HU IE IT LI LU MC NL PT RO SE SI SK TR on the calcium-binding properties." BIOSCIENCE, BIOTECHNOLOGY, AND (30) Priority: 27.11.2002 US 429924 P BIOCHEMISTRY MAY 2001, vol. 65, no. 5, May 2001 (2001-05), pages 1187-1190, XP002549556 (43) Date of publication of application: ISSN: 0916-8451 14.09.2005 Bulletin 2005/37 • KATAYAMA SHIGERU ET AL: "Antioxidative stress activity of oligophosphopeptides derived (73) Proprietor: Ampio Pharmaceuticals, Inc. from hen egg yolk phosvitin in Caco-2 cells." Englewood, CO 80112 (US) JOURNAL OF AGRICULTURAL AND FOOD CHEMISTRY 8 FEB 2006, vol. 54, no. 3, 8 February (72) Inventor: BAR-OR, David 2006 (2006-02-08), pages 773-778, XP002549557 Englewood, CO 80110 (US) ISSN: 0021-8561 • OKAMOTO ET AL: ’The interleukin-8 AP-1 and (74) Representative: Weber, Joachim kappa B-like sites are genetic end targets of Hoefer & Partner FK506-sensitive pathway accompanied by Patentanwälte calcium mobilization.’ JOURNAL OF Pilgersheimer Strasse 20 BIOLOGICAL CHEMISTRY vol. -
Table of Contents (Print, Part 1)
CONTENTS - Continued PHYSICAL REVIEW B THIRD SERIES, VOLUME 90, NUMBER 16 OCTOBER 2014-15(II) COMMENTS Comment on “Canonical magnetic insulators with isotropic magnetoelectric coupling” (3 pages) ............... 167101 J. M. Perez-Mato, Samuel V. Gallego, E. S. Tasci, L. Elcoro, and M. I. Aroyo Reply to “Comment on ‘Canonical magnetic insulators with isotropic magnetoelectric coupling’ ” (1 page) . 167102 Sinisa Coh and David Vanderbilt Comment on “Ideal strength and phonon instability in single-layer MoS2” (3 pages) .......................... 167401 Ryan C. Cooper, Jeffrey W. Kysar, and Chris A. Marianetti Reply to “Comment on ‘Ideal strength and phonon instability in single-layer MoS2’”(3 pages) ................ 167402 Tianshu Li The editors and referees of PRB find these papers to be of particular interest, importance, or clarity. Please see our Announcement Phys. Rev. B 77, 130001 (2008). CONTENTS - Continued PHYSICAL REVIEW B THIRD SERIES, VOLUME 90, NUMBER 16 OCTOBER 2014-15(II) Readout and dynamics of a qubit built on three quantum dots (12 pages) .................................... 165427 Jakub Łuczak and Bogdan R. Bułka Experimental verification of reciprocity relations in quantum thermoelectric transport (6 pages) ................ 165428 J. Matthews, F. Battista, D. Sanchez,´ P. Samuelsson, and H. Linke Noncollinear magnetic phases and edge states in graphene quantum Hall bars (5 pages) ....................... 165429 J. L. Lado and J. Fernandez-Rossier´ Roton-maxon spectrum and instability for weakly interacting dipolar excitons in a semiconductor layer (9 pages) 165430 A. K. Fedorov, I. L. Kurbakov, and Yu. E. Lozovik Influence of edge and field effects on topological states of germanene nanoribbons from self-consistent calculations (7 pages) ................................................................................ 165431 Lars Matthes and Friedhelm Bechstedt Electronic structure and magnetic properties of cobalt intercalated in graphene on Ir(111) (10 pages) .......... -
KNOWN and SUSPECTED HUMAN CARCINOGENS Carcinogens Reference List
KNOWN AND SUSPECTED HUMAN CARCINOGENS Carcinogens Reference List SOURCE AGENCY CARCINOGEN CLASSIFICATIONS: OSHA (O) Occupational Safety and Health Administration ACGIH (G) American Conference of Governmental Industrial Hygienists A1 Confirmed human carcinogen. A2 Suspected human carcinogen. A3 Animal carcinogen. “Available evidence suggests that the agent is not likely to cause cancer in humans except under uncommon or unlikely routes or levels of exposure.” A4 Not classifiable as a human carcinogen. “There are inadequate data on which to classify the agent in terms of its carcinogenicity in humans and/or animals.” A5 Not suspected as a human carcinogen. IARC (I) International Agency for Research on Cancer (World Health Organization) 1 The agent (mixture) is carcinogenic to humans. 2A The agent (mixture) is probably carcinogenic to humans; there is limited evidence of carcinogenicity in humans and sufficient evidence of carcinogenicity in experimental animals. 2B The agent (mixture) is possibly carcinogenic to humans; there is limited evidence of carcinogenicity in humans in the absence of sufficient evidence of carcinogenicity in experimental animals. 3 The agent (mixture, exposure circumstance) is not classifiable as to its carcinogenicity to humans. 4 The agent (mixture, exposure circumstance) is probably not carcinogenic to humans. NTP (N) National Toxicology Program (Health and Human Services Dept., Public Health Service, NIH/NIEHS) 1 Known to be carcinogens. 2 Reasonably anticipated to be carcinogens. CP65 California Proposition 65, “Chemicals Known to the State to Cause Cancer.” Abbreviation: n.o.s. Not otherwise specified; i.e., there is no PEL or TLV. Note: CASRNs fitting the pattern 0-##-0 or 1-##-0 are generated for electronic database purposes only. -
1 Abietic Acid R Abrasive Silica for Polishing DR Acenaphthene M (LC
1 abietic acid R abrasive silica for polishing DR acenaphthene M (LC) acenaphthene quinone R acenaphthylene R acetal (see 1,1-diethoxyethane) acetaldehyde M (FC) acetaldehyde-d (CH3CDO) R acetaldehyde dimethyl acetal CH acetaldoxime R acetamide M (LC) acetamidinium chloride R acetamidoacrylic acid 2- NB acetamidobenzaldehyde p- R acetamidobenzenesulfonyl chloride 4- R acetamidodeoxythioglucopyranose triacetate 2- -2- -1- -β-D- 3,4,6- AB acetamidomethylthiazole 2- -4- PB acetanilide M (LC) acetazolamide R acetdimethylamide see dimethylacetamide, N,N- acethydrazide R acetic acid M (solv) acetic anhydride M (FC) acetmethylamide see methylacetamide, N- acetoacetamide R acetoacetanilide R acetoacetic acid, lithium salt R acetobromoglucose -α-D- NB acetohydroxamic acid R acetoin R acetol (hydroxyacetone) R acetonaphthalide (α)R acetone M (solv) acetone ,A.R. M (solv) acetone-d6 RM acetone cyanohydrin R acetonedicarboxylic acid ,dimethyl ester R acetonedicarboxylic acid -1,3- R acetone dimethyl acetal see dimethoxypropane 2,2- acetonitrile M (solv) acetonitrile-d3 RM acetonylacetone see hexanedione 2,5- acetonylbenzylhydroxycoumarin (3-(α- -4- R acetophenone M (LC) acetophenone oxime R acetophenone trimethylsilyl enol ether see phenyltrimethylsilyl... acetoxyacetone (oxopropyl acetate 2-) R acetoxybenzoic acid 4- DS acetoxynaphthoic acid 6- -2- R 2 acetylacetaldehyde dimethylacetal R acetylacetone (pentanedione -2,4-) M (C) acetylbenzonitrile p- R acetylbiphenyl 4- see phenylacetophenone, p- acetyl bromide M (FC) acetylbromothiophene 2- -5-